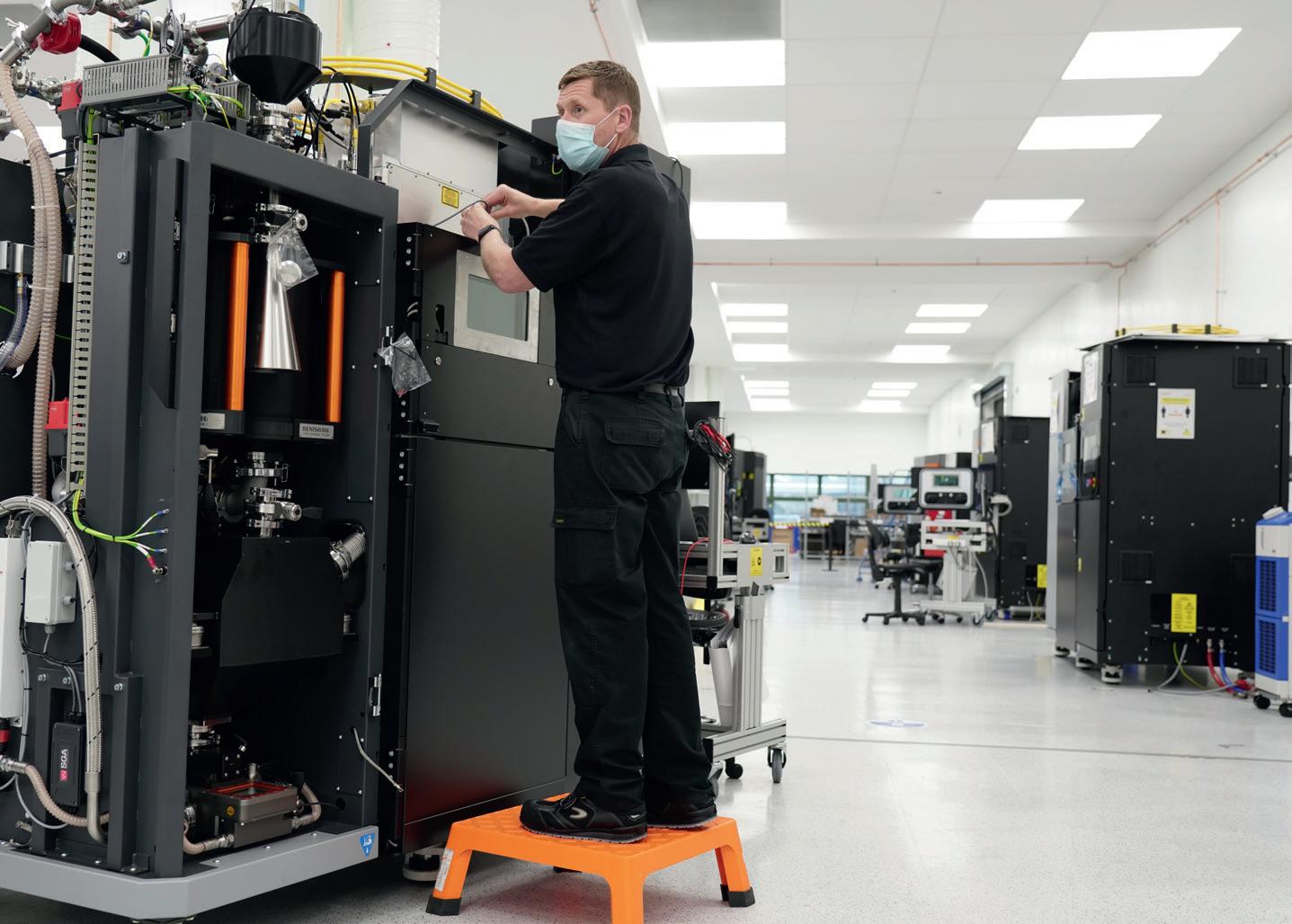
5 minute read
RENISHAW IS READY
Laura Gri ths takes a tour of Renishaw’s Miskin facility as the company celebrates five decades of UK engineering.
On a particularly snowy day in a quiet Welsh village, a company is celebrating a milestone.
It’s been 50 years since Renishaw, now a global engineering firm, was formed o the back of an invention that would solve a tricky measurement problem for Rolls Royce.
Sir David McMurtry, now Executive Chairman of Renishaw, had designed and built a prototype touch-trigger probe for co-ordinate measuring machines (CMMs) used to measure the instrumentation pipes on the Olympus engines that propelled the Concorde supersonic aircraft. The invention was a success, and McMurtry, together with colleague, John Deer, now Renishaw’s Non-executive Deputy Chairman, believed this technology breakthrough could hold much greater commercial promise. After Rolls Royce agreed to licence the patent, but only to a limited liability company, the duo went and purchased an ‘o -the-shelf’ company and on April 4th 1973, Renishaw Electrical Ltd. was registered.
Cut to March 2023, we’re sat in a small meeting room in Miskin, opposite the space where Renishaw’s additive manufacturing (AM) systems are manufactured, waiting to hear from a panel of senior executives. There are whispers that McMurtry, who stepped down as Chief Executive in 2018 but never too far away from the action, might make an appearance. Sure enough, he does, and his presence and bullish opinions on everything from sustainable business practices to nurturing engineering talent, captivate the room.
The conversation is far reaching and while today’s story focuses on the origins of a company that has its roots in industrial metrology and precision measurement, one thing is palpably clear: McMurtry is invested in the next generation of metal AM.
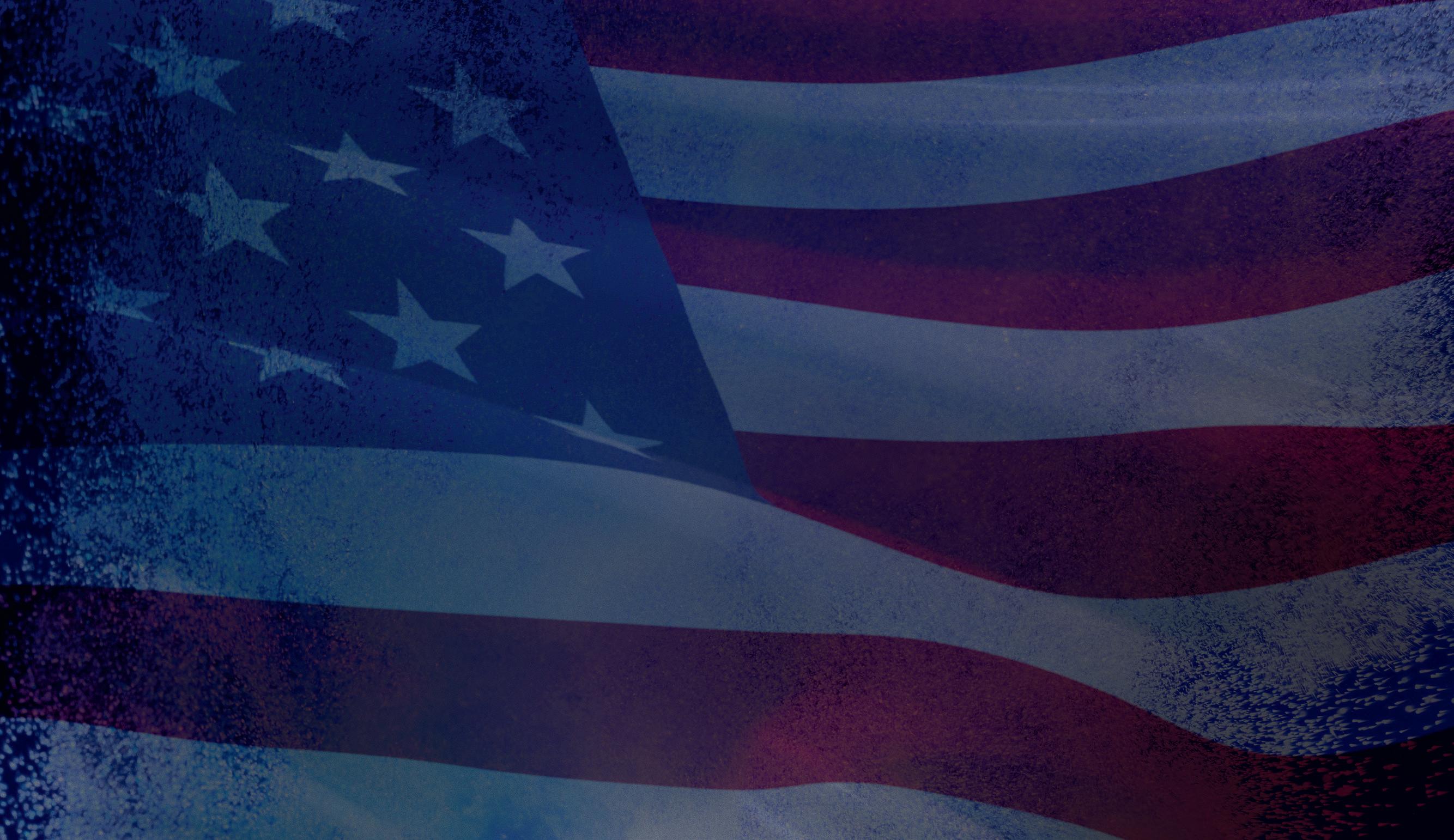
