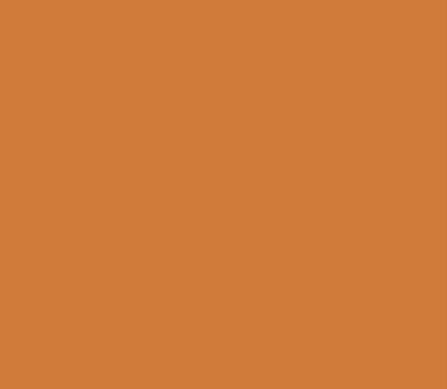
4 minute read
FIT FOR THE FUTURE
ADDMAN &
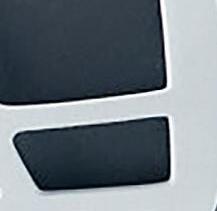

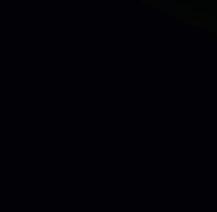
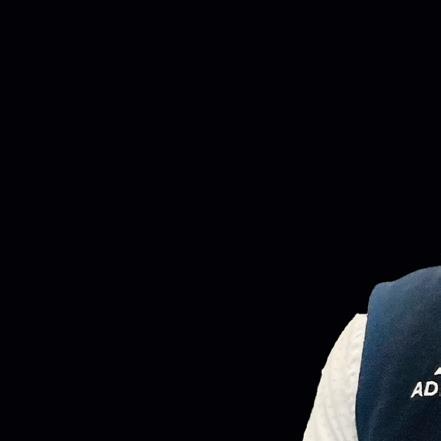
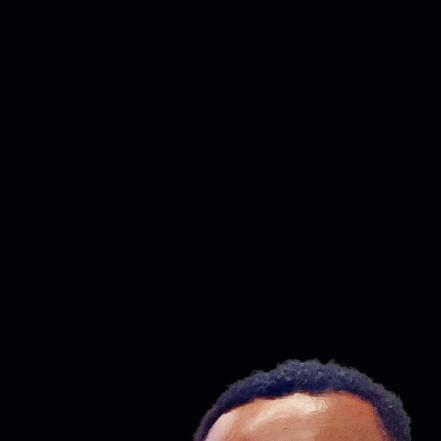
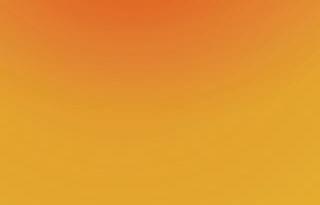
In January 2023, after more than 20 years operating as an independent company, Californian 3D printing service bureau Dinsmore was brought into the ADDMAN Group family, with the manufacturing solutions provider seeking to enhance its o ering with polymer additive manufacturing (AM) expertise.
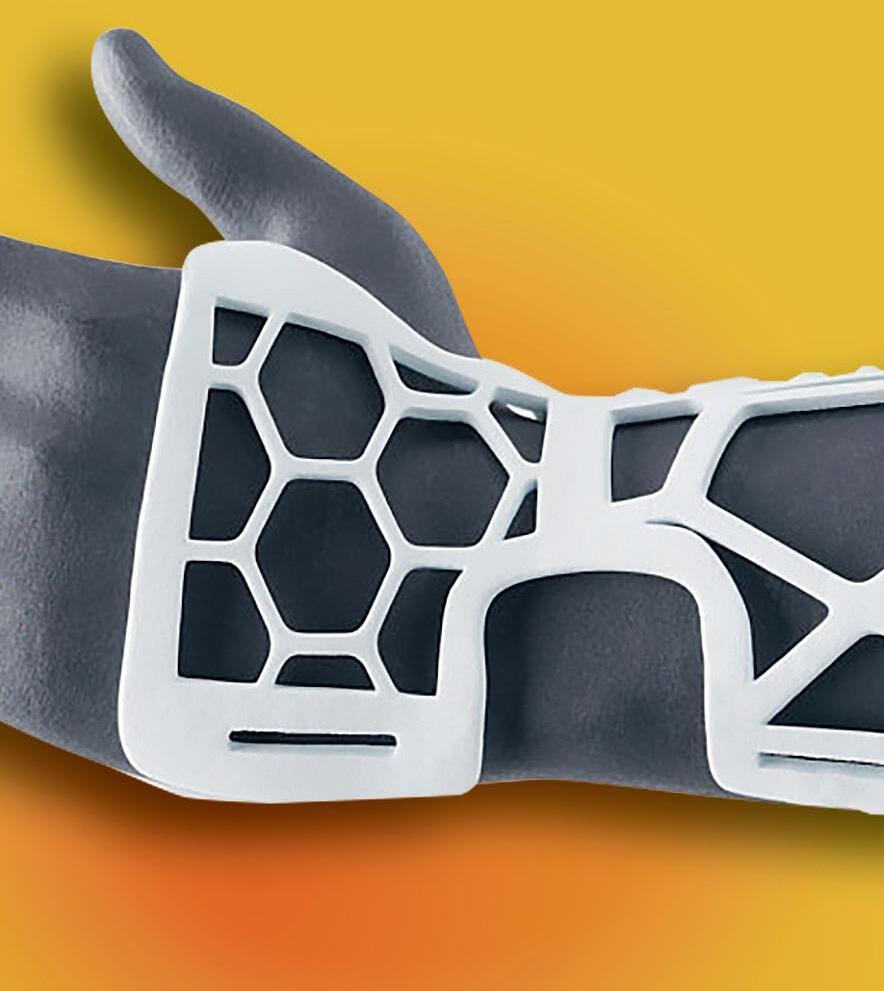
