
30 minute read
CHAPTER 3: CASE STUDIES
CHAPTER 3: CASESTUDIES
3.1 GANGA MAKI STUDIO, UTTARAKHAND:
Advertisement
LOCATION: Bhogpur, 30kms from Deharadun, Uttarakhand.
SITE ANALYSIS:
Climate: Subtropical climate. Up to 40 degrees during summer and below 5 degrees during winters.
Rainfall: 1285mm per annum Accessibility: 6kms away from Dehradun airport. Terrain: Fragile terrain, built on the foothills of the Himalayas. Geographic features: Good range of viewpoints of the mighty Himalayas. Soil type: Brown forest soil.
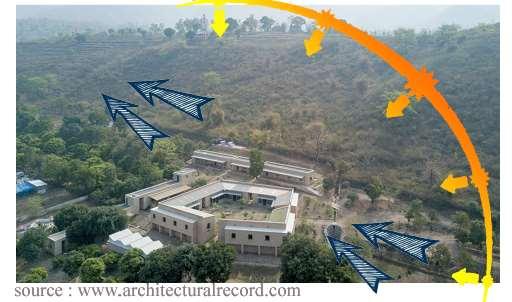
The Ganga maki studio is a collaborative project which is undertaken by the maki studio from japan and commissioned to one of the India’s leading architecture firms’ studio Mumbai. The project is an innovative combination of traditional craft and local materials.
The complex took 4 years to complete. It was designed by the architect Bijon Jain and his team, the time was taken to innovatively and carefully combined different natural materials to produce a finely textured, functioning facility.
Architect: Bijoy Jain Firm: Studio mumbai, Maki studio, Japan Project size: 1300 square meters Completion date: July 2016
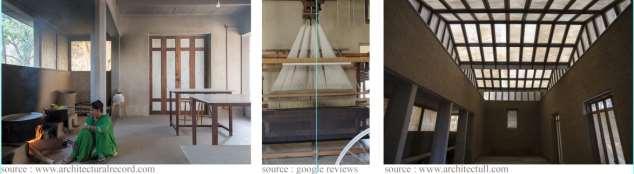
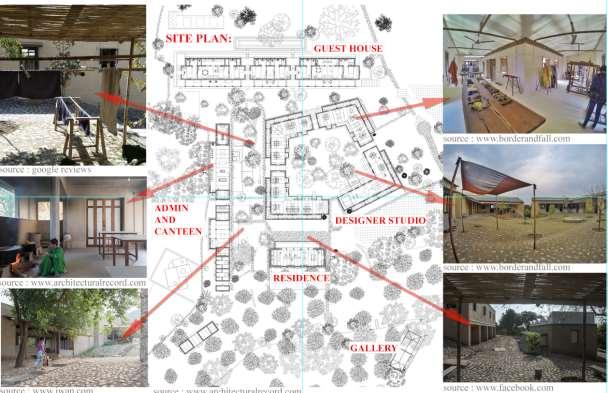

MATERIALS USED:
Locally available materials are innovatively used for the construction. The main spaces are made of bricks, finished with lime, and are covered by asbestos free cement sheet roofs, and paved with stone floors. Adjacent working areas have lime floors and stone slab roofs.
Sumptuously lit, earthy and comfortable, the studios accommodate weavers who sit at their looms in the central mostly men, sky-lit area. Women who knit, stitch and spin yarns cosily use the raised workspaces.

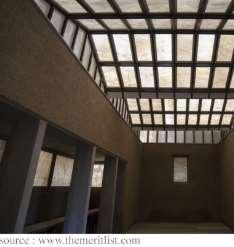
INFERRENCE:
An innovative combination of traditional craft and local materials propels us to rethink how craft is understood.
The design of studio shows how to incorporate both weavers and the designers at a same place by giving importance to both. This project says that virtue is gained not because of impressive array of natural materials, nor because it was handmade. The value is gained because of how the materials are used in keeping with their intrinsic character and the purpose. Famous architect Peter Zumthor said that ‘materials in themselves are not poetic, they can assume a poetic quality only if an architect is able to generate a meaningful situation for them.’ The remarks resonates with the current project. Diffused light is used in the studios. Innovative roof techniques can be seen in the
project.
Courtyard spaces are centred to give inclusive feeling to the people working in the studios. Dyeing unit is placed separately to avoid fumes and heating.
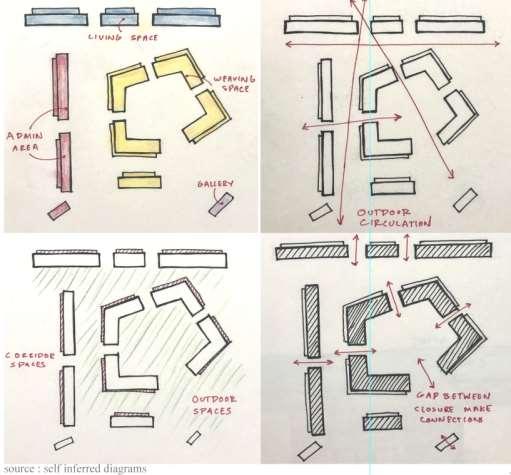
3.2 KHAMIR CRAFTS RESOURCE CENTER, KUTCH:
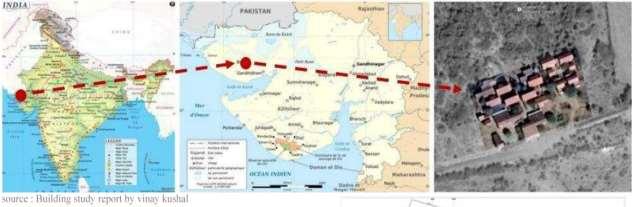
SITE ANALYSIS:
Climate: The average temperature during summer months can rise up-to 31 deg Celsius. In winters the temperature drops and average temperature in the months of winter is about 12 deg Celsius.
Wind: 12-45 kmph Rainfall: 912mm per annum Context: Khamir is located in the outskirts of the city 10 km away from Bhuj. The immediate context is open lands Vegetation: Gentle contours Terrain: Flat land.
Soil type: Sandy loam.

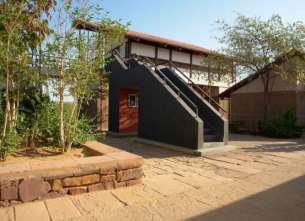
Khamir operates out of a unique campus in Kukma, Kachchh. Which is located 15 kilometres from Bhuj. The district is surrounded by ocean on one side, and the Rann of Kachchh, a vast salt desert, on the other. Once a major trade hub of the Indus Valley delta, Kachchh has long been a melting pot defined by fluid boundaries.
It is a meeting point of people, cultures, faiths, languages, and traditions across a diversity of ecosystems and terrains. The campus is a space for artisans, resource groups and institutions, buyers, suppliers and craft lovers from around the world to gather under one roof to exchange ideas, collaborate and learn.
DESIGN CONCEPT:
Khamir was designed to create 2500 sq m facility for the promotion of craft in Kutch. Concept of planning this center is derived from the local streetscape and village pattern noted before earthquake.
Distance of 13.7 km from Main town creating a calm atmosphere in the building and the villages are around a proximity of 3 km from the building which helps the users for easy access to the building.
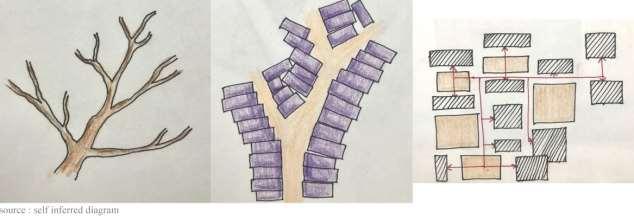
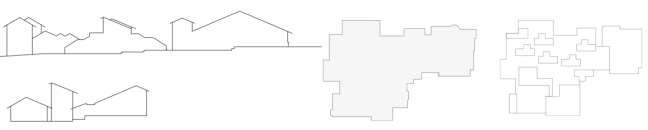
It is a combination of similar style of masses. it together for a unit to whole concept. A geometry is seen in its arrangement in height and proportion. it is the idea of addition and subtraction of a form. Defined area of the building unit to whole. Single complex, all units are joined together. Reinforced by geometry and structure. Each individual unit have a relationship of repetitive to unique.
Interrelation between closed, semi open and open spaces to create natural and fresh environment for people working there. Kattas (outdoor seating) are provided in courtyard. Staggered arrangement of built form.

