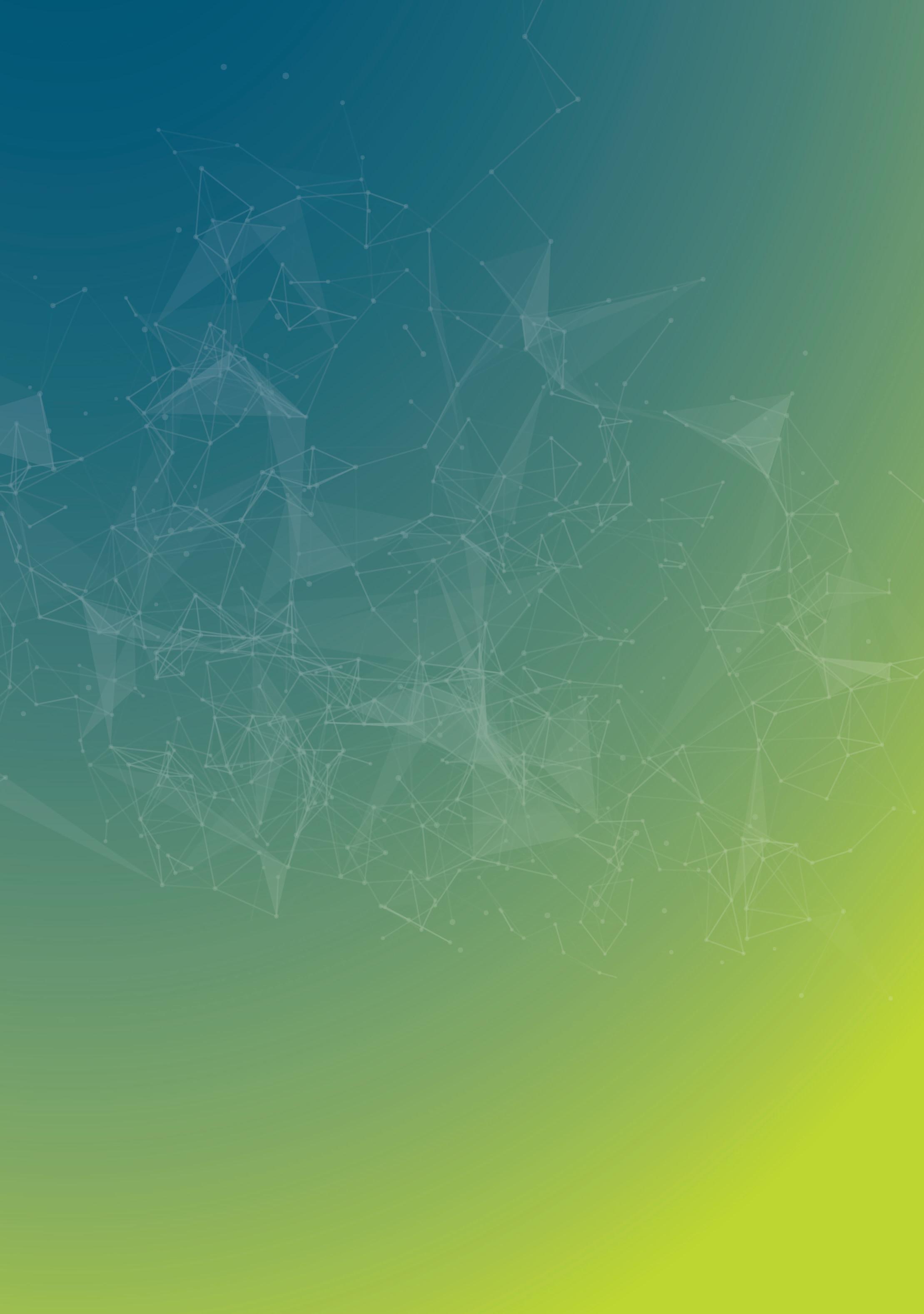
26 minute read
TECHNOLOGY & SPEAKER HIGHLIGHTS
from TCT Europe 30.6
by TCT Magazine
FORMNEXT PREVIEW
2022 A look at the speakers and exhibitors headed to Frankfurt.
It's that time of year again when the clocks go back, the weather gets cooler, and the additive manufacturing industry descends on Frankfurt.
As we all ready ourselves for Formnext, TCT has compiled an extensive preview of the event across the next ten pages. Throughout, we bring you technology highlights, product teasers and speaker spotlights.
On the show floor, you can expect to see product launches from AMT, Lithoz, Authentise and Solukon; product updates from Machineworks and TRUMPF; and a European debut from Inkbit.
And on the TCT Conference @ Formnext stage, you can get the latest additive manufacturing insights from GE Healthcare, Divergent Technologies, Finnegan, Keio University, Boston Consulting Group, the Women in 3D Printing Board, and much, much more.
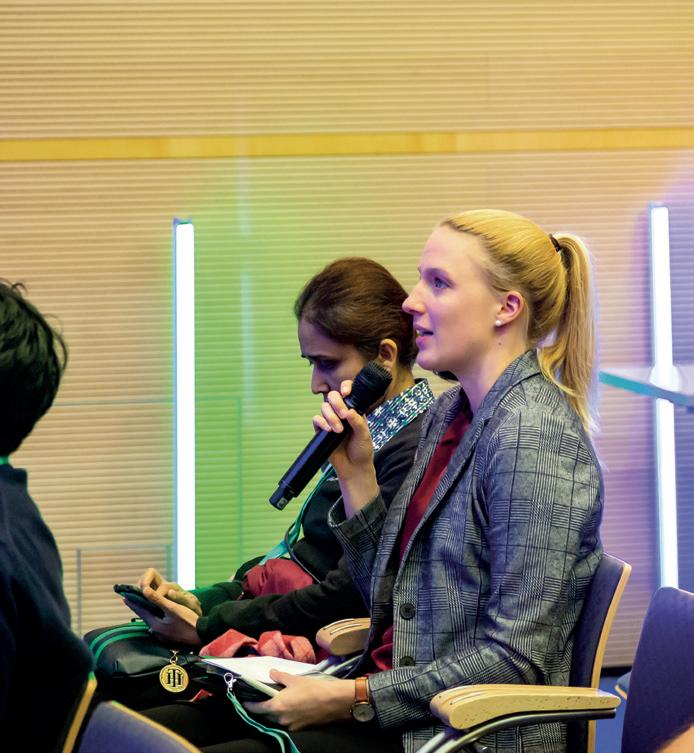
TICKETS FOR THE TCT CONFERENCE @ FORMNEXT CAN BE FOUND HERE: mytct.co/tctfnxt22
AND YOU'LL FIND TEAM TCT IN HALL 12.0, STAND E42. SEE YOU THERE!
CONFERENCE
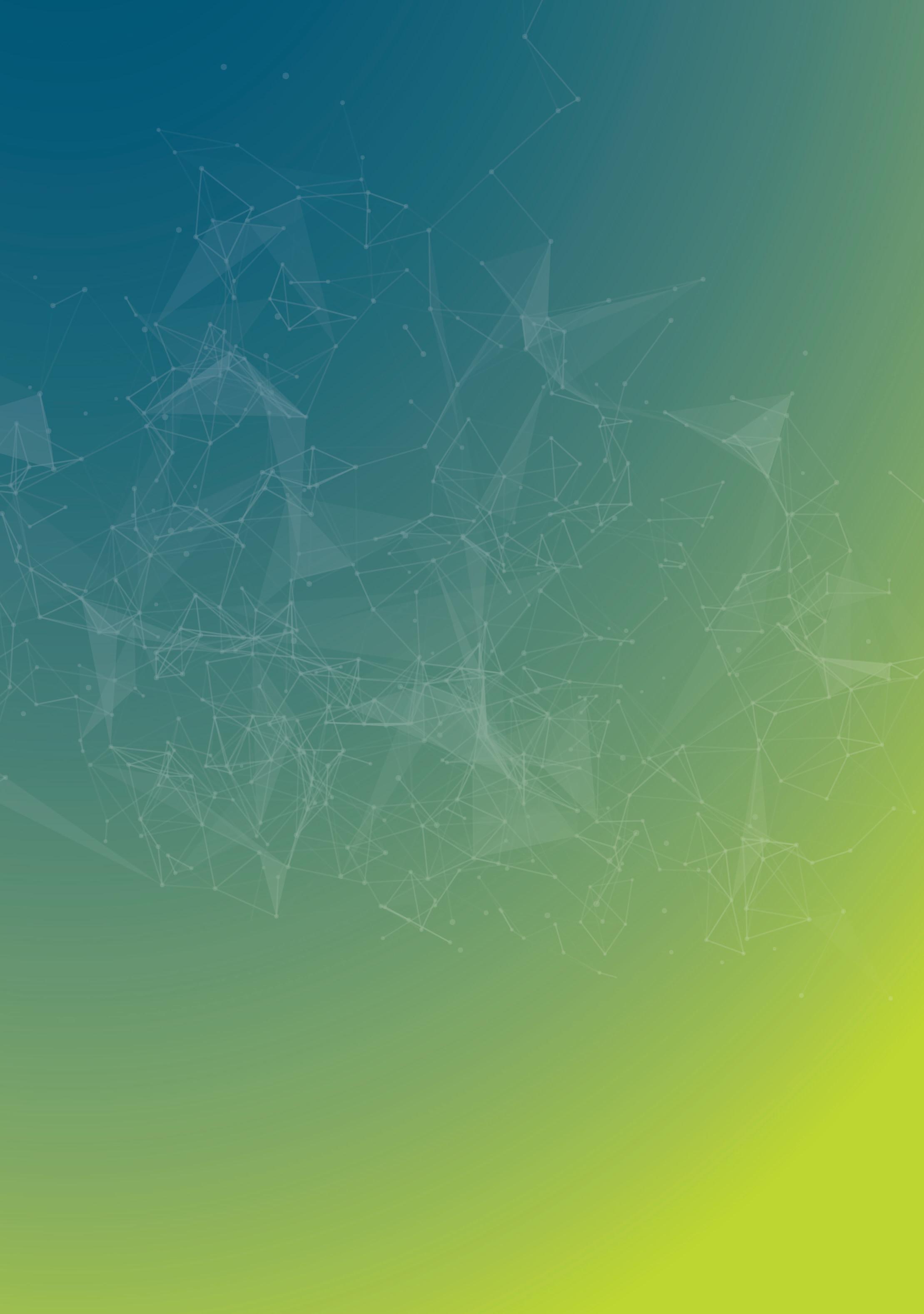
TECHNOLOGY & SPEAKER HIGHLIGHTS
VELO3D
HALL 12.0 | STAND D01
At Formnext, Velo3D will be showcasing a range of parts printed on its Sapphire XC metal laser powder bed fusion printer. The Sapphire XC 1MZ system is equipped with eight 1KW lasers and a build volume of 600 mm x 1,000 mm. It was launched earlier this year to bring high levels of quality and productivity to service manufacturers, aerospace firms and defence customers.
nLIGHT
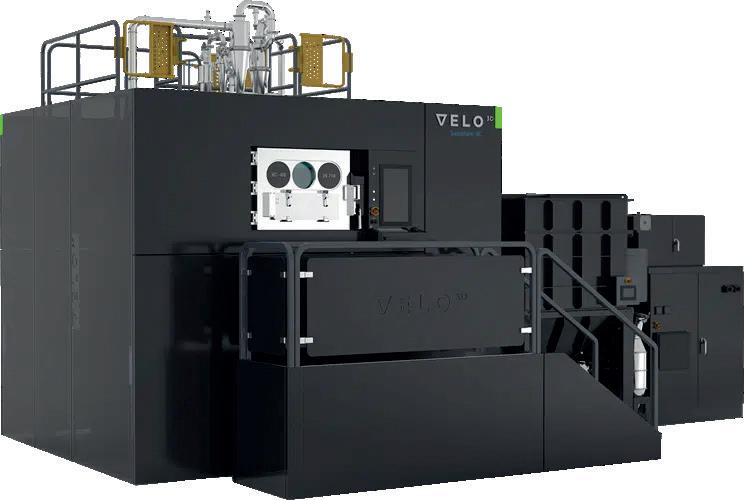
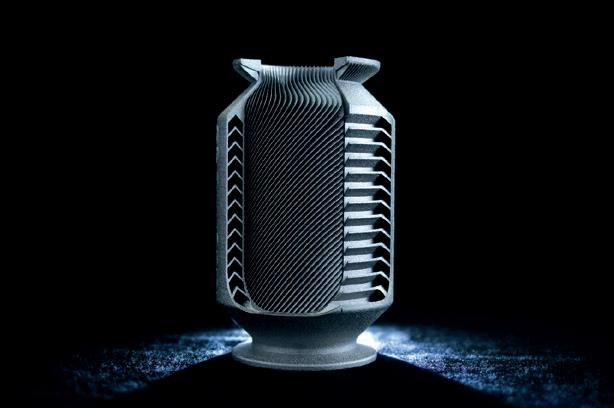
HALL 12.0 | STAND D132
nLIGHT will be highlighting its Corona beam-shaping lasers at Formnext with the launch of the AFX-1500. With its dynamic ring-beam shaping, nLIGHT’s AFX Series is said to enable faster printing, increased melt pool stability and improved material properties. The company will also feature the plasmo and cirrus digital manufacturing platforms, which provide a suite of advanced analytics and real-time data stream capabilities.
SPEAKER SPOTLIGHT
VISHWANATH NAYAK, GE HEALTHCARE
METAL ADDITIVE IMPLEMENTATION INTO PRODUCTION IN MEDICAL DEVICES | FRI NOV 18, 10:00-10:30
Q. What can you tell us about your presentation at Formnext?
A. I am presenting one of the unique case studies of metal additive (DMLM) part/assembly, that we pioneered at GE Healthcare into production in medical device[s] on a CT scanner. I am also going to talk on how the business case could be made despite several challenges today, and I will also touch base on how we established process of powder re-use strategies, with different types of machines, powder sources and parameters.
Q. Can you elaborate on the importance of materials evaluation for medical device development?
A. Material evaluation needs to be very carefully done with several established processes that we have developed in some areas with rigorous amounts of testing over years to understand its behavious over a period of time, for its sustainability and to check effect, degradation, etc. Challenges associated with each medical device are very unique to the type of device and its function, [for example] some have Autoclave requirements, cleaning and disinfection needs, MDR compliance, FDR compliance, IFR V0 flammability needs, and many other regulatory requirements.
Q. Who should come see this talk?
A. Additive machine manufacturers – metal and polymer; technology solution providers; consultants; academics & researchers; business collaborators and enablers. We are looking at developing and partnering with the ecosystem to continue [our] additive journey in a larger scale.