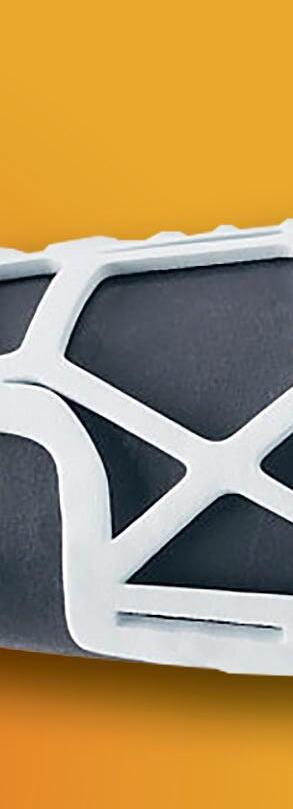

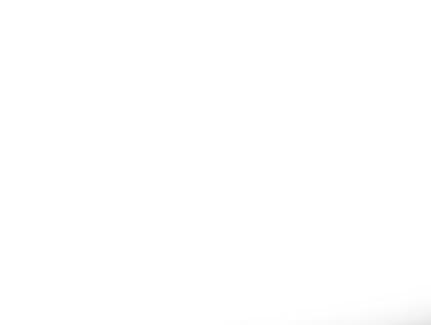
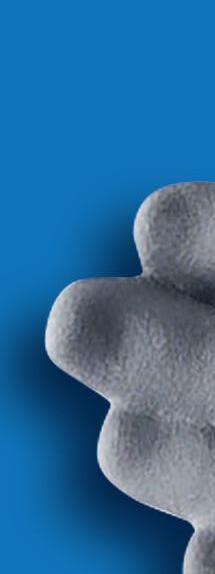
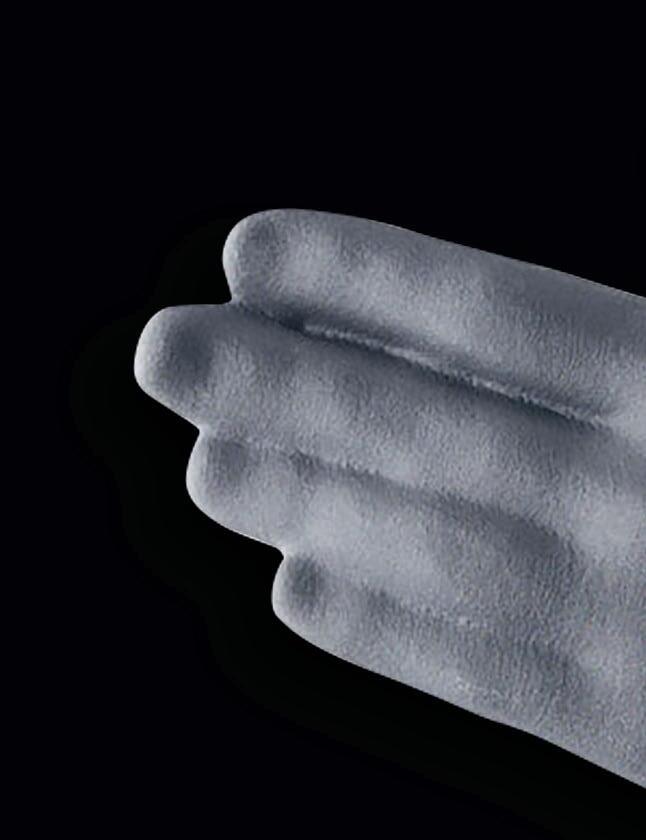
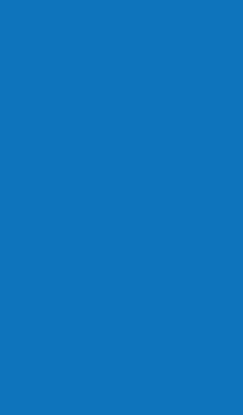
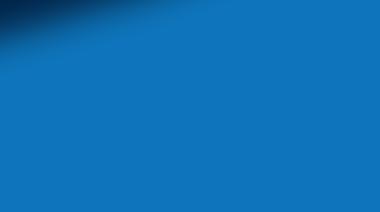
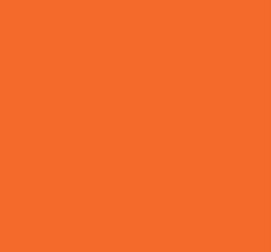
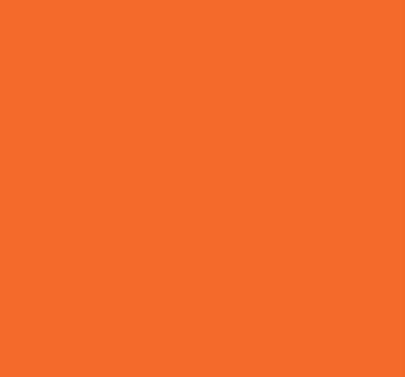
Dinsmore was integrated into ADDMAN to augment its existing polymer and metal additive capabilities, alongside the likes of HARBEC (injection molding), Stanley Engineering, Domaille Engineering, Tech Manufacturing (all CNC machining), and Castheon (metal AM).
