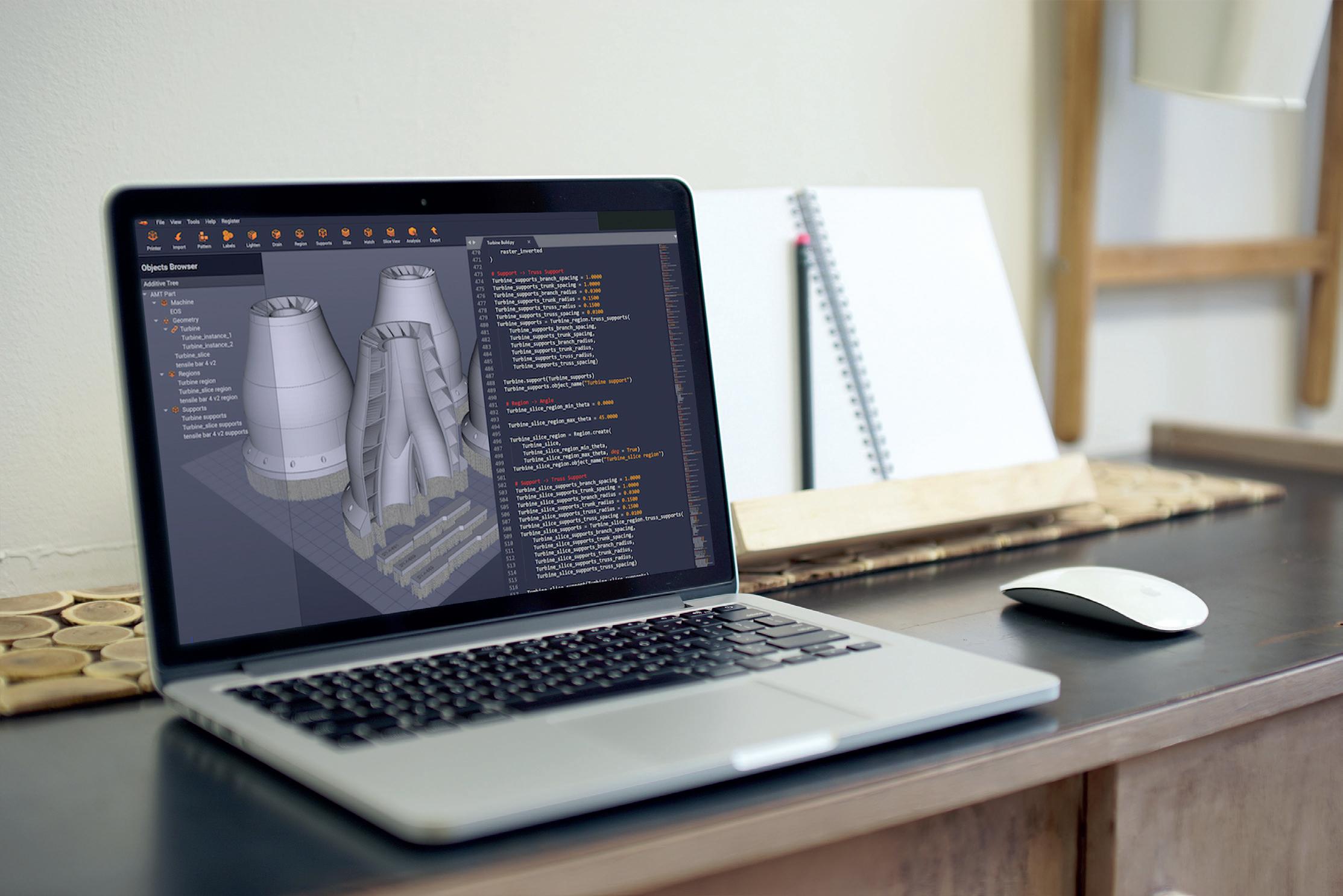
7 minute read
WE CARE ABOUT
from TCT EU 28.1
by TCT Magazine
DYNDRITE: “WE CARE ABOUT EFFICIENCY, QUITE A BIT.” team of mathematicians, scientists and software experts saw were holding the additive manufacturing industry back.
“We're at a unique point in time where the hardware has actually outpaced the software,” Goel tells TCT. “It's not even just on the design side. It's just how do you go from CAD to print?”
Dyndrite is not a design tool. It’s not a simulation tool either. So, what exactly does it do? Behind the bold statements about ushering in a new era of manufacturing, its interests lie in geometry and the crux is to help people gain control of their CAD to 3D print process. At the core is the Dyndrite Accelerated Geometry Kernel (AGK) and Dyndrite ACE (Accelerated Computational Engine), the world's first fully GPUnative geometry engine. Put simply, the kernel is the central maths behind a programme’s operating system and you can do a tonne of stuff with it. Powered by NVIDIA Quadro, ACE has been built from the ground up for modern computer architecture, modern manufacturing and modern design needs, according to Goel. 30 Under 30 inductee makes it look so simple that I walk away believing even I, three engineering degrees less qualified, could take the mouse and churn out some successful parts.
