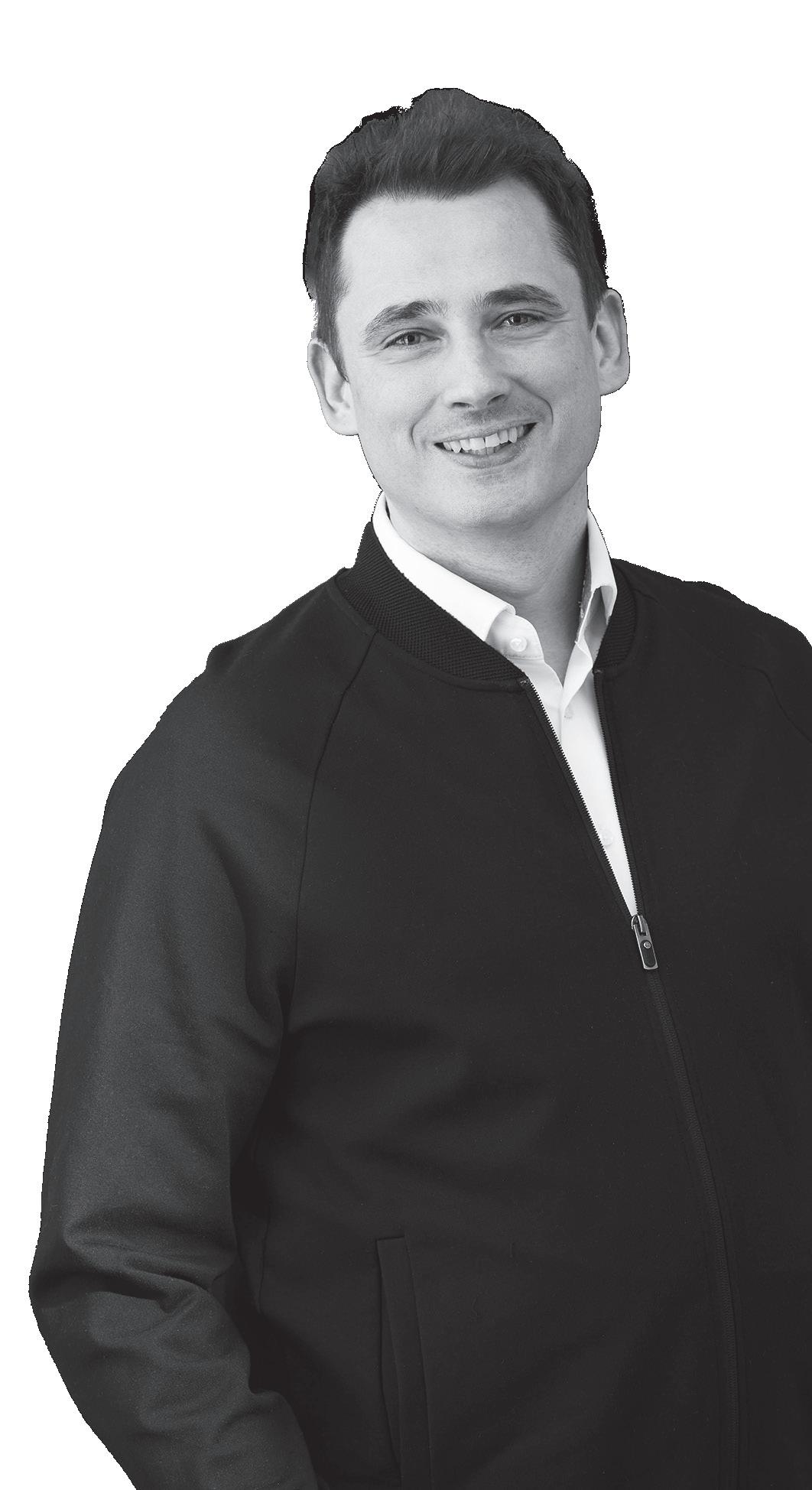
7 minute read
‘AMAZON FOR ADDITIVE’
from TCT Europe 30.6
by TCT Magazine
Laura Griffiths speaks to MakerVerse CEO & Managing Director Markus Seibold about AM services, supply chain, and lessons learned from Siemens Energy.
