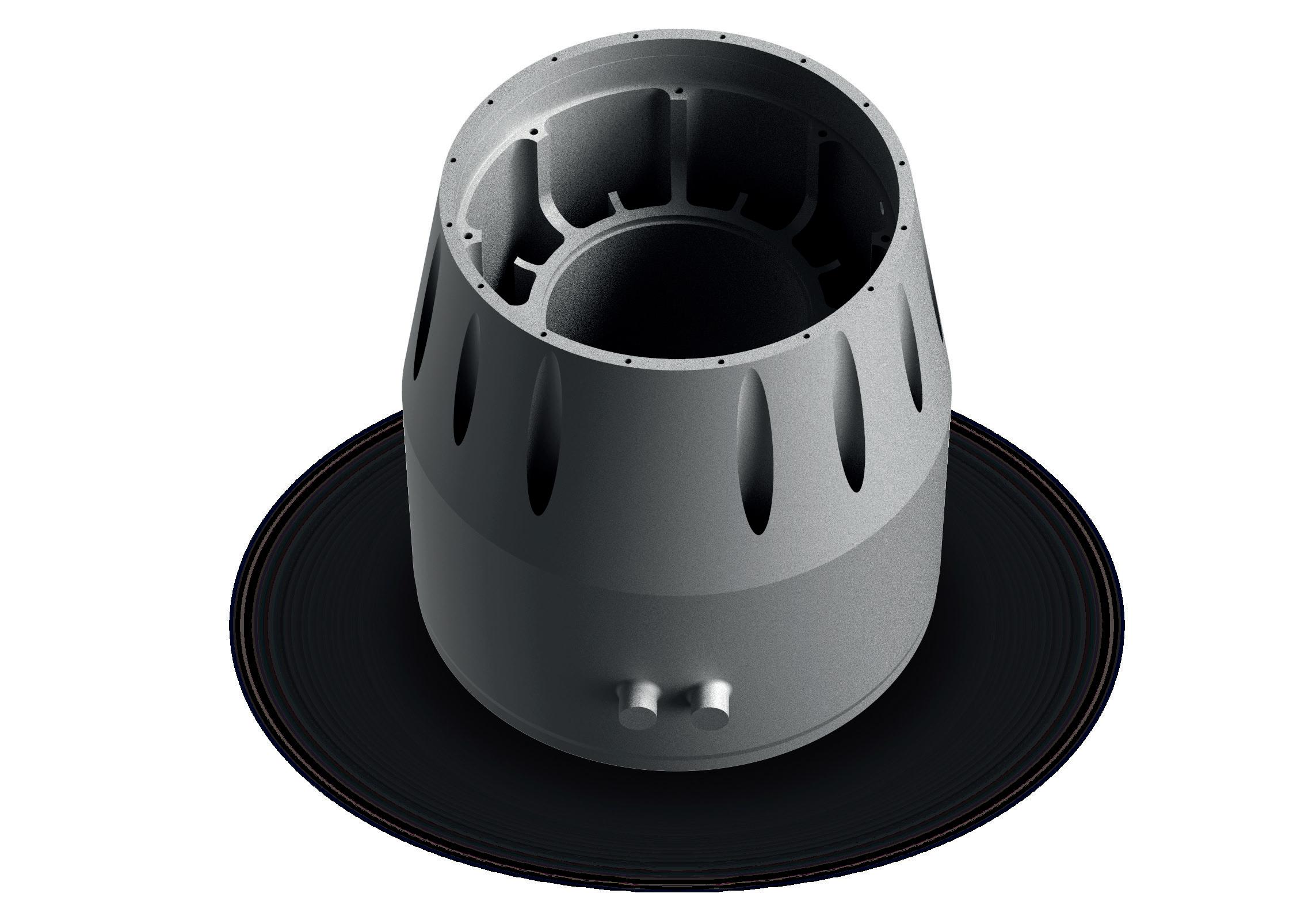
3 minute read
THE EASY PART
WORDS: SAM DAVIES
THE EASY PART
When asked to tell the story of a redesigned aerospace-grade turbogenerator housing powered by nTopology software and metal 3D printing, KW Micro Power’s President, Enrique Enriquez, questions why anyone would need to know anything beyond the 44% weight saving.
“I would be more than happy with just 20-25% weight reduction,” he is quoted as saying on the nTopology website. But thankfully Ryan O’Hara, the software firm’s Technical Director of Aerospace and Defense, never tires of regaling nTopology’s wins.
KW Micro Power is a manufacturer of high-power density Auxiliary Power Units (APUs) for commercial aviation and military applications. For APUs on board aircraft or drones, the weight is considered to be the most important consideration. Previously, a CNC machined version of the generator housing weighed 10.4kg, but after the redesign with the nTopology Platform, this was brought down to 5.9kg. Such a weight-saving was achieved with variable shelling after the loads on the housing were confirmed to be relatively small using nTopology’s integrated static and modal analysis simulation tools.
“We handle geometry as one math equation,” O’Hara told TCT. “In a traditional CAD tool, they think of each surface as its own individual set of math equations because it’s a bunch of surfaces tied together. By treating it as one, we can shell a part and we can vary that thickness where we need to. We made it thick at the ends and thin in the middle. That’s really all we did in this case.”
Having removed some material from the housing, O’Hara’s team then ran some stress simulations on the loading conditions provided, adding material back where a high stress was detected. Even still, nTopology was able to remove twice as much weight as KW Micro Power had anticipated and did so within a single day’s work.
And that is only half the story. While removing weight from the redesigned model within nTopology’s software, O’Hara’s team recognized the opportunity to integrate cooling channels in the hollowed-out structure. “Everybody wants a lighter part,” O’Hara said, “but they also want it to perform better, right?”
This was the first time that KW Micro Power had used cooling channels on a microturbine component. Using engine fuel as the cooling medium, the cooling channels reduced the maximum operating temperature by 33%, with the external temperature of the generator dropping 86%, down to 27°C, making it safe to touch. This allows KW Micro Power to use Aluminum F357, which is certified for mission critical applications, to print the part with VELO3D’s metal powder bed fusion technology.
To understand the impact these design changes would have on the housing, thermal FE analysis and CFD simulations were then carried out, while nTopology also tested the solution for fatigue strength, grip force, pull-out breaking force and behavior during take-off and landing.
“Anytime you can get the design and the simulation closer together, the better your solution is going to be,” O’Hara explained. “Now the housing doesn’t just hold the generator anymore, it’s cooling the generator, it’s preheating the fuel.”
Such rewards normally come after such hard work. But within a day, O’Hara and his team were able to reduce its weight by nearly half, cool the temperature by a third, and integrate multiple functions into a single part. Yet, he claims it was the ‘easiest part ever.’
“One of the big reasons I came to work for this company was that engineering is unnecessarily hard sometimes,” O’Hara finished. “And then I think, what a fascinating time we live in when we can design these [parts]. Key to this is that the manufacturing capabilities or the ability to do complex parts is better than what we can actually design. A big mission for us is to even that playing field out.”