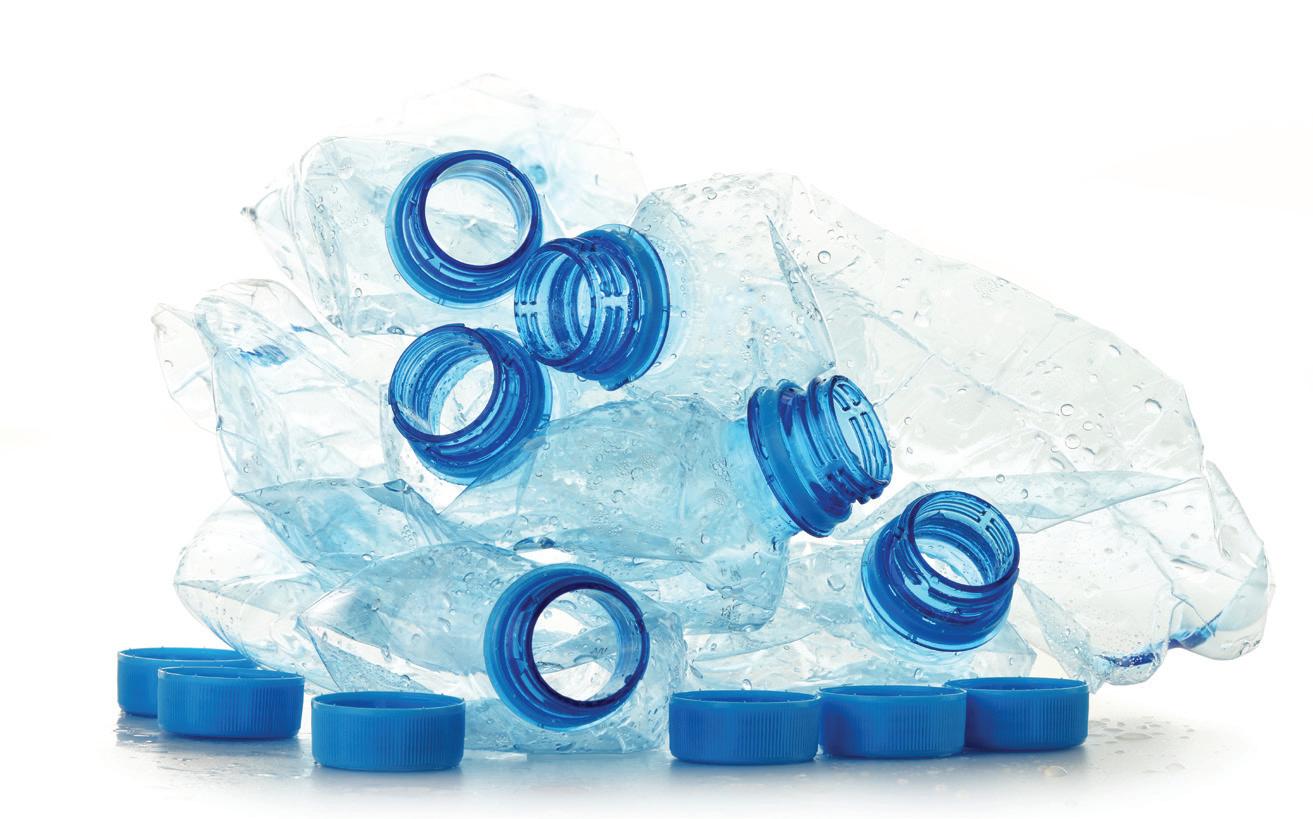
10 minute read
DESIGNING FOR AND FROM RECYCLING: WHAT’S NEXT?
Mark Hester BSc (Hons) MCSD, co-founder and
director of technology at London-based strategic design and engineering agency the Imagination Factory, explores ways that designers can help to solve the world’s ongoing plastic crisis
Since the beginning of its mass production during the 1940s, plastic has become a ubiquitous part of human life. As of 2018, global annual plastic production amounted to almost 360 million tonnes. By 2050, production is expected to have tripled and will account for a fifth of global oil consumption. Unfortunately, the low cost of production and widespread use mean that far too much plastic ends up in our environment, either as landfill or as litter.