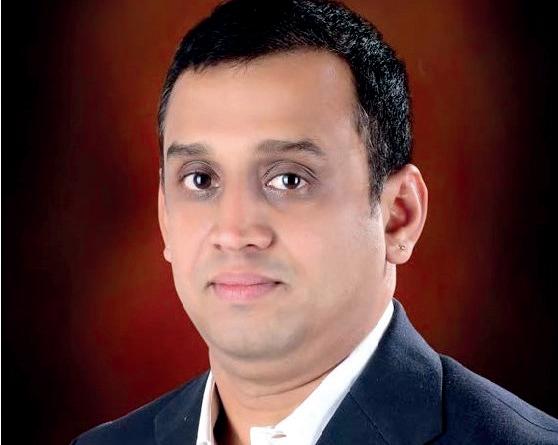
CIM 500 - High-performance, thermoset casting material that prints industrial molds for composites
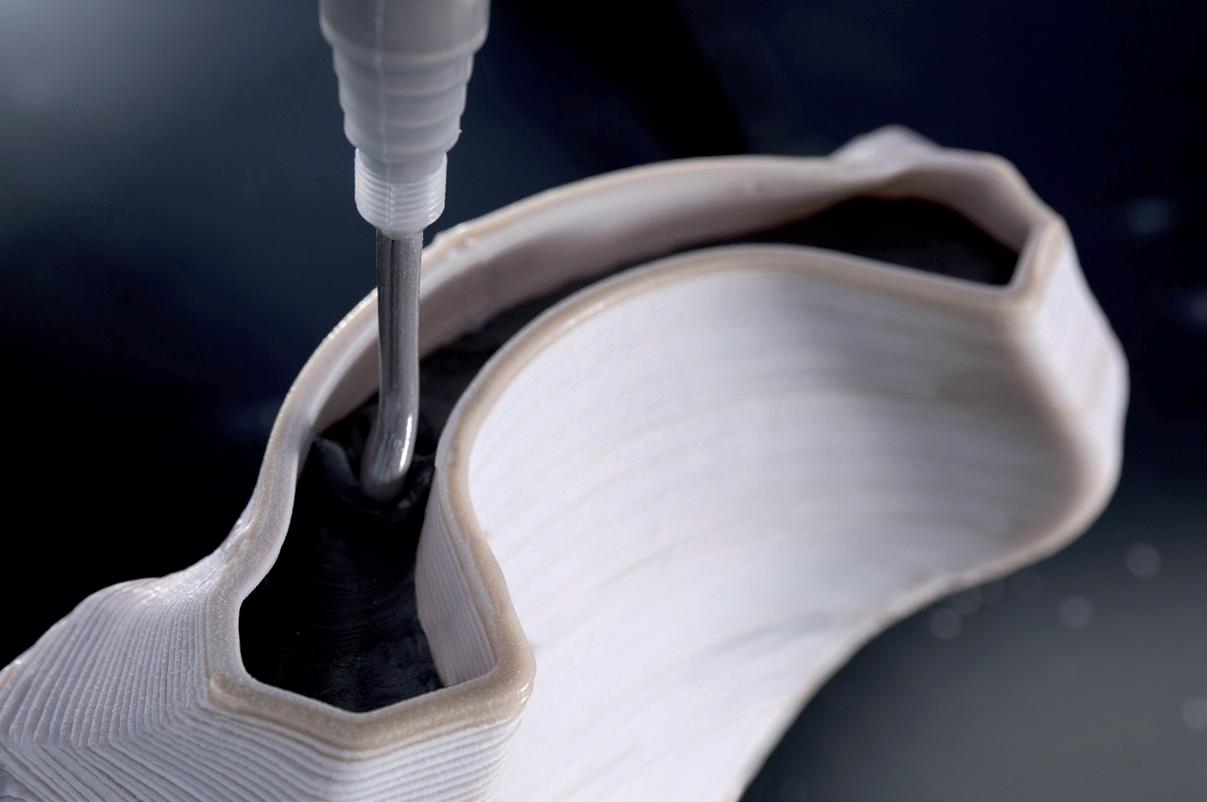
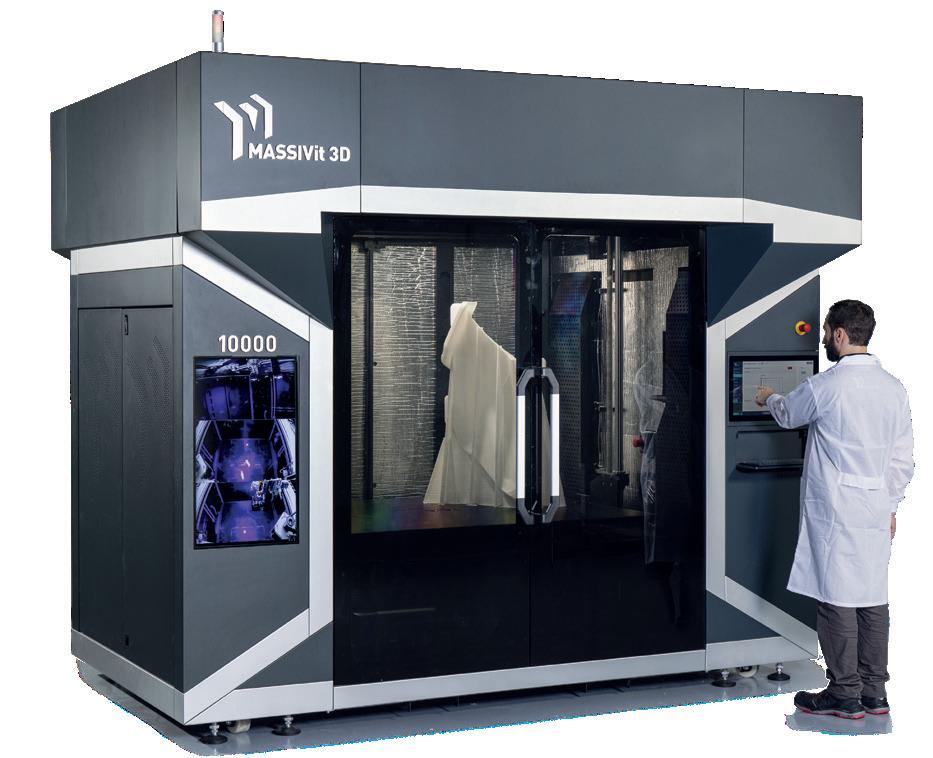
Large-Scale, Fast AM Takes a Leap with New, Thermoset Photo-Polymers
For additive enthusiasts, the focus has traditionally been on thermoplastic printing materials. However, advancements in fast-curing thermosets are shifting how we look at additive manufacturing, opening new possibilities for speed, build volume, and waste reduction.
One provider of largescale 3D printing systems, Massivit 3D, has developed an array of innovative, photo-polymer, thermoset “gels” that enable full-scale parts to be produced within a matter of hours. One of the properties that enables high-speed printing is the material’s unique viscosity – that practically eliminates the need for support structures.
The company’s range of “Dimengel” thermoset, thixotropic resins includes purpose-designed materials for requirements such as flame retardancy, highdefinition needs, and transparency. Massivit
3D is set to launch its strongest and toughest material to date at the upcoming Formnext show in Frankfurt.
Impact Resistance for Large-Scale AM
DIM 400 is an advanced thermoset material that provides twice the impact resistance of existing Dimengel materials, and a high Heat Deflection Temperature (HDT). Designed for production of large, sturdy parts, DIM 400 is also suited to harsher outdoor conditions as well as elevated transportation temperatures. It supports all five layer thicknesses available on the Massivit 5000 large-scale 3D printer.
Curing On-The-Fly
Dimengel thermoset materials enable manufacturers to directly print large parts and molds at up to 30 times the speed of thermoplastic-based 3D printers. Single parts can be printed up to 1450 mm x 1110 mm x 1800 mm and can also be joined together using the same material used for printing.
Unlike thermoplastic materials, Dimengel is printed and fully cured at room temperature and does not require melting or cooling down in order to cure. The printing heads have a specially customized UV ring that instantly cures the extruded material on-thefly while printing, allowing ready-made solid parts to be lifted straight off the printer without the need for post-curing.
Large Parts, Wide Applications
From automotive wide body kits, motorcycle panels and Formula car parts to customized marine end parts, railway fairings, and amusement park sets, Dimengel thermosets overcome pertinent obstacles in large-scale AM workflows. 500 material has a low CTE and a high HDT, making it suitable for a variety of manufacturing applications in the Automotive, Marine, Defense, Bath Ware, and Sporting Goods industries.
New Directions in Composite Material Manufacturing
Based on Massivit 3D’s thermoset AM materials, the company has recently launched an AM system set to change the course of composite manufacturing. The Massivit 10000 additive manufacturing system enables rapid printing of complex molds for composites as well as mandrels, masters, jigs and fixtures. It will be showcased for the first time at Formnext 2022. Advances in fast-curing thermosets are generating accelerated adoption of thermosets in the largescale AM arena due to their inherent benefits for workflow efficiencies.
For more information on thermosets or to schedule a for large-scale AM demo at Formnext, please contact Massivit 3D at
info@massivit.com.
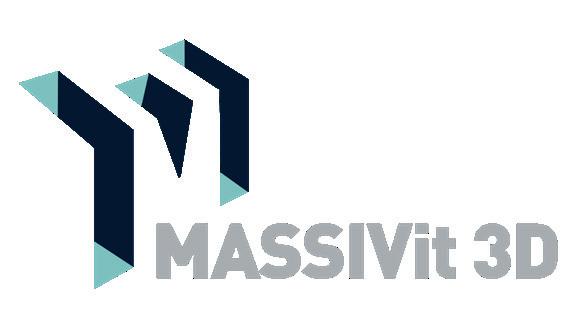
Based on the company’s new, hybrid Cast In Motion technology, the system’s printing head rapidly prints an outer sacrificial shell using a water-breakable thermoset material. The 2nd head intermittently casts a thermoset casting material into that shell as it builds, forming an isotropic, 3D printed mold for composite material components. CIM
New DIM 400 Material – Impact Resistant, High HDT
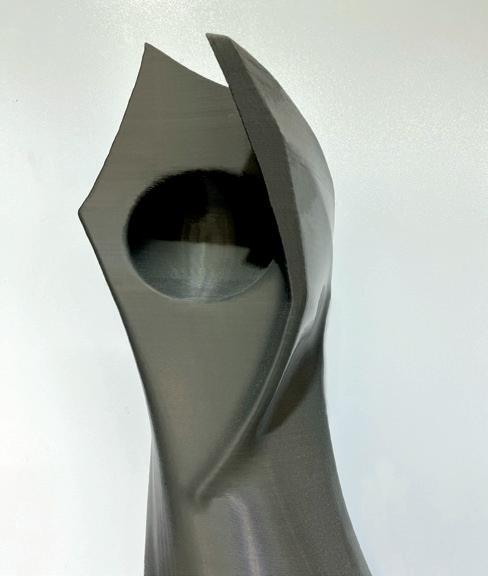
APIUM
HALL 12.1 | STAND E10
Apium will showcase its P400 additive manufacturing system. With independent dual extruder (IDEX) capability and a high flexibility in print head selection, Apium is delivering a multi-function platform that can process high-performance materials such as PEEK. The machine is also said to deliver outstanding layer adhesion thanks to its adaptive zone heating system, which helps to ensure part strength and quality.
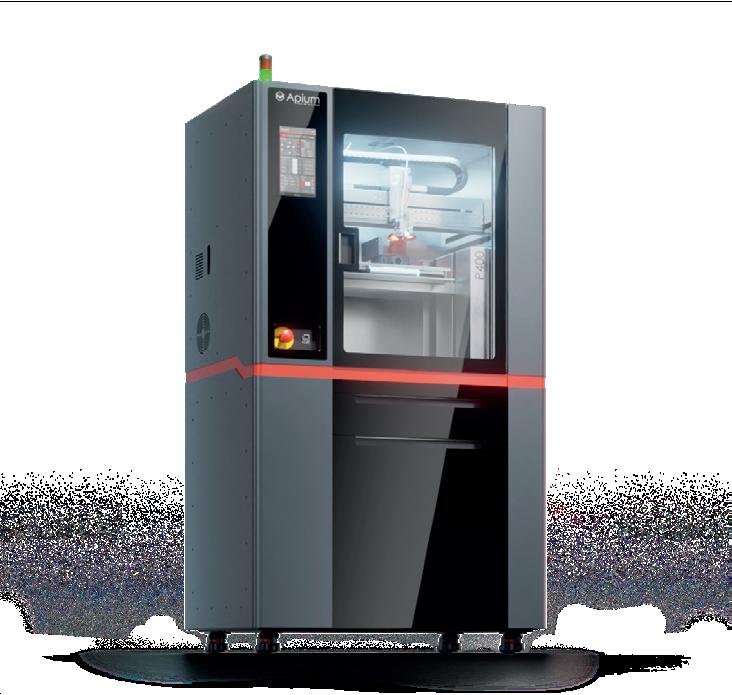
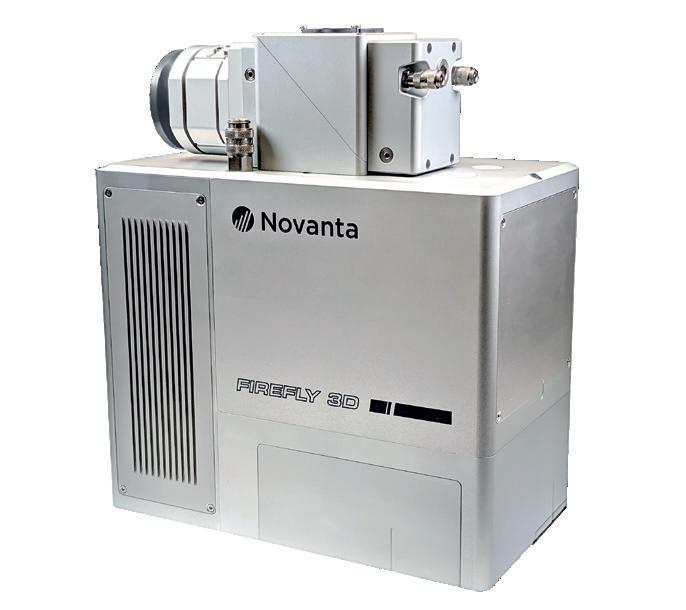
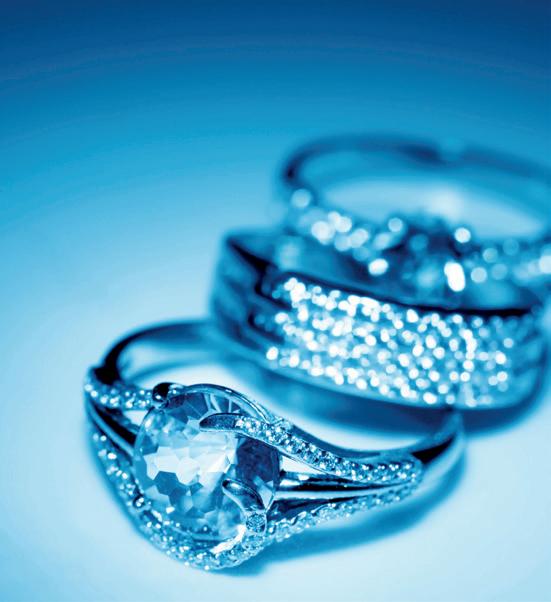
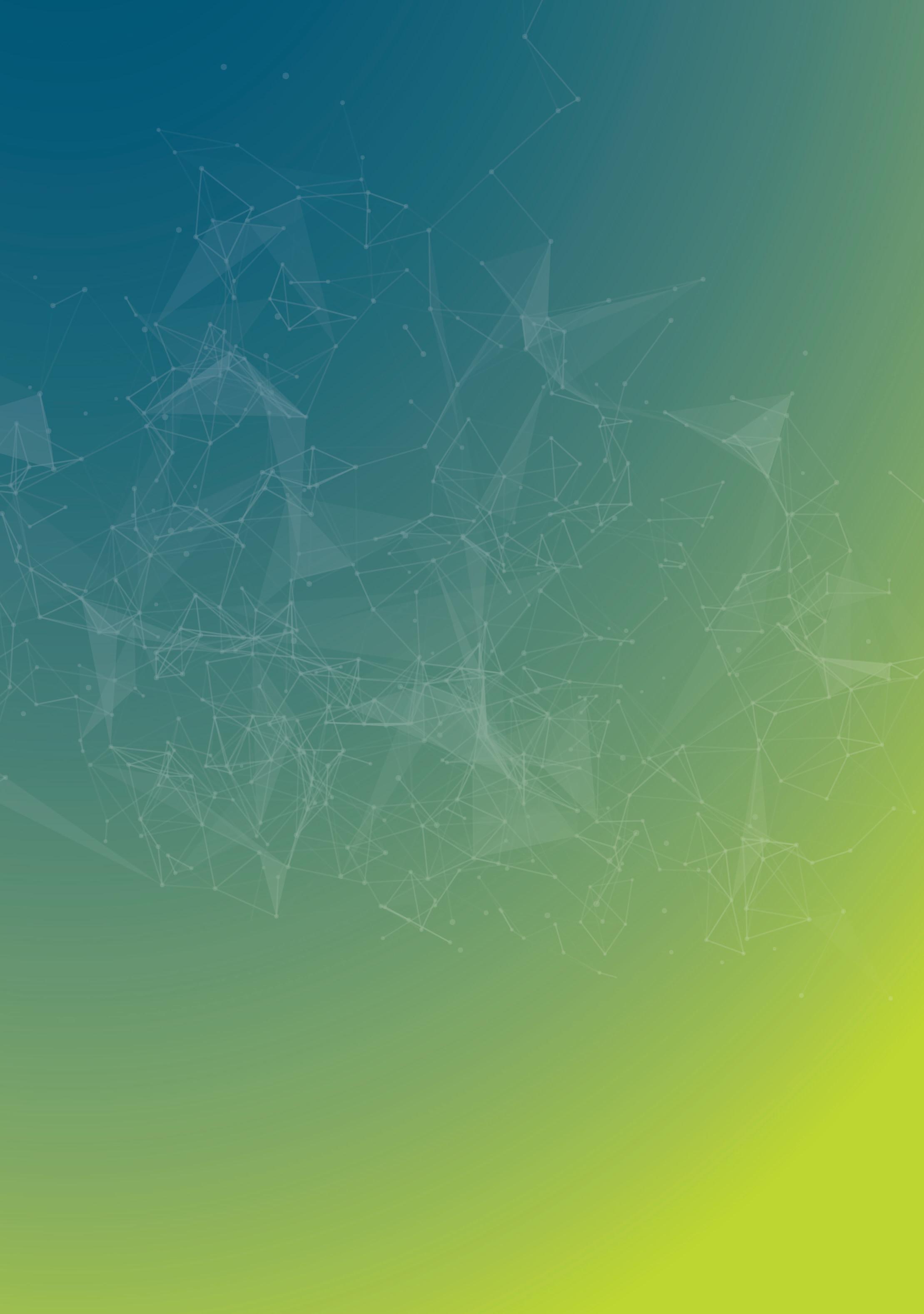
NOVANTA
HALL 12.0 | STAND E08
On the Novanta stand, the company will showcase its newly launched Firefly 3D 3-axis scan head designed specifically for laser powder bed fusion (LPBF) machines. The firefly 3D has been designed to boost performance of LPBF with monitoring and control, enabled by advanced processing tools that facilitate real-time changes to scanning operations.