What this next generation will look like or unlock is not for today’s conversation but Louise Callanan, Director of Additive Manufacturing, has been tasked with leading and is careful not to give a micron of that progress away.
“In terms of the future, I suppose the most important thing really is to say that we're continuing to invest in AM in many areas - in our people, and in the technology,” Callanan told TCT.
When we meet, Callanan has been in the role for just over a year and still counts herself as a newbie to the AM industry. Yet she has built a long career at Renishaw after joining as a Graduate Design Engineer 26 years ago, and has always been aware of the technology’s benefits whether supporting development functions internally or facilitating very low volume production runs. “It was just the excitement, from a development point of view of being able to quickly visualize your concepts, to be able to iterate those really quickly, and ultimately, to be able to accelerate the development process,” Callanan said.
Callanan’s tenure is a prime example – and there are several on the panel with similar stories – of how Renishaw seeks and maintains its talent, something she believes will be integral to this next phase of AM growth.
“I think that commitment to the future of AM means we can really start to attract and retain the right talent, the highest quality talent, which is massively important to the success of the future.”
Renishaw first ventured into additive in 2011 with the acquisition of MTT Technologies, a UK-based manufacturer of laser melting systems, which McMurtry noted at the time for its potential in aerospace and medical markets. Today, Renishaw’s technology is used in everything from custom implants and neurological drug delivery systems to complex heat exchangers and aircraft assembly parts. Recently, the company announced the extension of one already successful partnership with British Cycling ahead of the 2024 Paris Olympics. The pair previously worked together to develop a track bike featuring metal powder bed fusion parts for the Tokyo Olympics and 2022 Commonwealth Games, securing seven Olympic medals in the process, and now plan to increase the bike’s speed with an enhanced design.
