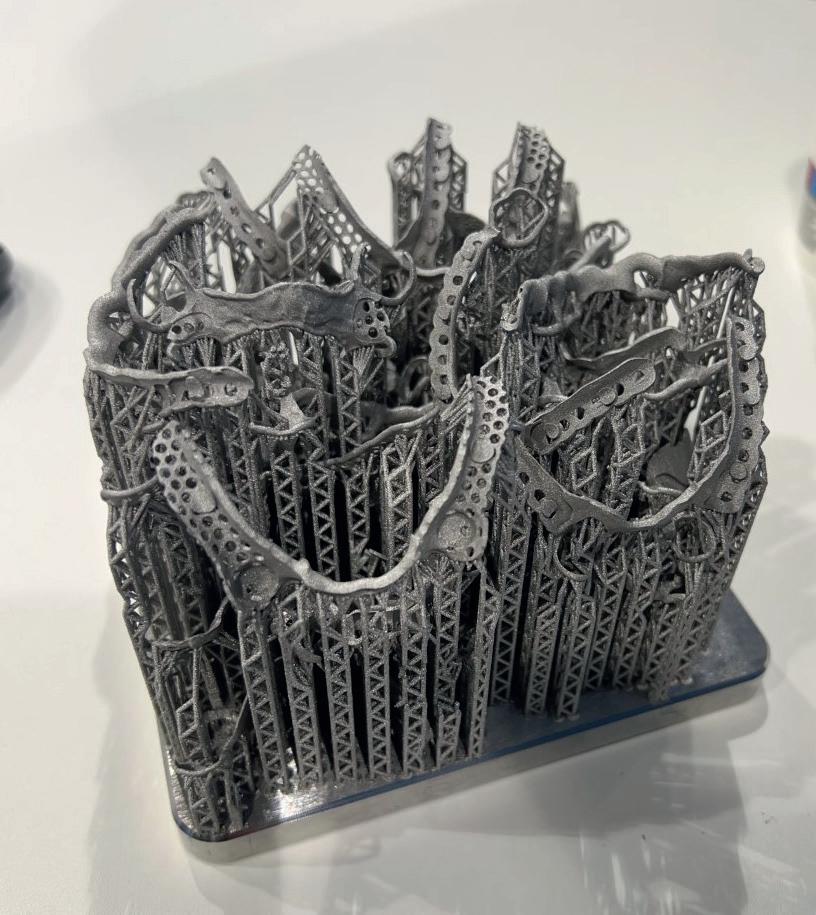
3 minute read
HEA IN THE CLOUD
The first time TCT met with Oqton’s Ben Schrauwen, the CEO and co-founder lamented the lack of communication between additive manufacturing (AM) hardware and software as the company set out to make its “vision of autonomous manufacturing” a reality. When we reconnect at Formnext this past November, four years have passed, and a lot, according to Schrauwen, has changed.
“That is really the future,” Schrauwen tells TCT, reflecting on the shift from loading files to printers via USB sticks to automatically pushing build jobs through cloud environments. “This is something that five years ago, everyone was still dreaming of. I think the time has really come and everyone is starting to understand that this gap needs to be closed. That's something we worked very hard on to make it possible.”
Despite being acquired by additive manufacturing pioneer 3D Systems in 2021, the manufacturing software solutions provider operates as a separate subsidiary and remains “totally neutral” to work with other industry vendors. Supported by a sturdy data firewall, Schrauwen lists collaborations with machine manufacturers like EOS, TRUMPF, and SLM Solutions, the latter of which recently added Oqton to its new software partner ecosystem in an effort to streamline and enhance its metal AM production processes through automation, integration and increased visibility.
That acquisition has, however, led to the unification of all of 3D Systems software offerings from its Geomagic reverse engineering portfolio to its 3DXpert build simulation software.
“We've really been combining all of the software solutions into a connected ecosystem where we can seamlessly go from scanning to build preparation, to production environments, in a very unified way,” Schrauwen explains.
One of the biggest takeaways Schrauwen points out during our conversation is a new feature in 3DXpert which integrates implicit surface-based design capabilities into build preparation, enabling surfaces to be fully blended and integrated with the existing solid modeling geometry. It’s a tool which Schrauwen describes as “very unique” to the industry and there are plenty of examples on the Oqton booth which demonstrate the impact of such new features.