“That's the point,” Goel tells me. “Honestly, if someone has difficulty learning how to use this, we did not do our jobs right. This is supposed to be like English and this is supposed to be really, really accessible. You should be able to go from CAD to print within five minutes of installing the software.”
Dyndrite (pronounced “den-drite”), is a Seattle-based outfit which emerged after more than three years in stealth to a captivated crowd at the Additive Manufacturing Users Group last year. Backed by Google’s Gradient Ventures and former Autodesk CEO Carl Bass, the company aims to provide an alternative to the software tools which Goel and his T he above is the key theme that Harshil Goel, founder and CEO of additive manufacturing software developer Dyndrite, says he wants me to take away from our conversation at last year’s Formnext.
It’s a concise introduction from a company built on the enormously complex language of kernels, GPUs and CPUs, but a few simple clicks into a demo, I quickly discover that making complex tools efficient and approachable is what Dyndrite is all about.
'Quick' is a prime word here. Within the first five minutes of our meeting, Goel has successfully imported a model into the Dyndrite platform, generated supports, made some changes, run the next iteration, copied and pasted the new design, added some crucial labels, performed slicing - basically the many steps that designers and engineers have to go through day in, day out to take their design from file to finished part. The recent Forbes WORDS: LAURA GRIFFITHS
4SOFTWARE & SIMULATION FEATURE sponsored by
“We specifically decided to build an additive manufacturing application because we saw a bunch of people in quite a bit of pain running around with their heads on fire and said you know, I think we can build you something to help.”