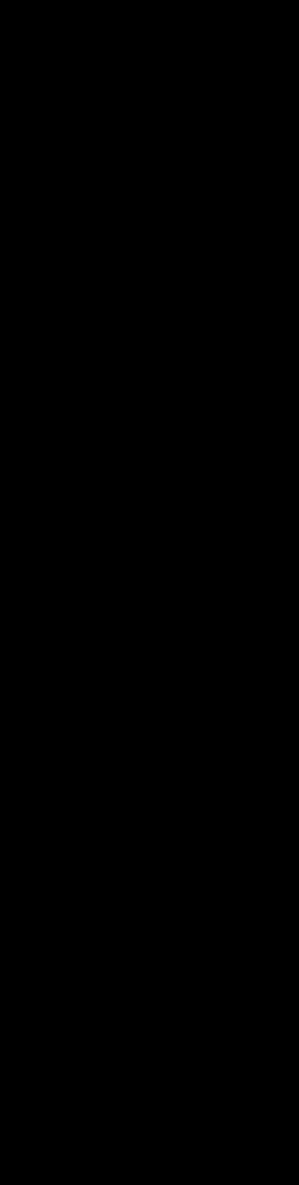

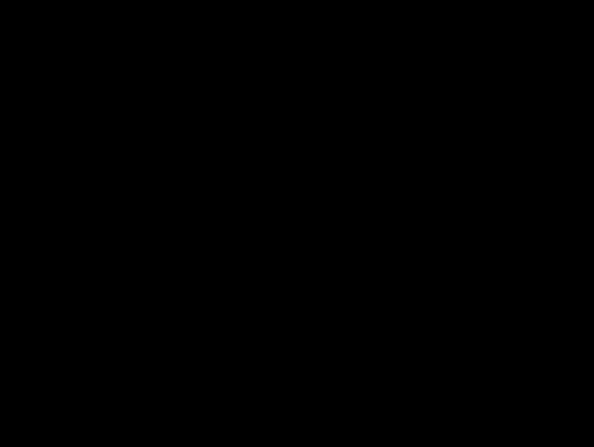
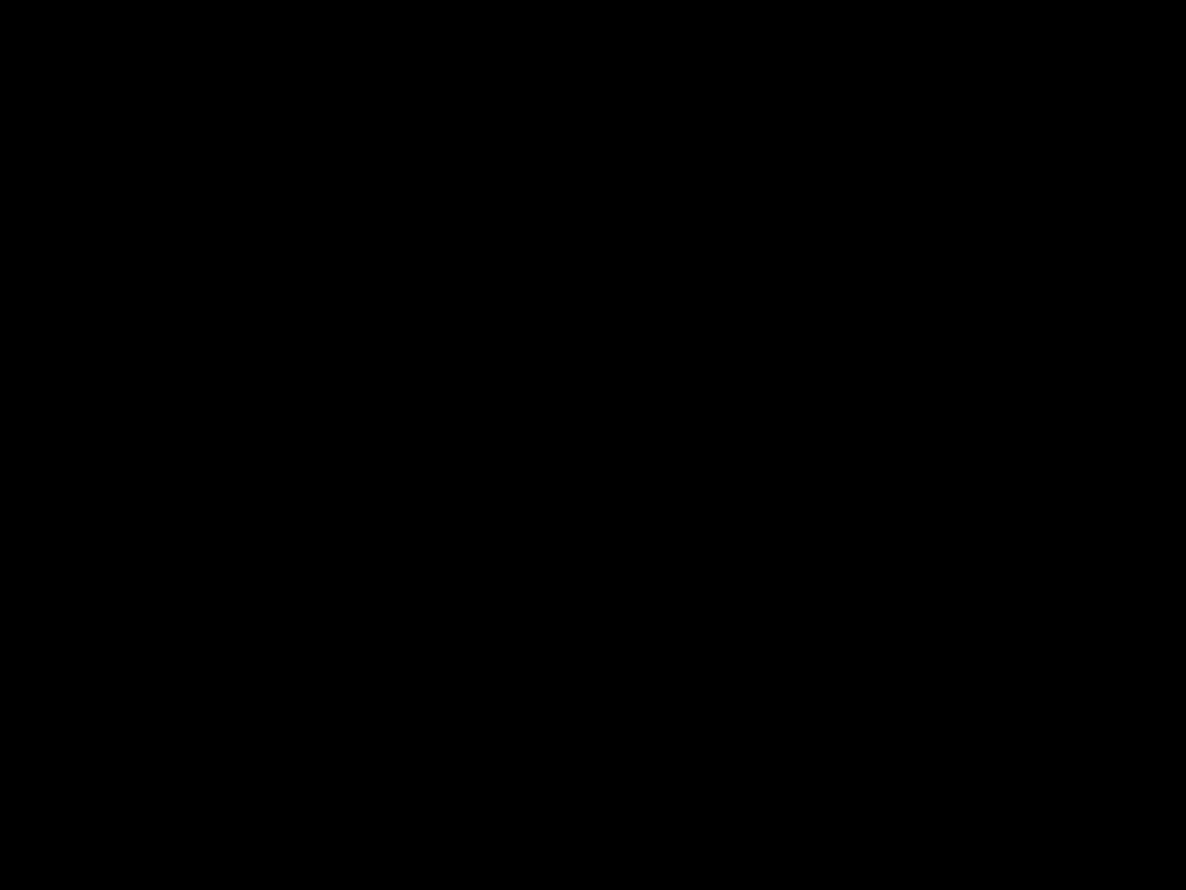

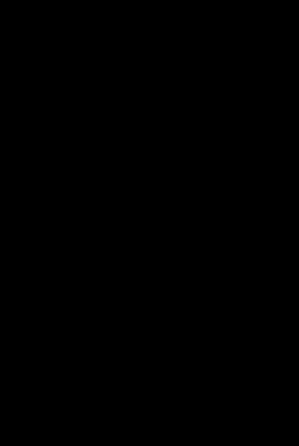

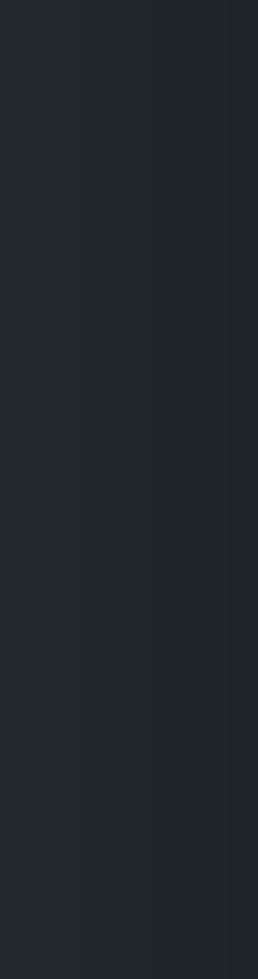
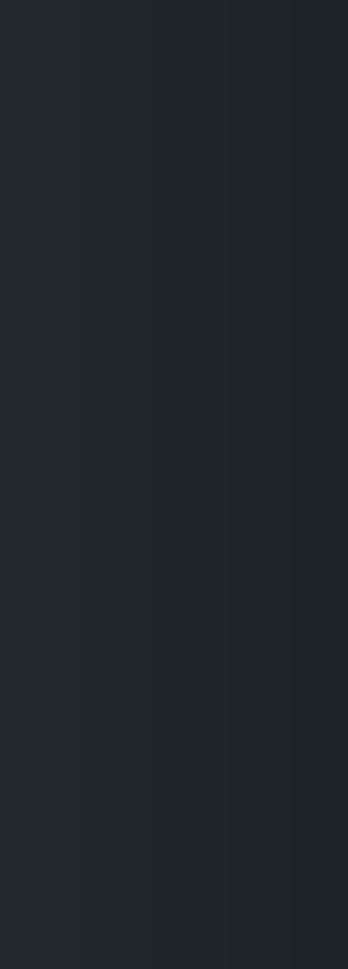
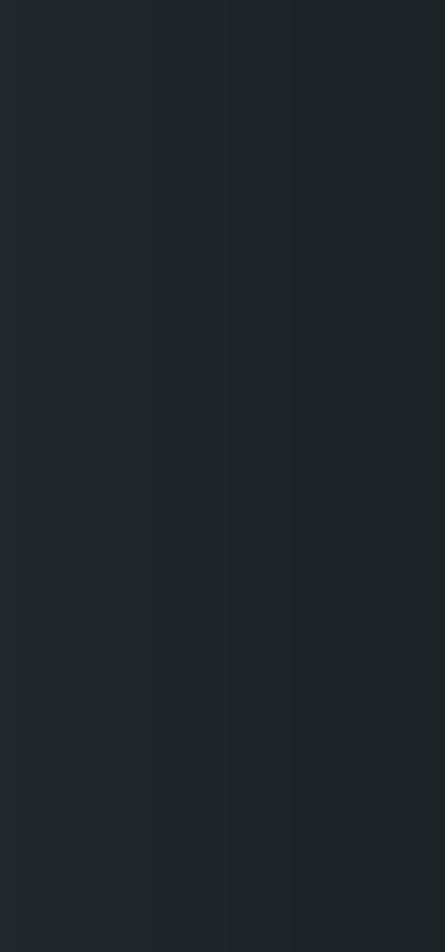
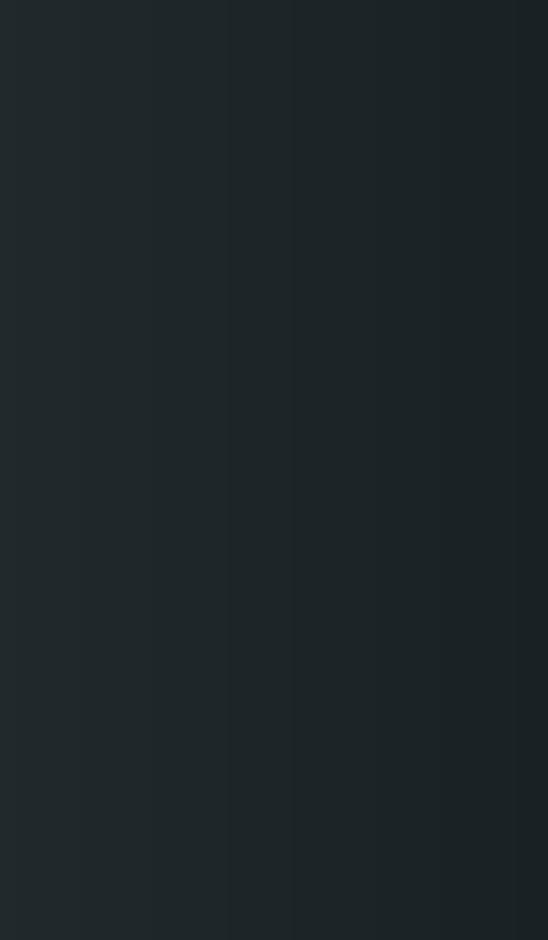
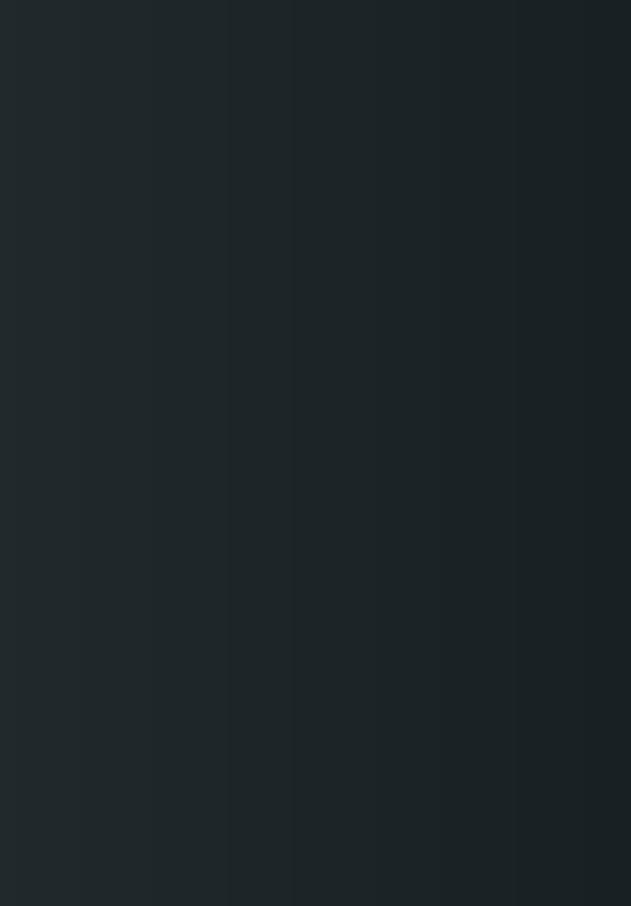
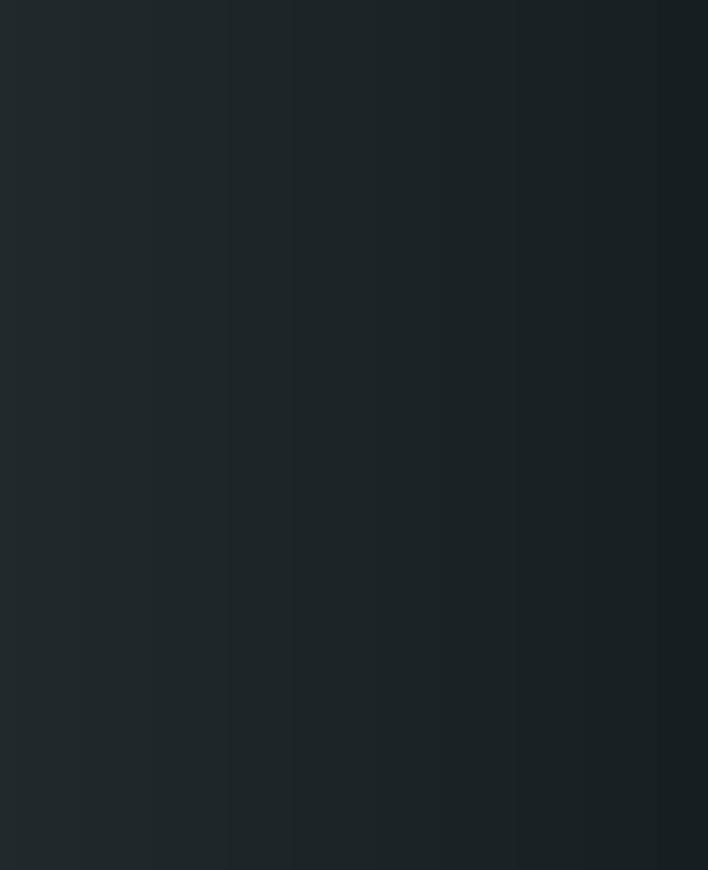
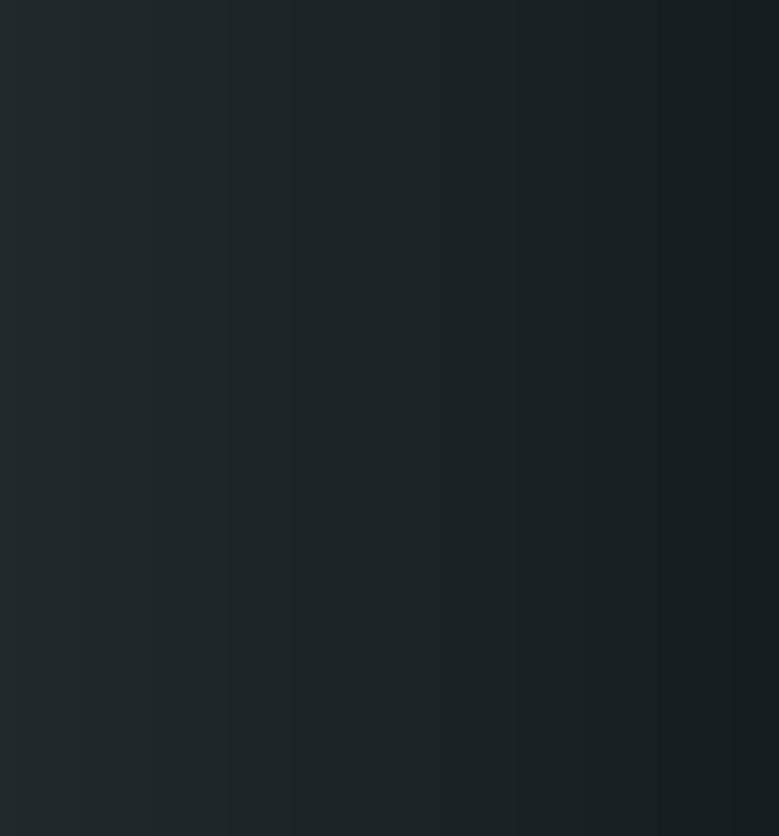
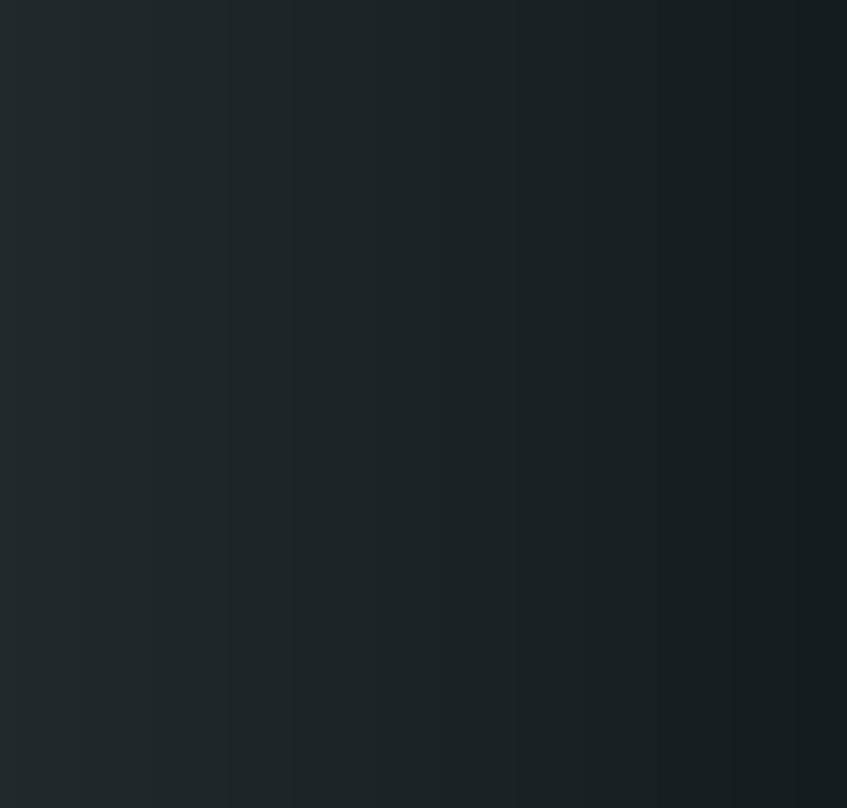
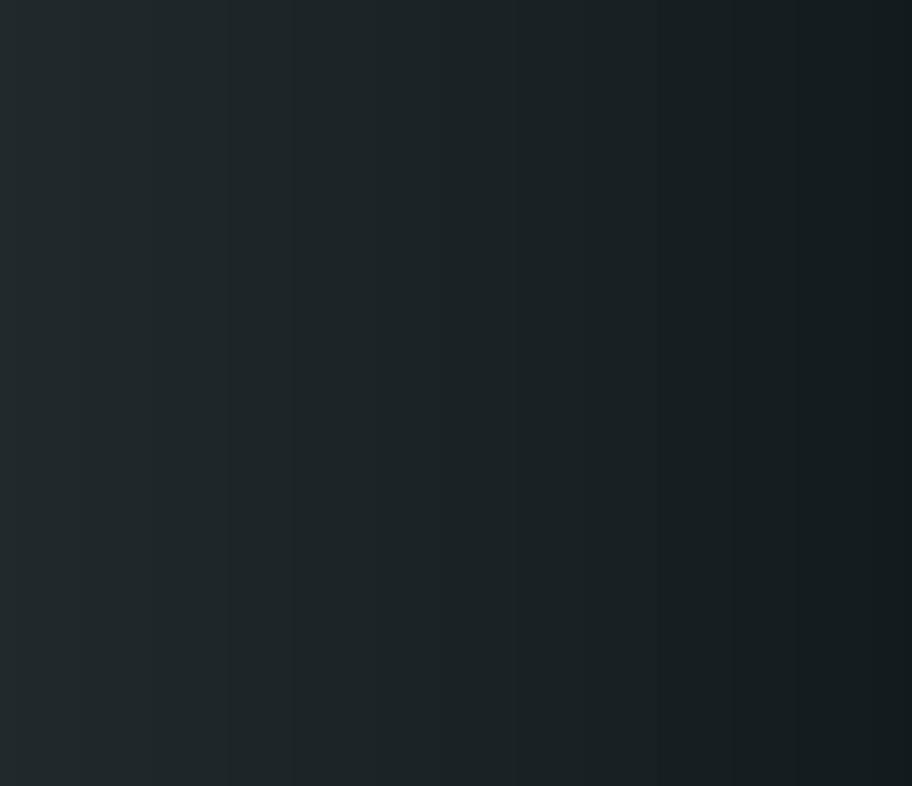
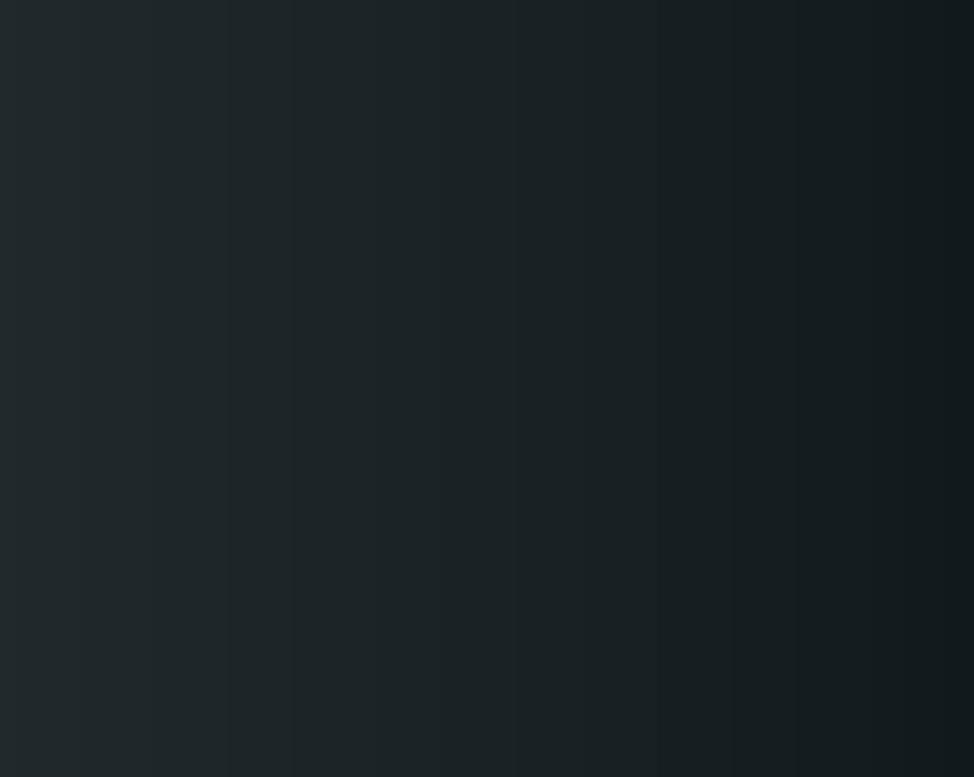
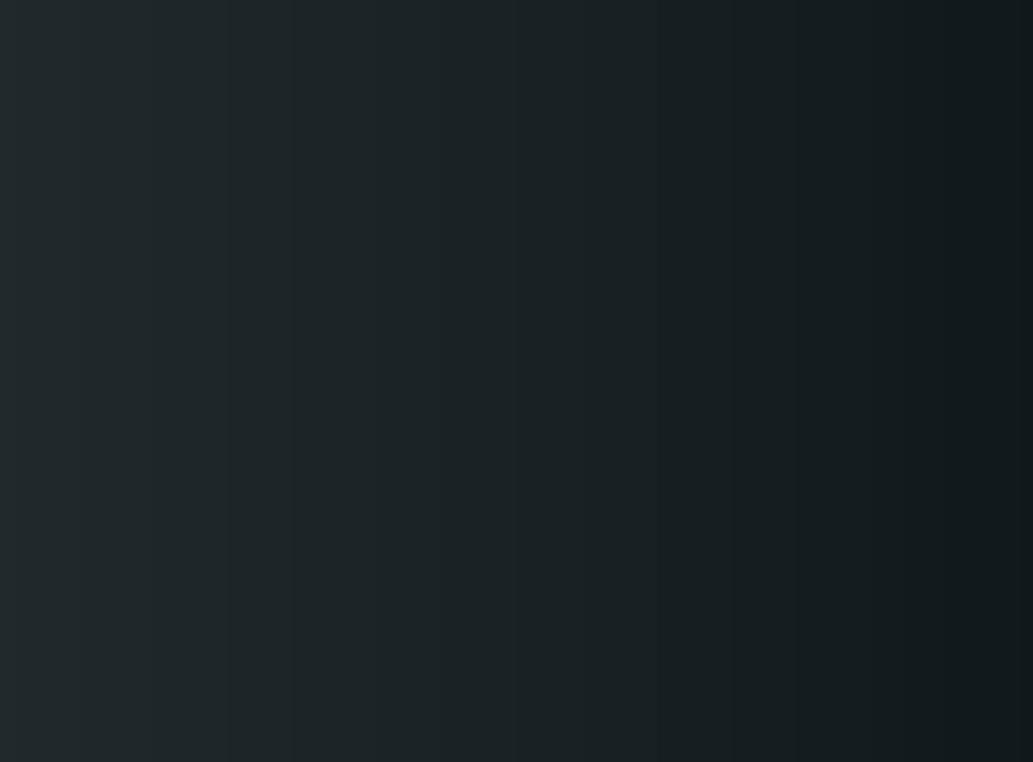
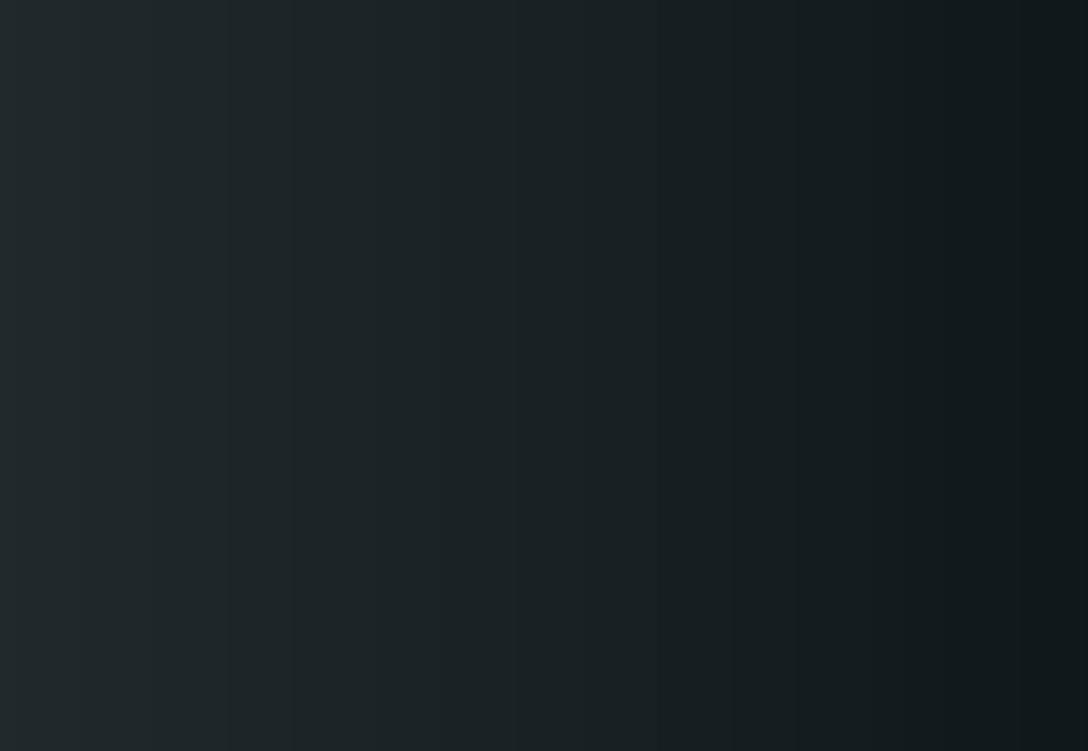
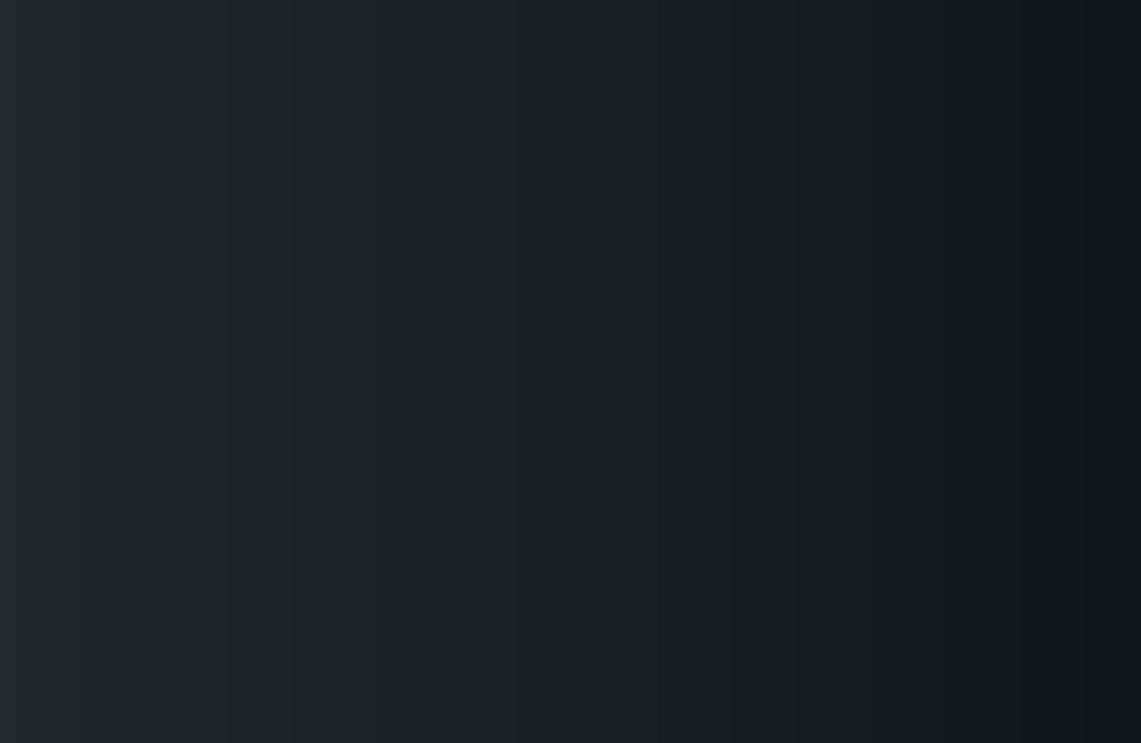
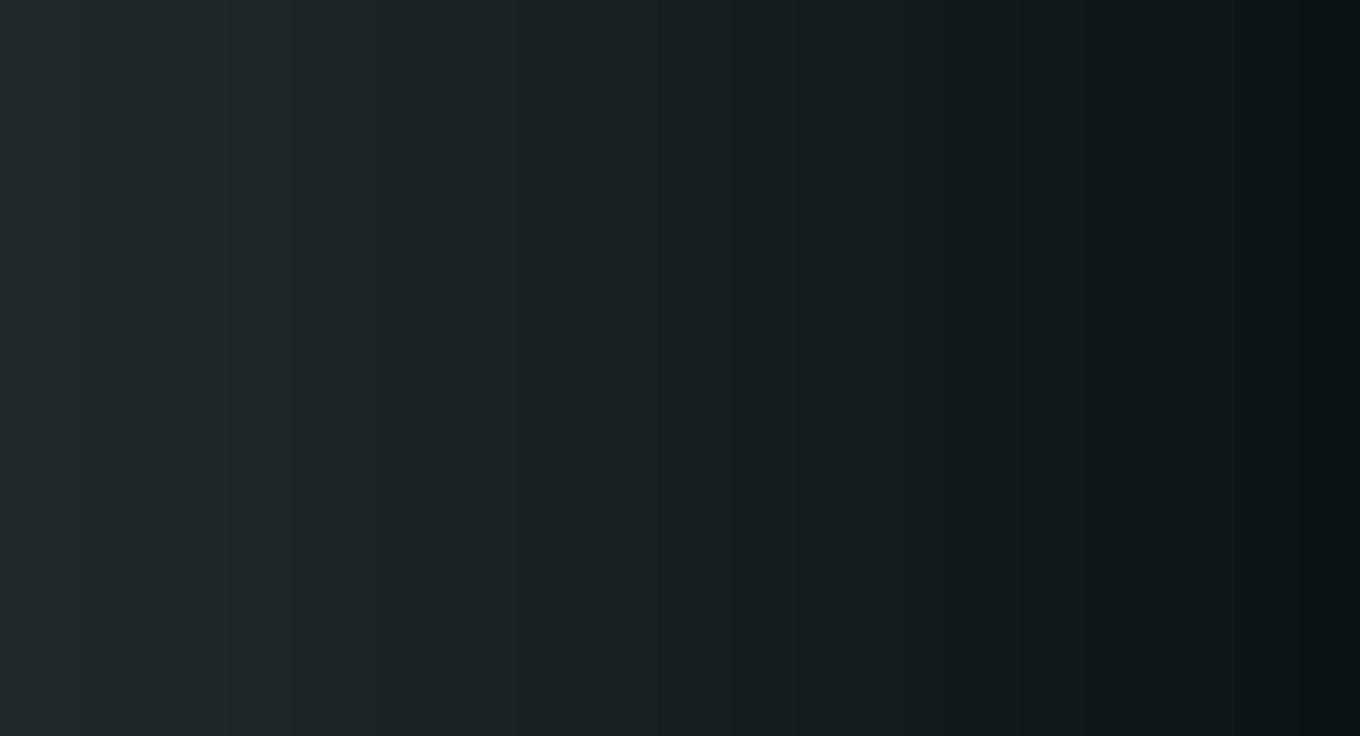
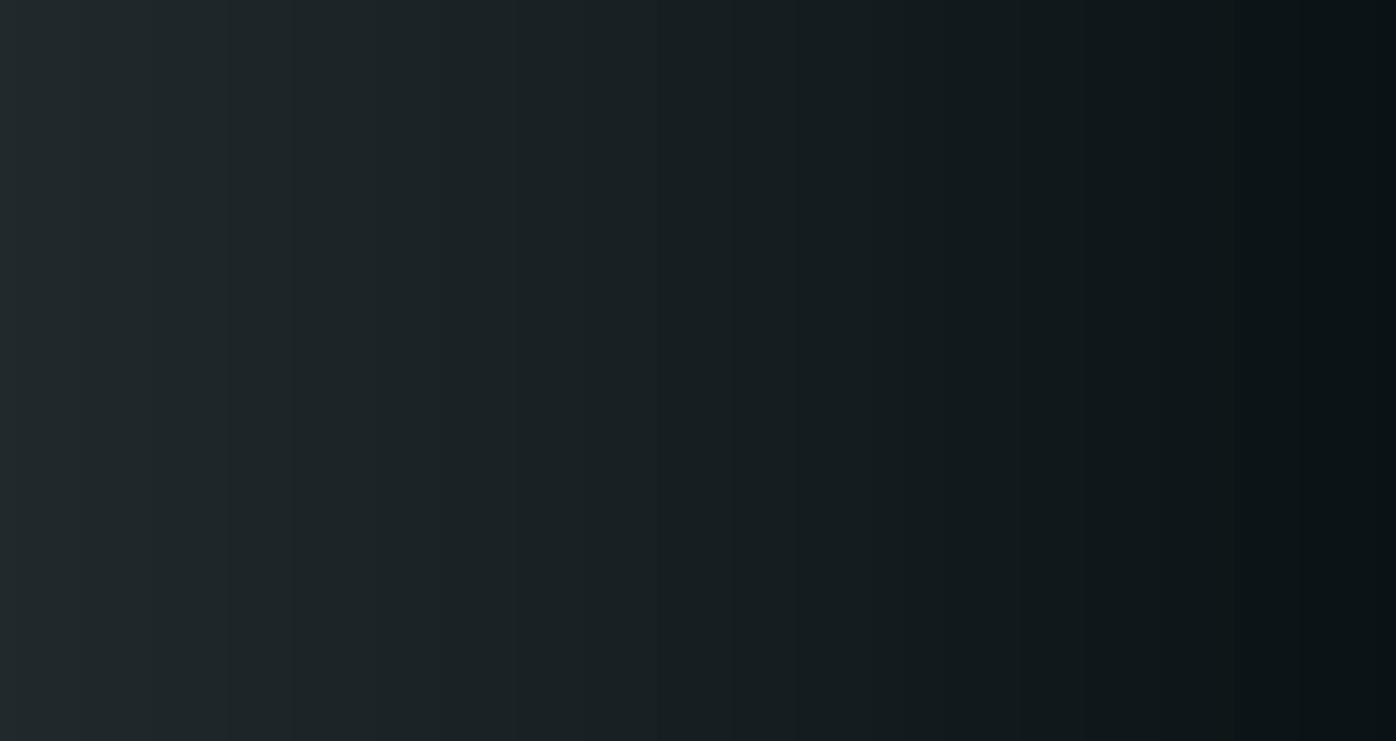
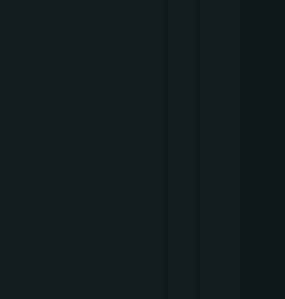
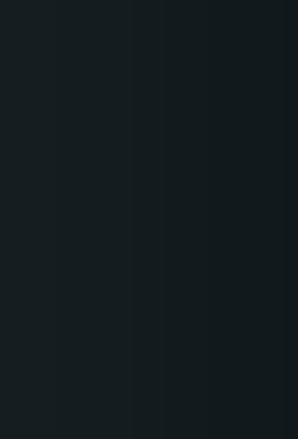
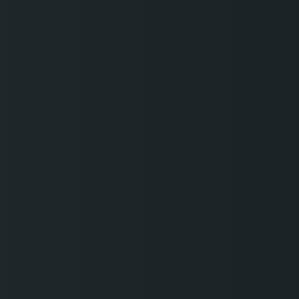

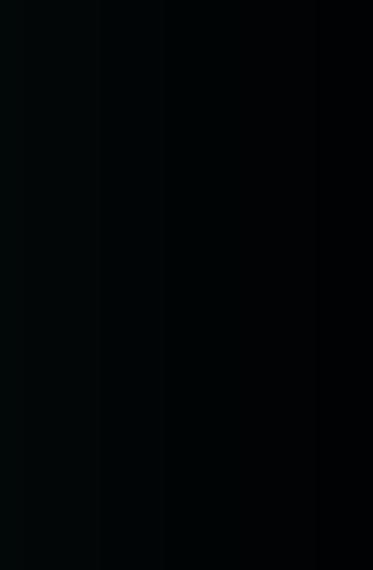
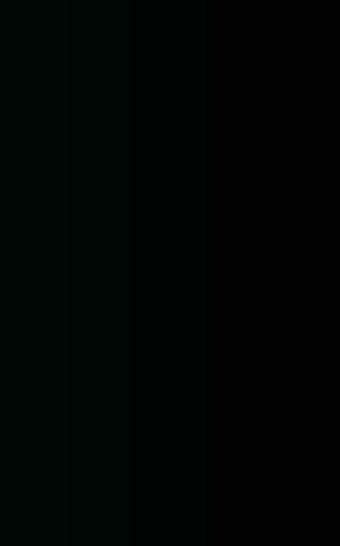
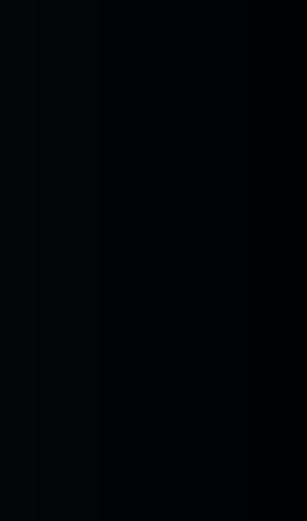
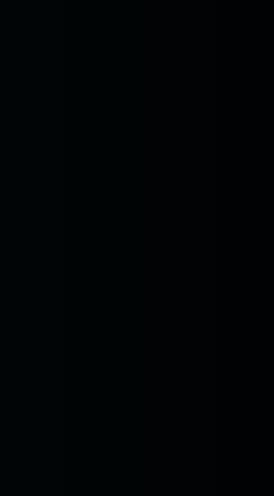
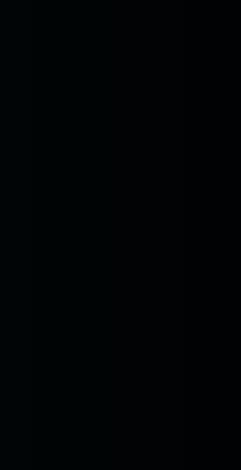
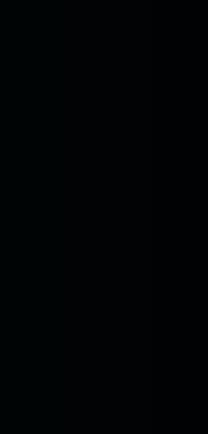
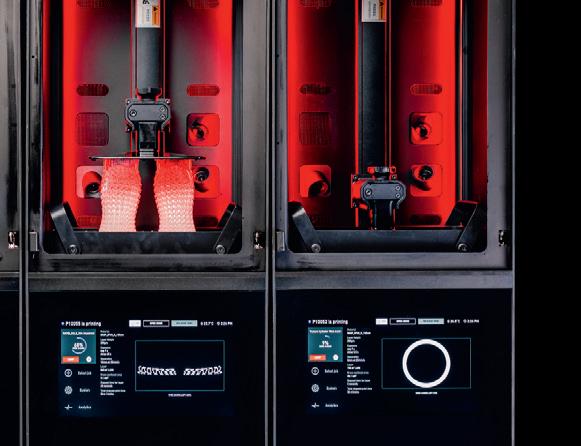
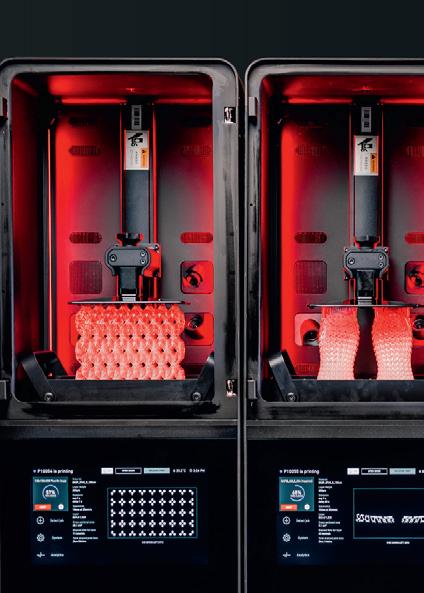
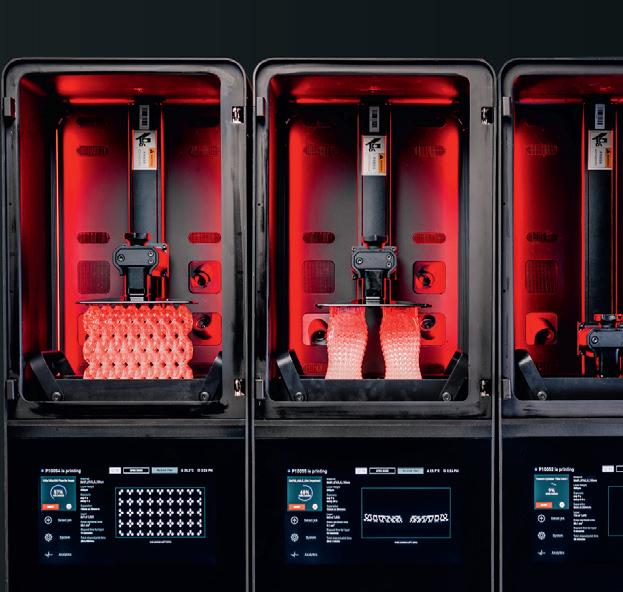
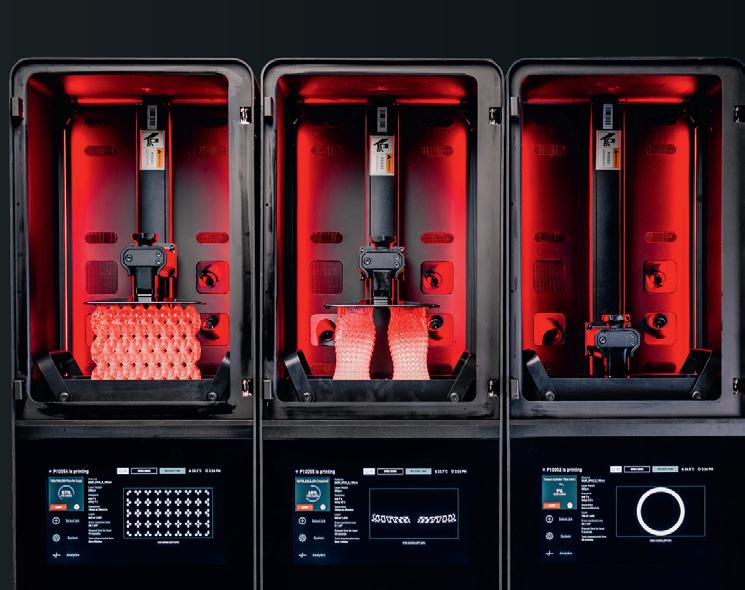
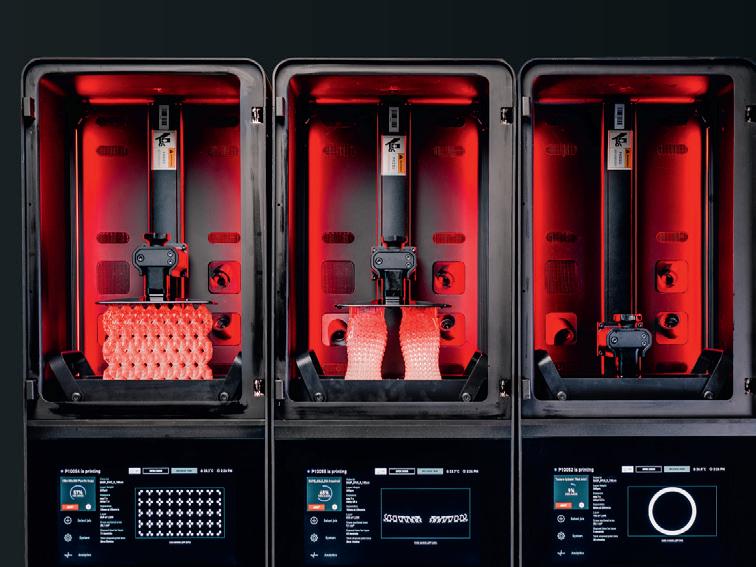
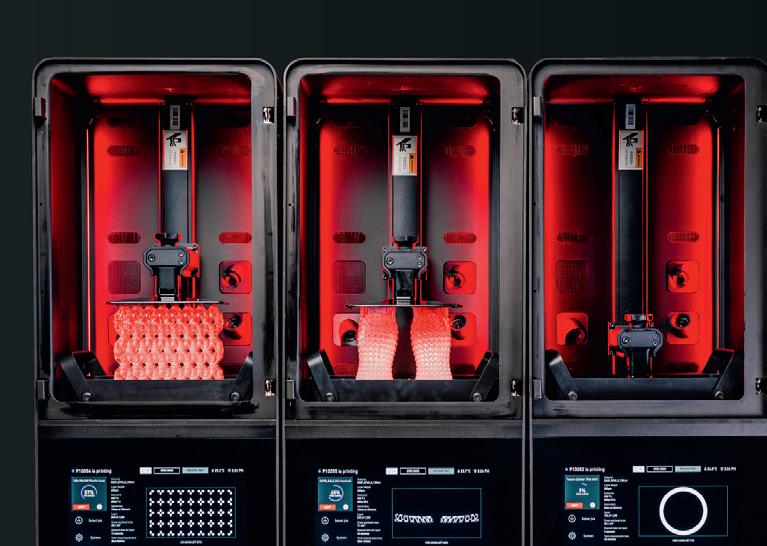
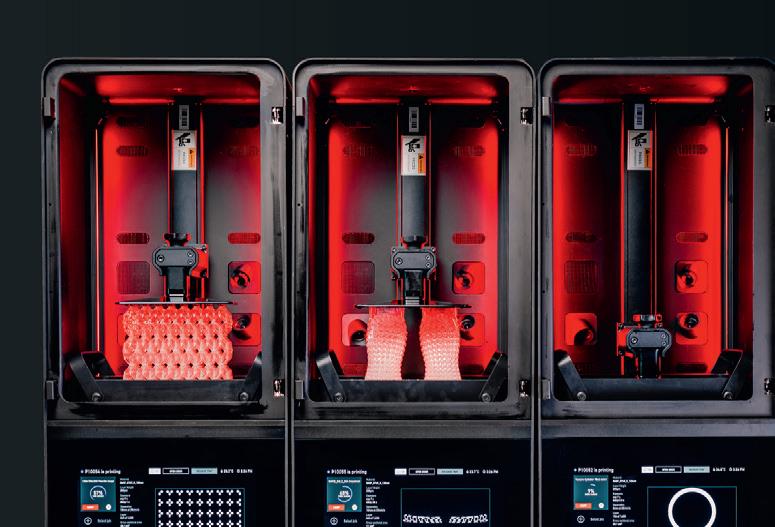
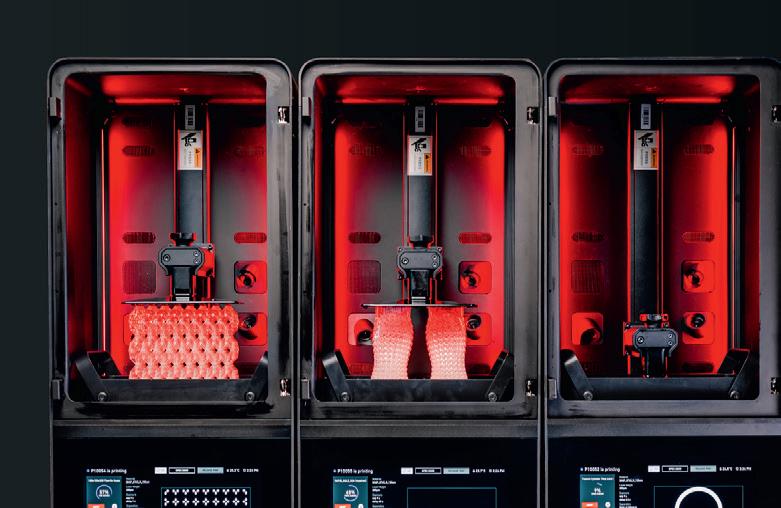
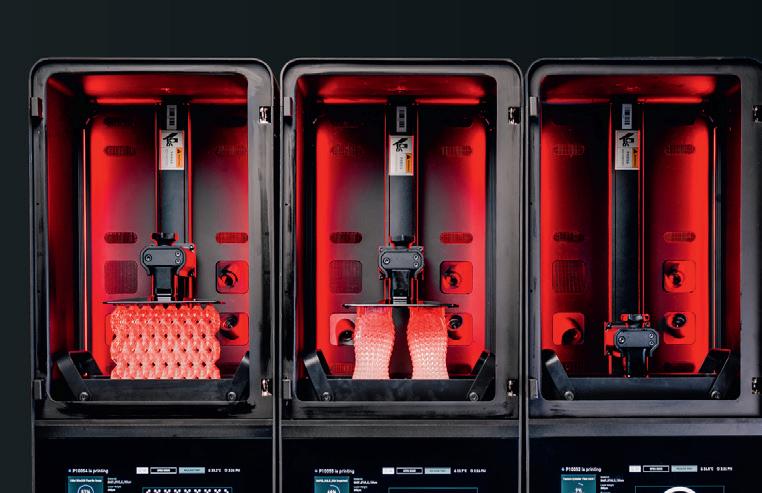
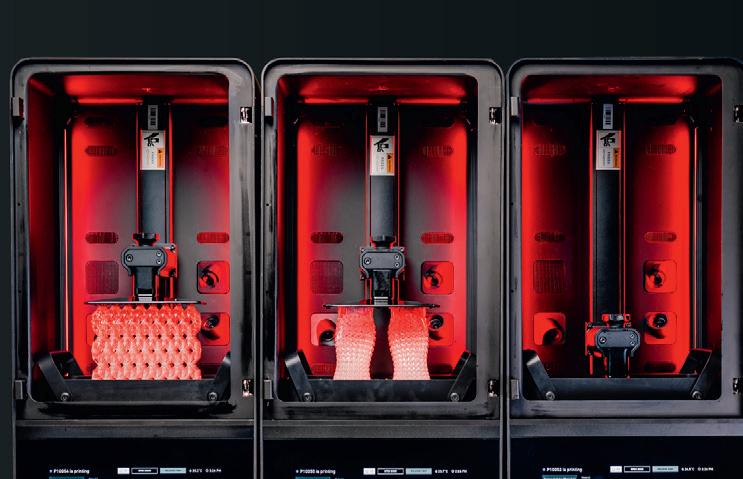
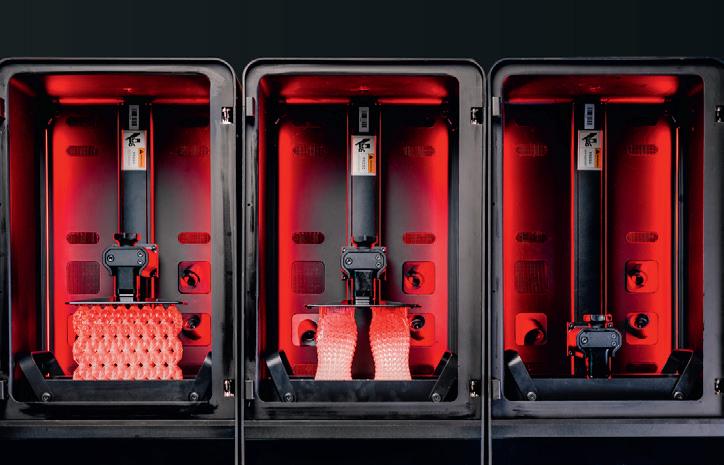
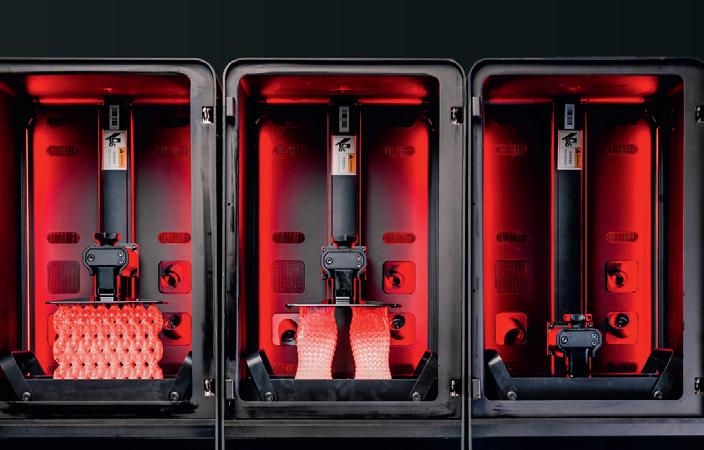
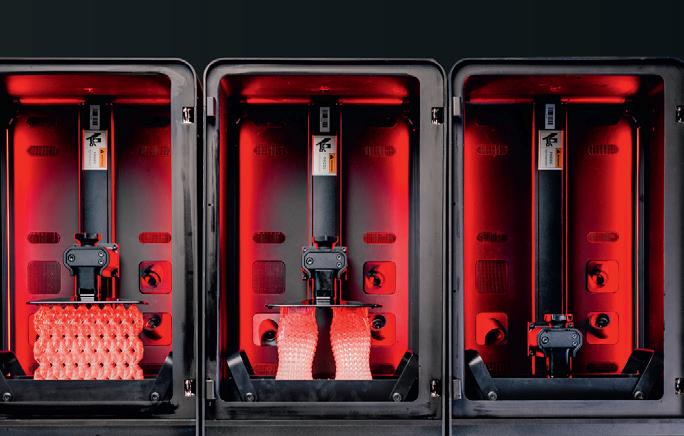
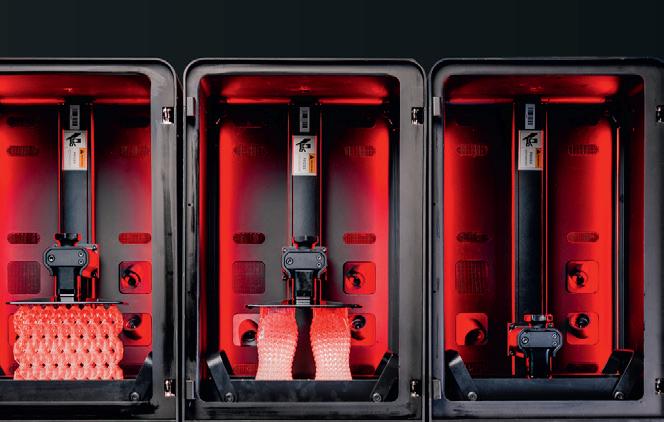
