
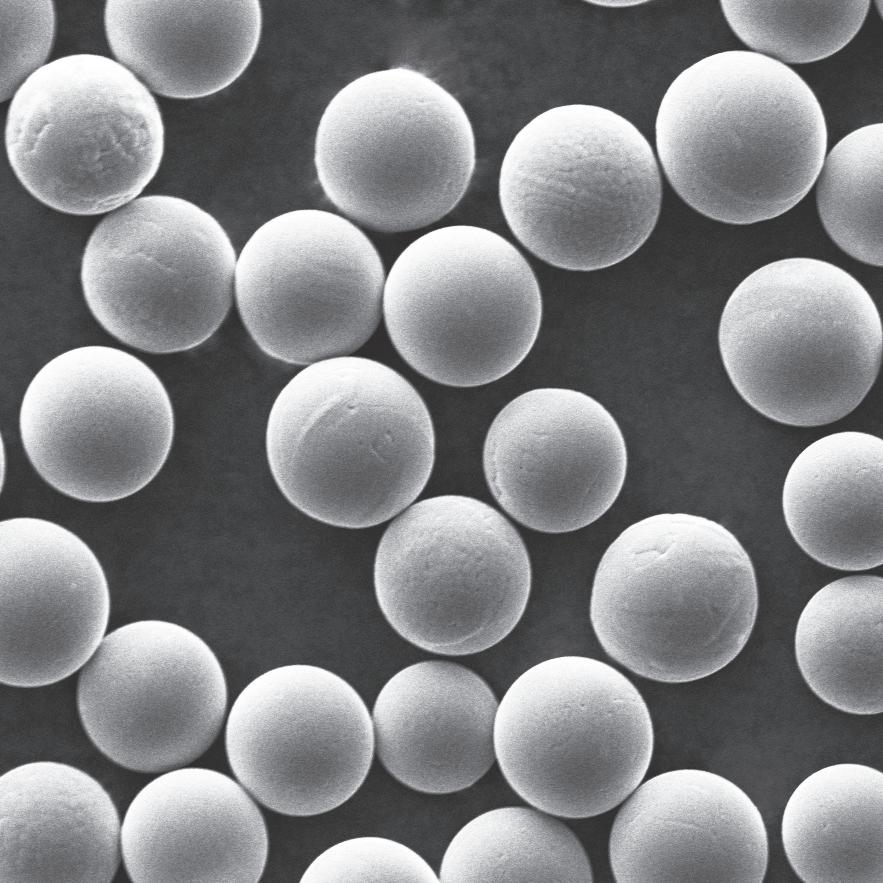

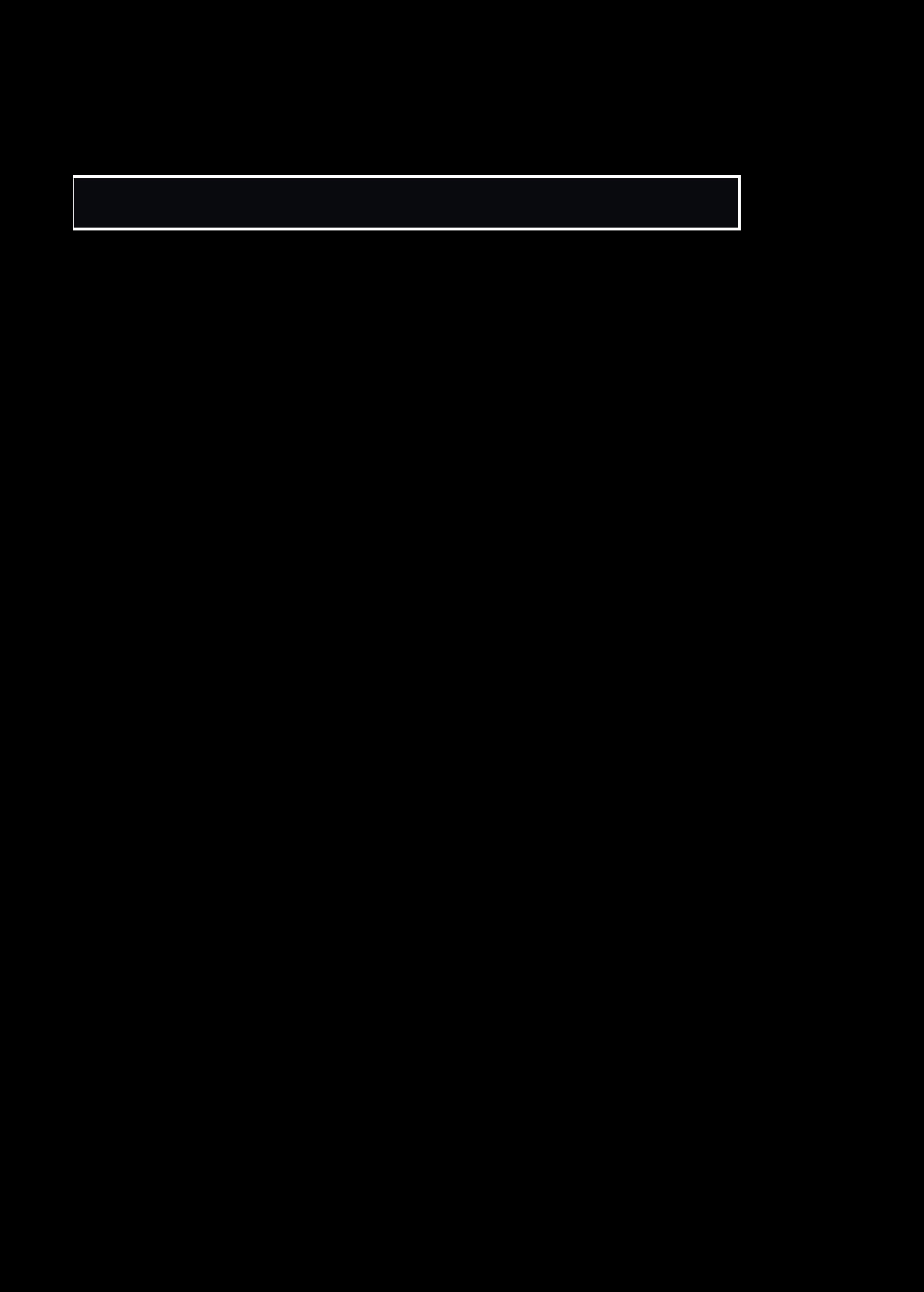
EDITORIAL
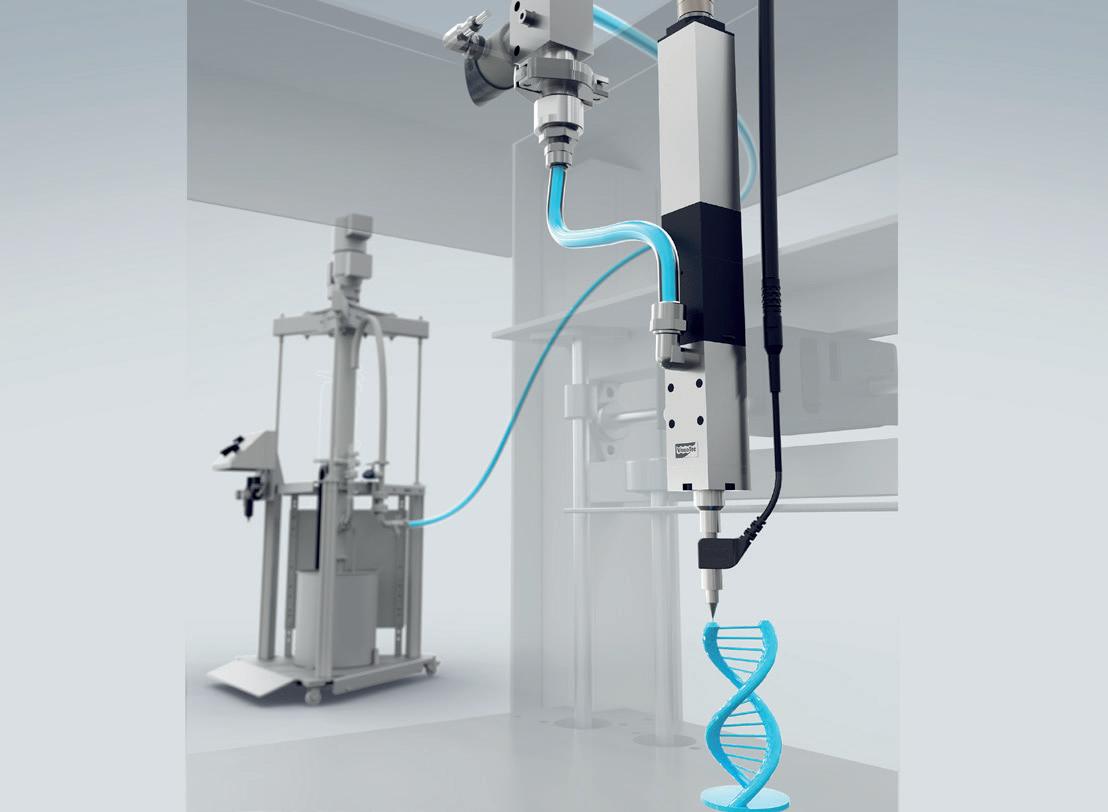
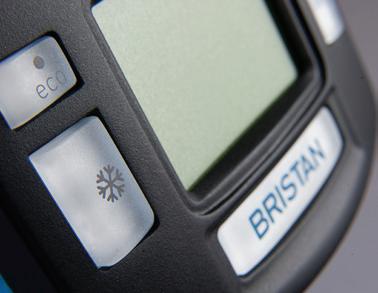
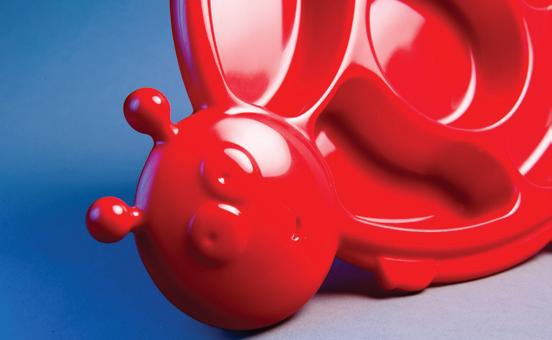

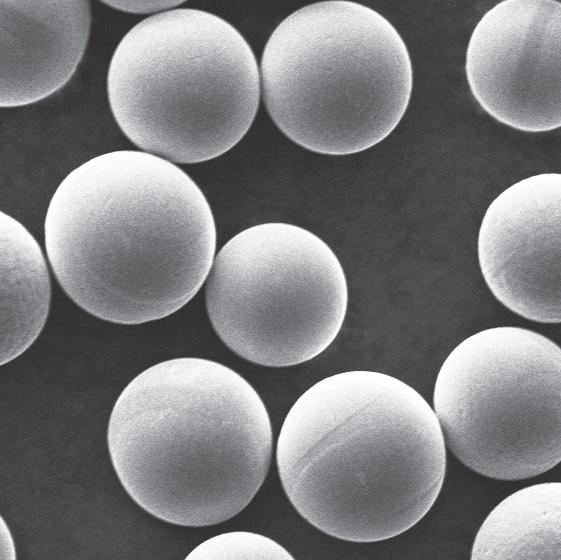
HEAD
HEAD
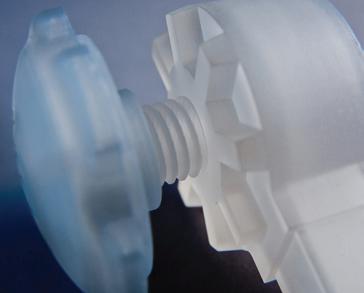
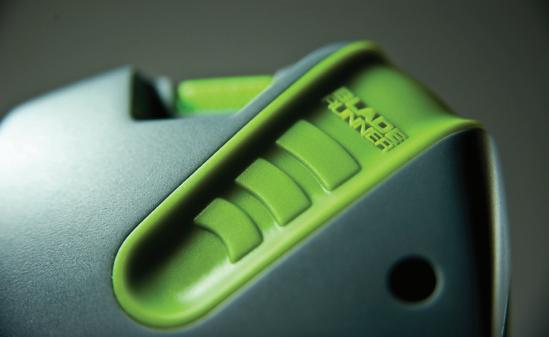
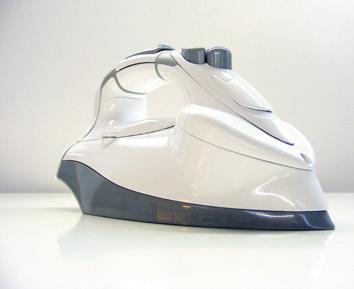
