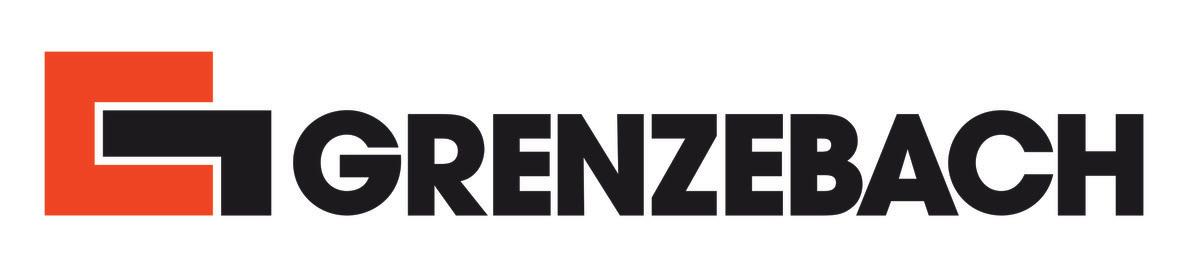
4 minute read
With automation solutions in additive manufacturing to series production
The additive manufacturing (AM) market is growing. According to Ampower (www. ampower.eu), the global market for AM raised continuously and will reach 20 billion euros in 2026. Ampower still sees significant productivity gains in new disruptive AM technologies based on powder materials in the polymer area. Combined with automated process steps, this has the potential to make the technology suitable for mass production across all industries in the next years.
Oliver Elbert, Head of Additive Manufacturing at Grenzebach Group, a holistic system provider in the automation of additive manufacturing, reveals how you can open the door for a future-proof and productive series production in the field of AM by automating.
WHICH PROCESS STEPS CAN BE AUTOMATED?
Elbert: All process steps – pre, in, and post – can be automated. Meanwhile, the in-process is often fully automated. In contrast, the post and pre-processes are partly or almost not at all automated. Unfortunately, independent process steps or components such as transport or software solutions show the same picture.
But companies that start right here can make their production fit for series production and save up a great part of their manufacturing costs. Why? Upstream and downstream production steps have significantly shorter cycle times than the production time. By intelligently networking and synchronizing all process steps with suitable, state-of-the-art transport, software and printing solutions, there will be no idle time anymore. Companies boost their productivity by reducing downtimes to a minimum due to faster and outsourced processes like cooling, unpacking, and setup. At the same time, they minimize physical strain for the machine operators because tasks are focused on essential and demanding operating steps.
WHAT ARE THE MAIN REASONS FOR THE AUTOMATION OF ADDITIVE MANUFACTURING?
Elbert: There are three key reasons:
1. Lower cost per part: by crosslinking the production steps, you enhance productivity due to higher equipment workloads along the process chain and reduce manual e ort. This decreases the cost per part significantly. Automation solutions pay for themselves within a short time.
2. Active occupational health and safety protection: the risks of dust exposure or hazards from hot objects are reduced to a minimum when automated guided vehicles (AGV) with suitable sealed transport solutions network the working stations or automated AM solutions print the parts. As a result, companies can cut down the costs for technical protective measures and personal protective equipment.
3. Repeatability and reproducibility: the process steps are fully controlled and consistently uniform. By always following the same procedure for each process step, unwelcomed influence on the often still sensitive manufacturing process is minimized, and the product quality rises.
WHAT CHALLENGES CAN ARISE IN THE AUTOMATION OF AM PROCESSES?
Elbert: Smooth automation stands and falls with the right provider of automation solutions. Therefore, you need a reliable partner that helps to find the best solution for your requirements and AM processes – along the whole process chain.
Together with leading manufacturers of industrial 3D printers and post-processing equipment, Grenzebach, for example, develops and o ers state-of-the-art solutions: from single machines to holistic automation concepts for de-powdering, transport, bin picking, and exchange. Our automation concepts mechanically, electrically, and digitally link network systems and foster optimal process flow. Grenzebach’s automation solutions can be combined with di erent printing technologies – both new and existing, metal and polymer. In addition, Grenzebach also supplies comprehensive service o ers. As journey partner of their customers, Grenzebach will support throughout all phases of the system’s lifecycle, always aiming to enhance production e ciency. The company makes sure that the invested technology stays in top shape.