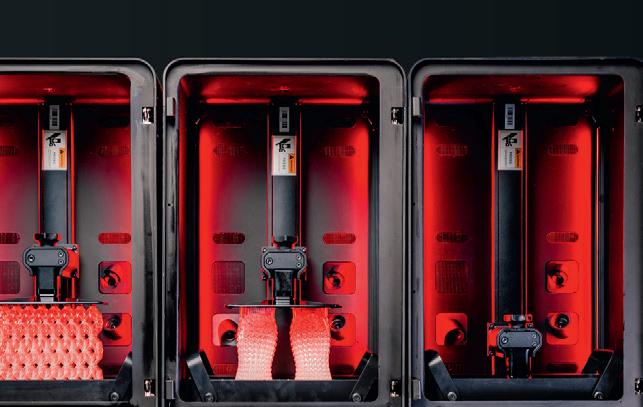
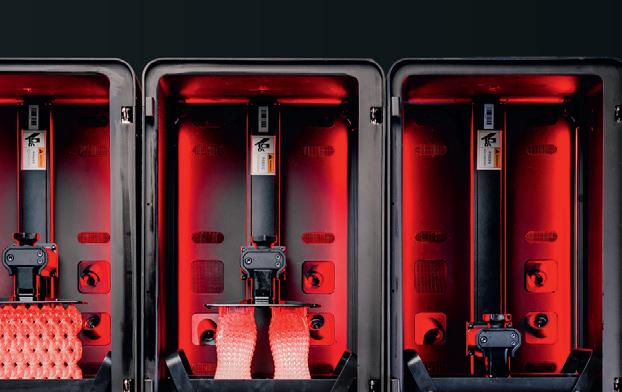
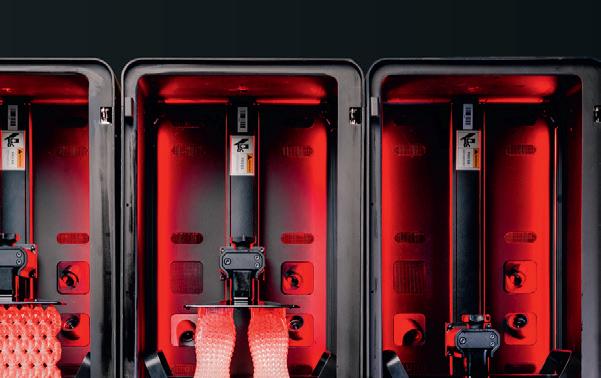
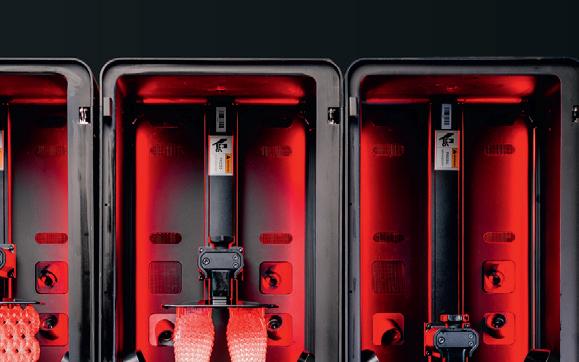
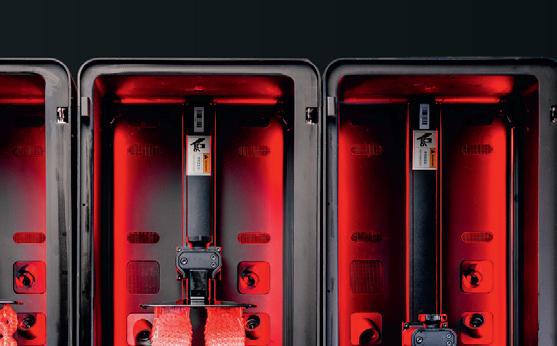
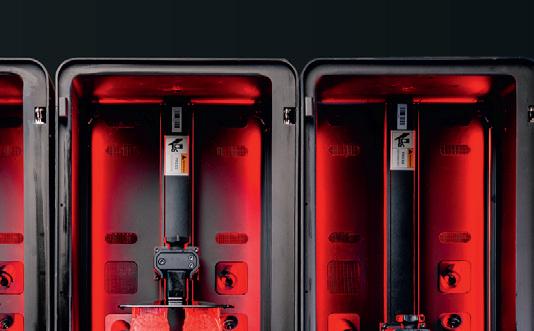
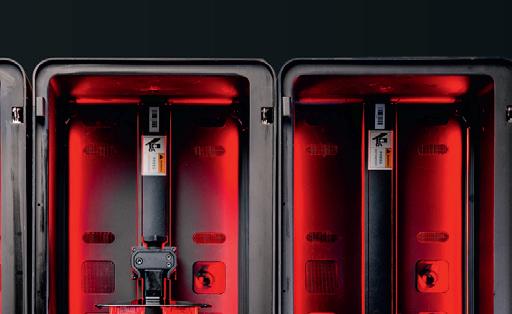
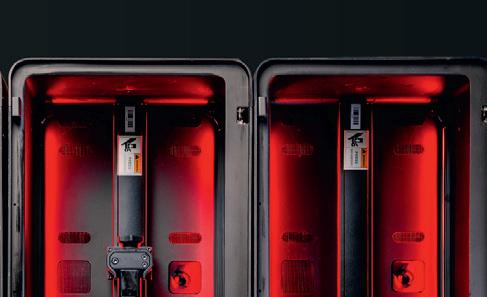
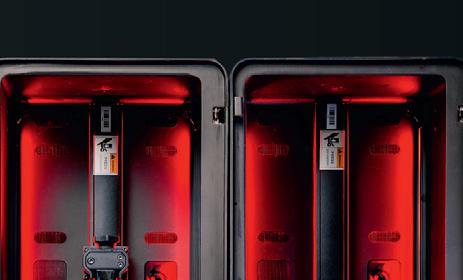
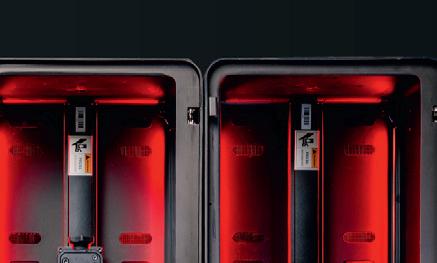
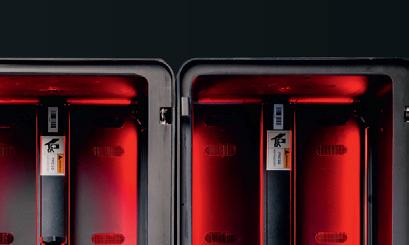
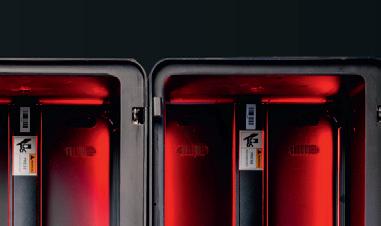
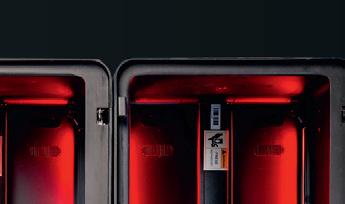

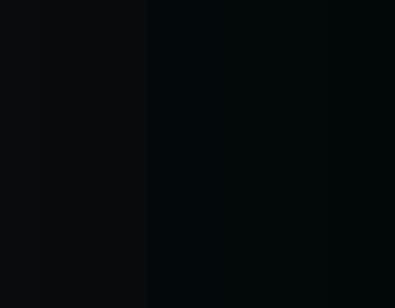
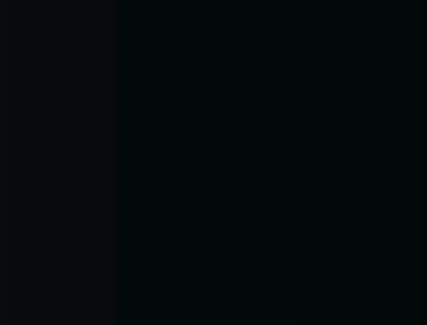
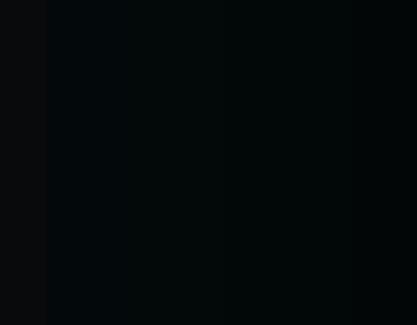
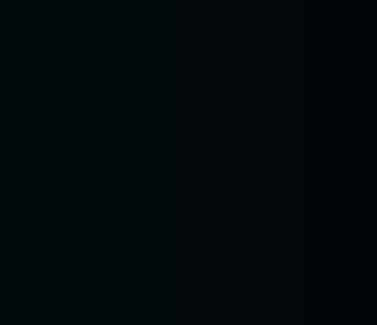
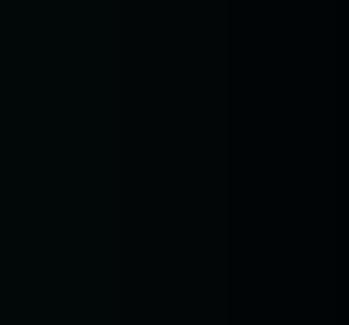
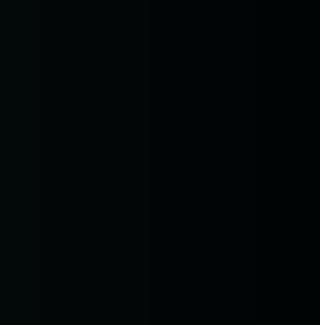
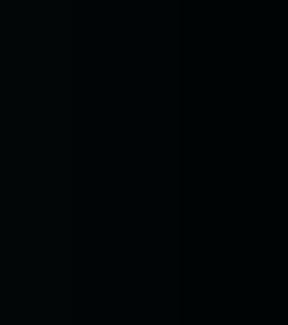
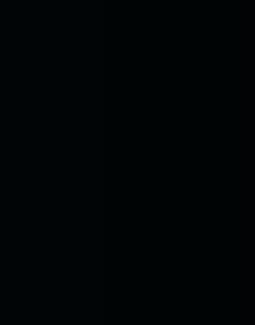
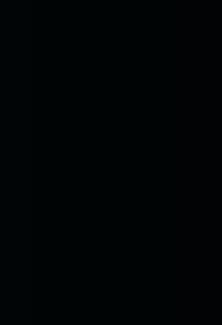
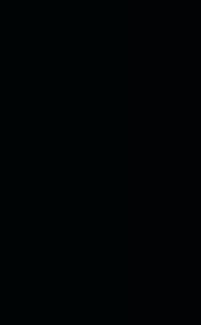
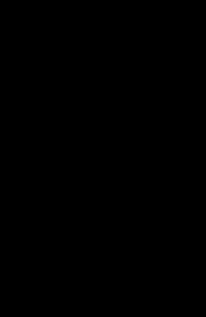
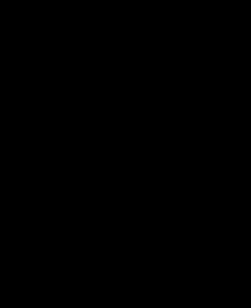
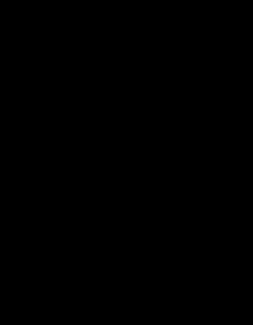
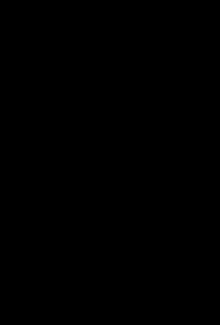
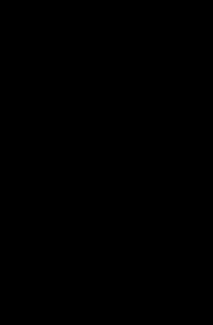
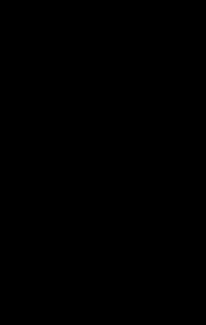
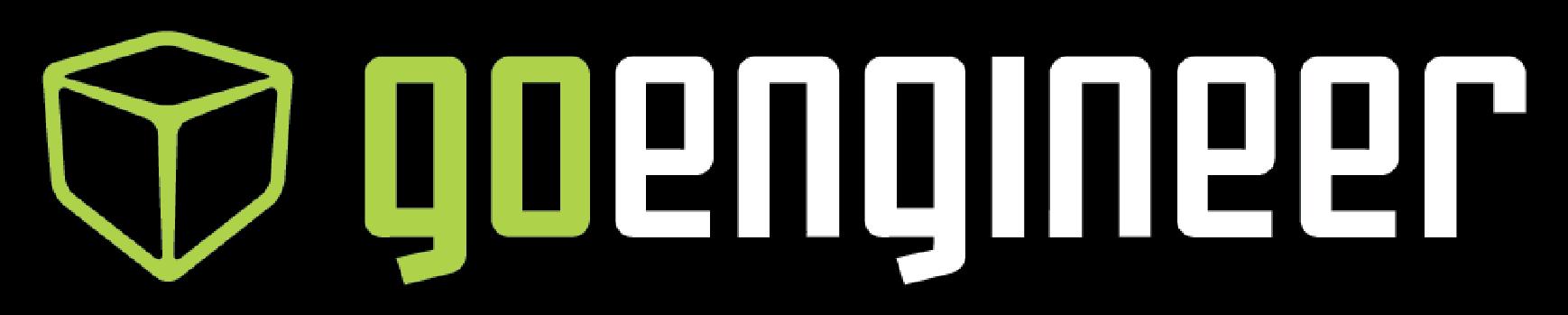
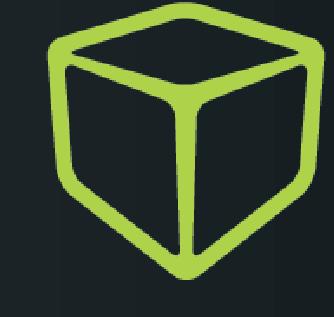
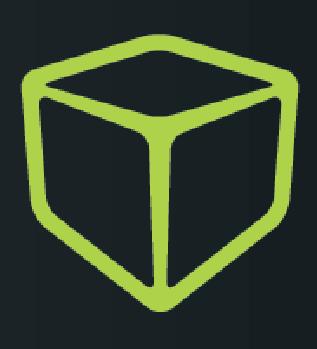
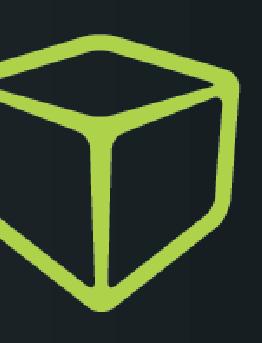
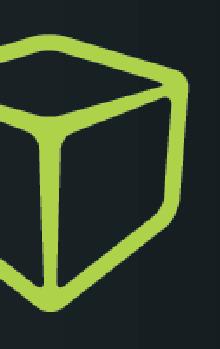
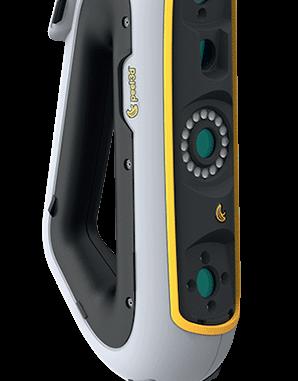
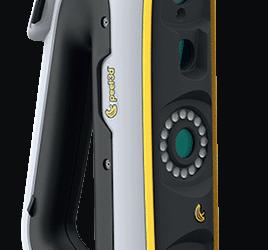
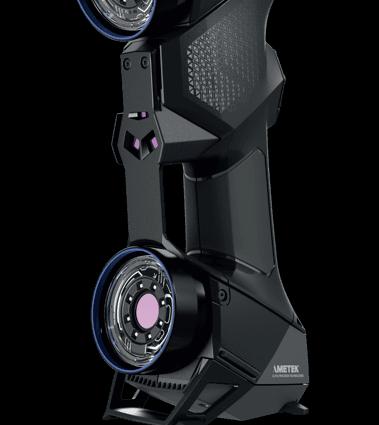
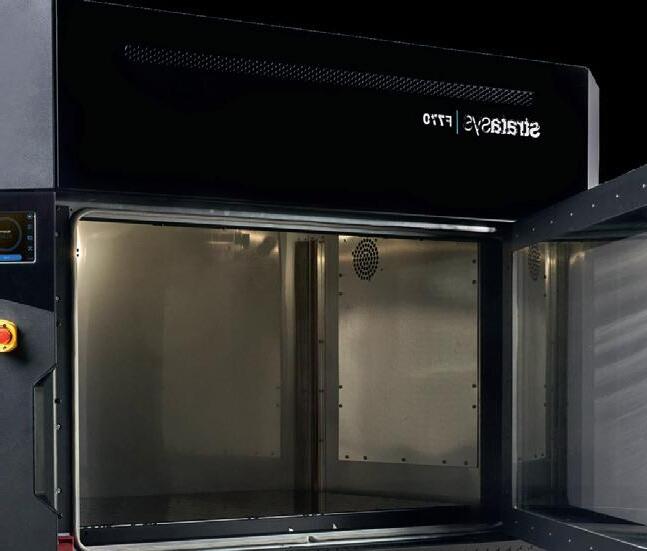

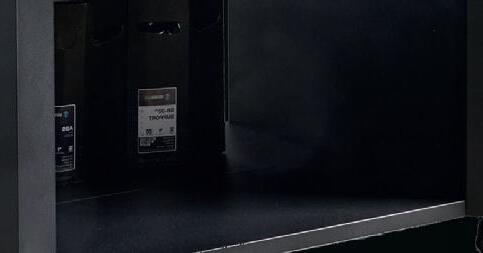
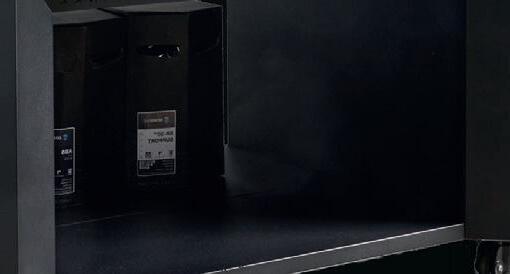
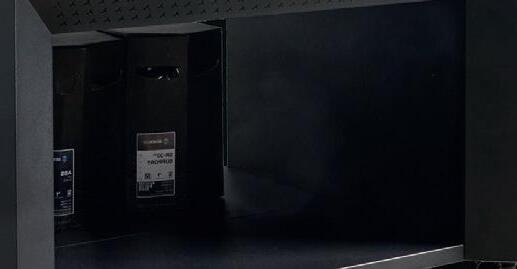
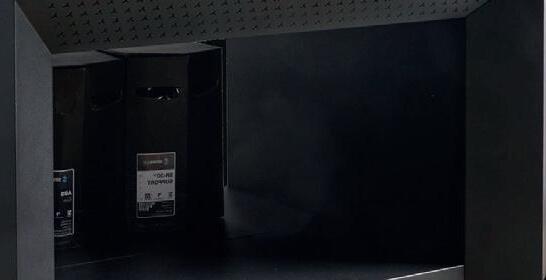
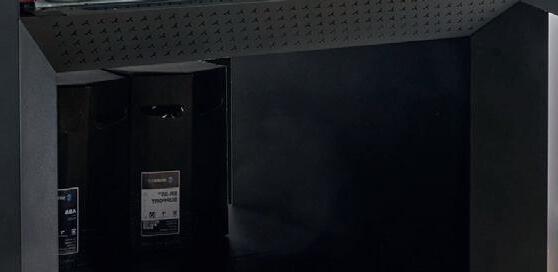
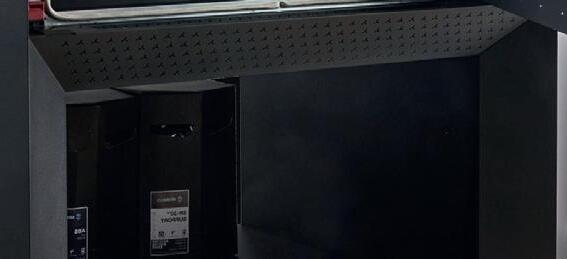
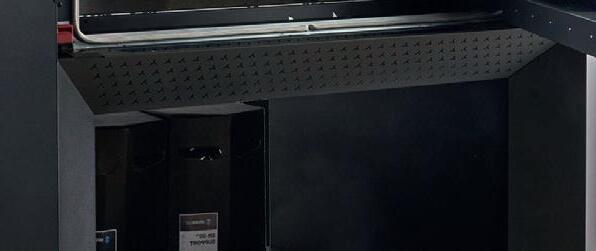
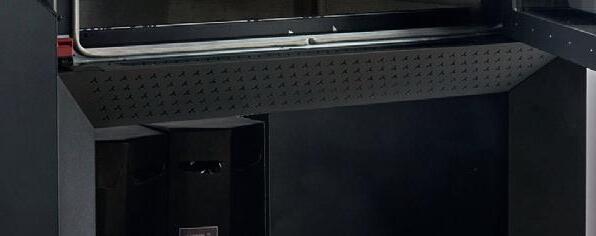
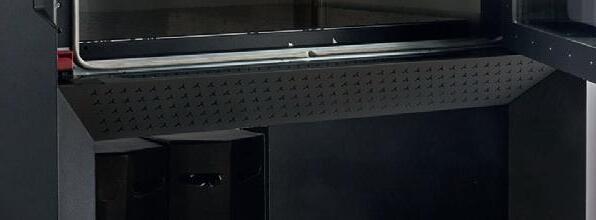
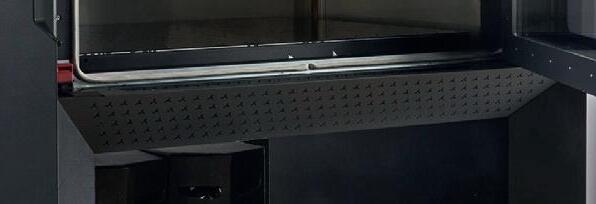