Q: You spent the past seven years as VP Additive at Siemens Energy. Tell us about how MakerVerse came about. Siemens Energy has gotten really deep and really good [at] metal powder bed fusion for high temperature applications for gas turbines. This was the real sweet spot. When I left, early 2022, there were more than 200 people now working on additive and the company overall has more than 50 metal powder bed fusion printers installed in our global Siemens Energy network. […] There is the saying ‘when you have a hammer, then everything looks like a nail’ and what happened at Siemens Energy, we looked at every potential component like a metal powder bed fusion, hightemperature AM component. The reason Siemens initially started to think about MakerVerse was that there was a need for a second pillar in the strategy. To fulfil a few requirements, it should give Siemens Energy access to a whole array of different additive manufacturing technologies and materials that the company didn't have in its own very deep footprint. Number two, it should do that at industrial-grade quality so that Siemens Energy really could take prototypes all the way to a certified spare part. And number three, it should support specifically the on-demand nature of nonplannable prototypes, of unsteady spare parts. And with those three requirements, one-stop shop, industrial grade quality and on-demand manufacturing, the idea was created to turn this into a digital platform model. It's intended to be something like the Amazon for industrial 3D printing.
Q: We understand MakerVerse aims to offer a ‘full technological service spectrum’. Which specific technologies/ services will that include? This is an always evolving story. If you go to our platform today, you will find on the metal side, metal powder bed fusion, and on the polymer side, you will find selective laser sintering, HP’s Multi Jet Fusion and FDM technology. Then there's of course a different set of materials below each of those four technologies and our operations team is continuously working on expanding the technology and materials portfolio. […] We will broaden our scope step by step. Currently we are an additive manufacturing platform but we believe that this needs to be integrated with conventional technologies like CNC machining, so over the next weeks and months we will also broaden the technology focus beyond additive to also include conventional technologies so MakerVerse is a true one-stop shop for both additive and conventional requirements.
