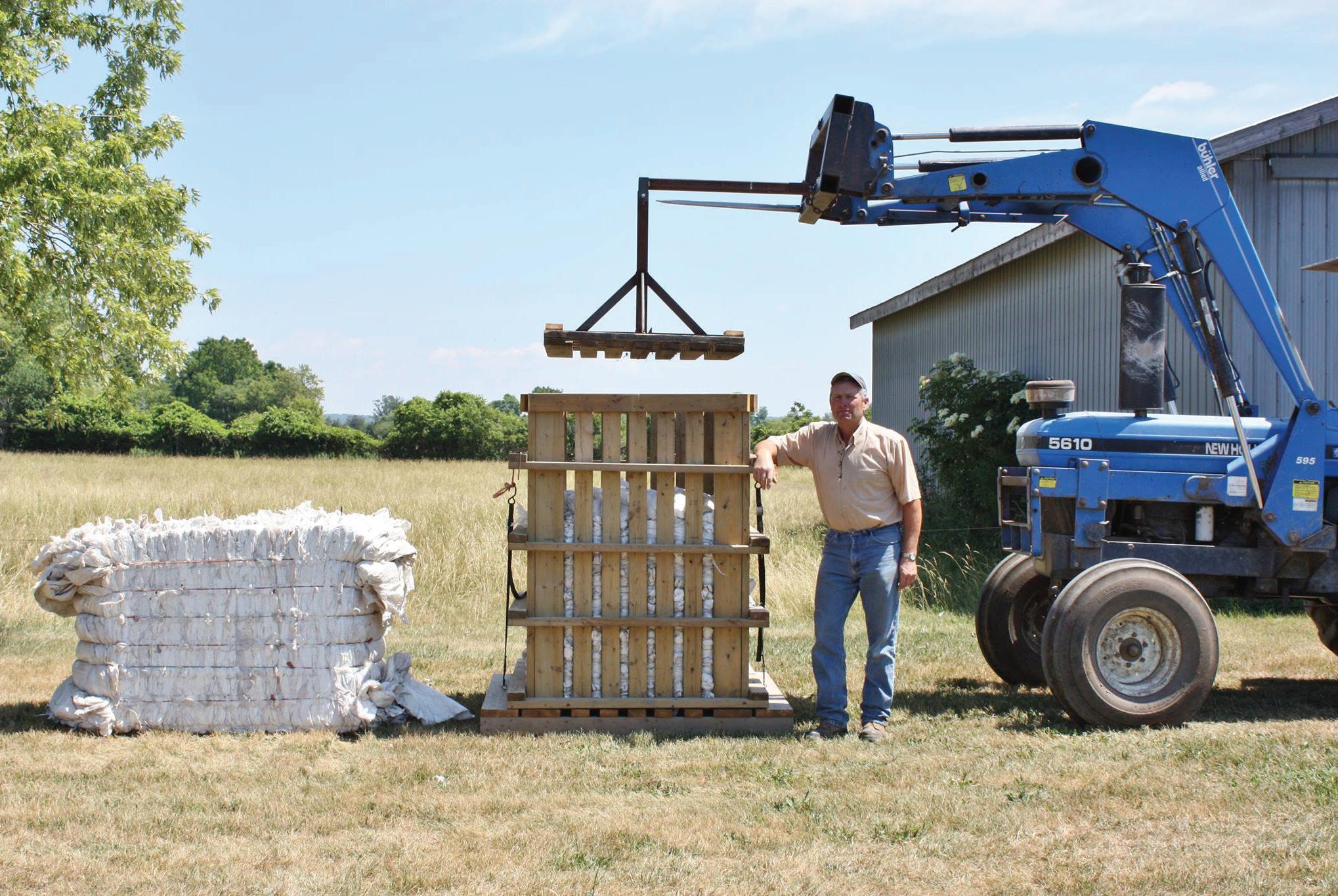
6 minute read
ENVIRONMENTAL STEWARDSHIP Celebrating
Leavitt’s Black Angus Beef, Ontario Beef producer takes the lead in promoting recycling of ag plastic
is then tied with several wraps of plastic bale twine. The loader is used to lift the crib off the plastic and voila... you’ve got a 1,000-pound bundle of used agricultural plastic ready to be shipped to the recycler.
As Leavitt came up with the design for the PacIt compactor, he created a company — U-Pac Agri Service to help market the compactor and promote the idea of recycling agriculture plastic to other producers. You can learn more about the company and compactor on the U-Pac AgriService Facebook page.
“It is just a small operation that is based in a shop here on the farm,” says Leavitt referring to U-Pac AgriServices.
“It certainly isn’t a high profit operation. It is more like a hobby that got out of control.”
ByLeeHartForTheCanadianCattlemenAssociation
Lynn Leavitt can go to bed each night with relative peace of mind knowing he is doing his part to help farmers properly manage an agricultural by-product — long considered a nuisance — while at the same time benefiting the environment.
Leavitt, who runs a commercial Black Angus beef operation in Eastern Ontario near the community of East Lake, about 40 km south of Belleville, over the past few years has developed a system for collecting, compacting and wrapping agricultural plastics — bale wrap, silage bags and plastic twine — so these materials can be neatly and economically trucked to a plastic recycler.
