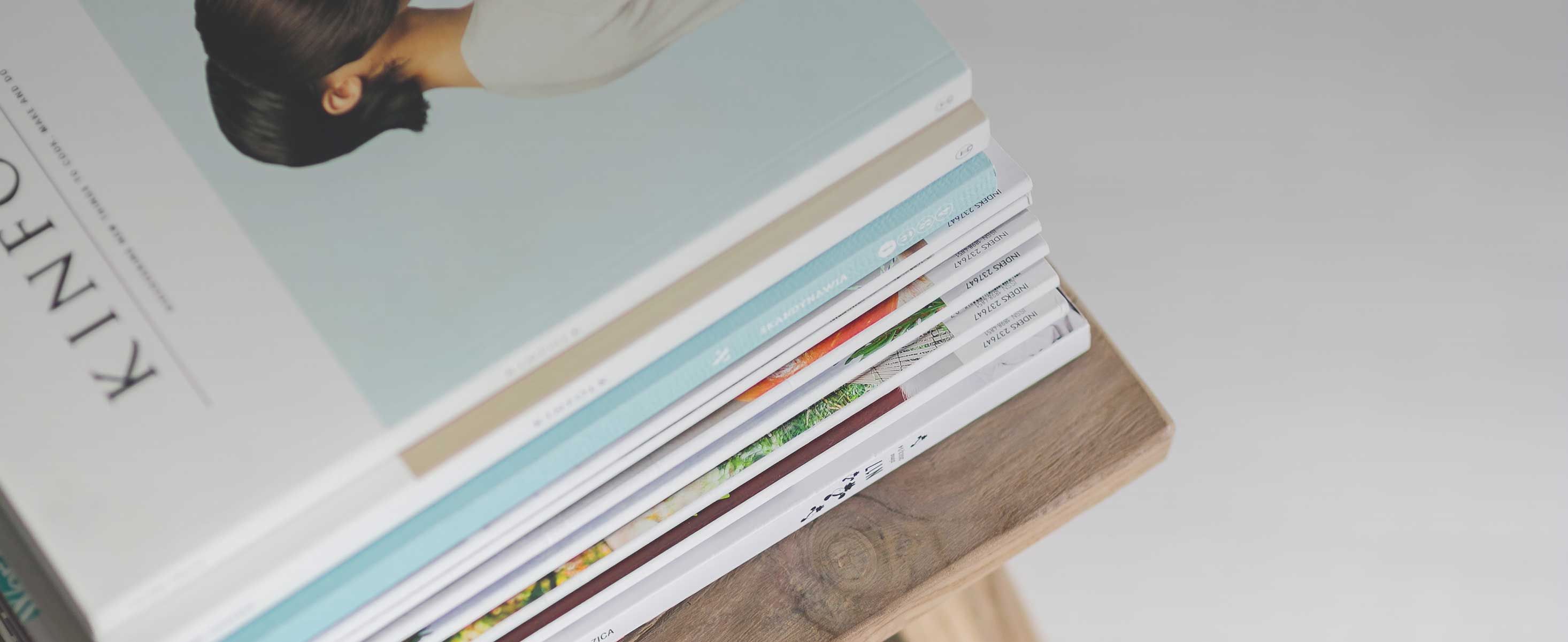
2 minute read
Paging Dr. O
This story isn’t about Gholami, however, despite his contributions to 3DI’s work. It’s about saving children’s lives, something the lab assists with in numerous ways. For instance, the team might print a replica of a patient’s heart or lungs for surgical planning. That same model could also be used to explain the upcoming procedure to family members, train medical students, and evaluate novel instruments or techniques, all of which enhances the medical community’s capabilities and improves patient outcome.
Kip Hanson
Contributing Editor
Brains, bones, blood vessels—all these and more can be imaged via computed tomography (CT) scanning or magnetic resonance imaging (MRI). The resulting “slices” are then reconstructed into a digital model, and the results are sent to one of half a dozen 3D printers at the 3DI Lab. These include an HP Jet Fusion 580 Color 3D printer, a J750 Digital Anatomy printer (also color) and an F370 FDM machine, both from Stratasys, and a few vat photopolymerization (SL) printers from FormLabs and 3D Systems.
Olga Ivanova has 3D-printed plenty of interesting parts during her time in manufacturing. Rocket nozzles. Turbine blades and impellers. Neonatal tracheostomy tubes. There are more, which we’ll get to in a moment, but to Star Wars fans, it’s the Static Dissipative Yoda that’s most intriguing.
Whatever AM technology was used, such 3D-printed organs and musculoskeletal reproductions do much more than bring physicians and patients up to speed—they also help identify potential fit and function roadblocks with surgical devices,
“We printed a bunch of Yoda and Groot (Guardians of the Galaxy) figurines for high school students who visited our facility recently,” said Ivanova, director of technology at Mechnano, an additive manufacturing materials
As noted earlier, Gholami has a background in video game development. He is therefore well equipped to develop an intuitive user interface that allows medical personnel to quickly review and analyze these 3D datasets. Provided the virtual models are sufficiently robust and accurate, this might eliminate the need to 3D print a physical replica, saving the hospital money and getting important information into practitioners’ hands more quickly.
Olga Ivanova Master networker RAPID + TCT Director of Technology Mechnano
The process of generating these models is called segmentation and reconstruction. It’s normally performed by a highly trained technologist or radiologist and saved in a Picture Archiving and Communication System (PACS) database.
developer near Phoenix. “It’s our way of getting young people interested in additive manufacturing.”
PACS databases are optimized for the radiologists and rarely consider the end user being a surgeon or interventionalist. Gholami—under Ryan’s direction—developed a 3D viewer that provides the radiologic results to the surgeon in an intuitive manner. The result is a streamlined surgical planning experience. Because Gholami “removed around 50 buttons” compared to legacy viewing tools, the software is easy enough for anyone to navigate.
Padawan Learning
She’s quick to point out that those educational giveaways were made of a gray-colored base resin, not the more expensive static dissipative material (which is black) that she spends much of each day working with—and yes, which she occasionally uses to print Yodas that are just as resistant to electrical charge as they are to the Dark Side of the Force.
Gholami also developed a tool that helps any hospital bring 3D datasets into their PACS environment. The no-cost software Media2DICOM takes an electronic folder filled with image or 3D files and compiles them into Digital Imaging and Communications in Medicine (DICOM) format, the industry standard. Media2DICOM also supports the addition of metadata that, according to Ryan, is not only a huge time saver but eliminates the possibility of errors.