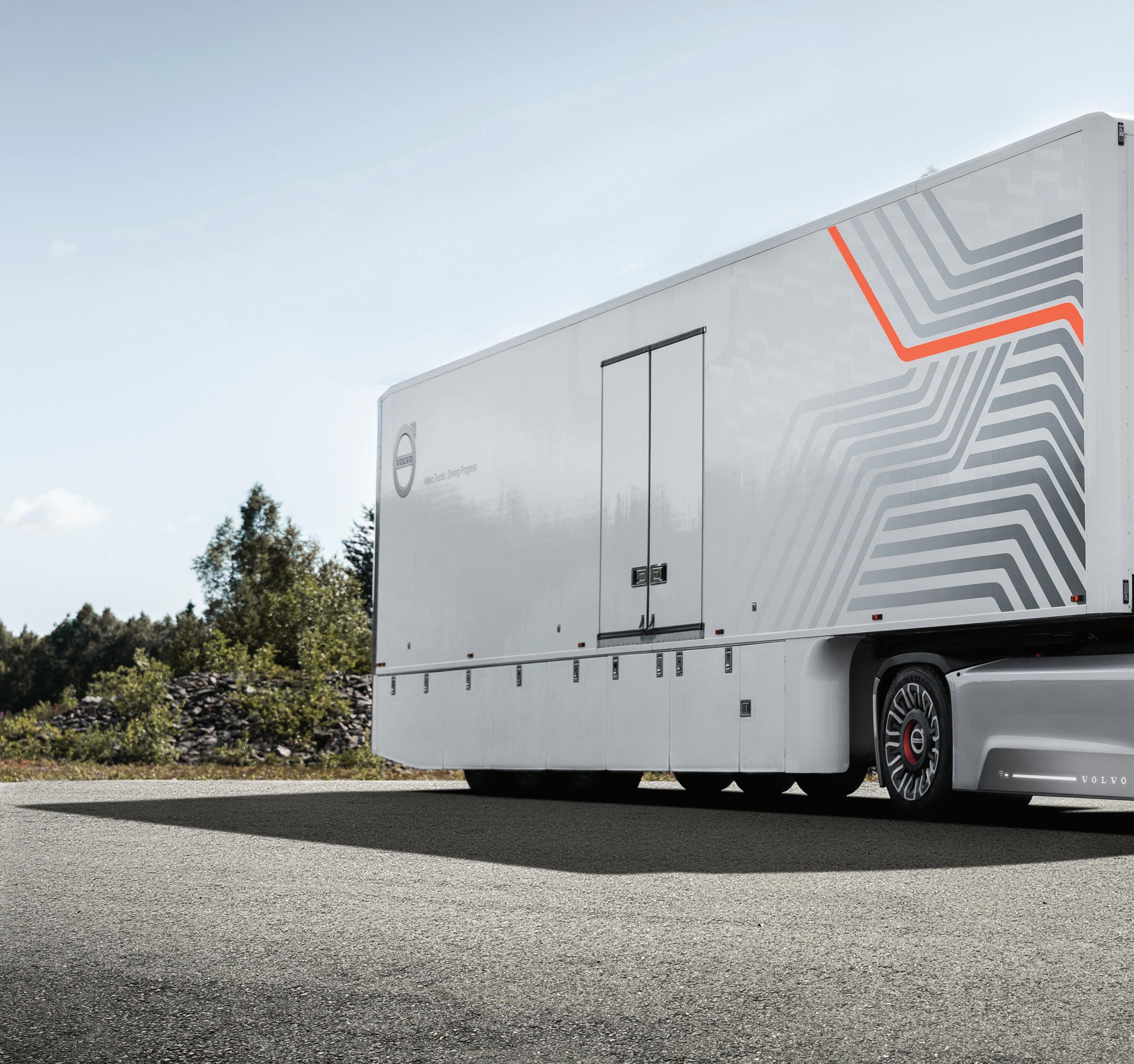
11 minute read
FREIGHTED WITH AUTONOMY
While companies such as Tesla, Uber, Cruise and Waymo have been making a lot of noise about their self-driving cars, another group of almost a dozen companies have been quietly leapfrogging them in their quest to create autonomous trucks, which promise to have a profound impact on the transportation of freight
All over the world, heavygoods-vehicle drivers are in short supply. In the UK, there is a shortage of about 100,000 drivers; Germany has 45,000 truck driving vacancies and estimates suggest that two-thirds of all German lorry drivers could retire within 15 years; and the American Trucking Associations has projected that the driver shortage in the USA will exceed 160,000 by 2028. Numerous factors are to blame, but chief among them is an ageing demographic: the US Bureau of Labor Statistics estimated that in 2019, the average age of a commercial truck driver in the USA was 55 years old; in the UK, the average age is 48 years, almost half of drivers are over 50, and only one per cent are under 25.
