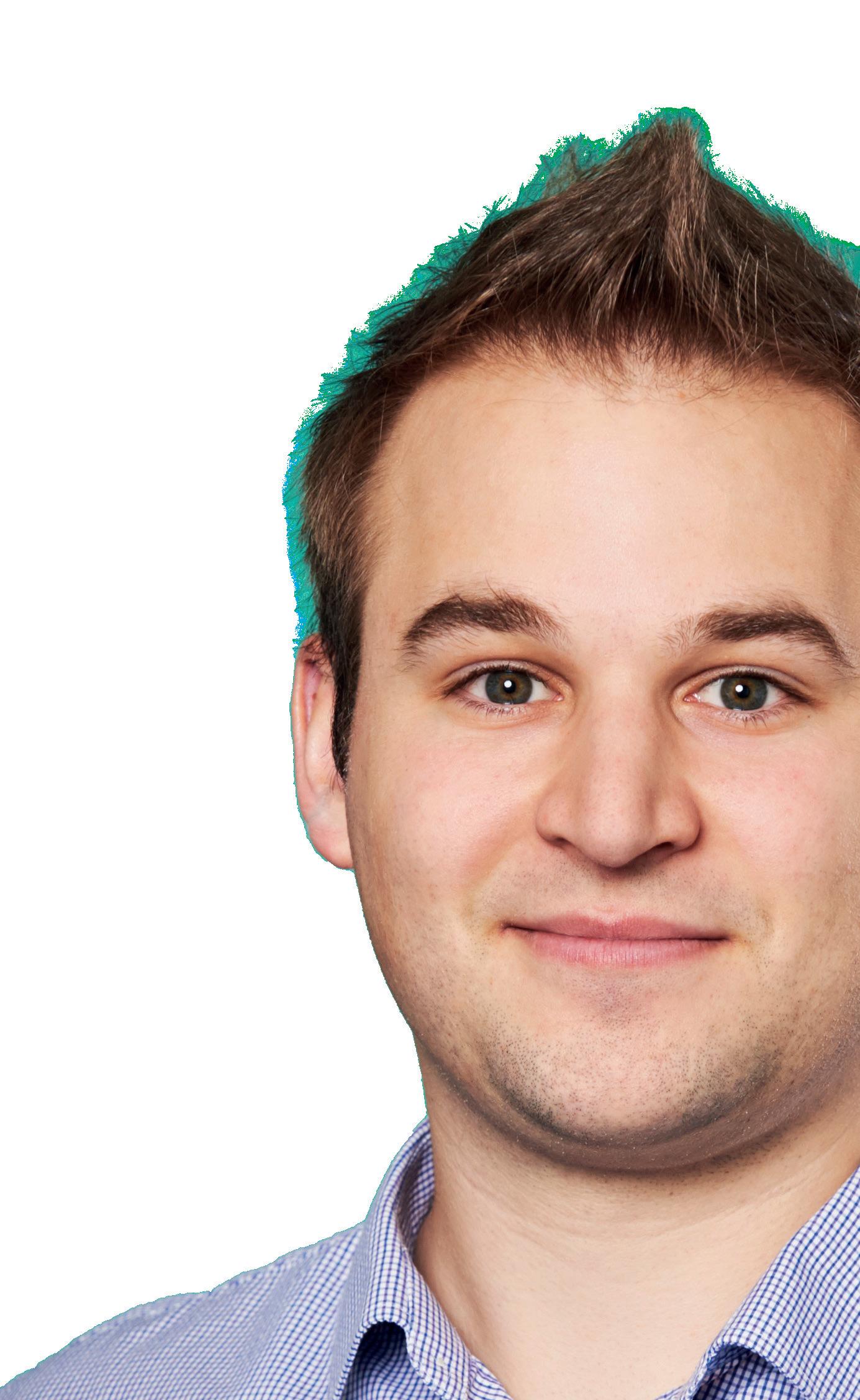
3 minute read
AUTOMATION AND ERROR DETECTION IN AM
WORDS: Pascal Becker, Research Scientist, FZI Research Center for Information Technology
Additive manufacturing (AM) is playing an increasingly important role in today's production. This is not only due to the fact that complex geometries can be produced with AM, but also because this type of production is economical, especially for small quantities and individualized products.
However, the work has so far been bound up with many manual steps. To begin with, the CAD data must be sliced for printing. The more experience and knowledge the employee has about the printing process, the more likely a successful print result is. The number of possible error cases varies depending on the type of process, and the possibility of observing the printing process in-situ also varies depending on the process type.
