
8 minute read
GE Aerospace’s additive manufacturing journey, application by application.
It is August 2016, and the US Army has granted GE and the Advanced Turbine Engine Company – a joint venture between Honeywell and Pratt & Whitney – 24-month contracts to take their proposed engines for the Boeing AH-64 Apache and Sikorsky UH-60 Black Hawk military helicopters through preliminary design review. By April 2018, it is time for demonstrations.
One of the key requirements of the contract, in addition to power increases of, say, 50%, and fuel consumption reductions of, say, 25% was that the new engines fit inside the existing airframes. To successfully validate its engine design fit correctly in the helicopters, GE leveraged its polymer 3D printing lab at its Additive Technology Center (ATC) in Cincinnati to develop a printed prototype of its T901 engine true to size.
GE’s T901 engine includes numerous technological advancements that were successfully demonstrated in this rig and engine testing phase, which led the US Army to award GE with a 517 million USD contract that will allow the company to flex its metal additive manufacturing (AM) muscle once again. Engineering and manufacturing of several additive metallic T901 engine components is progressing well. The first development engine ran in 2022 and the first flight test engines are now scheduled to be delivered by the fall of 2023.
Last month, on a tour of GE Aerospace’s ATC in Cincinnati, TCT was given some context behind the T901 AM applications for the Apache and Black Hawk platforms.
Here is GE Aerospace’s AM journey, application by application.
THE FIRST FAA APPROVED PART
“It all started with this one part,” is the line GE likes to use to refer to its 3D printed LEAP fuel nozzle tip. And while this tip –with its 25% weight reduction and 30% cost e ciency increase – did kickstart the company’s additive manufacturing voyage, it was the quick turnaround of the GE90 T25 sensor housing that brought the first FAA-approved 3D printed part eight years ago.
The part needed to undergo a redesign, so the ATC was enlisted to use additive manufacturing to quickly develop and industrialize a new solution. Ten parts were consolidated into one, and 12 units were printed in a single build. Approximately 400 of these components were manufactured and installed on the GE90-94B engines.
“We needed to do it quickly and be able to iterate fast, which is why we used 3D printing,” ATC Site Leader Chris Philp says.
OVER 180,000 3D PRINTED LEAP FUEL NOZZLE TIPS HAVE NOW BEEN SHIPPED, WITH 1,000 UNITS MANUFACTURED EVERY WEEK AT GE’S AUBURN MANUFACTURING FACILITY.
Heat Exchangers
After enhancing the T25 sensor housings, similar design concepts were quickly
SHOWN ABOVE: T25 SENSOR HOUSING, GE’S FIRST FAA-APPROVED 3D PRINTED PART. THE SENSOR PROVIDES PRESSURE AND TEMPERATURE MEASUREMENTS FOR THE GE90 ENGINE’S CONTROL SYSTEM applied to heat exchangers, with significant reductions applied to part assembly, size, weight, and cost. On the GE9X engine, for example, GE has incorporated an aluminum F357 heat exchanger manufactured on the Concept Laser M2 that is 40% lighter. It also boasts a part consolidation of 163 traditionally manufactured components into a single printed piece.
“A [conventional] heat exchanger has a lot of tubes welded together and we've 3D printed it as a solid body,” Philp explains. “So, it's a lot more durable and has less source of failures.”
A NEW APPLICATION
Having proved to the FAA it could additively manufacture reliable aircraft parts, GE was buoyed. As it stepped into its GE9X engine platform, it saw the opportunity to leverage 3D printing in its new engine.
The team decided to apply additive manufacturing to a flowpath component, that could otherwise not be produced conventionally within the constraints of the engine. In doing so, GE designed a cyclonic inducer component which uses centrifugal forces to ‘divert particles of dust to the outside of the flowpath, before being ingested into the main stream, improving durability,’ per Philp. GE was so confident in the additive design of this component that it had developed its engines with the part in mind before FAA certification was granted. This component is manufactured on the Concept Laser M2 system in a cobalt-chrome alloy and has been consolidated from 13 parts into one. It is also said to be twice as durable as before. Eight 3D printed cyclonic inducers are fitted to every GE9X engine.
Low Pressure Turbine Blades
As previously detailed in TCT Magazine, GE is also having success with the Arcam Electron Beam Melting (EBM) technology. A total of 228 low pressure turbine blades are being additively manufactured on the Arcam EBM A2X in titanium aluminide for each GE9X engine. These components are contributing to an improved fuel e ciency of 10% and are 50% lighter than their traditionally manufactured counterparts. Because of the EBM process raising the temperature inside of the machine to 1,200°C, there are smaller thermal gradients generated and the components experience less residual stress during the build.
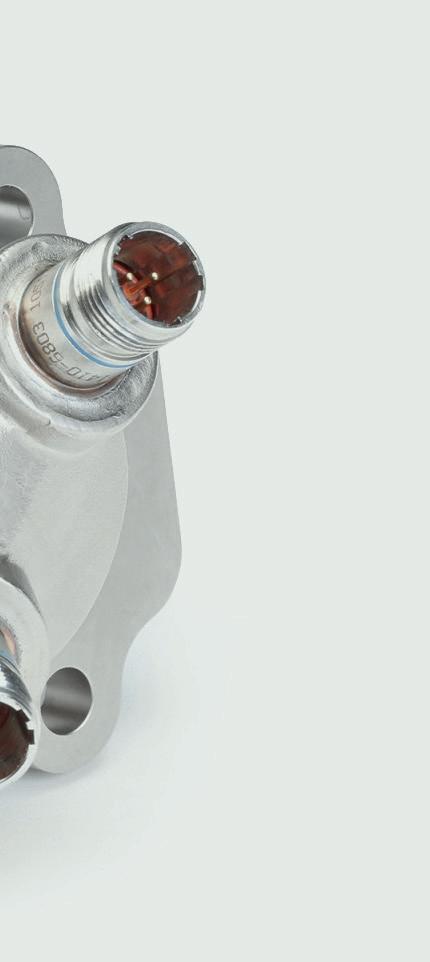
THERE ARE PLANS TO RE ENGINE AROUND 1,300 SIKORSKY UH-60 BLACK HAWK HELICOPTERS AND 600 BOEING AH-64 APACHE HELICOPTERS. EACH HELICOPTER HAS TWO ENGINES.