Q: We’re talking a lot in this issue about how AM can bring agility to supply chains. How does MakerVerse fit in? There are two very fundamental different use cases [for AM]. One is, you design a new part, taking into account the design possibilities that additive offers and then you can think about all these topics like performance improvement, weight reduction. So, you start a new project, you design a new component for a new product. Then you can, from the very beginning, design for additive and then you also need to think about industrialisation of this part in terms of qualification of the entire process: machines, powders, printing processes, post-processing. The second category is that you have an existing part, you have an existing supply chain, and you want to mitigate your supply chain risks by, for instance, reducing lead times by nearshoring production through additive manufacturing, and then usually your design is an existing design that has been sourced from wherever, and rather than improve the design of the part, you want to mitigate the supply chain situation. The big challenge that I see still for additive here is cost because the original design wasn't designed for additive. So, you usually face higher product costs and you need to trade these higher product costs with the effects you gain on lead times or on not having a part at all, because of supply chain disruptions. And yet, in the second case of supply chain resilience, you still need to make sure that when you convert a conventional part to an additive part, you meet certain properties in terms of material.
What a digital platform like MakerVerse can offer for the first category, the design iterations, it can offer you super-fast access to different technologies and materials,
SHOWN:
MAKERVERSE CEO MARKUS SEIBOLD
SHOWN:
MAKERVERSE IS AIMING TO BECOME THE AMAZON OF AM
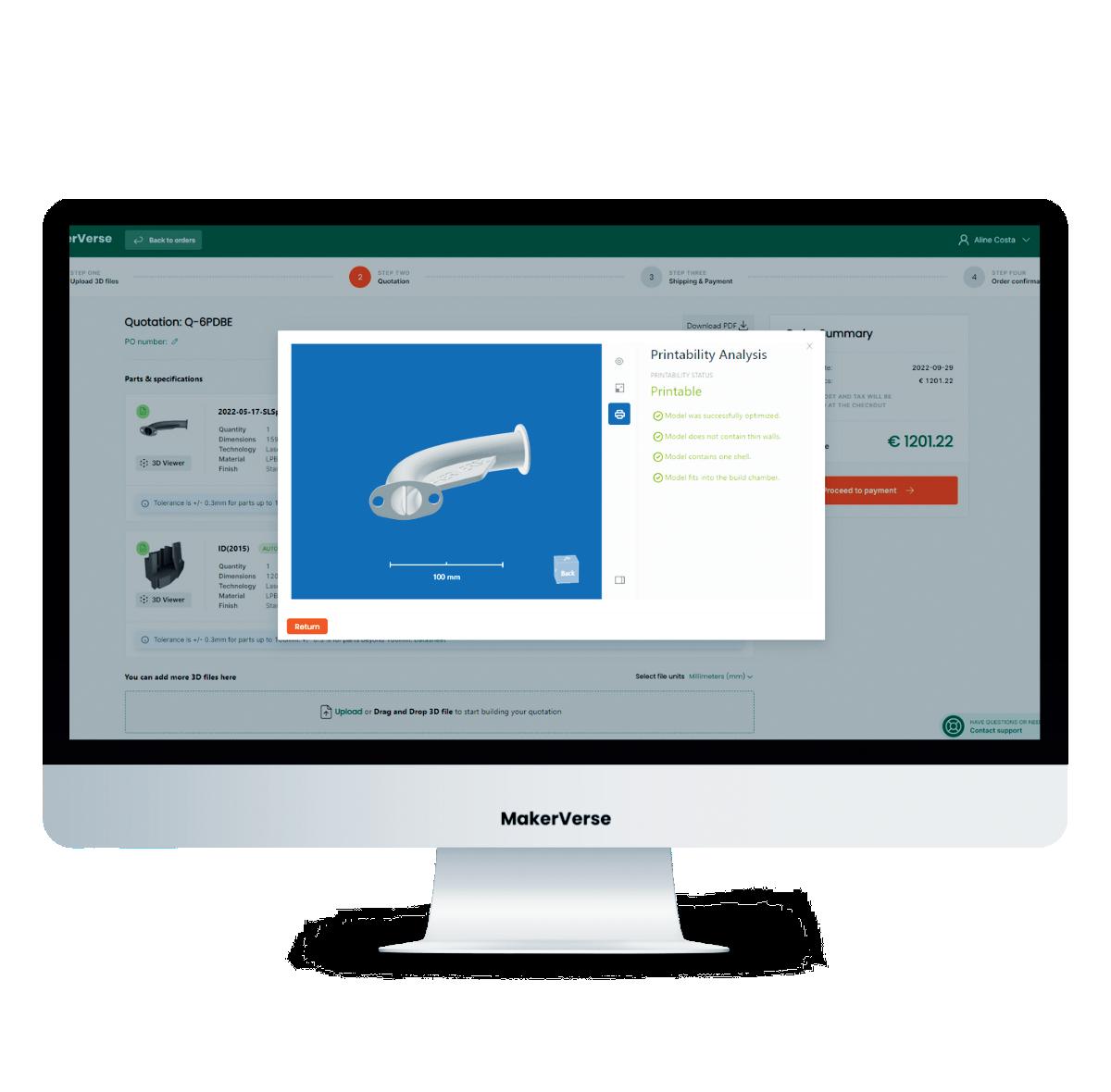
and it can really help you to accelerate development speeds, that's the classical use case. When it comes to the second use case, of on-demand, supply chain needs, […] for every technology/material we offer on our platform, we have multiple suppliers behind each technology/ material combination. So when you have an on-demand situation, that you need certain parts that run in your supply chains, quickly, on-demand, in unsteady quantities, MakerVerse as a digital platform has the advantage of always having, at any point in time, multiple suppliers qualified for this material/ technology combination so we can react super quickly.
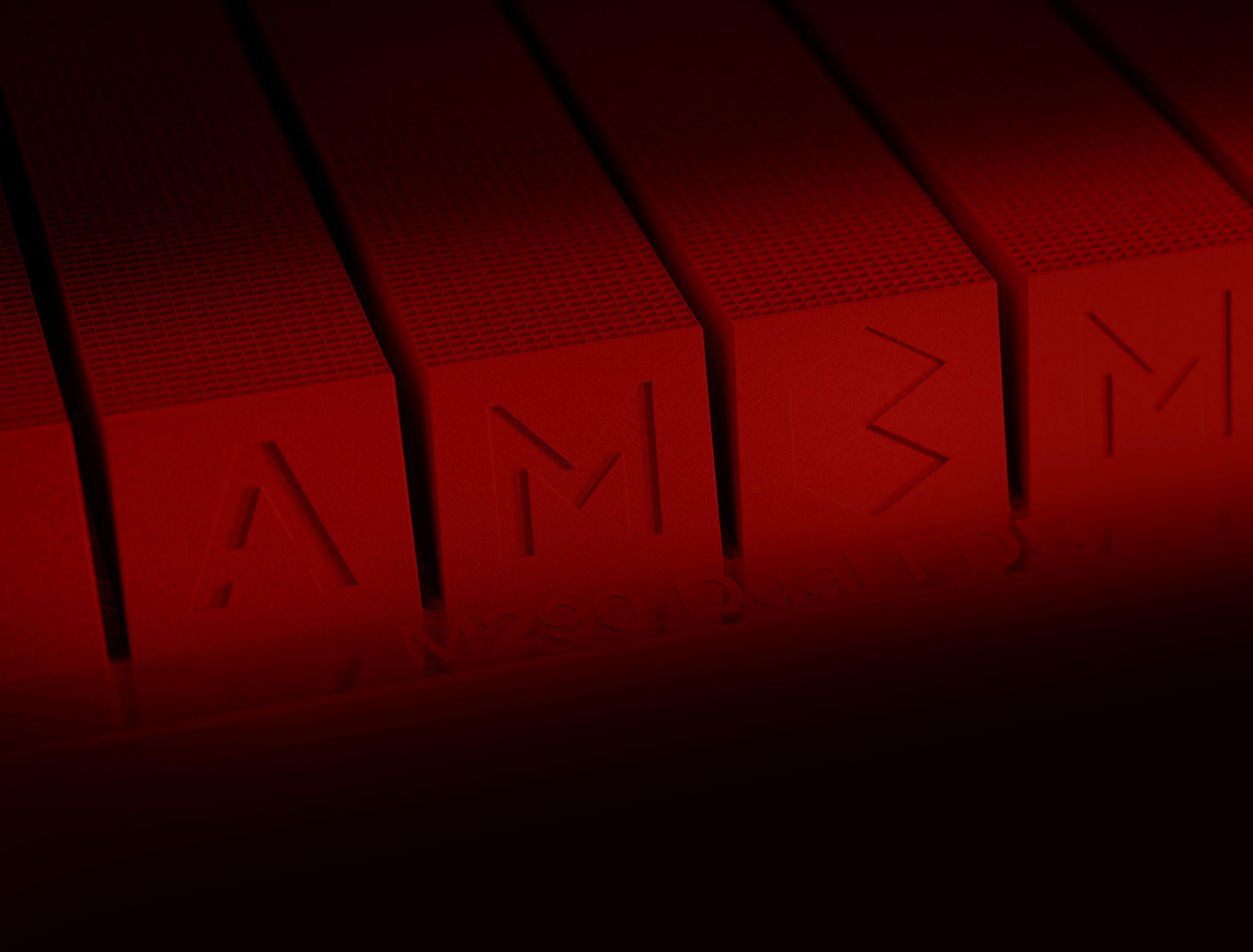
Q: Who is currently using MakerVerse? I can't share names but I can share applications that I think are quite interesting. One category we are currently seeing is development projects. Heat exchangers being one example where companies are currently developing and designing different designs for heat exchangers, trying to see how much they can push the engineering limits in terms of wall thicknesses, cooling hole sizes in the internal structures and they want [quotations] for different