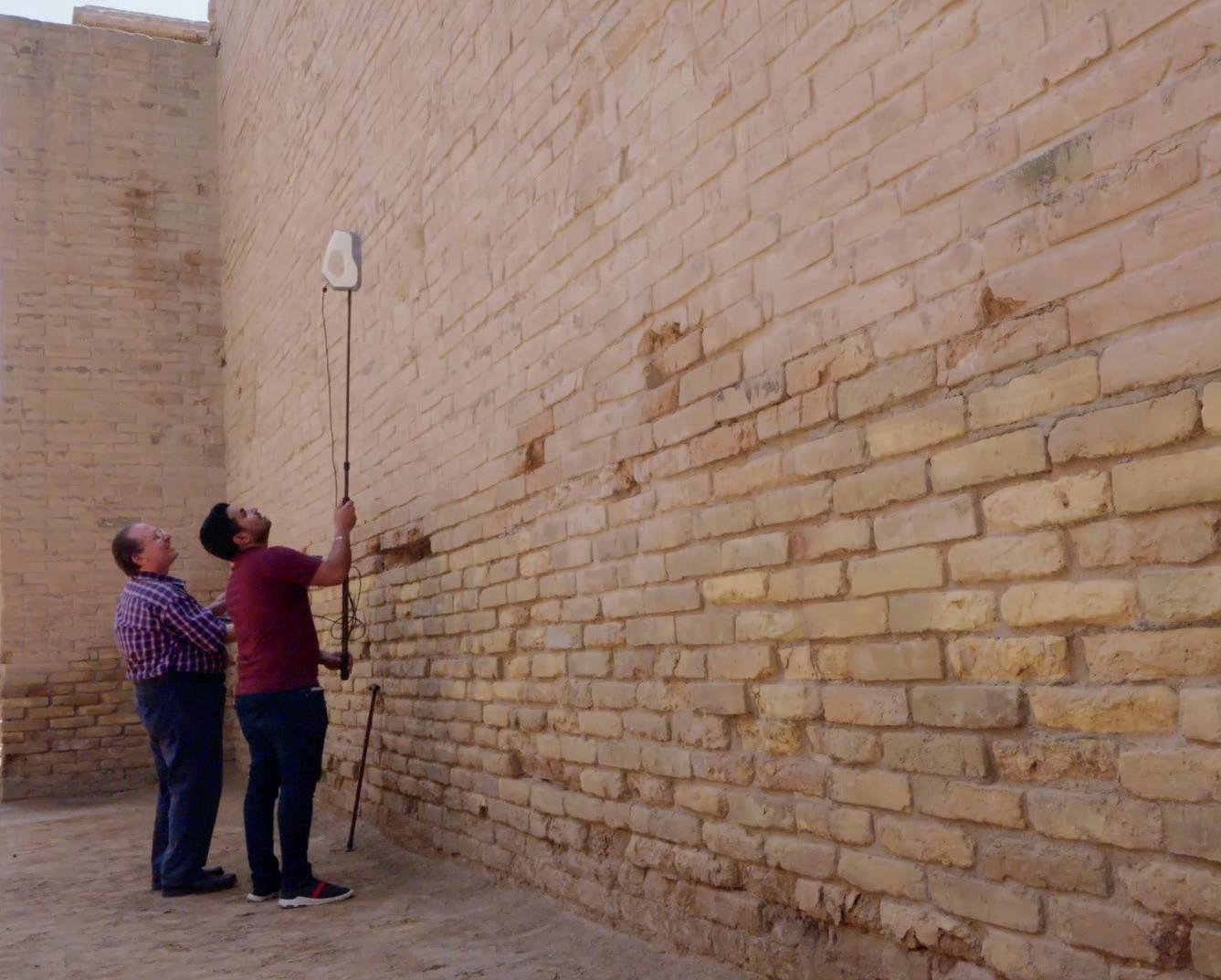
7 minute read
PRESERVING THE CRADLE OF CIVILIZATION
Head of Content Laura Griffiths speaks to filmmaker Ivan Erhel about using 3D scanning to digitize the past.