PRIMA ADDITIVE
HALL 12.0 | STAND E81
Prima is bringing its Powder Bed Fusion (PBF) and Directed Energy Deposition (DED) offerings to Formnext. For PBF, its PrintGreen 150, featuring a 150 x 160 mm build area and 200W green laser, will be on show, while for DED, the lanus laser processing robotic cell will also be showcased.
ADDIBLAST
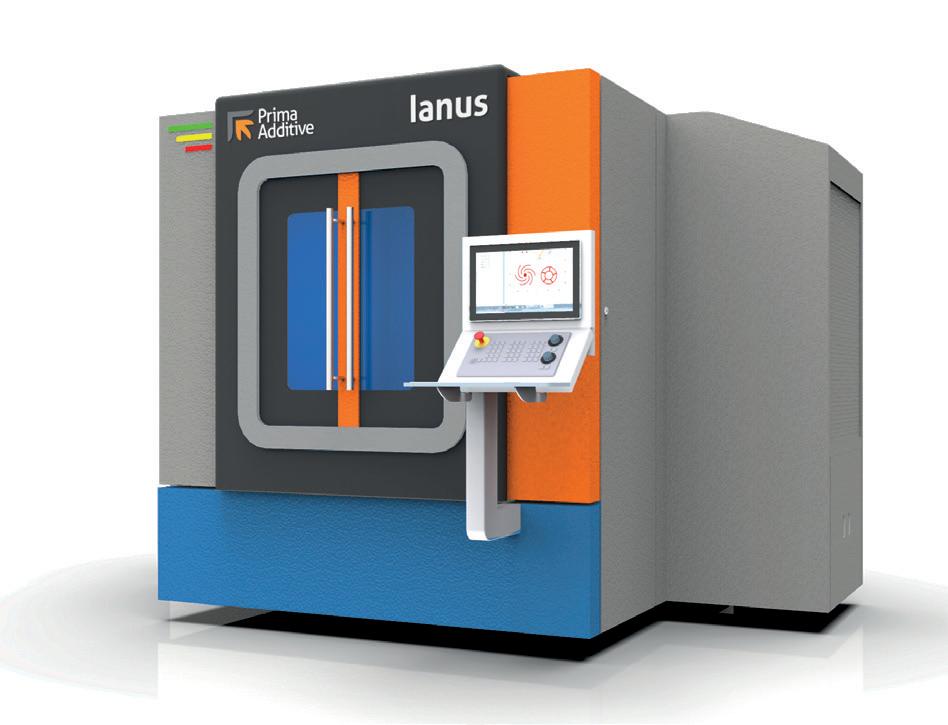
HALL 11.0 | STAND D28
Addiblast will display its depowdering, powder recovery and conditioning and surface treatment platforms, as well as a new app for real-time monitoring.
BOFA INTERNATIONAL
HALL 12.0 | STAND E18
BOFA will showcase its 3D printing filtration and atmosphere management systems, introducing an enhanced capacity 3D PrintPRO 4 and its new 3D PrintPRO HT.
SCIAKY
HALL 12.0 | STAND A74
Sciaky will be present to discuss its EBAM technology, which is being used to produce parts on land, at sea, in the air and in outer space.
FLOW-3D AM
HALL 12.0 | STAND B75
Flow-3D AM will share its latest developments in computational fluid dynamics, with a focus on modeling fluid flow, heat transfer, phase change and Marangoni effects for powder bed, extrusion and DED processes.
GRAPHY
HALL 11.1 | STAND D21
Graphy, a company backed by JW Holdings, will showcase its direct 3D printing clear aligner material and permanent tooth materials at Formnext.
SPEAKER SPOTLIGHT
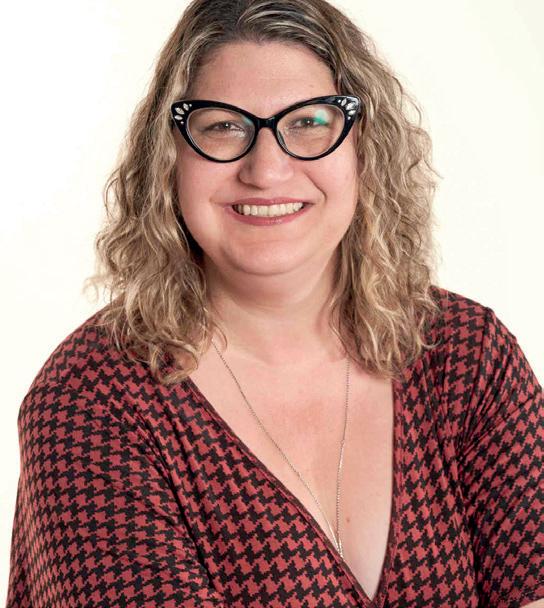
SARAH GOEHRKE, FOUNDER - ADDITIVE INTEGRITY
THE VITALITY OF THE AM WORKFORCE: A WI3DP PERSPECTIVE (A PANEL WITH WI3DP BOARD OF DIRECTORS) | WED NOV 16, 15:00-16:00
Q. What can you tell us about your panel at Formnext?
A. This panel is one of the first times the Women in 3D Printing (Wi3DP) Board of Directors will come together on a public stage to share a look at what makes this industry organisation so unique – and so vital. Wi3DP has grown to a global community of tens of thousands, and it all started with a single observation: there are significantly fewer women in the 3D printing workforce than there are men. That doesn't make AM unique, especially in manufacturing or tech more broadly. What it does do, though, is provide us with a base. For this panel, the Wi3DP leadership team will frankly and openly discuss what today's AM workforce looks like and examine opportunities for growth.
Q. You describe how the workforce in AM does not yet reflect the world in which it operates. Can you talk about how Wi3DP is working to change that?
A. The foundational Wi3DP mission was pursuit of gender parity in AM (an industry that currently comprises about 11% women). From there, we have expanded our mission statement to more broadly encompass support for growing and shaping an industry more reflective of the world in which it operates. That growth has come from the learning experiences of Wi3DP leadership, from hard conversations in diversity, equity, and inclusion, and from truly listening to the experiences of our colleagues across this global industry. Wi3DP isn't necessarily working to change this; rather, we're working with the industry to help change the status quo. It isn't on any one organisation to change existing culture or workforce approaches. What Wi3DP does is offer a starting point for connection, for conversation, for resources.
Q. Who should come see this talk?
A. Everyone. We’ll be addressing topics that offer insights to leaders as well as to non-managing team members. We’re all people; this is relevant for us all.
RAPIDIA
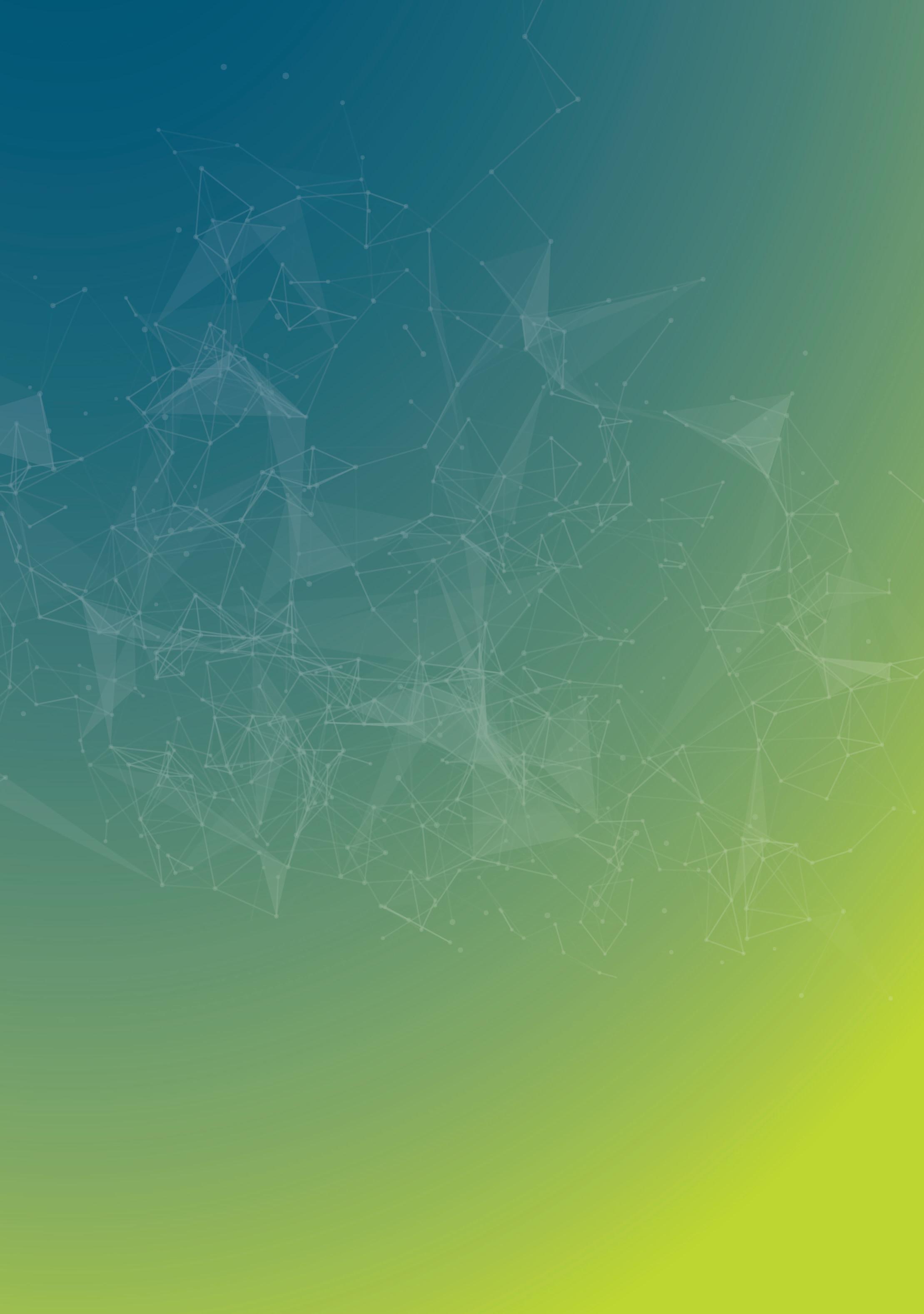
HALL 12.0 | STAND E122
Rapidia will be exhibiting its newly-launched F2 advanced vacuum sintering furnace, which was developed to support its metal extrusion printer. The company first launched its two-step bound-metal AM system, based around an innovative water-based feedstock, in 2019. The new sintering furnace is said to amplify the performance of its AM system by providing excellent metallurgy with low sintering gas consumption and high atmospheric purity.