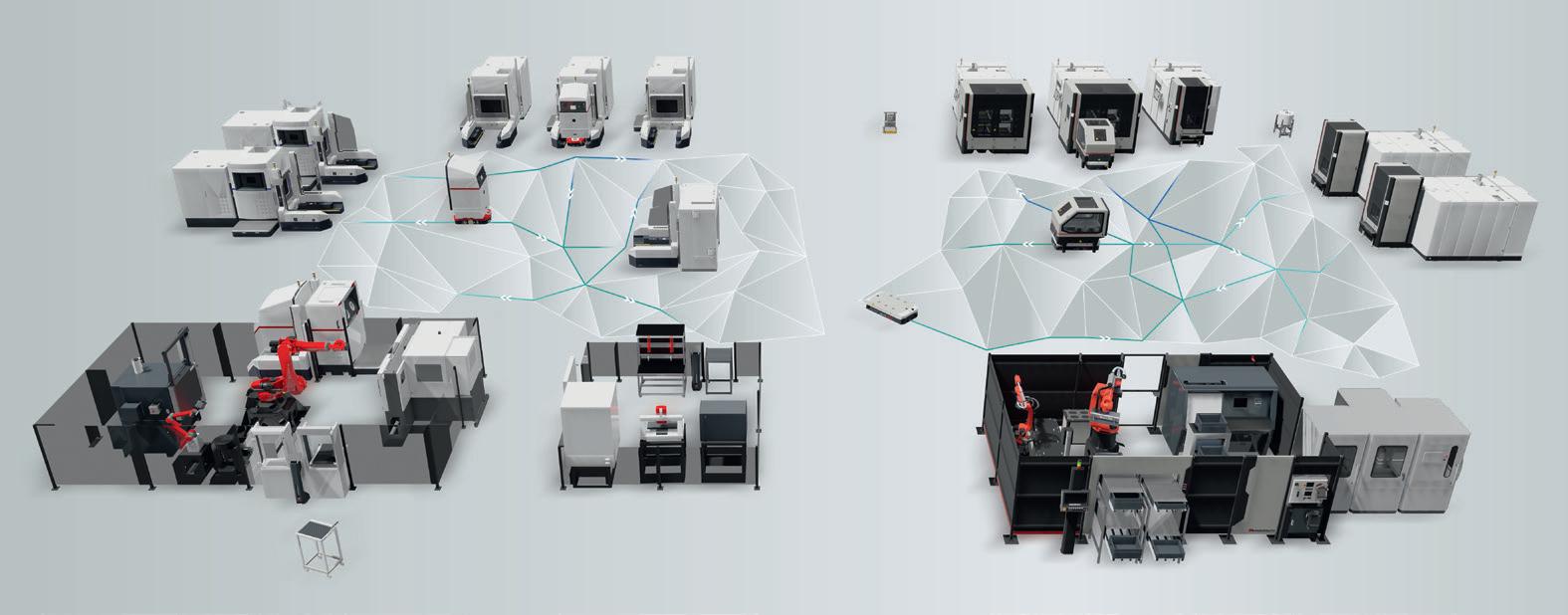
PHOTOCENTRIC #1715
Visitors can see the Photocentric workhorse LC Magna and opensource LC Opus 3D printers, both tried and tested for applications in dental, model making, automotive, medical and engineering industries. There will also be a selection of UV and daylight durable, flexible and rigid resins alongside the co-developed BASF Forward AM Ultracur3D EPD Daylight product line. During the RAPID + TCT Conference, delegates can hear Merit3D’s Spencer Loveless and Photocentric’s Sally Tipping talking about how to scale up production from 50 to 1,000,000 parts with AM.
TRUMPF #4218
TRUMPF introduces its redesigned TruPrint 1000 for additive series production to the North American market. The printer features two 200watt lasers and a multiplate option, which allow users to run multiple builds by automatically exchanging the build plate. Users can stack up to four build plates on top of each other and the system prints components on them one after the other. A new compact design means the TruPrint 1000 only uses half of the floor space needed by previous editions and can pass easily through a standard door.
