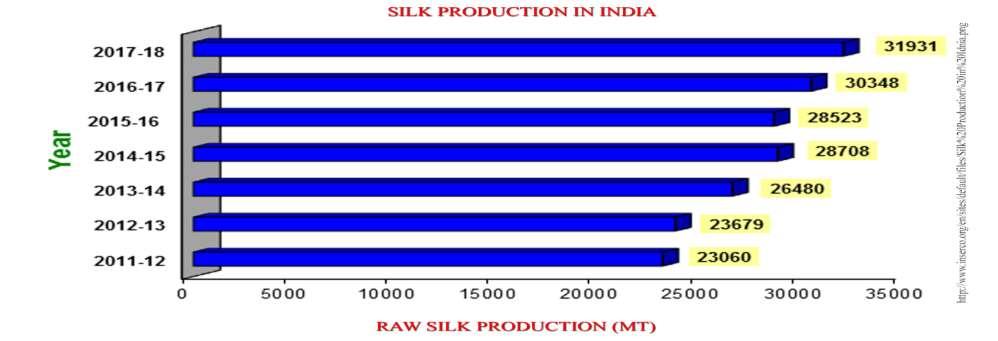
6 minute read
CHAPTER 2: BACKGROUND STUDY
2.1 SILK INDUSTRY IN INDIA:
India is the second largest silk producer of raw silk and also has the distinction of being the world’s largest consumer of pure silk.
Advertisement
India is the only country in the world to produce all the four known varieties of silk including mulberry, eri, tasar and muga. Mulberry is the largest practiced sericulture industry accounting for almost 76 percentage of the entire silk production.
The traditional passion for silk-based products with amazing forms of silk garments endeared at home helps the country to fabricate challenging position in silk industry, as second largest producer of silk and also the largest consumer of silk.
Silk not only is a source of foreign exchange earnings, but also provides employment to 6 million people (mainly hailing from weaker sections of society) in 60,000 villages. It therefore, provides a sustainable boost to rural youth and women to receive handsome remunerative returns mostly as a form of alternative agricultural practice.
Silk industry is further divided into two types based on the labor force and the scale of the organization. The traditional type and modern type.
The traditional industry uses locally available material and skill set and the production takes place at the individual level. Hence the industry is highly scattered and is unorganized. This industry uses very less hired labor where most of the work is done in households.
The modern small scale industry stands closer to the large scale industries in terms of production and the labor hiring but is closer to the traditional industry in terms of organization.
The industry provides employment to more than 7.6 million people across 51,000 villages, who operate 328,627 handlooms and 45,867 power looms with 8,14,616 weavers. Domestic demand stands at 28800 MT compared to production of 23679 MT annually thanks to the growing demand for silk fabrics and sarees from Indian women.
Aggressive promotion of the silk industry in India has attracted a large number of organized players to set up modern units for both apparel as well as home textile production.
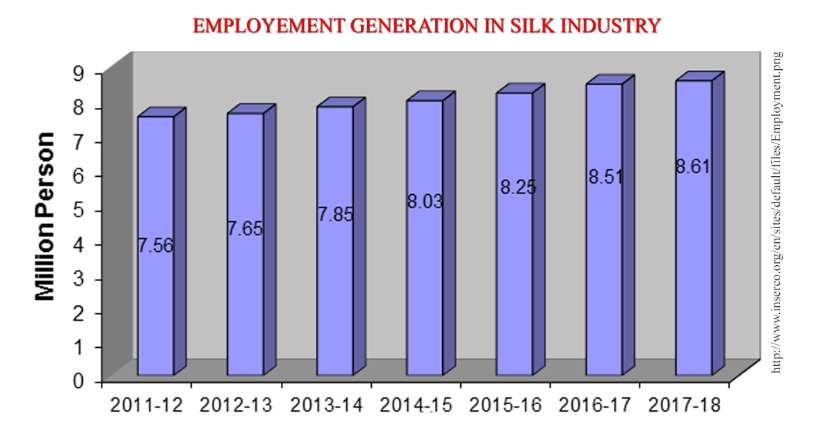
2.2 HANDLOOM INDUSTRY IN INDIA:
The handloom sector is known for its heritage and the tradition of excellent craftsmanship. It provides livelihood to millions of weavers and crafts persons. The industry has not only survived but also grown over the decades due to its inherent strengths like flexibility of production in small quantities, openness to innovation, low level of capital investment and immense possibility of designing fabrics.