Logistics companies are scrambling to find ways to convince young people to join the industry, but elsewhere, numerous start-ups are working their way towards another solution: do away with drivers altogether. Among the companies vying to bring robotic trucks to our roads are TuSimple, Gatik, Aurora, Embark, Locomation, Plus.ai and Waymo, the Alphabet spin-off that has long focused on self-driving cars. The general consensus is that the current leaders in the race are TuSimple, Aurora and Waymo.
The underlying technology in both autonomous cars and autonomous trucks is relatively similar. Both use sensors – typically a combination of cameras, lidars and radars – to collect data that are then fed into an onboard computer that controls the vehicle using algorithms finetuned during extensive training and simulation that may involve millions of kilometres of test driving.
Trucks offer an excellent platform

Volvo’s distinctive cab-less Vera autonomous truck
for autonomy. Their size makes it possible to mount sensors higher off the ground, giving them an improved field of view and also enables greater processing power for the on-board computers. Both of these are important factors because trucks also bring specific problems. Because they are much heavier than cars, they have a much longer stopping distance and hence need to be able to sense conditions further in advance. In most autonomous cars, the primary lidar sensor has a practical range of about 200 metres; whenever possible, the multiple high-definition cameras on TuSimple’s trucks look up to a kilometre ahead, which is about twice as far out as professional truck drivers look while driving. The onboard computer system uses input from the cameras to detect other vehicles and then calculates their trajectories.
The weight of the vehicles also means that there’s greater scope for damage if an accident does occur. ‘Because of the heavier weight of the vehicle and the high speeds, if something goes wrong, it’s catastrophic. You don’t get a small accident with a big rig truck,’ says Bruno Bowden, a former engineering manager for simulation at Aurora. ‘The heart of the problem for driving is predicting about five seconds into the future.’ However, with trucks, he says, that figure doubles.
Freight-hauling trucks have another advantage over passenger vehicles: they typically follow fixed routes and spend most of their time on highways, which tend to be more predictable (no traffic lights, cyclists or pedestrians) and easier to navigate than local streets.