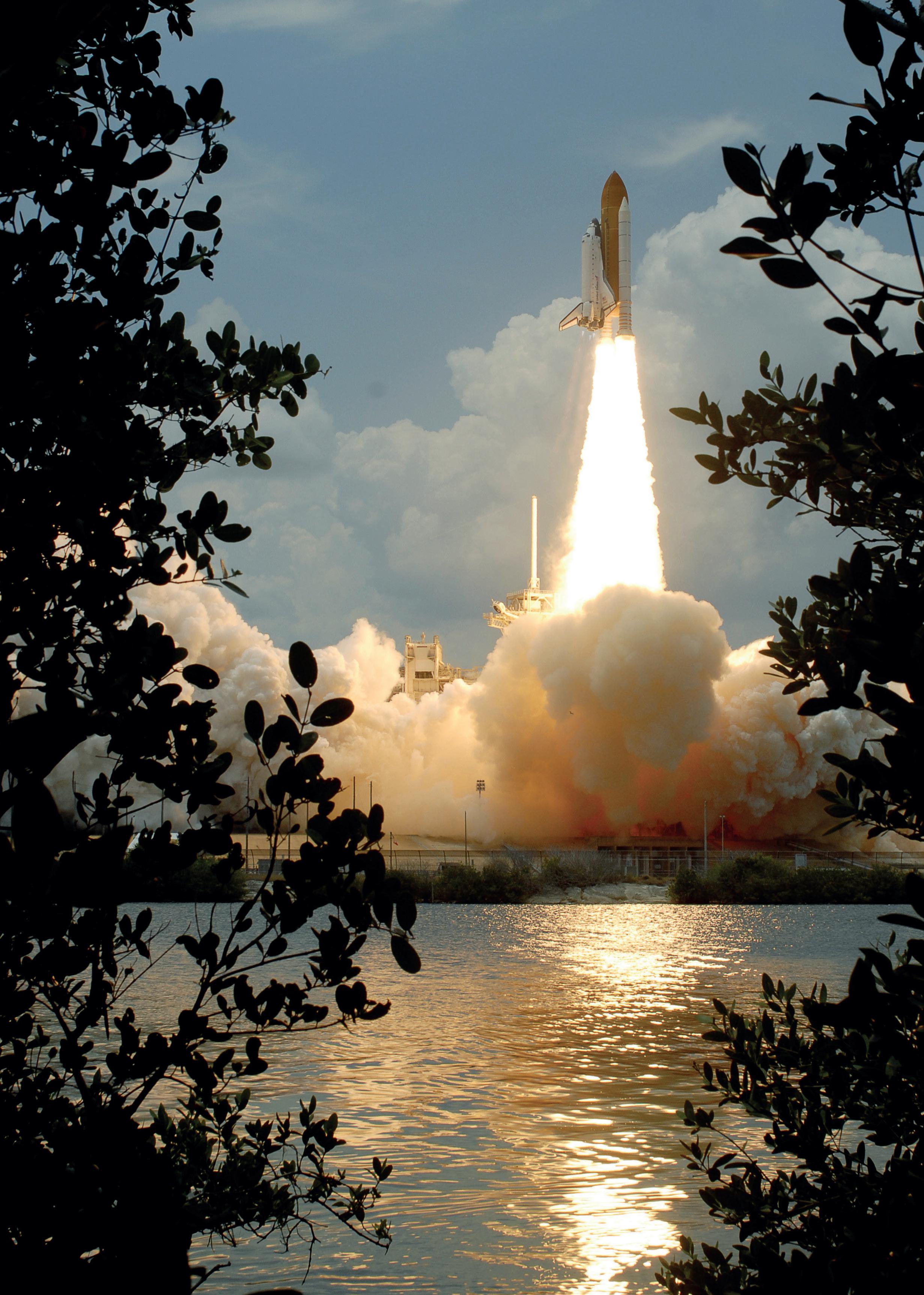
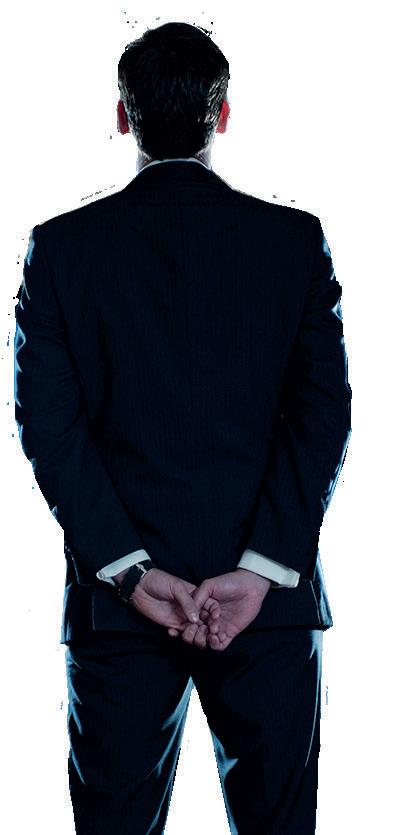
HEAD
HEAD
The month of May is always a significant one for the additive manufacturing (AM) sector owing to the annual RAPID + TCT event. But this year, it was doubly so as weeks earlier President Biden launched an initiative designed to support the take-up of AM at small and medium businesses (SMB).