It has been a few years since China stopped accepting the contents of our recycling bins. Since then, pressure has been mounting globally for manufacturers to take a more resource-conscious approach to design, with the end of a product’s life in mind. All too often, product lifecycles are linear rather than circular because the initial design fails to take into account the recycling of the product’s constituent materials.
It’s clear that we need to work towards significantly reducing our reliance on virgin and singleuse plastics. As designers and engineers, we’re strategically placed to have a significant impact on this problem by making smarter decisions about the materials we specify for the products we design. By understanding the choices that we make about recyclability at the earliest stages of our design thinking, we can significantly affect the end of a product’s life and greatly increase the proportion of the product that’s available for recycling. The ultimate goal is to create products that can be turned back into their original materials at the end of their life and used to make more products.
FOR AND FROM
There are two elements to this process: designing for and from recycling. Designing for recycling means creating a product that enables better and easier recycling at the end of its life without compromising on its requirements during the useful stage of its existence; designing from recycling means creating a product (wholly or partly) made from recycled materials.
There are many reasons why designers and engineers struggle to engage with designing for and from recycling, but it doesn’t have to be this way. A project with which I’ve been heavily involved over the past four years proved that working together across sectors is the most effective way to improve the situation. But at a local level, if each of us plays our part in understanding how designing differently and increasing the demand for recycled plastics effects change, we’ll see more rapid improvements.
Obviously, there are obstacles to the use of recycled materials that need to be dealt with. Perhaps your company has had a bad experience with recycled materials, such as unpleasant smells, failures in functional testing or poor surface finish. There may also be issues related to cost or availability, or simply a lack of expertise or confidence when it comes to designing for recycling. Cost is a potentially significant stumbling block. Recyclers currently operate on very small margins, so turning products back into useable materials favours metals rather than plastics. Producing recycled plastic
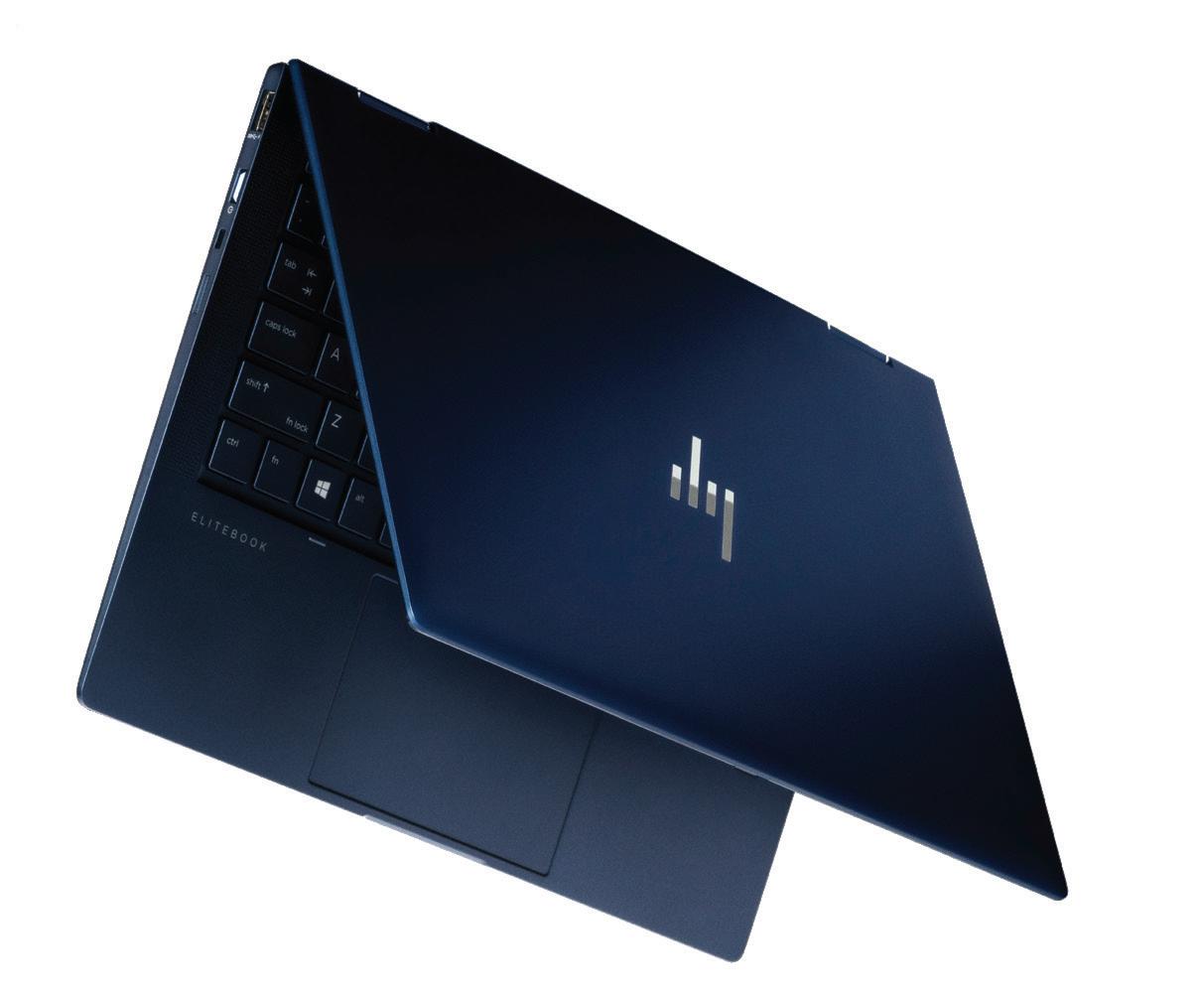
Sony’s HX99 camera features the company’s own SORPLAS recycled plastic
can also require a lot of effort (and hence cost) compared with virgin plastic. This is compounded by the fact that the cost of virgin plastic doesn’t currently factor in the impact on the environment of the oil used in its production, nor the cost of disposal. The decreasing price of oil has also made it harder for recycled plastic to compete against virgin materials.
