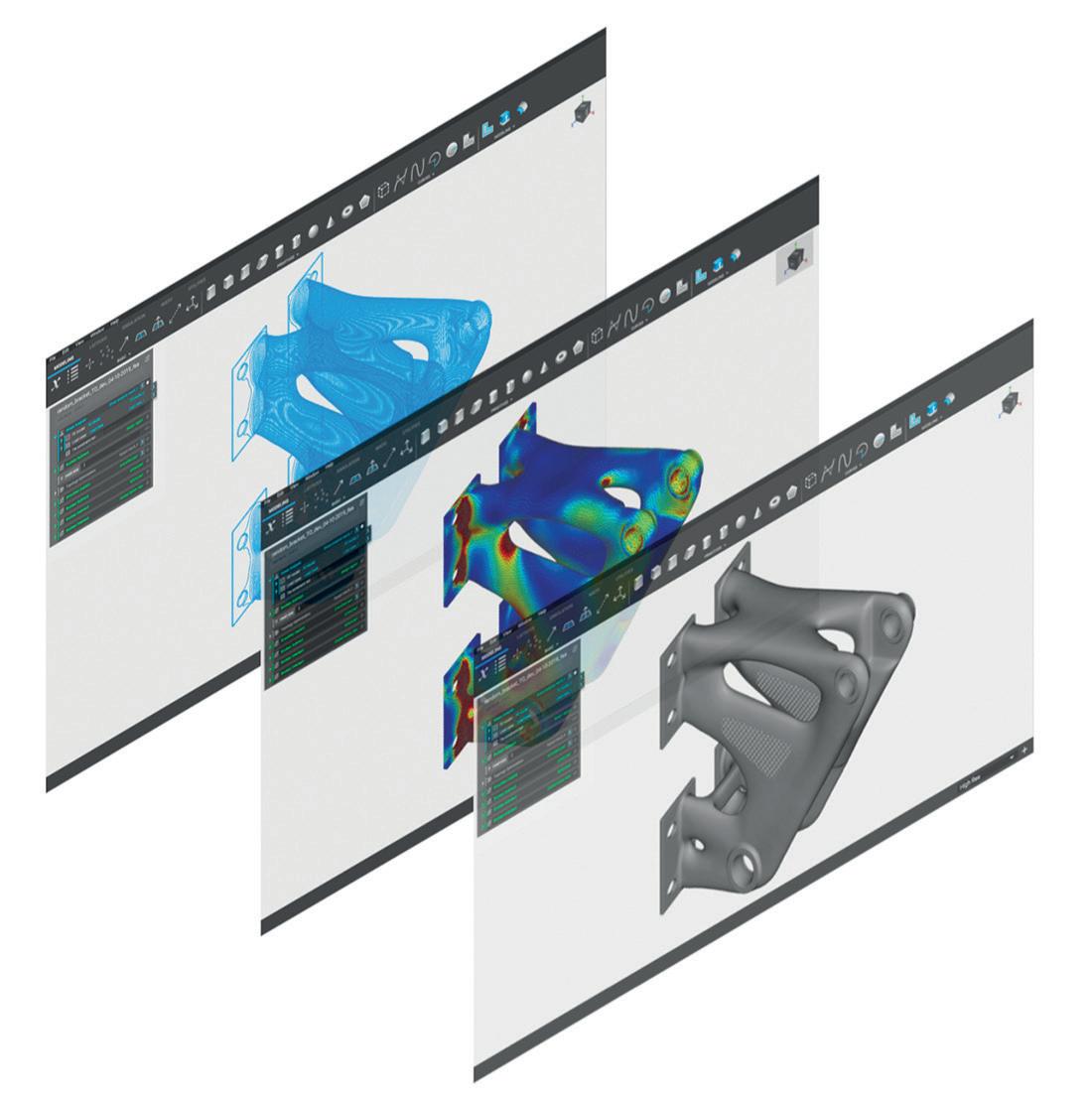
7 minute read
A PLATFORM FOR
from TCT EU 28.1
by TCT Magazine
WORDS: LAURA GRIFFITHS
Additive manufacturing (AM) technology is outpacing our current software toolset. At least that is the take from one New York-based software developer nTopology, with 30.7 million USD in funding to do something about it.
“People have been working in AM for many years and they’ve had these dreams of things that they’ve wanted to create. It’s not easy to do that with the tools that they have today,” Blake Perez, Application Engineer at nTopology tells TCT during a meeting at last year’s TCT Show. It’s a good introduction as to why the company’s computational modelling platform exists today, described by Perez as “a modelling tool and engineering knowledge-capture tool for high-performance geometry.” The comments were made back in September when the company made its debut at the Birmingham event and scooped up a TCT Award for its nTop Platform.
Co-founded by Grey Schroy and CEO Bradley Rothenberg, nTopology first arrived on the AM scene in 2015 with its Element lattice design software. With a powerful modelling kernel on their hands, the team started looking at ways in which the software could be expanded to open up more applications. After working with a number of pilot customers, nTop Platform was born.
Formally launched last May, nTop Platform offers a number of toolkits for lightweighting, topology optimisation, additive manufacturing, design analysis and architected materials for users in the aerospace and defense, automotive, medical and industrial design sectors; the company already counts the likes of Lockheed Martin amongst early users. Two months on from that TCT Award win, nTopology announced the next iteration, nTop Platform 2.0, with updated toolkits and the opportunity for users to create their own workflows.