ONE ENGINE – ZERO TOLERANCE TO FAILURE
GE has also thrown 3D printing at its Catalyst engine for the single-engine Cessna Denali aircraft. And it is here where its application of additive gets bigger and more complex.
“We really took a fresh approach to design this engine. This is the next step up,” Philp says.
In the additive manufacture of the turboprop engine components, GE has incorporated integrated airfoils into the interiors of engine components to facilitate better performance. The engine is also said to burn up to 20% less fuel and achieve 10% more power than other engines in the same class. Among the parts printed for the Catalyst engine are an advanced turboprop fuel heater, exhaust case and C Sump component.
T700/CT7 MIDFRAME
“This is one of the hardest parts still to make, and we’ve been making it for 35 years,” Philp notes of the T700/CT7 midframe.
GE prototyped an additive version of the CT7 midframe, again, focusing on part consolidation. One of the weightsaving opportunities it had recognized was to consolidate parts so that it could remove flanges, nuts, and fasteners in a bid to help save weight, and so it could remove the ‘very complicated’ welding, brazing and assembly of parts. In the development of this prototype, which was subsequently validated on a development engine, GE incorporated 3D printing as much as it could, with the performance ‘exceeding expectations’ of previous iterations of the engine.
Philp suggests the work carried out to additively manufacture larger, more complex components like the CT7 midframe has helped the company to land the T901 contract, within which GE has currently printed and tested additively manufacture components to be used in engine qualification and flight testing.
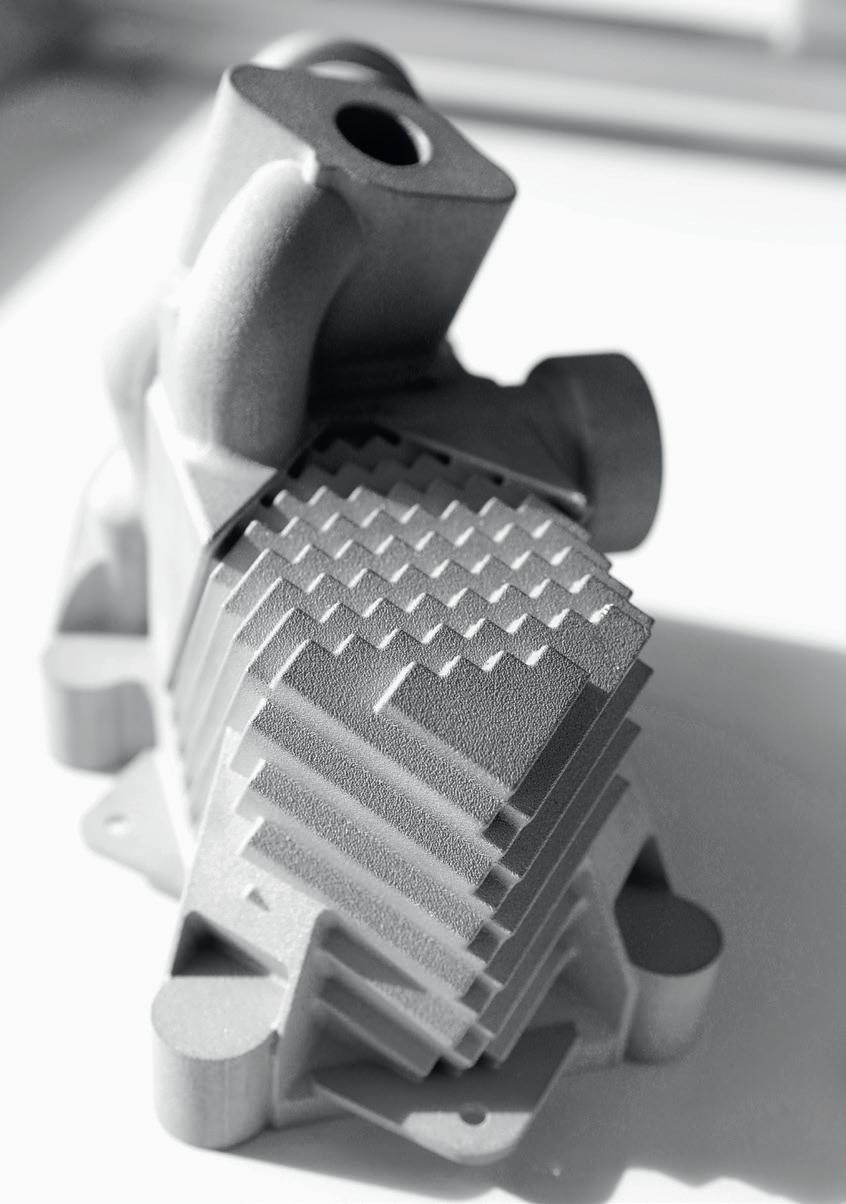
“We use those lessons learned, that knowledge [from previous projects], to say maybe we took it a bit too far, let’s pull it back a little bit. What you see here are all components for new engines, and that’s really where we see the most bang for our buck in 3D printing,” Philp say. “It’s not just saying I can replace this one part in an engine – that sensor housing was a separate story – when you start to design the engine as a system, with all the benefits of 3D printing, that’s when you gain the performance, weight and fuel savings.”