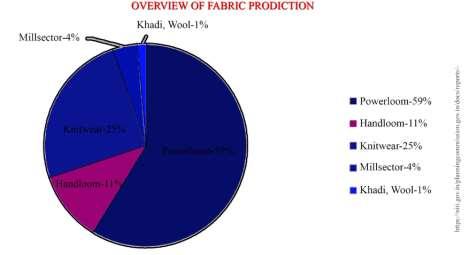
The handloom sector, being labour intensive, provides livelihood to 4.3 million weavers and ancillary workers. The industry has grown over decades owing to its inherent strengths like flexibility of production in small quantities, openness to innovation, low level of capital investment and immense design possibilities. Today, handlooms accounts for nearly 11% of fabric production in India and contributes Rs. 2812 crores to exports in 2012-13.
The handloom industry is a promising industry and undergoing lot of transformation. Large premium design choices - The sector enables larger varieties of design to be spun out which allows the consumers to have customized offerings which are unique in the world. Also, the industry is considered as a designer’s paradise.
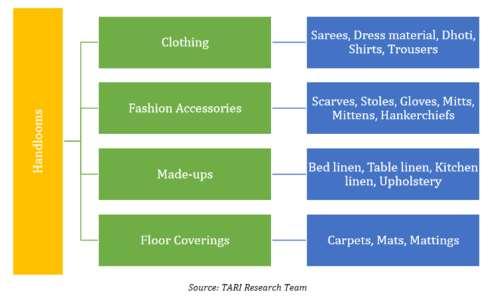
2.3 HISTORY OF WEAVING INDUSTRY IN HINDUPURAM:
Handloom industry occupied an important place in the economy of the town in ancient times weaving was practised in making of cotton, silk and wool. Of which the most important was the weaving of cotton cloth. The inscriptlonal evidence goes to show how the financial Incentives were provided to facilitate the development of the Industry.
A Canarese record from Cholasamudram in Hindupur taluk mentions a tax fixed on each loom (Magga). Another inscription, dated 1536, 37 A.D. informs that the weavers at Hindupur paid half ga per loom, indicating a flourishing textile industry in the district. According to Atharvana Tanthram cotton fabrics were manufactured largely in these areas.
The people mainly engaged in this profession were Togatas, Devangas, and sales and a fair sprinkling of Muslims and Dudekulas.
2.4 SILK WEAVING IN HINDUPURAM:
The old Bellary Mannual (1872), covering a major portion of the present Anantapur district records that at some places in the district both silk and cotton mixed clothes were woven. Thurston, in his monograph on silk industry, refers to silk weaving having been carried on at Uravakonda and Krishtapadu with 300 and 100 looms respectively, mostly by weavers belonging to Devanga, Padmasale and Togota castes.
While women prepared the yarn the men engaged themselves in weaving. The old Anantapur Gazetteer (1905) records that silk cloth was manufactured at Dharmavaram, silk weaving was also taken up at Kalyandurg on a small scale.
The raw material was obtained from Bangalore, Bellary, Mysore and Hubli and the cloth woven was exported to places like Udipi, Hubli and Dharwar. At Tadpatri, cotton cloth was woven with silk borders. But at Dharmavaram the Industry was declining as the supply of raw silk from Bangalore had almost ceased.
2.5 SILK WEAVING PROCESS:
i. PURCHASE OF RAW MATERIAL:
The process of weaving starts with the purchase of raw material from different locations. The major quantity of raw silk that is used in Hindupuram is purchased from Sidlaghata town, secondary markets are ramnagar and kollegal.
ii. DYEING:
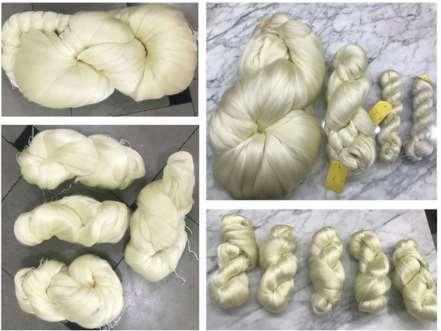
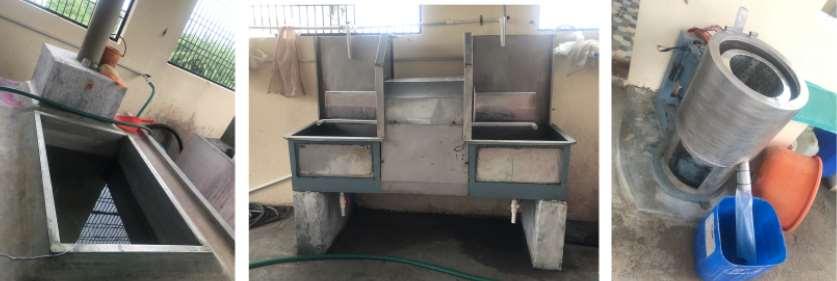
Pigments are added to boiling water and then yarn is twisted and mixed with coloured hot water. Yarn is left for 2-3 hours until all the threads gain proper colour. The coloured yarn is then sun dried in traditional way or can be dried with the help of driers.