SHOWN:
THE EVA WAS USED TO SCAN LARGER PIECES S ave what could not be saved.”
That was the mission French filmmaker Ivan Erhel appointed himself when he decided to travel from the South to the North of Iraq in a race to preserve what remains of the history of Mesopotamia, often referred to as the Cradle of Civilization.
That urgency is no exaggeration. With ISIS occupying over 30% of the country at the time, destroying museums and statues in the process, Erhel recalled in a conversation with TCT how, after seeing a video showing the destruction of a museum in Mosul - countless relics and history lost in the process - he felt compelled to do something, anything, to help save what was left of the world’s oldest civilization. A conversation with a friend who had just purchased an Artec Eva 3D scanner sparked an idea.
“He said, ‘If I were there sometime before ISIS, we could have saved it,’ and I thought that was really a great idea, so I decided to make a film about it.”
The film centers on the journey of an Iraqi writer who, after three decades living in France, returns to Iraq to help preserve its history using 3D scanning. Prior to this project, Erhel had never used a 3D scanner and now left co-ordinating the project on his own with the support of 3D scanning specialist Artec 3D, set out with its Space Spider and Eva scanners in tow.
The destruction of the Mosul Museum and Nimrud, once a major ancient city 20 miles south of the city of Mosul, were the starting points for the project. The first piece to be scanned was the Processional Way, a 250-meter-long brick road 120 km south of Baghdad, featuring carvings of various animals and legendary creatures, much of which had already been destroyed by erosion. For larger pieces like this, a handheld Eva was propped up on a stick to reach harder to access areas while the blue light Space Spider was put to work capturing intricate details on smaller objects using a turntable. The team also scanned people, including soldiers who initially questioned Erhel’s
intentions with the technology (“It looked like a spy thing!” Erhel said) but after the project was explained to them, agreed to be scanned and are now featured in the film.