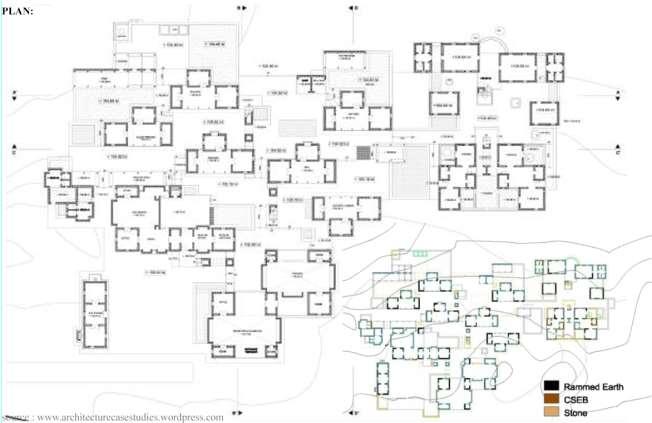
70% of the total area consist of open areas which acts as circulation area, workshop area.
Most of the activities occur in these areas more than the built area.
The void organizes the Surrounding and is necessary to make it workable. Permits circulation among the path admit light and air.
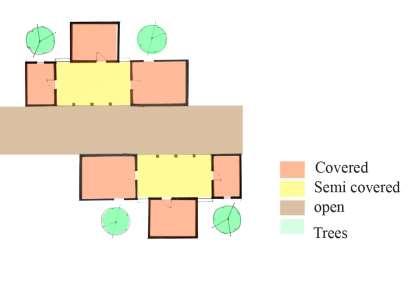
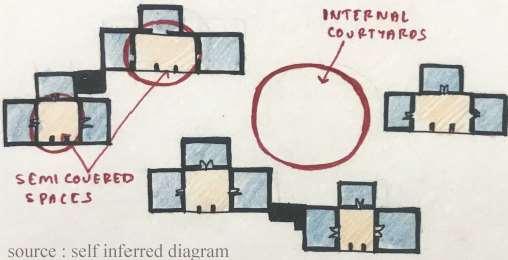
CONSTRUCTION DETAILS:
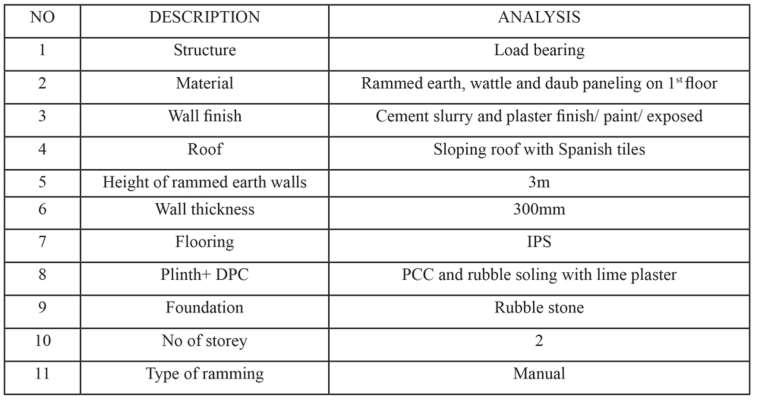
Table-1
It is a combination of columnar and planar structures. Columns and walls form the basic structure. It has a concept of simplicity and pattern in it.
The complex has a combination of mainly three forms. The workshop area, Administration and residential. All the forms are repetitive expect the toilets and part of administration.
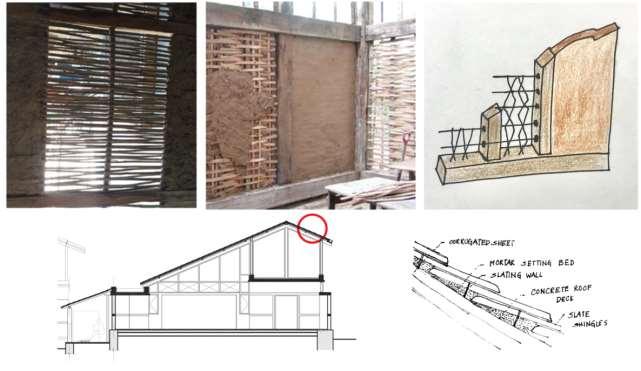
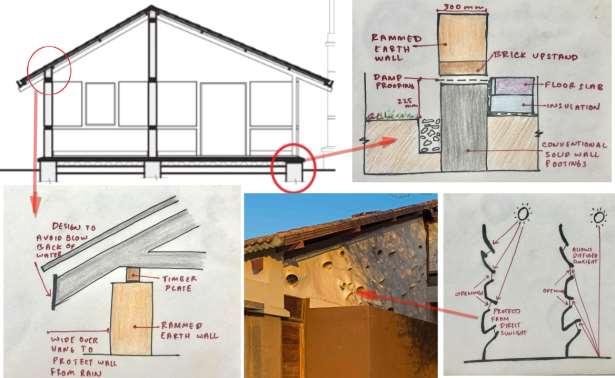
Self-inferred diagrams:
Interrelation between closed, semi open and open spaces to create natural and fresh environment for people working there. Building module are placed in such a way to form narrow pathways and shaded spaces. Courtyards are connected by shaded pathways.

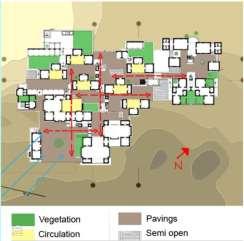
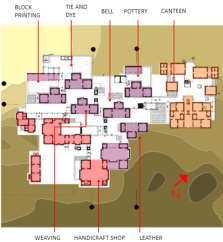
INFERRENCE:
The locally available materials rammed earth, rubble stone, wattle and daub, light weight metal lath plaster and panelling are used effective. Designed in response with the climate, openings are made small in such a way without letting sand and dust enter inside and filter the light coming. The movement through the verandas of the workshop buildings across a series of shaded courtyards recreates the winding patterns of the village, from courtyard to courtyard, from one house to another.
The residential buildings are more humble in comparison with the others. They are carefully positioned in the relatively private and calm diagonal extreme of the campus. Manifestation of the idea of local availability and sustainability. Disaster resilient techniques. Clubbing of courtyards and activities. New techniques like POP sculptures wall. The site selection criteria should be based on the location of the users.
3.3 SHRUJAN, BHUJ:
Location: Bhujodi, Kutch, Gujarat.
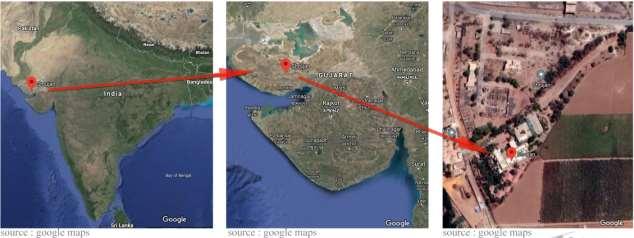
SITE ANALYSIS:
Climate: Hot and dry climate. up to 49 degrees during summer and 19.5 degrees during winters. Wind: 12-45 kmph Rainfall: 912mm per annum Accessibility: State highway adjacent to the site, easily accessible by buses and cabs. Vegetation: Arid desert vegetation, arcades with varied fruits. Terrain: Flat land.
Soil type: Sandy loam.
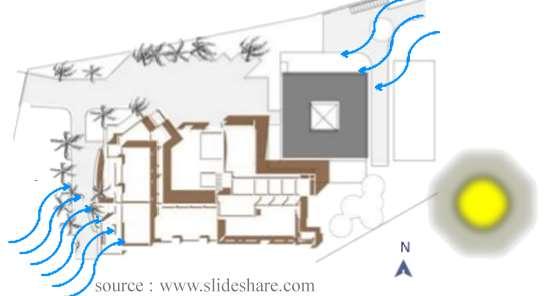
Shrujan is a non-profitable NGO that works for the sustainable livelihoods and craft revival for women in kutch. Shrujan Trust has been committed to income generation and craft revival of craftspeople for 50 years. Every year there are over 4,000 women who work from their home at their own time and their own pace.
Shrujan reaches the raw material, textiles and the threads to their doorstep and settles payments also at their doorstep as soon as the embroidery is done. The “Living and Learning Design Centre” in Bhuj is an ambitious 8 acre campus that houses India’s largest crafts museum. The project aims at being a melting pot of creativity and collaboration for design and craft work in the years to come, not only in India but globally too.
Client: Shrujan Campus- Bhujodi Kutch Location: Bhujodi, Dist Kutch, Gujarat Project type: Public institution of arts and crafts, trading center Architects: indigo architects, Ahmedabad Design Team: Uday Andhare, Mausami Andhare, Arpan Shah, Pragnesh Patel, Mitesh Panchal Consultants: Ami Engineers Ahmedabad Site Area: 8 acres (33000 sqmts) Built up Area: 8558 sq.mts Completion Year: 2004 Civil Engineers: Desai Builders, Bhuj
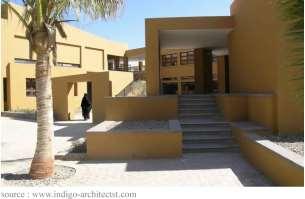
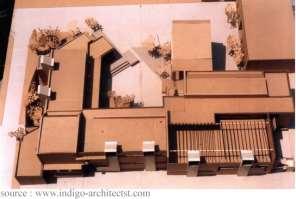
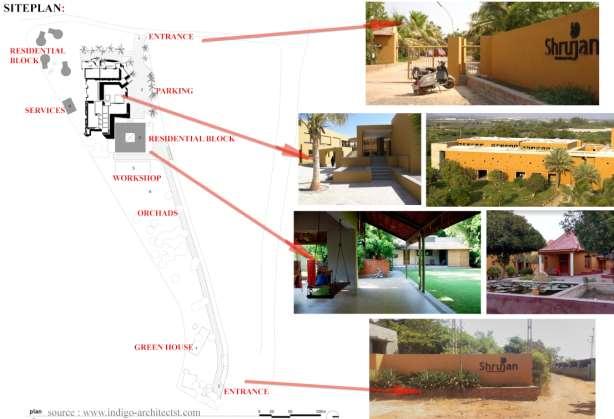
The project incorporates an expressive public face with its main retail store, visitor’s lounge, textile design cell, as well as internal workshop areas, an exhibition gallery, offices, textile conservation cell, residential quarters and auditorium space.
The client brief demanded a sustainable architectural in response taking into account the seismic stability and harsh desert climate. The flagship store for its products was to be incorporated in an attempt to create a new face for Shrujan and provide a marketing platform for its wholesale international clientele.

