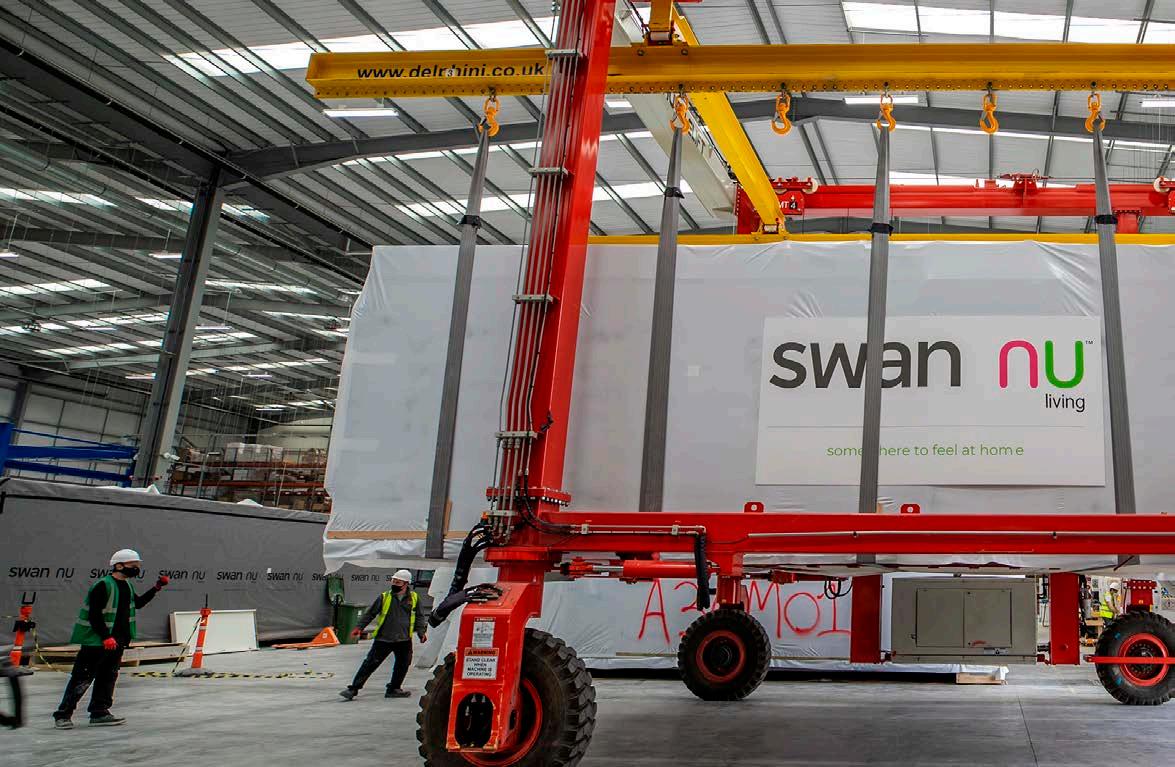
3 minute read
Our approach to Modular
Late in 2017, our first modular homes were delivered to the £130m regeneration at our Beechwood development in Essex, after being precision manufactured in our factory in Basildon, Essex. Our custom build modular homes at Beechwood continue to be in high demand. You can watch the latest video here: https://www.youtube. com/watch?v=d1rCoQRzvQ0
We opted to use MMC at Beechwood after exceptionally bad weather and subcontractor insolvency had contributed to delays in earlier phases of the project. Combined with the well documented macro-economic issues such as skills shortages and low productivity in the construction sector, these factors led us to decide to invest £3m in setting up our first factory.
Advertisement
Having taken the keys to the factory in January 2017, our first precision engineered modules were fitted out (including kitchens, bathrooms and even wine fridges) in October and then delivered to Beechwood. We’re also now onsite in Tower Hamlets. We're so committed to using offsite construction as a key part of our development programme going forward that in October 2020 we acquired a second modular housing factory, securing a newly built 116,841 sq. ft. industrial unit which will open later in 2021. Factory 2 is situated opposite our existing modular housing factory in Basildon. This new factory will be used to manufacture steel modular housing and will operate alongside Swan’s existing Cross Laminated Timber volumetric system delivered in Factory 1.
This expanded capacity will not only allow Swan to build high quality modular homes for its own secured development pipeline but also will position NU living, in time, to provide additional capacity to support Swan's partners and other stakeholders in meeting the growing expectation from the government for a proportion of modular housing to be incorporated in their own programmes. Swan’s modular factory is able to save 50% on time during the modular construction process, also saving 10% on cost and 90% reduction in waste, along with increased quality and safety. Taking a modular approach will help us "Love the Planet" and ensure we are able to respond to future home standards and sustainability and zero carbon targets. With both factories in full operation, NU living will eventually be capable of delivering over 1,000 modular homes each year.
The acquisition of the second factory was also a key strategic move as it will give us additional capacity to build at height using a steel framed approach and to increase the use of pre-manufacturing methods, including componentisation. We are committed to supporting the communities in which they operate and opening the factory will create over 120 jobs by the time it is in full operation. In addition, Swan will be providing apprenticeships in the Basildon factories in order to allow more young people to flourish and learn modern methods of construction. All these benefits helped us secure £4.5m of Getting Building Funding from South Essex Local Enterprise Partnership to fund the fit out of Factory 2.