On top of logistical challenges around securing a visa and permissions to film, Erhel’s bid to capture as many monuments and artefacts as possible posed very real risk with the sounds of gunshots and further destruction never too far behind. For many of the sites, Erhel and his small team were the first to arrive and without the luxury of spending weeks scanning some of the larger monuments, including one that measured up to 75 meters wide and 30 meters high, often had to capture what they could in a matter of hours.
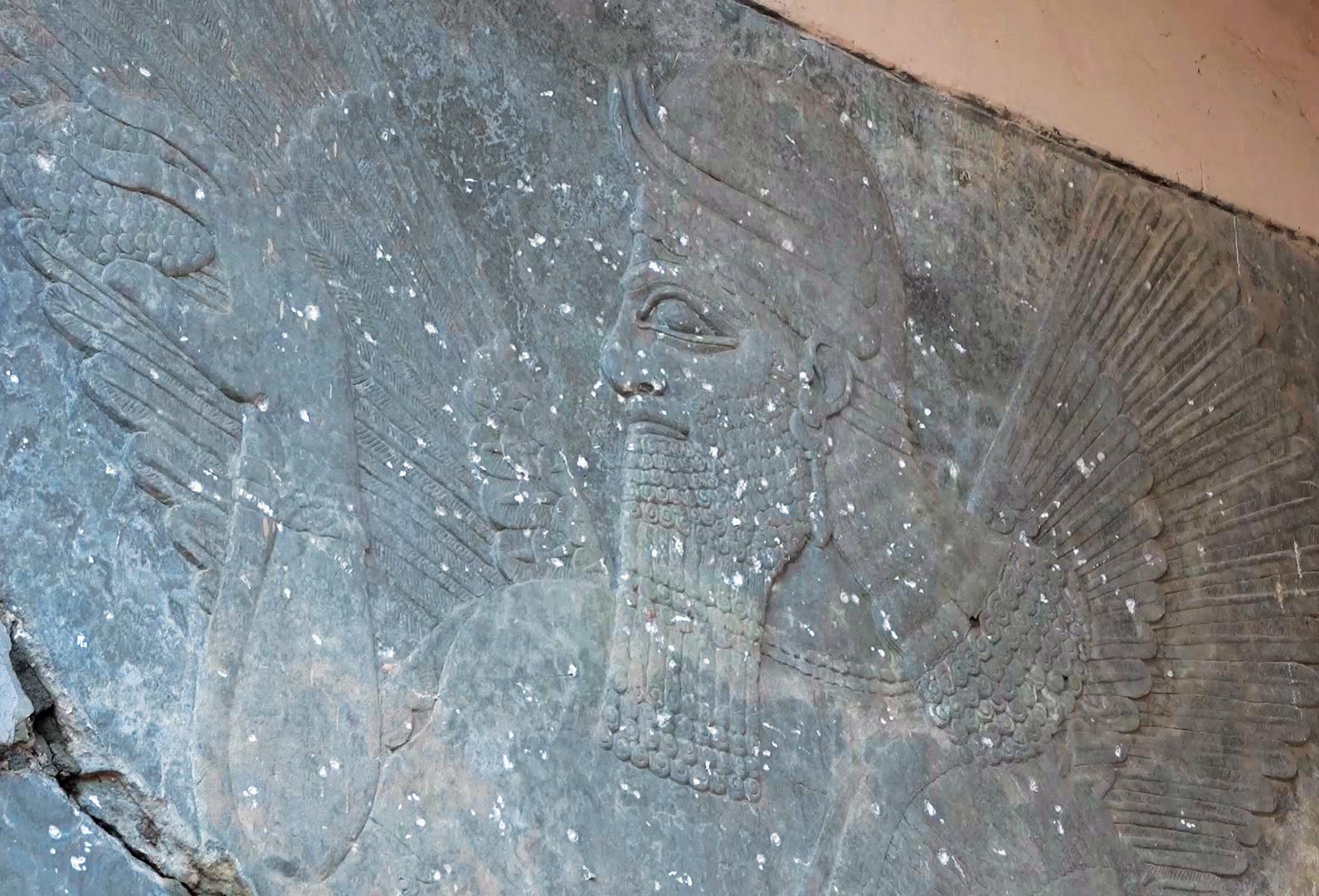
“We had to be very careful,” Erhel said, describing the “tense” situation the team found itself in while determined to scan what was dubbed “Last Survivor of Nimrud.” “There was one sculpture standing, the last one and we scanned it with the [Artec] Eva.”
Some of the scans are available to view on SketchFab and Erhel has even brought a couple of those files back into the real world with 3D printing. He’s holding one - printed using a powder-based process - as we speak. Erhel caveats that he’s not too enthusiastic about the quality of printing compared to 3D models (“You can’t compare with the original,” he said) and he shared how there was some hesitation from officials about letting the crew scan some artefacts through fear they would produce copies. That said, he believes the support of Artec 3D afforded the team a lot of credibility and believes there is real value in what they set out to achieve.
“Any documentation is welcome,” Erhel said. “Even if it comes from me who was not a professional in 3D, was not a professional in archaeology, I was nothing. I think a 3D model is so much more accurate than photography, it has much more information and you can understand much more by looking at 3D models, you can easily look at it through all angles. When you look at a model of all sides, then you see things that you cannot see on a photograph.
“If we were there sometime before we'd still have a trace of what Nimrud was because all we have is our photography and that photography is incomplete. So [3D scanning] is a way to give eternity.”
The film has since been completed and is currently available to watch in France, but Erhel’s mission continues. Now, he’s in the process of setting up workshops across the country to teach young people of Iraq about 3D scanning technology in what he hopes will serve as inspiration to start a movement of preserving heritage.
