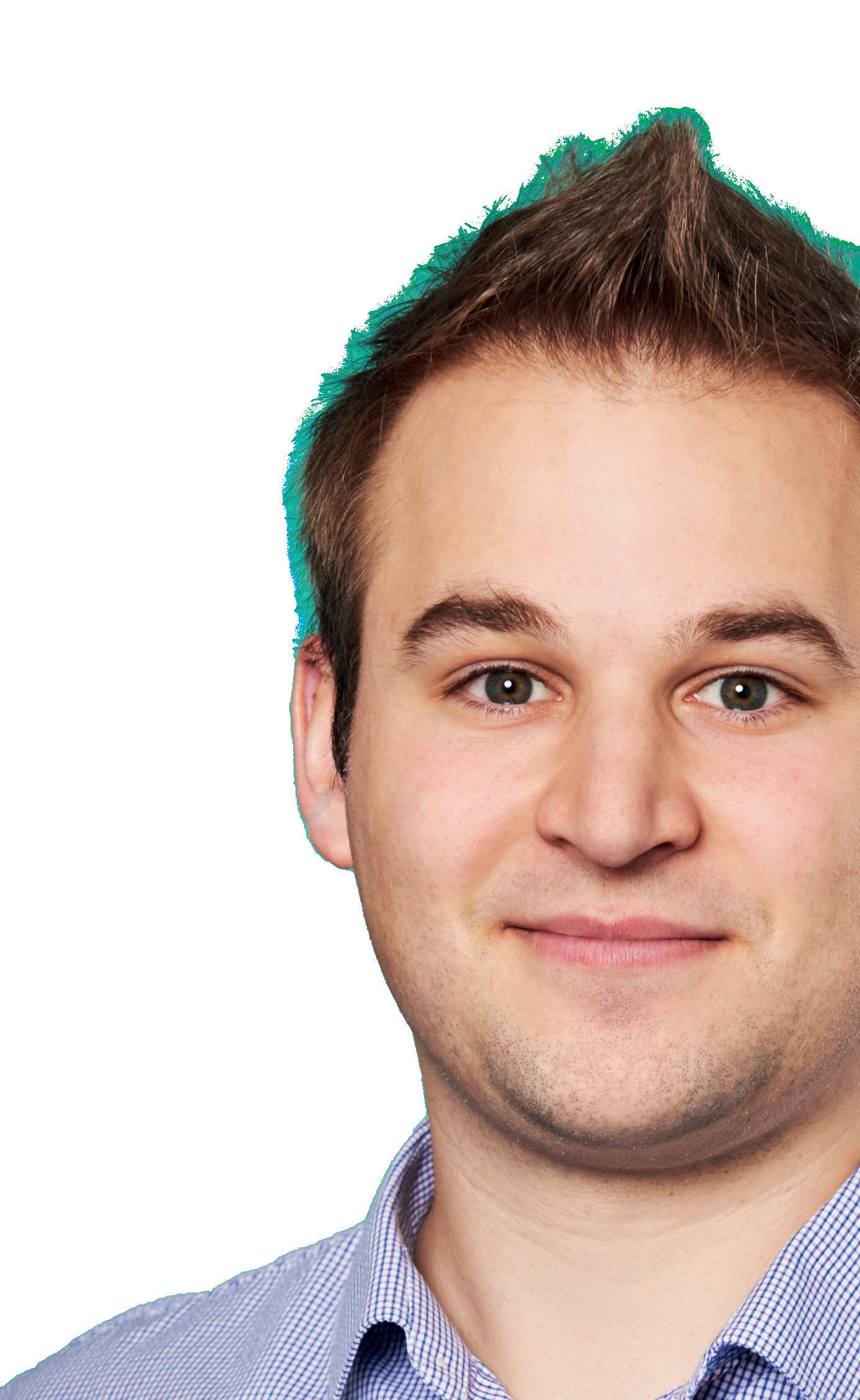
8 minute read
AUTOMATION AND ERROR DETECTION IN AM
from TCT Europe 29.6
by TCT Magazine
WORDS: Pascal Becker, Research Scientist, FZI Research Center for Information Technology
Additive manufacturing (AM) is playing an increasingly important role in today's production. This is not only due to the fact that complex geometries can be produced with AM, but also because this type of production is economical, especially for small quantities and individualised products.