Workshop areas require daylight open towards the court with large continuous bay windows towards the north. Circulation is both through and around the court. The courtyard also offers a dynamic release of space at the corner on a diagonal axis to the main entrance. The entrance is signified by tiered plinths and a short flight of steps to access the retail store.
A ramped corridor links the entrance to the visitor lounge, the workshops and the café, on the ground level. Space is modulated in its proportions as one moves through the building, providing vignettes of the courtyard and the sky. The resultant architectural form is a layering of contrasting elements.
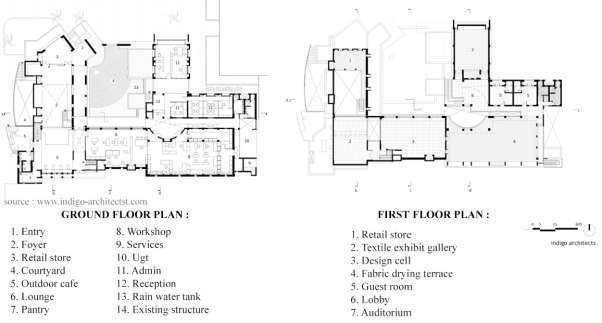

INTERIORS:
The sense of contrast is carried into the choice of materials and textures within building. The entire interior of the shop reflects a contemporary modern design idiom, juxtaposed with display of embroidered garments through a spectrum of colours in silk, cotton, and wool. This idea also highlights the value of these artistic traditions for a modern lifestyle, creatively offset against materials like glass, steel and polished wood. The décor attempts to weave together diverse range of displays from hanging textiles, island units for small patches and borders, using homogeneity of white colour and seamless sequence of spaces.
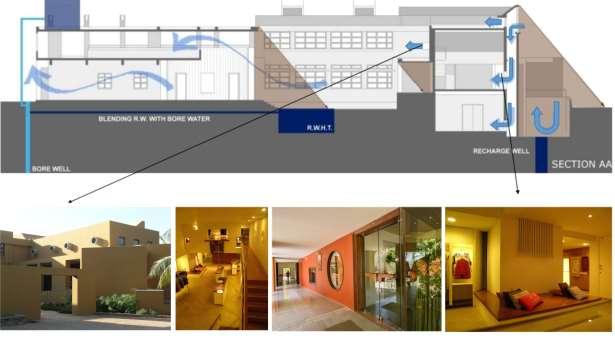
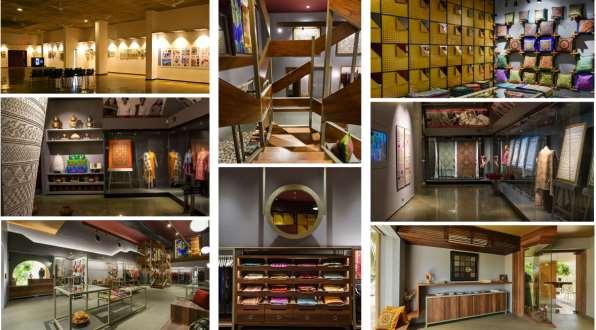
INFERRENCE:
The design of the shop attempts to rekindle the timeless beauty and warmth of our textile traditions and reinstates their usage in a contemporary context. Shrujan is an attempt to weave together holistic concerns of the site, context and the program to define an architecture that heralds a contemporary idiom even as it is inextricably rooted in its local sensibilities. The project says the rationalised decision making for each design element with a balanced analysis leads to a sustainable design in its true valour. The principal idea of wind catchers is learned through the design, in which the building is oriented towards the south and west directions, creates a passive cooling mechanism that works for all the major spaces. The frugality in achieving longevity and stability of the buildings, comfort for its habitants, ideal conditions for the preservation of textiles and the use of passive methods to achieve these goals are easily understood. The buildings present, an open-endedness, their amorphous quality and contemporary visage being both deliberate and desired. The design responds, to the local climate, program, economic realities and the need to create a thermally stable environment for the exhibits.
CHAPTER 4: REQUIREMENTS AND AREA STATEMENTS
4.1 INSTITUTION:
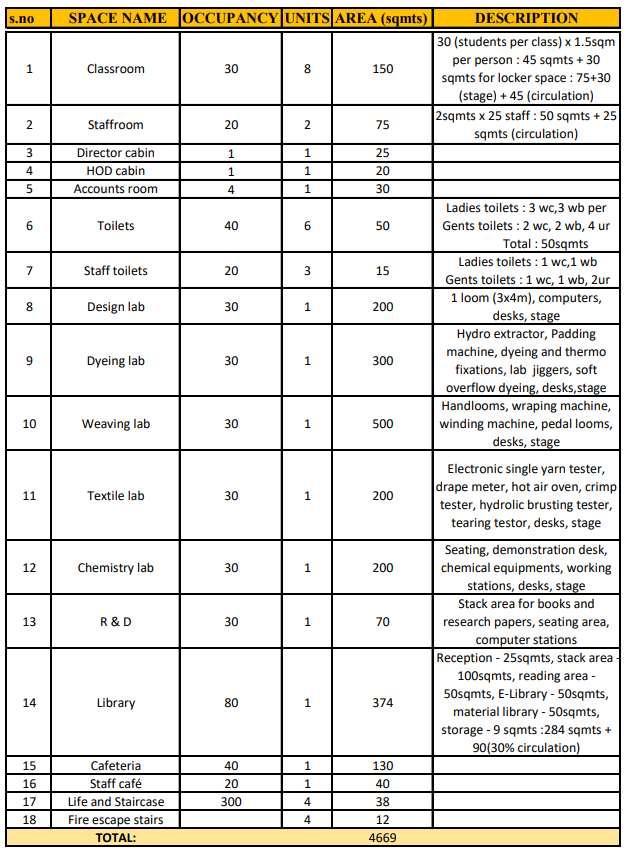
Table-2
No of students per class/year: 30 students x 2 sections: 60 students Total no of students: 60 x 4(years): 240 students
No of teaching staff required: 1staff for every 8 students: 30 teaching staff No of library staff required: 1staff for every 16 students: 15 library staff
4.2 PRODUCTION UNIT:
Total number of handlooms in the town: 450-500(according to local municipality) : considering 500 handlooms. Time taken to weave 1 saree: 3 - 20 days depending on design. Number of sarees produced in a day: 150(Approx) Silk requires for a saree : 450gms(weft) + 350gms (warp) : 800gms Silk required per a day for 150 sarees: 150 x 800: 120000gms: 120kgs