AM Forward will see manufacturing leaders like GE Aviation, Honeywell and Lockheed commit to purchasing 3D printed parts from smaller US-based suppliers, while also training workers and engaging in AM standards development.
In response, Fortify CEO Josh Martin described AM Forward as a ‘great signal’, noting how the local use of AM during the COVID-19 pandemic helped ease supply chain issues, while Xerox's Tali Rosman told TCT it was now a matter of national security that AM adoption is supported.
The notion that AM is a matter of national security may seem dramatic, but when you consider, for example, the prospect of the military not having an efficient procurement process for missioncritical spare parts or the economic impact of supply chains in other essential industries breaking down, it makes sense. Countries can’t run without manufactured parts and products, and as the pandemic showed, they can’t always rely on supply from elsewhere either.
Of course, AM isn’t the answer to every manufacturing problem – in fact, it’s not for most – but when it does make sense, it’s known to add value, reduce lead times, cut costs, and as was exhibited during the pandemic, provide solutions at the point of need.
It didn’t go unnoticed in the US, though it must be said that AM Forward, at this stage, is only a plan. But it is significant in both its timing and structure. After the supply chain issues brought on by COVID-19 (and the Suez Canal blockage, and the Russian war in Ukraine), AM Forward is part of a strategy to encourage the reshoring of manufacturing by incentivising the adoption of 3D printing and building out AM supply chains from smaller suppliers up to blue chip brands.
Others should follow suit.
In the UK, for example, AM strategies have been drafted with little to no take-up. There have been isolated government investments in companies like Wayland Additive and WAAM, and the creation of catapult centres like the MTC and AMRC, but a broader structure to move the technology forward is lacking. That a nation with such AM legacy isn’t deploying such a strategy has led to much frustration – not least when the 2017 Industrial Strategy to ‘build a Britain fit for the future’ made only one mention of AM across 255 pages.
Across the pond, the Biden Administration seems to have recognised the value AM can bring in a prospective era of reshoring. What’s more, they’ve put a plan in place that has the buy-in of manufacturers big and small. Similar initiatives in other countries would be welcome. Without them, those nations risk being left behind.
As JEOL USA President Robert Pohorenic told TCT, manufacturing is going in this direction with or without government support, but it’ll go a lot quicker with it.
Sam Davies speaks to John Crane about how its UK-site is pushing the envelope in AM production.
Anna D’Alessio shares how Ivaldi is helping customers in heavy industry to digitise their inventories for on-demand manufacturing.
ABOVE:
IMPELLER
Sustainability across the value chain is a trend that is getting increasing coverage internally and externally and is becoming a key part of decisionmaking for companies that are looking to lower their carbon footprint. Additive manufacturing (AM) has typically been recognised as a much more sustainable way to manufacture in comparison to conventional manufacturing but this does not take into consideration how the metal AM powders are manufactured.
6K Additive has changed not only how metal AM materials are produced but has completely changed the sustainability game for AM powders, helping organisations achieve their goals in a very tangible way.
6K Additive has a storied 25-year history of recycling and upcycling metals such as titanium, where they are made into an additive compact for the aluminium melt industry. Chances are if you drive a Ford F150 your truck bed contains 6K Additive products or if you have had an MRI, your scan was enabled by metal components utilising 6K Additive products. The company has taken its expertise and extensive knowledge in milling technology and process and combined it with the UniMelt spheroidisation technology to develop the most sustainable manufacturing technology for AM powders. As a result, 6K Additive can produce premium AM powders including nickel 718 and 625, titanium 64 grade 5 and 23, copper 18450 and GRCop, stainless steel 316 and 17-4, and refractories like tungsten and tantalum, all made from sustainable sources.
With its proprietary UniMelt technology, the world's only microwave productionscale plasma system, 6K Additive specialises in the sustainable production of metal powders for additive manufacturing. This fast and environmentally friendly process uses virgin, scrap and used powder as feedstock to make high-quality and infinitely flexible metal additive manufacturing alloys. 6K Additive uses a proprietary milling and cleaning process that ensures contamination-free, highquality powders in under two seconds. UniMelt provides 99% efficiency (microwave to plasma) and is 99.999% contamination-free.
Using feedstock from the manufacturing process, including used AM powders, support structures, failed prints, and certified chemistry scrap, 6K Additive is able to source materials economically and without reliance on overseas sources. UniMelt then achieves nearly 100% yield within the targeted particle size distribution (PSD) producing zero waste.
Customers can also benefit by selling their scrap material to 6K Additive for credit towards their next metal AM powder purchase, creating a circular economy that is valuable and sustainable for the future of AM. With this realisation, organisations now recognise that there is more value in their scrap material both in terms of sustainability and ensuring certified chemistry as the feedstock for the powder-making process. Additionally, having the ability to control supply chain
not only for companies but equally important for the Department of Defense and other government agencies, has become vital. Lastly, the availability of new materials that are simply not available for additive in any scalable way, is now being demanded by aerospace and medical companies whose applications surpass the capabilities of today’s available AM powders.
6K Additive on changing the sustainability game for AM powders.
While many impact categories were modelled and are included in the full report, the two most relevant categories for reducing the environmental impact were Energy Use and Carbon Emissions. The high-level results are highlighted in the graph ( left ).
It was found that for nickel, 6K’s UniMelt process used 6,265 MJ of energy and produced 301kg CO2-eq for every 100kg delivered to the customer. This represents a 91% energy reduction and 92% carbon emissions reduction from traditional processes in the Cradle-to-End User Scope.
It was found that for titanium, 6K’s UniMelt process used 56,268 MJ of energy and produced 2,748kg CO2-eq for every 100kg delivered to the customer. This is, at minimum, a 74% energy reduction and 78% carbon emission reduction from traditional processes in the Cradle-to-End User Scope.
performance of the UniMelt metal powders surpasses that of other providers’ materials because of the 6000K microwave plasma process that utilises a much lower gas volume during spheroidisation. A uniform plasma beam eliminates gas entrapment within the particles, producing dense powder particles that are highly spherical, without satellites and have no internal porosity, resulting in smooth flowability and higher tap density than traditional methods.
The shape, flow, density, and porosity of UniMelt powders are such an improvement that any AM operator will immediately see the difference. Gas atomised powders, for example, include many elongated particles that are under-finished. With UniMelt, the targeted PSD, consistent spheroidicity, and surface smoothness improves flowability, feeding of powder into the 3D printer, and helps with the density of the powder in the build chamber, thereby improving part quality and printer productivity.
6K Additive customers have seen an overall improvement in printed part specifications including improved part density when using 6K Additive’s powders. The added benefit of an environmentally friendly process and domestic supply chain adds to the overall benefit of looking at 6K Additive for your powder needs.
“6K
SUSTAINABLE POWDER THAT SURPASSES INDUSTRY STANDARDS
additive opens up a whole new raft of opportunities for how we can approach these types of problems,” Johnston noted.
In bringing AM into the Berkshire facility, John Crane had to contend with the apprehension that comes with enacting change. This internal hesitancy has been overcome with an education and risk management process, with John Crane first deploying the technology on tooling, jigs and fixture applications – parts in which the company has complete control over the design, implementation and monitoring – before stepping things up.
As a 100+-year-old company with more than 5,000 employees, John Crane operates 200 global facilities. But there is one unlike any other.
While there are multiple facilities running 3D printing technology within the company’s footprint, its site in Berkshire is the one that is pushing the envelope in terms of additive production. At least that was the case towards the end of 2021 – John Crane’s utilisation of the technology continues to gather pace.
A manufacturer of mechanical seals, power transmission couplings, filtration systems and more, John Crane was increasingly hearing demands from customers that lend themselves well to additive manufacturing technology, encouraging the company to purchase a Stratasys Fortus 450mc.
“A lot of our RFQs are coming through with increasingly shorter, tighter demands around lead time,” Liam Johnston, John Crane AM Program Manager, told TCT. “Cost as well is a big area, being able to drive cost not just out of our products but also out of production processes. Being able to consolidate certain processes, consolidate part assemblies, that’s a big demand for us. Another big one that’s become a focus recently is environmental impact and footprint. A lot of
customers are starting to see that, in some cases, they wouldn’t mind paying a little bit more for a product if we can show that it’s having a positive impact on footprint and carbon emissions with production.”