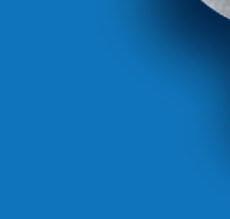
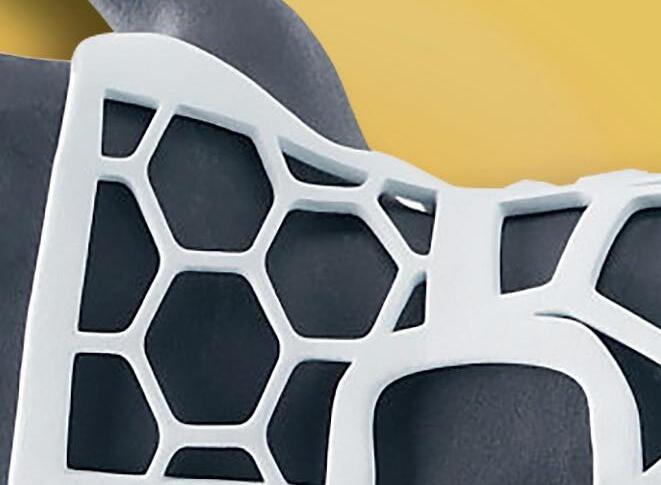
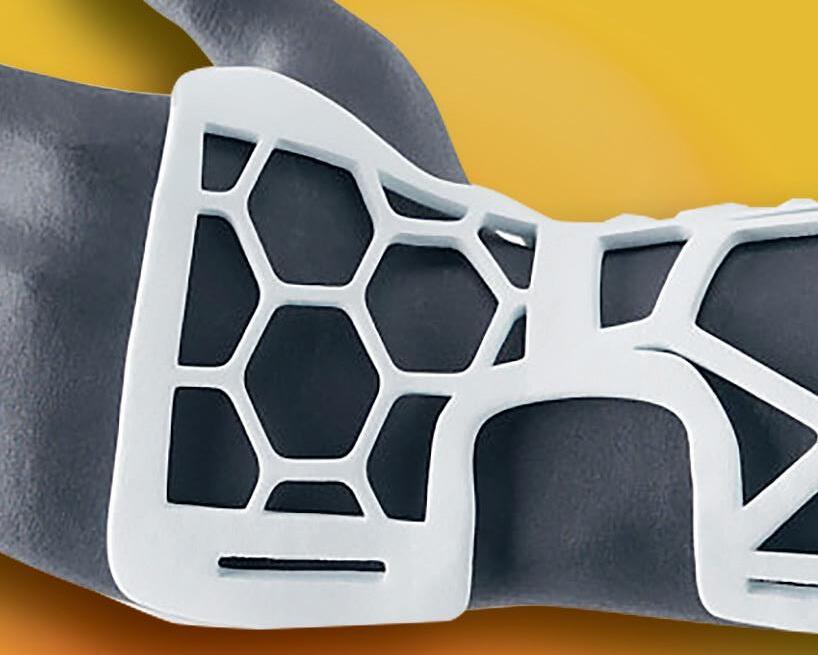
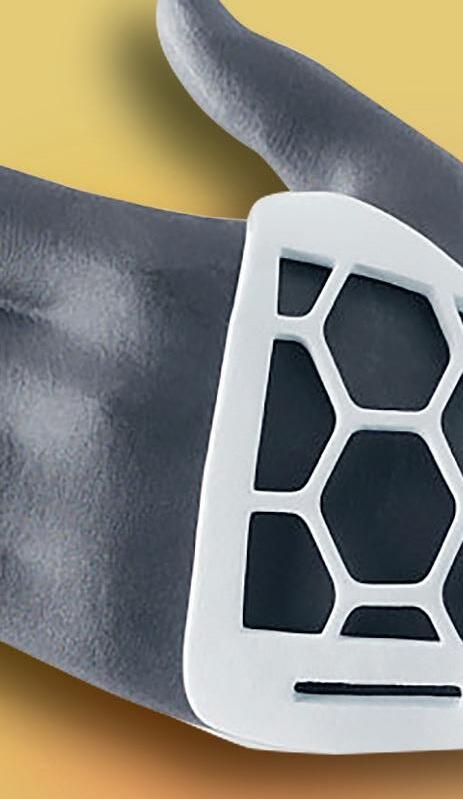
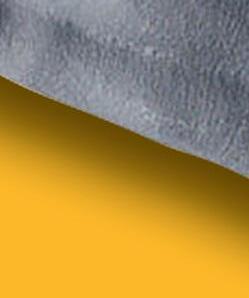
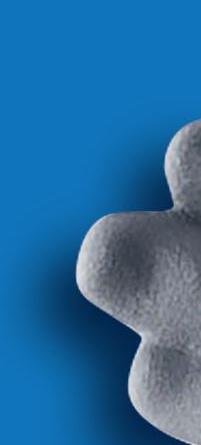
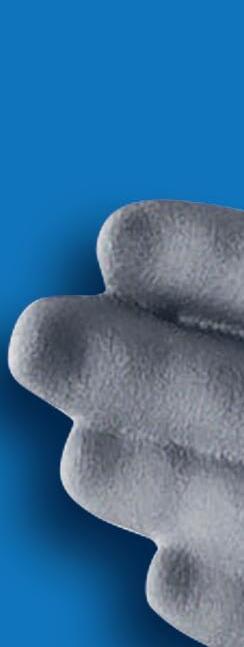
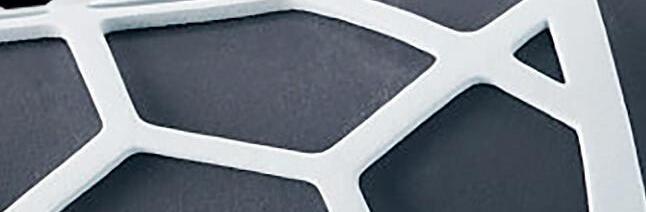