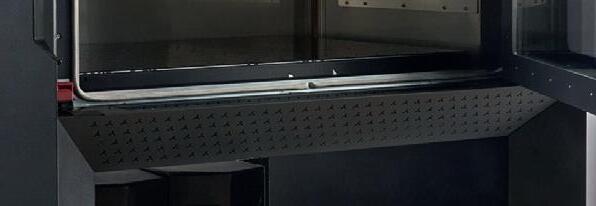
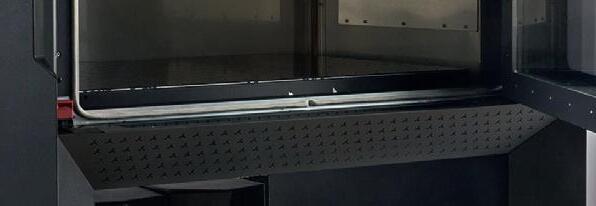
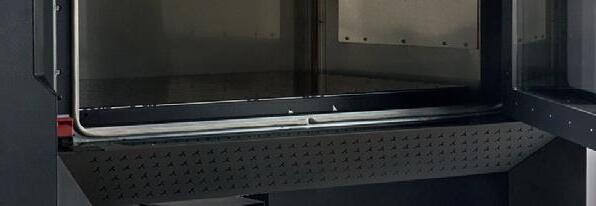
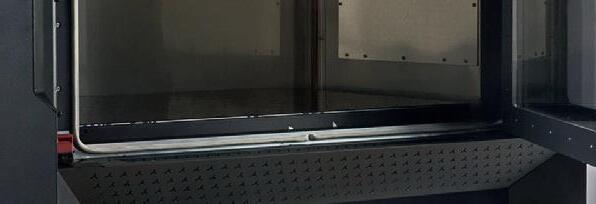
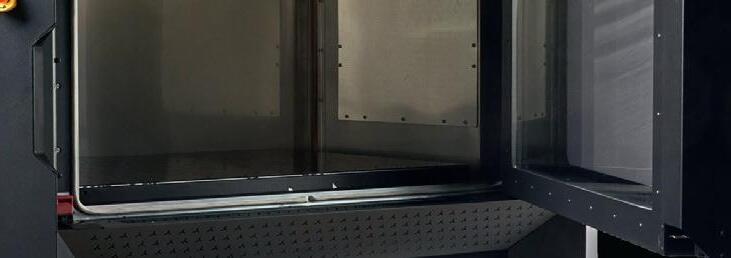
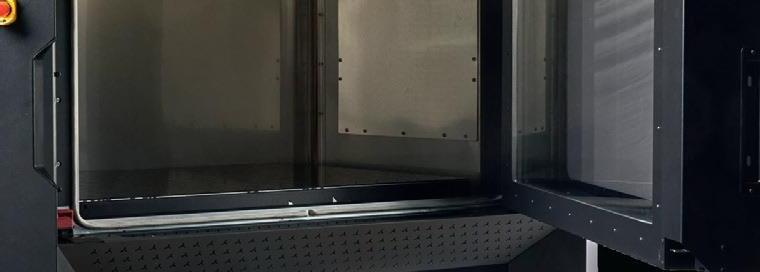
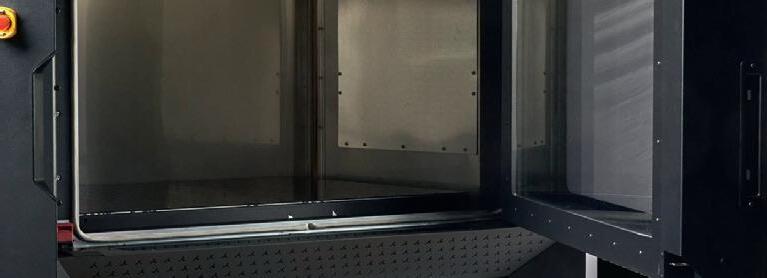
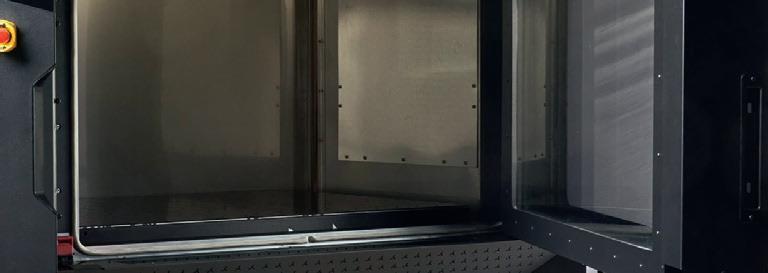
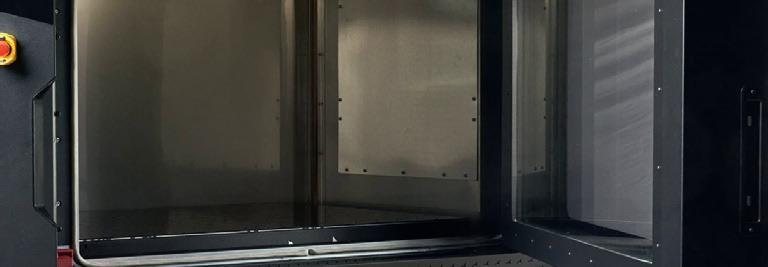
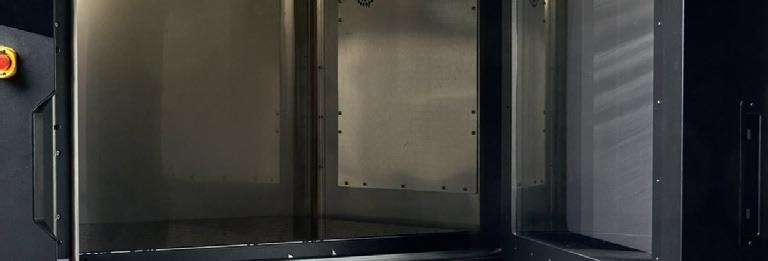
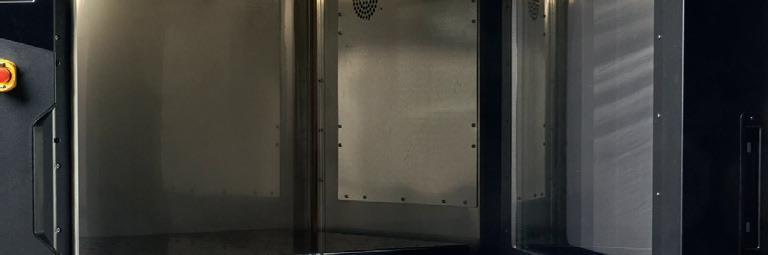
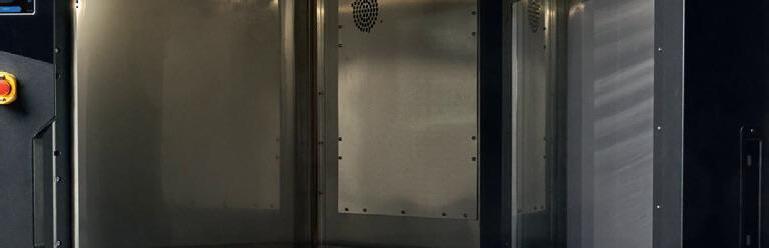
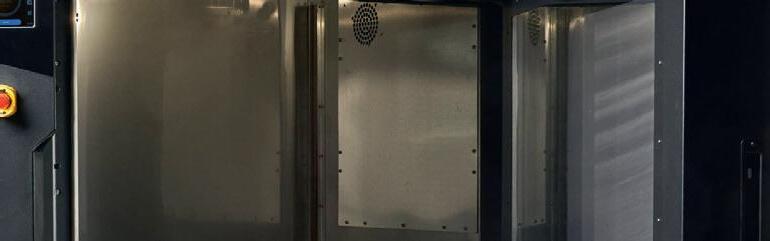
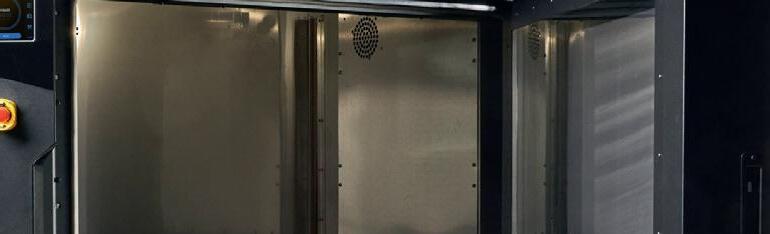
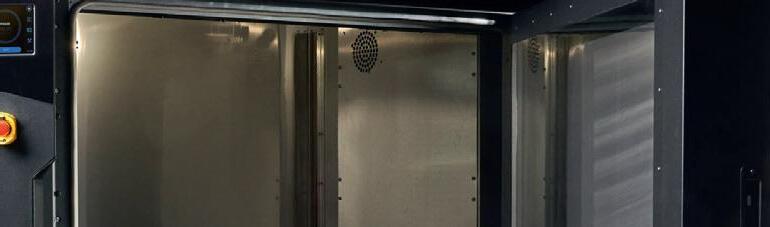
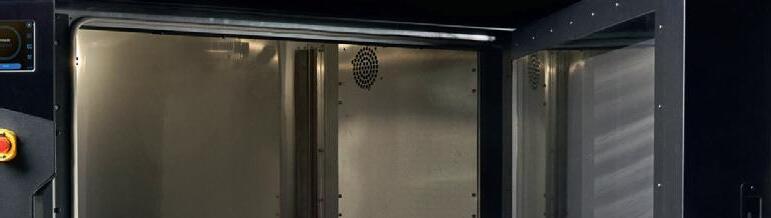
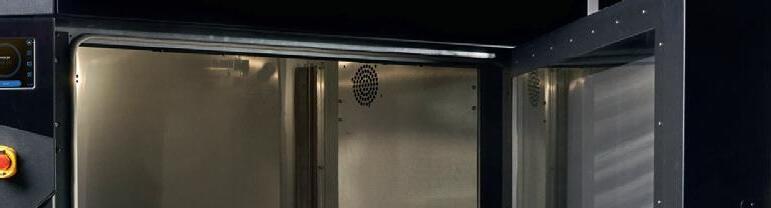
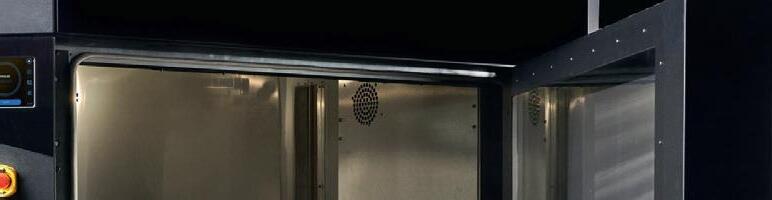
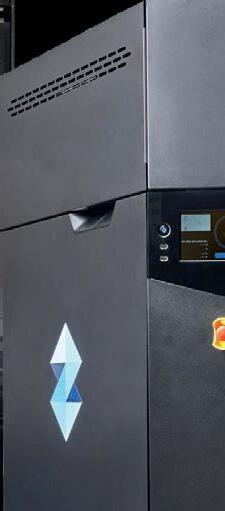
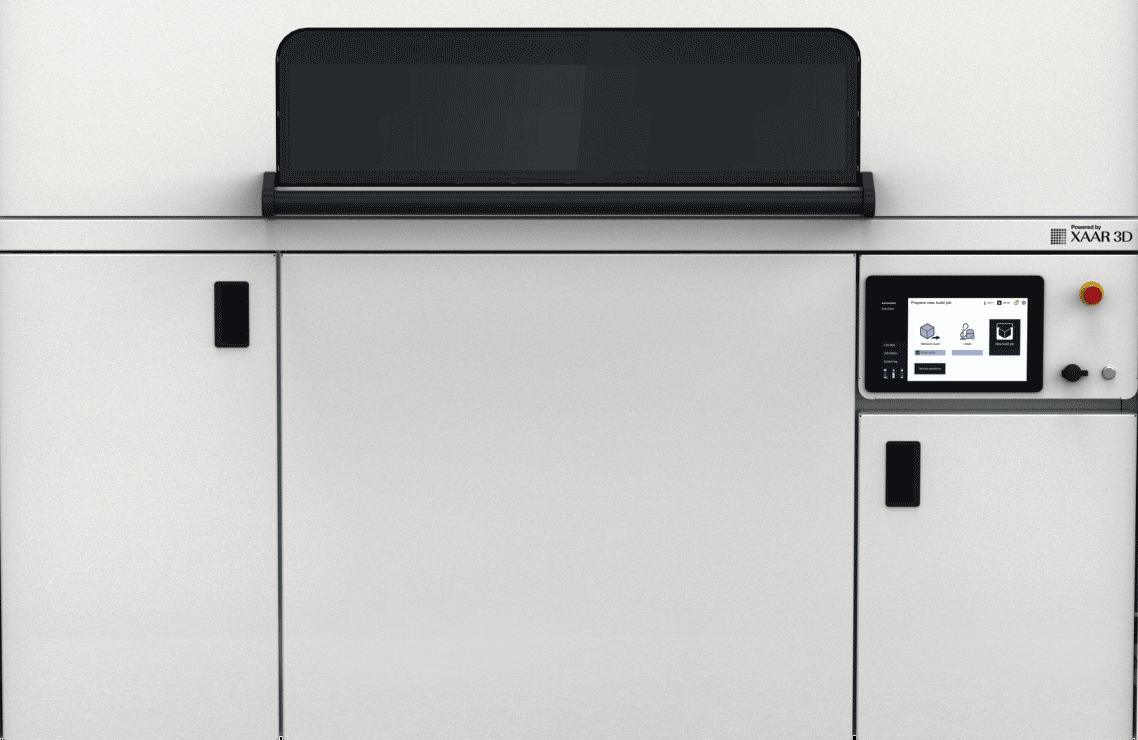
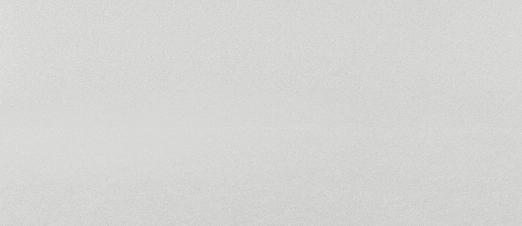
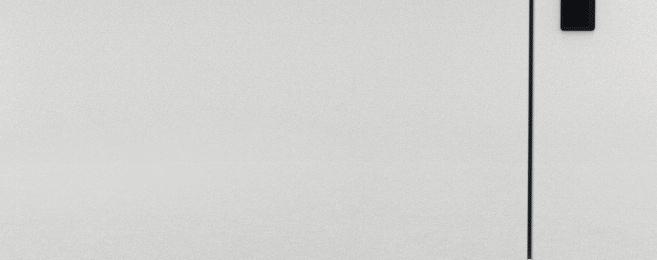
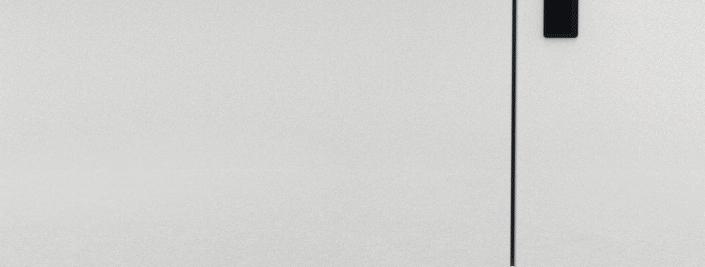
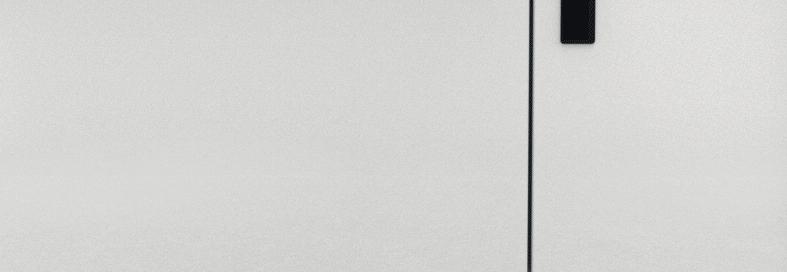
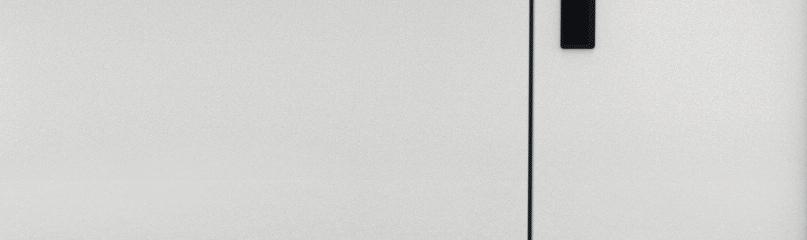
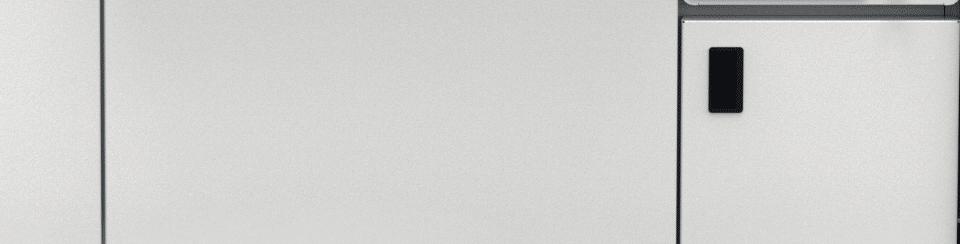
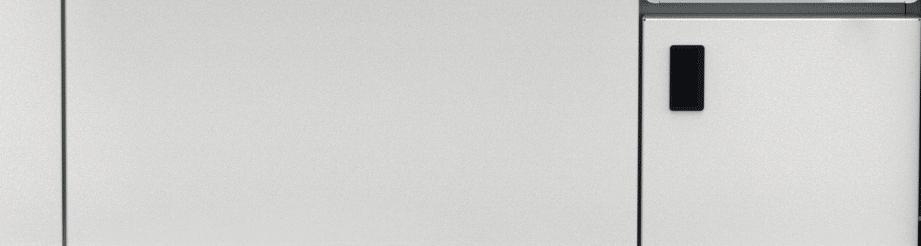
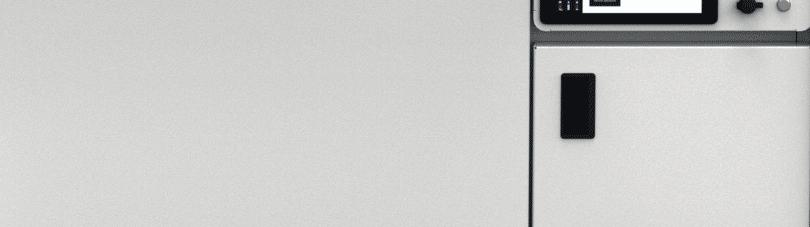
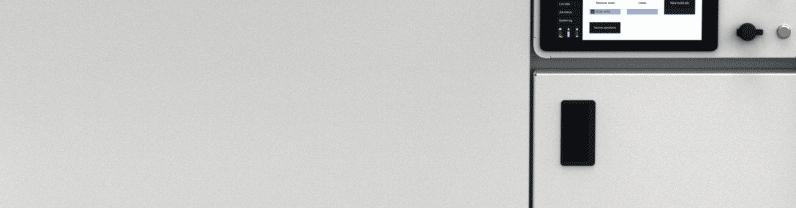
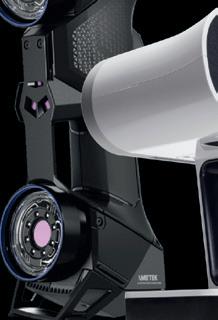
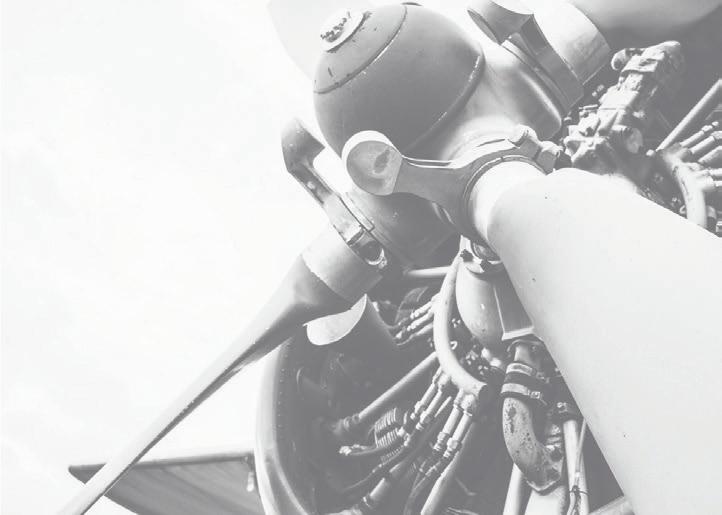
“I think the common thing with all of those [partnerships] is that companies may operate in di erent industries but they're partners to us who share that same passion for technology and quality, that passion for innovation,” Callanan said. “I think that's really what makes those partnerships work very well together. There's a lot of mutual respect for each other's area of expertise.”
Taking a walk through Renishaw’s facility feels like getting a covert behind the scenes tour. I’m waiting for the inevitable ‘no photos, please’ but instead, Renishaw has laid bare its production bay featuring rows of RenAM 500 systems in various stages of completion.