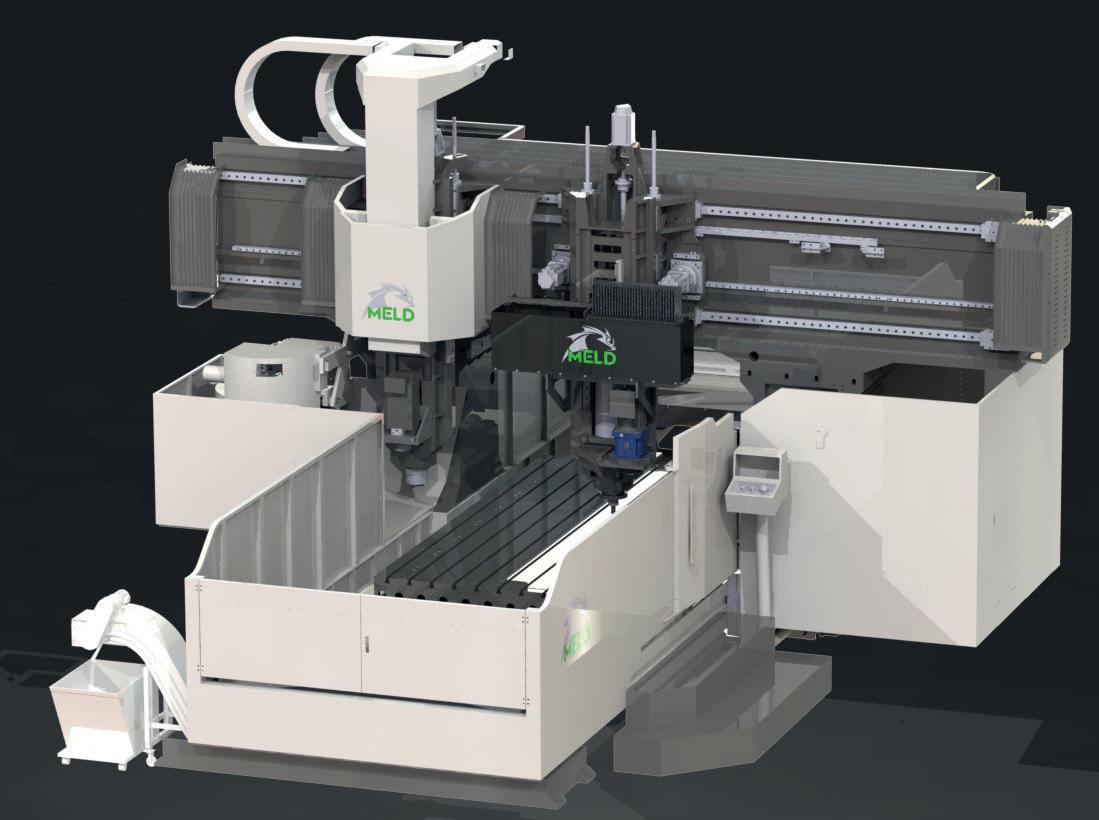
MELD MANUFACTURING #4641
MELD o ers
3D printing and hybrid machines for printing metal components using MELD’s patented no-melt, open-atmosphere technology for large metal parts. It yields near-net shape, isotropic, fully dense parts with low residual stresses. Material is deposited at least 10x faster than other AM processes. MELD’s newest machine 3PO combines additive and subtractive technology into one hybrid machine. It boasts a print capacity of 157.5” x 106.0” x 39.4”.
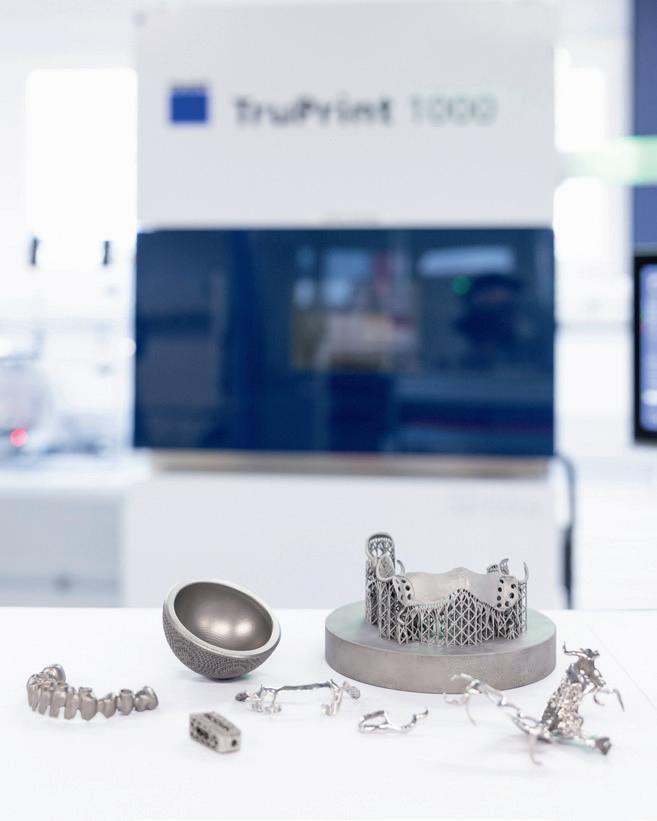
AMERICA MAKES #1851
TCT is proud to be partnering with America Makes as its Game Day returns to RAPID + TCT for 2023. Together, we’re looking forward to showcasing the most exciting additive manufacturing applications and technology developments through daily broadcasts live from the show floor in Chicago.