Two very different worlds with very different needs must come together for things to improve. On the one hand, you have design and manufacturing, and on the other, you have material recovery. Typically, these two worlds haven’t communicated often or effectively. Designers and engineers haven’t understood the implications that the decisions they make when designing a product have on the material-recovery phase of that product. And those carrying out the recycling haven’t always considered the requirements of designers and engineers.
As designers, when choosing or specifying a material for a project, we want to be confident that it will be repeatable and reliable, and will consistently behave the way we want it to. Recyclers haven’t always been able to provide us with that confidence; a high-end product has been particularly difficult to source. If you were using a plastic for garden furniture, for example, many recycled plastics would be fine, but it would be too risky to use the same material in, say, a new vacuum cleaner.
This isn’t down to a lack of willingness on the part of the recyclers. It has more to do with the level of demand from manufacturers and their willingness to take on some of the risk to see progress, driving down some of the costs in order to encourage more widespread adoption of recycled plastic. Recyclers need to be supplying materials that enable them to make money from material recovery. They also need to understand that engineers want to use recycled plastic, but need it to reach a certain level of quality; it’s rare for a recycler to go to a manufacturer and ask, ‘What is it that you want the plastic to do?’
CIRCULAR ECONOMY
Five years ago, we began to talk with a group of innovative thinkers across Europe, including manufacturers, polymer scientists, designers and recyclers, about how we might collaborate to bring these two worlds together and find a way forward. The result was PolyCE (Polymers for the Circular Economy). With EU support, we were able to create new materials together and prove that they could be produced at sufficient scale to make them economically viable.
One of the 20-member consortium’s most exciting breakthroughs involved the
Philips SenseSeo coffee machine. Philips challenged its coffee machine department to develop the most sustainable Senseo machine possible by incorporating recycled material and closing the loop. The creation of a Senseo Eco demonstrator enabled Philips to overcome challenges such as material availability, heat stability and colour freedom while also reducing the product’s environmental footprint, creating new and useful aesthetics, and helping to raise consumer awareness. The process proved that the machine could be made with three quarters recycled content and provided a test case for the integration of recycled plastics in new products, thus helping to build the internal confidence needed to continue sustainable development at Philips.
We also produced a set of guidelines for designing for and from recycling, focusing on the consumer electronics market, which has often been neglected. However, the principles can be applied across the design of most durable plastic products.