In the USA, about 80 per cent of freight travels along 20 per cent of the country’s highways. ‘By automating these high-volume freight routes, there will be tremendous efficiencies gained in terms of improved safety, increased capacity, lower operating costs and a reduced environmental impact,’ say Jim Mullen, TuSimple’s chief administrative and legal officer. TuSimple’s fleet of 40 autonomous trucks is already hauling goods between freight depots in Arizona and Texas, following routes that are about 95 per cent highway under what’s known as level 3 or ‘supervised’ autonomy (see Autonomy levels), in
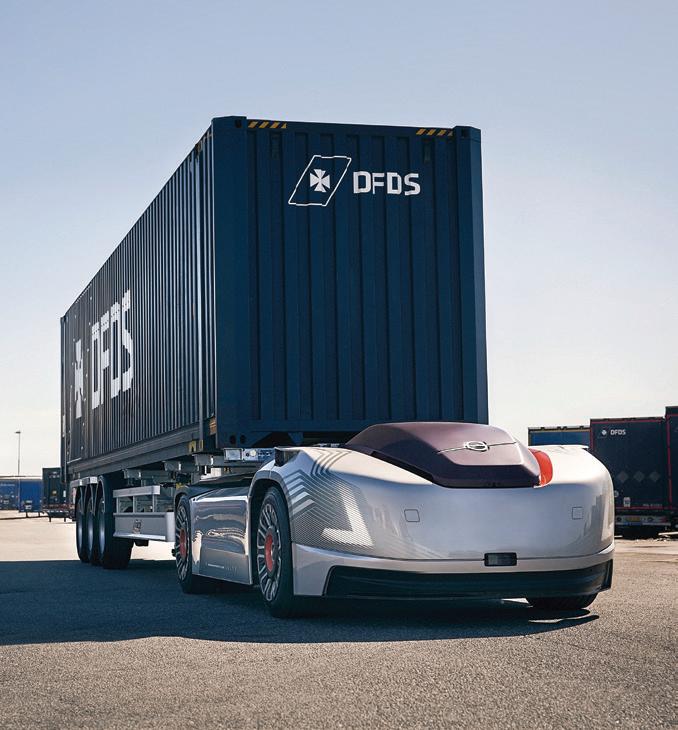
Volvo is working with ferry and logistics company DFDS in Sweden Waymo has adapted technology developed for self-driving cars for use with Class 8 trucks

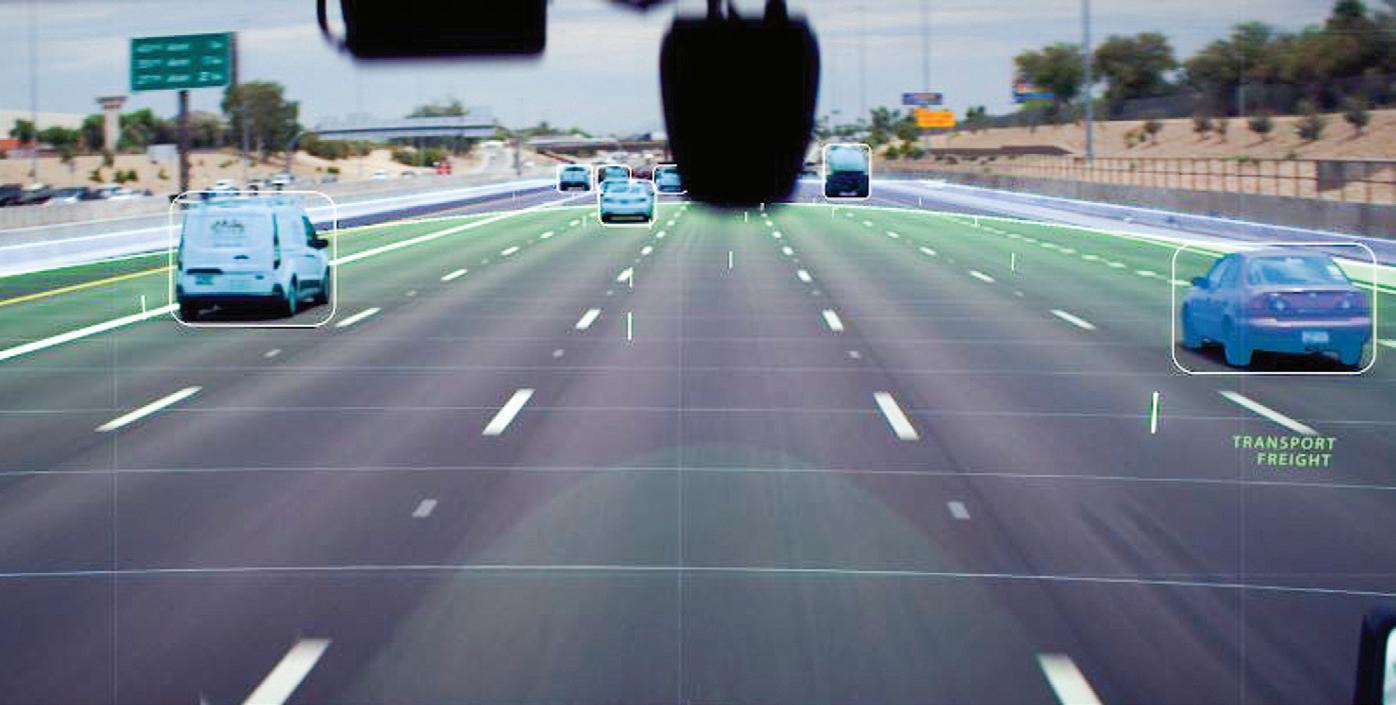
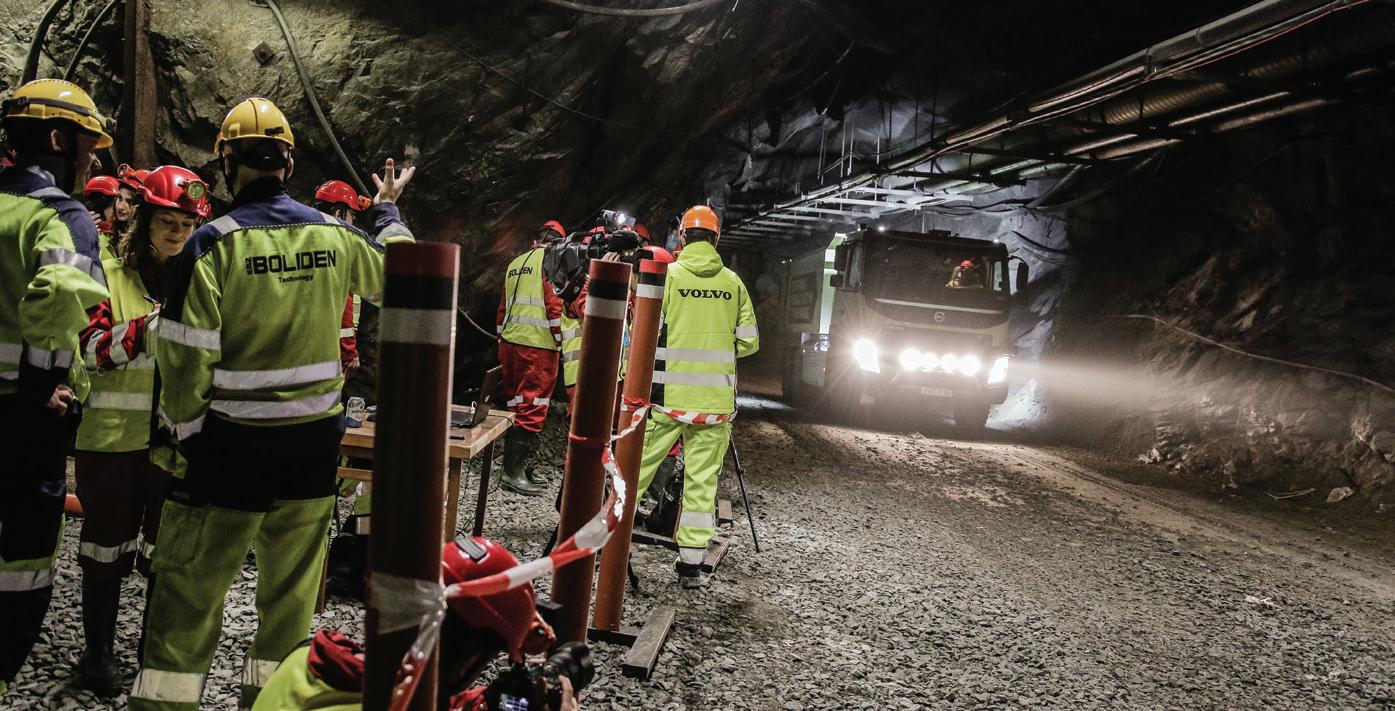
Volvo’s self-driving FMX truck is being tested in operations in the Boliden mine, Sweden
A TUSimple-computer’s-eye view of the road
which a driver rides in the cab, ready to take the wheel if required.
TuSimple plans to achieve level 4 autonomy by 2024. Later this year, the company will hold its first ‘driver out’ test, running a fully autonomous truck for more than 100 miles, including at night, to show what its technology can do. ‘This is no longer a science project,’ says Chuck Price, chief product officer at TuSimple. ‘It’s not research; it’s engineering.’