Farmers aren’t getting paid for recycling this used plastic, but Leavitt says there is considerable value in knowing this material is being repurposed rather than being burned (which is illegal) or buried in a landfill.
“This product — agricultural plastic — is one tool we have available that actually makes it possible to cheat nature,” says Leavitt.
“We don’t want to lose the option to use it. It is a product that allows us to put up winter feed supplies without spoilage — some people call it hay-in-a-day. It is a great tool. But then what do you do with all the used plastic? There is a lot of it, and if it is not handled properly, we run the risk of not being able to use it. So, it is important that all sectors of the agriculture industry work together to make sure it is recycled properly.”
In 2016, after feeling guilt and frustration that there were no proper recycling systems available for the agricultural plastic used on his farm, Leavitt designed and built what was later to be called the Pac-It compactor. It is a relatively low cost but effective way to handle used plastic so it can be recycled.
His efforts in developing the Pac-It compactor and promoting agriculture plastic recycling over the years, earned him recognition as the Beef Farmers of Ontario’s 2023 nominee for The Environmental Stewardship Award (TESA).
The compactor is a slated, wooden “crib” with an open top and bottom that fits on a conventional wooden pallet. The crib is roughly 54” x 50” by 67” tall.
The idea is to put clean used plastic wrap — low density polyethylene plastic — inside the crib, compress it with a plunger that attaches to the frontend loader of the tractor, keep adding material and compacting it inside the crib until it is full. The bundle
“One of the main objectives is to show other farmers there is a better way to handle this used plastic. I recall one guy who said he had this “mountain” of scrap plastic. We put it into the Pac-It compactor and got it tied into a bundle and then somehow that mountain of plastic wasn’t so much of a problem anymore.”
U-Pac AgriService sells the pre-built Pac-It compactor. The cost is $750 which covers $600 in materials and $150 in labour to cut the wood and assemble. Shipping is extra. And shipping a unit any distance can be expensive. So as an alternative U-Pac AgriService also sells the blueprints so farmers can build their own. It is not a patented design, but it has been proven to work well. U-Pac AgriService has sold about 300 of the pre-built cribs. And blueprints which cost between $20 and $30 have been sold to producers in Quebec, Ontario, Manitoba, and Saskatchewan.
Leavitt says his main interest is to raise awareness among producers that there are better options for handling agricultural plastic.
As the fourth generation operating the family farm, Leavitt runs a herd of about 100 head of commercial Black Angus cows. He keeps all his own calves for backgrounding and finishing. He works with a local abattoir to have roughly 18- month old finished animals processed. He supplies some meat products to local restaurants and there are two other local retailers who carry Leavitt Black Angus Beef meat products.
“We started finishing cattle and direct marketing meat back when BSE hit,” says Leavitt.
“We have worked with the same abattoir and have had some different markets over the years, but we have many repeat customers who keep coming back for our 21-day dry aged meat products. We need to maintain a flow of finished cattle throughout the year, so we are feeding cattle year round.”
The Prince Edward County farming operation includes 200 acres of deeded land, and another 300 acres of rented land. As well as they purchase 100 acres of standing hay each year. Of all the acres, about 175 acres are used for grazing cows and calves. Stored feed for the cattle includes dry hay, baleage (high moisture hay bales that are wrapped in 500 foot-long plastic tubes), corn silage stored in 10 foot diameter, 200 foot long silage bags as well as grain corn.
That plastic obviously is a key part in storing the feed supply for the year, “but there was no practical way to deal with the used material,” says Leavitt. He connected with a local plastic manufacturing company in Belleville and while they weren’t involved in recycling, it led Leavitt to connect with a recycling operation in London, ON. They were willing to take clean agricultural plastic collected from within a three-hour driving radius of their plant, if it could be assembled and transported economically. (And clean doesn’t mean the plastic needs to be washed. Once it is removed from the bale or the silage bag is empty, the plastic needs to dry, so any loose particles of forage will fall off. As long as it is dry it can be compacted.)
That led Leavitt to design the Pac-It compactor as way to bundle the plastic in a neat, dense package that could be economically trucked. Each bundle from the compactor weighs about 1,000 pounds. As other farmers in the Quinte Region got involved they too began to bundle agricultural plastic.
The farmers bring their bundled plastic to the Leavitt farm. When there are enough bundles to warrant a load to the recycler, Leavitt brings the bundles to the warehouse of a local agricultural plastic retailer, where they are loaded onto the recycler’s trailer.