Table-3
4.3 EMPORIUM:
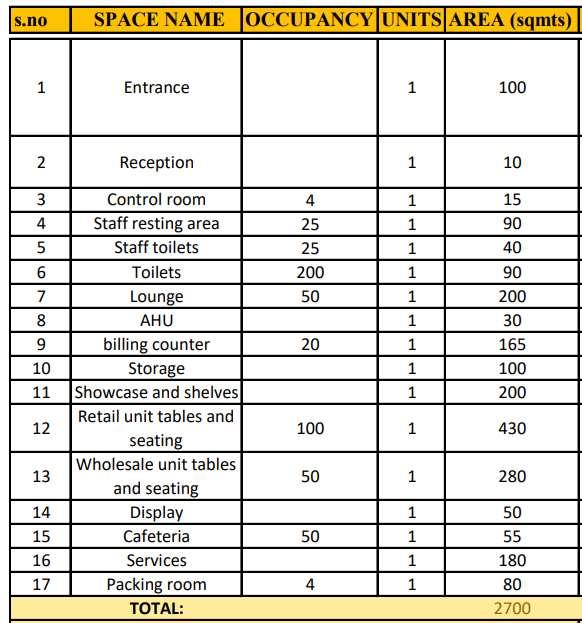
Table-4
4.4 ADMIN OFFICE:
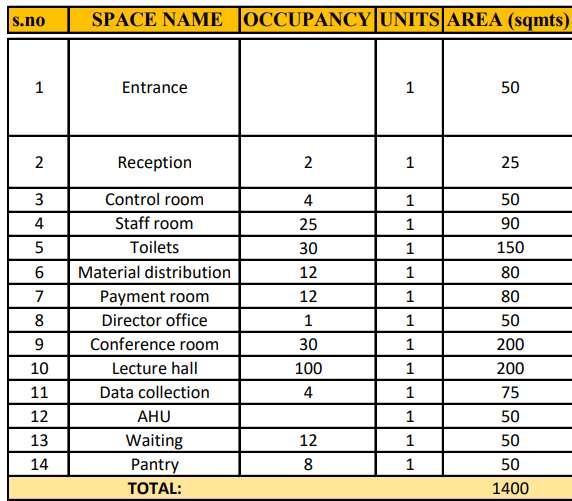
Table-5
4.5 PUBLIC SPACES:
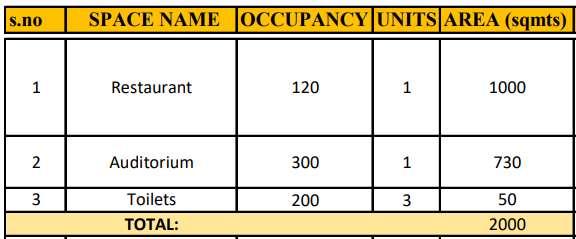
Table-6
4.6 PARKING:
For institutions and industrial buildings 20% of the built-up area is considered for parking. For commercial building 25% of the built-up area is considered for parking. 70% of the parking area is considered for 4 wheelers and 30 % for two wheelers.
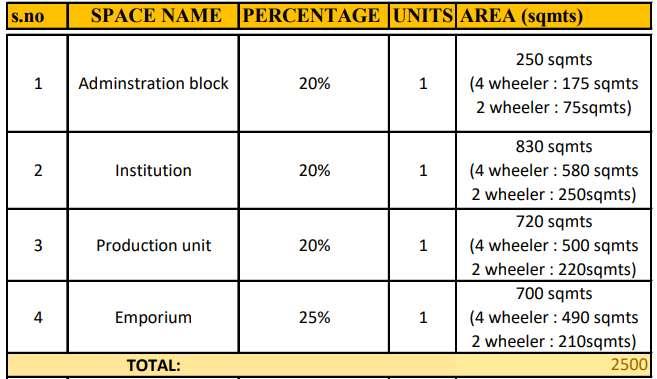
Table-7
4.7 STANDARDS:
SPACE REQUIREMENTS AND SERVICES (CRDA, AP Byelaws-2017- Chapter-iv)
(a) Plinth:
(i) Main Building: The plinth or any part of a building or outhouse shall be so located with respect to highest road level from site so that adequate drainage of the site is assured. The height of the plinth shall be not less than 450mm from surrounding ground level.
(ii) Interior Courtyards, Covered Parking Spaces and Garages: Every interior court yard shall be raised at least 150mm above the determining ground level and shall be satisfactorily drained either by gravity or by mechanical means.
(b) Boundary wall height:
(i) In Industrial buildings of workshops and factories, electric sub-stations, transformer stations, institutional buildings like sanitaria, hospitals and educational buildings like schools, colleges, including hostels, and other public utility undertakings and strategically sensitive buildings a height up to 2.4m may be permitted. (ii)Side walls and back wall: 2.4m from ground level to be solid (stone/brick/masonry etc.).
(c) Capacity of Exits:
The capacity of exits (staircase, ramps and doorways) indicating the number of which persons could be safely evacuated through a unit exit width of 50cm shall be as given in the Table below.

(d) Doorways:
Table-8
(i)Every doorway shall open into an enclosed stairway, a horizontal exit, on a corridor or passageway providing continuous and protected means of degress. (ii) Doorways for bathrooms, water closet, stores etc. shall be not less than 0.75m wide. (iii)Doorways shall not be less than 200cm in case of assembly buildings. (iv)Doorways shall be not less than 2m in height. (v)Exit doorways shall open outwards, that is away from the room but shall not obstruct the travel along any exit. No door when opened shall reduce the required width of stairway or landing to less than 0.9m. Overhead or sliding door shall not be installed. (vi)Exit door shall not open immediately upon a flight of stairs. A landing equal to at least, the width of the door shall be provided in the stairway at each doorway. Level of landings shall be the same as that of the floor, which it serves.
(vii)Exit doorways shall be openable from the side, which they serve without the use of a key. (viii)Revolving doors shall not be provided as a means of fire exit. (ix)Mirrors shall not be placed in exit ways or exit doors to avoid confusion regarding the direction of exit.
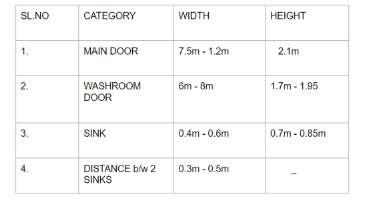
Table-9
(e)Canopy:
Canopy to be provided within the building envelope or in setback subject to setback conditions but inside plot line, however over the entrance in the front setback should not be more than 3m and inside setbacks may be up to the plot boundary or maximum 3m, whichever is less. Canopy can be at the structural floor level.
(f)Staircase Requirements:
(i) For buildings such as assembly, business, education, hazardous, industrial, institutional, Mercantile Building, High Rise Building, Multilevel Car Parking Building, Office Building (premises), Special Building, Storage Buildings and Wholesale Establishment, there shall be minimum of two staircases and one of them may be enclosed stairway and the other shall be on the external walls of building and shall open directly to the exterior, interior open space or to any open place of safety.
(ii) Single staircase may be considered for Non-high-rise residential, educational, business or group housing society where floor area does not exceed 500 sq. m. and height of the building does not exceed 18m (including Stilt Floor) and other requirements of occupant load travel distance and width of staircase shall meet the requirement.
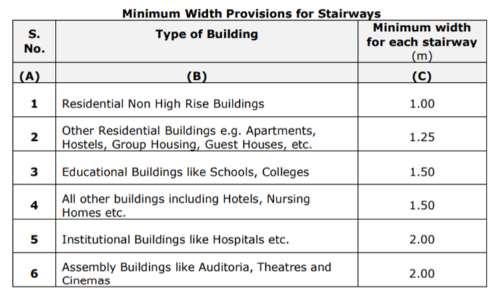
Table-10
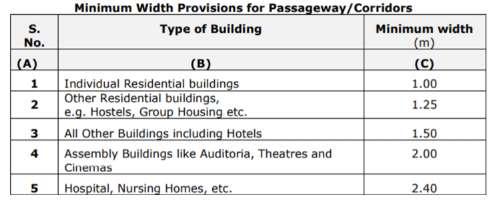
Table-11
(g) Provision of Lifts:
(i) It shall be made mandatorily for all buildings which are 15m and above (without stilts) /18m and above (with stilts) in height. (ii) For buildings less than 15m (without stilts)/18m (with stilts) the provision of lift is on the discretion of the owners in order to facilitate movement of elderly people. (iii) All the floors including basement and terrace shall be accessible for 24hours by the lifts. (iv) The lifts provided in the buildings shall not be considered as a means of escape in case of
emergency. (v) The lift machine room shall be separate and no other machinery shall be installed in it. (vi) Grounding switch at ground floor level to enable the fire service to ground the lift car in case of emergency shall also be provided.