The southwestern US states – specifically, Texas, Arizona and New Mexico – are where most of the testing of autonomous trucks has been taking place, due to a combination of favourable regulation, weather and road conditions. ‘In 2018, we identified Texas as the ideal location to start commercialising our autonomous trucks because of the dry weather, massive freight economy, strong highway infrastructure, innovation friendly regulations and public-private partnership potential. It’s why our first route was Dallas–Houston in 2019,’ says Kodiak Robotics CEO Don Burnette.
One reasons why driverless trucks have attracted so much interest is the cost reductions they offer, projected to amount to 30 per cent or more per kilometre. They offer increased productivity because vehicles can essentially operate 24/7, stopping only to re-fuel. The algorithms that control driving behaviour also ensure that the trucks choose the safest and most efficient way to drive, using their brakes less often than humanoperated trucks, which improves fuel economy by about ten per cent. By driving more steadily, with less sideto-side movement in their lane, they bring additional efficiency gains and minimise tyre wear. The improved safety promised by driverless trucks is also likely to bring down insurance costs. ‘As long as there are human drivers out there, there will be accidents, but you are taking a lot of cases away where it’s the truck driver’s fault, due to fatigue or other factors,’ says Bart De Muynck, an analyst at market-research company Gartner. ‘When you take that fatigue away, you improve safety.’
Cheng Lu, TuSimple’s CEO, goes further, stating that removing human drivers and allowing trucks to run more hours on the road will cut freight costs in half. ‘When we started the company in 2015, it was very obvious to us that logistics would be first,’ Lu said. ‘We’re hauling freight, we’re not hauling people, so obviously it’s a different technology framework. I don’t know why it’s taken some people five years to realise this.’
TuSimple recently said that trucks using its automated driving systems while hauling fresh watermelons along a 1,530-kilometre route from Nogales, Arizona, to Oklahoma City cut ten hours off what’s normally a 24-hour journey. Although a human driver was on board for safety purposes and worked on the pick-up and delivery of the produce, during the long middle segment of the drive, the vehicle drove itself.
While most of the testing of selfdriving trucks on public roads has taken place in the USA and China, Scania, which is working with TuSimple, was recently granted permission by the