MAKE THE WORK FLOW
nTop Platform has been designed to handle complex geometries in a repeatable way. Users can design engineering workflows which can be deployed to a whole product family or organisation to speed up the design-tomanufacturing process. Geometries can be modelled directly in the software or design data can be imported from most major CAD tools, optimised, latticed, sliced and supported within a single platform, holding the user's hand through pre-installed data sets or allowing users to build
SHOWN: TOPOLOGY OPTIMISATION OF AN AEROSPACE BRACKET
on top of those and input their own IP. “That’s why we call it a Platform,” says Perez.
“Typically, the workflow is, you have this very talented engineer who takes analysis results data, looks at it, has some intuition about how that gets applied to the geometry and it’s back and forth, that person has to be in the middle,” Perez says of the current workflow. “Now you can set up these loops where that happens automatically.” The typical design-to-manufacturing workflow is a long one with many components to contend with. Designers and engineers are required to switch between multiple pieces of software in order to get a design to the point of manufacture and for every design iteration, those many steps have to be carried out all over again. That’s where repeatable workflows come in.
“The more you enable your team to iterate, make design changes, learn from failures, the better your outcome is, we all know that,” Perez says. “We kind of tied all these processes together, bringing in the simulation data, bringing in your existing geometry, the optimisation, and putting that all together in a single tool. So now you can say, okay I’ve learned from my part, I need to make this design change and go back and make it. Your part rebuilds and then you can just print right way, you don’t have to worry about costing your company man hours in making that design change.”
There are a growing number of programmes on the market offering tools like topology optimisation and we’re seeing more examples of generative design everywhere from aerospace brackets to car steering wheels. nTopology’s take is, topology optimisation is just another tool in the box and nTop allows users to quickly create geometry directly from that without having to manually remap engineering data. That said, it’s still very much a collaborative process between engineer and software.
“If you Google generative design, you’ll get hundreds of answers," says Perez. “What we do is we provide a toolkit for generative design. We give you all of the basic tools that you need to string together whatever workflow you would like to have. It’s not a black box, everything is very open, you know exactly what’s happening with the software. You as a user can put this together and you can generate your multiple outcomes, you can choose based on the constraints that you have, the machine that you have.”
A FRESH APPROACH
Those advances in software products positioned towards additive manufacturing mean some older ways of doing things are gradually being phased out. STL for example, a file format that has been subject to a committee of industry leaders wanting to see it gone in favour of a modern format, may want to watch its back.
“One of our main efforts right now is to really get rid of the STL file entirely,” Perez says. “If you think about it, STL adds no value to your digital tool chain. It’s a translation mechanism. So, we’re slicing parts directly, we’re providing

slice outputs from our software directly to machines, we’re working with machine vendors and I see that attitude changing as well, where people are being a little more open about the types of files that they accept from their customers, from their users. So, slice export has been incredibly successful in getting these geometries out of the screen and into the machines and that has relied heavily on our relationship with the machine OEMs.”
nTopology has been actively working with OEMs like Renishaw and EOS to further explore the potential of this technology and how it meets the needs of various processes (“We know that there are hundreds of AM technologies out there, we’re not going to build for just one, we’re going to build for all of them,” says Perez). Most recently, the company joined EOS’ Digital Foam programme as a partner to support the 3D printing of applications like protective headwear and performance footwear. There’s also an ongoing discussion around the relationship between AM hardware and software, the idea that one is always going to outpace the other. Perez doesn’t think that’s such a bad thing.
“I don’t think we ever want them to be on the same playing field, because innovation in each area is going to drive innovation in the others,” Perez explains. “Right now, we’re essentially seeing our hardware advance leaps and bounds beyond our digital capabilities, our software capabilities. Software is catching up and then somewhere in the middle is the material space where I think we also have incredibly advanced materials. Now we have to figure out how do we process them? How do we represent them in the software? […] There’s so much good hardware out there. We’re just waiting for the tools.” The last year has been one of huge growth for the company. It recently opened an office in Regensburg, Germany to cater for its growing European customer base and raised an additional 20 million USD in funding. nTopology says it is now focusing its efforts on user experience, ensuring nTop fits into existing workflows and building out the platform to allow people to customise it to their needs, giving them the
ability to create optimised workflows, package them and then share across an organisation or the wider user community. It is also turning its attention to other forms of advanced
manufacturing like composite layup and hybrid technologies where it believes, like additive, there is a sizeable gap in the design tools readily available. “One of our next big expansion efforts is, what does that
community platform really look like?” says Perez. “Are there communities based around
it? How can I download new functionality that maybe nTopology didn’t create but someone else did? That’s where you really gain a lot of collective knowledge and you’ll see just leaps and bounds of where the software goes.”
April 20-23, 2020 Anaheim (CA) Convention Center
NORTH AMERICA’S MOST IMPORTANT ADDITIVE MANUFACTURING EVENT
RAPID + TCT is the must-attend event for anyone involved in or exploring additive manufacturing. See the latest innovations, network with like-minded peers and industry experts, and gain insight into the countless possibilities of additive manufacturing, all at one place.