However, the work has so far been bound up with many manual steps. To begin with, the CAD data must be sliced for printing. The more experience and knowledge the employee has about the printing process, the more likely a successful print result is. The number of possible error cases varies depending on the type of process, and the possibility of observing the printing process in-situ also varies depending on the process type.
After preparation of the print data and the printer hardware, the process can be started. The print itself typically takes several hours, if not days. In that time, various errors can occur such as warping. Sometimes the errors are so serious that the print job can be aborted immediately, since the final part deviates greatly from the desired geometry and cannot be used. There are currently only a few options for automated error checking here. Various research institutes are therefore trying to implement this in-situ error detection using the current technologies. Not only does the choice of software approach (artificial intelligence, classical sensor data processing) play a role, but the choice of sensor technology is also very specific to the printing process. In addition to imaging methods such as 2D, 3D or thermal imaging cameras, acoustic and optical microphones, as well as vibration sensors are also being investigated. These sensors must be integrated into the hardware and the process, and the sensor data must be processed and evaluated in order to obtain added value.
Continuous monitoring of the current printing situation is important in many ways. Thus, the print can be monitored automatically and the recorded data can be used for quality assurance, as well as for predictive maintanence for the machine. Reliable error detection enables the print job to be aborted at an early stage, thus saving valuable time and material. As a result, the corrected print job can be started earlier and losses are reduced.
Once the print job is finished, the objects are manually unloaded, cleaned and post-processed. Depending on the object geometry and printing process, this can involve a lot of manual work. This is where the two modern technologies of AM and robotics need to be combined. According to some scientific publications, unloading the component with the help of a robot is very flexible and economically feasible. In the field of post-processing, there are both the first startups and already scientific results that have studied and partially solved the problem.