As a company with such legacy in its areas of expertise, it has developed deep manufacturing competency over the last century. It has enabled the firm to become a leader in its field, serving users in oil and gas, power generation, chemical, pharmaceutical, mining, food and beverages, and more. But it has also brought John Crane to a point where, when customers asked for parts that could run without fresh water supply or needed a reduced footprint or required an improved strength to weight ratio, a change in approach was needed.
“I think we’re starting to reach that point where we squeezed as much as we can out of our conventional manufacturing processes and design methodologies, so I think
One of the key points of contention for engineers was placing confidence in a polymer material, for example, when a metal had previously been used. The responsibility of the team leading the AM charge within John Crane was to prove additive manufacturing’s capacity to deliver the performance requirements engineers were used to.
“Naturally, people hear the term polymer material and they think it’s a downgrade [on metal],” Johnston said, “but they don’t understand that with 3D printing, you can design with the function of the purpose in mind, so you can reinforce the part, you can design with lattice structures, use different geometries, different ways of design that can redefine how you solve a problem. People were naturally apprehensive to some of those changes, some of which were coming from an industry perspective, thinking there might be certain standards that specify it has to be a certain grade of stainless steel or whatever it is.”
“I think we’ve educated the workforce to think much more scientifically in such as this part was made of metal, the part has to have a tensile strength of whatever, polymers, composites can now achieve this,” Matthew Bourner, John Crane Advanced Manufacturing Engineer, added. “I’d say the skill set is often the hardest part. As a business, you can always buy machines, you can buy people if you want to, but if you want to grow the skill set organically, that takes a bit of time. But with engineering, some of
our commercial teams, they [have] come around to the idea of utilising the technology for what it has to offer.”
John Crane thus has an increasing number of success stories. As it progressed from tooling components to end consumer products, the company threw polymer 3D printing at some installation and transportation components for seals – chosen because of their low performance requirements, simple geometry and high level of design variation – of which 6,000 devices were produced annually at around 70% cheaper than their metal counterparts. The parts are now printed on-demand, reducing the need to hold large amounts of inventory on site and indicating the technology’s potential application for spare parts.
“The oil and gas sector, that’s a massive area for them,” Johnston said of spare parts. “Every hour of downtime on your refinery is X many millions of pounds lost, and they’re distributed all over the place in some of the most arid, out of the way areas. So, ensuring that we can get parts to customers quickly, having spare parts on-demand, is something that we think additive will hugely benefit us on.”
To create the infrastructure that will facilitate the distribution of spare parts on-demand from a digital warehouse will take time, but the confidence in AM is now comprehensive. So much so, John Crane has also widened its adoption of the technology to include metal processes.
As it stepped into metal 3D printing, the company targeted its filtration system products. Here, internal flow vortices can reintroduce contaminants that reduce system efficiency, impacting the life of the seal or rotating equipment and costing the end user maintenance and repair expenses. But with AM, John Crane has sought to address those challenges by developing a bespoke flow straightener which is installed in front of the filtration element and removes vortexes from the gas flow.
This flow straightener is an integral part of John Crane’s Indufil FCF Series Seal Gas Filtration System that removes liquid and particle contamination for reliable dry gas seal operation, complies with international pressure vessel and design codes, and is designed in alignment with the API614 and API692 standards. It has been designed with a honeycomb lattice structure to have minimal wall thickness while maintaining part strength, is scalable for different filter sizes and helps to achieve a 50% lower loss of pressure and up to 60% improved flow capacity. Able to be additively manufactured in Inconel 625 and Ti64, John Crane expects to produce hundreds of filter parts per year using AM, and also wants to explore how the straightener’s lattice structure can be adapted to meet the properties of the customer’s gas flow by varying the unit cell size across diameter of the element.
“I asked the engineering team afterwards,” Johnston recalled, “why is that honeycomb lattice
uniform throughout? Your flow is not uniform throughout, so why have you kept a uniform lattice? Why don’t you look at considering the varying unit cell size as we get towards the edge of the flow? That’s surely where you’ll get more disturbance, friction and drag as you get to the edge. Because that was something they couldn’t ever do using conventional manufacturing, they were used to buying the off the shelf standard honeycomb media.”
The learning process continues and John Crane’s appetite for AM technology intensifies. Johnston and Bourner confirmed the company is exploring other 3D printing processes, with wire arc suggested as a technology that could facilitate spare parts and binder jetting touted as one that could enable more applications like the lattice flow straightener in its filtration systems. The technology is changing the way John Crane produces parts, from production line tools through to the systems in its extensive product portfolio. And starting in Berkshire,
the hope is that these gains will gradually be attributed across its global footprint.
“We’ve always had some level of 3D printing across the business, largely for rapid prototypes, jigs and fixtures on the relatively small scale, but the UK was the first site where we pushed production levels,” Johnston finished. “We see that as our primary site where will try new processes, not just specifically for printing but the whole process chain, quality management systems, workflow management systems, the skill and design tools, and then replicate and expand those out to some of our other sites.”
“We've squeezed as much as we can out of conventional manufacturing.”
RAHN AG Zurich, Switzerland
RAHN GmbH Frankfurt am Main, Germany
RAHN USA Corp. Aurora, Illinois, USA
RAHN Trading (Shanghai) Co. Ltd. Shanghai, China
energycuring@rahn-group.com www.rahn-group.com
The UK government has ambitions set on delivering 24 gigawatts of nuclear capacity by 2050 as part of its new energy security strategy. The Nuclear Advanced Manufacturing Research Centre (Nuclear AMRC), with its base in South Yorkshire and specialist manufacturing centres around the UK, is exploring how advanced manufacturing processes may help us to get there. Additive manufacturing (AM) is one such process and Udi Woy [UW], Nuclear AMRC Additive Manufacturing Technology Lead, who is responsible for developing the centre’s strategy for AM and AMfocused projects, recently spoke to TCT about the centre’s work with DED, where AM is uniquely equipped to meet the demands of the nuclear market, and future application opportunities.
TCT: Hi Udi. Tell us about the types of AM technologies you’re working with at the Nuclear AMRC.
UW: Predominantly we use Directed Energy Deposition (DED). PBF (Powder Bed Fusion) is also of significant interest but our emphasis is on DED because of the flexibility and ability to scale. When you're looking at large-scale or ultra large-scale products and parts, one of the main considerations from an R&D perspective is to investigate the scaling factors because it has a significant bearing on the industrial relevance of our outputs. With
AM, you don't have a linear relationship between inputs and outputs. If you're going to make a small part, you concentrate a lot of heat in a small area. But when you're building a much larger part, you're concentrating heat locally but over the scale of the build. If you're using DED, even if you're using powder bed, you're cooling at different rates, you're heating at different rates. That has implications even beyond the localised heat input so if you're looking at your design requirements, you have to scale that appropriately.
One of the things we were quite clear about at the start were bulk additive manufacturing applications. The emphasis on bulk meaning we’re appropriately scaling the research, the requirements, the parameters, we’re appropriately controlling all of the factors that are of interest in industry so when they come to adopt the process and take the parameters, it's immediately relevant to the work that they want to do.
TCT: Can you share any examples of where AM is being used in the sector currently?
UW: The trajectory is similar in some respects to those of other industries where you usually start with prototyping and tooling applications but there are also opportunities to fabricate high entropy materials, which are generally challenging to process but offer the desired combination of characteristics that are required for critical parts and components. We're quite interested in developing qualification procedures around not just the application but also the alloy. For instance, on one of the projects we've
been investigating 316L and we've produced debris filters, which are usually used in fuel assemblies. It's got a network of holes and features that make it challenging to fabricate using traditional approaches without the right sort of tooling, which is expensive to do and so there is interest in using AM to manufacture stuff like that.
On the other end, we are looking at obsolescence issues and legacy parts. For legacy parts, it's a bit more challenging because it's already been in service so you want to preserve the properties and the performance, you're essentially restoring it or maintaining it to continue being used in service. It's not like starting on a blank canvas where if you make any errors, you can maybe scale it back and start again, these are legacy parts and the industry requires solutions to ensure that plants are operating at optimum capacity and doing so efficiently.
In terms of where AM could be used is in addressing the requirements for obsolescence
and management of legacy parts. I said could because we're not there yet because current applications are in prototyping, tooling. The older the component, the more stringent the regulations to ensure that it satisfies the requirements for safety and performance.
TCT: On a panel at TCT 3Sixty, you spoke about opportunities around designing AM parts for maintainability. How significant is redesigning for AM? Or do certification requirements make those redesign opportunities a challenge?
