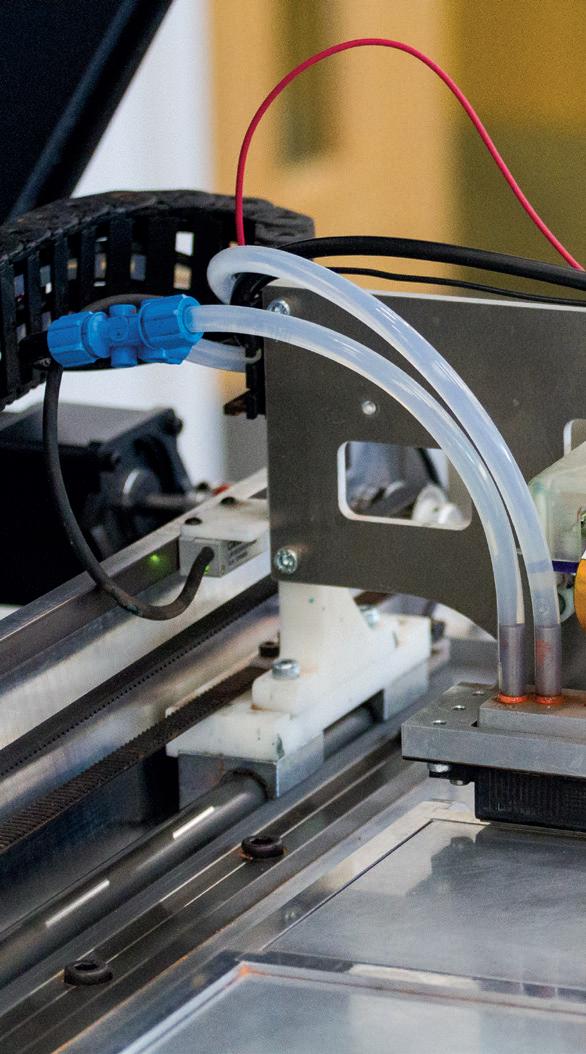
7 minute read
EVOLVING BINDER JET
At several intervals over the last ten years, the business decisions of GE have marked the progression of metal additive manufacturing (AM). There was the LEAP fuel nozzle application, proving its capacity for volume production; the acquisitions of Concept Laser and Arcam to further underline its commitment to AM technology; and then its entry into binder jet with the H2 program, a validation of this particular process’ potential.
Famously, GE Additive’s binder jet project got underway when then General Manager Mohammed Ehteshami tasked a team with developing a new machine within 55 days. They had a prototype ready to announce within 47 but have spent the subsequent three years taking a steadier approach as it readies to introduce a commercial product to market. The H2 efforts have gone on to encompass a beta program that piqued the interest of power generation firm Cummins, metals specialist Sandvik and transportation company Wabtec.
Wabtec has been using the technology for two years, deploying it alongside its existing laser melting 3D printing platforms in its Grove City, PA facility after initial work in GE Additive’s Cincinnati labs. The company considers binder jet to be a ‘unique metal process’ and is using applications of casting as its guidepost to identify additive manufacturable parts. Currently, Wabtec is carrying out business case analyses on engine components, traction systems and emission control systems in line with its services to the freight and transit sectors, while spare parts are also on the agenda.