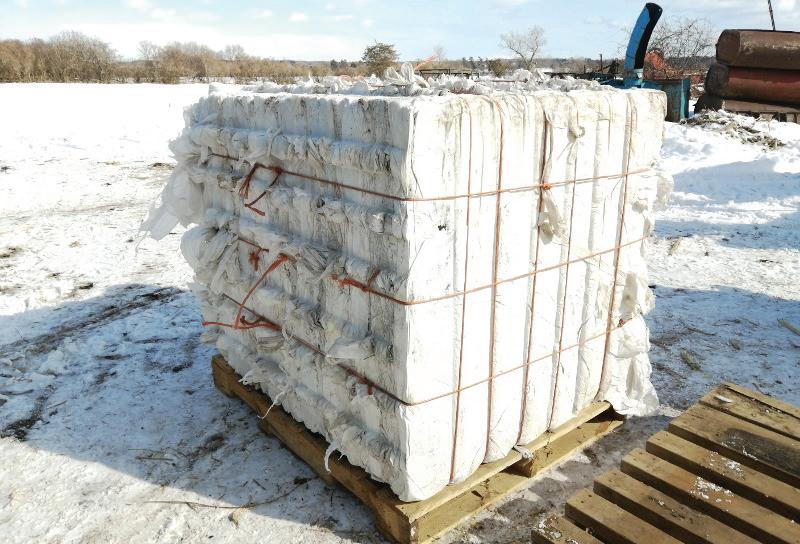
“A 53-foot trailer can carry about 45,000 pounds which represents about 45 bundles of plastic,” says Leavitt.
“Each bundle fits on a pallet. When the truck arrives, we have volunteers helping out and it takes about an hour to get the truck loaded and then it is on its way.”
Over the years, Leavitt says the plastic recycling system to date has sent about 225,000 pounds of plastic to the recycling plant, and of that about 30,000 pounds has come from the Leavitt farm.
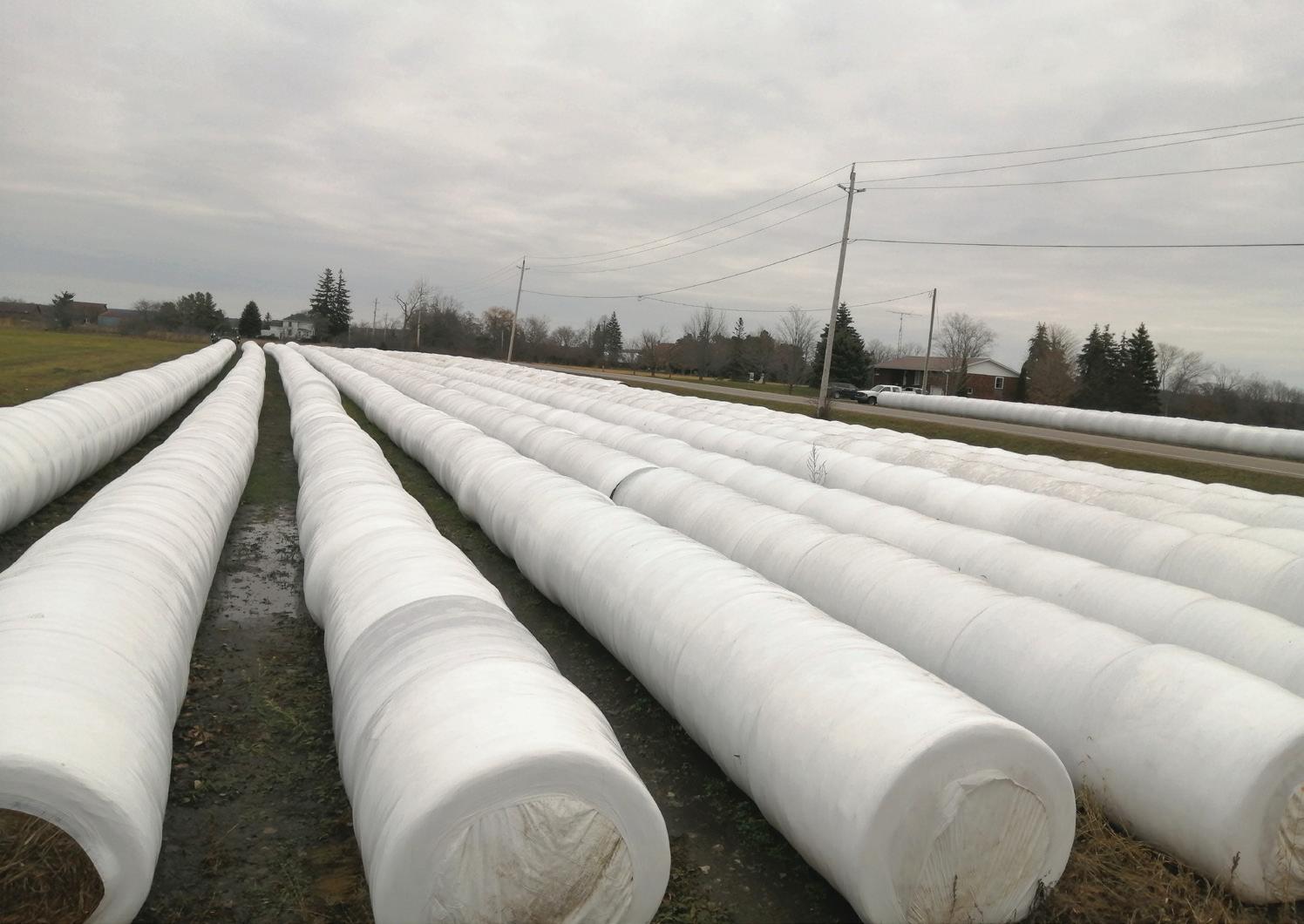
He is always interested in getting the recycling message out to other producers. He has made presentations at several events including the London Farm Show, Ontario Forage Council, Beef Farmers of Ontario and Peterborough Soil and Crop Association.