Here, it is important to consider the overall system. Depending on the unloading strategy, something must already be adjusted in the slicing process so that the removal can take place without damage. At the same time, the system should be designed in such a way that few additional components as possible are required and at the same time, almost all possible parts can be handled. For example, it makes sense to have several printers maintained by one robot on a mobile platform so that the robotic system is profitable for a huge workload.
One of the advantages of AM is also one of the biggest challenge for robotics - due to the fact that virtually any possible geometry can be printed, the requirements for grasp points, gripper jaw design, required opening widths of the gripper or the post-processing strategy, are complex and diverse. These must be taken into account and integrated into a coherent overall concept.
Overall, further automation of additive manufacturing is inevitable. The more objects that are mass-produced using AM, the more important it becomes to continuously monitor and detect errors during the printing process and at the same time, reduce the number of manual steps after printing. Appropriate approaches need to be developed and implemented for these two topics so that AM can better exploit its potential.
Hear more from Pascal at the TCT Conference @ Formnext on 17th November at 14:30-15:00.
GET TICKETS:
tctconferenceformnext.com

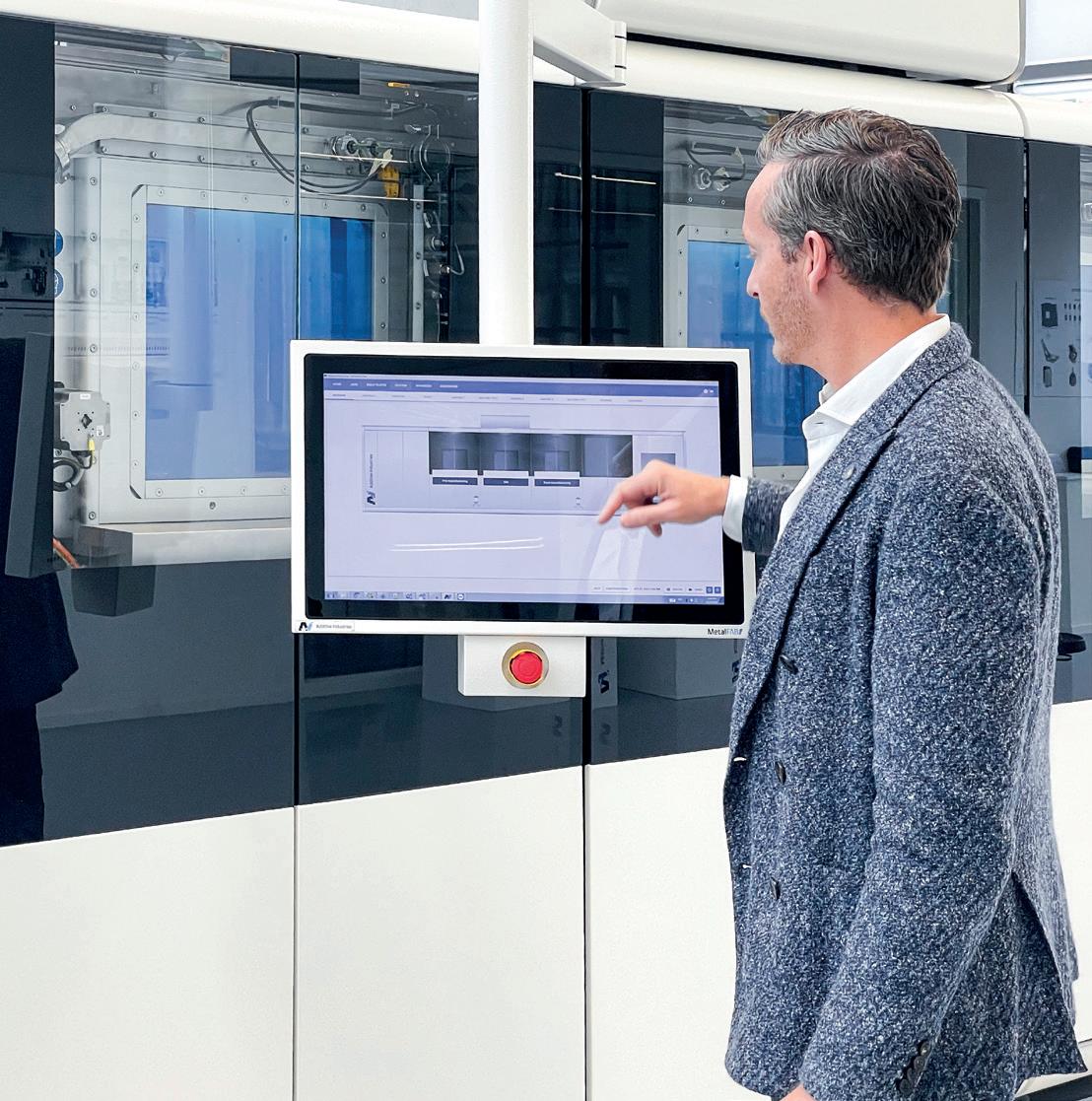
Q&A with Additive Industries CEO
Additive Industries CEO Ian C. Howe on the future of additive manufacturing.
Q: You took over as Additive Industries’ CEO back in April. What have you been focusing on since coming on board? A: The focus is on preparing the company for the next stage in its development. Since its foundation in 2012 the focus was heavily on developing the technology and the MetalFAB1 with specifically chosen key customers. The next phase will focus on profitable growth driven by five strategic pillars: • Technology Leadership in industrial large frame metal
AM (continuing to drive productivity leadership for large frame systems) • Commercial Excellence (investing in commercial team to bring our solutions to targeted customers where we clearly add value to their business and strategy, and to deliver best in class customer service) • Service Offering (creating customer engagement and service to ensure delivery of best OE Availability,