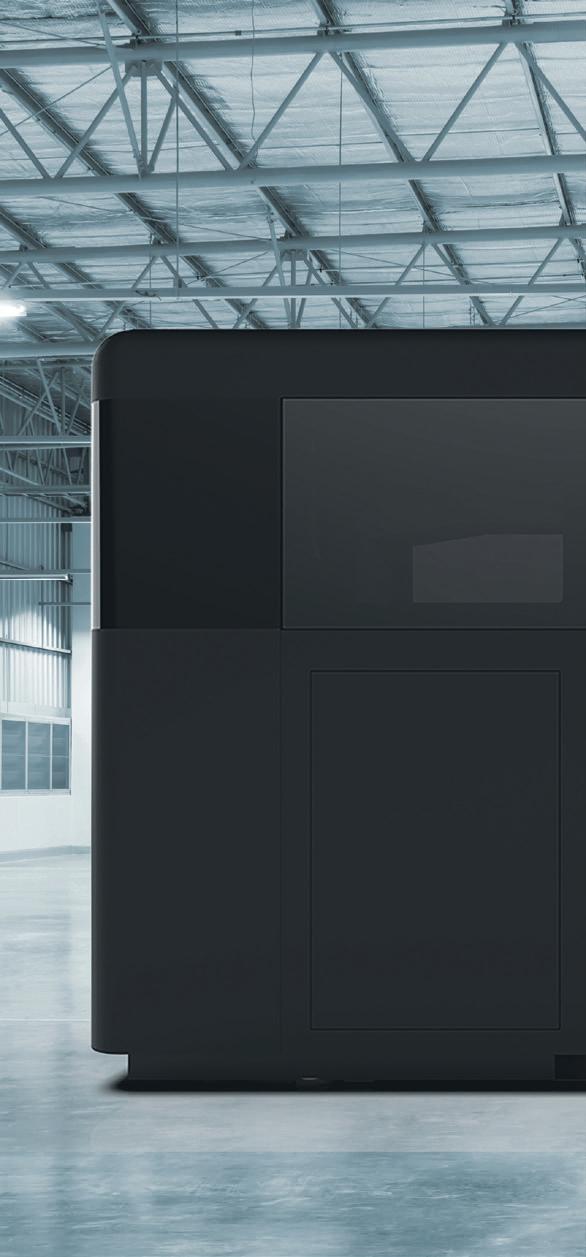
Wabtec's 13-strong AM team is being involved in the majority of the company's ‘major initiatives’, including its battery-electric freight locomotive efforts which will reduce emissions by at least 10%. It is said that AM is being embraced company-wide, with Wabtec excited to see how much disruption technologies like binder jet could cause.
“Additive manufacturing provides that opportunity to innovate by unlocking traditional design constraints,” Wabtec’s Global Additive Manufacturing Leader Anthony Mott told TCT. “There is an opportunity to improve rail products through the improved efficiency, better quality, better reliability, all at a competitive price point. And that price point is where binder jet really shines. Binder jet provides those traditional benefits but at a speed that provides better price per part cost. That makes that business case much more attractive.”
These benefits have not only encouraged GE to explore binder jet 3D printing but enticed Digital Metal, Desktop Metal and HP to follow the path set out by ExOne. What for a while was a niche 3D printing process, is now very much a competitive space. And with increased competition comes new ideas.
MEET META
Originating from within MIT, binder jet techniques typically see binding agents deposited onto a powder bed with a levelling roller laying down more powder to form parts layer by layer. After the print, parts are removed from the powder, cured and then go through sintering or infiltration.
GE Additive is perhaps the most tight-lipped about the intricacies of how its binder jet process works, but HP has publicly revealed there is no debinding step in its process. Meanwhile, Desktop Metal has come to market with a bi-directional single pass jetting technology that applies powder deposition, spreading, compacting, ballistic suppression and binder jetting with each pass over the build area. It also has the Live Sinter software platform which generates negative offset geometries to fill part designs with cells that go through the process of shrinking and distorting the parts’ experience in a furnace to eliminate the need for supports and reduce trial and error in sintering. Such increased competition has seen binder jet pioneer ExOne develop its patented NanoFuse binders which are embedded with nanoparticles to simplify the sintering process and improve part quality.
The latest company to step into the binder jetting ring is one spun out of the University of Liverpool: Meta Additive. Described as ‘reactive binder jet printing’, Meta’s process leans on a binder made up of molecular ink, nanoparticles and microparticles which can simultaneously bind and infiltrate the powder bed with functional build material. When the binder sees the powder bed, there is a reaction within the process that ensures the ‘green part’ is much stronger than conventional binder jet parts. As a result, parts can be up to 88% dense, meaning heat treatment is more of a ‘consolidation step,’ while shrinkage rates are as low as 2%.