After preparation of the print data and the printer hardware, the process can be started. The print itself typically takes several hours, if not days. In that time, various errors can occur such as warping. Sometimes the errors are so serious that the print job can be aborted immediately, since the final part deviates greatly from the desired geometry and cannot be used. There are currently only a few options for automated error checking here. Various research institutes are therefore trying to implement this in-situ error detection using the current technologies. Not only does the choice of software approach (artificial intelligence, classical sensor data processing) play a role, but the choice of sensor technology is also very specific to the printing process. In addition to imaging methods such as 2D, 3D or thermal imaging cameras, acoustic and optical microphones, as well as vibration sensors are also being investigated. These sensors must be integrated into the hardware and the process, and the sensor data must be processed and evaluated in order to obtain added value. ways. Thus, the print can be monitored automatically and the recorded data can be used for quality assurance as well as for predictive maintanence for the machine. Reliable error detection enables the print job to be aborted at an early stage, therefore saving valuable time and material. As a result, the corrected print job can be started earlier and losses are reduced.
Once the print job is finished, the objects are manually unloaded, cleaned and post-processed. Depending on the object geometry and printing process, this can involve a lot of manual work. This is where the two modern technologies of AM and robotics need to be combined. According to some scientific publications, unloading the component with the help of a robot is very flexible and economically feasible. In the field of post-processing, there are already start-ups and scientific results which have studied and partially solved the problem.
Here, it is important to consider the overall system. Depending on the unloading strategy, something must already be adjusted in the slicing process so that the removal can take place without damage. At the same time, the system should be designed in such a way that few additional components as possible are required and at the same time, almost all possible parts can be handled. For example, it makes sense to have several printers maintained by one robot on a mobile platform so that the robotic system is profitable for a huge workload.
One of the advantages of AM is also one of the biggest challenge for robotics - due to the fact that virtually any possible geometry can be printed, the requirements for grasp points, gripper jaw design, required opening widths of the gripper or the post-processing strategy, are complex and diverse. These must be taken into account and integrated into a coherent overall concept.
Overall, further automation of additive manufacturing is inevitable. The more objects that are mass-produced using AM, the more important it becomes to continuously monitor and detect errors during the printing process and at the same time, reduce the number of manual steps after printing. Appropriate approaches need to be developed and implemented for these two topics so that AM can better exploit its potential.
rapid3devent.com
MAY. 17-19. 2022.
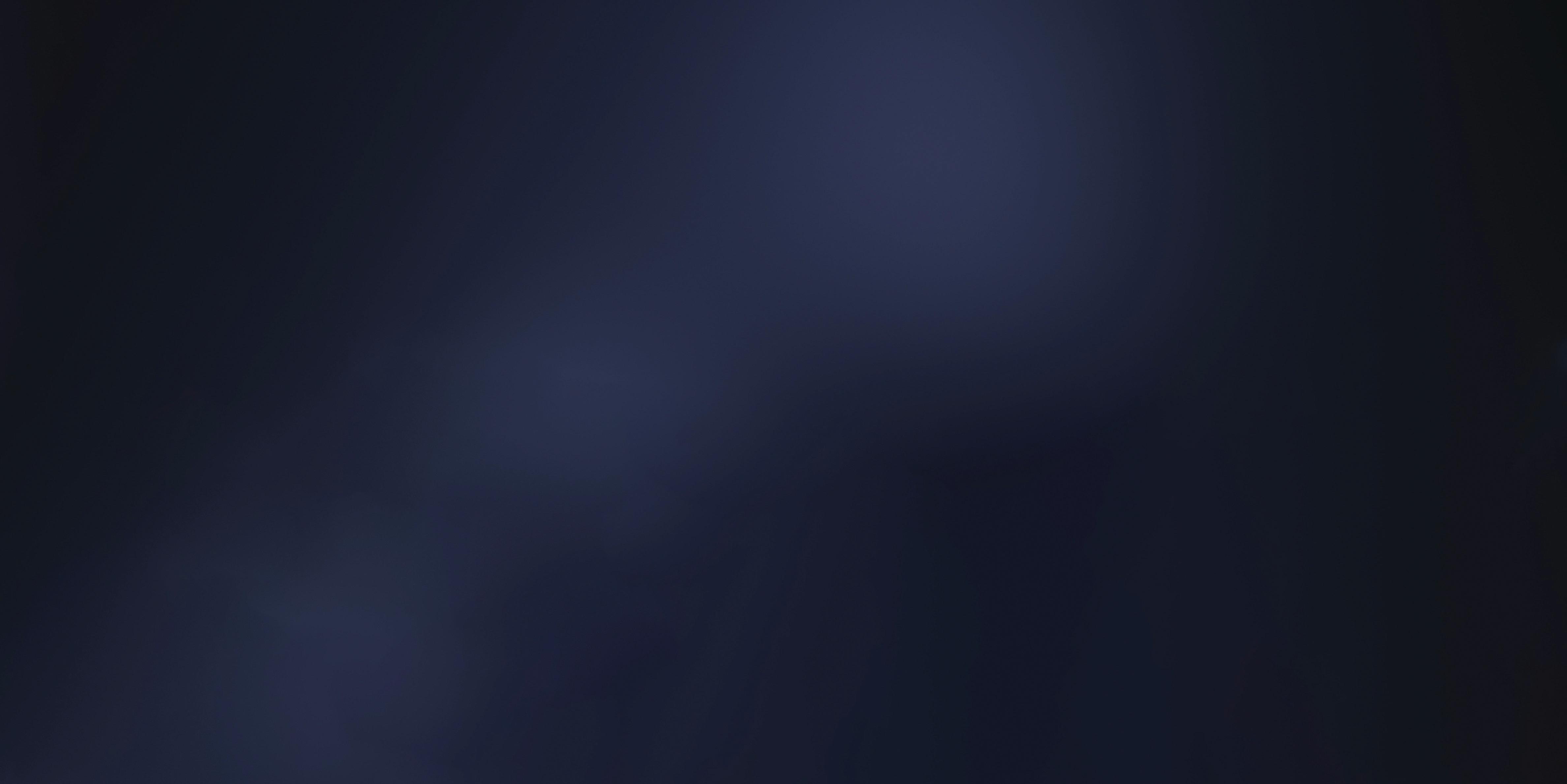
TCF CENTER. DETROIT.