UW: With AM, it's not like a traditional part where you have homogenised materials from which you're maybe machining. With AM, you're creating the material and even though it looks similar, it doesn't mean it's comparable. In nuclear, the whole point is to ensure that critical requirements have been met and in terms of qualification, that your material and your product complies or is equivalent to existing codes and standards for similar products. But the approach for demonstrating compliance or equivalence is where you have a lot of work in the creation of standards and implementing nuclear design codes and standards for additive because some may be transferable, in terms of maybe the base material or if you're using wire for DED, but there are other elements
that are specific without any basis for comparison.
I think durability and maintenance go hand in hand because when you want a part to last for 60 or more years, then you need to be able to maintain it for that length of time. In order to understand how it behaves, then you're looking at fatigue because over time, things wear and tear. In addition to your normal wear and tear, you're also looking at your operating environment so that adds an interesting dynamic to an already interesting situation where you have to think about your long-term implications for design for manufacturing and for maintenance.
TCT: You also talked about the sustainability opportunities, particularly around large structures. Can you elaborate?
UW: You need heavy engineering and plans to forge the reactor pressure vessels and you need special tooling and methods. AM is currently used for prototyping and tooling in the industry so that's another way to look at sustainability, rather than the traditional methods of making tooling, we can explore new methods. Some of the research I've been doing with another partner is on how we stack different types of materials and use AM to layer it or get the finished dimensions to be more creative in the way we apply the technology. I think the most important question is, how can we further exploit the potential of advanced manufacturing technologies to deliver the manufacturing efficiencies that are so desperately needed to address present and future challenges? I think, for instance, deploying AM for advanced on-site fabrication of large structures. There are
so many things we could do but the question is, how can we further exploit it? I don't think we're where we would like to be but I think we're heading in the right direction.
TCT: Where might AM capabilities need to improve in order to meet the demands of the nuclear sector?
UW: I think that work is ongoing, developing standards and submitting code cases but we have to substantiate the outputs on which these code cases and standards are formulated. In terms of the factors that would really help is a combination of skills training and experience. This is essentially looking at the challenges facing the sector and how AM can help. When I did my apprenticeship, I was handed a toolbox and I had to make the tools that went into it but our CEO talked about how he had to make his own toolbox and the tools. Now the next generation has the potential to print the toolbox and print the tools that go into the toolbox. So, I think it's just attracting the next generation of potential nuclear professionals and AM is such an attractive technology because the ability to really create what you're thinking, you can eventually review those designs, but the ability to start there, it creates that freedom for the next generation. I think that's the most important going forward because nuclear is not a short-term thing. It's a long-term approach and strategy. Part of that strategy is not just for the now, it's for the next generation, and the generations that have come before. How do we bring it all together? I think AM has the ability to unify all of these perspectives around a single technology and approach for working. It opens up the world of possibilities, but you have to start somewhere and AM is an accessible way of starting that journey and introducing the next generation to the whole world of nuclear manufacturing because the goal is to deliver clean energy for future needs.
[Editor: Answers have been edited for brevity and clarity.]
“Nuclear is not a short-term thing. It's a longterm approach and strategy. ”
Based on our 60 years expertise in manufacturing and development of refractory metals, we have developed AMtrinsic® atomized tantalum and niobium spherical powders and their alloys for demanding additive manufacturing technologies. Our ability to adjust specific intrinsic material properties enables us to push the limits according to the requirements of your application.
TANIOBIS GmbH announces the expansion of its metal additive manufacturing powders by addition of C103 (Nb-10Hf-1Ti) and FS-85 (Nb-28Ta-10W- 1Zr) pre-alloyed powders to its product portfolio. High-temperature strength, superior creep properties and their excellent processability with AM make these alloys great candidates as structural material for various aerospace applications. Additive manufacturing offers design freedom enabling manufacturing of lightweight components with complex features e.g. rocket thruster with integrated cooling channels which is the main application of our AMtrinsic® C103 and FS-85 alloys.
AMtrinsic® spherical tantalum and niobium powders provide outstanding combinations of material properties customized for specific applications. Aligned with 3D-printing technology, AMtrinsic® powders can help overcome hurdles in various high-tech industries. The high temperature stability, excellent corrosion resistance and biocompatibility of AMtrinsic® Ta, Nb powders and their alloys deliver a perfect fit for biomedical (Ta, TNT and TNTZ), chemical (Ta, Nb, Ta-W) and aerospace (Ta-W, C103 and FS-85) applications. In addition, AMtrinsic® Nb with its prominent superconducting property found its application in superconducting industry.
Based on, dare I say it, the hype around additive manufacturing’s (AM) role in supply chain over the last two years, the notion of ‘send files, not parts’ might seem novel. But for Ivaldi, a company which specialises in helping heavy industry to digitise its distribution networks, that mantra has always been at its core.
Back in 2017, the company set its sights on the maritime industry, first partnering with Wilhelmsen, which operates the world's largest maritime network, to create an in-port AM ‘micro factory’ which could deliver 3D printed marine parts on demand. In the years that followed, Ivaldi’s business model shifted away from ‘factory in a box’ style solutions, but the principal, that shipping files can reduce inventories, speed up delivery times, lower costs and emissions, remains.
“The original idea was to build these local manufacturing centres at different locations around the world,” says Anna D’Alessio, Director of Engineering and one of Ivaldi’s first hires. “So, focusing on the ports because we had started with the maritime industry but also, once you get into the port, you're very close to other heavy industries as well - it's very easy to get parts from those locations to where they need to go. […] We came to realise as we started to look through the data that there are more and more parts that had a wide variety of materials that made the most sense, which meant there were a wide variety of technologies that made the most sense. Instead of limiting ourselves to creating these parts using the specific technology and materials we have, we wanted to be able to expand.”
While Ivaldi initially offered in-house polymer 3D printing capabilities, the focus today is on analysis – identifying parts and partnering with on-demand manufacturers. To support that, the company has developed proprietary software which screens procurement and supply chain data to determine which parts are ripe for digital distribution.
“What we're trying to do is shift to a digital world, helping companies become digitally ready,” D’Alessio explains. “We start by looking at their procurement data, supply chain data, trying to understand what that means. What types of parts are they producing? How much do they cost? Where these parts are coming from, how long it takes to procure, how often they order them,
how many parts they have in stock because of supply chain issues or just in case.”
From there, Ivaldi creates a digital twin of those suitable parts, sometimes implementing minor design changes to better suit the manufacturing process, and stores them in a digital warehouse, together with design and manufacturing files and relevant testing and certification data to provide to local manufacturers as needed.
D’Alessio says the company is having ‘promising conversations’ and there’s an overarching understanding that digital is the future. The challenge, however, is: how? To answer that, Ivaldi has started helping companies identify specific steps they can take to digitise their assets. That often means low-risk parts such as spider couplings and scupper plugs, which are prone to wear but can be produced quickly and inexpensively with polymer 3D printing. Progress is happening, and D'Alessio notes the upturn in joint industry projects and dedicated divisions within larger organisations focused solely on AM.
“I have definitely seen more companies starting to say that we know we need to use AM, or we know that we need to shift to this digital world or create a digital warehouse, we just need to figure out exactly how to do it.”
Part of that, D’Alessio says, is about recognising where AM makes sense.
“There's a difference between having a part that is hard to source that you need to find a new way to make or be able to make on demand versus finding parts that are specific to AM. It's important to understand what the benefits of the technology are, which technology makes the most sense based on how this part is used and what it looks like, as opposed to just trying to fit something into that technology, just so you can say that you have a 3D printed part.”
But it’s not just end-users that need to be convinced. The shift to digital requires buy in from OEMs who have long been the main source of spare parts and equipment. Rather than replacing their role within the supply chain, Ivaldi is actively trying to work with them to rethink their own business models.
“What we're trying to do instead is work with the OEMs, to say, you're only usually supporting these parts physically for X number of years. If you work with us, you can support them digitally forever and there's no extra work. Once that part exists as a digital file in our digital warehouse, then you can continue to earn those royalties every time they're produced.”
There are other challenges, namely around certification, and Ivaldi is working with DNV in maritime and API in Energy, for example, to help create standards, but that trust will come with time and sharing of successes.
“There'll be more data, more longevity of these parts,” D’Alessio concludes. “And that'll help people to understand that this is a technology that will work.”
In a university research lab in West Lafayette, IN, a doctoral student is exploring the potential of a novel 3D printing technique to develop solid rocket propellant.
The motivation for trying to 3D print solid rocket propellant is to gain more control over its geometry – since this can affect how quickly propellant burns – and by the end of the research, Purdue University Assistant Professor Monique McClain will prove out the ability to 3D print a traditional mixture with all the volume loading content of traditional propellant and with no defects induced by the 3D printing process.