Each day will kick o with the SME leadership team followed by conversations with industry representatives from end-users and technology providers such as General Lattice, SAE, and more.
GOENGINEER #5232
Visitors will have a first chance to see the Onulis WRAPCure in person. This latest innovation pairs axial 3D printing and a post-cure apparatus in one piece of equipment. If you haven’t been able to see the J55 from Stratasys in action, now’s your chance. Take a spin on this fullpantone verified solution for ‘real’ experience — and determine for yourself what is real and what’s 3D printed. You can also meet with a team of experts with your current development issues and application needs for additional support.
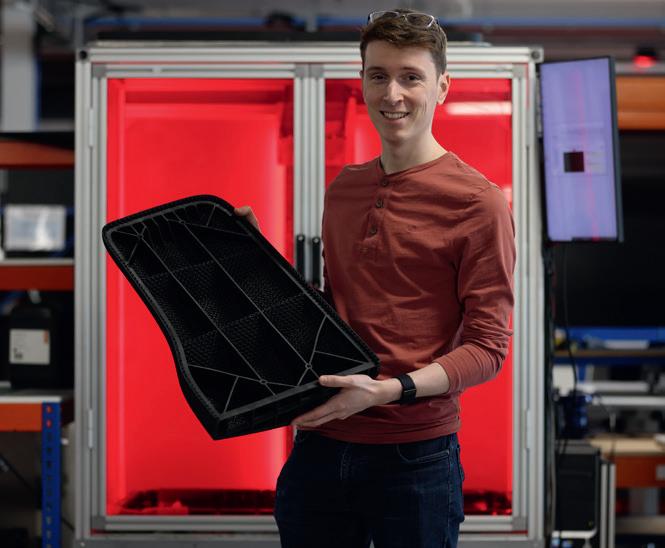
STRATASYS #5012
Visitors can see how successfully scaling additive manufacturing goes beyond the printer with high-performance polymers and manufacturing software. Stratasys also has multiple speaking engagements including a welcome by Dr. Yoav Zeif on Tuesday and three in-depth sessions on how Roush revs up production with additive manufacturing to in depth overview of our new software, solving major challenges through AM software, and bridging the skills gap by implementing 3D printing into your curriculum and training.
SLM SOLUTIONS #4018
SLM Solutions will focus on empowering mission-critical operations, leveraging the ability to lightweight, produce highly complex, and on-demand components for aerospace, aviation, defense, automotive, and energy. Stop by the booth to see a 1.5m combustion chamber from the newly launched NXG XII 600E.
Since 1945, NSL Analytical has been trusted to verify the highest standards of quality, performance and safety. NSL supports innovation by testing metal powders, condensate the Additive Manufacturing industry.
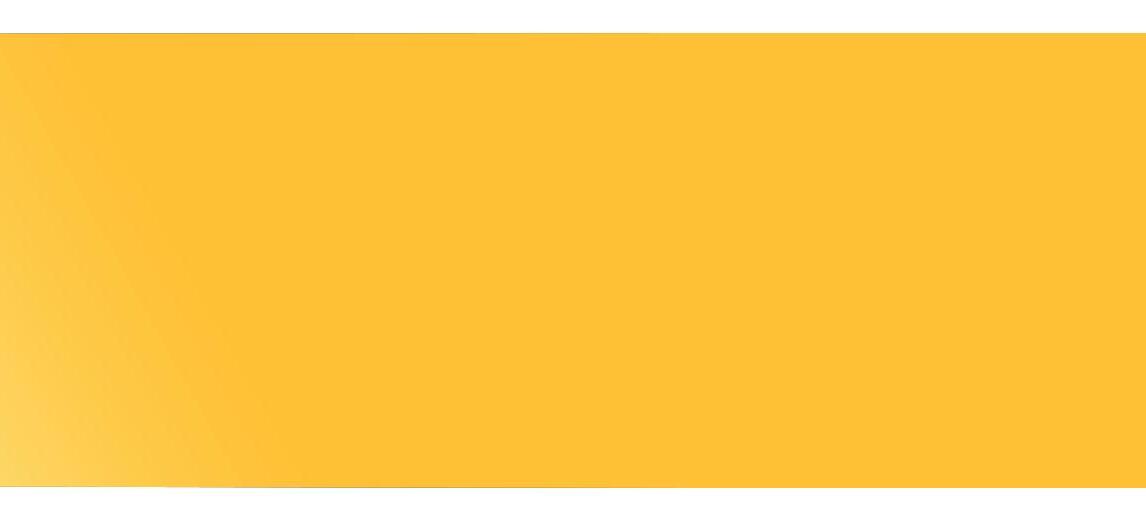