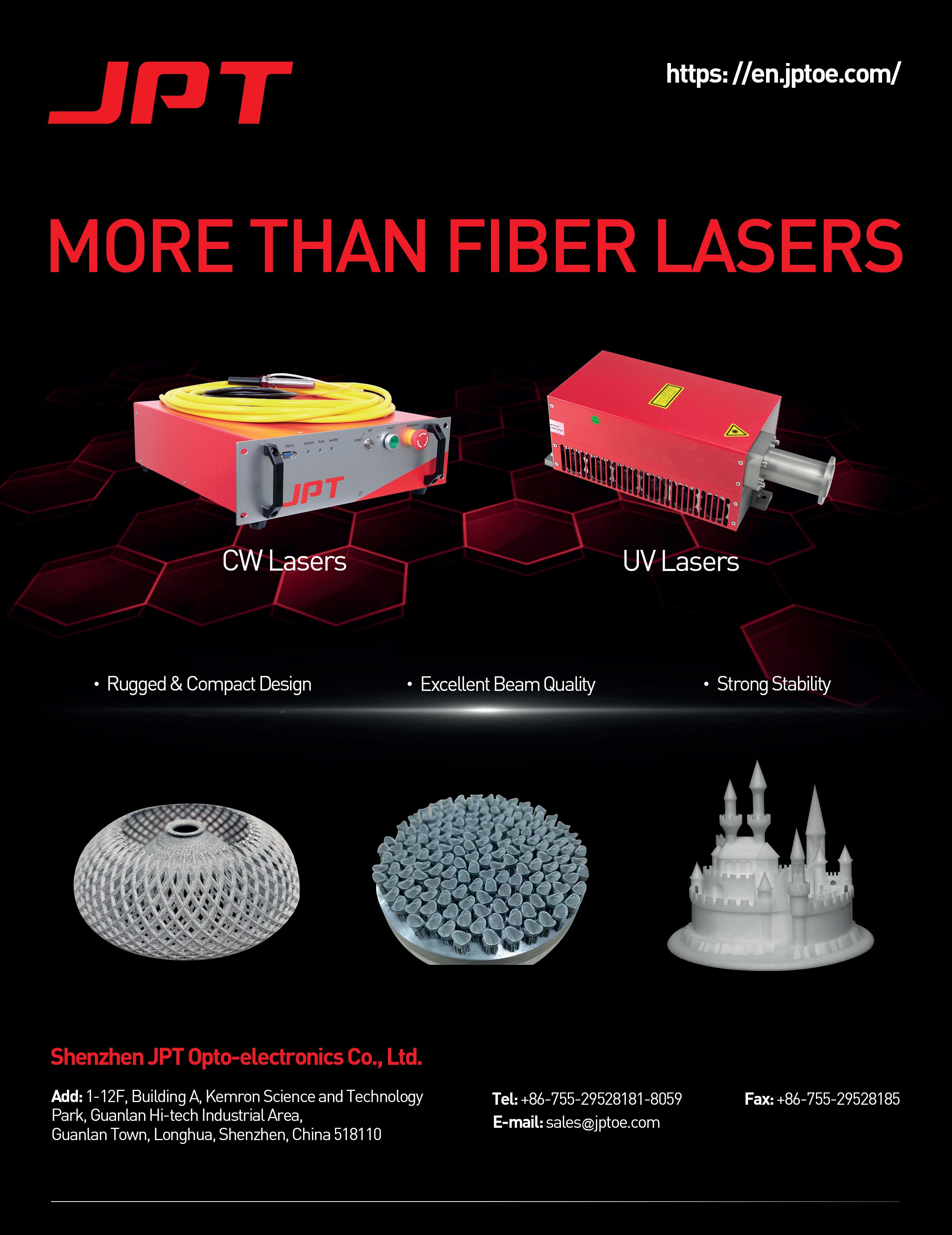