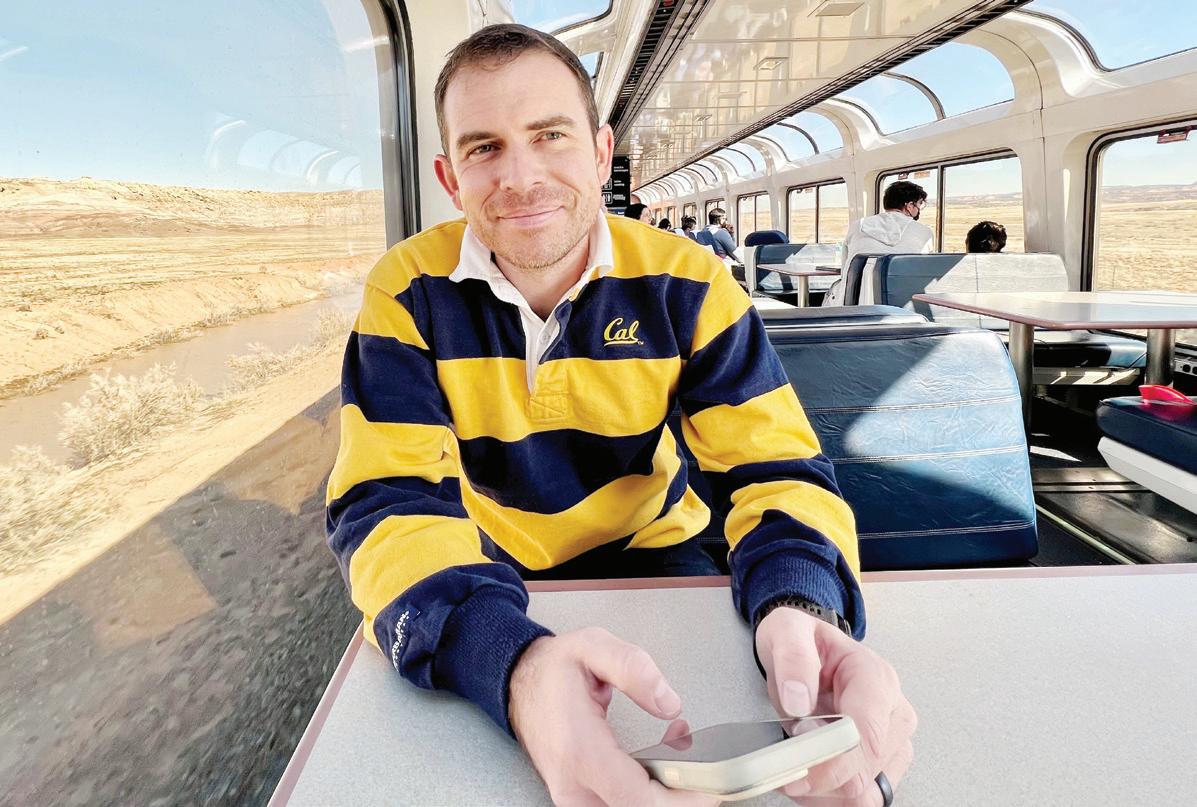
2 minute read
Paging Dr. O
Kip Hanson Contributing Editor
LeBrun explained that, despite its relative maturity and increased popularity for end-use, small-volume part production, AM remains out of reach for many smaller U.S. manufacturers. He noted that developing a competent AM offering is both nontrivial and burdensome for the country’s “Mom and Pop” shops, and even many larger companies. Unfortunately, these are often the businesses that have traditionally supplied parts to original equipment manufacturers (OEM) and their prime suppliers, a situation that—unless remedied—will hamper broader AM adoption.
lga Ivanova has 3D-printed plenty of interesting parts during her time in manufacturing. Rocket nozzles. Turbine blades and impellers. Neonatal tracheostomy tubes. There are more, which we’ll get to in a moment, but to Star Wars fans, it’s the Static Dissipative Yoda that’s most intriguing.
OComplicating matters is a trend toward increased specialization of AM equipment. Unlike a CNC lathe or laser cutter that can machine anything that fits within its axis travels and power constraints, 3D printer manufacturers are making tools that address particular customer needs. Those efforts require them to make specific design choices that determine how their systems operate and therefore limit the number of applications and materials their owners can adopt. This trend is distinctly different than the traditional jack-of-all-
“We printed a bunch of Yoda and Groot (Guardians of the Galaxy) figurines for high school students who visited our facility recently,” said Ivanova, director of technology at Mechnano, an additive manufacturing materials
“I’m glad to see support from the federal government, at least from a leadership perspective, but significant investment will also be necessary,” said LeBrun. “As we’ve seen, though, that’s something easy to ask for but difficult to receive.”