Products represent the total assembly of a collection of parts. At the product level, we must consider things such as usage, end of life, collection, pre-treatment, shredding, sorting and turning back into useful material. So, for example, we should avoid making assemblies with adhesives because they can interfere with shredding and sorting. At the part level, we must think about the material properties, production, moulding and geometry. Here, we might consider trying a recycled material instead of a virgin plastic to see how it performs, even if much of the overall assembly remains unchanged.
When designing from recycling strategies, it’s important to consider the four main parameters
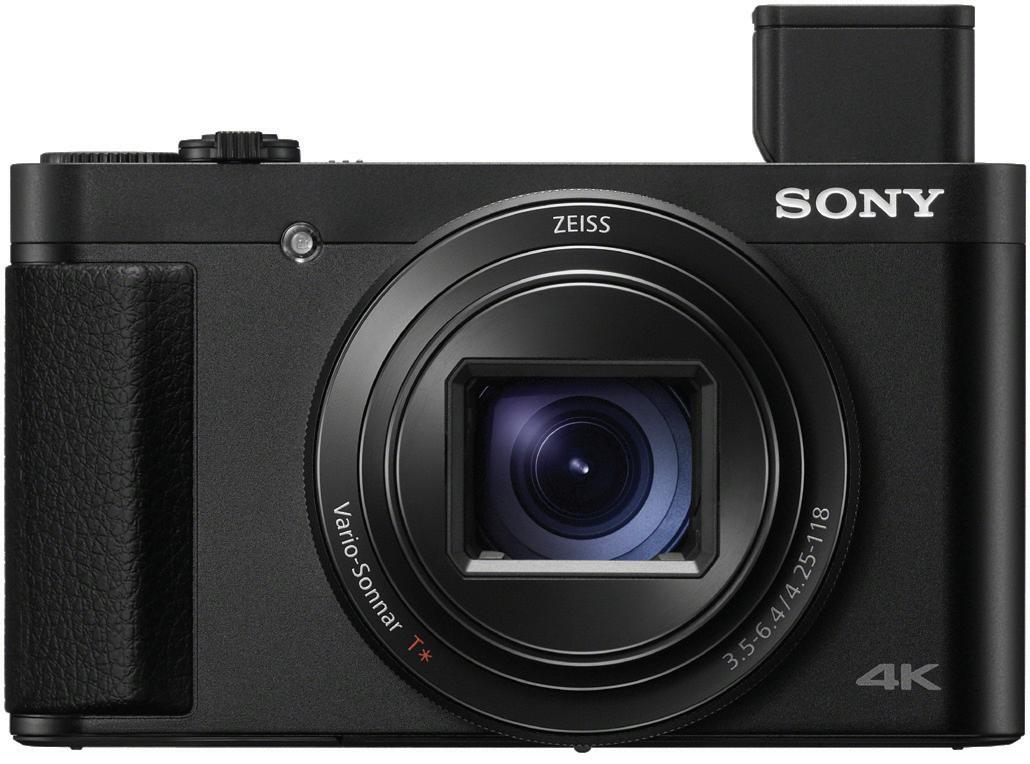
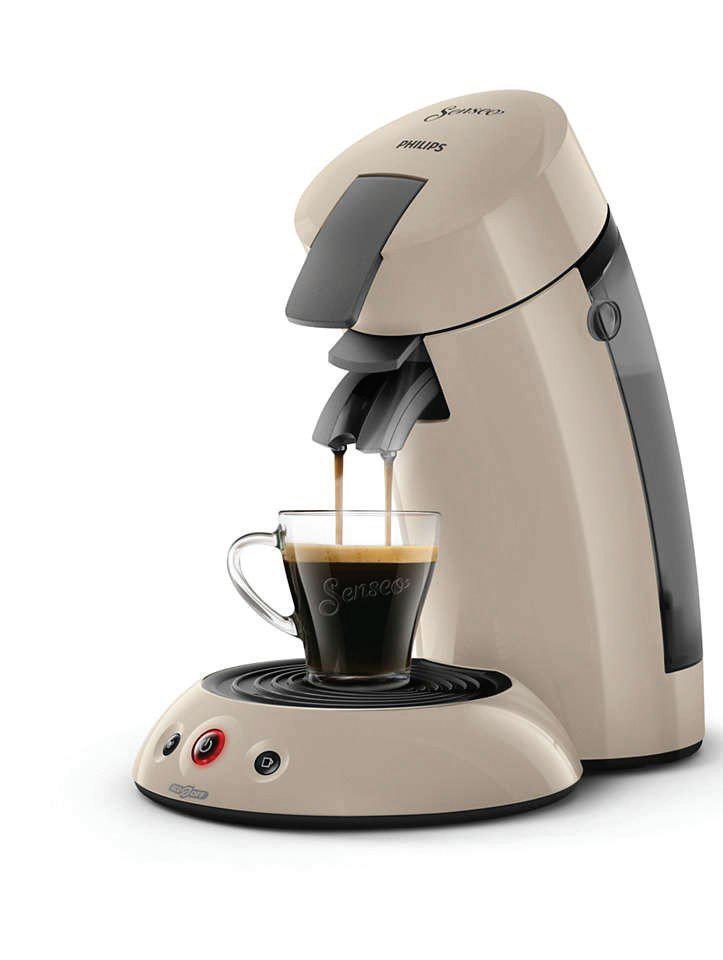
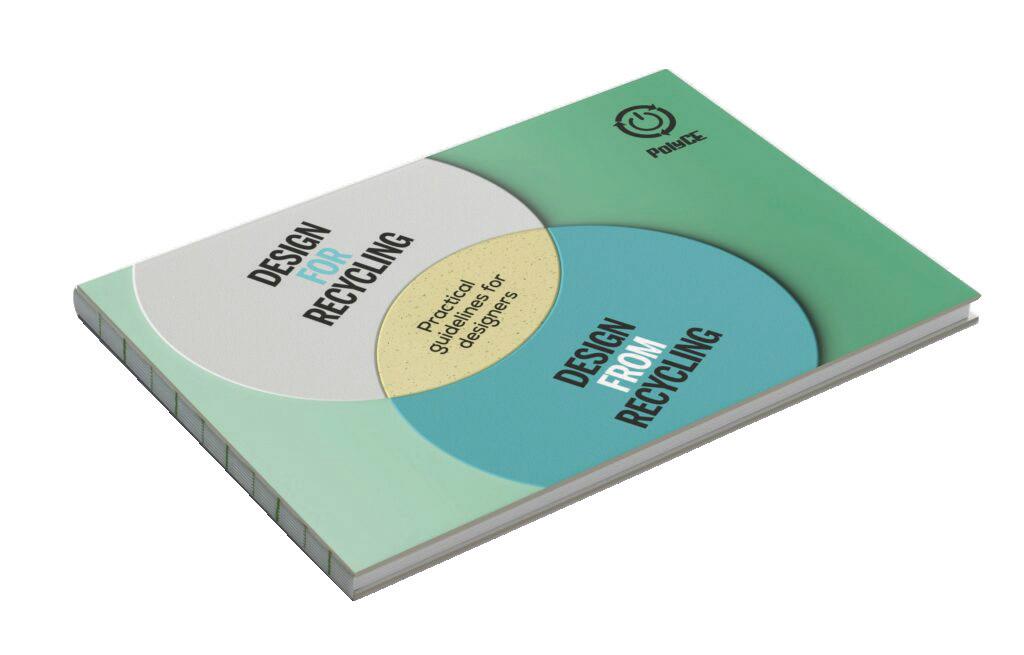