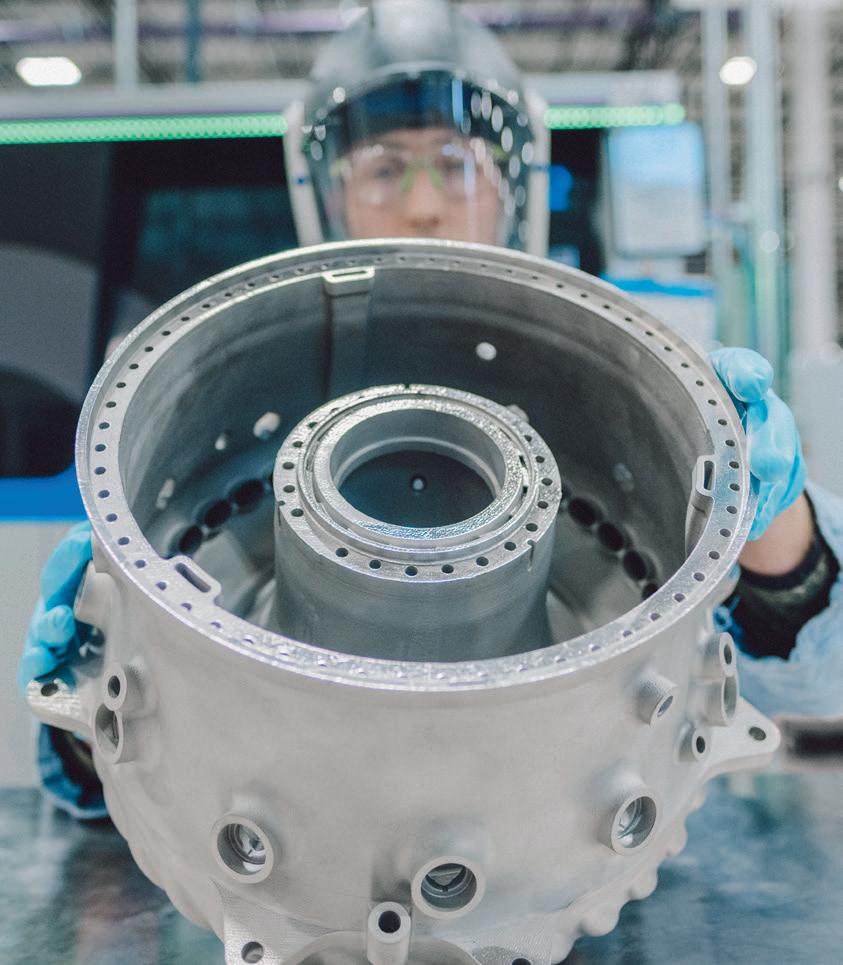
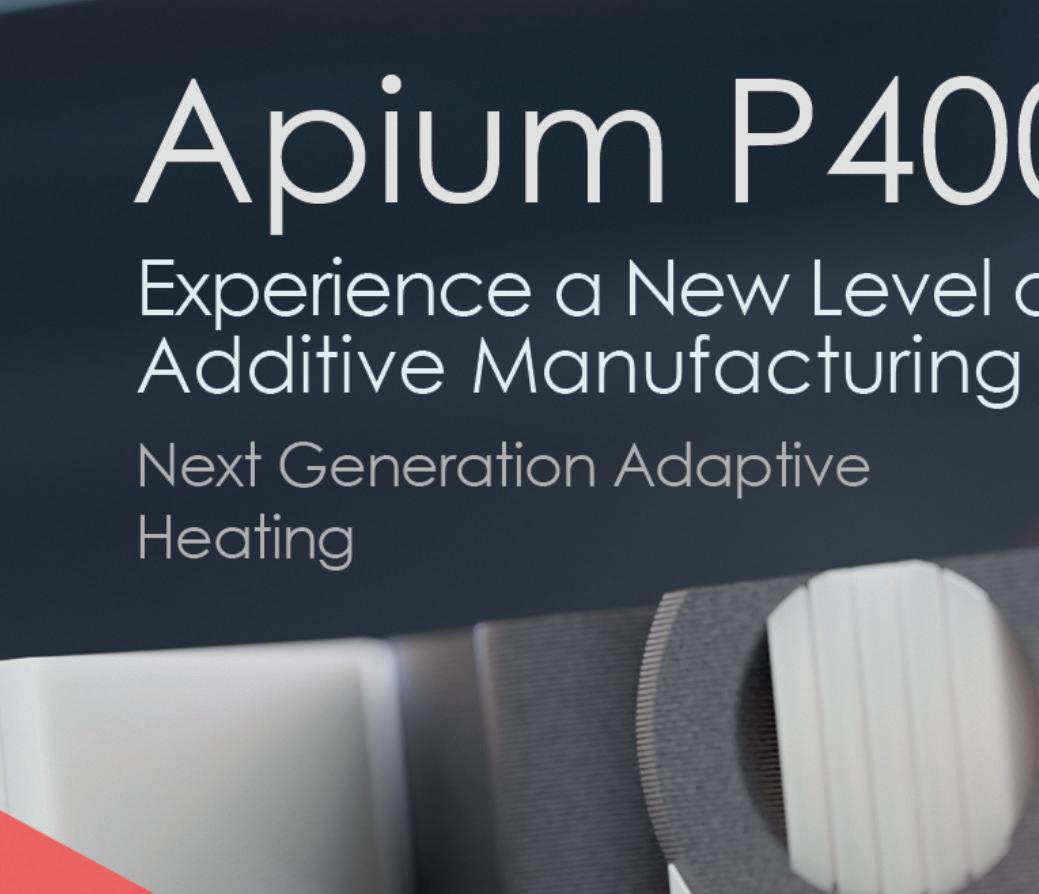
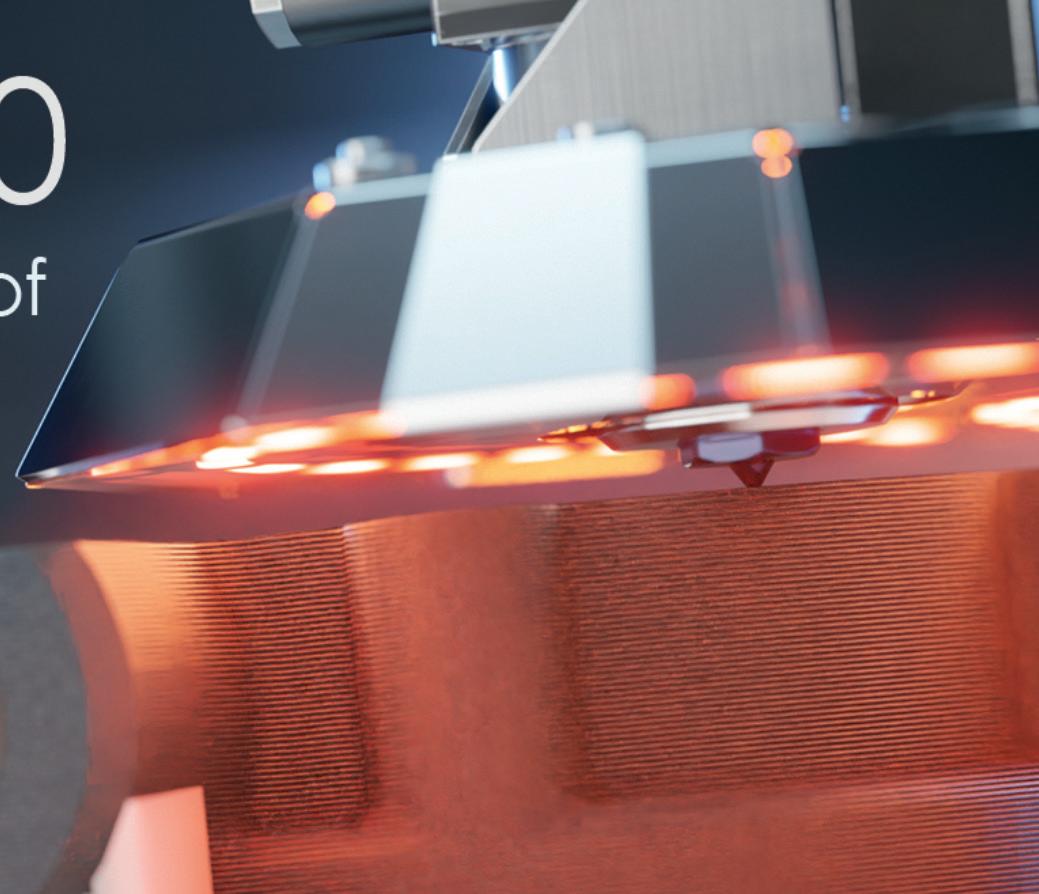

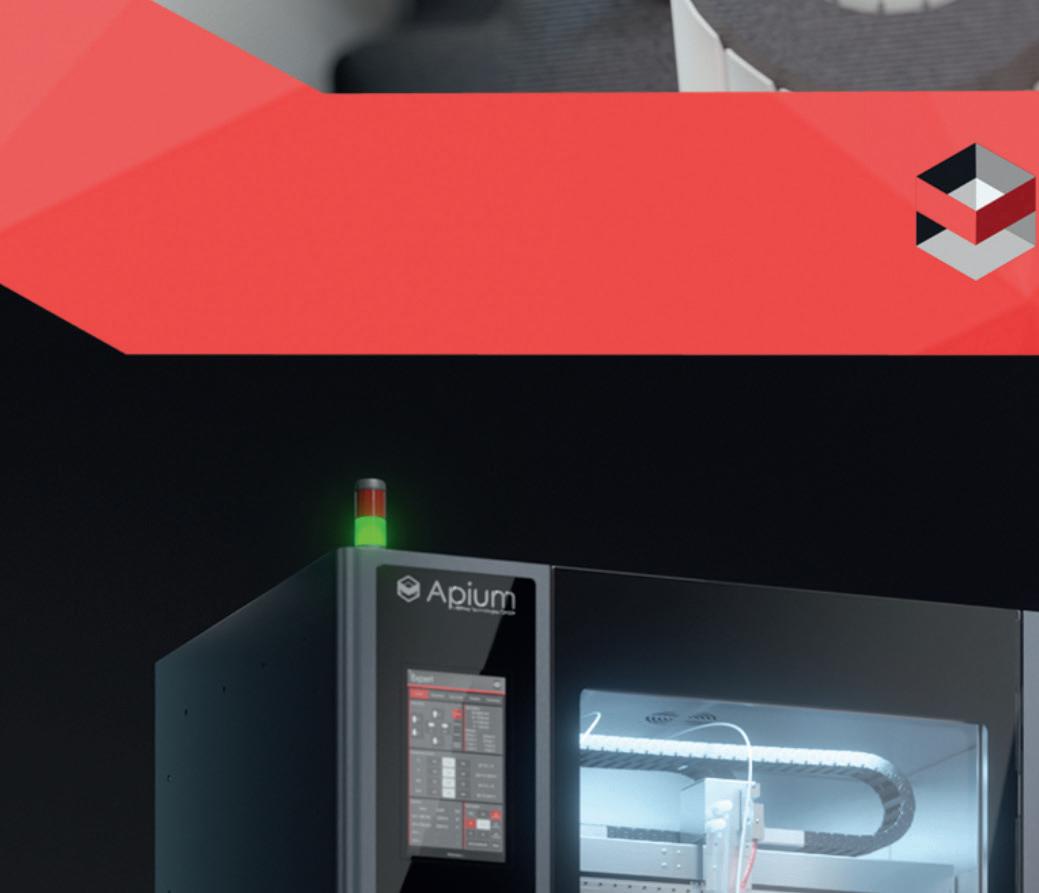
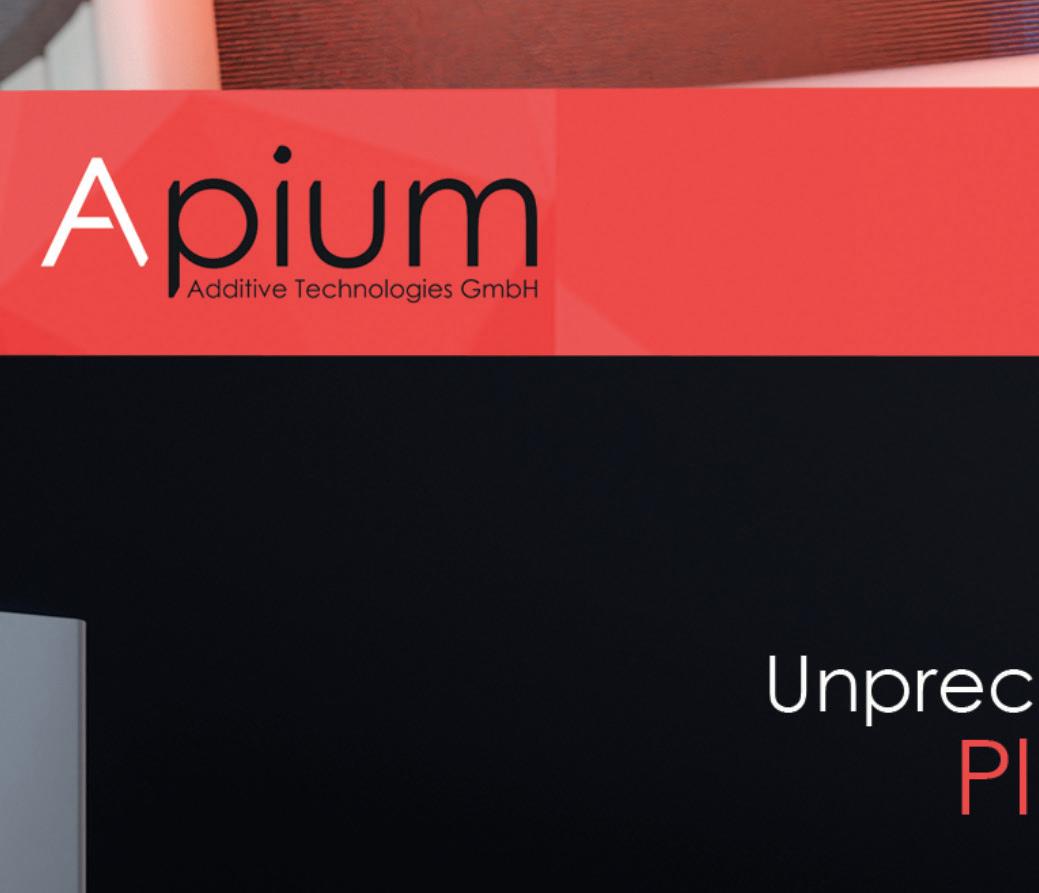
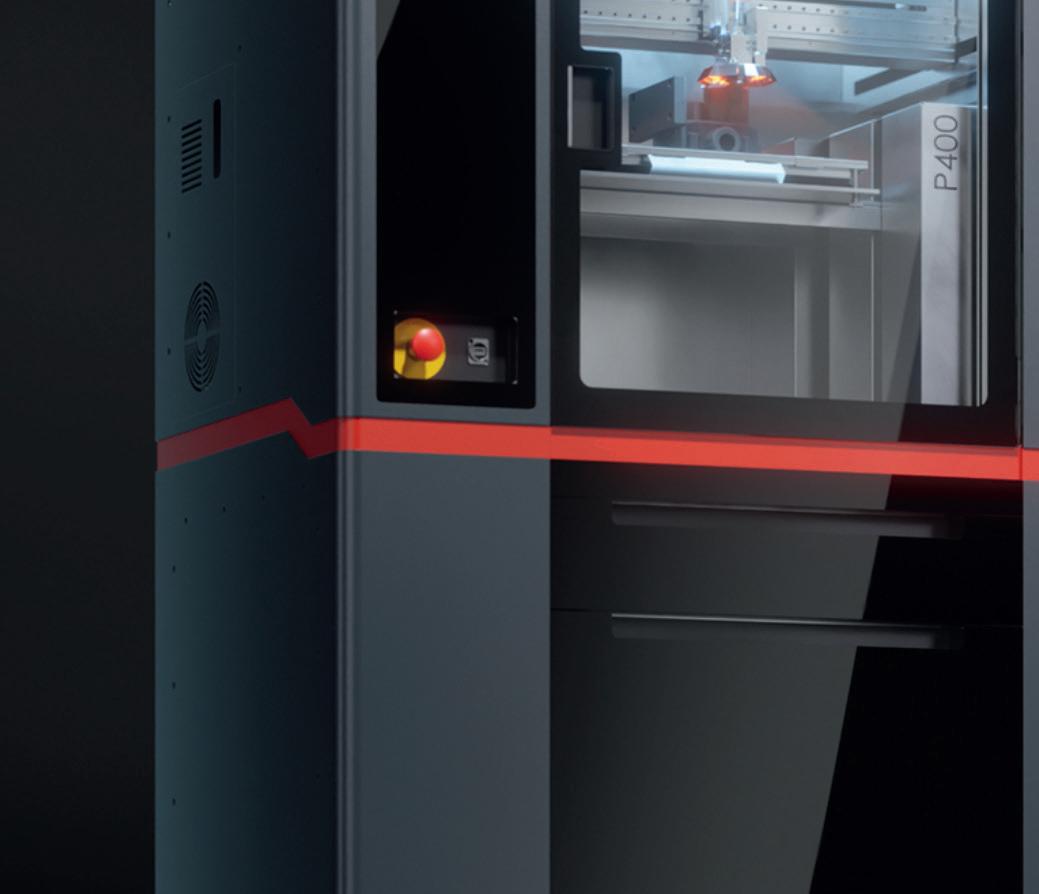
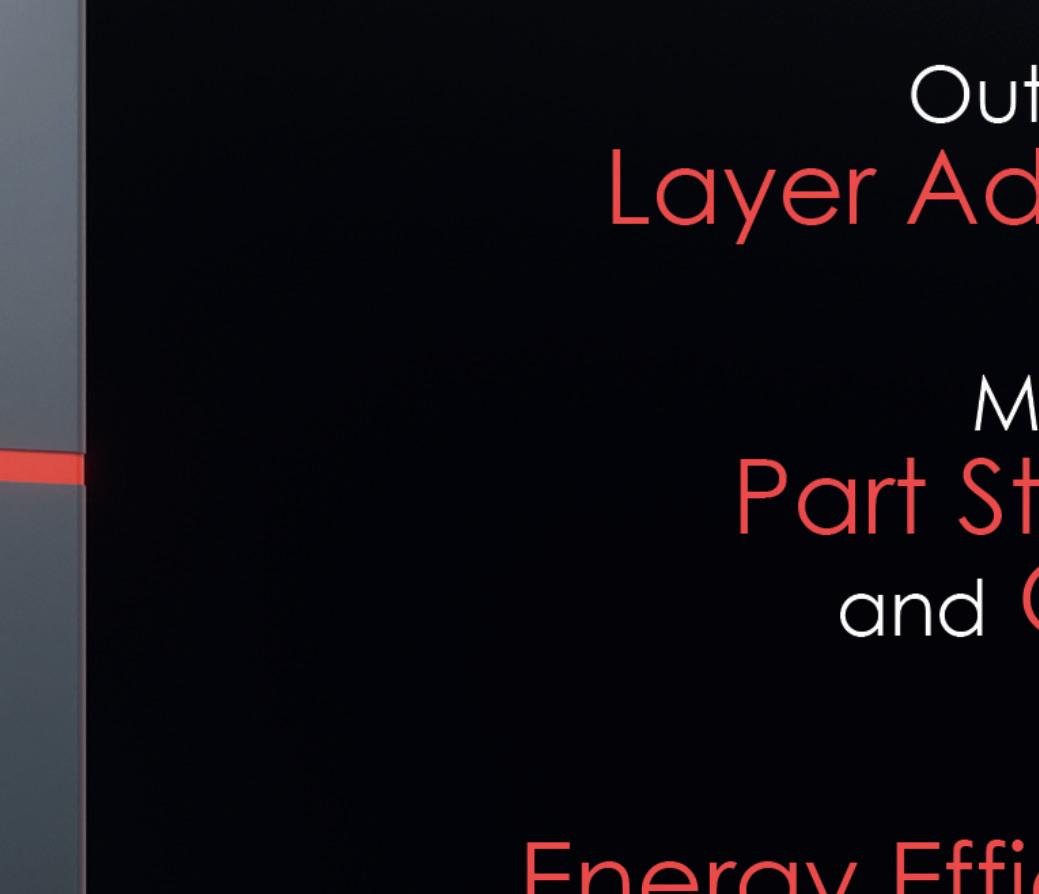