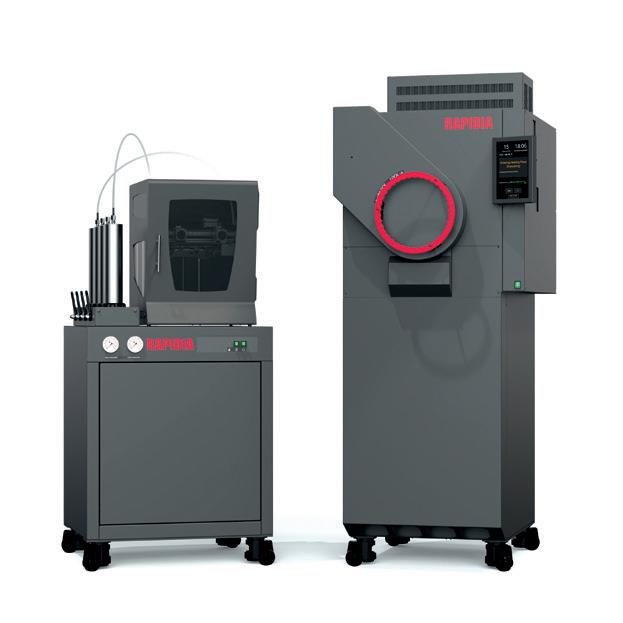
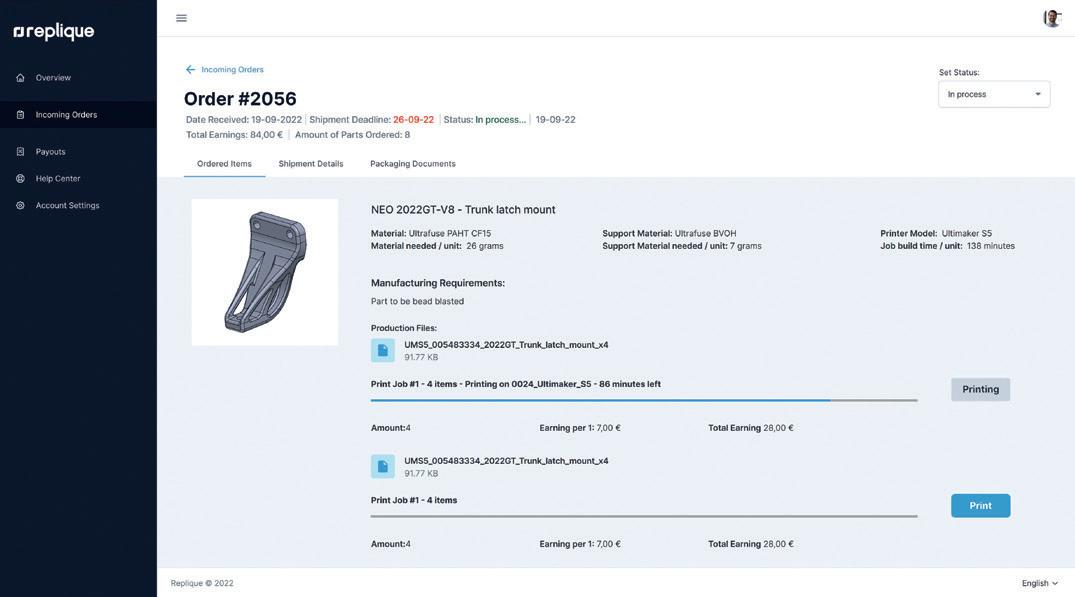
REPLIQUE
HALL 12.1 | STAND B73
Replique will use Formnext to launch its RSure quality tracking model, which enables users to track 3D printed parts directly and ensure they meet the necessary quality requirements. This platform gives users the power to set quality specifications, undertake digital inspections and trace parts, before the parts are sent to the customers.
AUTHENTISE
HALL 11.0 | STAND A51
Authentise will be exhibiting the capabilities of its recently announced Digital Design Warehouse (DDW) and Guidelines products. DDW allows users to securely share and discuss additive design projects, while Guidelines is a rule-based engine which enables users to capture tribal knowledge as ‘if-this-then-that’ statements to find applications throughout the company’s workflow management tools to ensure best practice is followed.
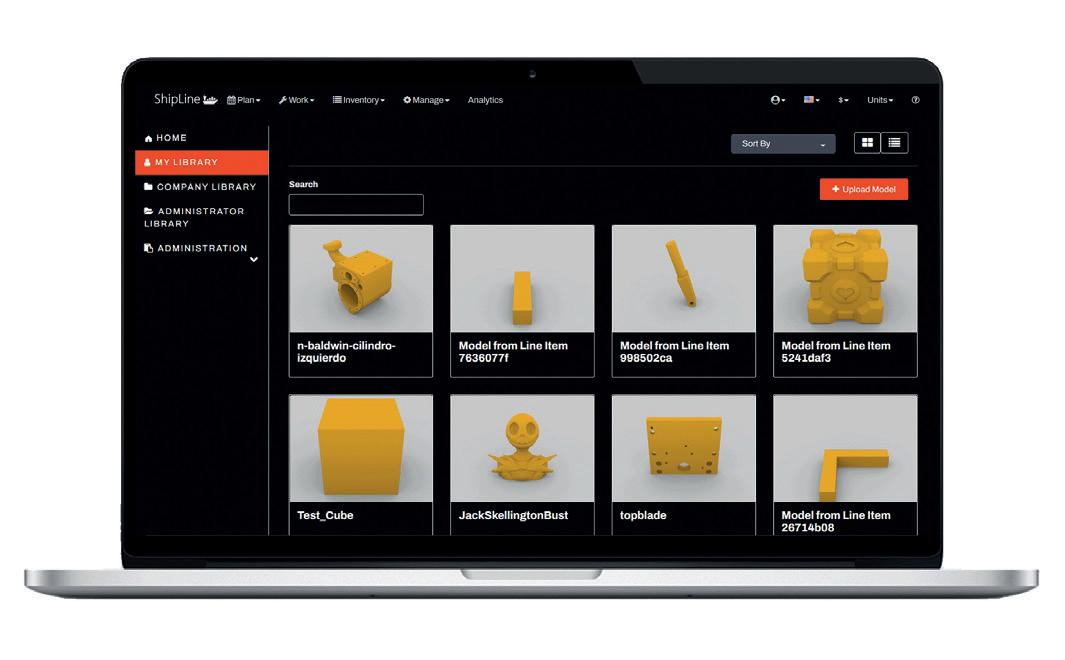
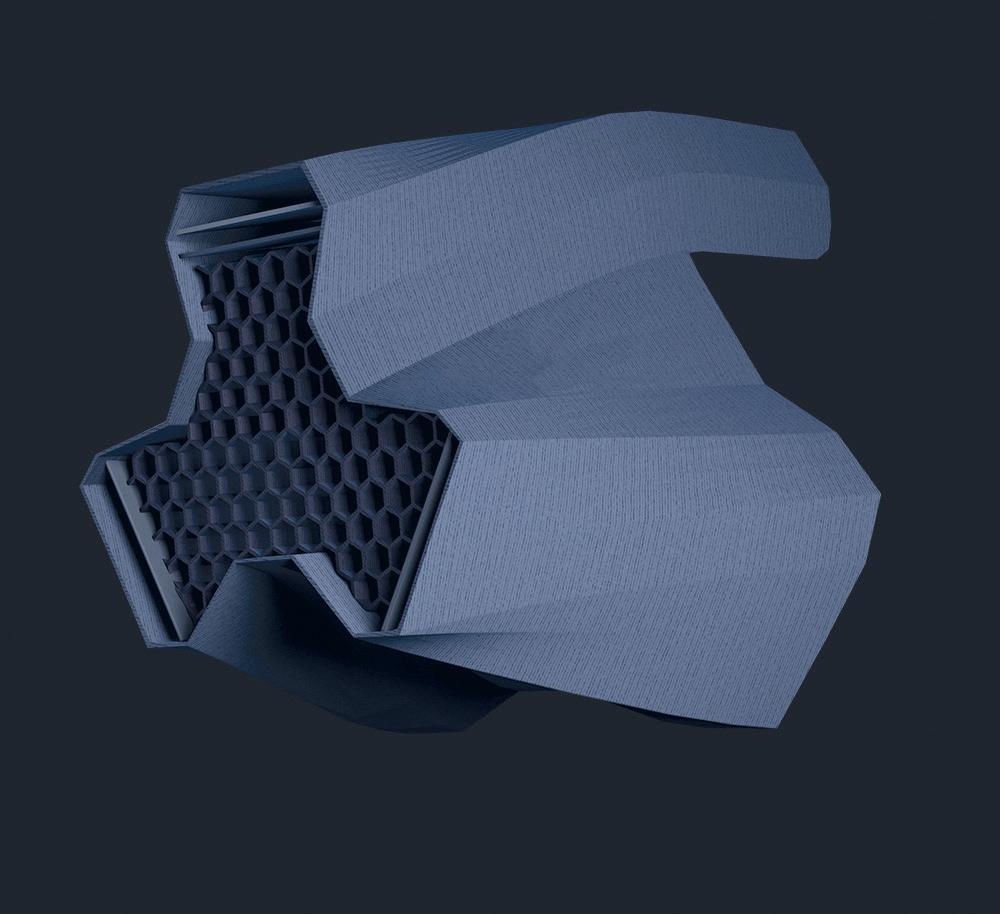
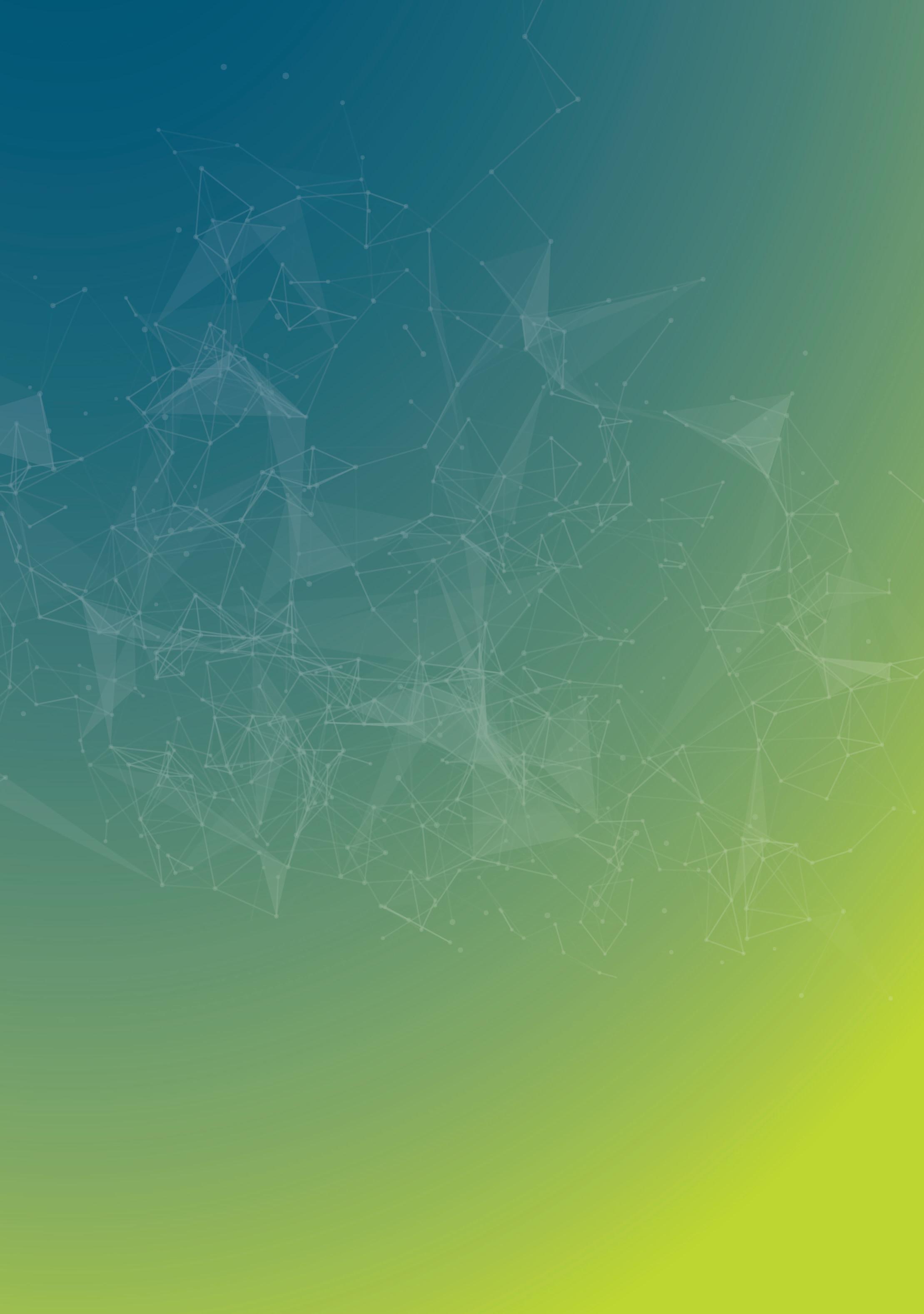
ROBOZE
HALL 11.1 | STAND C21
At Formnext, Roboze is promising to show, in a world premiere, its success in the field of materials capable of reducing CO2 emissions during the production process. In addition to this, the company will also display applications from customer collaborations in mobility, energy, aerospace and healthcare.
AMCM
HALL 11.1 | STAND C51
In Frankfurt this year, AMCM will be showcasing its capacity to deliver large build volumes, copper 3D printing and fine structures. The EOS start-up was founded five years ago to customise EOS technology to fit the needs of its customer base. Among the applications being showcased is the 800mm-tall AI-designed aerospike application developed in partnership with Hyperganic.
INCUS
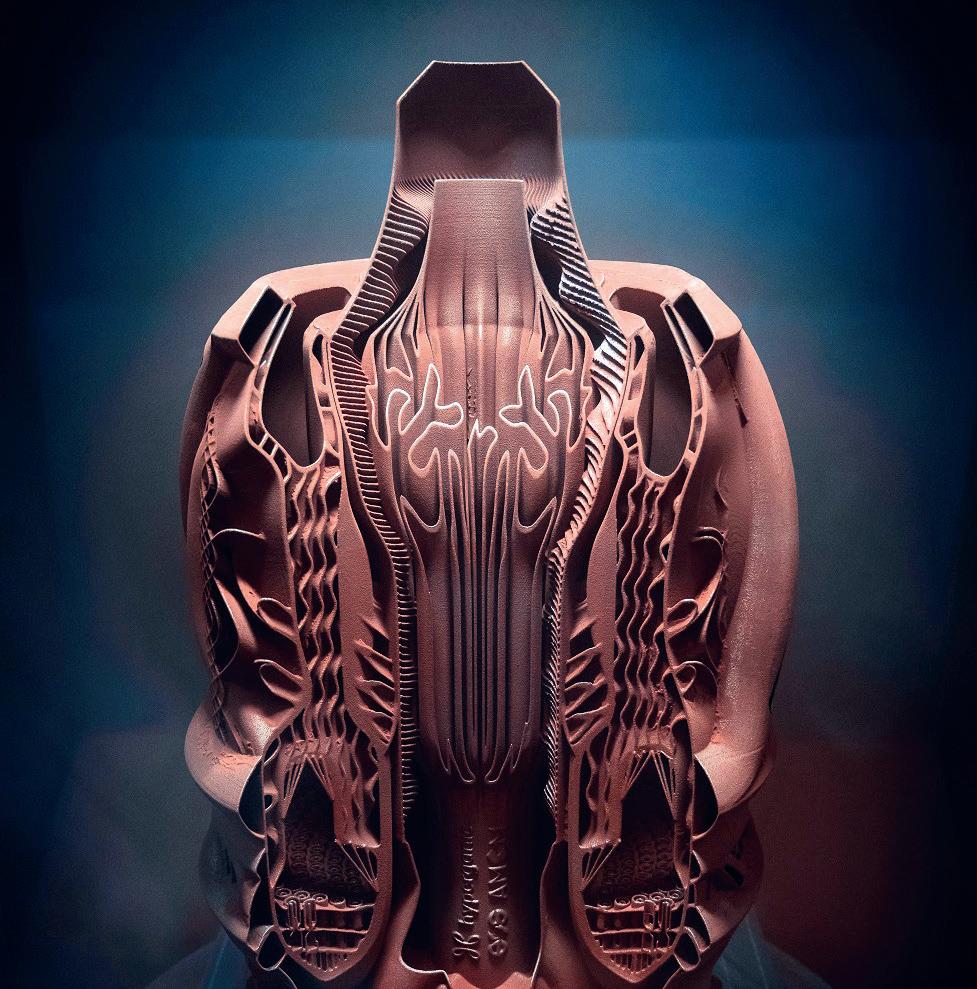
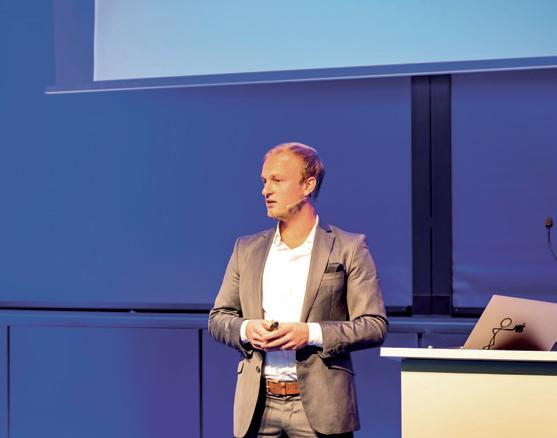
HALL 11.1 | STAND D42
Incus will exhbit its Lithography-based Metal Manufacturing process, which has been designed to reduce production costs for small and mid-scale additive manufacturing.