SHOWN:
META ADDITIVE'S BINDER JET TECHNOLOGY
SHOWN:
GE ADDITIVE'S H2 MACHINE CREDIT: GE ADDITIVE
WORDS: SAM DAVIES
BINDER JET

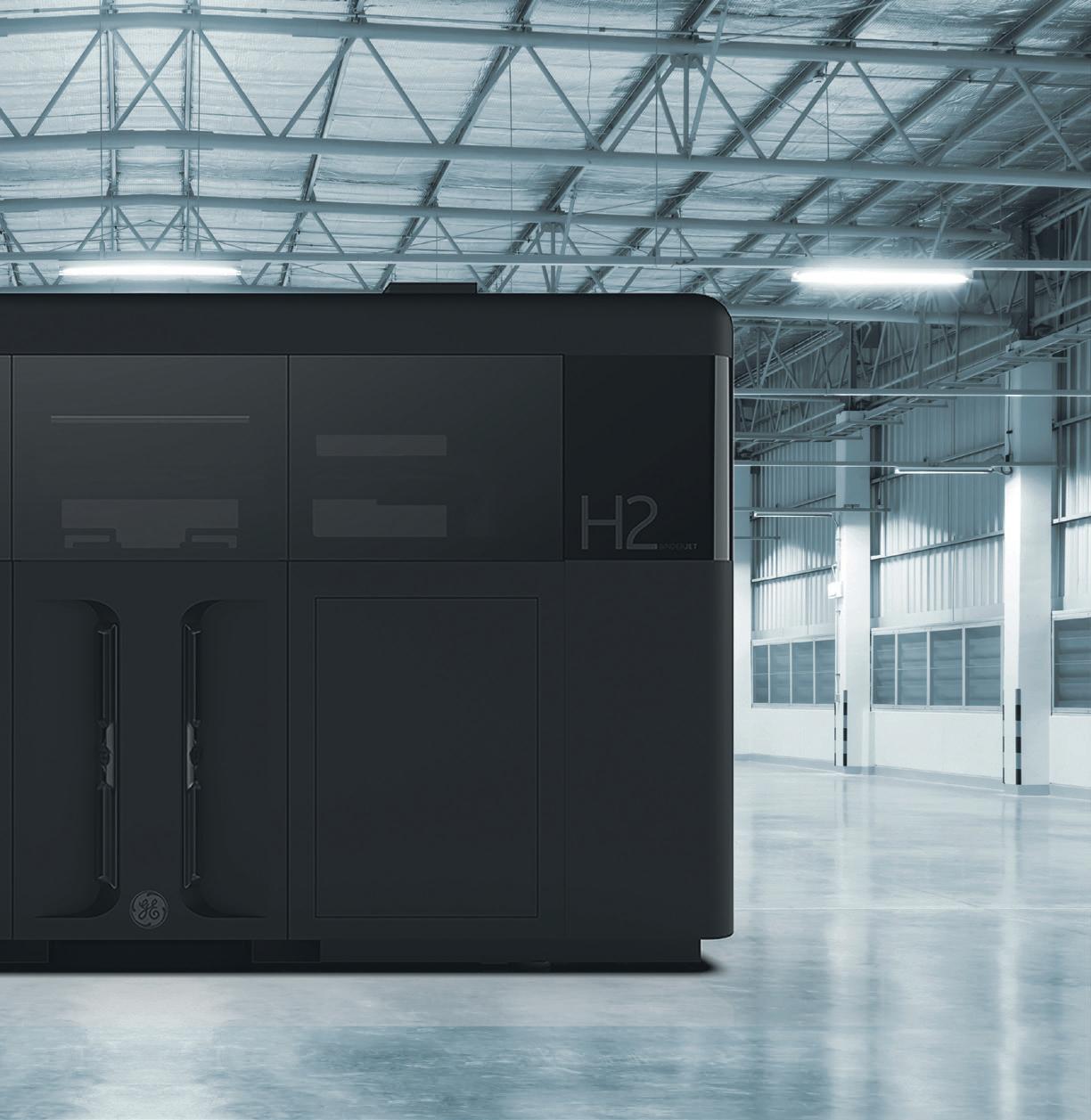
The research that has spawned this process has its roots in atomic layer deposition and chemical vapor deposition, with Meta founder and CTO Dr Kate Black eventually beginning to consider what impact the chemistries they were working with could have in a 3D printing process. In binder jetting, using a sacrificial binder causes implications with density and shrinkage which prolong the process. Meta Additive was born out of a motivation to address such issues.