Olga Ivanova Master networker RAPID + TCT Director of Technology Mechnano
developer near Phoenix. “It’s our way of getting young people interested in additive manufacturing.”
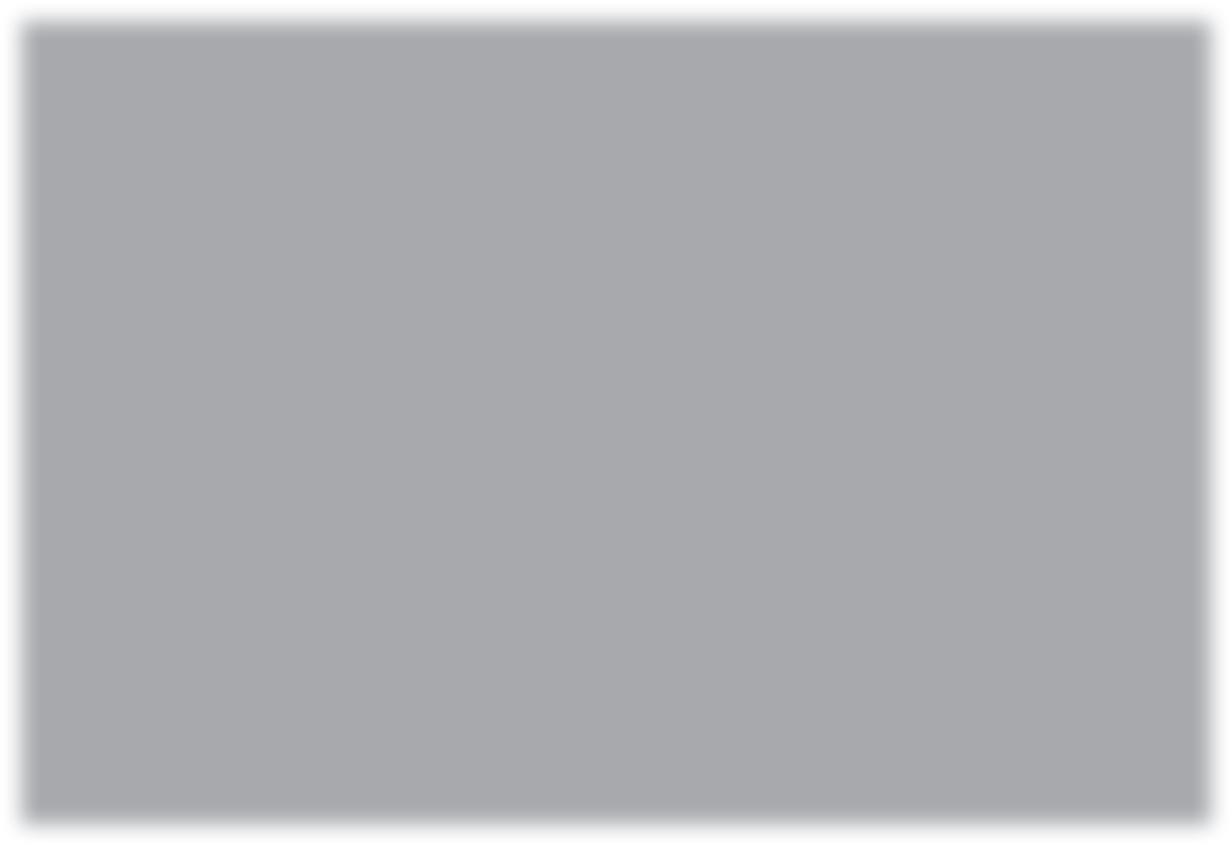
Padawan Learning
Difficulty aside, let’s hope this level of government and industry support continues—according to LeBrun, our country’s current AM leadership position depends on it. “As has been the case with many of the high-tech tools in use today, people will find ways to make those tools cheaper but just as effective, undercutting the existing OEMs to the point where they can no longer compete. That will create a race to the bottom, which won’t be good for anyone. We as a nation must find a way to avoid that, because it’s not something you can wrap a tariff or export control around. The only way to stay ahead of an offshoring wave is through broader domestic adoption, and that requires a certain level of championing beyond what we’re currently seeing.”