She does this with a 3D printing technology that utilises a vibrating nozzle which facilitates the flow of highly viscous materials. The key material is an ammonium perchlorate, which boasts particle sizes of around 200 microns, while the hydroxyl terminated polybutadiene binder used has a honey-like consistency. The viscosity requirement of the build material and binder is important for this application
because, per McClain, there is a minimum number of particles required in rocket propellant for it to burn.
Purdue’s novel printing technology – called Vibration Assisted Printing – was developed by Emre Gunduz because there was no such printing technology to be bought off the shelf that could print parts in the viscosities Purdue needed. In 2018, that was not just true of ammonium perchlorate, but polymer materials too. There are markets out there yearning for things to change.
“What we’re doing with solid propellants, doesn’t just have to stay relevant to solid propellants,” McClain told TCT.
Earlier this year, BCN3D joined a select few others in the commercial 3D printing space looking to enable the printing of materials with higher viscosities with its Viscous Lithography Manufacturing (VLM) technology. A material’s viscosity is measured in
centipoise (cP) or millipascal-second (mPas) – 1cP equating exactly to 1mPas – and refers to its resistance to flow because of its molecular makeup. Such flow resistance can make it challenging for some 3D printing technologies to process highly viscous materials.
Though BCN3D has so far specialised in extrusion-based methods, it has not followed in Purdue’s footsteps with a vibrating nozzle technique. Instead, the company landed on a lamination process in its bid to ‘enable manufacturing autonomy.’
“We wanted to bring value to this segment of the market by producing real functional parts, beyond prototyping, using resin,” BCN3D CTO Eric Pallarés Garcia explained. To do that, BCN3D developed a patented photopolymerisation technology whereby resin materials are picked up by a roller, laminated to the underside of a transparent film, transferred to the printing area and when the build
“We wanted to bring value to this segment by producing functional parts.”SHOWN: PARTS PRINTED WITH VLM WORDS: SAM DAVIES
plate rises to meet the recently laminated resin, a UV light engine cures the resin in specific areas to build up parts. The build plate then retreats, peeling the recently cured layer from the film, with the unused material being recovered for the next print. BCN3D claims VLM can process resins that are ‘50x more viscous than standard market resins’ and says it can also tackle multimaterial applications.
Per Garcia, VLM can process materials of higher viscosities because it is spreading resin like butter, rather than relying on the flow of liquid as in vat-based technologies. Other challenges in the 3D printing of highly viscous materials include the durability of the machinery required. Daniel Rothfuss, Global Head of Application Engineering for 3D Printing at Henkel – a BCN3D partner – noted how the high force load of more viscous materials can damage build trays, while there are also concerns with the creation of air bubbles on the resin. Heating resins can make them easier to process but that reduces the viscosity of the material – something the likes of BCN3D are trying to move away from.
In Xaar and ViscoTec there are two more companies who are channelling their expertise into the development of print heads that can facilitate the 3D printing of highly viscous materials. Four years ago, Xaar exhibited its High Laydown inkjet technology for photopolymer materials at TCT 3Sixty, with plenty of additional R&D ongoing since.
High Laydown allows Xaar to output ‘a lot of material very fast’ and increase the viscosities its print heads can handle from 100 centipoise to 130 centipoise, enabling parts with enhanced material properties.
“What high viscosity is enabling is true additive manufacturing,” Xaar Business Development Manager for EMEA + Israel Gareth Neal suggested. “There’s 3D printing, which makes parts in 3D, and then there’s additive manufacturing things which goes beyond making shape. We can put conductives into the ink, we can put dielectric properties into the ink, ceramics for structure or heat deflection temperature.”
ViscoTec, meanwhile, is developing printheads for filament 3D printing systems, with its vipro-HEAD range said to be able to process pastes with viscosities up to 1,000,000 millipascal-second (mPas). These
printheads are said to be able to gently flow material when building up parts and are compatible with off the shelf epoxy resins, acrylates, silicones, waxes and more.
Xaar has identified several niche applications within 3D printing for High Laydown, including windshield frits (those black dots that protect your eyes from the sun) and digital braille on packaging labels. ViscoTec, on the other hand, sees a lot of scope in automotive, medical and sealing applications, though Business Development Manager Simon Kasböck noted materials supply chain that makes sense for 3D printing volumes are lacking –particularly for silicones.
BCN3D’s solution on materials has been to align with Arkema and Henkel to work on the development and supply of highly viscous 3D printing materials for VLM. With this pair, BCN3D has set its sights on acrylic resins, epoxy resins, silicones and materials filled with inorganic fillers like metals or ceramics. With such an offering, BCN3D is looking at enabling elastomeric applications with good rebound energy return, while also hoping to facilitate parts with flame retardancy, low emissions and good insulation properties.
“If you bake a cake and only have flour, eggs and sugar, you can do a good cake, but if you have access to more ingredients, you would be able to do something more tasty,” Garcia said. “With high viscosity, you’re getting rid of limitations in terms of the ingredients you can use to make your formulation and to make your product.”
“It’s like giving an artist a full colour palette when they’ve had monochrome for their entire career,” Neal offered.
It would be fair to say that
with this year’s launch of VLM, the print head developments for inkjet and extrusion technology by Xaar and ViscoTec, the material development at the likes of Henkel, and even the high viscosity capabilities of machines like the ETEC Xtreme 8K, a trend is emerging. McClain also suggested the vibrating nozzle technique developed at Purdue could, in theory, be used for high viscosity polymers.
And you don’t have to look too far to find the applications. Whether it’s in the implementation of braille on a label, the production of a medical device in a hospital, or the development of rocket propellant in an R&D lab, there is a demand for the durability of traditionally made parts, and the geometric freedom of 3D printed ones.
“The additive manufacturing industry is looking for more durable and functional resins and products to unlock new applications in automotive, railway, medical, everywhere where you have very demanding requirements,” Rothfuss said. “Also, long-term stability is one of the many requirements we are frequently asked [about]. And one possible solution to fulfil those needs and to develop new resins is to add functional additives into the formulation.
“What you’re enabling with a higher viscosity printhead, or a higher viscosity technology, is not only material capability, there’s [also] a resolution and speed which makes manufacturing viable,” Neal finished. “You’re giving materials engineers a wider gamut of materials to play with, you’re giving them a wider range of applications they can fix, so really what we’re giving is opportunity.”
As creative 3D printing job titles go, it probably doesn’t get much better than the one that belongs to Naomi Kaempfer, Art, Design and Fashion (ADF) Creative Director for Stratasys.
It’s a role Kaempfer has been building towards since 2003 having led fellow 3D printing pioneer Materialise’s .MGX department, working with artists, designers and architects to explore the use of 3D technologies in creative markets. Now at Stratasys, the purpose, Kaempfer tells TCT, of the additive manufacturing (AM) leader’s ADF business is to ‘dig deep’ into 3D technologies and investigate new applications in the design, fashion, and art sector.
“We’re not looking at prototyping,” Kaempfer emphasised, but rather “ways to use 3D printing technology for manufacturing.”
ADF is an area Stratasys has been working in for a long time, with Kaempfer at the helm since 2014 overseeing projects with designers like Jenny Wu and fashion house threeASFOUR on statement jewellery and fully 3D printed garments. Having proven the effectiveness of its multi-colour, multi-material Polyjet technology across numerous creative collaborations, with artists like Julia Koerner already experimenting with printing directly onto fabric back in 2020, these efforts
recently led to the launch of a new machine, the J850 TechStyle, an evolution of its J-series 3D printers, engineered towards creative markets to allow inkjet polymer 3D printing onto textiles.
“We’ve [already been] working in fashion activities, […] these were more unique pieces for ladies like Björk or Lady Gaga,” Kaempfer explained of some early projects. “In this kind of style, it was more the idea of wearing a sculpture on top of an underskirt. The fixture that we
needed to figure out for that sculpture to work on the body was quite complex. Since our R&D team was able to solve the topic of 3D printing directly to textile and now the textile is carrying the dynamics of the 3D print, we can go much more into the details.”
The TechStyle can process a range of CMY Stratasys VeroVivid resins, producing over 600,000 colours, along with Stratasys Vero ContactFlex, a transparent coating which can be used to simulate different soft textures and finishes. The technology was the focal point of a collection at Milan Design Week this summer, which brought together seven design groups to produce luxury garments, accessories, and cosmetics under the theme of ‘Reflection.’
“This collection is a reflection on the last two years and what it means to us as designers and customers and anybody involved in the market,” Kaempfer said of the collection’s inspiration. “What happened in these two years? And how does it change our perspective on design, on consumerism, on production and on our society as a whole looking forward in the design sector?”