The RenAM 500 is Renishaw’s flagship machine. It can be equipped with one or four 500W lasers across its 250mm x 250mm x 350mm build platform, but all configurations adopt the same gas flow system, safety and precision digital optics, and smart connectivity capabilities. While eight, even 12-laser systems are now not uncommon in additive (Callanan doesn’t reveal if this next generation will follow a similar trajectory), Renishaw was one of the first companies to introduce a multilaser system of this size back in 2017 and has quietly iterated on features like automatic and flexible powder and waste handling options, and intelligent software solutions ever since.
“We know that we don't want to rest on our laurels and we do need to make sure that we remain competitive,” Callanan said. “And that means that we need to continue to ensure that we're also delivering quality parts in a cost-e ective way. So we're continuing to work on projects to improve the usability, and to improve the productivity of the current 500 platform.”
The RenAM 500 Flex has been designed to allow for easy switching between material types and was first put to work at the UK’s Digital Manufacturing Centre to verify its capabilities in a commercial production environment. In November, the Royal Air Force announced it would be using the system to produce custombuilt structural aircraft components for rapid repairs and advanced component manufacturing, a first for the organization.
“One common vision for everybody in AM is the adoption of additive manufacturing as a viable high volume production technology. And we're no di erent there, certainly from a next generation perspective. That's where we're really focused and really looking to make a step change in that productivity benefit and cost per part and looking to open up that additive technology to more applications.”