“We are very focused on different verticals and delivering solutions specifically to these verticals,” Schrauwen says, handling a stacked metal build plate packed to the brim with dental implants. “One vertical where additive of course is very successful is dental and we have very unique solutions for the whole dental spectrum, everything from a small dental lab with one machine where we use
AI techniques to automate the build preparation, all the way to some of the largest clear aligner production facilities where we manage the complete process, everything from printing, vacuum forming, laser marking - it all gets run from Oqton at the center.”
Those large-scale production facilities are where Oqton stands to have significant impact, particularly those running multiple machines across multiple locations. Schrauwen says Oqton allows organizations to manage their operations from a single central database and ensure standardized processes across all facilities.
Harking back to that original ambition shared four years ago, Oqton’s cloudbased Manufacturing OS (MOS) was designed to accelerate scalable digital manufacturing. One component of that is artificial intelligence (AI), and as a former professor of machine learning, Schrauwen describes how Oqton is using AI to free up engineers from repetitive tasks like stacking builds plates and generating supports, and has developed a core set of vertical specific AI solutions that “work out of the box.” For Schrauwen, these are no longer future technologies. In fact, today, customers expect them.
“Machine efficiency ten years ago was 30% - this industry is not going to grow up with machines that are only operating 30% of the time,” Schrauwen says. “The goal is 90-plus percent, similar to other manufacturing equipment and people really start paying attention. If you buy a machine, by default, they want to have internet connected IoT so they are able to remotely monitor that everything is still operating. The same with the cloud. When Oqton started, people were very nervous about the cloud. Now it's become the norm, even some of the largest automotive OEMs, if you want to work with them, if it's not the cloud, it's an exception. So, there's been a total shift in the last five years since I started, and it's great that we were on the right side.”
Apanel of additive manufacturing (AM) software business leaders is sat silent as one voice dares to suggest what he believes many others are thinking. Minutes go by. And then, a passionate, frustrated monologue reaches its conclusion.
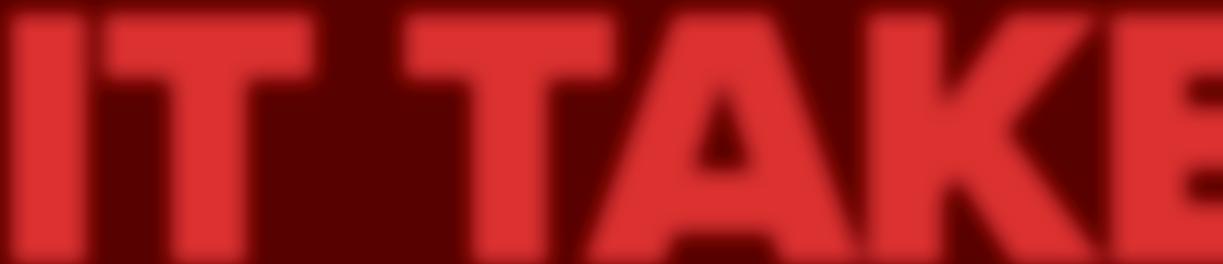
Some smirk, others nod, and one offers hushed applause. In front of more than 100 AMUG Conference delegates, Andre Wegner calls for his peers on the panel – which includes representatives of Materialise, AMFG and 3YOURMIND –to never pay an upfront fee to an original equipment manufacturer (OEM) for API access ever again.
Just like that, those in attendance have been made aware of a point of friction between MES providers and 3D printing hardware vendors. What’s more, a customer base has been introduced to the prospect of division when it is screaming out for collaboration.
At Formnext, Wegner, the Authentise CEO, elaborated on his position.
“A system like Authentise, workflow management in general, has two main objectives,” he explained. “One is [to] increase efficiency. So, we reduce the total cost of ownership [for] production. The second is that we capture the data and create a full digital thread, and therefore make it more reliable, and suitable to higher quality industries. Those two things mean we're helping OEMs sell more machines – we’re reducing the cost and we’re increasing the types of markets that they can [sell into].”