He has also been involved with and received support from CleanFARMS, a not-for-profit industry stewardship organization led by the plant science industry. CleanFARMS is committed to environmental responsibility through the proper management of agricultural waste products such as empty agricultural pesticide and fertilizer containers, grain bags, seed and pesticide bags and other ag plastics.
“In order to be able to recycle and repurpose plastics in a cost-effective and efficient manner, farmers, local municipalities, other levels of government, and industry players must work together to set up a recycling system on a local or regional basis,” says Leavitt. “This can be a challenge, since farmers tend to be naturally independent, so it will require a change in thinking. They need to understand it only takes a small investment of their time and resources to handle plastics correctly.
“It is great to see this plastic being recycled and repurposed into other plastic products, but I believe where the idea will really gain traction is when the used plastic is converted to biofuel, and that can be done,” he says.
“Then we will have a system that goes full circle. The used plastic is made into biofuel, the biofuel is used to power the farm tractor that is putting up feed into plastic bags and tubes, and then that used plastic will be used again to produce more biofuel. It will be one more way to reduce the carbon footprint of agriculture.”
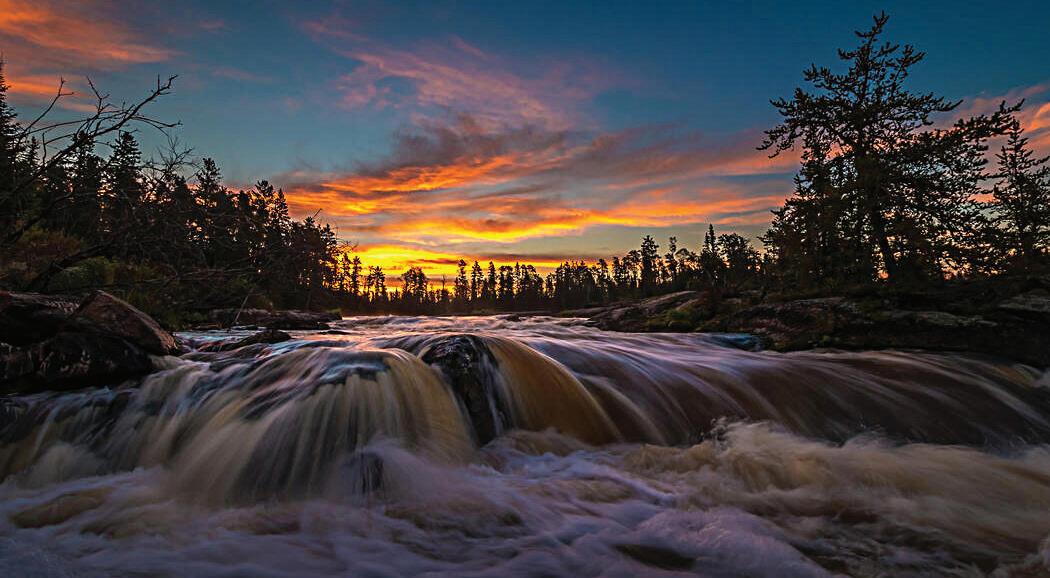
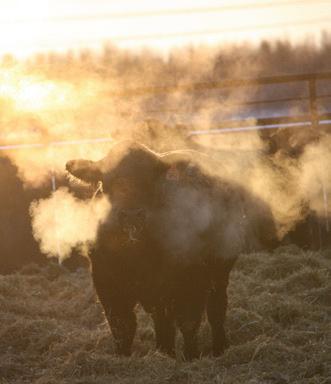
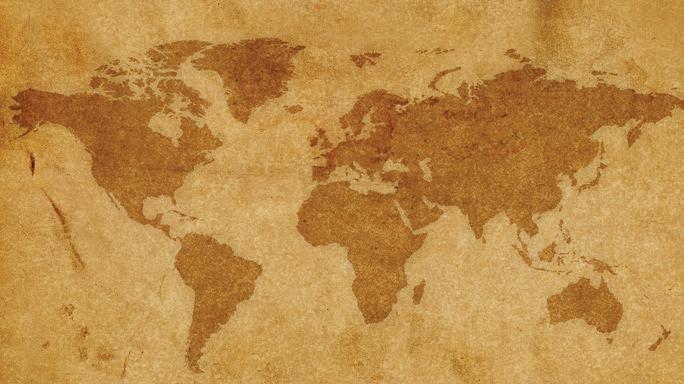