Utilization, Reduced Scrap) • Exploring adjacent markets / technology areas
Q: You’ve previously worked in the aerospace, energy, and automotive sectors. From your experience, where do you see the biggest opportunities for AM right now? A: Currently in terms of spend, growth and technocommercial fit for Large Frame Industrial metal AM solutions, the largest opportunities lie within the following market verticals: • Medical (€1.1b in 2021, growing CAGR 27%, to €3.7b in 2026) • Space (€800m in 2021, growing CAGR 24%, to €2.5b in 2026) • Automotive (€600m in 2021, growing CAGR 28%, to €2.1b in 2026) • Industrial (€500m in 2021, growing CAGR 22%, to €1.5b in 2026) • Aviation (€200m, growing
CAGR 26%, to €700m in 2026) • High Tech (€300m, growing CAGR 30%, to €500m in 2026)
Q: We’ve seen more emphasis put on the opportunities for AM in Spare Parts/Legacy Program management over the last years. What are your thoughts on the role AM can play? A: AM as a technology is already fulfilling customer needs here as the digital nature of AM perfectly manages the complexity of such problems. Imagine high value capital goods that have useful life cycles of decades. How can one manage all those spare part inventories, specifications and drawings, not to mention production toolings etc over many decades. AM provides the ideal digital solution to manage the complexity in a
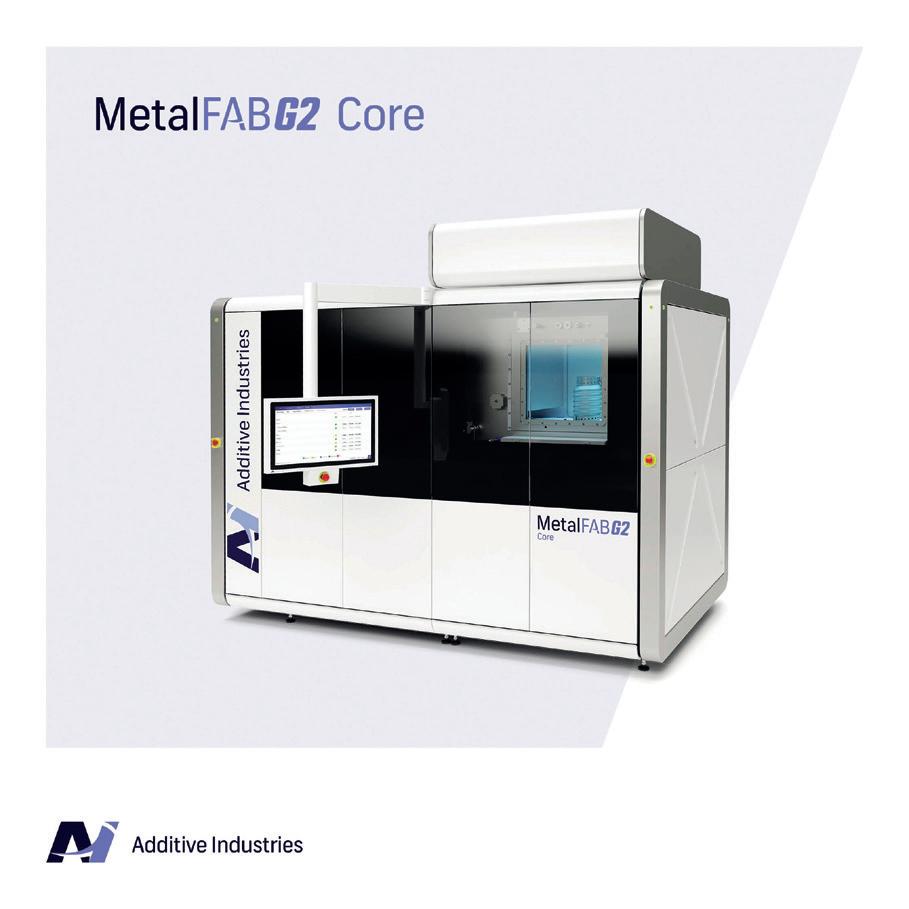
cost efficient manner. This awareness is spreading and OEMs are deploying such cases to drive their strategies.
Q: At last year’s Formnext, Additive Industries debuted the MetalFAB-600. Can you give us an update on the progress being made there? A: The company took a strategic decision to keep its innovation focus on productivity leadership and driving down cost / kg of AM produced metal components on the MetalFAB1. This was a conscious decision based on customer demand / needs and has led to the launch of the MetalFAB G2, the next generation system in productivity leadership, at Formnext 2021 amongst other improvements. We still have large demand for solutions that can only be realized with faster and more cost-efficient solutions, hence this focus area/ opportunity remains in focus. However, we have indeed still progressed innovation of some of the critical systems such as the Optics development.