Table-12
(h) Exterior open spaces:
(i) For all buildings, the open spaces/setbacks, covered area, FAR if any shall be as per Master Plan/Zonal Plan requirements and as per these Rules. (ii) Every room that is intended for human habitation shall abut on an interior or exterior open space or on to a verandah open to such interior or exterior open space. (iii) In case of High-rise buildings, the exterior open spaces around a building shall be of green or hard surface capable to taking the load of fire engine weighing up to 45tonnes.
(i) Height Limit:
(i) If a building abuts on two or more streets of different width, the building shall be deemed to face upon the street that has the greater width and the height of the building shall be regulated by width of that street. Height shall however, not exceed the maximum height as provided in the Master Plan/Zoning Development Plan/Zoning Regulations/these Rules.
(ii) Height Exemptions: The following appurtenant structures shall not be included in the height of building covered under Building Rules. (1) Roof tanks and their supports not exceeding 1.5m in height. (2) Ventilating, air conditioning and lift rooms and similar service equipment. (3 ) Stair covered with Mumty not exceeding 3.00m in height. (4) Chimneys and parapet wall not exceeding 1.50m.
(j)Interior Open Space for Light and Ventilation:
(i) The whole or part of one side of one or more rooms intended for human habitation and not abutting on either the front, rear or side open spaces shall abut on an interior open space or an internal courtyard or chowk, whose minimum dimensions shall not be less than 9sq.m with no side shall be less than 2m for buildings up to 15m in height (excluding Stilt Floor). (ii) For buildings with above 15m in height, the minimum dimensions of the internal courtyard shall be with an area of not less than 25sq. m and no side shall be less than 3m in width. (iii) All such court yards / ducts may be allowed above stilt floor. (iv) Sunken Courtyard: Sunken courtyard up to 3m in depth from the ground level as ‘light well’ within building envelop shall be permitted for light and ventilation for basement area.
(k) Toilets:

Table-13
(i) Every bathroom or water closet shall be so situated that at least one of its walls shall open to external air.
(ii) unless mechanically ventilated, it shall have a minimum opening in the form of window or ventilation opening to a shaft or open space, of area not less than 0.3sq.m with side not less than 0.3m.
(iii) toilets / W.C. / Urinals are permitted within the building envelop in stilts area and basement or at ground level with subject to appropriate natural / artificial ventilation, drainage and sanitation provided the maximum size doesn’t exceed 3sq.m.
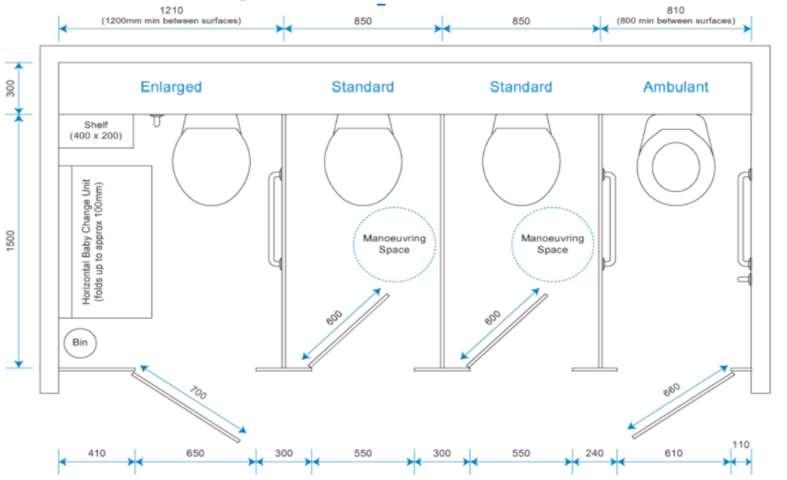
(l)Parking:
(1) The parking spaces should be efficiently designed and clearly marked and provided with adequate access, aisle, drives and ramps required for manoeuvring of vehicles. (2) The parking spaces may be provided in i. Basements or cellars (one or more) / multi-level (allowed for plots 750sq.m and above only) or ii. Stilt floor or in upper floors (at any level) or iii. The Open space over and above the setbacks i.e. after leaving the setbacks to be left around the building with adequate vehicular access, aisle, drives, and ramps required for manoeuvring of vehicles.
v. Any of the above or all the above or combination of the above. vi. Wherever Mechanical system and car lifts are proposed enabling two tier parking, the required parking is computed accordingly. (3) In the Stilt floor a watchman room and 2 toilets (W.C), with maximum built up area of 25sq.m may be allowed. Such space shall not be disposed and shall be part of common facility of the complex. For the sites above 750sq.m area such use is permitted subject to fulfilment of parking requirement as per the above Table (Parking Area to be provided in all Buildings). (4) For parking spaces in basements and upper floors, at least two ramps of minimum 3.6m width or one ramp of minimum 5.4m width and adequate slope 1 in 8 shall be provided. Such ramps shall not be allowed in mandatory setbacks including building line, however they may be permitted in the side and rear setbacks after leaving minimum 7m of setback for movement of firefighting vehicles. (5) The minimum width of the drive way shall be 4.5m. (6) Visitors’ parking shall be provided with minimum 10% of the parking area mentioned in the below Table (Parking Area to be provided in all Buildings) and may be accommodated in the mandatory setbacks other than front setback where ever such setbacks are more than 6m (excluding green strip). However this is not permissible in case of transfer of setback. The Visitors’ Parking facility shall be open to all visitors which shall be properly demarcated on ground. (7) Misuse of the area specified for parking of vehicles for any other use shall be summarily demolished / removed by the Enforcement authority.
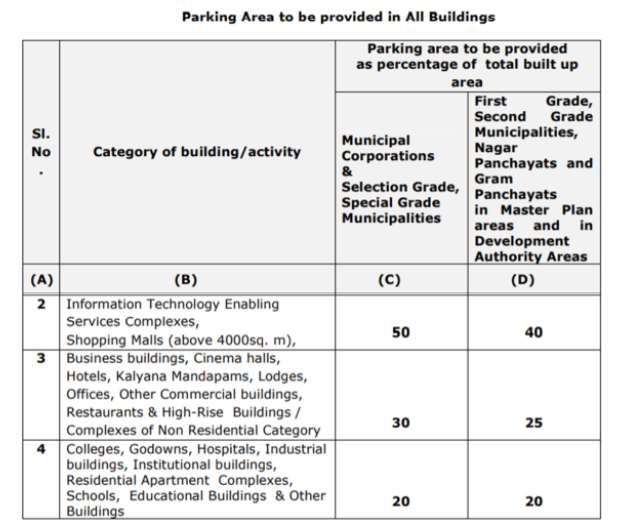
Table- 14
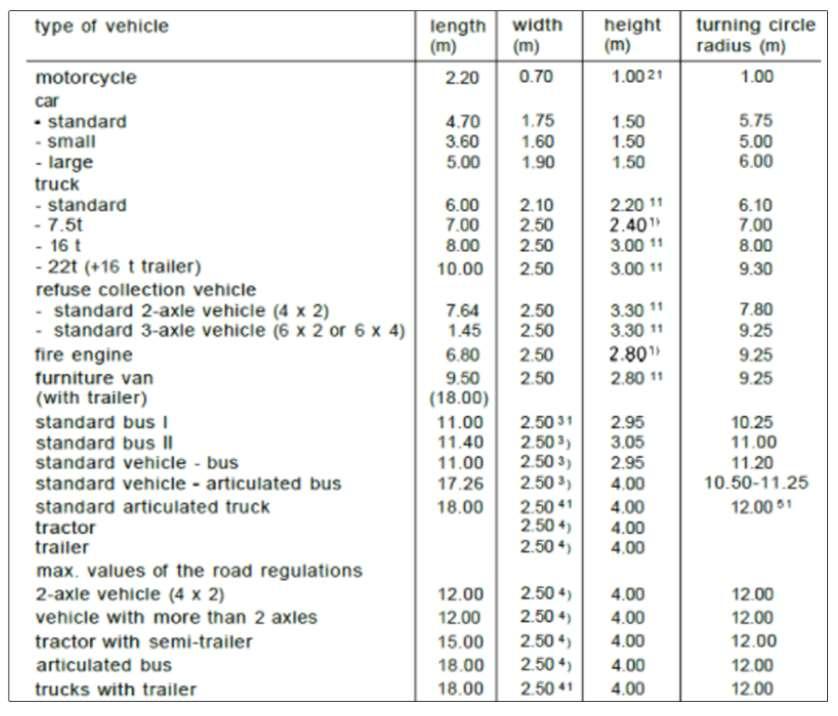
Table-15
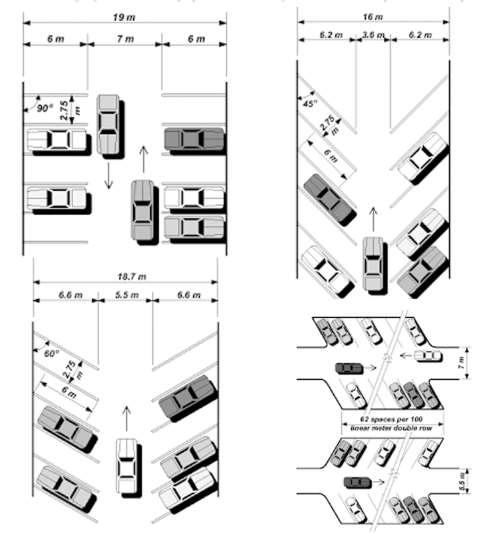
(m)Fire Protection Requirements:
Buildings shall be planned, designed and constructed to ensure fire safety and this sha1l be done in accordance with Part IV-Fire Protection of National Building Code of India, unless otherwise specified in these Rules. In the case of Assembly Buildings, Business Buildings, Educational Buildings, Hazardous Buildings, Industrial Buildings, Institutional Buildings, Mercantile Buildings, Mixed Land use Buildings, Storage Buildings and Wholesale Establishments the building schemes shall also be cleared by the APSDR&FSD. First Aid/Fixed Fire Fighting/Fire Detection Systems and other Facilities: Provision of fire safety arrangement for different occupancy from S. No. (a) to (w) as indicated below shall be as per Part IV-Fire Protection of NBC and as recommended by the APSDR&FSD.
(a) Access (b) Wet Riser (c) Down Comer (d) Hose Reel (e) Automatic Sprinkler System (f) Yard Hydrant (g) UG Tank with Draw off Connection (h) Terrace Tanks (i) Fire Pump (j) Terrace Pump (k) First Aid Fire Fighting Appliances (l) Auto Detection System (m) Manual operated Electrical Fire Alarm System (n) P.A System with talk back facility (o) Emergency Light (p) Auto D.G. Set (q) Illuminated Exit Sign (r) Means of Escape (s) Compartmentation (t) MCB /ELCB (u) Fire Man Switch in Lift (v) Hose Boxes with Delivery Hoses and Branch (w) Pipes Refuge Area
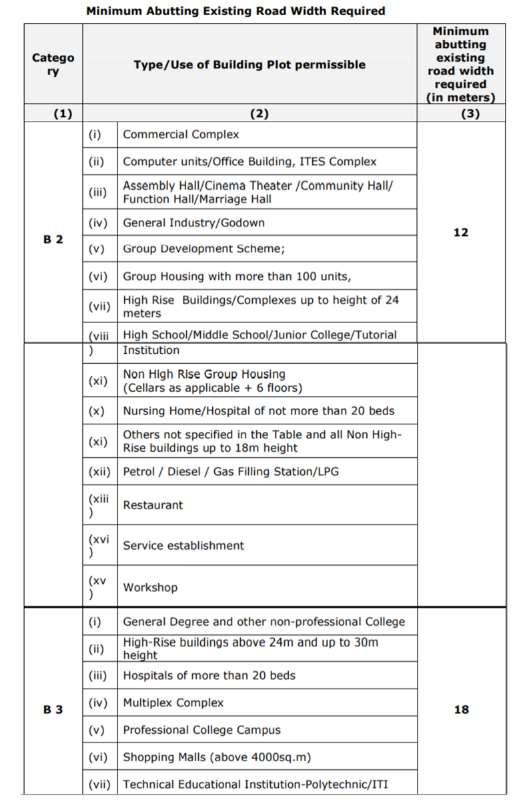
Table-16
(n)Permissible Setbacks & Height for All Types of Non-High Rise Buildings:
(1) The height of buildings permissible in a given site/plot shall be subject to Restrictions in the areas notified as (a) Sites in Old /Existing Built up areas/Congested areas/Settlement/Gram khatam and (b) Areas Prohibited for High Rise Buildings given in the Annexures.
(2) The minimum setbacks and permissible height as per Table and other conditions stipulated below shall be followed.
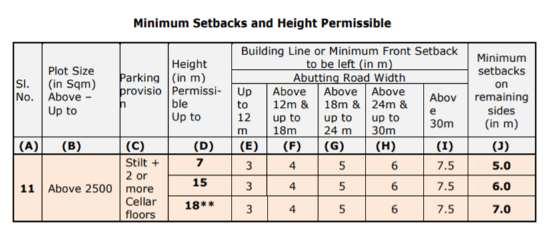
Table-17