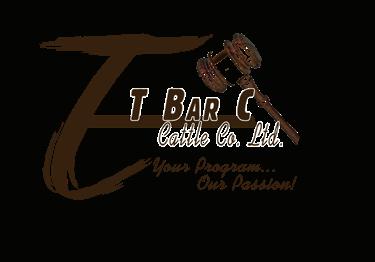
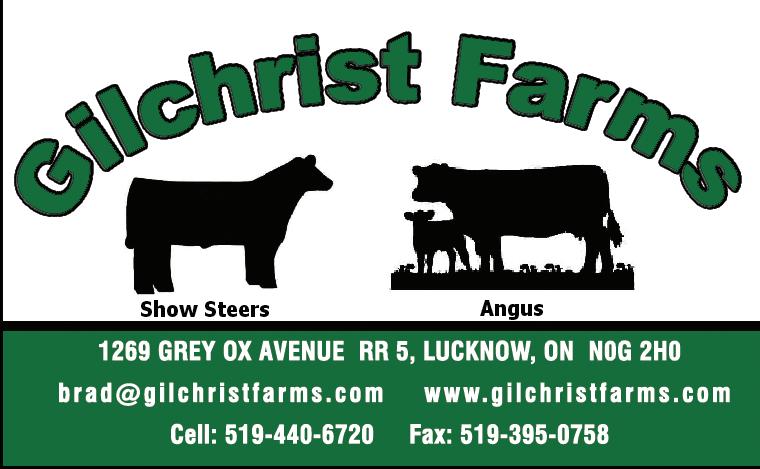
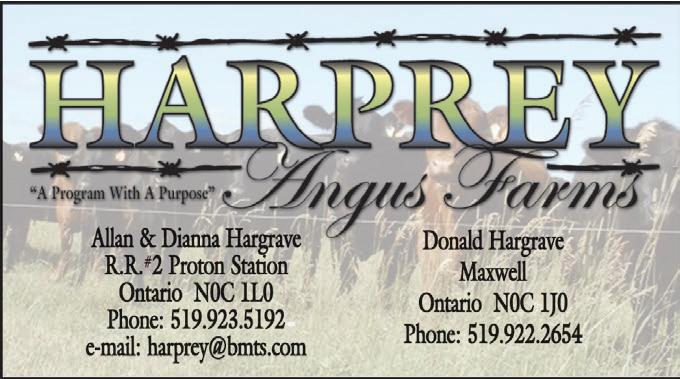
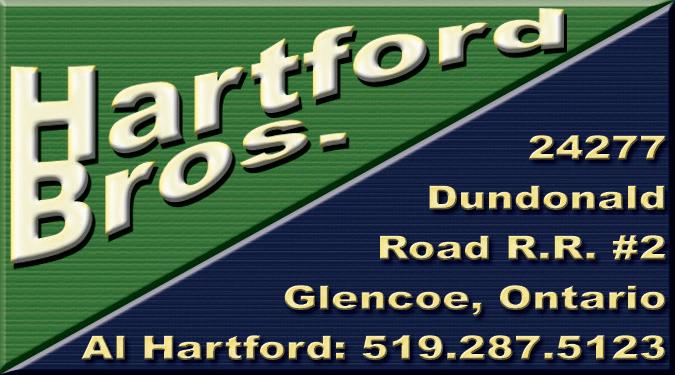
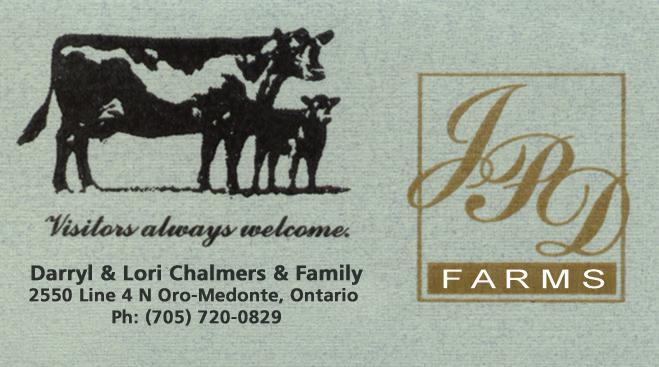
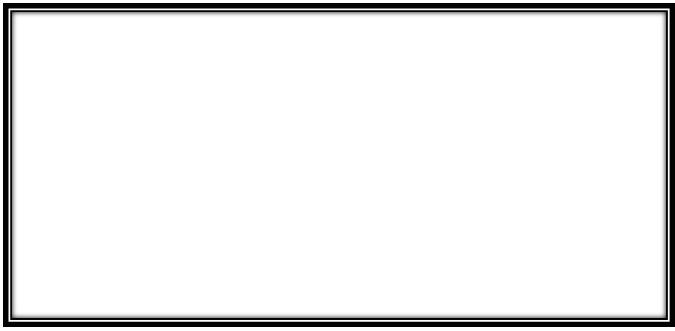
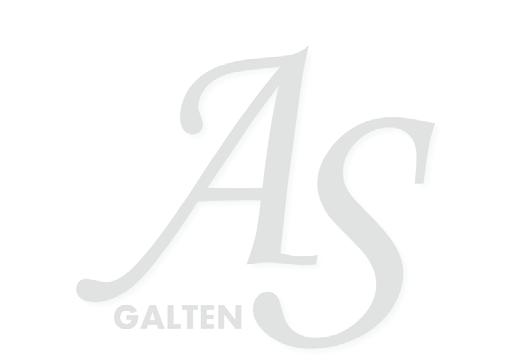
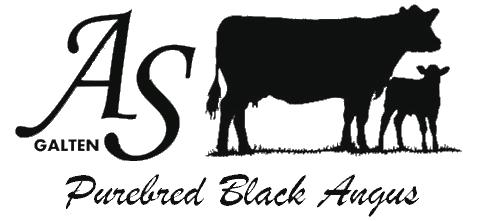
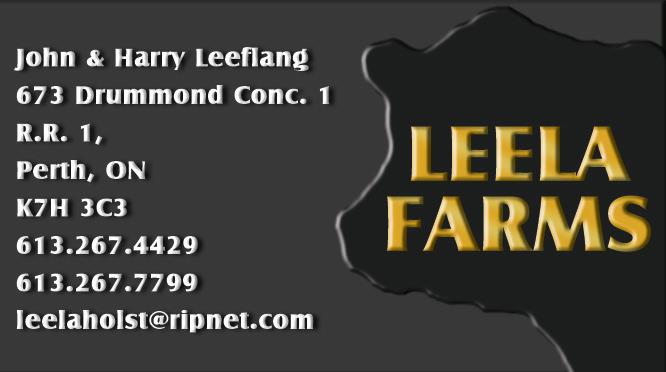

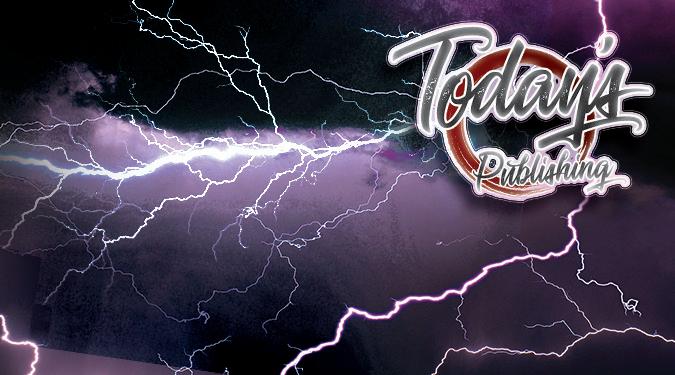
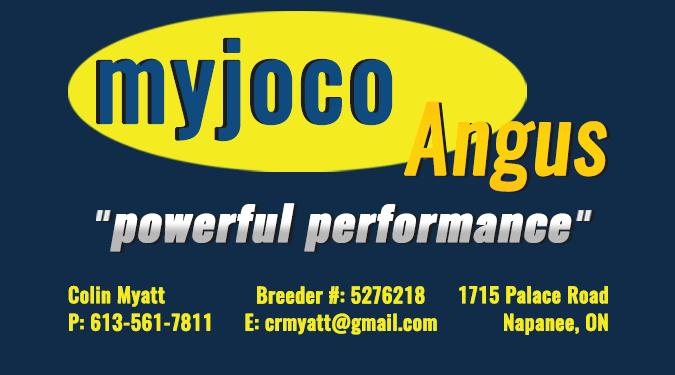
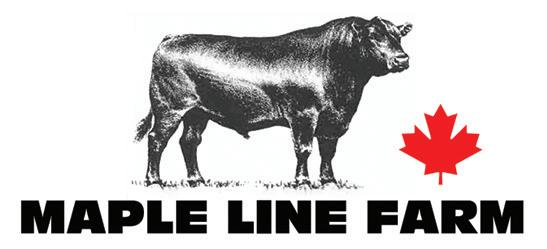
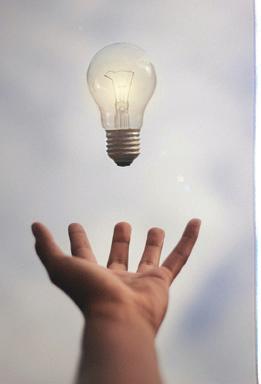