Q: What are the benefits of more laser power? A: More laser power indeed provides direct possibility to increase productivity / build rates. However, it needs also to be balanced with ensuring the quality of materials properties and component integrity
Q: What challenges do you think AM still faces in establishing itself as a mainstream production technology? A: There are a number of challenges: • Cost effectiveness versus traditional manufacturing solutions, including end to end processing.
Currently the technology is addressing the very high value components segment. • Standardization of processes, applications and materials enabling design engineers to choose AM as a robust and reliable process alternative • Scarcity of competent professionals and scientists/engineers in a fast-growing industry
Q: Where is Additive Industries’ technology making the biggest impact today? A: Currently we have deployed our technology into customers within the Space, Aviation Turbine, Automotive, Industrial and High-Tech market verticals.
Q: Can you share any launch plans for Formnext 2021? A: We are excited to announce several new developments for our (prospective) customers during Formnext 2021: • MetalFAB G2 – Launch of next level productivity leadership: The MetalFAB
G2 is offered in three key configurations, depending on customer needs; • MetalFAB G2 CORE • MetalFAB G2
AUTOMATION • MetalFAB G2
CONTINUOUS
PRODUCTION

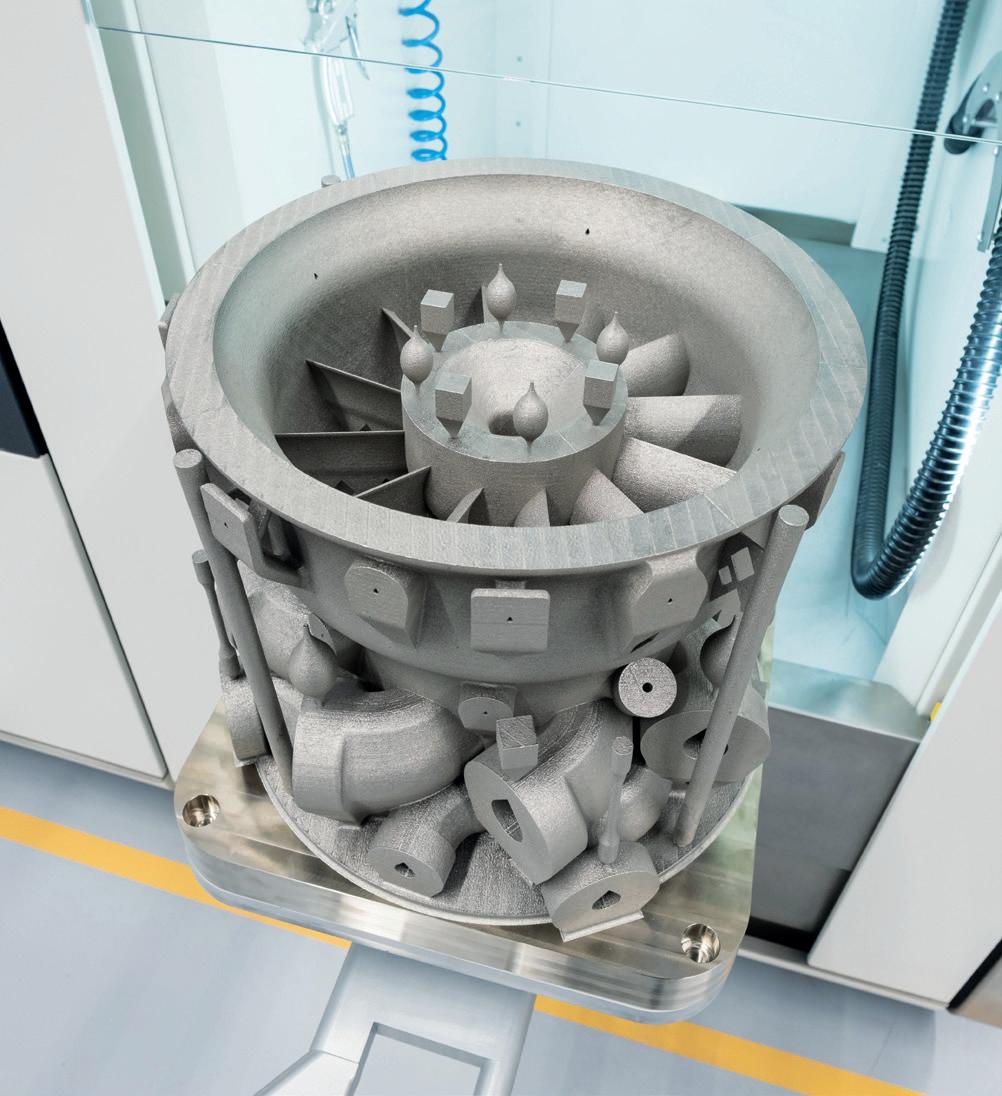
Alongside our new system, the next generation MetalFAB, we are going to announce innovations that improve both the accessibility of its machines and users’ quality assurance capabilities during operation. We are presenting a multibeam qualification tool, which is a big step forward in multi-laser system quality assurance.