Three main pillars: personal space, social inclusion and mindful manufacturing, are woven into the collection which includes work from designers Karim Rashid, Jasna Rok Lab, Ganit Goldstein, FORÆVA, Assa Studio, Illusory Material, and KAIMIN. Stratasys also worked with Dyloan and the D-house fashion innovation centre in Milan, where pieces from the collection were presented throughout Milan Design Week, and where Stratasys’ technology has been made the focus of a new D-House Academy for fashion designers. The resulting pieces feature a mix of textures, transparencies and themes inspired by everything from natural textures of the seasons found in Goldstein’s
Than have a look on our TruPrint 3000. In addition to performance increase with fullfield Multilaser option, the focus of the TruPrint 3000 is on improving process robustness and various operating scenarios. High process reliability due to newly developed gas flow and high part quality are proofen with Melt Pool Monitoring. The 3D printer can be tailored to your production process needs.
More information www.trumpf.com/s/truprint-3000
heavily textured “GnoMon” collection to Assa Studio’s Origami inspired customisable clutch bag.
“We never had this kind of aesthetic appear or being offered in the past,” Kaempfer said. “If there is any possibility to bring elements on top of textile, this is usually done by hand, very labour intensive, and requires very high skill and a lot of years of knowledge. We're not competing with this or trying to throw this away. But we're offering another solution to bring very highly complex aesthetic solutions to the textile.”
The leap from handcrafted to digital similarly requires an understanding of digital skills in order to design for and exploit the advantages of 3D. While several 3D printed garments have popped up on runways and red carpets over the last decade, 3D printing directly onto textile is a new technique, and Kaempfer shared that the ADF department has sought collaborations with architects, fluent in designing in 3D, to work alongside designers on the project.
“There is a nice link between the architecture way of thinking and construction and the mapping out of forms in the architectural way of design that is very, very relevant here for textiles," Kaempfer said.
In perhaps one of the best monologues in comedy-drama history, Meryl Streep’s Miranda Priestly famously uses a lumpy blue sweater (“It’s not just blue, it’s not turquoise, it’s not lapis, it’s actually cerulean.”) to provide a biting lesson on how the high fashion industry influences the clothing selection on your local high street. Just as the icy fashion magazine editor describes the influence of Oscar De La Renta’s colour palette trickling down into more affordable,
everyday attire, the influence of 3D printing on textiles could, depending on its accessibility, follow a similar trajectory.
“We are focused on the high-end fashion market,” Kaempfer said. “This is very, very new. Even though [Stratasys has been working] on this for quite a while officially, for sure this is only the first iteration, the first step in penetrating the fashion market. As this is starting to play a role in the high-fashion market, I'm certain that we will also see a huge evolution coming and a rollout that will help us to answer more and more needs and requirements for the fashion market and allow us to embed easier and more accessible solutions.”
While that might not materialise as a clothing rail stocked with wholly 3D printed garments, it could, very feasibly, mean taking advantage of the TechStyle’s ability to print directly onto fabric to add embellishments onto existing garments, potentially breathing new life into tired pieces.
“The possibility of taking a denim that you have in the closet and applying it onto the machine and 3D printing an embellishment on top of your favourite pants or your jacket or your T-shirt,” Kaempfer said of the potential upcycling value. “The idea would be to make it very high-end but also customising very simple elements that allow us to celebrate garments that we already have and give them a second life.”
It's something renowned fashion trend forecaster Lidewij Edelkoort has called 'an answer to a million prayers' thanks to the possibilities the machine allows for embellishment. But it also could help answer pressing calls on the industry to reduce the damaging impact of fast fashion by shifting the way we consume fashion from mass produced commodity to a more considered and customised view. That could mean reworking a pre-loved item of clothing or even using 3D technologies to customise a piece to perfectly fit the customer, produced locally and on-demand.
“We try to understand what does it mean to be attached or to consume responsibly and to manufacture responsibly, but these two things are intertwined,” Kaempfer explained. “So we also want to educate our consumers and allow them to feel more engaged with the product. The idea that fashion has to be retailed 10 seasons per year and entertain customers for a very short span of attention and then be thrown into the garbage is not wonderful for our environment. Through 3D printing we want to show the story that we can have something that is much more valuable to us as consumers to be involved in the creation of it, customise, personalise, and have aesthetics that are phenomenal and cannot be created by any other means.”
“We want to educate our customers and allow them to feel engaged.”SHOWN: TRAVIS FITCH SWATCH BOOK SHOWN: GANIT GOLDSTEIN - GNOMON (PHOTO BY YARON ATIYA)
The subject of climate change is now a mainstay of our news cycles. Whether it’s protests by activists, pleas from campaigners or the policies (or lack thereof) set by governments, rarely a day goes by without the theme debated or the latest developments reported.
In additive manufacturing (AM), it is not quite a daily occurrence, but the soundbites in interviews and declarations in marketing messages aren’t exactly rare. Through TCT’s editorial and conferencing channels, we have covered the topic extensively, platforming those who believe AM can be used to boost the sustainability of products, and those who warn of potential greenwashing.
As recent extreme weather events would suggest, it is important that AM, like any other manufacturing sector, gets it right.
In 2019, Sintavia led the charge and set up the Additive Manufacturer Green Trade Association (AMGTA) - read our Q&A with the AMGTA's Sherri Monroe on page 34. In establishing the AMGTA, Sintavia CEO Brian Neff suggested that while the AM industry focuses on the cost and time benefits of the technology, less emphasis is placed on the ‘very real environmental benefits of AM over traditional manufacturing.’ That point may be up for debate, but from the outset, the AMGTA aimed to raise awareness of said benefits… in good faith.
To do that, the organisation was to commission its own research efforts, and as of this year, award those members of its organisations that did the same. In May, the AMGTA handed out 27 awards to 20 of its member companies –including 6K Additive, EOS and Materialise, all of whom have recently carried out lifecycle assessments (LCA) on 3D printed products.
“We want data-driven decisions,” 6K Additive President Frank Roberts told TCT. “Our goal is, ultimately, we want carbon neutrality. The only way to understand how to get there is to generate the data and benchmark, so that was the first step. But other companies are starting the process – some are doing more ESG (Environmental, Social & Governance), some are doing LCA – but the fact that people are talking about it, I think it’s awesome. I spent a lifetime in wrought products, and no one really talks about it, so it’s exciting that that’s now happening. But getting the data is key.”
Getting the data is what 6K Additive has sought to do via Foresight Management, which recently carried out two LCAs on behalf of 6K. While a
titanium material processed with UniMelt was found to use up to 76.7% less energy and produce up to 78.4% fewer carbon emissions compared to plasma and gas atomisation processes, its nickel material faired even better. Measuring UniMelt against induction furnace gas atomisation for the nickel LCA, Foresight Management reported that UniMelt used 125kg of material for 100kg product compared to 400kg with the gas atomisation process, while also only using 6,265 megajoules (MJ) of primary energy and 5,135 MJ of non-renewable energy compared with 69,780 MJ and 58,759 MJ. This is said to amount to a 91.5% reduction in global carbon emissions.
When carrying out LCAs, vendors like 6K Additive typically seek to outsource the testing of processes to third-party organisations that have no dog in the fight. Then, the organisation will make a holistic assessment of a process, considering, for example, the extraction and raw processing of raw material, the inbound shipping, the printable powder production, and the distribution of the final product to the customer.
The information gathered here can then be used to either promote the sustainability benefits of a product and its manufacturing process or to guide the relevant parties in finding ways to mitigate whatever issues have been highlighted – often bringing things into scope that hadn’t previously been considered.
As LCAs become more prevalent, the process is becoming slicker and companies like EOS are learning to re-use findings where applicable.
“What we see is we’re getting faster because [for] some parts, you can use them again for other [LCAs],” Björn Hannappel, EOS’ Head of Sustainability, said. “If we’re doing an LCA on PA 1101 and then we have the next one which is
based on a PA 1101 but [with] more ingredients added to it, then we already have half of it. We don’t need to do this again.”
“It’s similar to where we were years ago when it came to calculating business cases and cost per part,” added Florian Alefeld, Senior Manager, Academy & Consulting, EOS. “It used to be we have a time study, now we need to measure the energy input into the system – it was pretty manual, we had to do a lot of calculations to get a very accurate cost per part that was more than +/- 20%. Now, we’re at a point where we need a few input data, we have a database in the back end that spits out a cost per part and even a return-oninvestment calculation. It’s the same for carbon footprint. Today, we do a lot of manual labour and data collection, but we will get to a point where, just like a five-dollar cost per part, we will have a five-kilogramme carbon equal emissions per unit and additional data, such as how much agricultural lands have to be used.”