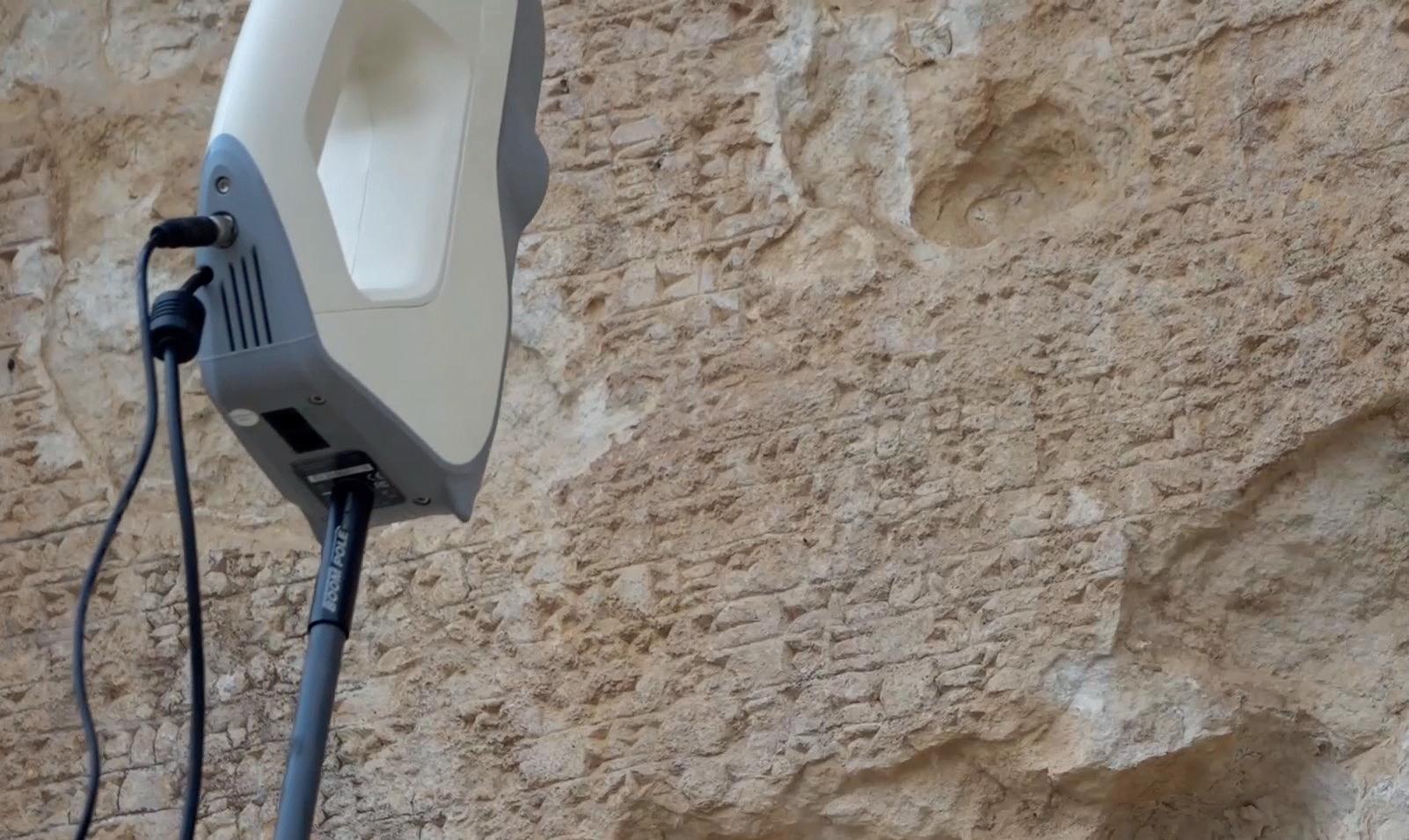
“The country is divided and it's very different when you're from the South, from the North or from the center,” Erhel explained, adding that he wants to create three workshops across these three distinct parts of the country, “So that they can work together on keeping this country together and scanning and sharing our common heritage because they are the guardians but this heritage belongs to all of us."
SHOWN:
DIGITISING HISTORIC CARVINGS IN 3D
SHOWN:
THE ARTEC 3D EVA HANDHELD SCANNER
For the technology itself, Erhel believes projects like his also show how 3D scanning can provide more meaningful value.
“I believe this technology was in search of a purpose, apart from [reverse] engineering, which is the obvious purpose,” Erhel offered. “But world heritage, human civilization, is a cause.”