That "something" is Dyndrite's Additive Manufacturing Toolkit (AMT) and accelerated production preparation build processor for 3D printing, both unveiled at Formnext. The platform allows users to import native CAD data, any geometry type and huge data sets (goodbye STLs), and export to any 3D printing process. It also comes with integrated Python API for scripting automated workflows and applications which can be used on laptops, desktops, local servers or the cloud.

“Of course, making complex geometries is difficult but I actually think that's a red herring. I don't think many people really care about lattices at all. They look interesting but you can't QA them, you can't clean them, you can't service them and you can't figure out how to fix them,” Goel explains. “On the other hand, being able to iterate is significantly more important. If it takes you 15 minutes to load a file and you do that four times a day and you have 10 people in your company and your burn rate is $100 to $200 an hour, you've now burned $10-20,000 a week just opening files.”
Processes that have traditionally taken engineers multiple pieces of software and hours or days to complete can now be done in a matter of minutes. Goel shared how some customers who were used to taking up to 70 hours to slice a design were now able to do so in under two hours. Furthermore, the ability to handle complex geometries natively without constant importing and exporting means part quality is controlled.
“The idea is to make every single person Superman or Superwoman," Goel adds heartily. "Again, the whole point is efficiency. Everything that we do is basically ROI guaranteed. If we are not saving you money or time in some way then we're probably not interested.”
Another big part of Dyndrite’s growth plan is its Developer Council which has already on-boarded an impressive roster of AM leaders. The council is part of the Dyndrite Developer Program which
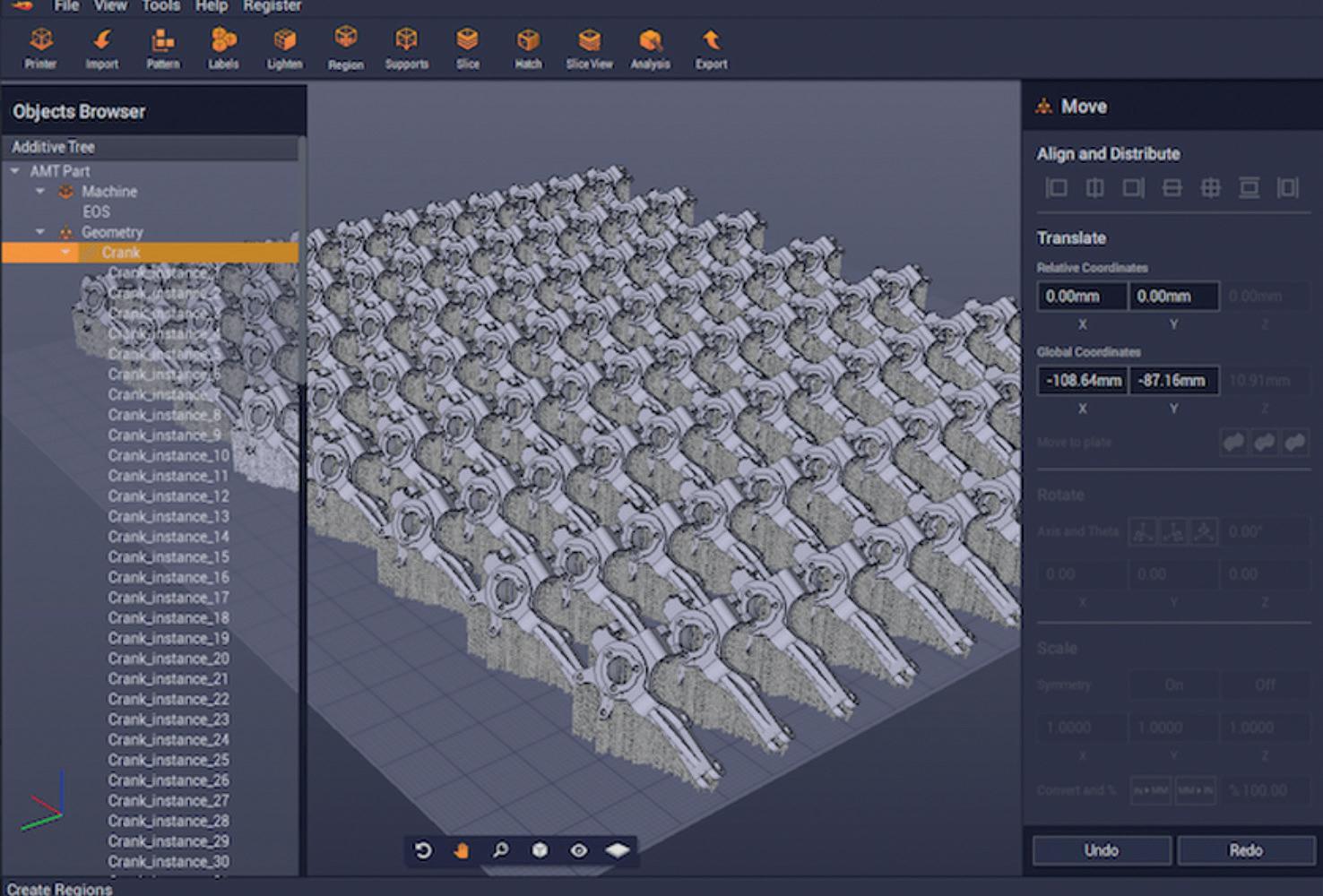