Nadim Zahawi, then Parliamentary Under Secretary of State (Minister for Business and Industry) and now Education Minister, said on a visit to the factory in 2020:
Modular construction is helping provide more affordable homes in the UK and it was fascinating to learn more about this type of engineering at the Swan Housing Association factory.
We are backing this type of development through our Construction Sector Deal and I am pleased to see how it is being used to help build new communities.”
Factory 1
Factory 2
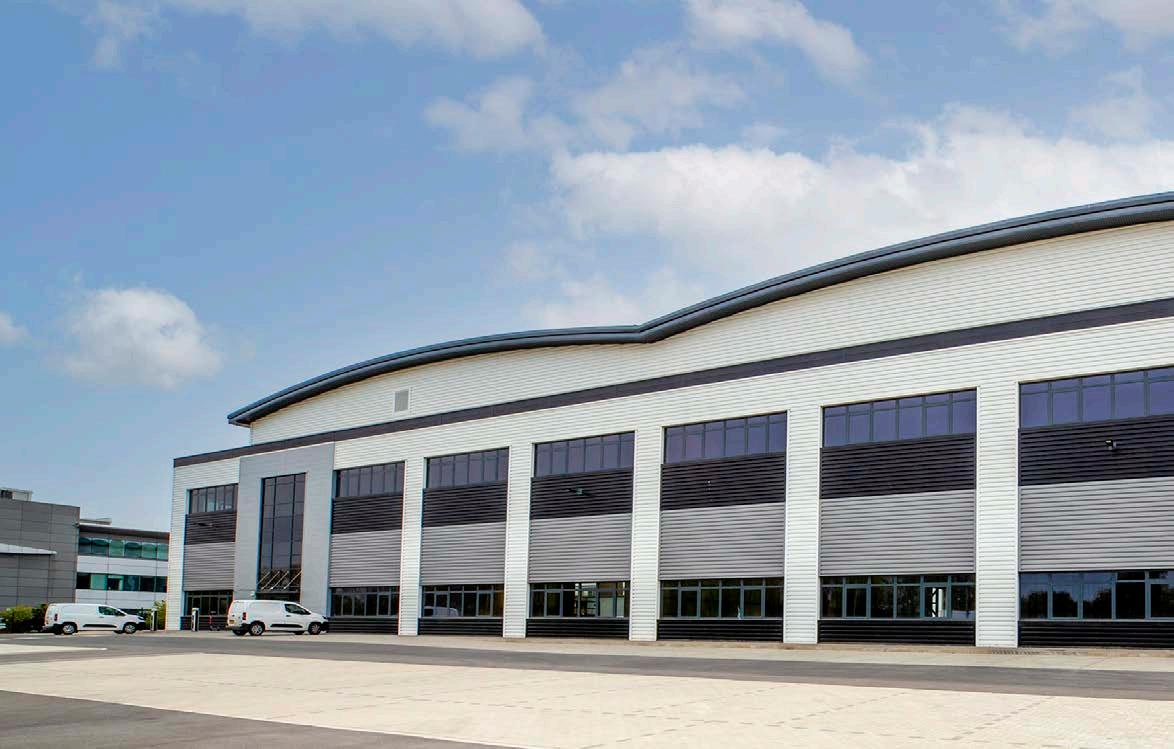

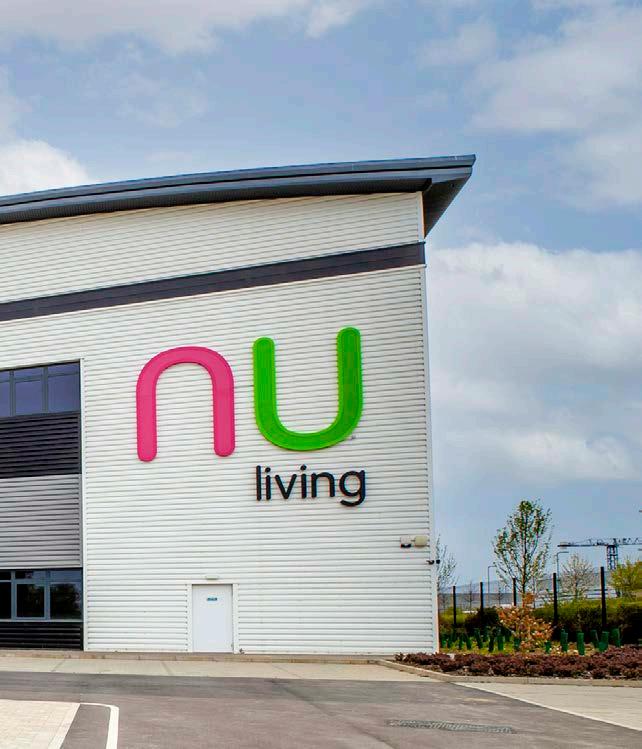
Factory 1