She’s quick to point out that those educational giveaways were made of a gray-colored base resin, not the more expensive static dissipative material (which is black) that she spends much of each day working with—and yes, which she occasionally uses to print Yodas that are just as resistant to electrical charge as they are to the Dark Side of the Force.
Walk into the 3DI Lab at Rady Children’s hospital and you’ll find this display case filled with 3D-printed models, a testament to the team’s work.
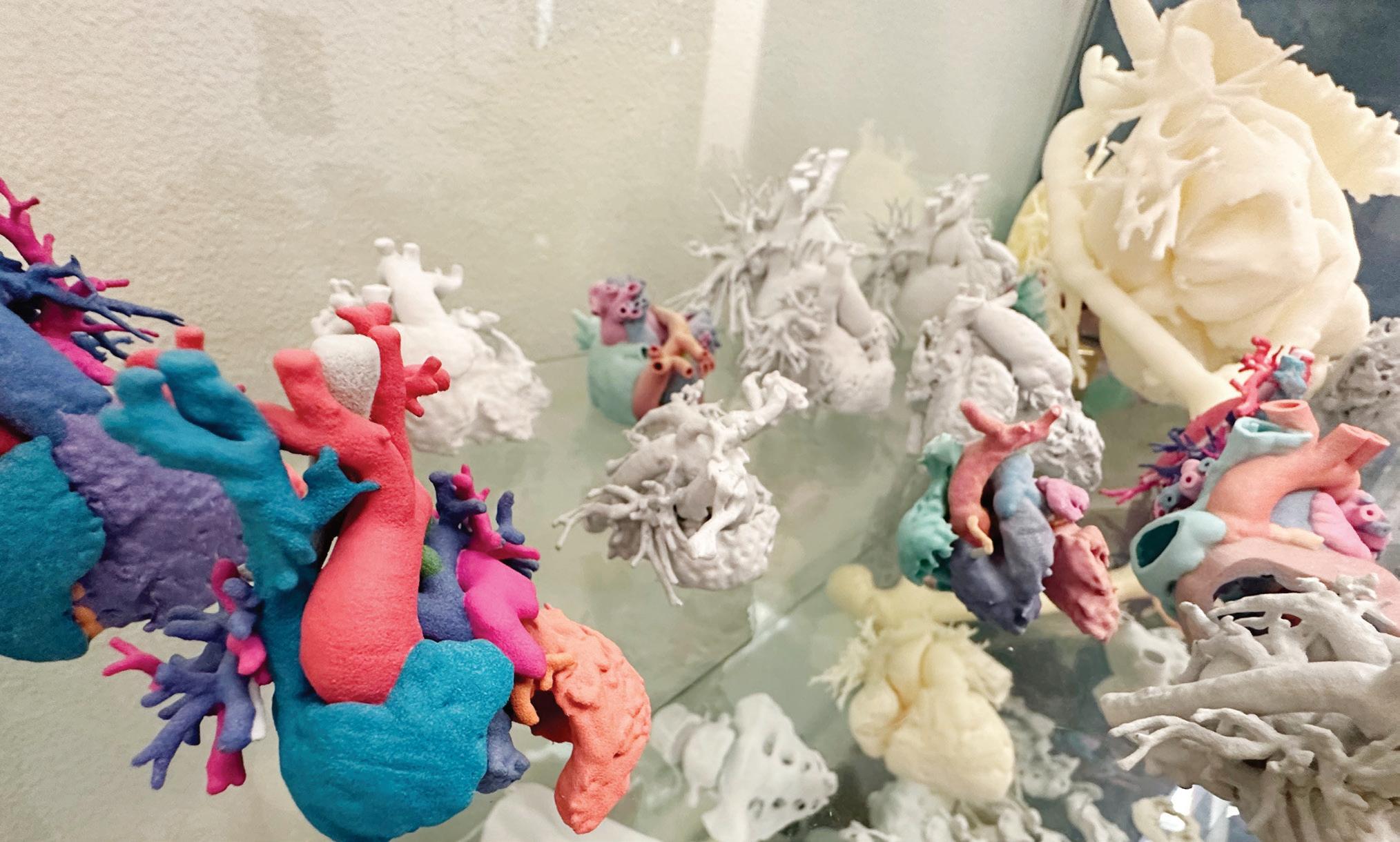