designs quickly, they want to know how fast it is until you can really have hardware so that they can test this. […] Another customer category that I see now emerging is potential spare parts on-demand. So, it’s parts that are not necessarily designed for additive from the get go, this is a legacy part and in most of the cases actually, even unsteady demand or potentially even lower volume parts. […] We currently see traction from customers that are prospectively interested in converting these legacy spare parts to 3D printed spare parts. A third category is production aids, grippers for robots and certain toolings or jigs and fixtures.
Q: Siemens is arguably one of the biggest industrial users of AM. What lessons were you able to learn there about adopting the technology? I spent quite a bit of time in the past years reflecting with the team on what were certain hurdles and what were success factors for Siemens Energy because I believe our global teams have really done a fantastic job of being super effective and focused on driving additive into serial production. […] I think an already very commonly accepted success factor is that you need to stop trying to quote the same designs that you optimised for turning, milling, injection moulding, and hope that additive can make those parts cheap - it just doesn't work. Usually when you try to copy the same design, and make it by additive, additive is at a cost disadvantage. It's all about design for additive. At Siemens Energy, for instance, you can build internal cooling channels into parts that you could never cast, you could build combustion system components that allow you to better mix air and fuel in a way that you reduce emissions. In a corporation like Siemens Energy, like any automotive OEM, like any aerospace OEM, additive is a new thing and big companies have a lot of responsibility for the end product. It's very hard to introduce a new method of manufacture and design because you have no long-term proven experience. So, it's actually really difficult for an engineering-driven business to say, 'I'll put an additive component on my car, on my plane, on my gas turbine,' because you just don't know how this material or how this part will behave over time. So, you need a certain risk culture. This doesn't mean that you go just completely crazy and put parts you don’t understand on engines, but you need openness on the level of the famous middle management in terms of product owners, component owners, part owners. […] So, you need this risk culture on the mid-level so that you incentivize additive, look at it, and push it against real component applications.
Listen to the interview in full on the Additive Insight podcast: mytct.co/AIPodMakerverse
[Editor: Answers have been edited for brevity and clarity.]