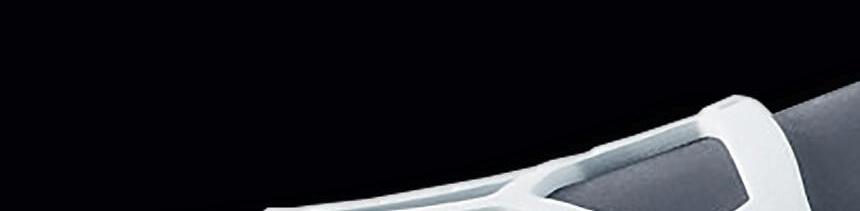
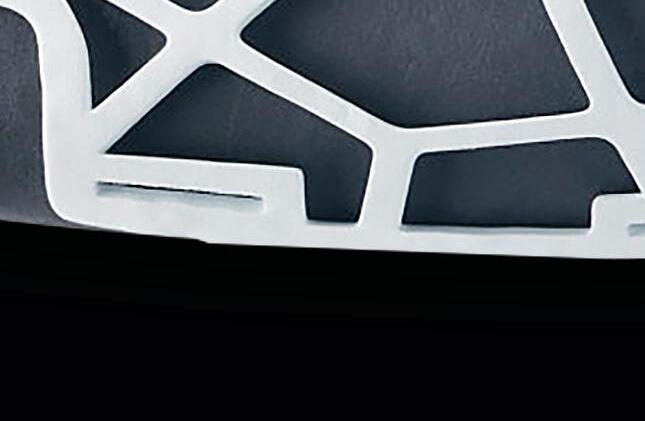
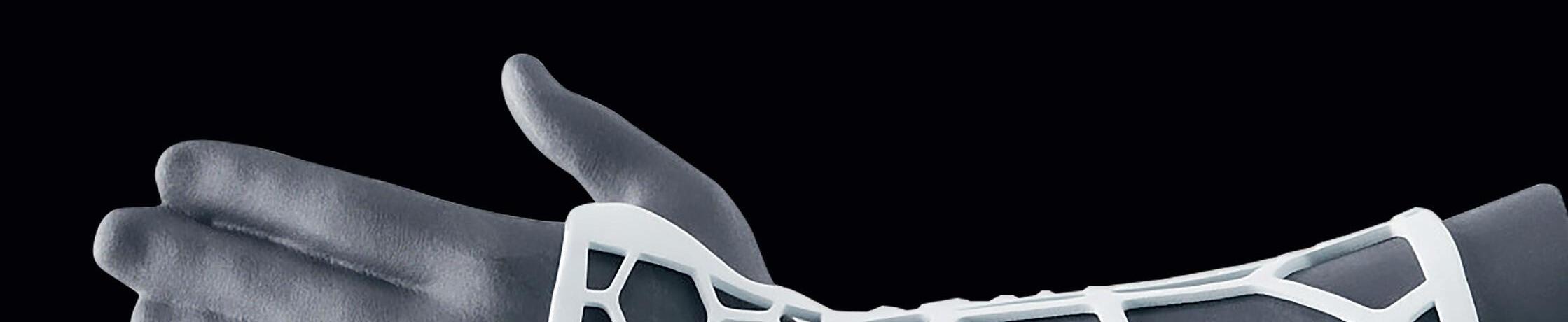
As the companies prepare to co-exhibit at RAPID + TCT in Chicago this May, Dinsmore founder Jay Dinsmore and ADDMAN CEO Joe Calmese discuss how the acquisition came about and what it means for Dinsmore moving forward.