iii. WINDING:
The coloured yarn is then sent to winding process after the dyeing process. The threads are separated and then spun to bobbins of different sizes. The winding machines are used to spin threads to bobbins.
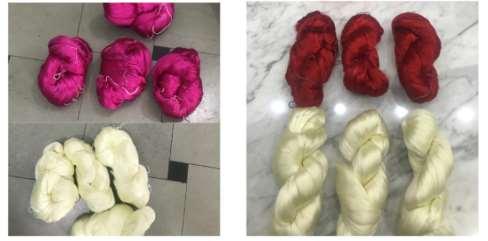

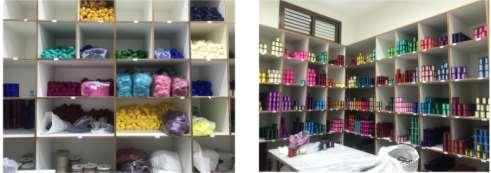
After winding process the threads from bobbin are taken and winded to iron pipe forming thick cylindrical shape. These cylinders are called as warp. Different colours, shades of threads are used to form saree. Warp consists the vertical strands of the saree.
v. WEAVING:
After the spindles are ready, they are fitted into the bobby for the weft yarns and others are hanged on the edge of loom for warp yarns. Due to the motion of the hands, legs and the loom, warps and wefts merge and fabric is composed.
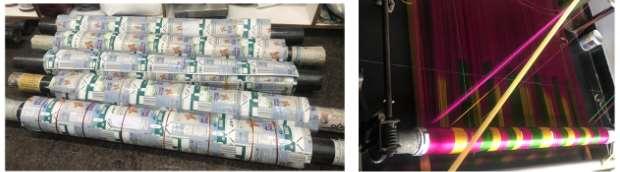
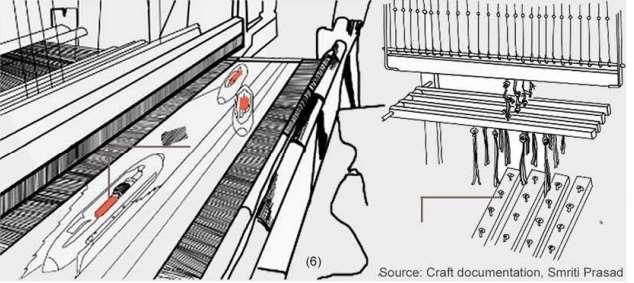
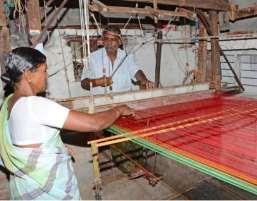
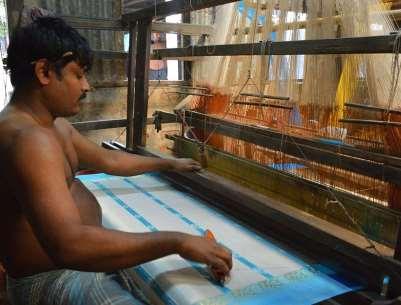
Despite the importance of the industry it is one of the fast-declining industries. The reasons are many and the government is introducing many policies to save the industry. There are several reasons for the downfall of the handloom industry. Few reasons are as follow.
Poor ergonomics and working conditions. Inadequate welfare measures. Limited availability of resources. Unorganised production process. Lack of social security. Low profits. Noise pollution. Unorganised waste disposal. No recognition of talent. No communication between weavers and buyers. Lack of financial support. Presence of middlemen between weavers and market.
Lack of new people in the field. Scattering of the administrative infrastructure.
2.7 POSSIBLE INTERVENTIONS:
Bring in skilled weavers and designers together. Improving financial literacy. Improving professional market chains. Providing opportunity to showcase talent. Attract customers with innovative design. Collaborating learning and business. Improvise weaving techniques. Introducing waste management system. Encourage sustainable materials and reduce pollution.