While the ‘what’ and ‘when’ around Renishaw’s next move in additive remains untold, the ‘where’ is not so closely guarded. Last Summer, Renishaw announced an investment of around 65 million GBP to almost double the footprint of its Miskin site and help meet its weighty Net Zero emissions targets. Its ambitions include the development of 400,000 sq ft of low-carbon buildings that will house a new production hall for its AM machines. We’re invited to get a peek from the top floor of its current site that’s currently tightly packed with an orchestra of machining, electronics, precision and large equipment assembly operations downstairs.
“Our strap line is ‘apply innovation’ and I think it's definitely more than just a strap line,” Callanan said. “It's something that's completely embedded within the company and it gives us that ability to challenge the status quo, to always be pushing technology innovations forward and really looking at the future in terms of the long term.”
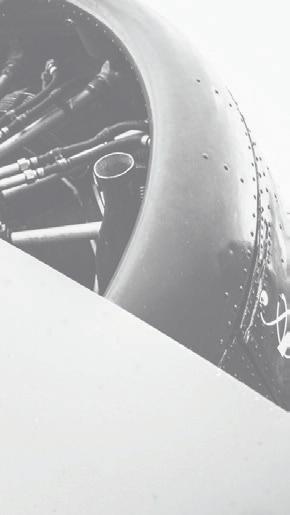
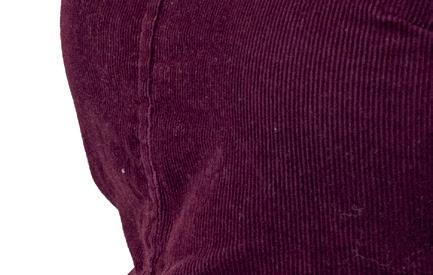
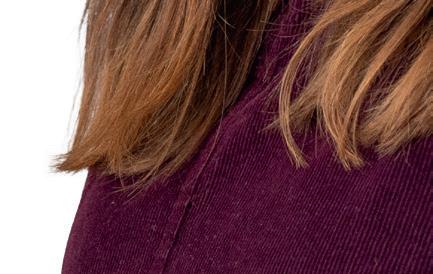
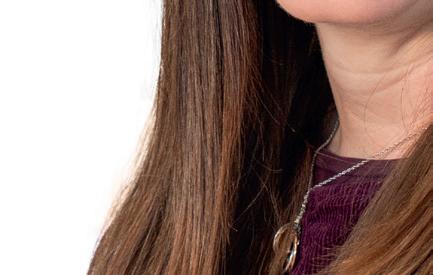
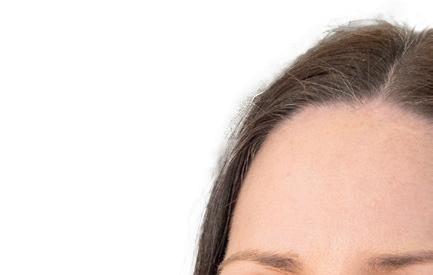
What that means for additive in particular, we’ll have to wait and see, but Callanan says its success in AM won't be just about the machines.
“We're a part of the Renishaw family, we can o er that end-to-end process and I think that really is where we bring something di erent than anyone else. So whilst AM seems relatively new, for Renishaw, we're in our 12th year at this stage, so we're not really the newbies anymore, and our long-standing history shows that we have got that track record of sticking with new technologies that we believe in. We're just a member of the Renishaw team. That's how we see it, we see it being an area that will continue to grow, and we will definitely establish ourselves at the table alongside our more traditional manufacturing technology product lines, industrial metrology and position measurement. But I think the key thing for us is the overall success and growth of Renishaw, which we're very confident about.”