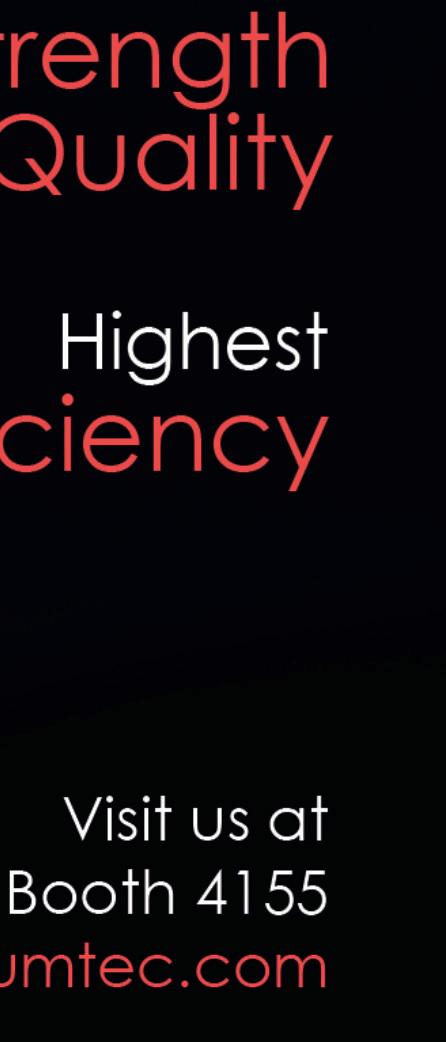
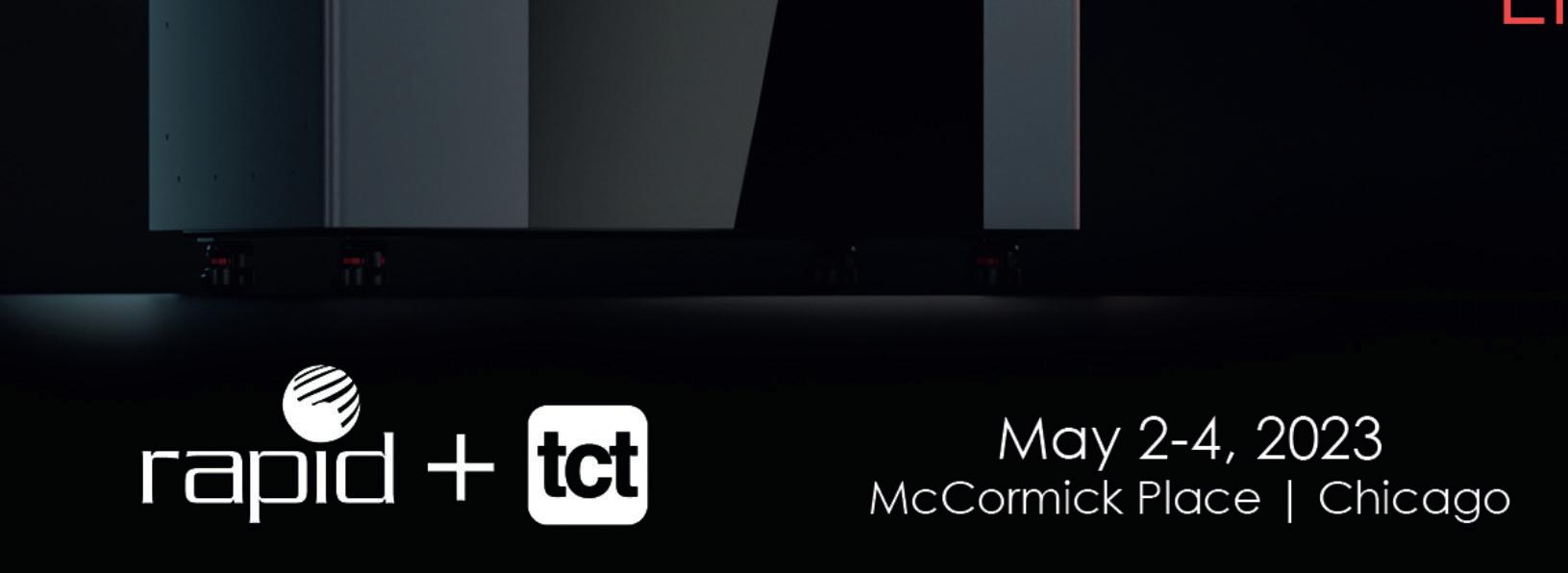
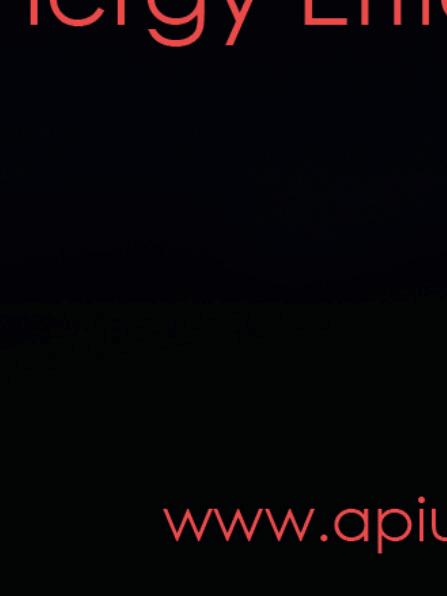
Sam Davies speaks to Sidus Space about its use of 3D printing in the design of a lightweight satellite set to be launched on the SpaceX Transporter-9.
During design iteration, Boschi incorporated fastening functionality into the structural components so that parts fit into a slot and lock into place. This has not only helped to shave o weight by removing screws and bolts but has also made the satellite sturdier.
As he extols the virtues of the technology facilitating a satellite weighing less than 100kg, Tony Boschi shows the depth of his experience with the repeated use of two words: rapid prototyping.
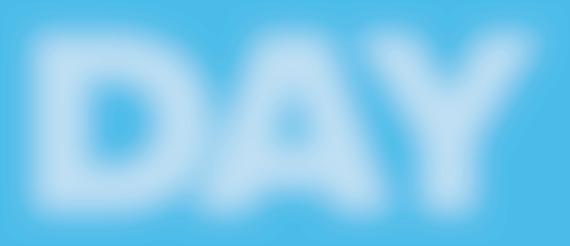
Boschi has been working with 3D printing technology for so long, that he not only refers to the processes using that phrase, but he also has the war stories. When he first used the technology, for example, he and his colleagues took to squirting hairspray on stereolithography (SLA) parts to prevent the sticky texture they were left with when coming out of the printer, and in turn allowing any paint applied to the components to dry faster.