AUTONOMY LEVELS
AS SET OUT by the Society of Automotive Engineers, the different levels of autonomy for vehicles are as follows: ■ LEVEL 1: a single aspect is automated, for example, radarmanaged cruise control and lane-keep assist. ■ LEVEL 2: two or more elements are automated, for example, cruise control systems that take over directional, throttle and brake function, lane-changing modes and self-parking features. ■ LEVEL 3: conditional automation, where the vehicle can control all aspects of driving but a driver must be on hand to respond to a request to intervene. ■ LEVEL 4: fully autonomous in controlled situations, such as particular times of day, in certain weather conditions or on premapped routes. ■ LEVEL 5: fully autonomous anywhere, anytime. ■
IN POD WE TRUST SWEDISH START-UP Einride is taking a slightly different approach. In addition to producing electric heavy trucks driven by humans, it’s also developing autonomous electric pods that are designed to carry freight. In addition to operating autonomously without human intervention, the unusual-looking cabless pods can be controlled by a remote operator who may be located hundreds of kilometres away using Einride’s own in-house tele-operation technology. Einride plans to produce pods with differing levels of autonomy and functionality for use in different settings. For example, the fully autonomous AET (Autonomous Electric Transport) 1 Pod is for use in closed facilities with predetermined routes, while the AET 2 pod is designed for closed-facility operation but also has the capability to travel on public roads over short distances. Both have top speeds of 30 km/h, weigh 26 tonnes, a payload capacity of 16 tonnes and a battery range of 130–180 kilometres. The AET 3 pod is designed for rural use and the AET4 for highway travel. Einride claims that its new vehicles will ‘reduce transport costs by up to 60 per cent and CO2 emissions by a staggering 90 per cent’. It aims to have the level 3 and 4 pods ready to ship to customers in 2022 and 2023. ■
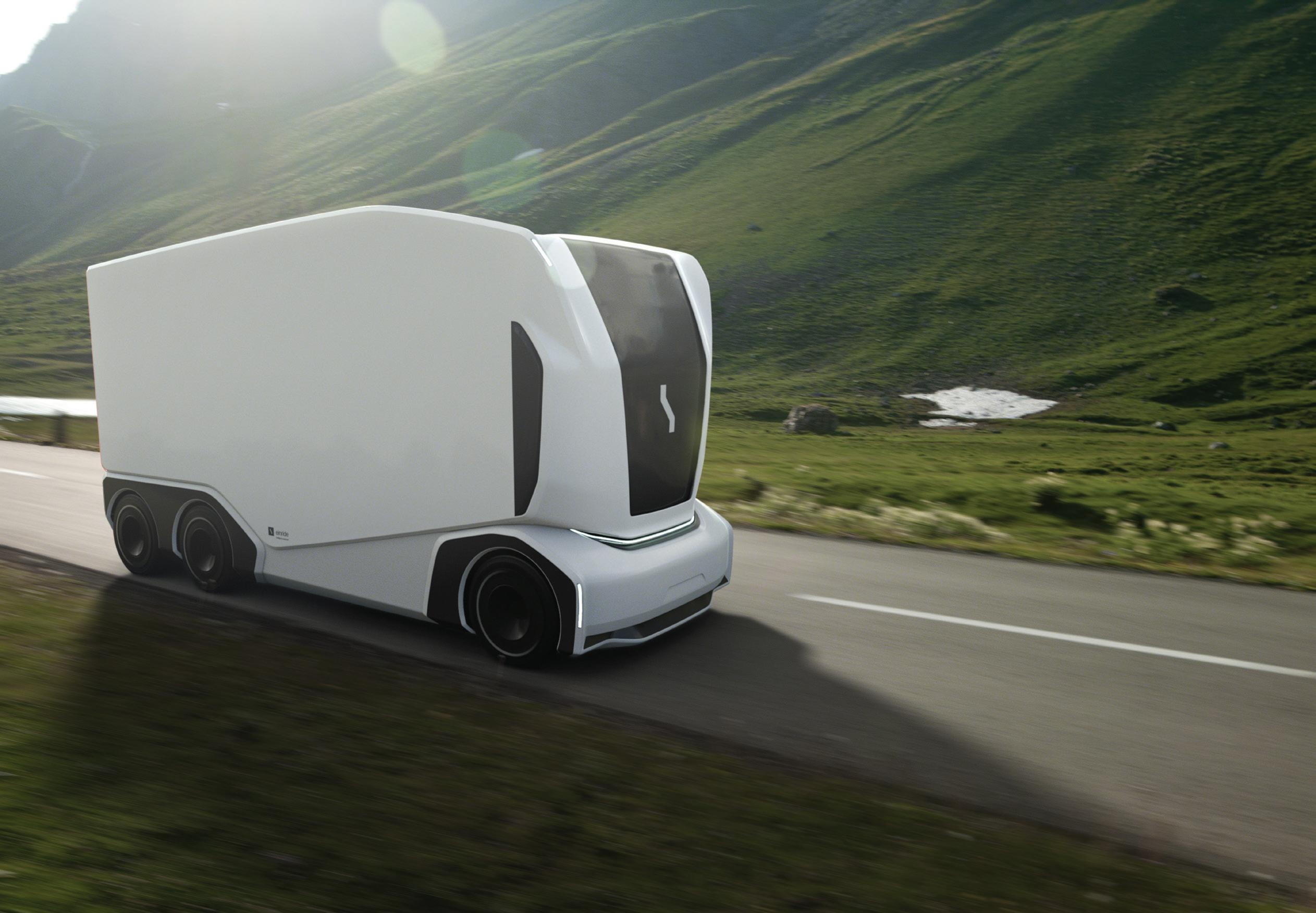
Swedish Transport Agency to carry out human-driver-supervised tests on the E4 motorway between Södertälje and Jönköping. A test engineer will also be on board to monitor and verify the information transmitted to the truck’s onboard computer by its sensor array. ‘In the coming years, we also expect to be able to test the technology in other European countries and in China,’ says Hans Nordin, who heads up Scania’s Hub2hub project.