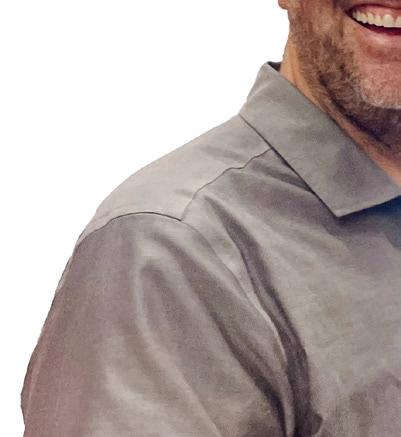
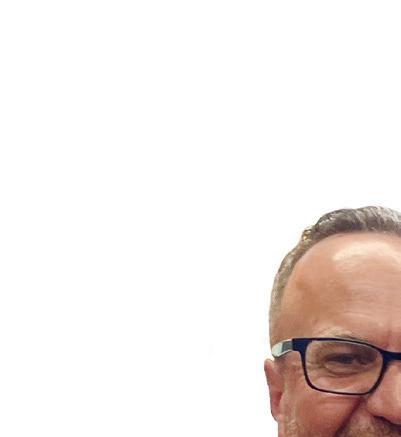
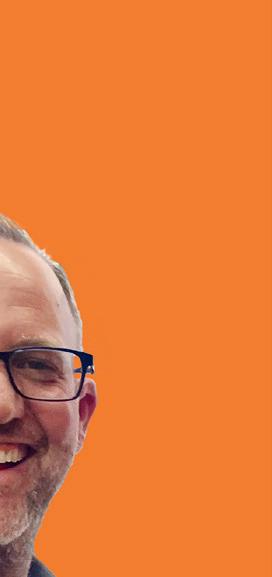
Can you tell us how ADDMAN’s acquisition of Dinsmore came about and why it made sense for both companies?
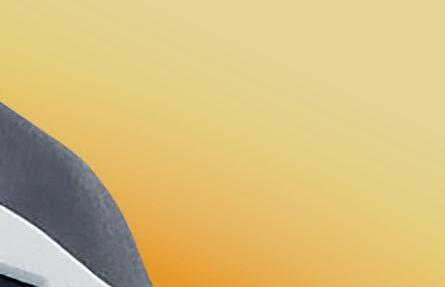
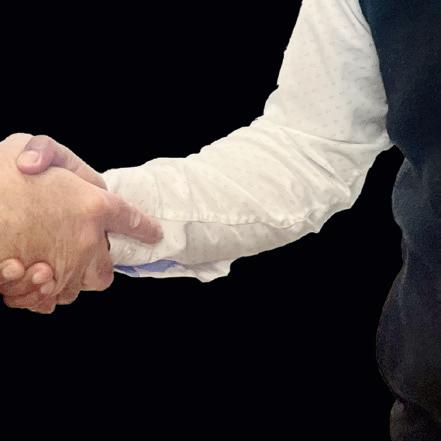
Dinsmore came about and why it made sense
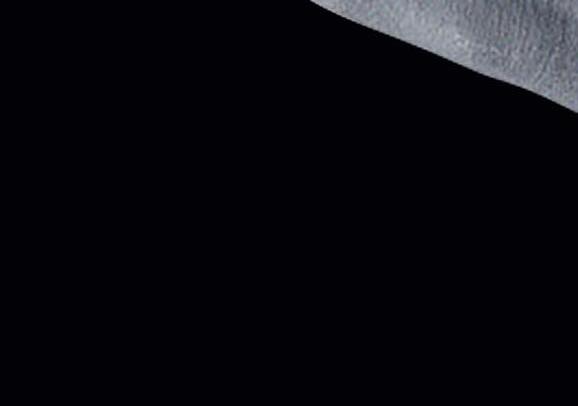
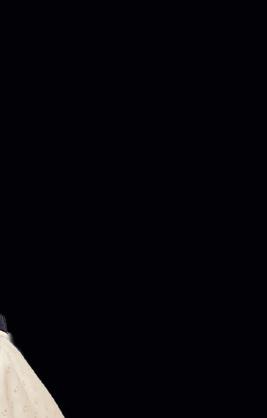
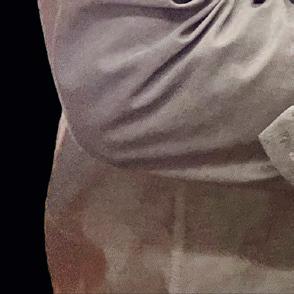
Jay: I've known a lot of the ADDMAN industry veterans for several years now. It really feels full circle now, as it was Bob Markley that introduced me to Joe Calmese, Deven Suthar and a few other members of ADDMAN's team at RAPID + TCT in 2021. That was my first introduction to the company, and over time, we established Dinsmore as a strategic partner of ADDMAN, specifically in polymer additive.