The final and perhaps most enduring impact is the new light Erhel hopes his film and the scans taken along the way will place on Iraq. He wants viewers to recognize that the country is more than the images we see of war and destruction. It is the birthplace of much of human civilization, where the foundations for language, architecture, agriculture and more were built thousands of years ago.
“I think that's a good way to promote this heritage and to remind the world that Iraq is not just a conflict zone, Iraq is the cradle of civilization,” Erhel concludes. “Western civilization, we have a debt, an important debt, towards Mesopotamia and to this country.”
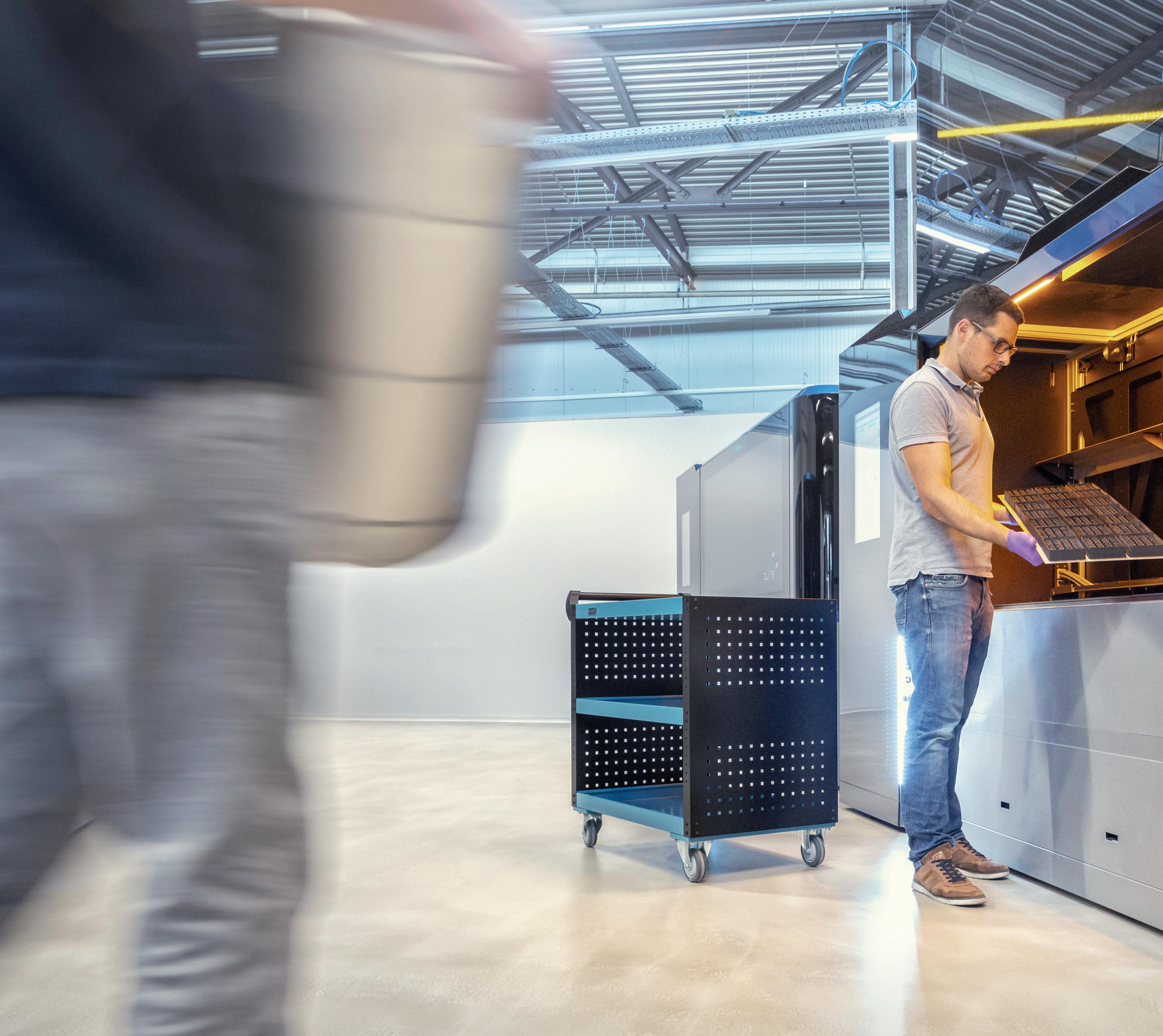
Cubicure starts digital series production: Cerion
The overhaul of stereolithography has been a long time coming. One Austrian 3D printing company bids to answer the call: Cubicure has just presented Cerion, a large-scale production plant which closes the gap to toolless, fully digital series production of polymer parts. Apparently, the machine is already in use with some pilot customers and has proven that it delivers on its promises.