Additionally, we are revealing the integration of a beta version of Sigma Labs’ PrintRite3D offering into the MetalFAB, the launch of the latest build processor it has developed in partnership with Materialise, the launch of our Additive Studios, a new additive manufacturing consultancy services and training program, and a strategic collaboration with a machining company Makino, resulting into an end-to-end process chain for scaling metal 3D printing
Q: Can you talk about your overall vision for the future of the company? A: Additive Industries is the driving force for large frame metal additive manufacturing. Our vision is to transform the metal components industry with the largest, fastest, highest quality metal AM technologies, to enable our partners to realize sustainable and profitable growth.
The next phase is about executing the strategy for profitable growth driven by technology leadership in industrial large frame metal AM, commercial excellence: bringing our solutions to customers, offering world class, and exploring adjacent markets/technology areas.
Visit Additive Industries at Formnext (Hall 12.0, booth D119).
For more information contact: sales@ additiveindustries.com


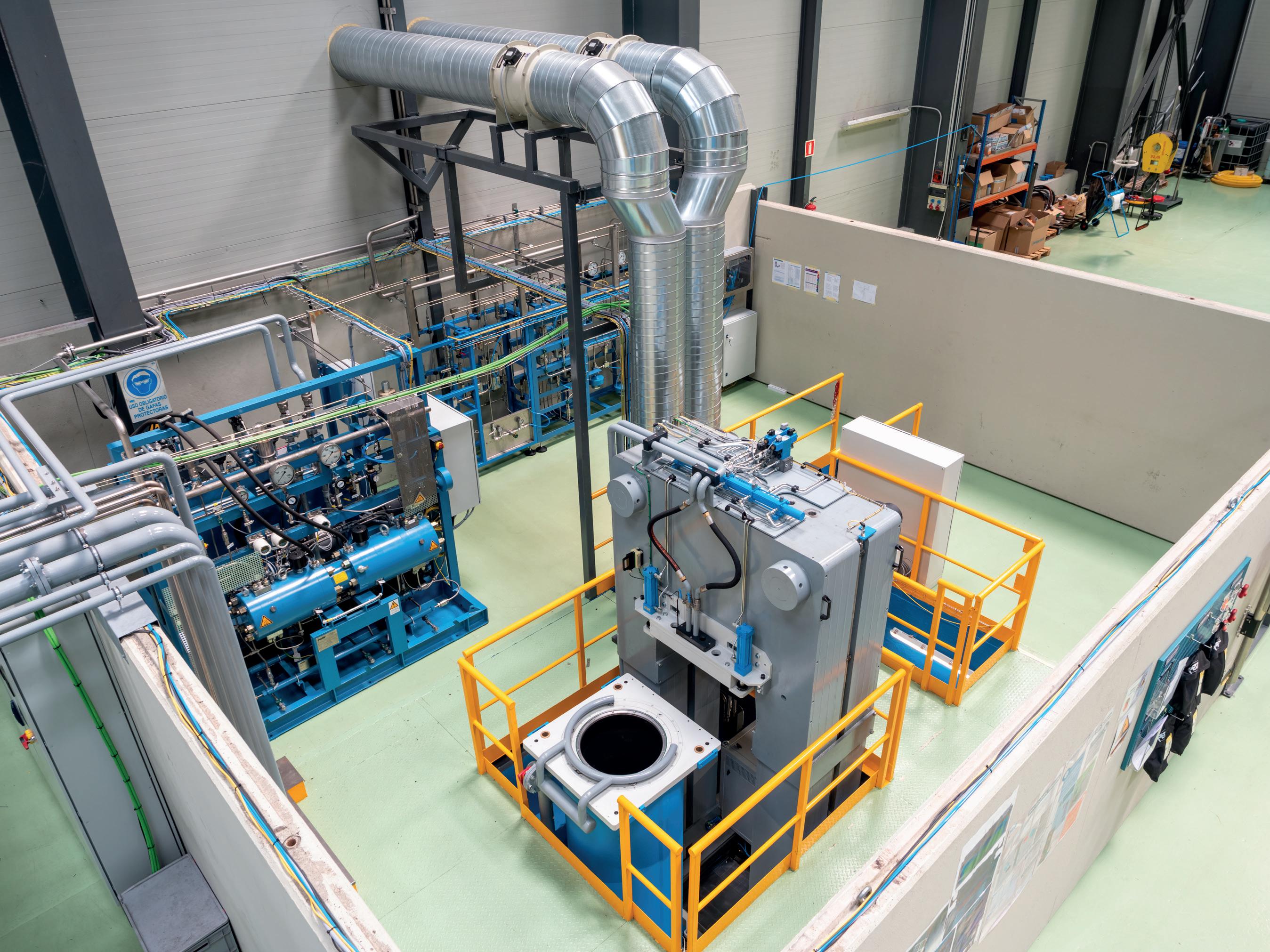
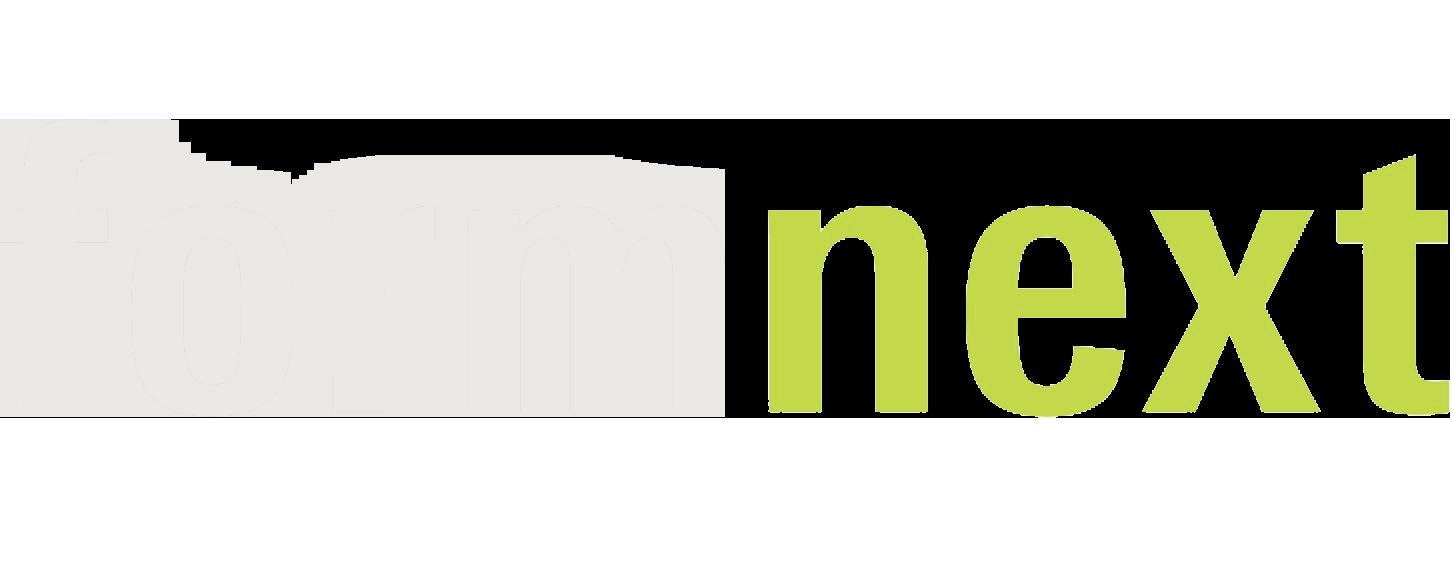