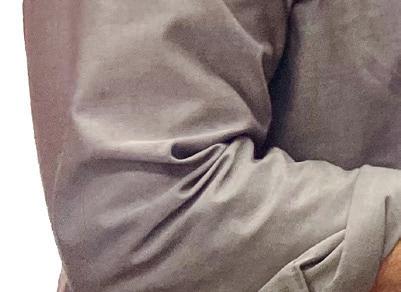
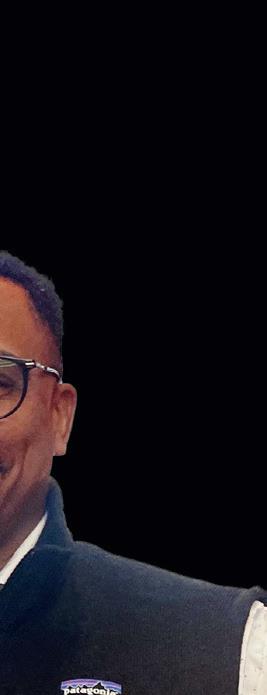
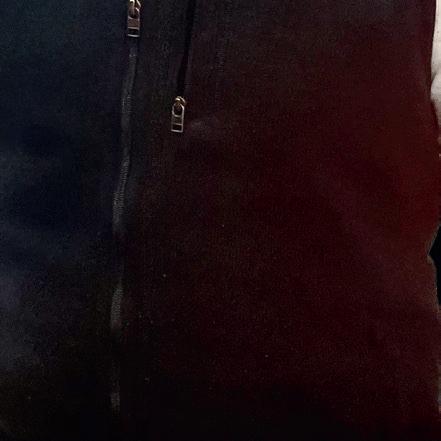
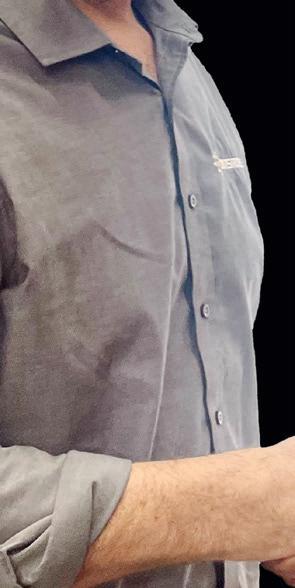
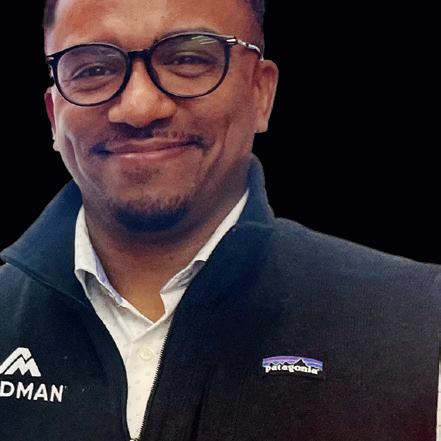
Suthar and a few other members of co-investment in the polymer product noticed side of things.
As I learned more about ADDMAN and everything they were doing, the conversations flowed from partnership to being fully a part of the team. It just made sense, and I was so impressed with their work in the hypersonics business and the intellectual property they had developed.
One thing led to another, and now I’m proud to be a leader within ADDMAN myself, and play a part of shaping the future of the company.
Dinsmore is a 20+ year old company, why was this year the right time to align with a company like ADDMAN?