Rethinking stereolithography
It needed a new way of thinking to turn dreams of the future into productive reality. No more resin baths or material trays; enter a process that doesn’t even need to limit itself to one single lighting technology. Cerion’s particular strength is a completely novel printing head that smoothly glides over the building area and, layer by layer, combines all building processes in one fell swoop.
With a giant building platform measuring one meter by thirty centimeters, one might think Cerion would need to take its sweet time to achieve an optical precision of 50x50 µm². Think again: Each layer is printed in just under a minute, completely independent of how many parts need to be produced in what size or how complicated their geometry is. So above all, Cerion is scalable, in its dimensions and its throughput. A few bulky or thousands of minute parts can all be printed simultaneously. „Due to the type of processing with a traversing printing head and exceedingly precise lighting control, there is no variance in manufacturing accuracy distributed over the build area,“ confirms Dr. Bernhard Busetti, process engineer and product manager for AM systems at Cubicure. The newly developed process even improves the reproducibility of print jobs. In addition, Cerion relies on Cubicure‘s seasoned Hot Lithography technology. It might be a new system, but it already hasa broad range of applications backing it up. „This is the essential breakthrough in the industrial upscaling of lithographic printing processes“ enthuses Managing Director and CTO Dr. Robert Gmeiner. „After three decades of stereolithography, finally an industrially scalable process has been found.“
Make the next step towards toolless manufacturing and come see the future of light-curing 3D printing for yourself at the trade show Formnext in Frankfurt am Main in mid-November.
Cubicure will be exhibiting in hall 12.1 at booth F39.
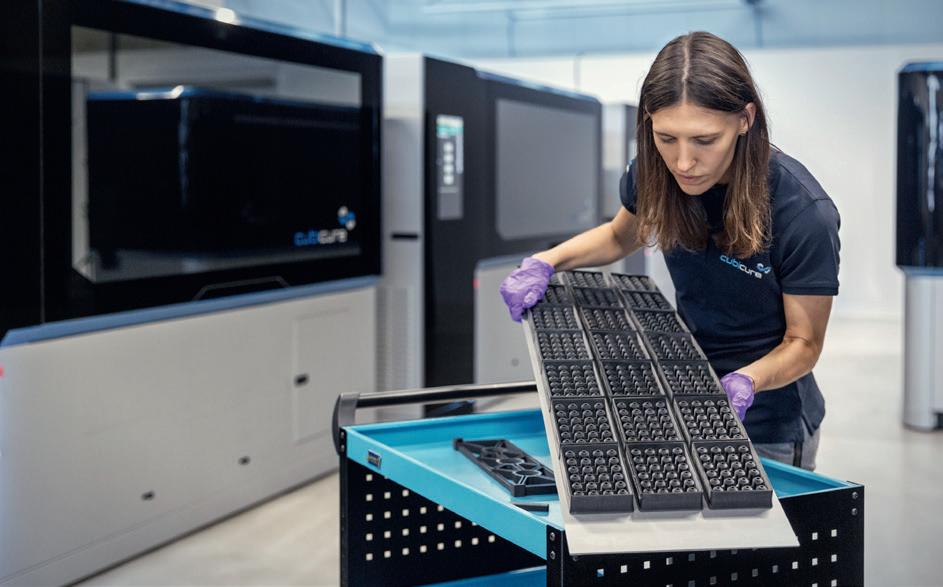