“It was one of the greatest things in the world,” he recalls thinking. But such glee is relative. These days, as Lead Design Checker at Sidus Space, he has printed sample holder parts in Markforged’s Onyx carbon fiber-filled nylon material that formed part of a flight test platform installed on the outside of the International Space Station (ISS) for a year. That the parts survived on the ISS with next to no degradation emboldened Sidus Space to push forward with the idea of producing the structure of its LizzieSat satellites with 3D printing.
Sidus Space was founded by Carol Craig, a former US Navy o cer who became the first woman eligible to fly combat aircraft in the US Navy, to carry customer sensors and collect data for a multitude of di erent customers at the same time. The partially printed LizzieSat constellation will launch for the first time later this year on the SpaceX Transporter-9, if it weighs less 100kg.
This has represented a significant challenge for Boschi and the Sidus team, especially since integral componentry like batteries and computers take up a significant portion of the satellite's overall weight. But it is one they backed themselves to overcome with the combination of their engineering prowess and 3D printing technology.
In the design of the LizzieSat, they have applied Markforged’s composite 3D printing technology to the entire structure of the 31 x 31 x 18 inch satellite, harnessing the company’s Onyx FR and Onyx FR-A materials on eight vertical and eight horizontal components that hold in place a honeycomb structure. With this use of carbon-fibre filled nylon, Sidus says it is able to leverage similar strength qualities to aluminum, while reducing the weight and iterating on designs much more quickly.
“When we started doing the preliminary analysis, you could see that when the parts were bolted together, they were all separate,” Boschi says. “But when we made the locking feature, then the entire ring became one piece, so that we’re only pulling on one structure, as opposed to 16 pieces – because there are eight columns and eight pieces in between to hold them together. Now we put everything together, they all get bolted to the honeycomb or the aluminium pan on the other side, it’s more of a stronger, stout structure.”
At the time of writing, Sidus is in ‘full print’ mode ahead of the prospective SpaceX launch later this year. The design has been locked in, the honeycomb and base plate are due for arrival in April, and then the satellite will go through an extensive testing process to prove out its durability. The LizzieSat satellite has been built for a five-year life, while Sidus has had to keep in mind that as it is launched into outer space, it will have to take 5G loads, withstand solar radiation, and deal with vast temperature swings of around 200°C as it goes from the exposure of direct sunlight to the shade of the Earth’s shadow.
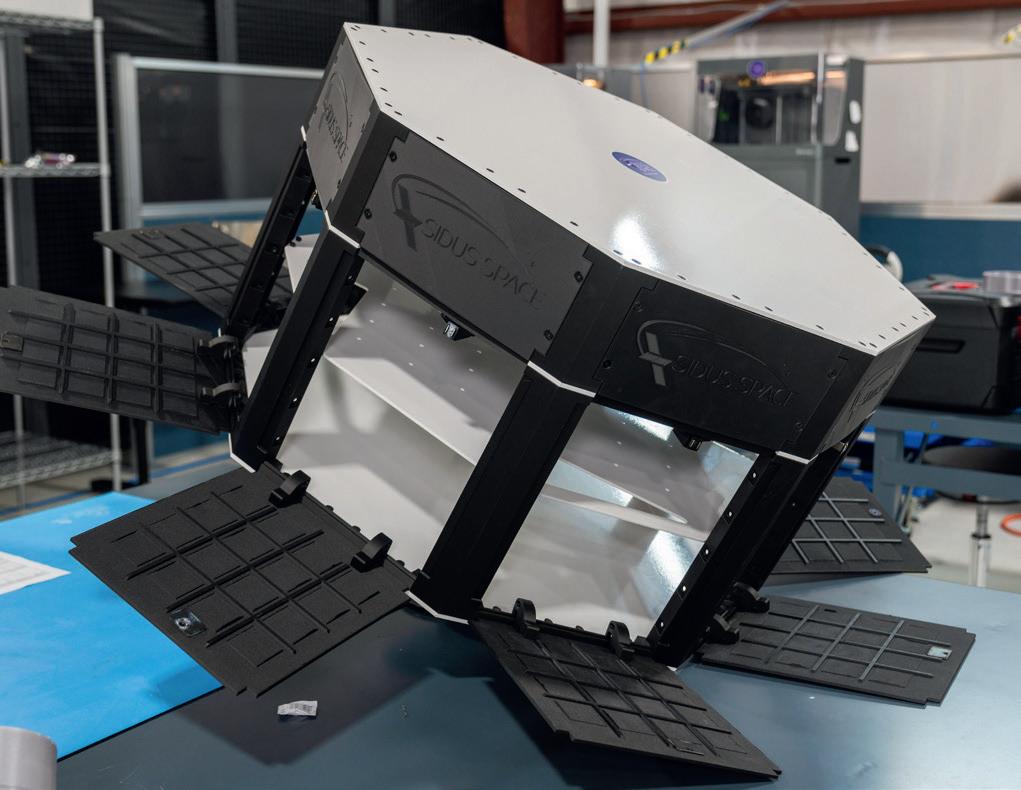
For Boschi, he’s never been more sure that 3D printed parts can manage it.
“When I first did parts years ago with SLA machines, we would break them taking them out of the machine. If you didn’t put it down right, it would break. And it’s advanced from that point forward. Now we’re in nylon. Better materials, it’s changing everything. From that point when I was first [using 3D printing], it’s night and day.”