The timing of our alignment with Dinsmore was perfect for several reasons. One of the main factors was that we were making an intentional co-investment in the polymer product lifecycle with injection molding via HARBEC. We've noticed that more and more, projects are being started with a fast-fail concept, and we were already participating in the production side of things.
By adding Dinsmore to our portfolio, we gained extensive front-end capabilities that will allow us to shrink development cycles significantly. We see tremendous value in this approach, and we're confident that our integration with Dinsmore will help us achieve our goals and deliver even more value to our customers.
Jay: As the founder of Dinsmore, I've been approached by various companies over the years but never seriously considered partnering or selling the company. However, the timing felt right this year due to the consolidation happening in the industry and the opportunity to align with a company like ADDMAN who has exceptional talent and expertise in manufacturing. This allows us to o er a full suite of services to our customers, including polymer and metal additive, subtractive CNC, and injection molding. It also brings exciting opportunities in the space and defense markets. Furthermore, partnering with American Industrial Partners (AIP) provides me with the chance to continue learning and growing in my career. Overall, it just felt like the right fit for the future of Dinsmore.
One recent development has seen Dinsmore install the HP Multi Jet Fusion 5420W, and through its work as a beta user, the company has been involved in the development of a medical-grade white nylon material. What impact do you think this material will have for your customers in the medical field?
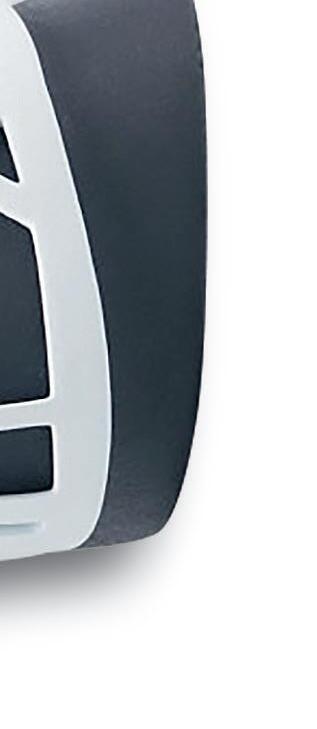
Jay: As a beta user of the HP Multi Jet Fusion 5420W, Dinsmore has been involved in the development of a medical-grade white nylon material. HP approached us about a year and a half ago to participate in their beta program and we were excited to be involved, as Dinsmore has always been an early adopter of technology. With our extensive experience in serving the medical industry, we pushed HP to make the white material medical grade, which they fortunately listened to. Now, we are already in production with several of our medical customers for White MJF HP part. This material will have a positive impact on our customers in the medical field, as well as other industries that require non-black parts. Overall, we are thrilled with the opportunities this material will provide for our customers.
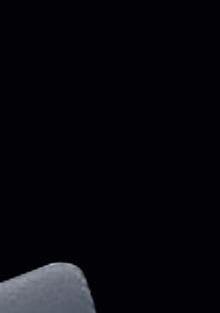
When the acquisition was first announced, ADDMAN cited the medical industry as a key market –how great is the opportunity for you both in this space?
Joe: Our investment in the HP Multi Jet Fusion 5420 hardware and software technology has been substantial, and we are confident that the combination of this technology with our ADDCAAM software will allow us to produce stronger medical devices that blur the line between polymer and metal. In addition, we're working on advancements in digital anatomy printing, and we have some heavy-hitting strategic partnerships in the works that will be announced soon. These partnerships will also be a game changer for tooling and instrumentation. We plan to participate and transform medical manufacturing in a big way.
What do you see as the biggest misconception about additive manufacturing technology today?
