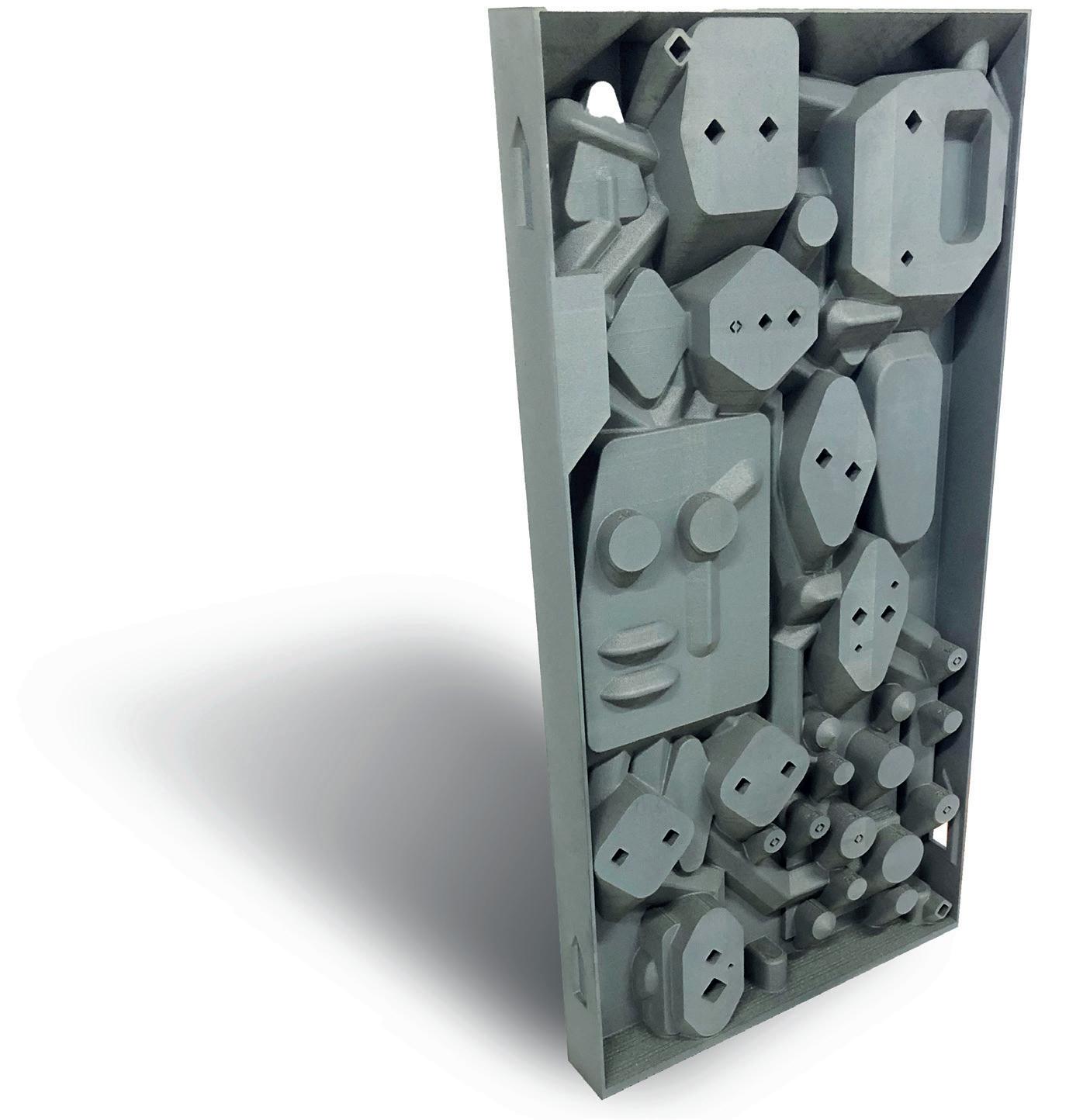
3 minute read
BIG BRAKE
from TCT Europe 29.5
by TCT Magazine
Head of Content Laura Griffiths finds out how Wabtec reimagined a large locomotive component with AM.
On the cover of this magazine, we’ve featured a titanium brake caliper from Bugatti, landing gear for a private Bizjet plane, a Czinger supercar loaded with weight-saving 3D printed parts, all manufactured using SLM Solutions’ selective laser melting technology. You might be thinking, ‘That’s great, but it’s not everyday life.’ Well, if the work the German metal AM leader is carrying out with Wabtec is anything to go by, that may not be the case for very long.
Wabtec, a supplier of equipment and services to the global rail industry, recently set itself the task of redesigning a traditionally manufactured locomotive brake panel. The metal panel is a critical component made up of four different parts and a heavy one at 52 lbs. Manufactured in France with a lengthy lead time of 3-6 months for a customer in the U.S., Wabtec looked to AM to develop a more efficient alternative.
“The challenge we had was to deliver some parts, very few parts, to one of our customers in North America,” Henri de Chassey, Additive Manufacturing leader for Wabtec Transit, told TCT. “The problem we have is that the normal lot to produce this kind of part is very high. We're speaking about 20 or 30 parts, and the quantity here was only three to four pieces. So it was very difficult for us to find a supplier. That's why we considered, very quickly, [an] additive manufacturing solution.”
With a full team devoted to AM, and a newly opened 11,000 square-foot facility at Pittsburgh’s Neighborhood 91 AM production campus, Wabtec currently has a number of metal machines inhouse covering both SLM and binder jet technologies, including an SLM 280 geared to Inconel and SLM 800 dedicated to aluminium. It was the scale and speed of the latter that enabled the company to redesign the brake panel as a single component.
After what Henri describes as a “complete rework of the plate”, the panel’s weight was halved, and lead times reduced by 70%. The part was put through rigorous testing and certification processes to ensure both its safety and so that the full lifecycle of the panel, which could be at least ten years when installed on a train, would be equal, or even superior to the original part.
The brake panel is just one part Wabtec has been exploring with AM. The company has also been testing out other critical components such as heat exchangers and brake calipers as it looks to develop pilot projects with its customers to demonstrate where the technology makes sense. Right now, the biggest opportunity is in part obsolescence where Henri says around 66% of printed parts could be produced for such use cases. Wabtec recently shared that it plans to use additive technologies to produce over 25,000 parts by 2025 in support of its internal supply chain.
“When we speak about obsolescence, for example, it's really important that our customer [is] able to have the part as soon as possible,” Henri said. “We speak about 10 kilo to 15 kilo a day for our customer when the train is stopped at the depot so you can imagine the pressure they have. If you're able to come and say, ‘look guys, I have a solution that can provide you the missing parts to put [the train] back in service’, of course, it will be very well appreciated.”
This new method of manufacture has also brought sustainable advantages due to reduced material and transportation emissions, bolstering Wabtec’s mission, first set out in 2017, to create greener and more future ready products. According to SLM Solutions, the ability to sync print parameters to any SLM 800 machine around the world also makes it much easier to manufacture locally.
“[This machine] is opening a new world for us because we can now bring to market very big parts,” Henri concluded. “We have many other ideas and I'm quite sure it's also changing the way to think on the original equipment side because people on our R&D are now also starting to think directly to additive manufacturing. This is really interesting because we are thinking about solving issues with obsolescence for our after-market customers […] and thankfully with this machine we’ve [succeeded with] some very incredible parts.”
SHOWN:
WABTEC BRAKE PANEL 3D PRINTED ON AN SLM 800 (SOURCE: WABTEC)