“WeWORDS: SAM DAVIES
Last year, both EOS and Materialise carried out LCAs on 3D printed eyewear products, with both returning positive assessments compared with conventional means of manufacture. In the EOS study, which was carried out by Fraunhofer EMI, the 3D printed YOU MAWO eyewear product was said to yield a carbon footprint that was 58% lower than the conventional product and create 80% less waste. It also posited a reduction in powder refresh rate, the development of bio-based materials and the use of less expensive packaging as areas for improvement.
“We need to do more work around the lifecycle analysis,” Stephen Fitzpatrick of the National Manufacturing Institute Scotland added on the same TCT 3Sixty panel. “Until we’re able to measure that, we can’t prove something as sustainable or not. I think we all talk about the design opportunity for additive manufacturing and when you look at manufacturing in general, 80% of the top three emissions are locked in at the design phase. So, additive, with that design opportunity, does present that opportunity for us to be more sustainable. But we do need to measure that and until we do, we can’t prove that.”
Though all the LCAs highlighted in this feature point to positive environmental benefits of AM, it would be remiss to suggest as a blanket statement that AM is a sustainable technology. As industry consultant Phil Reeves noted during a panel session at TCT 3Sixty, “it’s application based.”
He continued: “I did some studies years ago with Virgin Atlantic on metal additive parts and what we realised was if we were making airframe components that would last for the duration of the aircraft, which is 30 years, it would be sustainable. But cabin interiors are refitted every five to seven years, so a five-to-seven-year lifecycle on a metal additive lightweight part doesn’t offset the fuel gain. So, even in aerospace, you could say, well, lightweight, aerospace, [it] must be good in terms of reduction of fuel. But it’s not always the case.”
Not every LCA carried out for an AM process, then, can expect to yield a positive outcome. But as the world looks to turn greener in the face of a climate emergency, it will provide valuable intel for technology suppliers as to what application opportunities they can target today, and the improvements that need to be made to widen that scope tomorrow.
In its role as the foremost sustainability organisation in the AM space, the AMGTA will continue to recognise efforts made by the industry players, but the true incentive will come from manufacturers who are working toward ever more demanding CO2 emission targets.
One of the most impactful changes in 3D printing is to switch to renewable energy. At Materialise headquarters, we’ve maximized the number of solar panels and operate all our processes on green energy — drastically reducing our carbon footprint.
2Create more transparency.
Today, there is insufficient transparency to make blanket statements about the sustainable nature of 3D printing. That’s why we are committed to creating more and more diverse life cycle analyses (LCAs). Innovate and invest.
3Materialise introduced Bluesint PA12, a rapid prototyping material that lets you print with 100% re-used powder. With Bluesint PA 12, powder that would typically be wasted can get a second life to make new parts.
Making 3D printing
sustainable
1Start by organizing yourself in a sustainable way
more
will require building a shared commitment to make a difference.
ARE YOU READY TO JOIN THE REVOLUTION?
Brilliant conversations’ at the UK's ‘leading additive manufacturing (AM) show’ which provides ‘a good melting pot for all the different technologies that are important to the industry.’
That was the verdict of several exhibitors and visitors to this year’s TCT 3Sixty, which saw hundreds of the former and thousands of the latter convene to showcase and evaluate the latest AM technology.
During the show, 60 world-class presentations were delivered across three conference stages, with Boston Consulting Group, the US Air Force and BAE Systems all featured, while HP, Additive Industries, EOS and more exhibited on the show floor.
Here, we have a quick snapshot of what went on at this year’s TCT 3Sixty, with plenty more available at mytct.co/3Sixty2022.
Not only did TCT 3Sixty see WAAM3D launch its RoboWAAM metal AM platform but the Cranfield University spinout also took home the trophy for TCT Hardware Award - Nonpolymers. With a build envelope of 2 x 2 x 2 metres and the ability to process virtually any wire form material, the young company is targeting industries such as aerospace, defence, and oil and gas, for the production of large-scale metallic components.
Filomeno Martina, WAAM3D CEO and Cofounder, said: “We're providing another tool to the modern manufacturing engineer. I'm very hopeful that we can improve the performance of metal making across the board."
Read more: mytct.co/WAAM3D
From a son and mother start up (Construct3D) to bio compatible reabsorbable resin (4D Biomaterials), innovative levels of all instances were present. That’s what really did it for me. This was an event where everyone could connect and be on the same level.
As I went from booth to more amazing booth, I was greeted with smiles and lots of high fives. I felt like I was with friends I had known for years. The layout was easy to navigate and the #TCT3SIXTY sign was the perfect spot for a little robot battle action.
Being able to have an impromptu battle session, then getting to check out ground-breaking machines all in the same spot is special. The TCT3Sixty event blended the best of both worlds together. From those just starting out to the leaders of our industry, I felt like this was a place where ideas and innovation could flow freely and work together. Based on the projects we have coming out of this event, that’s exactly what happened.
E3D is one of the foremost providers of FDM 3D printing hotends, extruders, nozzles and more. The company was founded when three friends identified a solution to a problem an entire community shared. In the development of an all-metal hot-end, the trio were onto something. They started the company from scratch, expanded into other FDM 3D printing componentry and established themselves as a market leader. Celebrating its tenth year in business, E3D co-founder Joshua Rowley sat down with TCT to reflect on the journey so far.
“People buy good technology,” Rowley says. “If you’re selling a product that solves a problem and makes life easier, then people are going to be interested in it. This industry, the people are very connected, they know what they want, they know what good looks like.”
Read more: mytct.co/E3Dinterview
TCT 3Sixty will return in 2023 between June 7-8, so save the date! For more TCT 3Sixty content between now and then – including interviews and podcasts from the show floor –visit mytct.co/3Sixty2022
TCT: What compelled you to join the AMGTA?
SM: This role, when I was first approached, really intrigued me. It really made use of my background and my interests. I've worked for a couple of very large non-profits in the US so I have that experience of bringing together a broad group of stakeholders around a common cause and understanding their sometimes competing objectives. I also have a background in the for-profit side and in innovations. So this is very much like that, not only in the fact that this is a new organisation so there's a lot happening and a lot of wheels turning, but also that innovation side of new technology and getting that out there and helping a broader audience understand the value and the potential.
TCT: You’ve previously said ‘AM has the potential to be transformational in how we sustainably manufacture.’ Can you elaborate?
SM: AM has been around for many years but really is coming into a new stage of life where we're going beyond just using it for things like prototyping, which is always going to be a big part of it because of how effective that is, but moving beyond simply making the same part that was made traditionally and making that through additive. Now, there are certainly instances where that provides huge value but I think where we're really going to see this next stage is where we're leveraging the power of AM design. The organisations that are able to do that now and leverage that are really seeing huge gains and so I think it really has the potential for really transforming the manufacturing landscape. I think we're going to see new processes, new supply chains, new systems, new
products, and it's really going to be a matter of finding those best uses.
TCT: We’ve recently seen more emphasis on LCAs in AM. What do you think this says about the industry’s commitment to sustainability?
SM: Talk is cheap, as they say, and actions really are where it's at. The work that 6K and Materialise and others are doing is so important because it provides information but it also shows the transparency involved. Transparency is critical because transparency leads to credibility and if you're making claims or suggesting that things are more sustainable, you really need to
be able to demonstrate that. Part of that process is actually defining what the lifecycle is. So how far back do you go? And how far out do you go in the life and the end of life of this product? So really studying that full lifecycle because the gains are in different places than it would be through traditional manufacturing.
TCT: There’s a worry around ‘greenwashing’ in AM. Where do you think the biggest challenges or unknowns lie?
SM: Whether it's looking in the hearts of an individual or looking into the heart of a corporation, sometimes it's hard to assess what their motivations are. I think we all know that there are companies that simply want something they can put in a paper or put on their website and say ‘we're green’ and move on about their business, while other organisations truly are committed to this. Sometimes those first steps that companies make may look like greenwashing but it may just be their first steps. They went for a couple of easy wins. What can we do quickly, easily? Why wouldn't you do that?
The low hanging fruit, let's go there first. So I think we have to be careful in labelling some of those things as greenwashing when it just may be, they're getting started. Let's recognise that, let's applaud that. Let's assist them, how can we help them share learning so that they can move further?
What I see in our membership is companies that are truly committed to this, this is not something that's being forced on them, that they see this as a strategic benefit.
Listen to the interview in full: mytct.co/SherriQA
[Editor: Answers have been edited for brevity and clarity.]
know that Additive Manufacturing offers undrea med-of potential. In addition to the printer, however you also need the upstream and downstream processes plus the experts, who have mastered the technology. You’ll only find all this at Formnext!