ROSLER AM SOLUTIONS
HALL 12.0 | STAND C81
Rosler AM Solutions will exhibit the S1 Wet surface finishing technology, alongside its S2 parts handling platform.
MASSIVIT 3D
HALL 11.1 | STAND C19
Massivit will introduce its Masivit 10000 additive manufacturing system, showcasing 'groundbreaking' automated mould production for composite material parts.
DRESSLER
Hall 12.1 | Stand C121
Dressler will exhibit its powder design and development capabilities, with a particular focus on its promise of reliability and its capacity to design powders specific to customer needs.

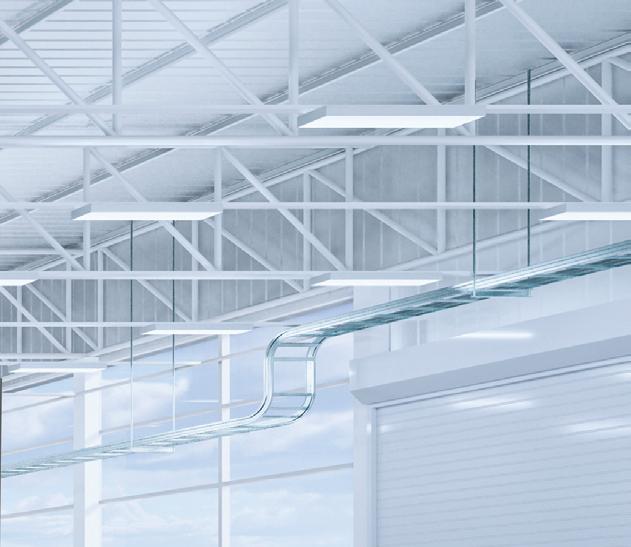
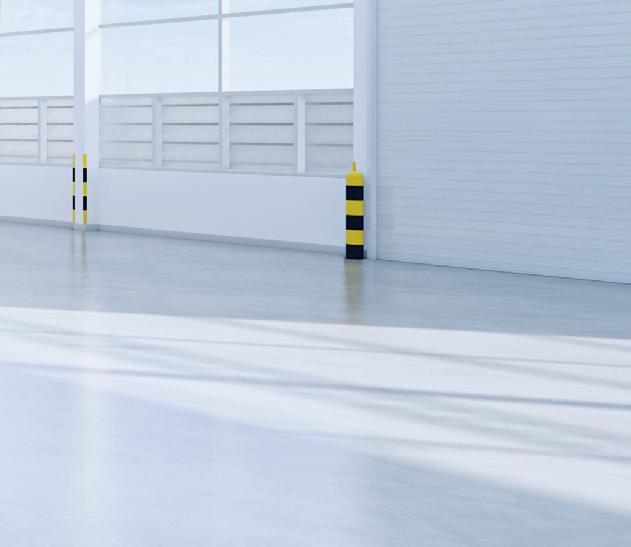
MACHINEWORKS
HALL 11.0 | STAND C02
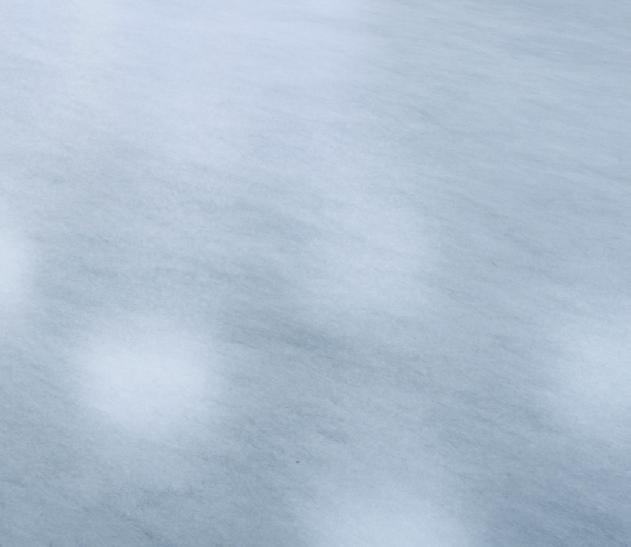
MachineWorks will demonstrate new functionality in Polygonica 3.2. Mesh deformation provides a powerful way to compute and compensate for on-machine deformation, while 3D medial axis offers potential enhancements to many algorithms including CAE midsurface creation. The fast multi-threading remeshing capability has been further enhanced to automatically preserve small features and optionally preserve exact shape.
AMT
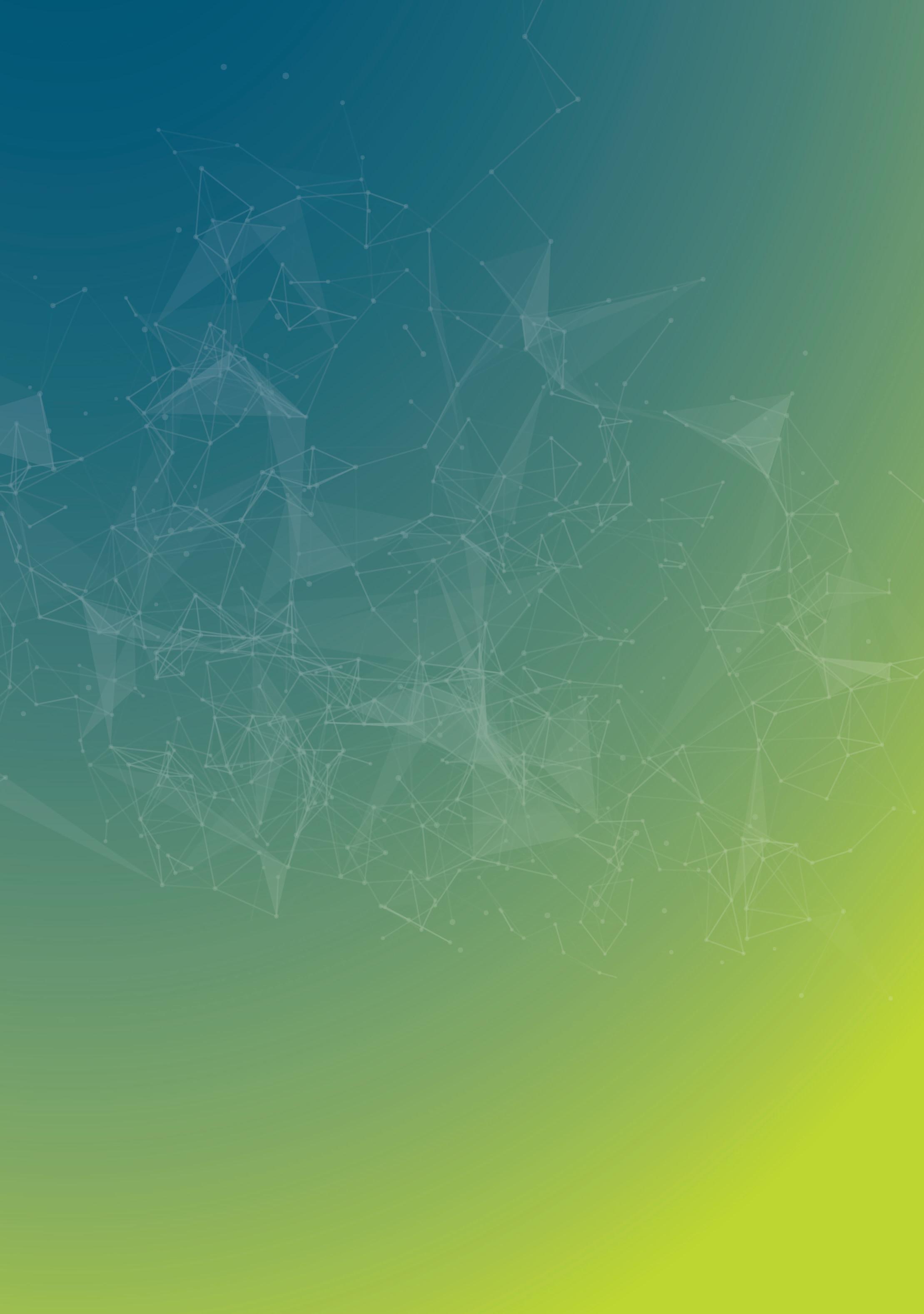
HALL 12.1 | STAND D39
On AMT’s two-story Digital Manufacturing Factory of the Future concept booth, the company will exhibit an all-new materialspecific Surface Finishing system which will be announced on the show floor. AMT’s booth will also feature the PostPro DP Max cleaning system, multiple SF chemical vapour smoothing systems, and a range of applications.
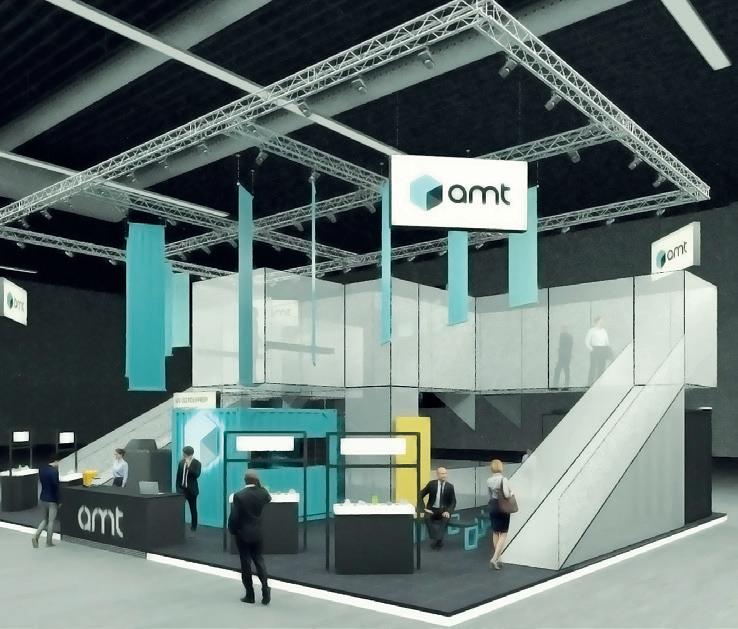
SPEAKER SPOTLIGHT
MICHAEL KENWORTHY, DIVERGENT TECHNOLOGIES
REVOLUTIONARY TRANSPORTATION: STRUCTURES THROUGH INTELLIGENT DIGITAL PRODUCTION WED NOV 16 | 10.00-10.30
Q. What can you tell us about your presentation?
A. Divergent’s presentation at Formnext will focus on our novel end-to-end Divergent Adaptative Production System (DAPS) and review DAPS-enabled designs for the automotive sector. In this presentation, the audience will hear about the value that DAPS has brought to existing OEM customers and best practices from developing productive parameters and materials.
Q. Can you explain the key capabilities of DAPS and why it is so suited to automotive?
A. We have built many additional hard and soft constraints into our design processes and moved them as far forward in the workflow as possible, to ensure that we can rapidly validate and deliver our high-performance solutions, with absolutely no design-specific tooling. Two illustrative examples are how we take into account unique constraints of our automated assembly process in the design of the topology optimised components and have developed specialised software tools to maximise print efficiency of our node-based assemblies.
Q. Who should come see this talk?
A. Anyone that wants to learn about how we have already introduced safety-critical structures – engineered and validated using DAPS – in fully homologated road vehicles, far ahead of the market. All those interested in digital manufacturing, AM automotive applications, parameter and materials development, will benefit from our presentation and hopefully robust discussions that follow.
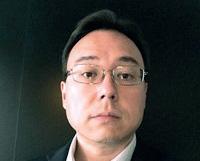
LITHOZ
HALL 11.1 | BOOTH D39
Lithoz will premiere its CeraMax Vario V900 printer with Laser-Induced Slipcasting technology. This machine will provide an opportunity to touch and feel fully dense ceramic parts with thick walls. The company will also premiere its patient-specific bone implants made from bioresorbable ceramic, and showcase its CeraFab S65 and CeraFab Lab L30 machines.