Scania has already gained considerable experience testing self-driving trucks for use in mining transportation in Australia, which has been taking place since 2017. ‘The experience gained from these tests shows that autonomous vehicles can become a reality in just a few years for transportation in closed areas such as mines and terminals,’ says Nordin.
Most observers agree that ‘depot-todepot’ transportation, where freighthauling trucks travel on highways between reloading centres, will most likely be the first use for completely autonomous trucks on public roads. Human drivers would handle local driving and cargo loading and delivery, while the self-driving trucks would operate in the more controlled highway environment. ‘We have come so far in the development of self-driving vehicles that the technology may be ready to be introduced to the market already within the next five years for this type of transportation. However, it will take longer before autonomous vehicles for driving on roads with twoway traffic and in urban environments becomes a reality,’ says Nordin.
Another option under consideration is human-guided autonomous convoying, where a human-controlled and supervised lead truck is followed by a self-driving truck. The driver would drive the trucks manually through the surface streets and onto the highway, at which point the autonomous system would be engaged.
It’s clear that the automation of trucking isn’t a question of if, but of when, where and how. And at the current speed of development, the when looks as though it will be sooner than you think. ■
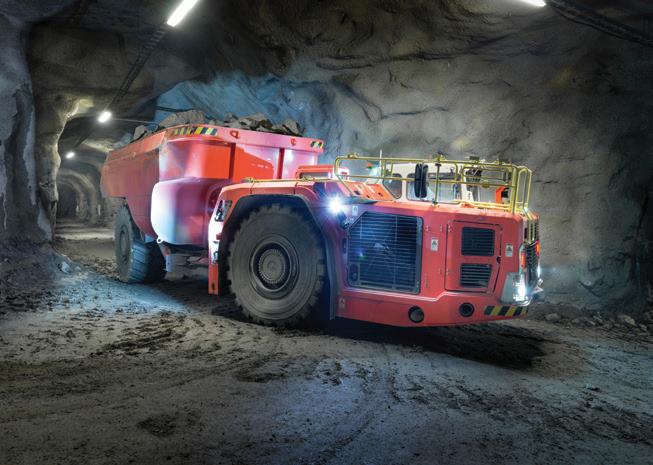
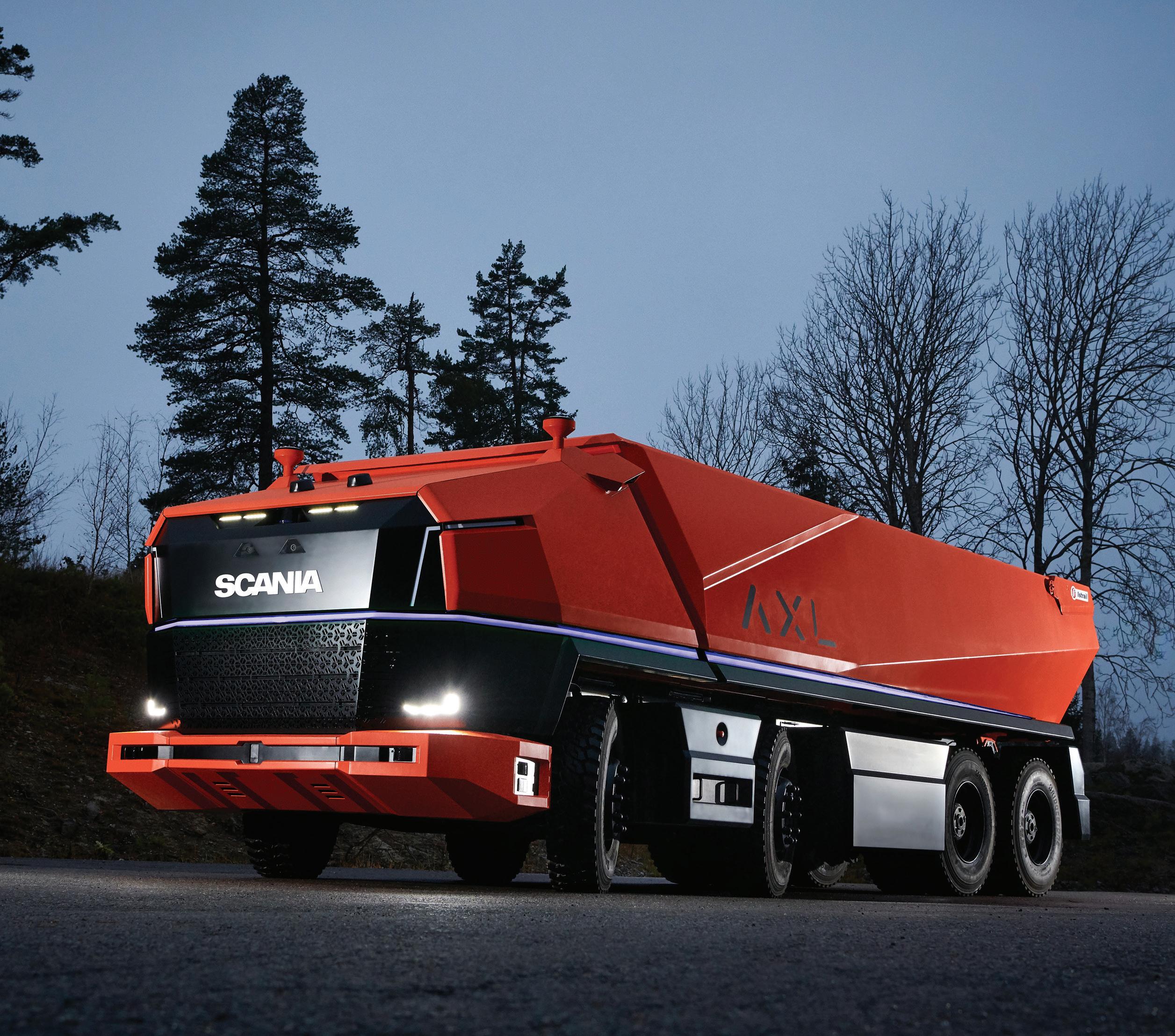
ROCK STARS