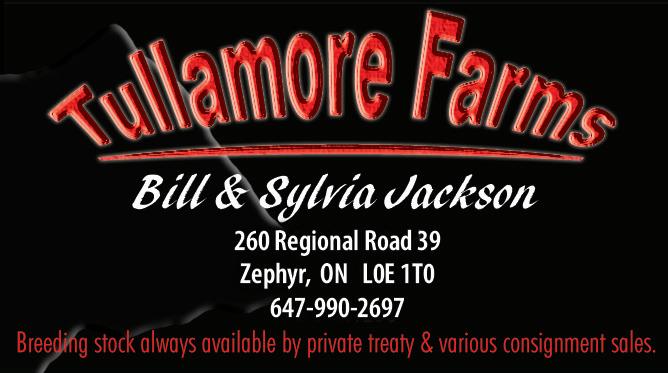
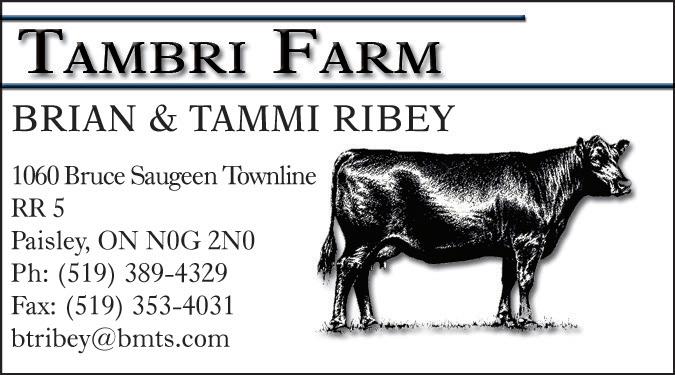
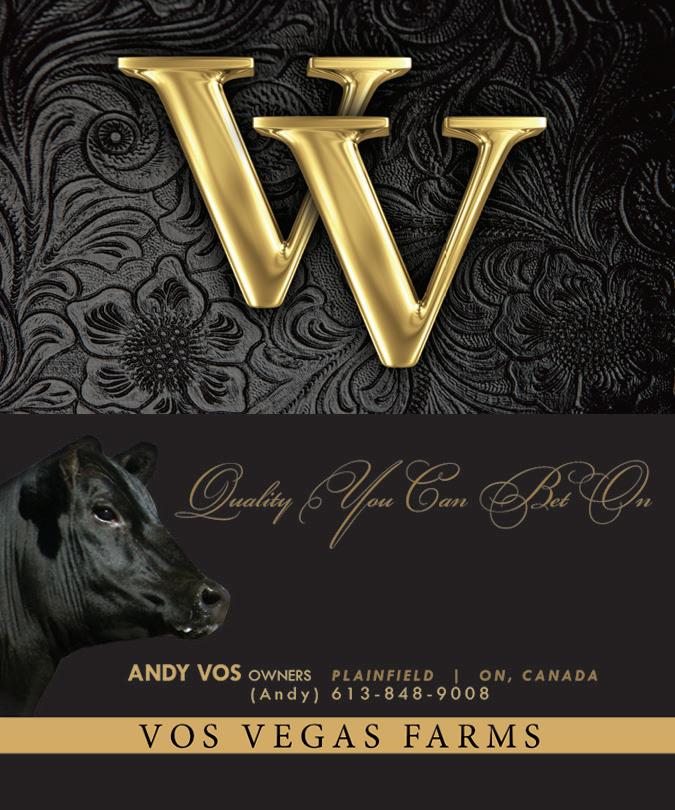
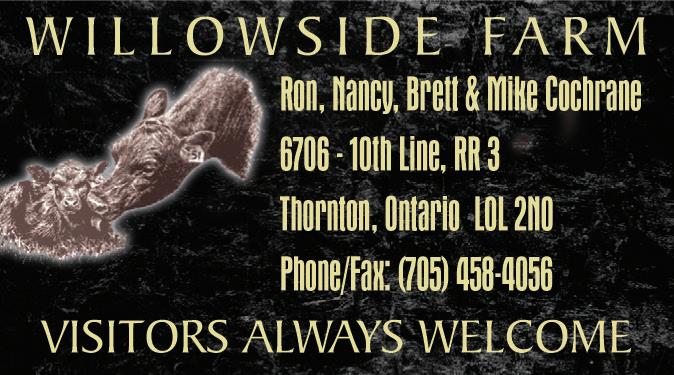

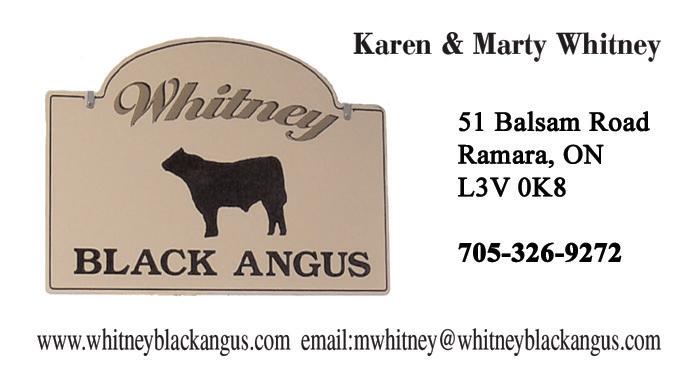
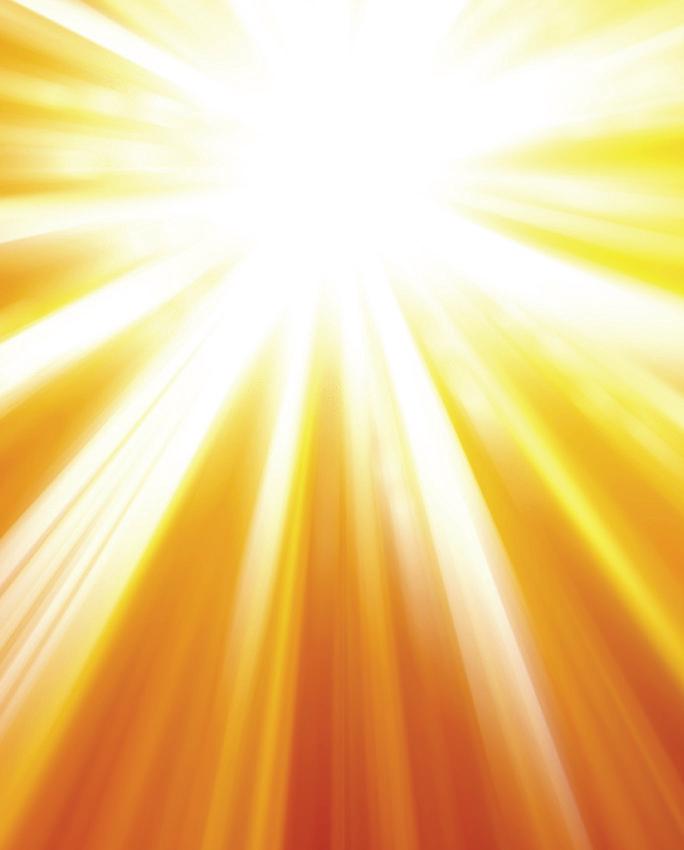
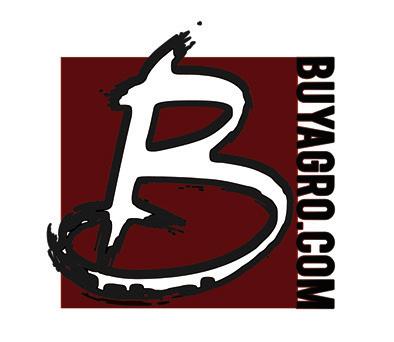
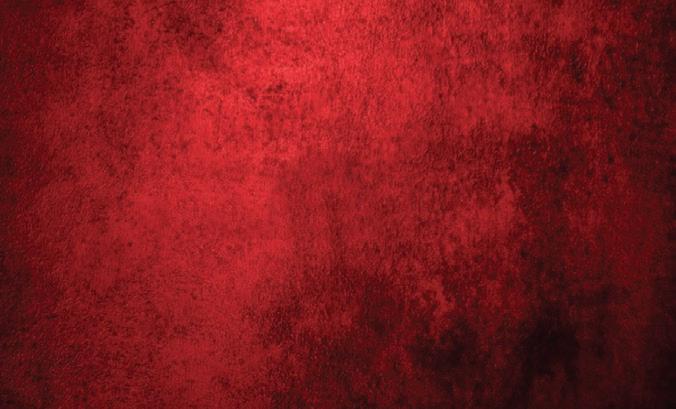
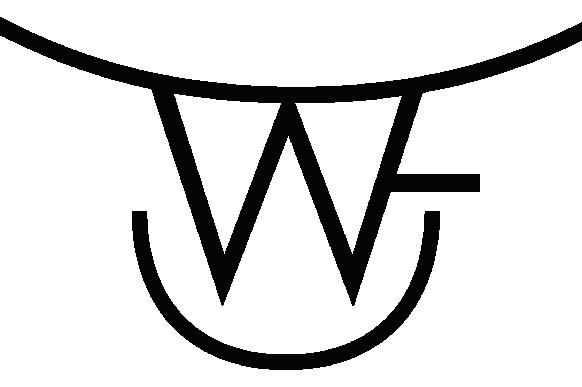

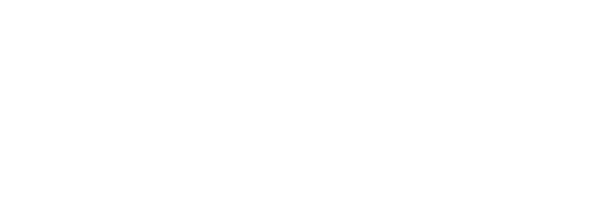
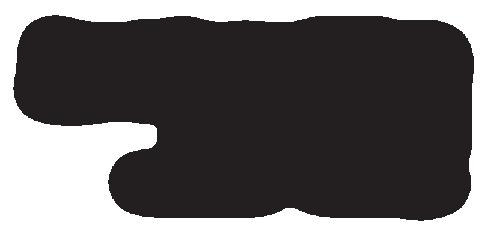

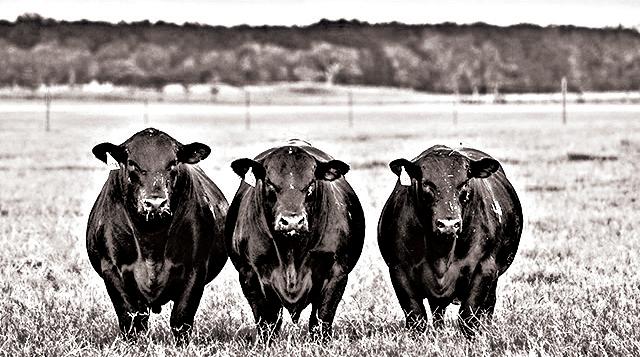

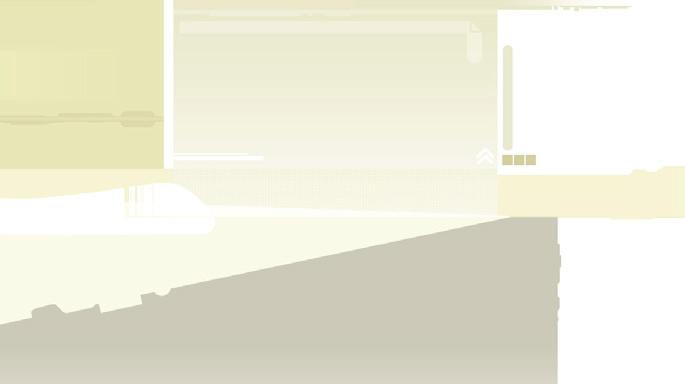