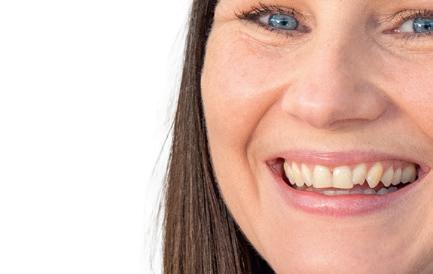
From
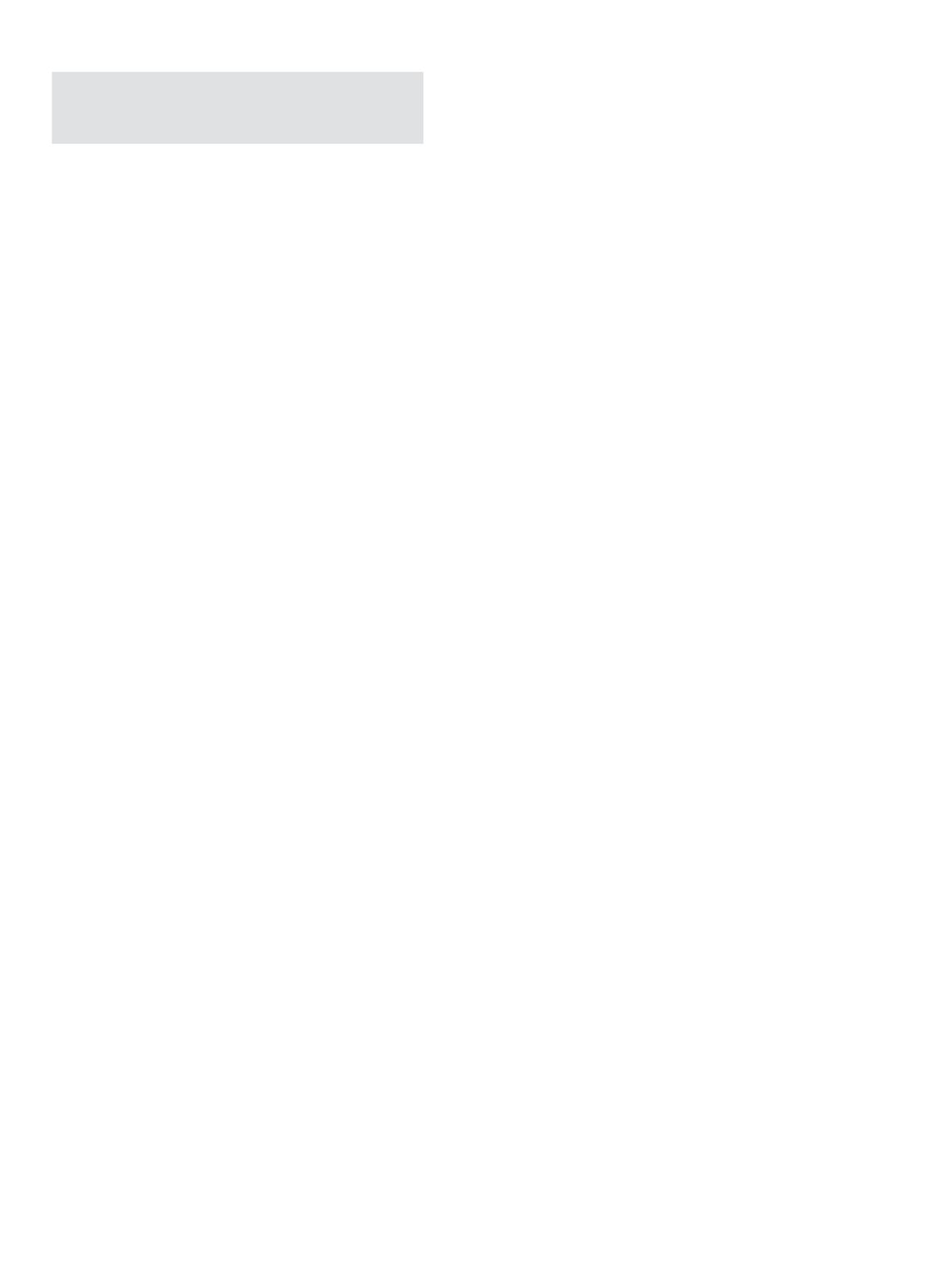
To
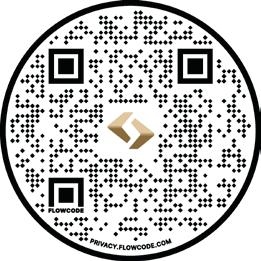
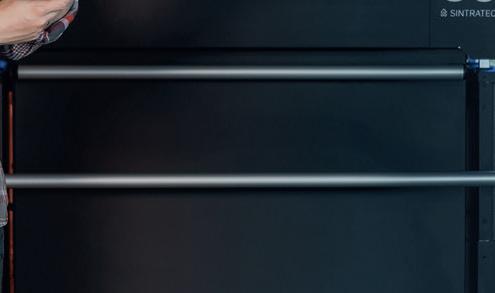
Printing parameters are the basis of additive manufacturing to produce defect-free parts. ZEISS AM parameter enables rapid development or optimization of parameters for new alloys, increased layer thickness and deformation-free parts. zeiss.com/metrology additive@zeiss.com
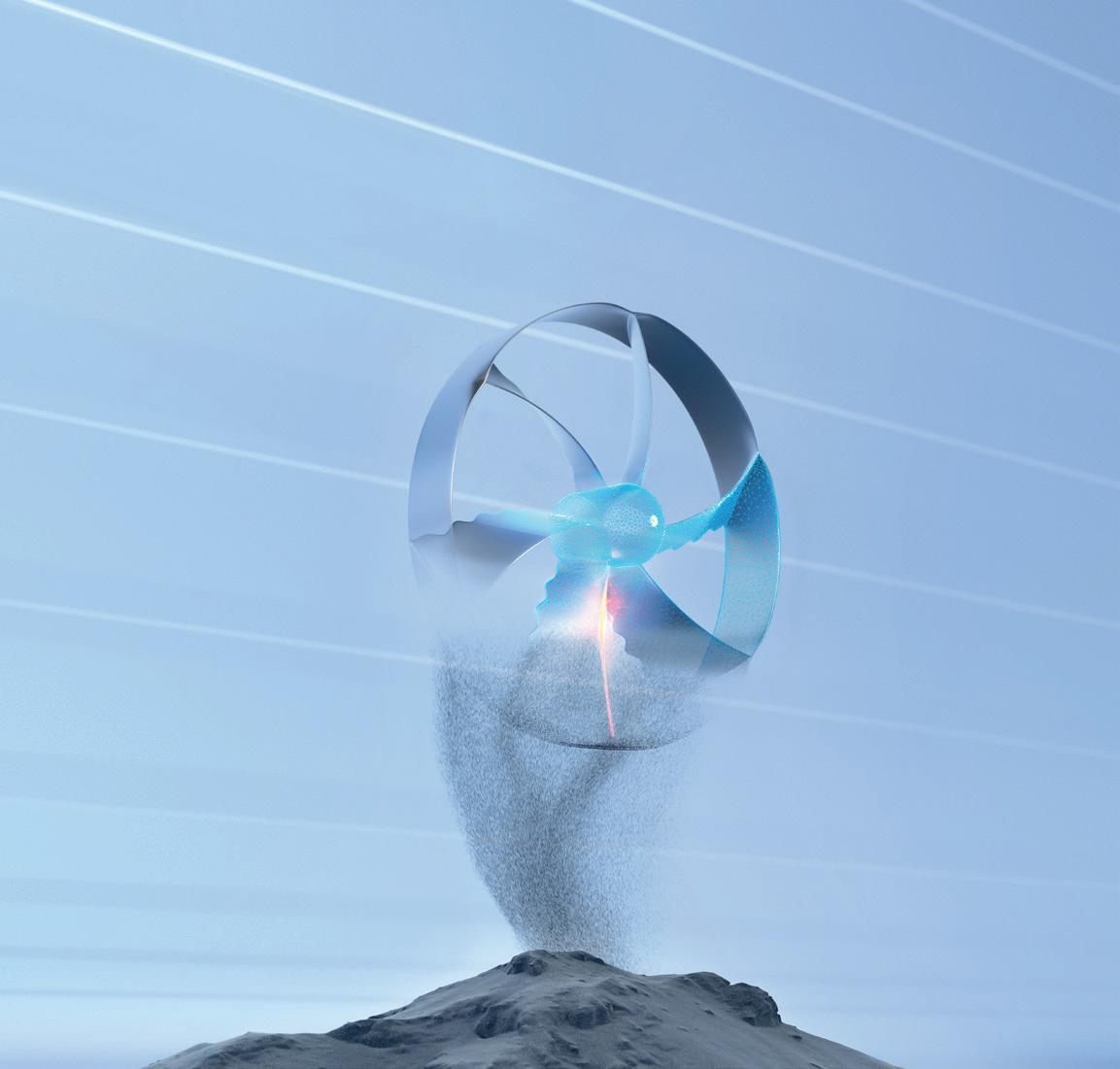
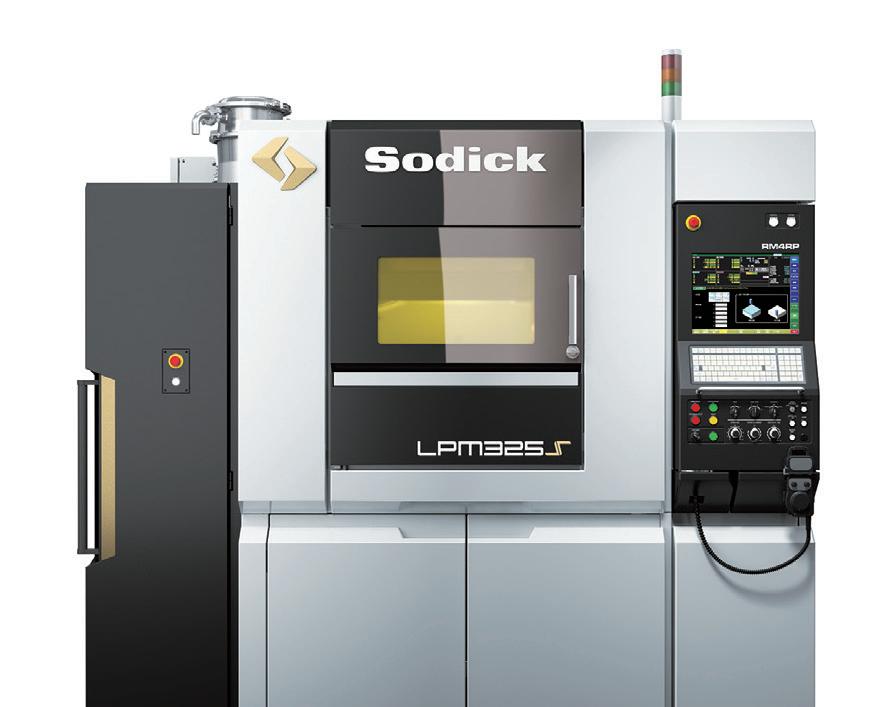
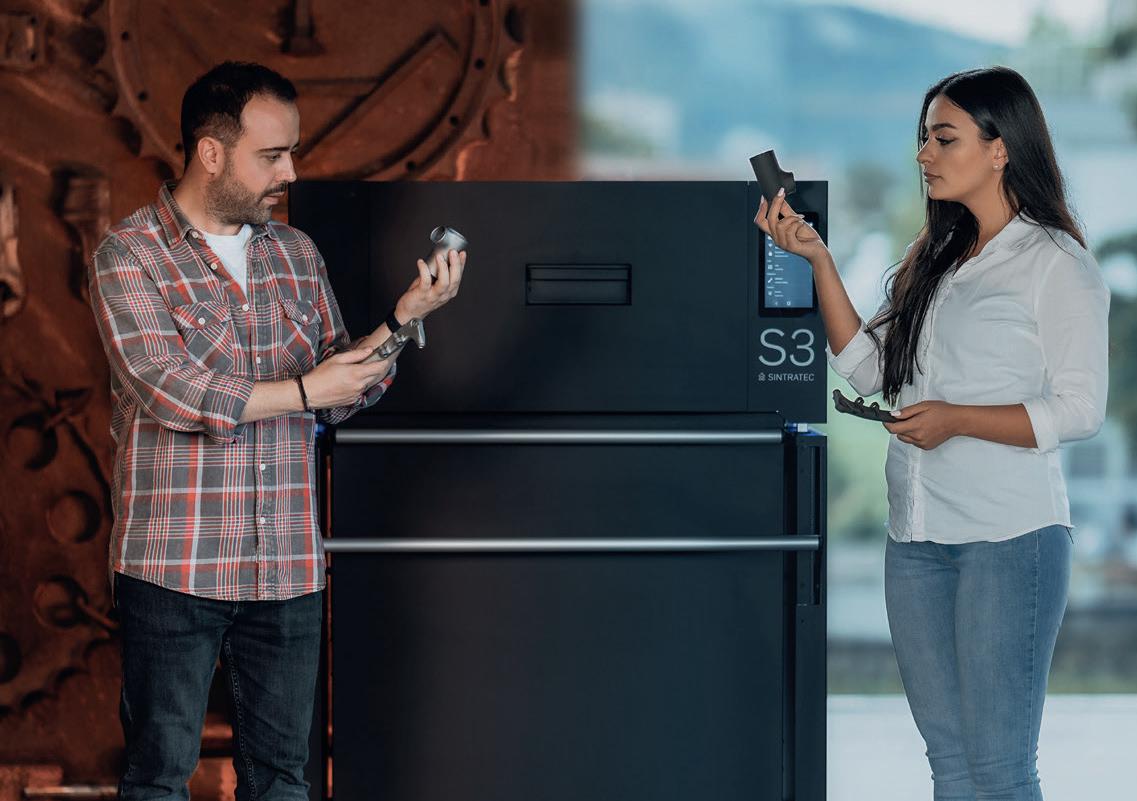
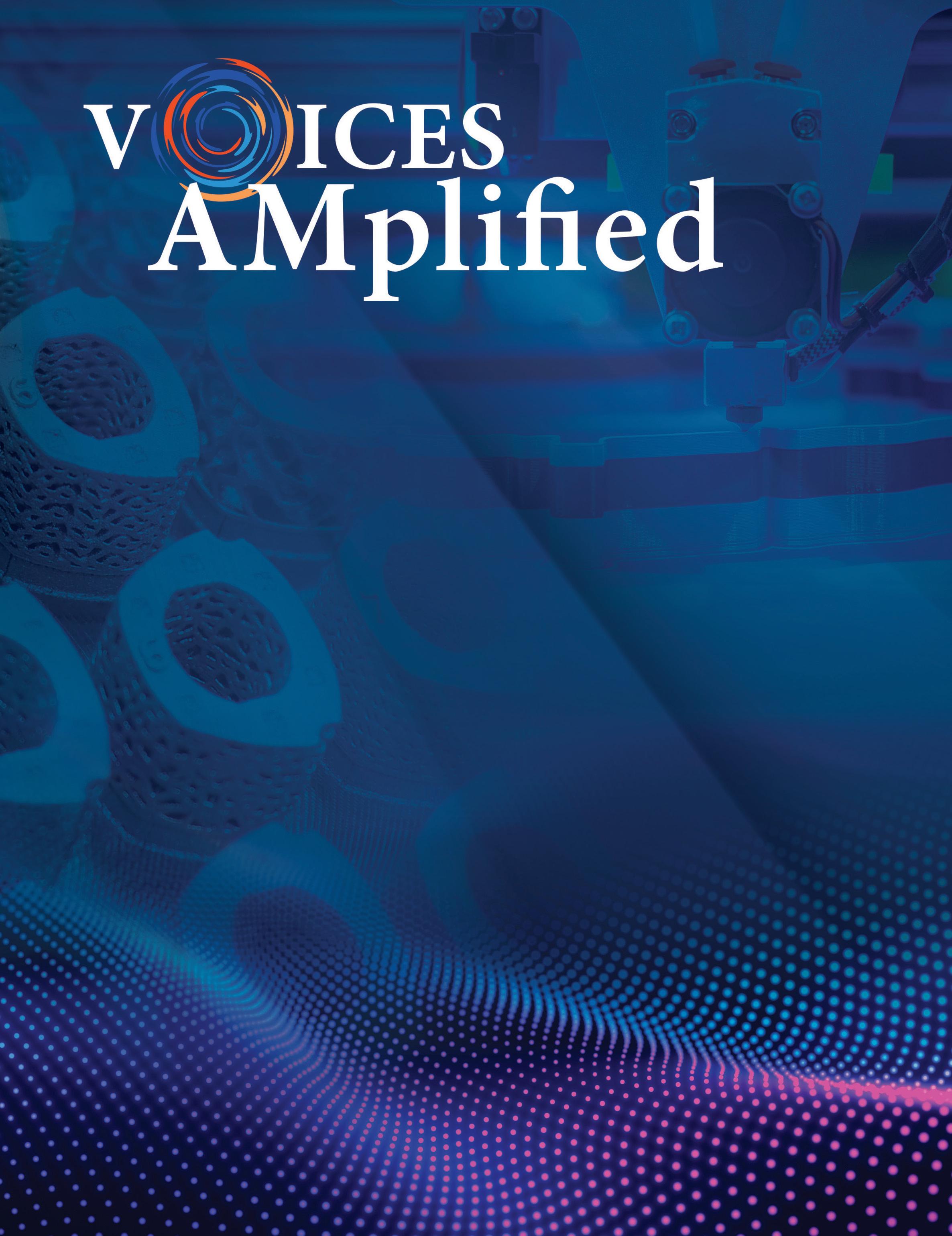
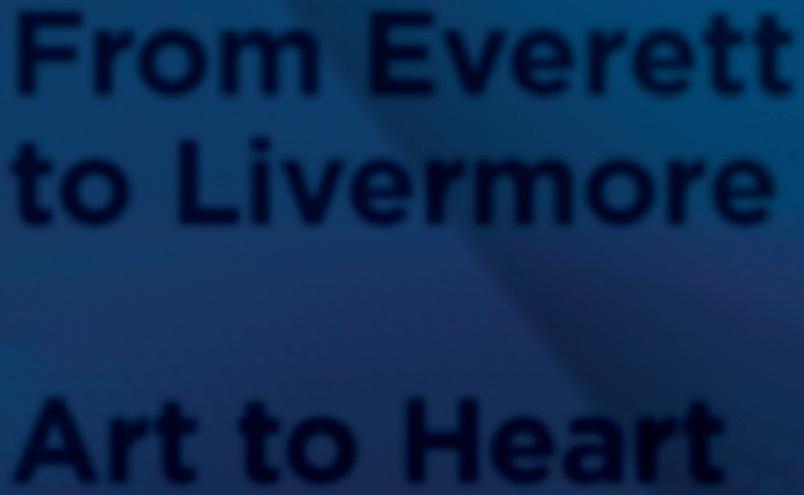