provides OEMs, software vendors and service providers with the necessary tools to develop for the platform. 3D Systems, ExOne, SLM Solutions, ANSYS and Altair announced their participation at Formnext, bringing this industry working group to a total of 15 members.
The company says it wants to be friends with everyone in the room. “There's no reason why we couldn't licence ourselves to everyone here,” Goel says, alluding to bigger ambitions of having a Dyndrite sticker on every machine (I spot several Dyndrite logos already dotted around on various booths on the show floor) but he asserts that while there is a lot of scope for this technology, Dyndrite is staying focused, honing in on five market segments: aerospace, automotive, energy, medical and service bureau.
It is clearly doing something right. Two major metal additive manufacturing players, Renishaw and EOS, recently teamed up with Dyndrite to adopt the AMT into their respective workflows. For Renishaw, that means integrating AMT into its QuantAM build processor to accelerate slicing, latticing and lightweighting while also speeding up the overall CAD-to-print process. For EOS, it will support the build processor for its direct metal laser sintering portfolio to increase performance, portability and repeatability.
After just under a year in beta mode, Goel says the company is getting close to having a product that’s ready for a full release. It also recently launched its limited-time Magic Amnesty Programme that will close in April. Until then, it's continuing to push the platform, bring in more developers, and excited to see what those first users do with the technology.
“As you can probably tell, we're pretty paranoid about making something perfect," Goel concludes. "We think that we're going to be flipping the switch sometime this year.”
27 28 29
JANUARY 2021 Tokyo Big Sight, Japan
SAVE THE DATE
One of the most reliable machines without wings Robust additive manufacturing systems by TRUMPF