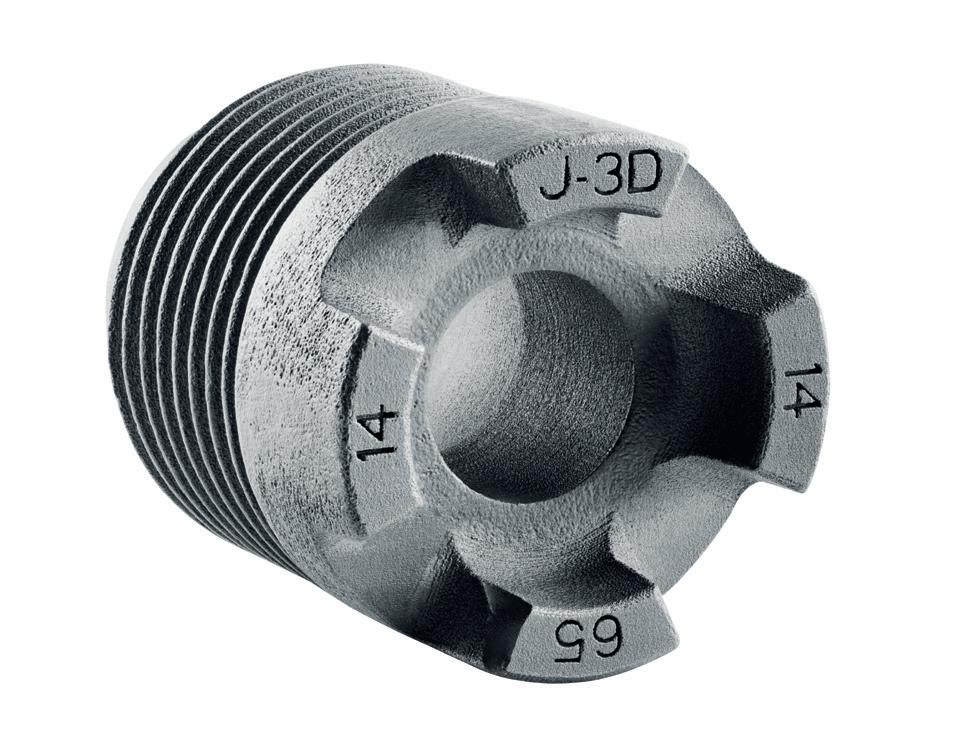
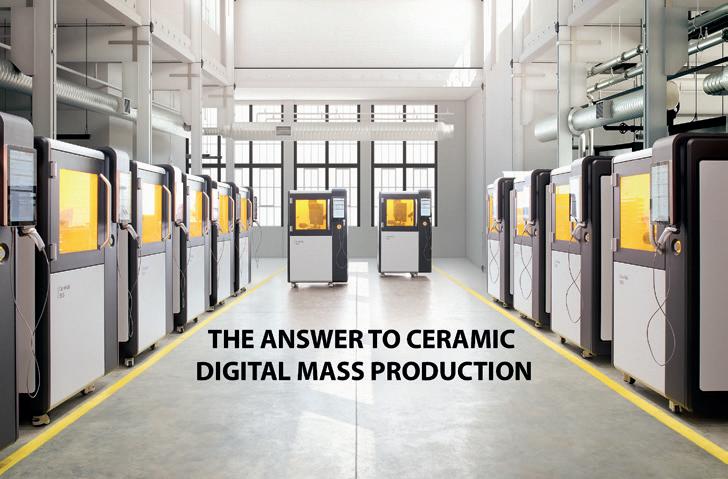
SANDVIK
HALL 11.0 | STAND D21
Sandvik, alongside BEAMIT, will demonstrate the very latest from its extensive offering, with new materials within its Osprey metal powder range hinted, and several customer use cases set to adorn the metal powder firm’s booth. Maraging steels and super-duplex stainless steels will be among the existing materials products highlighted.
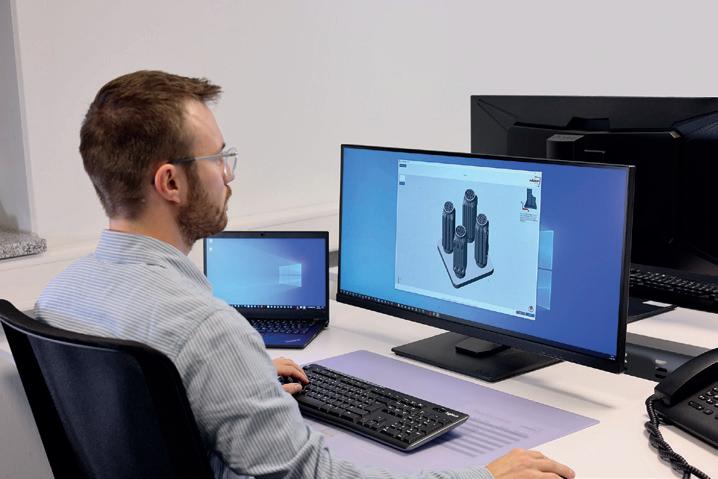
SOLUKON
BOOTH 12.0 | B21
Solukon is set to launch the SPR-Pathfinder depowdering software at Formnext, a year on from the introduction of its Digital Factory Tool. SPRPathfinder works to calculate the ideal motion sequence using the build job’s CAD file to remove excess powder from complex internal structures. These calculations are based on a flow simulation that analyses the part’s digital twin. Solukon will demo the software at Formnext, while also displaying its metal 3D printer suite.
ESSENTIUM
HALL 12.1 | STAND D11
Essentium will this year unveil its materials-first strategy that spans certification, open materials machinery, and partnerships. This strategy has been developed to help manufacturers achieve quality, reliability and repeatability in volume AM production. Essentium will be on hand to talk visitors through its materials-first approach, while also showcasing an array of use cases.
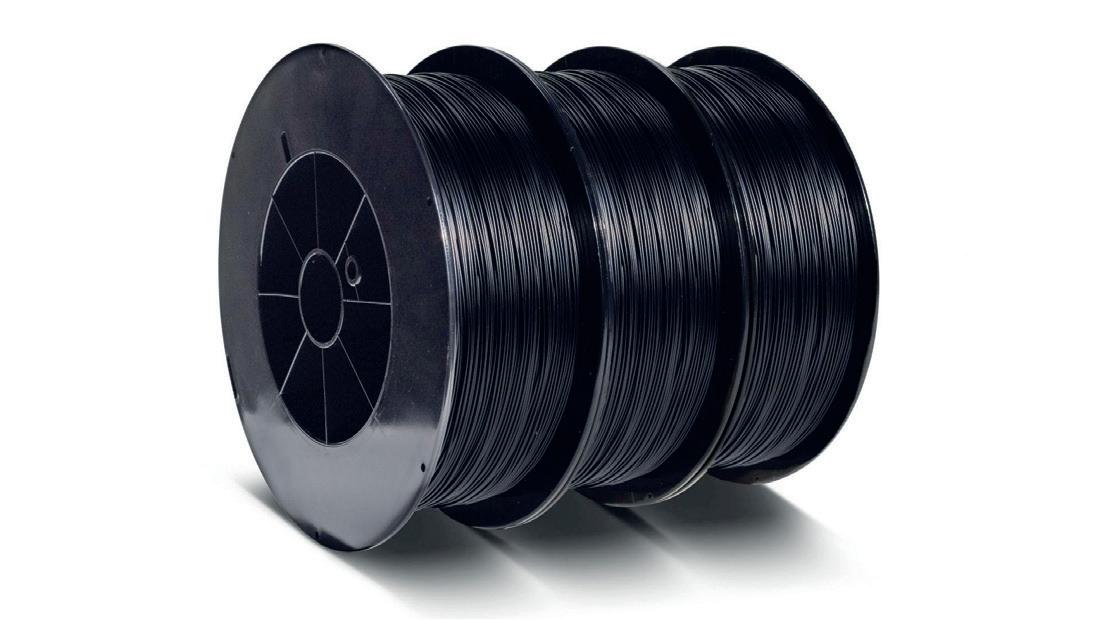
SPEAKER SPOTLIGHT
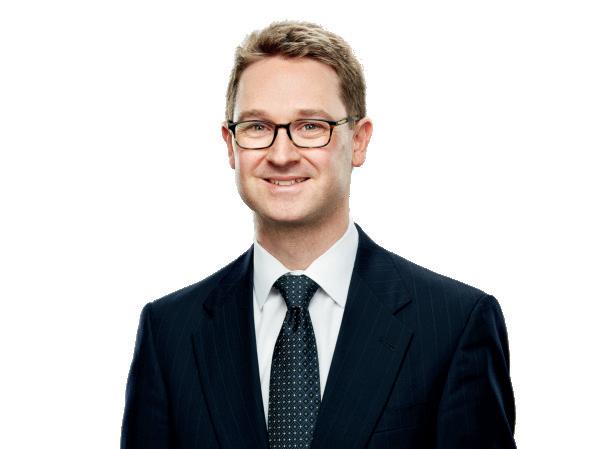
AIDAN SKOYLES – FINNEGAN
PATENTS IN AM: HOW IP CAN BUILD (OR HURT) CUSTOMER RELATIONSHIPS THURS NOV 17 | 15:00-15:30
Q. What can you tell us about your presentation?
A. I’ll be discussing the impacts of patents and standards on additive manufacturing. Every time I come to Formnext, I am amazed how companies are leapfrogging each other to improve systems, methods, and materials. However, in any rapidly changing technology, before companies start swapping ideas and data, care should be taken to protect valuable IP. Otherwise, a company might forfeit valuable investment in future potential products and end up in the courtroom. I’ll discuss effective strategies for industry-wide collaboration that balance protection of IP assets for ROI on R&D.
Q. What unique IP protection challenges does AM face?
A. About a decade ago legal scholars cried that the sky was falling when it came to protection of IP in a world of additive manufacturing. Who could or would protect anything in a world where anything could be printed on-demand? But it hasn’t happened. Instead, we’ve seen a blossoming of patent filings across industries including in the AM space. In that vein, with substantial R&D but limited IP budget, AM companies must decide what to patent, where to patent, and what to do when competitors are suspected of infringing. AM companies also have to balance interests of customers qualifying materials for their products. How much can AM companies disclose to keep customers happy while protecting their core innovations? How much should AM companies disclose to standards bodies to advance the industry? And, how can AM companies respond if their products are used to infringe third party IP?
Q. Who should come see this talk?
A. Innovators, customers, and investors in AM. From OEMs to print shops and customers, IP impacts all aspects of this industry. All players should be equipped with the basics to make smart decisions when faced with IP risks. This talk will get you thinking about how and when to use effective legal tools to move your business and the industry forward.
SIGMA ADDITIVE SOLUTIONS
HALL 12.0 | STAND C139
Sigma Additive will be showcasing its new Machine Health Module for standardising disparate machine health data logs. The solution allows users to connect machines via APIs or upload machine sensor .csv log files to create a standards-base file format for analytics, visualisation and reporting.
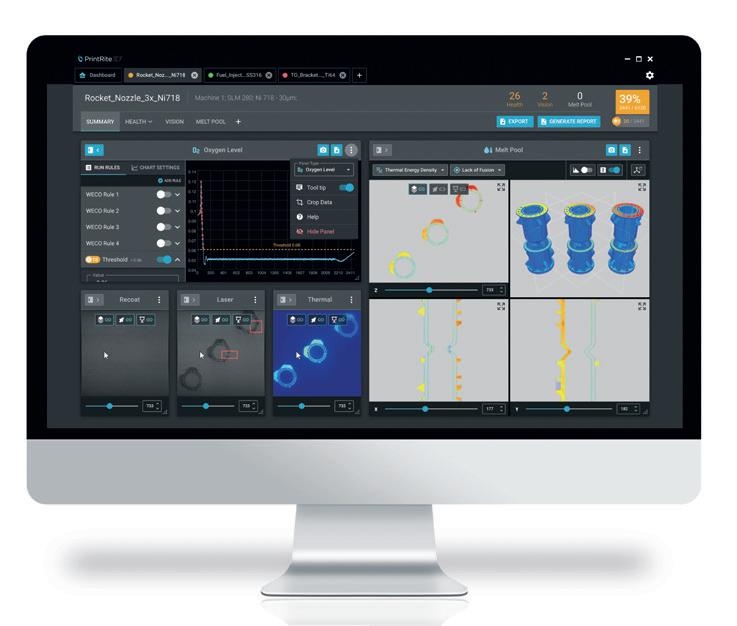
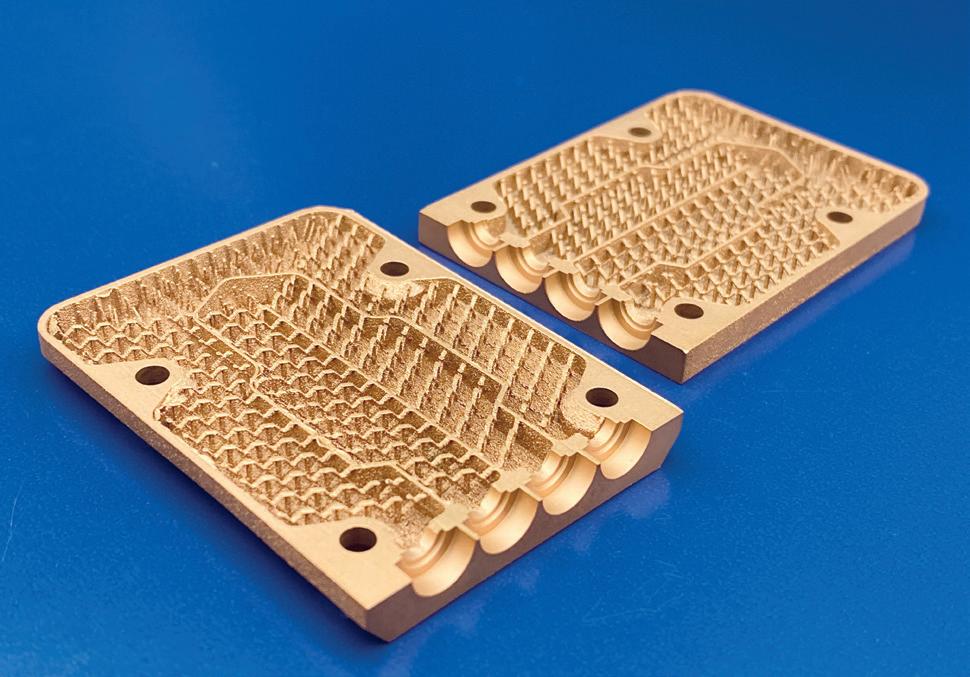
MITUSI
HALL 12.0 | STAND B65
Mitsui will introduce two types of CuCr alloy powders for laser powder bed fusion at Formnext. MA-CCR25L is applicable to thermal management and high voltage applications, while MA-CCR25H is said to equal the mechanical properties of GRCop42, while bettering its conductivity.
INTAMSYS
HALL 11.1 | STAND B29
INTAMSYS will showcase the latest addition to its AM solutions portfolio, the FUNMAT PRO 310, a new fused filament fabrication IDEX desktop printer designed for engineers. The machine is equipped with a thermostatic chamber and can process a range of engineering materials to meet a variety of application needs. Applications of other solutions in INTAMSYS’ portfolio include parts in automotive, aerospace, medical and oil & gas.
