
4 minute read
THE COST PER PART CHALLENGE


KIERON SALTER, CEO, Digital Manufacturing Centre
At a recent panel event, a longtime additive manufacturing (AM) professional remarked: ‘if you can manufacture something in any other way, you probably should.’ I’m paraphrasing, but the challenges around building an AM business case for production are well documented and multi-fold. Cost is just one, and according to some, the biggest. Here, we asked five experts for their take on AM’s cost per part challenge and what we can do to overcome it.
“Currently additive can still be an expensive option when looking at piece price, largely driven by machine cost and speed of build. These two factors mean that machine cost and amortization make up a large percentage of the component piece price - often well over 50% of the cost is machine cost. Lots is being done to increase productivity. In metals, we have quad laser machines, but as well as productivity we need machine builders to continue the drive towards lowering machine cost and increasing utilization rates. Polymer technologies like SAF, SLS and DLP are doing a good job in driving price down.
I say to all prospective users of AM: you have to choose AM for a real benefit otherwise you will not win. AM o ers lightweighting, reduction of tooling costs and the ability to create complex geometries or consolidate parts. If you are achieving any of these then AM will likely work for you. If you’re reducing mass, it’s probably for a good performance reason and therefore likely to be prepared for higher piece price. If you are eliminating tooling then the business case stacks up at a certain volume breakpoint. Similarly, if you are increasing complexity or integrating systems into one component, the business case often makes sense when you look at cost savings as a whole. It’s only when you look at the piece price in isolation that it doesn’t compare – you have to look at AM di erently to understand the costs. That said, as machines get more cost e ective and materials become more competitive, AM will continue to grow into a bigger manufacturing solution for large-scale digital production.”
BART VAN DER SCHUEREN, Chief Technology O cer, Materialise
“3D printing enables design optimizations that often create cost advantages that impact the overall end-to-end manufacturing cost. In fact, a recent survey commissioned by Materialise shows that “the ability to reduce the overall manufacturing cost” is cited as the most important benefit of 3D printing. But that doesn’t necessarily mean that the 3D printing process itself is cost-e cient. Several factors determine the cost of 3D printing parts, including the materials required, production time per part, the type of printer but also energy cost.
There are two important ways to reduce this. The first is by working more e ciently to increase production capacity. Software plays a major role in this, by making it possible to optimize the build and to tune the printing process to make it more e cient and repeatable. The second, less obvious one, is using tools that improve quality. Because quality comes at a cost. If we consider certified manufacturing in the medical or aeronautics industry, for example, we see that up to 70% of the production cost is in quality control. A good example is the Process Control software for metal 3D printing we just released. The software uses artificial intelligence to automate quality control, helping manufacturers to take control of the 3D printing process and ultimately save time and money.”
MELISSA ORME, Vice President of Additive Manufacturing, Boeing
“From the perspective of the aerospace and defense industry, additive manufacturing finds value in complex parts that are di cult to machine, such as part consolidations, assemblies, parts with added functionality such as internal cooling, and parts in which welds or brazes have been eliminated with the use of AM. Generally, such parts have a positive business case and provide cost savings, in addition to performance and quality improvements. Hence, the Boeing company focuses on the aforementioned complex parts in our AM portfolio.
On the other end of the spectrum, simple parts such as brackets, clips, or direct replacements of castings that are not optimized will be more expensive to produce with additive manufacturing and also require more energy to produce than traditional manufacturing and thus will have negative business and sustainability trades. The Boeing Company does not consider such parts good candidates for additive manufacturing unless the intent is to mitigate a critical supply chain shortage of the traditionally fabricated components.
Additionally, nonrecurring testing is a heavy cost in AM’s nascent stage, which will slowly diminish over time as the technology matures. For the correctly selected part portfolio, even with the inclusion of nonrecurring testing, the cost is still favourable for AM.”
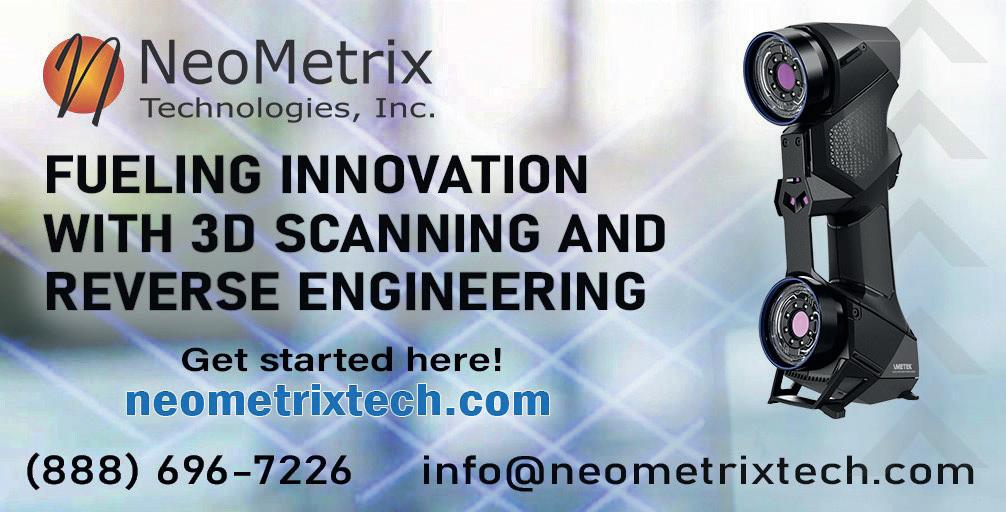
HODA AMEL, Technology Manager, Additive Manufacturing, The Manufacturing Technology Centre
“There is no doubt that AM can still be too expensive for producing large quantities of simple geometries, but there are still ways we can address this challenge. Reducing build failures and waste parts, increasing the life of feedstock by better understanding the e ect of recycling and potential routes to rejuvenate, automating pre- and post-processing steps are a few steps we can take to tackle the cost per part problem without challenging the material and machine costs.
We also need to become smarter with our use of AM and use it where it o ers the most benefit.”
TERRY WOHLERS, Industry consultant & President, Wohlers Associates
“People often asked about the most significant challenges the AM industry faces. At or near the top of the list is the cost of machines and materials. The price-to-performance ratio of AM products continues to improve, but it is far from where it needs to be.
One possible solution to the price of machines is to improve build speed. If speed improves by 2x, you can build twice as many parts in a given period of time. This spreads the machine depreciation cost over these parts, which reduces the cost per part. Imagine this cost reduction if a machine is 3-5x faster.
The price of materials needs to decline dramatically before adoption becomes mainstream among manufacturing companies. Some materials are priced orders of magnitude higher than similar materials for conventional manufacturing processes. This is mostly acceptable for prototyping and tooling quantities but becomes a “showstopper” when scaling to production volumes.
AM must create value. If it does not, companies cannot justify its use. Consolidating two or more parts into one, reducing material and weight, and improving a product’s performance are design methods that can help create value. This, along with a reduction in the price of machines and materials and improvement in build speed, will lead to a greater adoption of AM for production applications.”