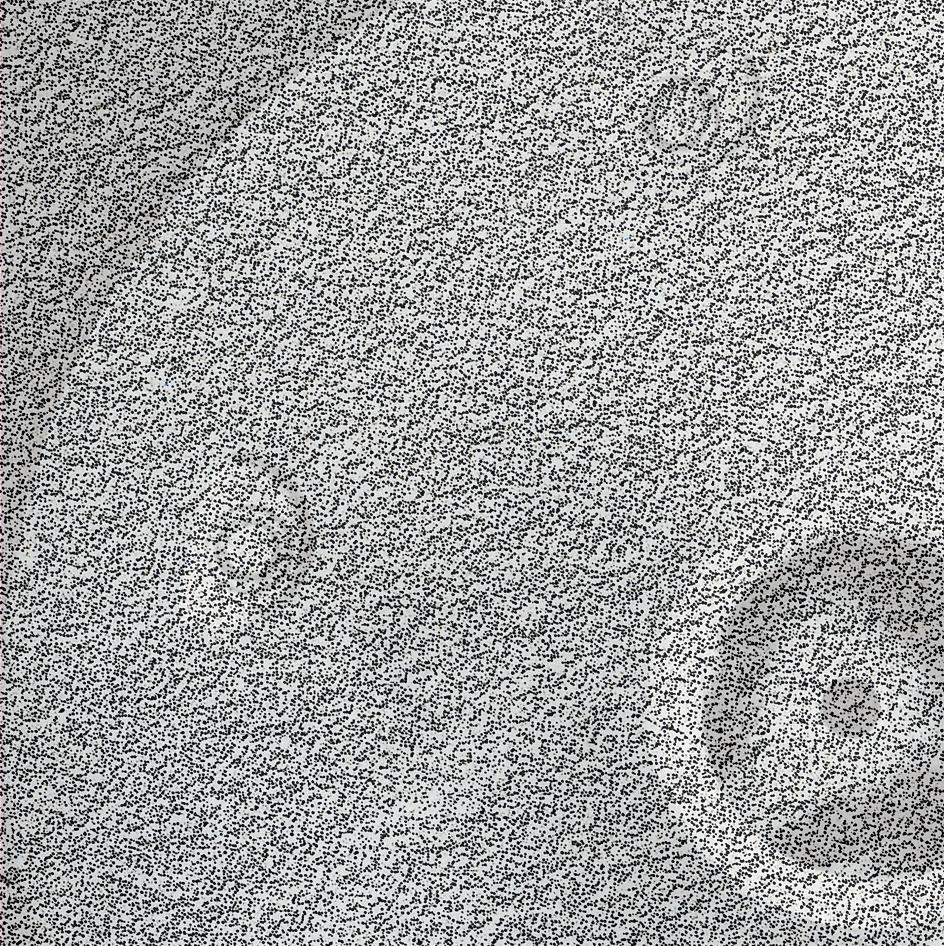
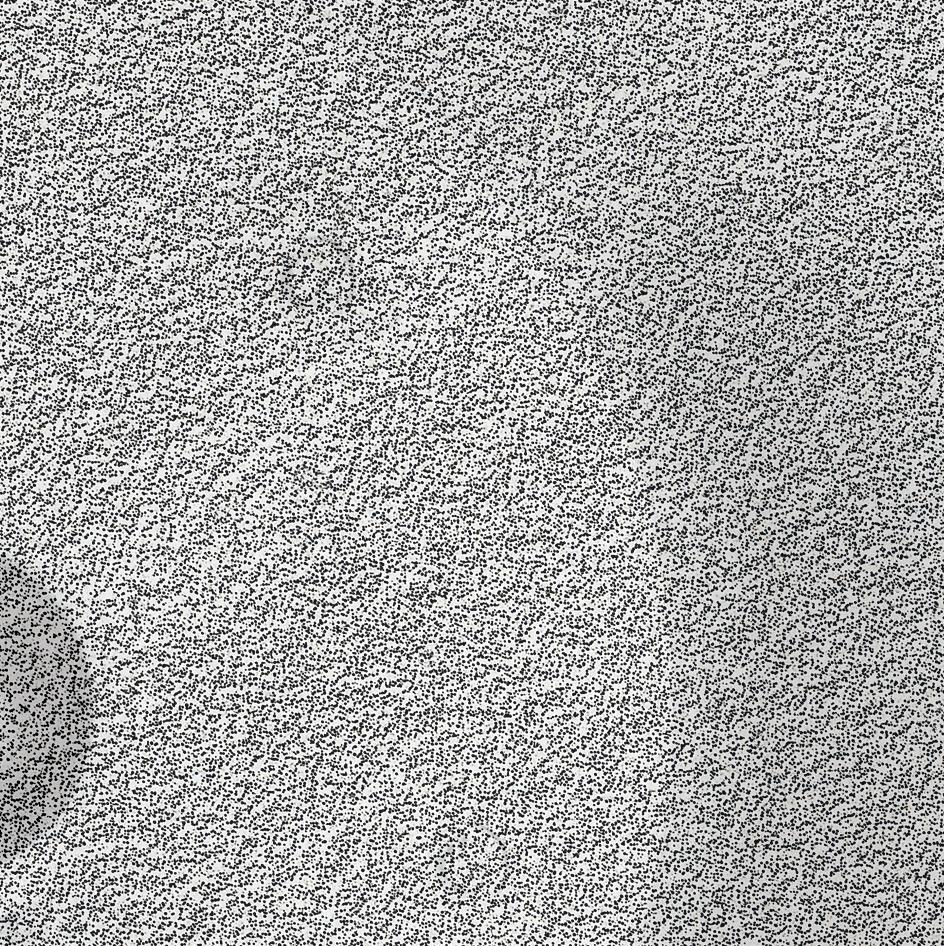
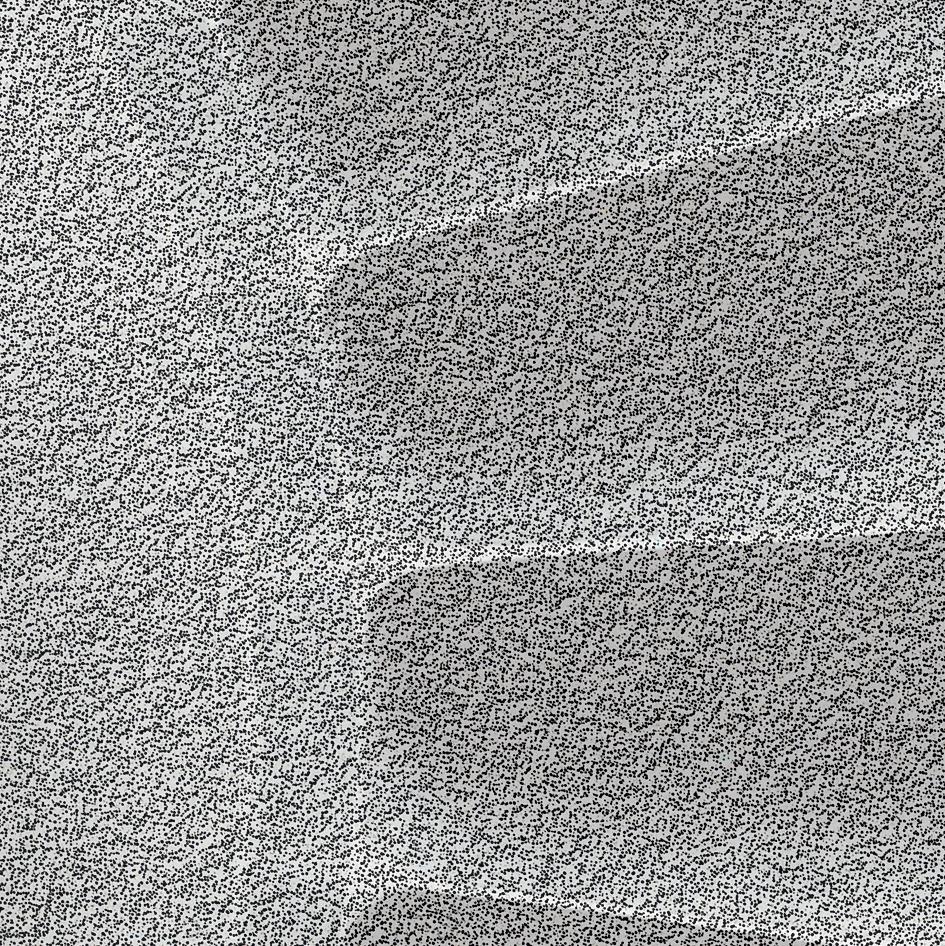
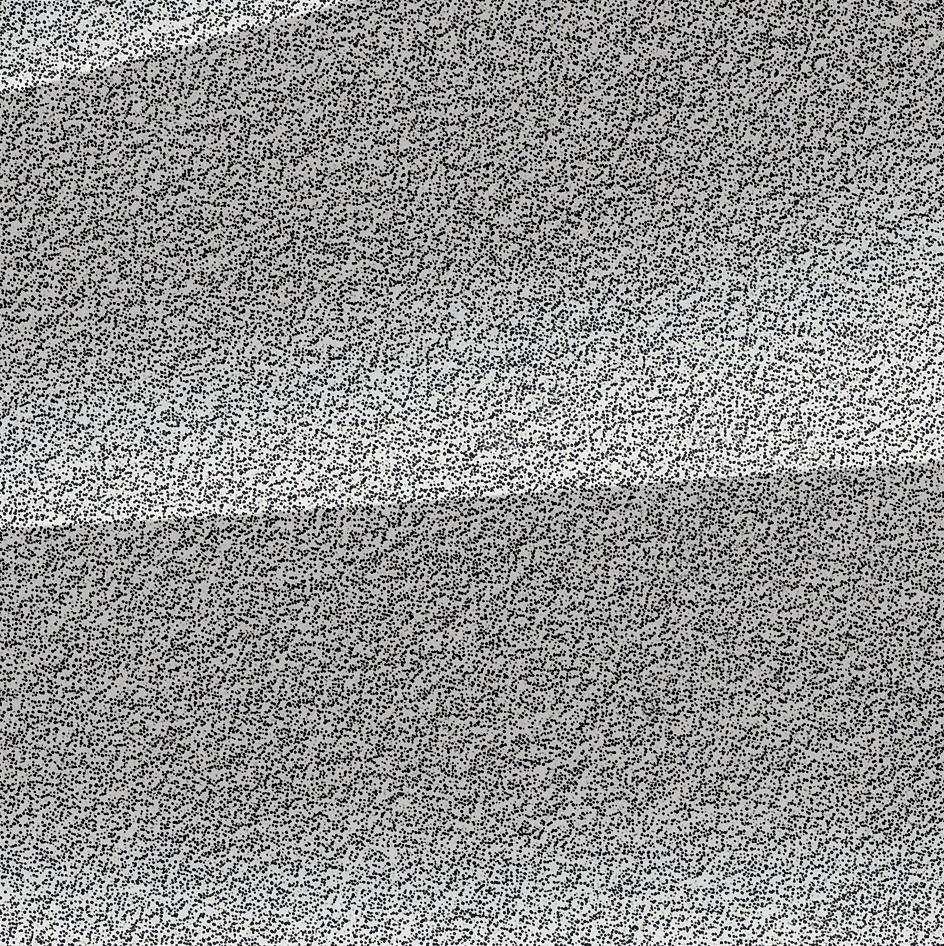
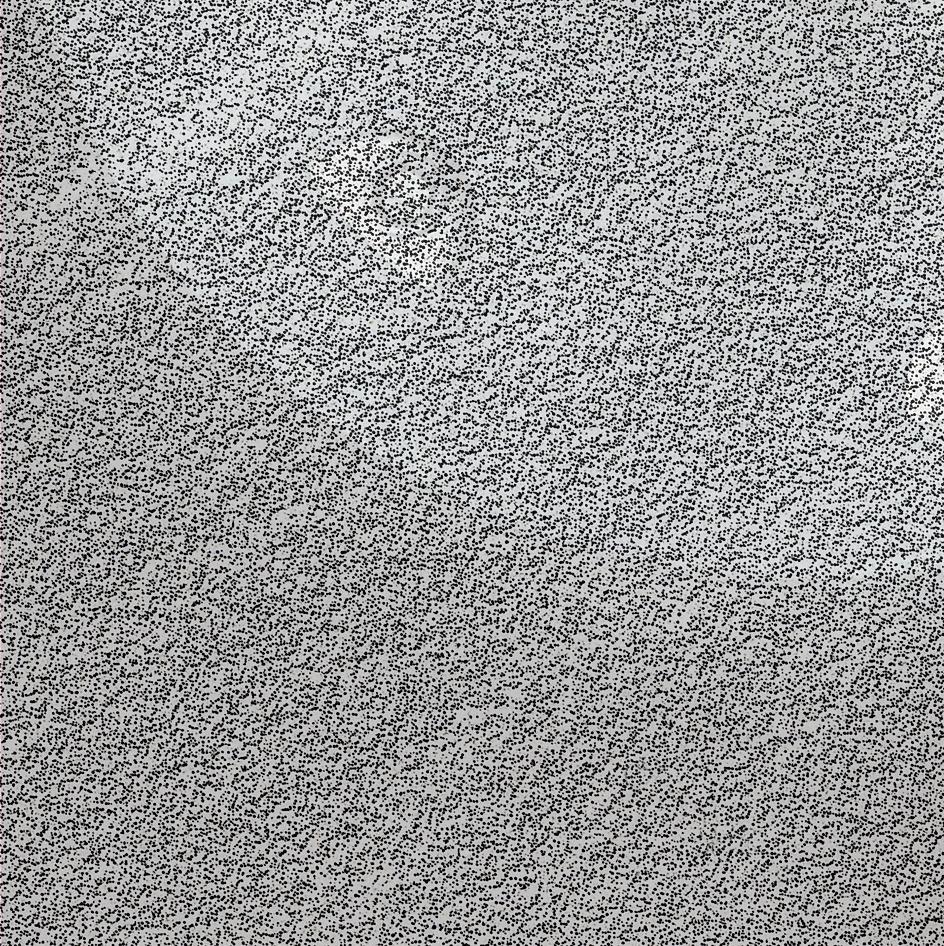

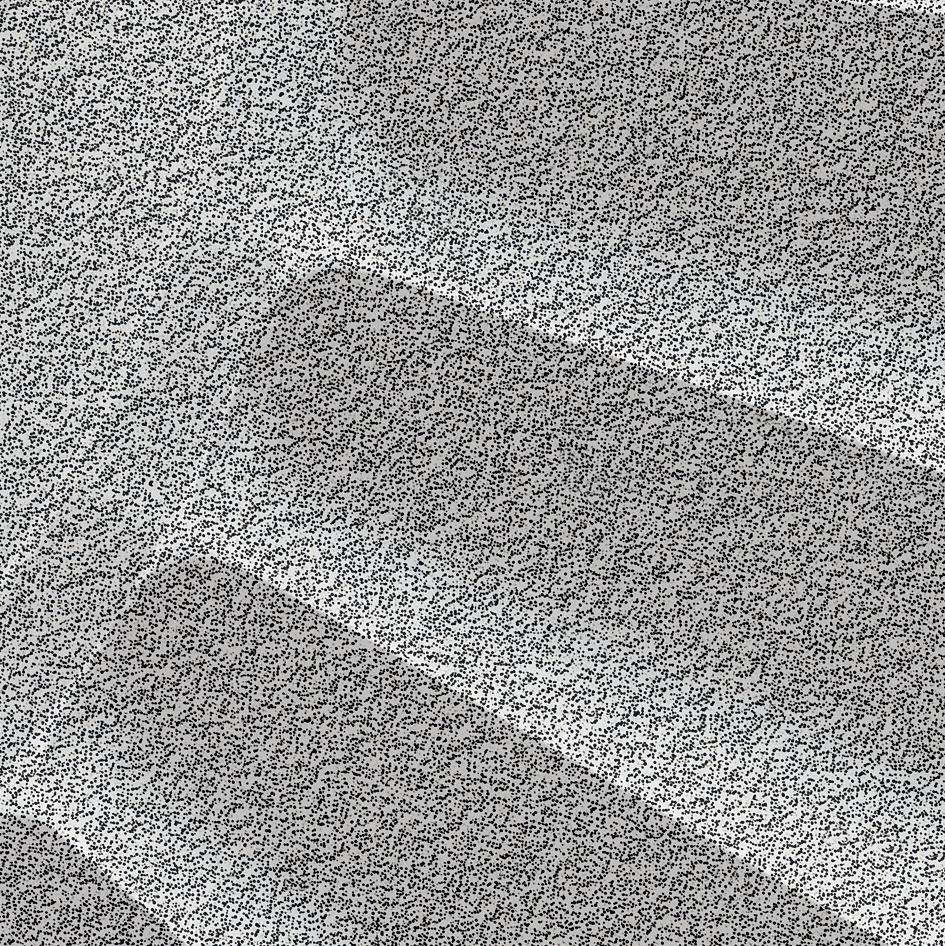
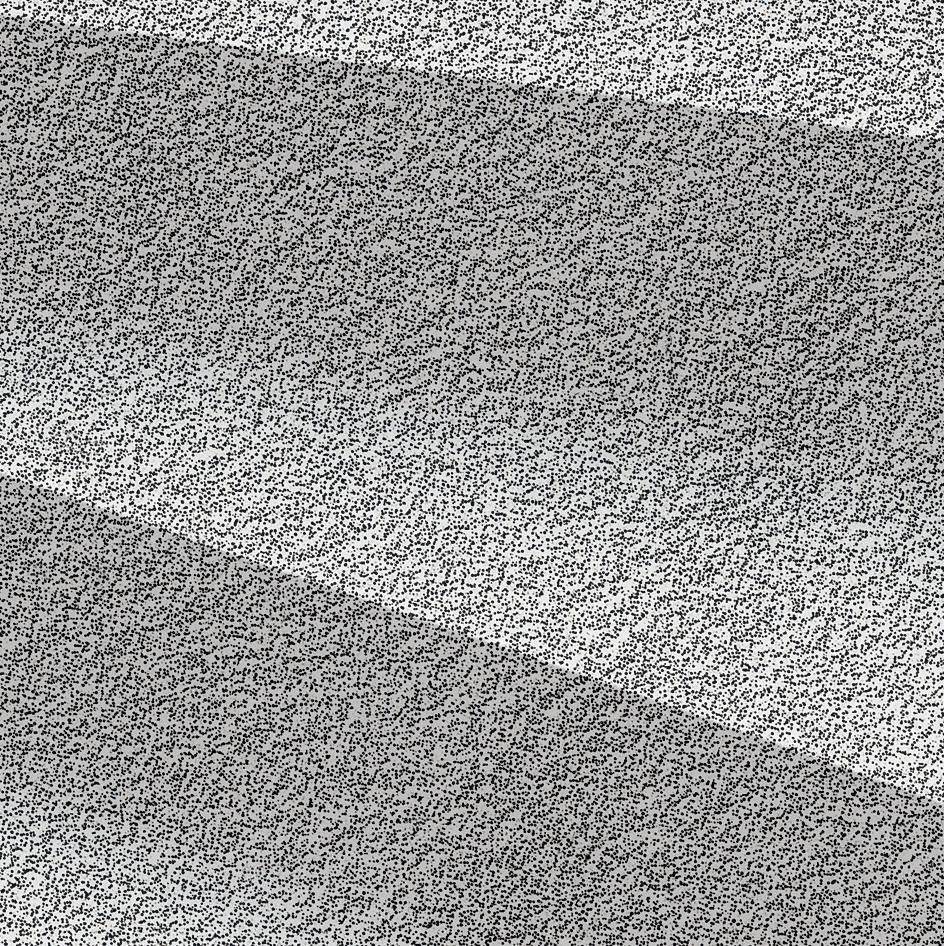

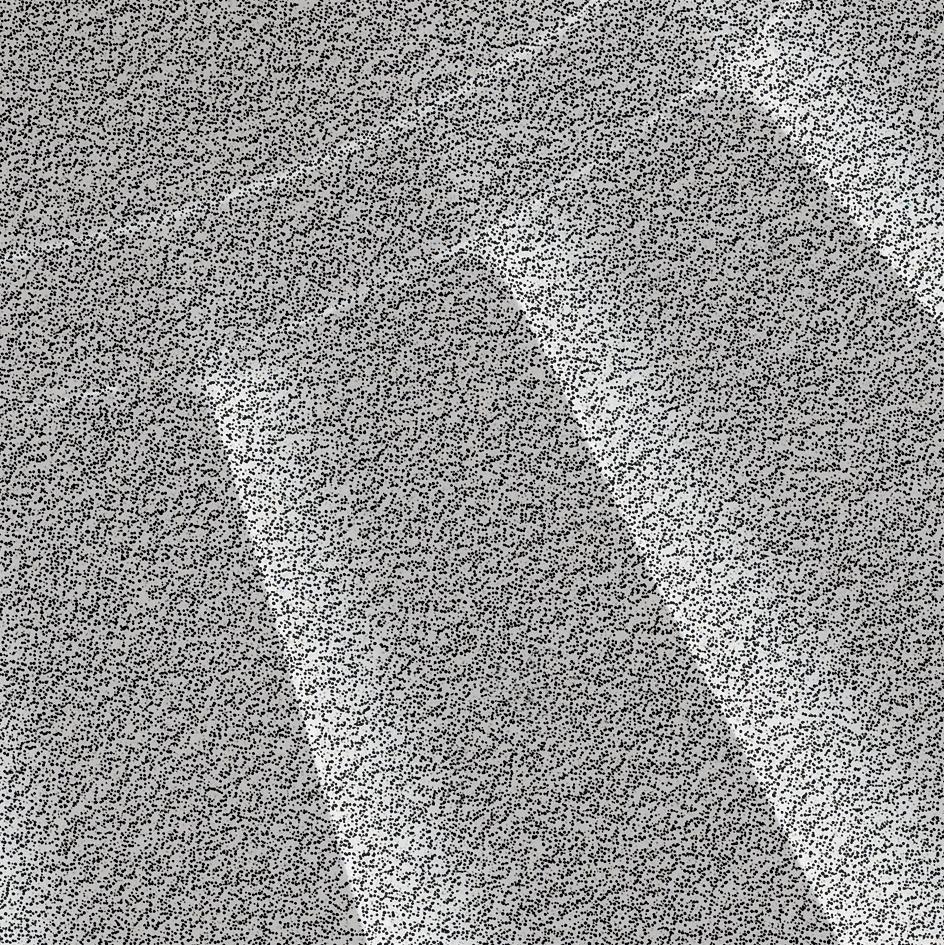
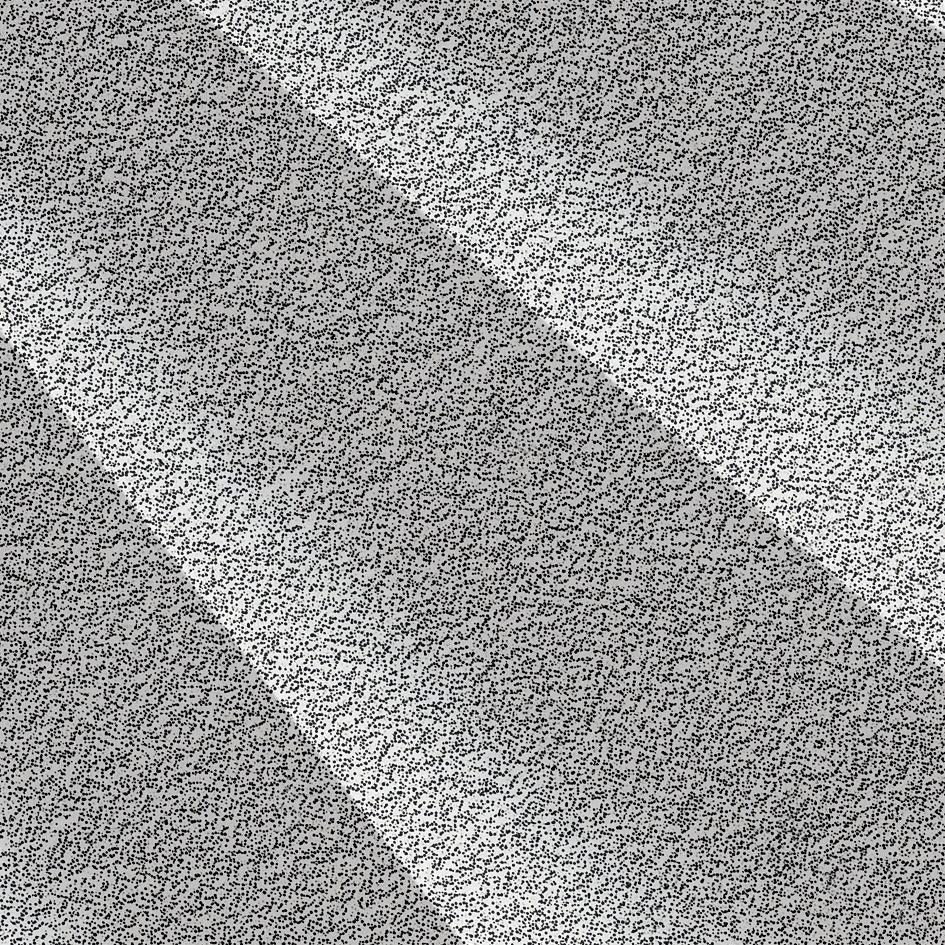


As a long-standing partner to the aviation and aerospace industry, we know all about the stringent requirements for quality and safety when it comes to components. With additive manufacturing, there are no limits to lightweight production and the functional integration of complex components. This means that brackets, turbine blades, and other applications can be produced quickly and reliably, and can be optimized for their specifi c purpose. The benefi ts this brings to aviation applications are clear to see.
www.trumpf.com/s/additivemanufacturing