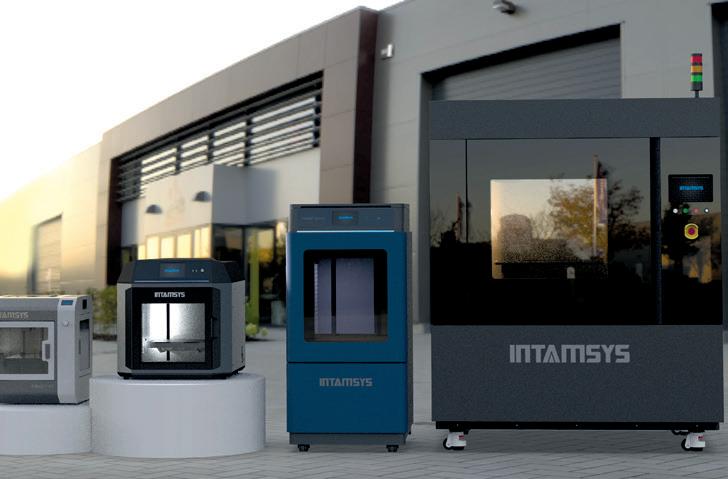
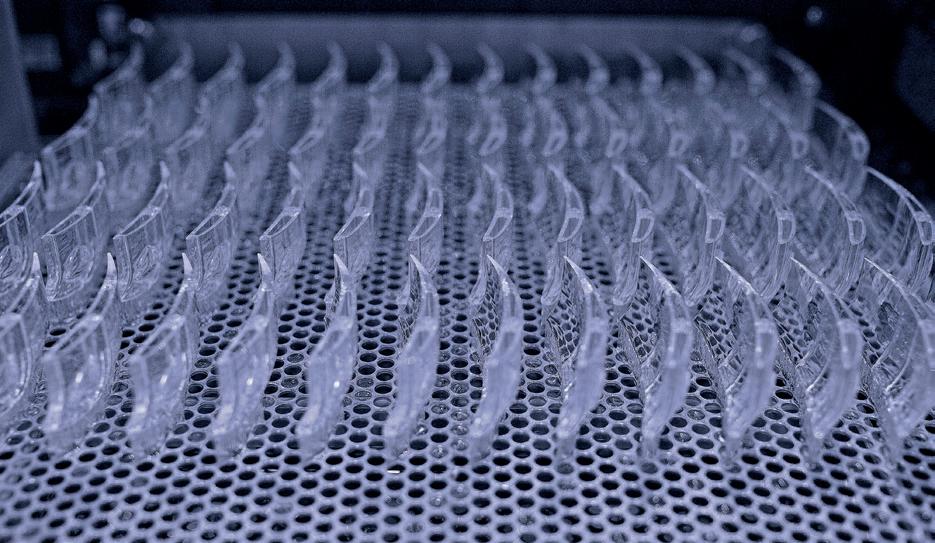
3D SYSTEMS
HALL 11.1 | STAND D11
At Formnext, 3D Systems will showcase its extensive portfolio of productiongrade materials, highlighting a host of real-world applications. The company will also exhibit its hardware solutions, including machines powered by SLS, SLA and its Direct Metal Printing technology. Kumovis’ extrusion technology and Allevi bioprinters will also be highlighted by 3D Systems.

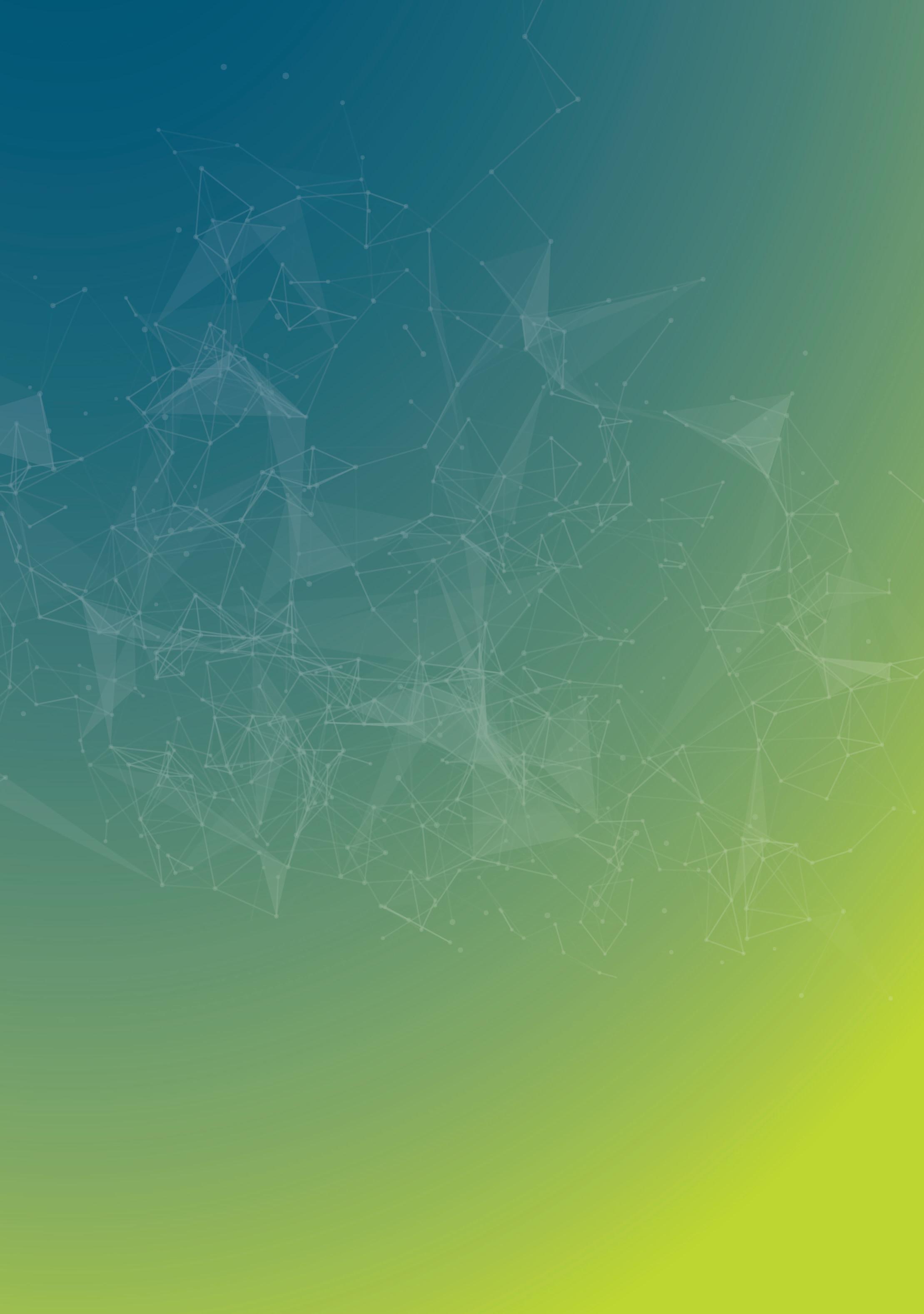
INKBIT
HALL 12.1 | STAND F39
After debuting its Vista additive manufacturing system at IMTS, Inkbit will give its flagship product its European debut at Formnext. Using Vision-Controlled Jetting technology and a low-labour support removal process based on wax
TRUMPF
HALL 12.0 | STAND D81
TRUMPF is set to premiere the next generation of its TruPrint 1000 metal 3D printing system, suggesting the platform will boast even higher productivity and premium quality. The company will also highlight its TruPrint 5000 system, which has some further updates as well, and has also hinted at news regarding the printing of large parts in pure copper. support material, Inkbit is confident its machine will be at home in high production environments. Visitors can also see a range of materials Inkbit has tailored to the machine, from tough and chemically resistant epoxies to soft elastomers.
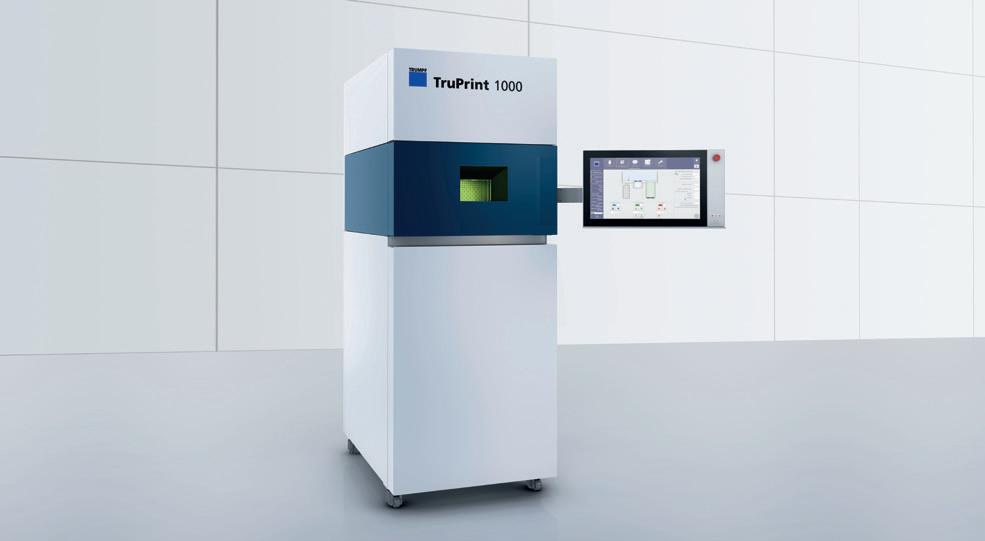
We bring solutions to problems!
Your trusted gas solutions providers
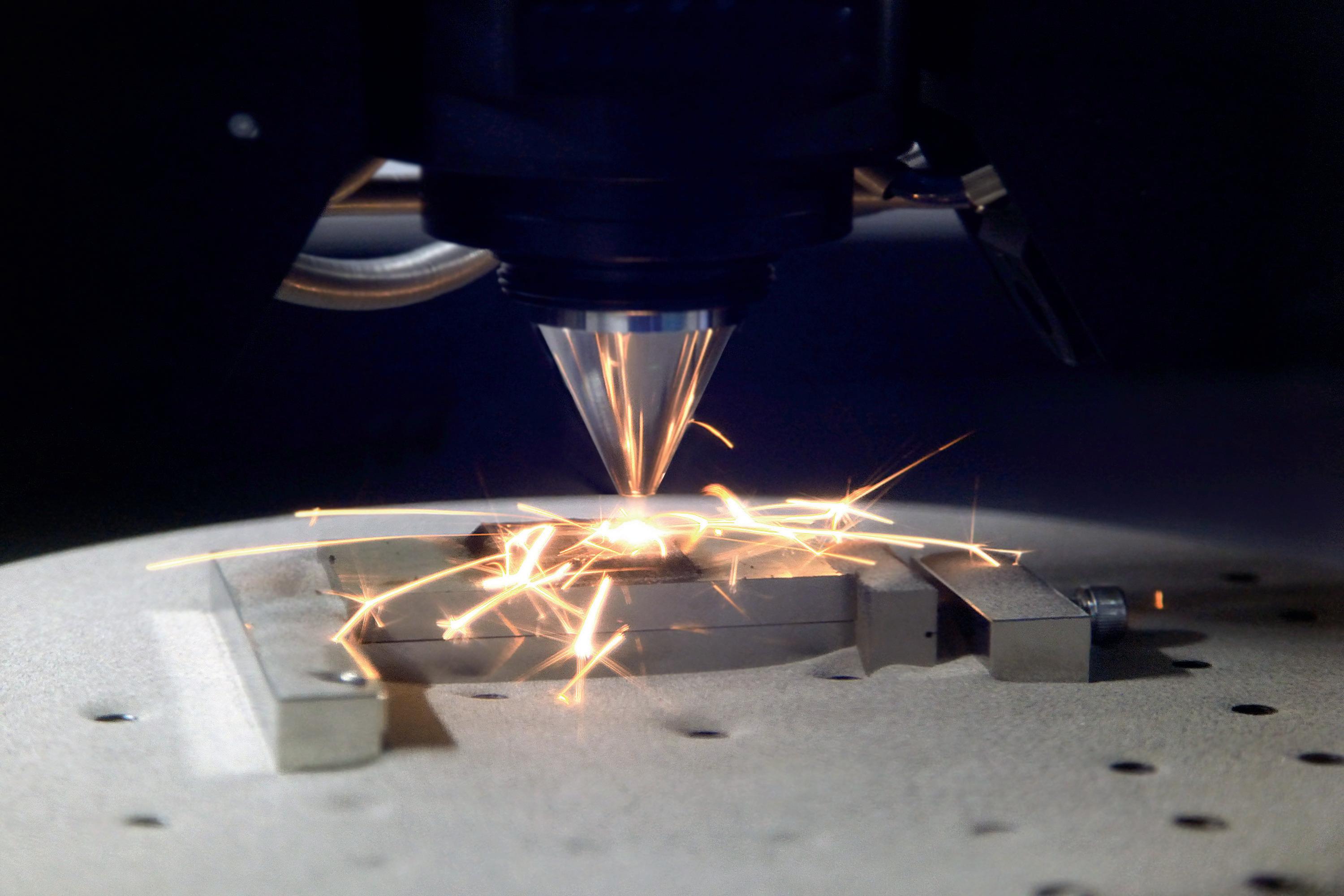
Hall 11 Booth B79
We are solution providers that optimize process quality, stability, and reproducibility - all whilst contributing to a more sustainable future. We bring solutions to problems!
Nippon Sanso Holdings Corporation has dedicated many years of research and development on additive manufacturing processes, and acquired outstanding expertise worldwide in 3D printing and its optimization. We develop quality-assured solutions for metallic additive manufacturing processes; resulting in our 3DPro® line.
Gases play a key role in the AM process chain. From the production of base materials, the inerting of process chambers, to thermal post-treatment - the use of the right process gas with the right purity can positively influence process quality, reproducibility and mechanical component
properties. All whilst making a deposit on sustainability. 3DPro® brings solutions to problems!
To learn more, our global research specialist in gas technologies for AM processes is giving an exclusive presentation at the next Formnext Tech Conference. Incorporating decades of experience, find out how our gas solutions - 3DPro® products - can improve the built part quality, part consistency and process reliability for sustainable Metal Additive Manufacturing.
Nippon Gases and Taiyo Nippon Sanso, part of Nippon Sanso Holdings Corporation, are your strategic partners for industrial and medical gases.
Contact info.3dpro@tn-sanso.co.jp Corporate website tn-sanso.co.jp/en/ AM solutions 3dpro.jp/
XJET
HALL 12.0 | STAND C01
XJet is to place its focus at Formnext on its Carmel 1400 solutions for metal and ceramic parts. The Carmel 1400M system will be running live on its stand, while the SMART Station for automated soluble support removal will also be exhibited. Materials developments will also be under the spotlight, with XJet presenting parts printed in 316L stainless steel, as well as zirconia and alumina.
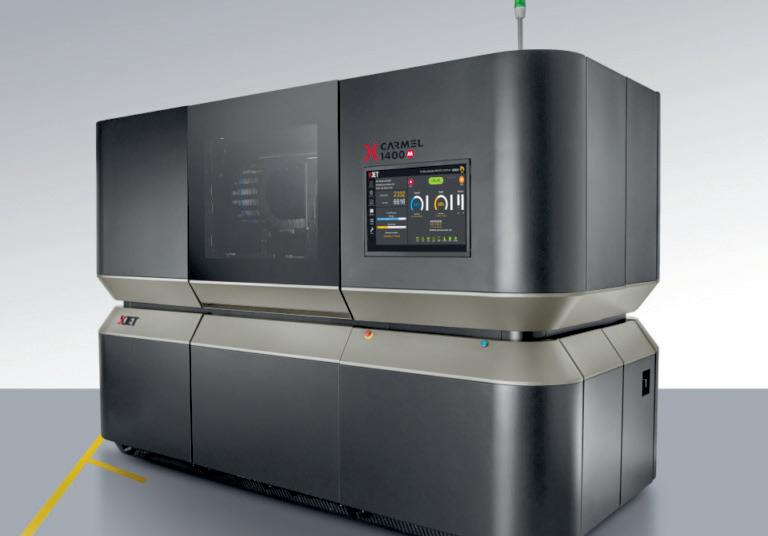

TCT INTRODUCING STAGE: AMC
MEETING AM INDUSTRY SOFTWARE DEVELOPER NEEDS THUR NOV 17 | 11.00-11.20 AM
Becoming a selected third-party developer of Dyndrite’s Application Developer Kit, AMC Bridge offers customised 3D design and additive manufacturing development services to create new, optimal production methods from part design to full production. AMC president Igor Tsinman will speak alongside Dyndrite founder and CEO Harshil Goel.