Table-18
CHAPTER 5: SITE SELECTION AND ANALYSIS
5.1 LOCATION:
Location: Hindupur, Andhra Pradesh
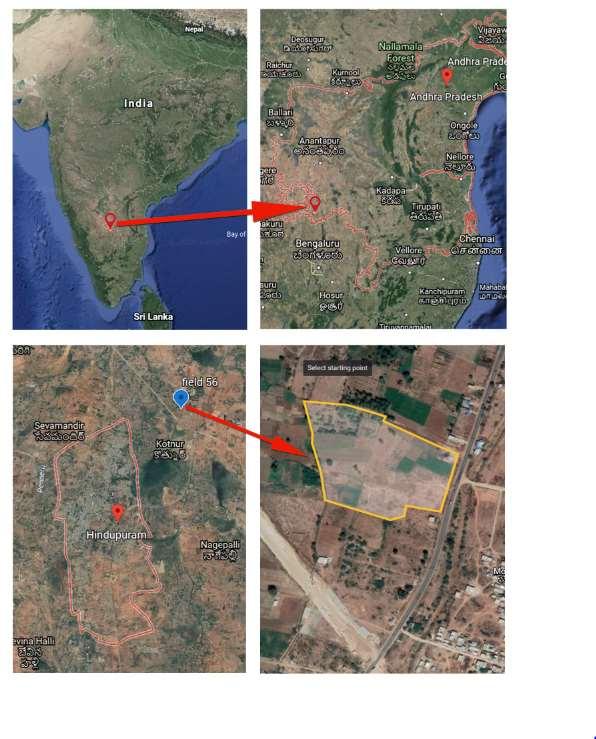
5.2 OWNERSHIP:
The site is owned by members of “Chenethi sangam” the local handloom society.
5.3 FEASIBILITY:
The site for the current thesis project is selected in Hindupuram, Andhra Pradesh. The reason why the site has been chosen in Hindupuram is it is easily accessible by the handloom weavers who resides in the Village mudireddipalli and attracts customers who visits the town to purchase silk products.
The site is located 5kms away from the main town and 3kms away from the weaver’s village.
5.4 CONNECTIVITY:
The site is well connected to the town and the village through main road and streets. New highway project has been taken up which is currently under construction. The site contains highway towards south and main road towards west.
Hindupuram contains transportation system on roads and railways. Which is well connected to Karnataka, Tamil nadu states and 100kms away from Bangalore city.