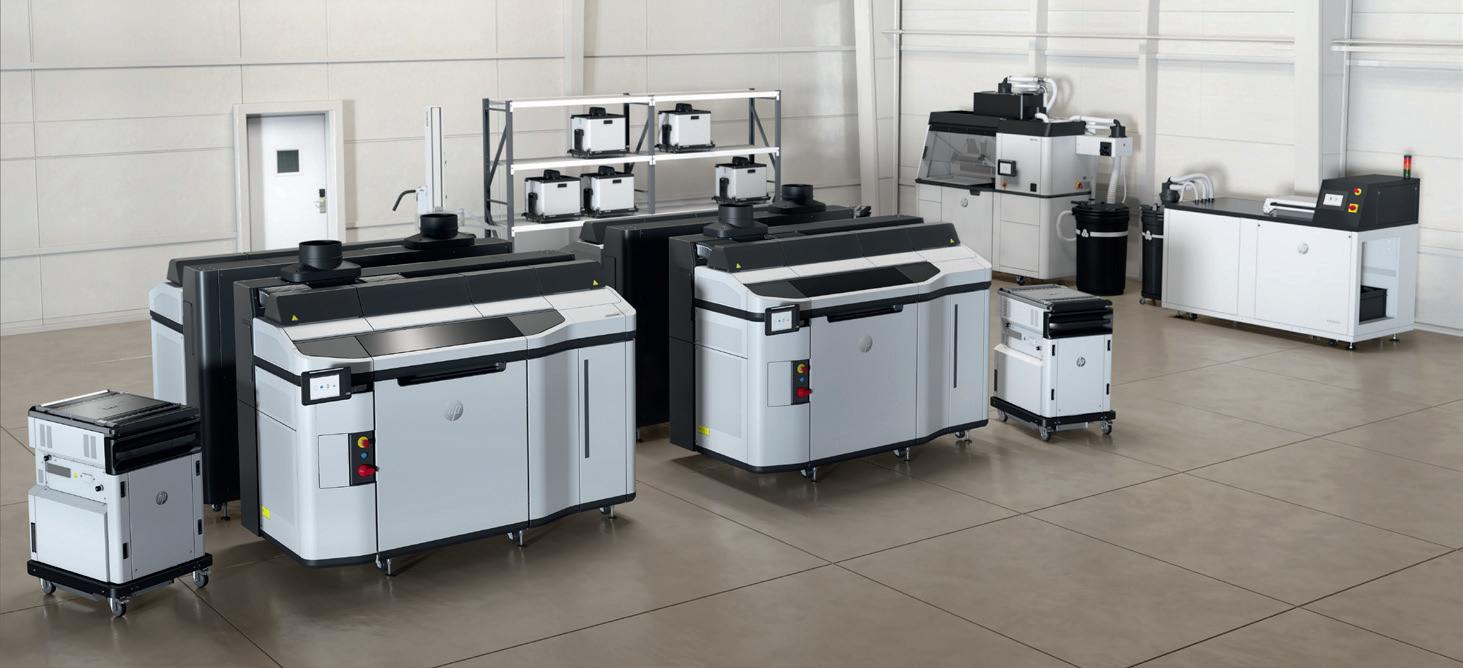
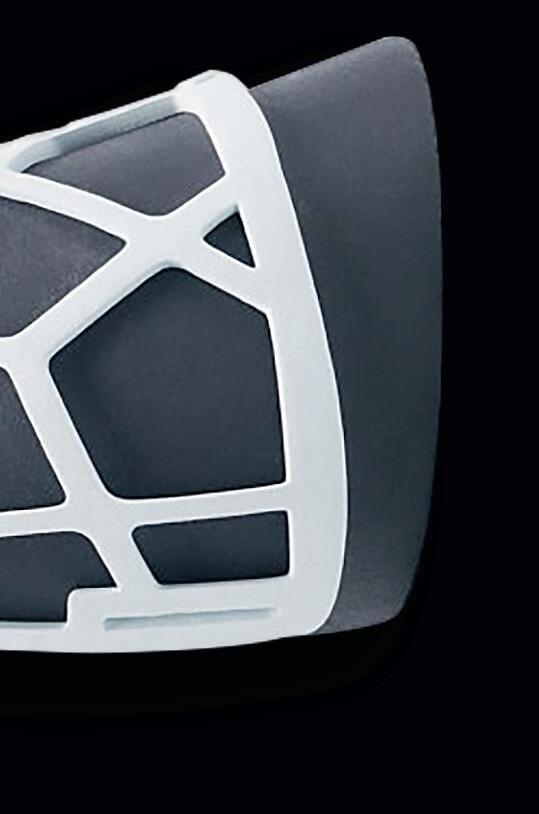
Jay: One of the biggest misconceptions about additive manufacturing is that it's a plug-and-play technology, and that you can simply print anything you want. But the truth is, every application is unique, and requires a deep understanding of the materials, design, and printing parameters. As someone who has worked extensively with 3D printing, I can tell you that it's not as simple as just hitting 'print' – it takes careful planning and optimization to achieve the desired results.
Joe: At our company, we have a mantra that guides our approach: any part, any volume, every step of the way. To best support our clients, we need full lifecycle solutions that leverage the strengths of both additive and traditional manufacturing methods. I think a misconception is that 3D printing is an easy button to get to market quicker. While additive manufacturing fits the bill in many cases, we recognize the importance of respecting and utilizing all available tools and techniques to achieve the best results for our clients.
Finally, what are you looking forward to at the upcoming RAPID + TCT event in Chicago?
Joe: I'm excited for the upcoming RAPID + TCT event in Chicago because it provides us with an ideal opportunity to showcase our company's core competencies and connect with our customers to better understand their needs. This event is where people come to find solutions to their problems, and we'll be there to demonstrate our cutting-edge technology and listen to their feedback. It's a great way for us to concentrate our e orts and show o our innovative solutions to a highly engaged audience.
ADDMAN Engineering and Dinsmore will be exhibiting at RAPID + TCT from Booth #4630 between May 2-4 at McCormick Place – West Building, Chicago, IL.