“Binder jet appealed to me because, inherently, the printing process is quick; it’s all the post-processing steps that are the issue,” Dr Black told TCT. “Can we eliminate some of those processes so that we can scale up for mass manufacture? Can we get rid of some of the issues that you’re seeing with shrinkage and density? Can we use chemistry to eradicate those issues? That was at the heart of what Meta wanted to do.”
The importance of chemistry, for Dr Black, goes beyond the binding ink and, unsurprisingly, converges on the build materials at the disposal of manufacturers. She analogizes an artist being constrained by working with one or two colors as opposed to a full palette; more materials will facilitate much smarter products being developed.
“Everything about manufacturing is to do with materials,” she said. “If we don’t have the materials, it’s just an idea in your head and it will stay an idea unless you have the materials.”
CHEMICAL COLLABS
The quickest way to provide those materials is via collaboration, like that between Desktop Metal and Uniformity Labs. Their partnership is several years old, yet only became public knowledge in March when the pair announced the development of Aluminum 6061 powder for Desktop Metal’s Production System.
Uniformity aligned with Desktop Metal because it values the Production System’s inert processing environment, which allowed it to produce a higher safety profile of powder, as well as its reliability and reproducibility. The resulting material is said to boast an elongation greater than 10%, improved yield strength and improved ultimate tensile strength versus wrought 6061 aluminum with comparable heat treatment.
Upon announcing the launch of the product, Uniformity Labs CEO Adam Hopkins noted that the door to a ‘wide variety of thermal and structural applications’ had been opened across industries. Hours later, a leader of one such industry, Ford Motor Company, had announced their own aluminum 6061 binder jet material in partnership with ExOne. For Hopkins, it was no surprise.
“The automotive industry has been massively interested in aluminum from the beginning. Ten years ago, people said ‘can we binder jet aluminum?’ But the real question was, ‘can you sinter aluminum?’ And the answer has basically been no, not to a good density, not to get great properties,” Hopkins told TCT. “There’s lots of press and sinter aluminum out there, hundreds of thousands of tonnes, if not millions of tonnes, per year in some cases. But can you make complicated parts? Can you pair that with jetting and can you get wrought-like properties? Can you get the properties that you might get from a machined block of metal? That type of capability is what we’re bringing to the table and that becomes really exciting.”
In, as ExOne dubbed it on the front cover of TCT Magazine volume 7 issue 1, the year of binder jet, the excitement is palpable. There’re new machines to come, process tweaks and process innovations, in-demand materials and as we detailed earlier this year, software developments aplenty too. Welcoming these efforts are Wabtec, Ford and many more industrial heavyweights, who see in binder jet technology a potential series production process. The determination of the machine vendors to reach that potential is clear for all to see. As is the pride of the company to first bring the technology to market.
“At ExOne, our team and R&D partners are really proud of the role we’ve all played in helping to evolve this now very active area of metal binder jetting,” ExOne CEO John Hartner told TCT. "After two decades, we now have a full family of production-ready metal printers, a vibrant market of competitors and interested industries, along with a stable of industrystandard materials, from 17-4PH to 6061 aluminum. [We] truly believe metal binder jetting has a unique role to play in delivering sustainable lightweight metal parts at high volumes that will make a difference to the world at large.”