Anantapur district has 9,306 kins of road and 589 kms of railway line. The district is linked with Chennai, Delhi, Bombay, Bangalore and Hyderabad by the railways. Guntakal is one of the biggest railway junctions in the country. A.P.S.R.T.C. Provides commuting facilities in the district. There are good number of Lorries in the district supporting the movement of goods. Anantapur district has also got an Airport at Puttaparthi.
5.5 SITE ANALYSIS:
Geography:
Hindupuram is located in the Anantapuram district. It is situated in the western part of Deccan plateau and forms the southernmost part of Rayalaseema region of Andhra Pradesh. The geographical area of the district is 19134- sq.kms.
The district is bounded on the East by Cuddapah and north Kurnool districts. Its southern and western boundary flanks the State of Karnataka. Anantapur is the biggest of the districts of Andhra Pradesh accounting for 6.9 per cent of total geographical area of the State.
Geographic location:
Between 13° 40' and 15° 15' Northern latitude and 76° 50’ and 78° 30' of Eastern longitude.
Soil condition:
The site contains red soil. The soils in the town are shallow, poor in nutrients with high water absorption capacity but poor in retention of moisture. 30 per cent of lands are saline and alkaline, especially river banks.
Rainfall:
Anantapur district is the driest part of the country with the second lowest average rainfall 544 mm, after Jaisalmar district in Rajasthan state. The rainfall is highly erratic, both temporally and spatially. During the past 33 years, the district was subjected to drought conditions in as many as17 years.
The Anantapur district is declared to be one of the six districts in India affected by severe drought frequently. In 1981 the annual rainfall in the district was 544 mm as against 896 mm in Andhra Pradesh.
Vegetation:
The site contains unwanted plants like Parthenium, sewan grass, and dried plants. There are no existing trees inside the site. Few area has mulbury plantation which is now left unmaintained.
Existing features:
The site is empty and does not contain any prominant features like trees and obstracles.
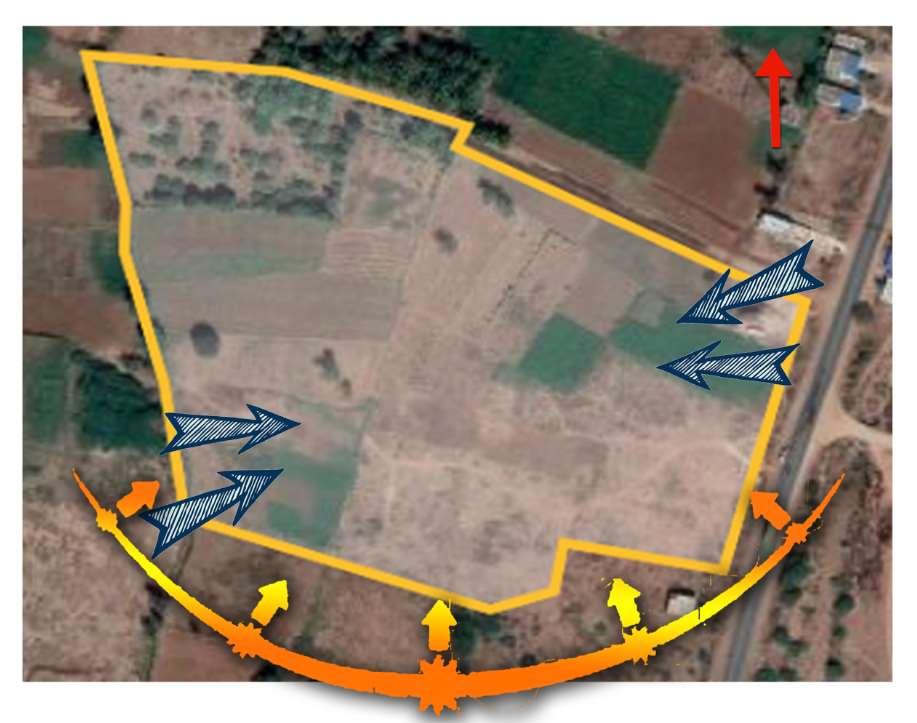
Topography:
Flat land.
Power supply:
The domestic and industrial power requirements of the district are drawn from Thungabhadra Hydel Project at Hospet. Integrated Power Grid is established at Gooty connecting Nagarjunasagar, Kothagudem and Thungabhadra.The district is provided with 73 electrical substations with 24,626 kms in total line length. All the revenue villages in the district have been electrified.
Irrigation:
Irrigation is the sine-quo-non for agricultural prosperity. The taluk has only one project, namely, the Penneru, Kumudvathi Project, connecting the two rivers, Penneru and Jayamangali, by an anlcut for supplying water to eight tanks through two channels. It is situated about 4 kms away to the south-west of Hindupur town. There is another popular stream known as Chitravathi. These rivers are torrential streams and carry water only when there are good rains. They are dry for the most part of the year. The Hindupur big tank (Pedda Cheruvu) is one of the largest in the district has an aspect of 1,992 acres.
Climate:
Hindupur has tropical climate, winters lastfrom november to february, while summer last from march to june. Rainfall is received during the months of july to august. In Hindupur, the wet season is oppressive and overcast, the dry season is partly cloudy, and it is hot year round. Over the course of the year, the temperature varies from 62f to 99f and rarely below 57f or above 104f.
5.6 SITE DRAWINGS:
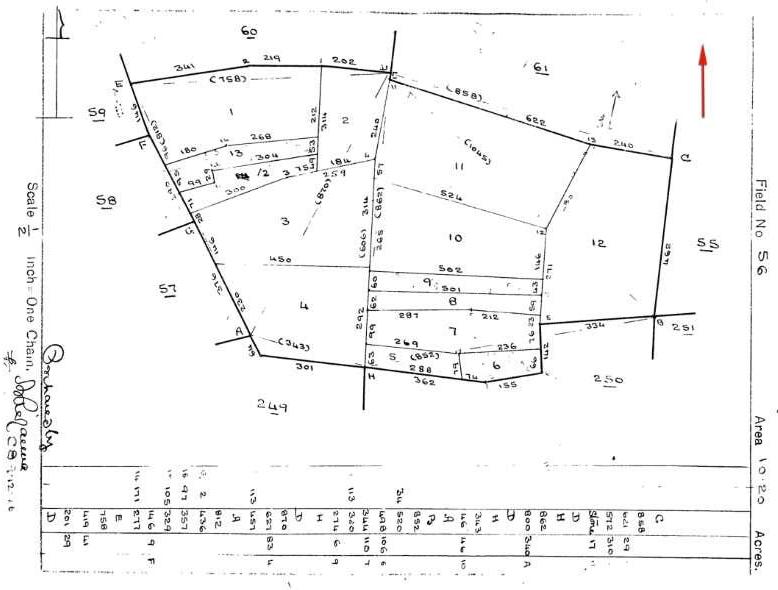
5.7 SITE PICTURES:
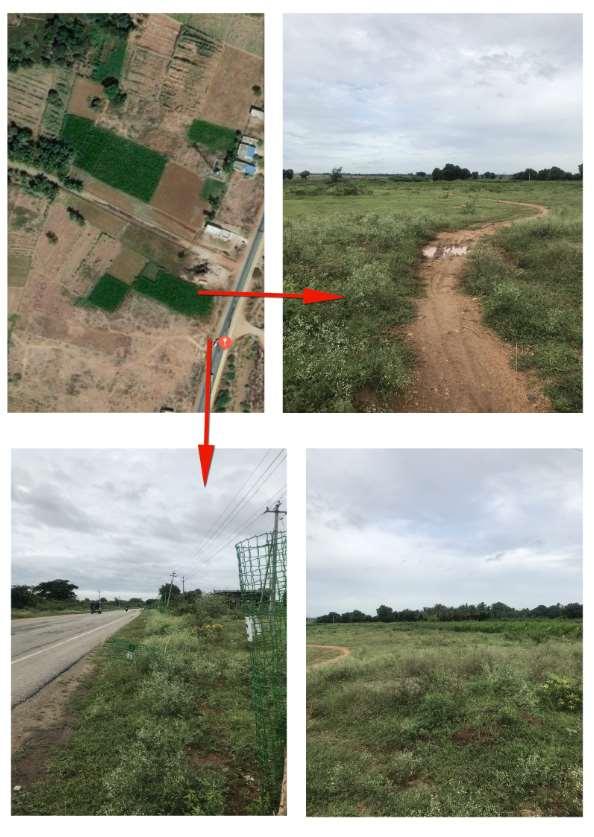
CHAPTER 6: DESIGN
6.1 CONCEPT:
“Architecture can’t force people to connect; it can only plan the crossing points, remove barriers, and make the meeting places useful and attractive.” said Denise Brown.
Although it cannot control the outcome, architecture holds the potential to set the stage for chance encounters and social interactions, thus nurturing community building and influencing the fabric of our social culture. The task of designing our built environment will be as much about designing the interactive experiences that happen in that space.
The handloom centre explores how architecture can improve the social capital of its surroundings through design strategies and thoughtful programming, creating the fertile ground for social interaction among students, workers and designers.
The above figure shows multiple interaction spaces where different groups of people gets to interact with each other. It is necessary for a group to interact amongst themselves, as well as interact with other groups to gain knowledge and exposure.
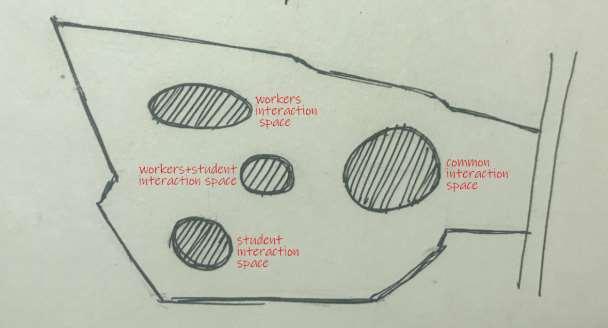

CIRCULATION:
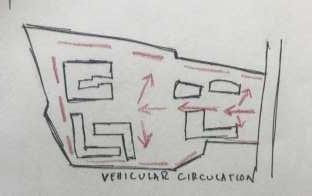

NORTH LIGHT: SUN BREAKERS:
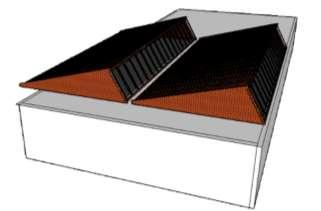
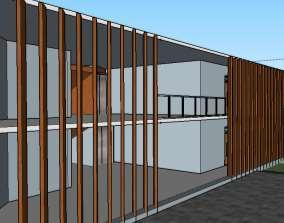
6.2 SITE ZONNING:
PRIMARY ZONING:
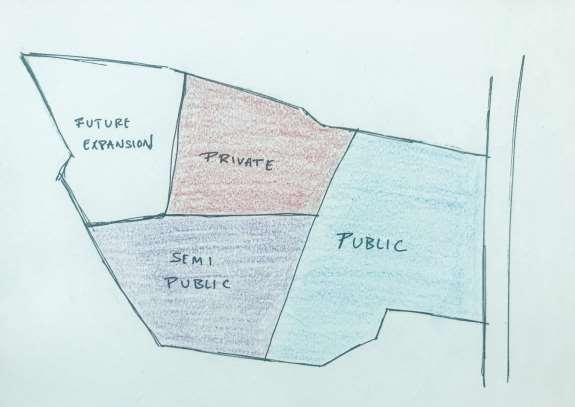
SECONDARY ZONING:

6.3 INSTITUTION:
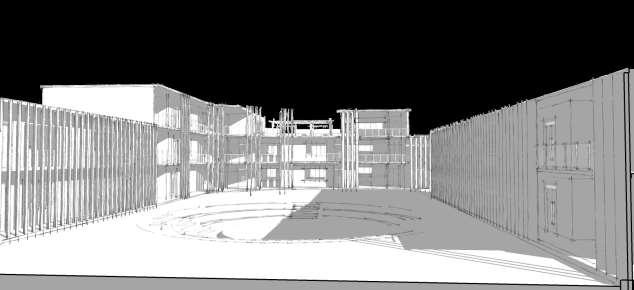

The open air theatre at the centre acts as an interaction space which allows students to interact with each other building bond between them. The wind breakers obstruct strong dusty winds and allows cool breeze into the corridors.
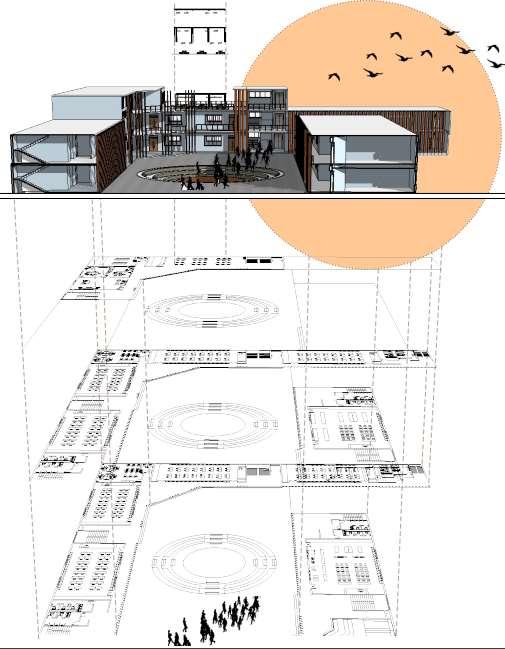
To bring in the feel of security and togetherness the number of entries and exits are minimized at the same time the circulation between outer spaces to inside spaces is also kept in mind providing openings wherever required.
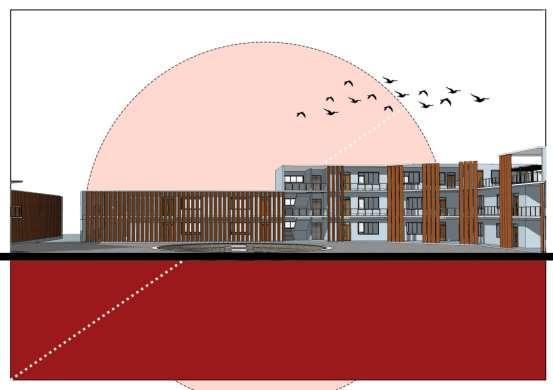
6.4 PRODUCTION UNIT:

The production house is the area that requires more light for the people to work. Sun is the natural source of light that saves energy and gives maximum amount of sunlight. In Andhra Pradesh the sunlight which is received is harsh which creates discomfort when hits the eye and skin.
The solution to this problem is north lighting. The north light truss prevents direct sunlight from entering the building. When the opening is made in the north with certain angle the maximum amount of required sunlight is entered through the opening and also harshness is reduced. North lighting truss helps to bring in diffused sunlight inside the building.
The interaction space in center gives opportunity for the workers to improve coordination and helps to relax before going back to work.
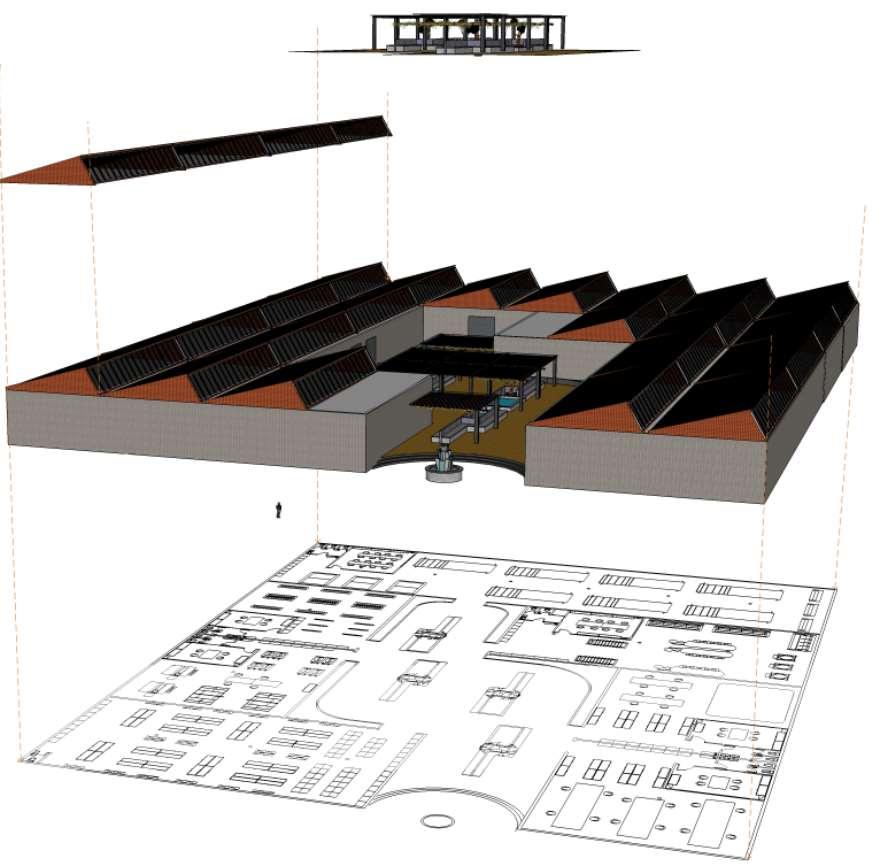
6.5 EMPORIUM:
The emporium resembles strength and rigidity through the form. Best products are displayed through the glass showcases which is one of the elements of the façade. The connectivity to institution and other blocks is shown through the vertical louvers.
The materials plays a prominent role in architecture design. The contemporary style is maintained throughout the design without losing traditional feel through choice of materials.


6.6 ADMIN BLOCK:


6.6 PUBLIC SPACES:

CHAPTER 7: CONCLUSION
7.1 CONCLUSION:
The design aim of the project was to integrate the different activities of the handloom industry in a single space for the betterment of the industry. The aim of this project was to formulate an architectural solution for the fast declining handloom industry in the town of Hindupuram, Andhra Pradesh.
After studying the problems faced by the weavers and the short comes of the industry, it is realized that the fragmentation of the industry is one of the main reasons that can be solved through the architectural influences.
The campus designed provides the scope for the research studies in the field and implementing it. In the case of satisfactory report, the upgradation can be implemented throughout the weaving industry. The campus also provides the opportunities for the designers to stay in campus and collaborate with weavers and design students.
The campus can be used for the guest lectures and seminars to the workers and the students which improves the communication between the students and workers breaking the barrier. Hence through this campus, the working of the handloom industry can be altered to suit the best interest of its actual stake holders, which is the weavers.
7.2 REFERENCES:
https://issuu.com/nehanowshath/docs/n.neha_-thesis_report https://www.academia.edu/28742538/Design_Education_and_Handloom_Weaving_in_Ind ia
https://www.financialexpress.com/lifestyle/thread-of-hope-weaver-community-in-indiacontinues-to-languish-in-obscurity/1156993/ https://www.tata.com/newsroom/community/empowering-weaving-communities-tata http://silkwormmori.blogspot.com/2011/05/indian-sericulture-industry-over-view.html https://inserco.org/en/india https://www.researchgate.net/publication/328677248_takshila_magazine_vol_122011 https://texmin.dashboard.nic.in/DashboardF.aspx https://counterview.org/2018/02/09/handloom-in-union-budget-lack-of-concern-for-thelabour-intensive-and-indigenous-sector/ https://textilelearner.blogspot.com/2017/04/handloom-industry-india.html https://www.unnatisilks.com/problemsofchiralaweavers.aspx www.nzdl.org https://frontline.thehindu.com/social-issues/article30225048.ece https://web.archive.org/web/20141203230916/http://cdma.ap.gov.in/Hindupur/Basic_infor mation_Municipality.html https://www.borderandfall.com/maheshwar-handloom-school https://www.metalocus.es/en/news/silk-weaving-facility-david-adjaye# https://www.borderandfall.com/karigar/progressive-weaving-facilities-part-2/ https://www.dezeen.com/2013/06/13/david-adjaye-reveals-design-for-a-silk-weavingfacility-in-india/ https://www.emaze.com/@AOROTCRLL https://thinkmatter.in/2019/05/15/khamir/ https://architecturecasestudies.wordpress.com/2020/04/15/khamir-craft-resource-centrebhuj/

74
75