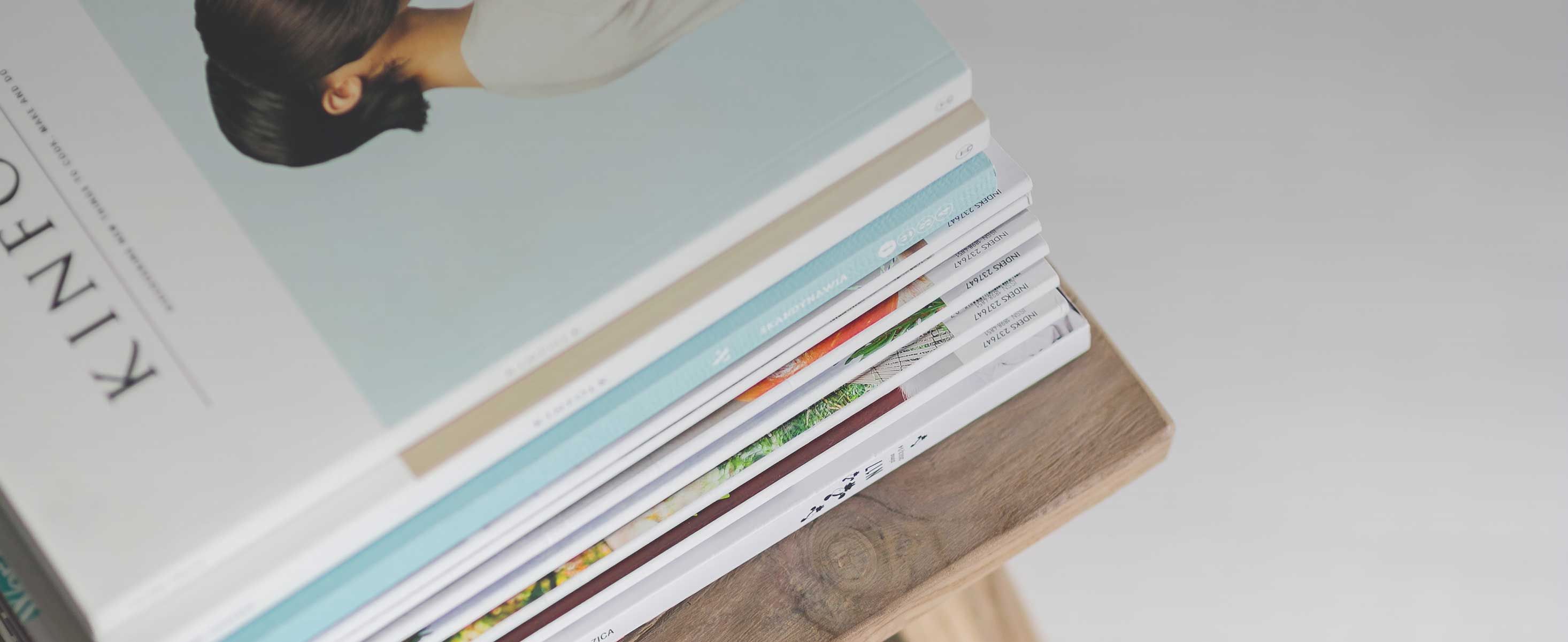
2 minute read
Additive Inspiration
The Wednesday evening social at this year’s AMUG Conference was the same as any other, until it wasn’t.
We were nearing the end of a week full of conferencing, networking, and learning. Two out of three keynotes had been delivered, ten DINO Awards handed out, and its famous o site event successfully kept secret. Most attendees were leaning into the steampunk aesthetic, gambling for ra e tickets, and raising the roof with some karaoke classics.
Except for the 50 or so people huddled around a flat screen TV. These people had room for more. They waited patiently. First for a passing boat to get out of the way, and then for some high winds to die down. They searched for the best vantage point, they reached for their phones, and they counted down from ten, nine, eight, seven.
At one, there was a pause. A burst of flame obscured the view momentarily. And then the place erupted. Some hugged, some cheered, some profaned. Relativity Space had done what some in attendance thought wouldn’t be done, maybe even couldn’t.
The first rocket made up nearly entirely of 3D printed parts passed Max-Q – the point in the launch sequence where a rocket experiences maximum dynamic pressure – and the 100km Karman line. Though it didn’t quite reach orbit, it certainly had lift o , and the engineers, designers and operators watching on were jubilant.
3D printing was proven to be viable for what might be the most inspiring application of the technology to date.
In our aerospace-focused issue, we unfortunately don’t have more from Relativity – they’ve been kinda busy – but we do explore 3D printing in outer space through the additive manufacture of a satellite set to launch on the SpaceX Transporter-9 later this year (P15) and the use of the technology for satellite sensors (P17). At 30,000 feet, meanwhile, we dig deep into GE Aerospace's AM journey, application by application (P12), and Cranfield University present findings from a feasability study centered on aircraft landing gear (P9).
Bringing us back down to earth are five industry experts who give their perspectives on one of AM’s most burning issues: cost per part (P18). But there are also reasons to be cheerful. We have tooling successes from Westec Plastics (P45), insights from AM business leads at Renishaw (P27) and Endeavor 3D (P21), and we hear from a selection of metal AM newcomers who are poised to deliver 3D printing at scale with their proprietary technologies and parts as a service business models (P39).
Closing our third issue of the year, we take a look at what’s to come at this year’s RAPID + TCT event in Chicago (P46), which has a jam-packed conference agenda and is set to have an equally busy show floor. We’ve gathered the highlights, and we look forward to seeing you there for more additive inspiration.