AS IS TRUE OF MICROGRIDS (see page 16), the mining industry has been an enthusiastic early adopter of autonomous-vehicle technology. At present, Australia dominates the market; in 2020, it had 80 per cent out of the almost 500 autonomous haul trucks that were in operation at surface mines around the world. Fortescue Metals Group’s Solomon Hub iron ore mine in the Pilbara in Western Australia is currently being developed into a fully autonomous operation.
While Volvo, Scania, Sandvik and Saab are all developing driverless mining vehicles, some of which are now in active use, Komatsu and Caterpillar together account for almost 95 per cent of the autonomous surface trucks in operation.
Mostly operating in iron ore and coal mines, the trucks offer improvements in productivity, a reduction in accidents and operating costs, increased machine and tyre life, and lower fuel consumption. Estimates suggest that the technology reduces operational costs by about 20 per cent and improves productivity by about 30 per cent, while cutting the number of safety-related incidents by half. According to Tim Day, vice president of BHP Billiton, this last improvement is the primary motive for the adoption of driverless trucks: ‘The single biggest reason is safety,’ he says. In 2017, the World Economic Forum predicted that the automation of mining machines would save more than 1,000 lives and avoid 44,000 injuries.
The vehicles use a combination of cameras, lidar, radar and GPS to navigate their way around a predefined course that takes them from loading units to dump locations. They are operated and controlled by a central supervisory computer that collects information from their sensors and directs them around the course, setting speeds and directions. The trucks can also effectively ‘talk’ to other trucks in order to optimise loading and hauling efficiency. ■
Above: Scania’s first fully autonomous self-driving concept truck, the AXL; Inset: Sandvik’s TH663i truck can be fitted with the company’s Automine control system