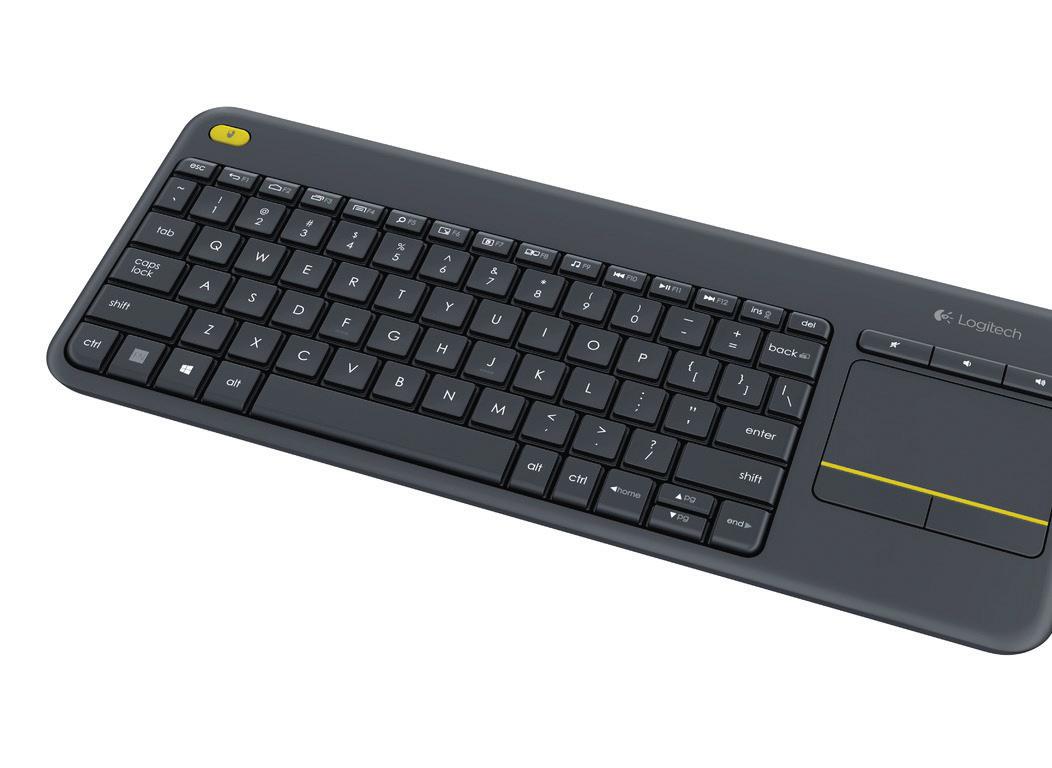
mentioned above – material, geometry, mould and production – each of which bring specific challenges. For materials, there may be a lack of specification data or information on how to best process the material, and there will likely be limited colour options and availability. When considering geometry, designers may need to experiment because the upper and lower limits of what can be achieved with the recycled material might not be known, or there may be little data available on mould flow. There is also the possibility that contaminants in the material will damage the mould, or extra cleaning might be required. And when it ultimately comes to production, problems may arise due to a lack of stability and repeatability between plastic batches.
To counteract these challenges, we recommend using what we call the drop-in method, which is based on three key pillars: a complexity-level tool, a ‘look and learn’ approach and six steps to material approval.
The complexity-level tool is a flowchart that allows designers to identify how feasible it will be to swap an existing part made from virgin plastic to one that is made from recycled plastic. Classifying the product parts creates a roadmap and a starting point. So, for example, it’s advisable to start with the ‘lowhanging fruit’ – parts that have relatively low technical and aesthetic requirements and are hence easier to manufacture from recycled materials – before moving on to more difficult parts. It also allows the identification of parts where it’s currently unfeasible to switch.