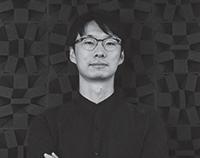
SPEAKER SPOTLIGHT
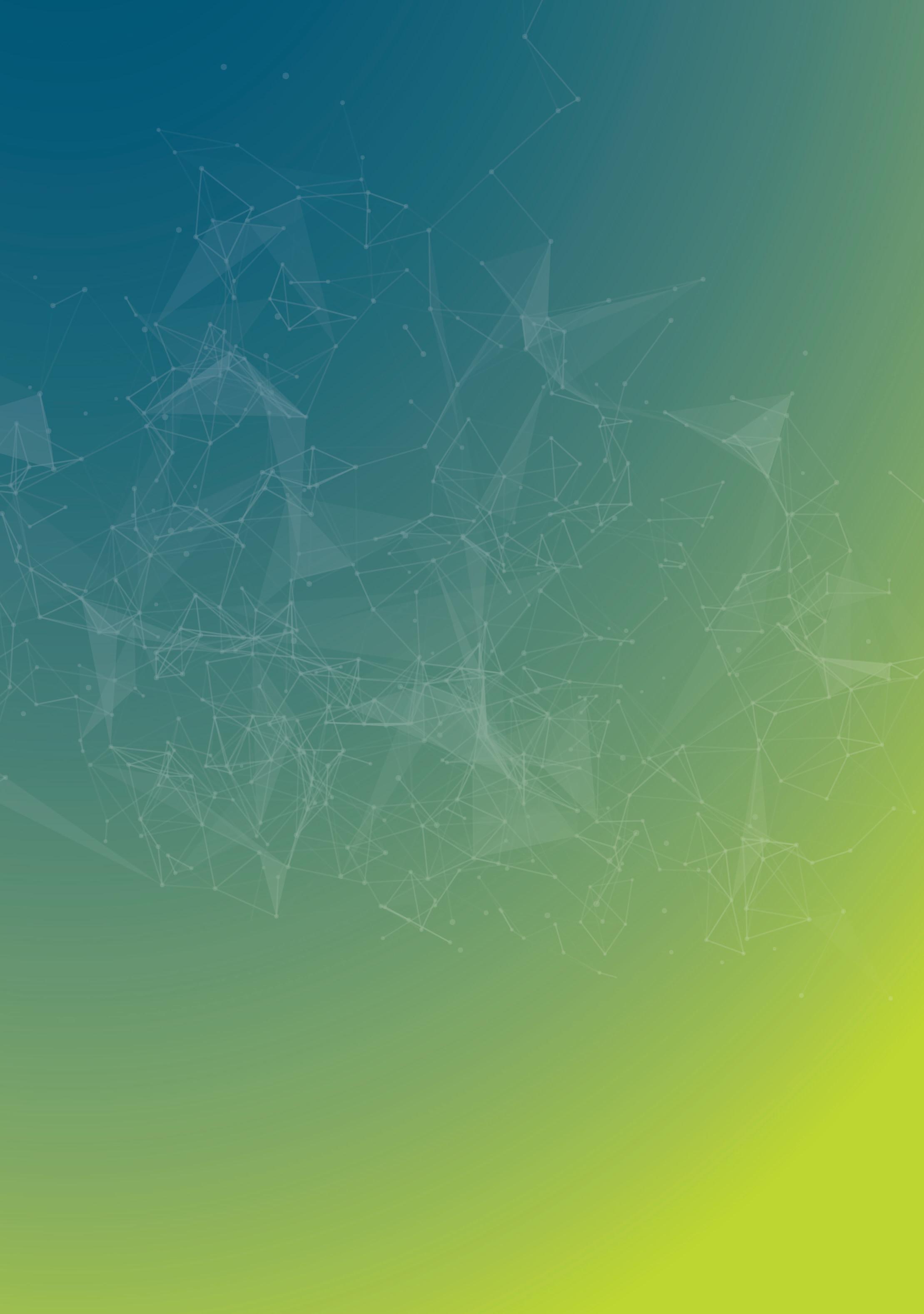
RYOHEI YUASA – KEIO UNIVERSITY, DIGITAL MANUFACTURING AND DESIGN CENTER FOR EMERGENT CIRCULARITY
AM FOR SUSTAINABILITY IN JAPAN FRI NOV 18 | 11:45-12:15
Q. What can you tell us about your presentation at Formnext?
A. The presentation will include an introduction to the overall activities of the Digital Manufacturing and Design Research Center for Emergent Circularity, newly established by Keio University Global Research Institute, and a representative example of the Up-Ring series, which launched 3D printed furniture in 2022 by Okamura inc., a major Japanese furniture manufacturer. There are many examples of 3D printed furniture around the world, but I believe this is one of the leading cases where a major furniture manufacturer has conducted evaluation tests. Standard furniture durability tests were tested, and the 3D printed UP-RING series passed them all. I hope this example will contribute to the further spread of sustainable products using AM.
Q. Who should come see this talk?
A. I am very interested in the EU's resource recycling efforts and would like to meet with people who are also interested in resource recycling through AM. I would also be happy to discuss with material manufacturers and manufacturers of daily necessities how their products could be made on the premise of recycling.
Q. What is the biggest opportunity for AM in terms of sustainability moving forward?
A. Material. I am an expert in 3D printing materials for the MEX method. My main task is to find materials that exist in the world but have not yet been applied to AM and adjust them for AM, thereby increasing the diversity of materials that AM can use. Recently, when companies develop new materials, they are often the first to try them out for use in 3D printing. This is because, unlike other manufacturing methods, it is possible to produce an optimally demonstrable example of the material in a much shorter period of time. These examples are leading to the adoption of the material in other manufacturing processes, such as injection moulding. AM has a very important role to play because it provides an opportunity to promote the use of environmentally friendly materials in society through this kind of movement.
SPEAKER SPOTLIGHT
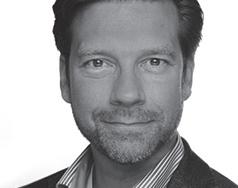
DR WILDERICH HEISING & THOMAS KRUEGER – BOSTON CONSULTING GROUP
ANYWHERE AT ANY TIME AND GREEN: ADDITIVE MANUFACTURING UNLOCKS MORE FLEXIBLE AND GREENER SUPPLY CHAINS THURS NOV 17 | 13:15-13:45
Q. What can you tell us about your panel at Formnext?
A. We will talk about how 3D printing unlocks distributed manufacturing and helps companies to be more resilient, greener, and even save cost.
Q. You describe distributed manufacturing as an interesting sweet spot for AM. Can you elaborate?
A. When we talk about distributed manufacturing that not only means geographic distribution but also distribution over time and in terms of who prints the parts. AM is a true unlock for distributed manufacturing as it allows flexible, low volume production with only very short lead time.
Q. Who should come see this talk?
A. Every user or potential user that wants to transform their production network. But also, all AM players along the entire value chain that want to sharpen their offering.
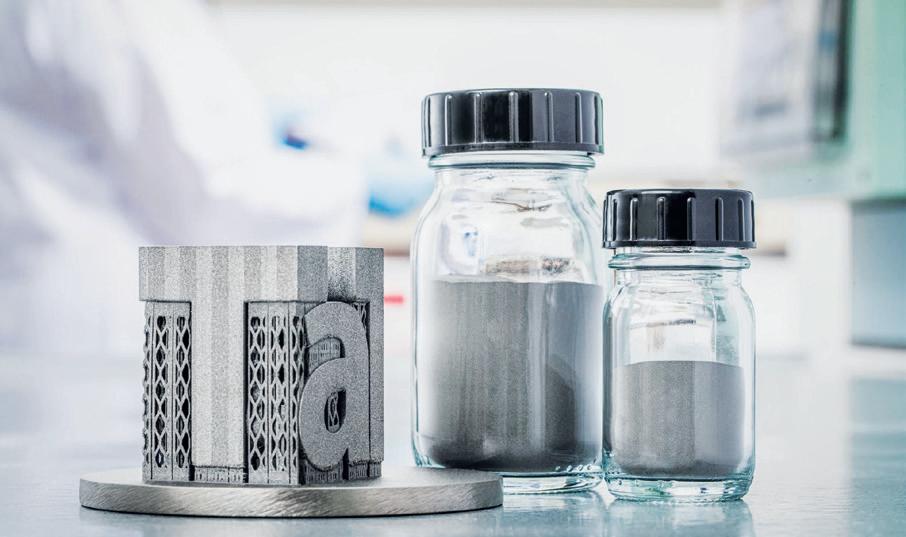
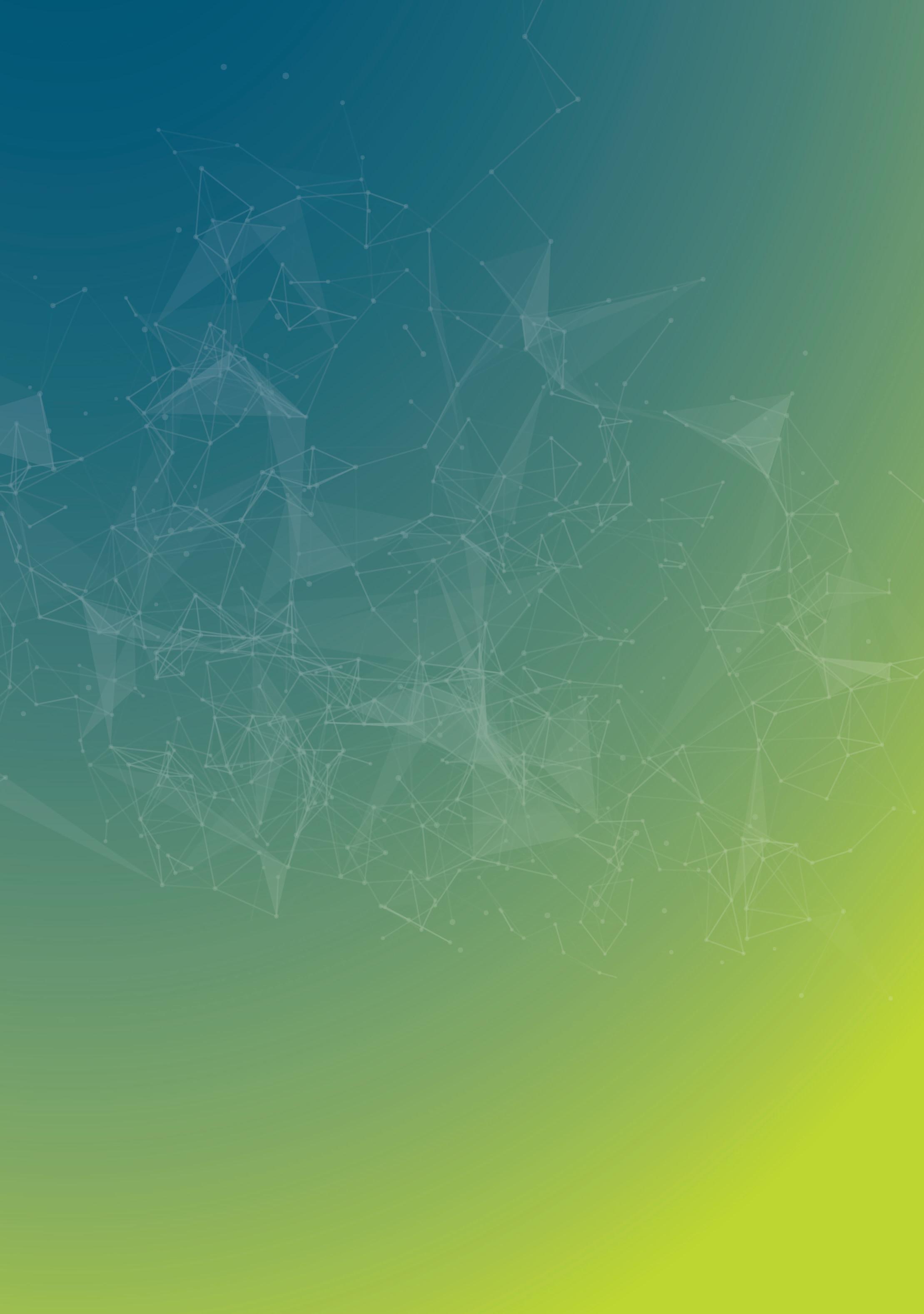
TANIOBIS GmbH
HALL 12.0 | STAND B47
TANIOBIS GmbH, a specialist in materials featuring niobium and tantalum, will present its AMtrinsic metal powder range for AM applications. The AMtrinsic powder portfolio includes elemental Ta/Nb powders as well as pre-alloyed powders ranging from binary over complex multinary to High-Entropy Alloys (HEA). The company says it also offers customer specific compositions. TANIOBIS is inviting visitors to its booth to learn more about the characteristics of its new C103 and FS-85 AM powders.
START-UP CHALLENGE WINNER: ROBERT BUSH, CEO AT RIVELIN ROBOTICS
TCT INTRODUCING STAGE – TUES NOV 15 | 15:20 (HALL 12 | STAND B41)
Q. Tell us about Rivelin Robotics’ technology – what is it and how did it come about?
A. I founded Rivelin Robotics while working as metals production engineer at 3T-AM (BEAMIT) after battling with the challenge of getting the first metal AM part through PPAP (Production Part Approval Process). The robotic finishing systems we have developed at Rivelin are empowering engineers to automate support removal and polishing to meet the standards of mission-critical production lines. Support removal in particular has been a key bottleneck for many metal AM applications.
Q. We know post-processing is a major challenge. How does Rivelin uniquely address that?
A. Rivelin’s solution for metal post-processing uses a robot to consistently perform at the top level of the world’s best metal finishers. We’ve taken inspiration from the reliability of casting automation and made it simpler and faster to deploy so the automation is almost as flexible as a hand finisher.
Q. Where do you see this having the biggest impact?
A. One of our early adopters, GKN Aerospace, said “Automated support removal would mean removing not only one of the most labour intensive processes in the AM chain, but also improve productivity with reliable turnaround times every time for every part.” I think this is an excellent summary of where Rivelin NetShape can have the biggest impact.
Embedding quality, reliability and repeatability into the postprocessing of metal parts across numerous industrial sectors is where this technology will have the biggest impact.
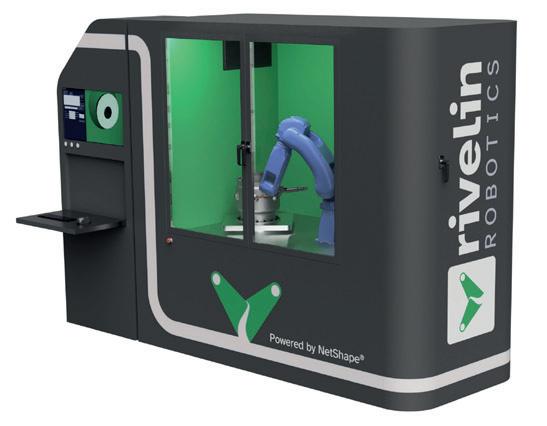