The look-and-learn approach involves designers building into their processes the creation of ‘demonstrators’: physical samples made using existing moulds that enable testing of the material’s aesthetic and functional properties, as well as the material’s behaviour during processing. This approach is all about removing specific uncertainties within each of the six
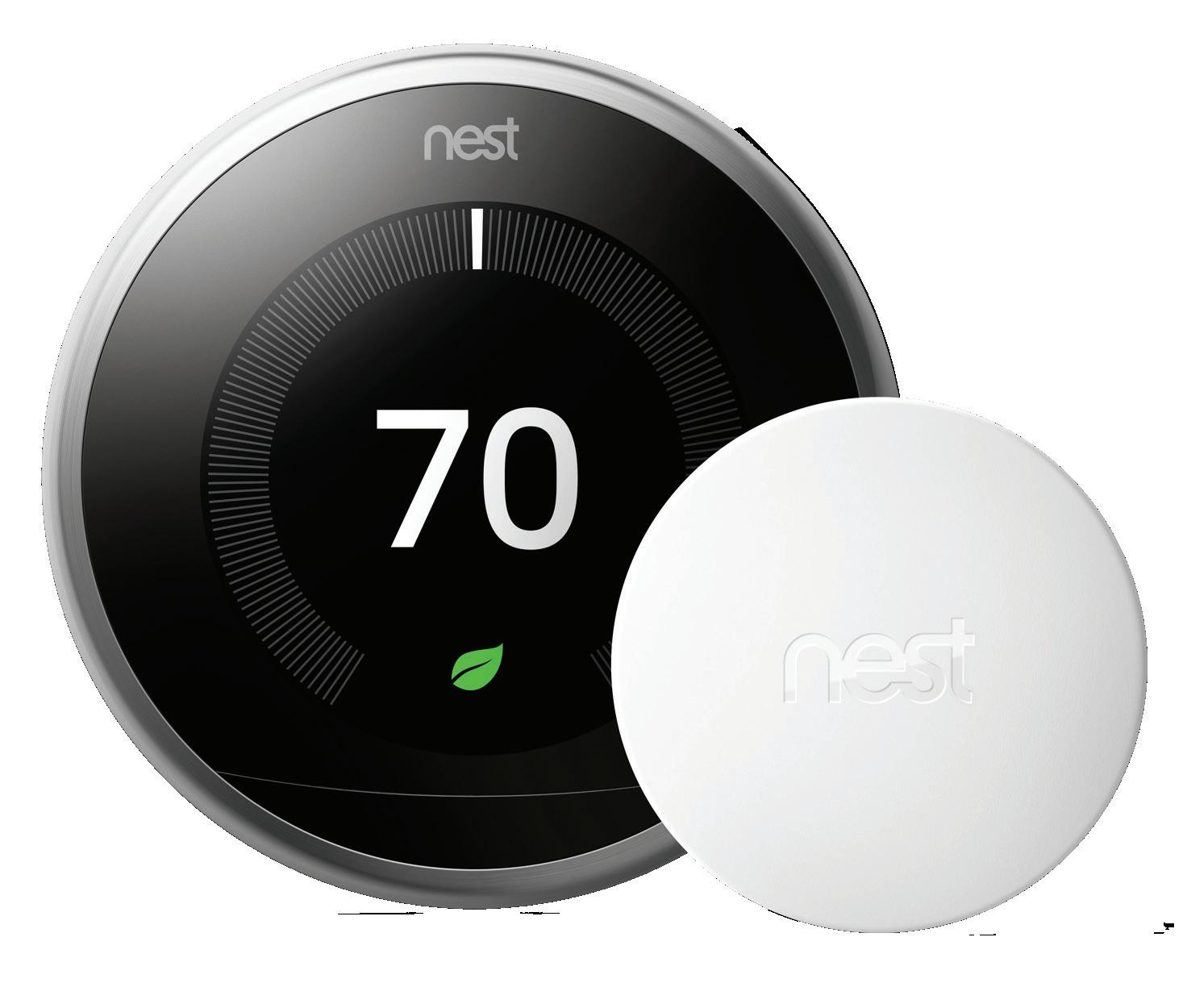
Google, Apple and Logitech have all committed to increasing the amount of recycled plastic in their products. Many of the larger electronics brands are also developing their own custom post-consumer recycled plastics in partnership with their suppliers
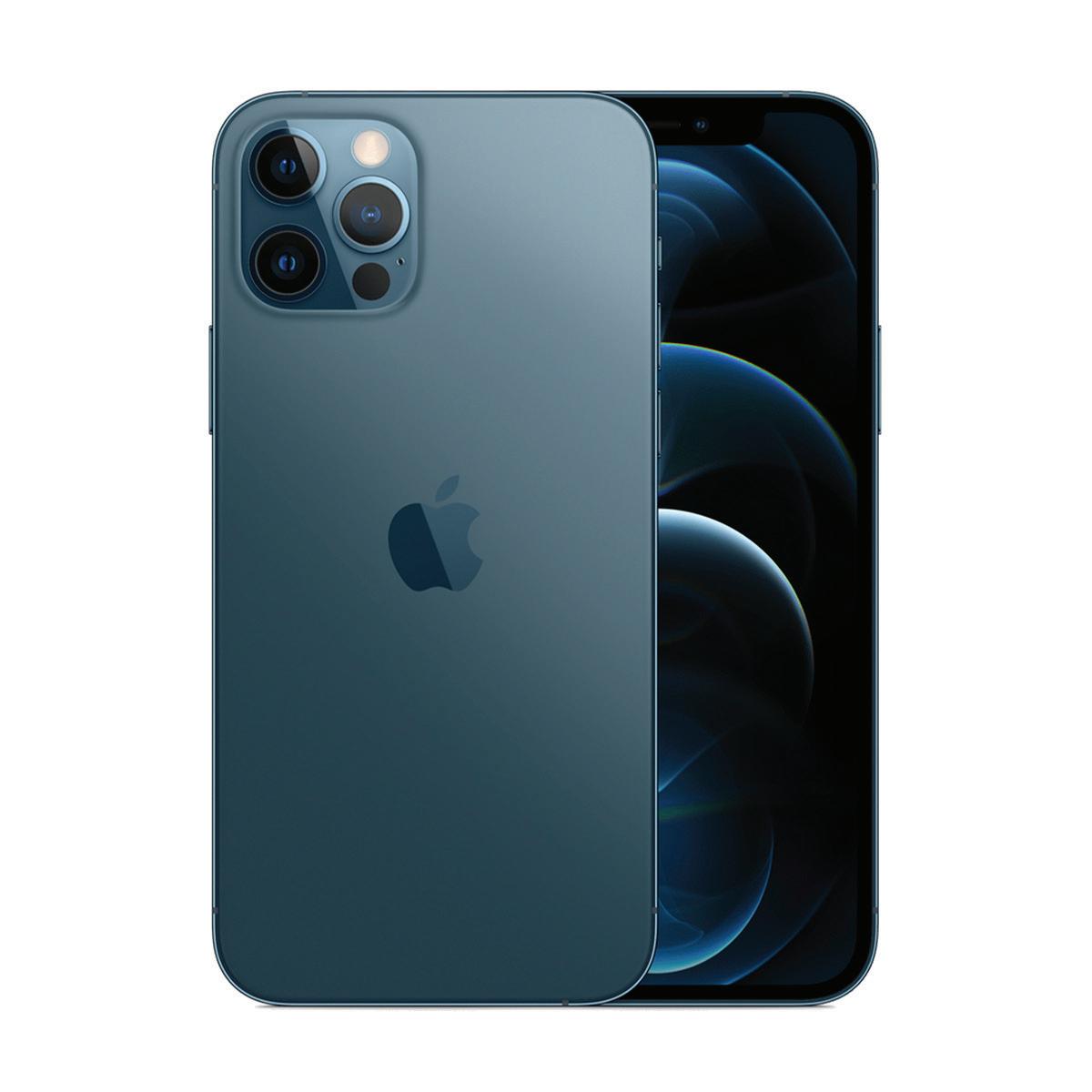
steps below. It will help to determine the feasibility and desirability of the recycled materials for your purpose and enables you to compare virgin and recycled plastics, and find out to what extent they match.
Once you’ve chosen which parts will be made with recycled plastics, the development process begins. There are then six steps to final material approval: material selection, property testing, pilot moulding, a large moulding trial, product assembly and, finally, mass production.
DRIVING DEMAND
The guidelines also go into detail about specific areas that designers need to look out for when designing for and from recycling. For example, when designing for recycling, it’s obviously best to avoid hazardous or polluting components, but if they must be used, it’s important to enable easy access to, and removal of, those components. When using recyclable materials, it’s important to avoid coatings, foam, thermosets and composites, plating and galvanising, uniform high-gloss surfaces, glass fibre, polymer blends and additives. You should also minimise the use of magnets, thermoplastic elastomers and thermoset rubbers, and where possible, use plastics that are in common products today. And finally, use material combinations that will aid liberation, so avoid overmoulding, moulding in inserts, bolts and the like, and attaching ferrous and non-ferrous materials.
If you’re involved in the design and manufacture of plastic products, consider how you might embed these guidelines into your business’s workflow. But don’t try to tackle the plastic problem alone – find an advocate inside or outside your business who’s already doing this and can provide you with advice and support. Ultimately, the aim is to help drive the demand for recycled plastic by finding ways to incorporate it in your next project. By doing so, you’ll be helping to save the world, a little bit at a time. ■