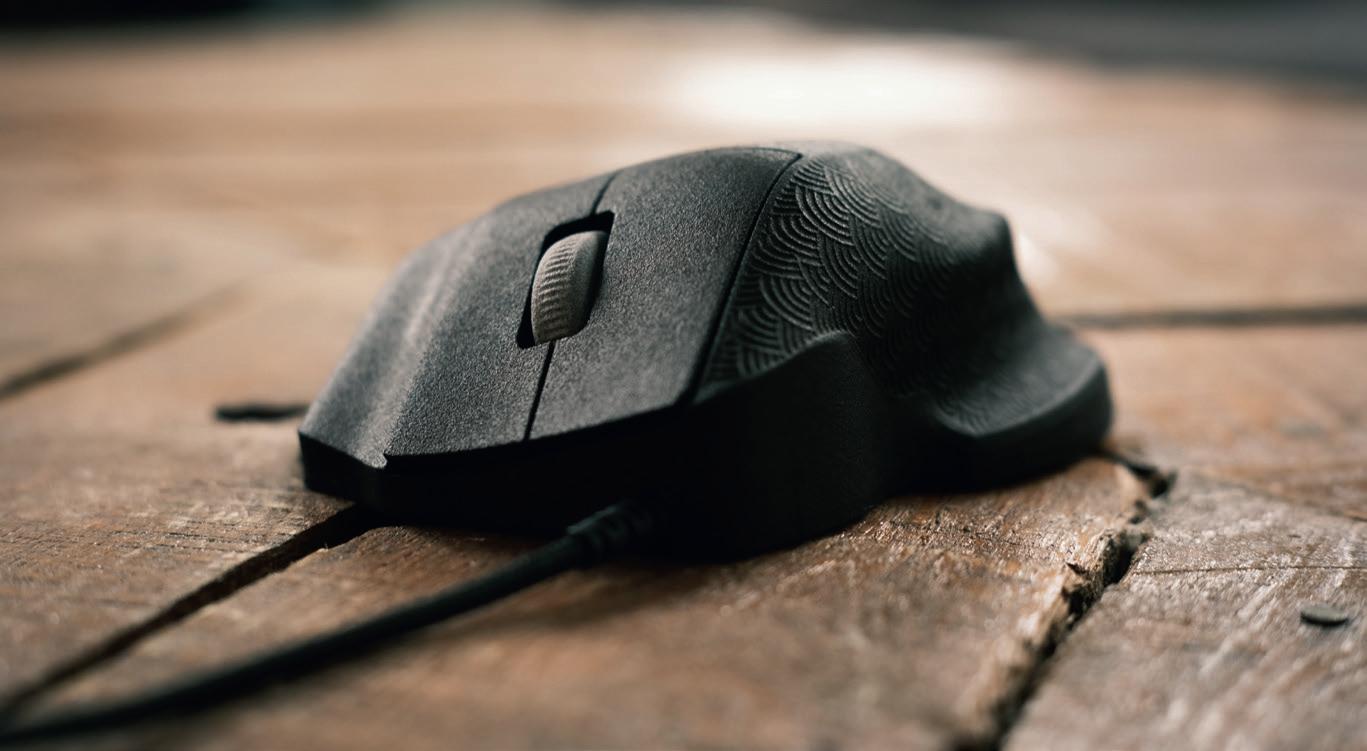
7 minute read
LET’S TALK AB UT STANDARDS
Laura Griffiths speaks to Amanda Allison at TWI on the progress being made in AM standardization and certification.
Standardization, certification, and qualification can pose significant challenges for additive manufacturing (AM). But, as Amanda Allison, Senior Technical Project Leader at TWI tells TCT, they’re also vital to ramping up adoption for critical end-use parts.
As a leading independent research and technology organization that has been providing knowledge and safety assurance in engineering, materials and joining technologies since 1946 - and the first organization in the UK to achieve a signed AM facility qualification from Lloyd's Register for the 3D printing of stainless steel parts by powder bed fusion laser beam - TWI perhaps knows better than most the hurdles around AM qualification processes.
“Ten years ago, the development of certification, qualification and standardization frameworks was minimal because of the low readiness of both technology and industry. There was also no priority placed on their development,” Allison said, reflecting on the changing AM standards landscape. “However, as the technology develops and more parts are being manufactured and put into service, there is an increasing pressure to focus and develop these frameworks to ensure the quality and safety of AM products.”
In 2015, TWI embarked on a joint industry project with Lloyd’s Register to explore the certification of metal AM components for industrial adoption in the energy and offshore sectors. As part of the collaboration, TWI worked with a number of Industrial Member organizations to test and certify demonstrator parts for AM production. From this, a set of industry relevant AM certification guidance notes for AM processes (powder bed fusion by laser, electron beam, directed energy deposition by laser, and Wire + Arc-based AM) were created.
“The development of standards is making it easier for industry to look to adopt the technology, but I think there is still a lack of confidence in some quarters because AM can be very disruptive and is moving rapidly. It also does not have a strong timeline of certified parts,” Allison said. “With a strong catalogue of standards, it does help give industry confidence in the use of the technology, and importantly, it standardizes the approach to the processes and procedures for implementation, regardless of who is using the AM technology."
Allison continued: “We also see a lot more examples of international standards committees collaborating together, which helps eliminate duplication and maximize resources. This is particularly important because the landscape is so huge, involving a vast number of stakeholders across multiple industrial sectors. Bringing expertise and knowledge together to harmonize the approach is something that I've seen develop quite rapidly in more recent years, and something I encourage.”
Allison points to the work of ASTM (which published the first AM standard in 2009) and the ISO committees which have been instrumental in the development of standards for AM processes. However, barriers and gaps remain: the need to avoid repeat testing for parts that might only have small design differences; standards that can support qualifying different AM systems; or the implementation of digital qualification and certification.
“AM part certification can be quite costly and it can also be a difficult journey, particularly when trying to navigate the AM standards and certification landscape alongside trying to link up with existing industrial sector standards,” Allison explained. “I also think, for facility qualification, the development and use of digital workflows is paramount in order to reliably track all process steps that parts undertake, and to monitor and control progress to ensure alignment with procedures.”
While awareness around AM frameworks is growing, an understanding of the various steps and considerations along the AM value chain takes time and education. According to Allison, "when it comes to investing in AM, certification can often fall last on the list of priorities."
“This can lead to problems further down the line,” Allison said. “For me, certification starts at the design stage. Organizations need to be looking into the requirements for certification at the beginning because it can have strong implications on the AM process chain.”
As AM adoption accelerates, part volumes increase, and the promise of distributed manufacturing materialises, frameworks must be in place to support such ambitions.
“The key is dissecting requirements in a methodical manner and understanding how you work through all the process steps to achieve part certification,” Allision added.
“At the moment, the certification journey is part-focused, and it is challenging to certify a family of similar parts. Having a means to standardize the process more rapidly, whilst providing confidence in the quality, safety and performance of parts, would help to advance the uptake of AM for industry.”
Formify, a start-up based out of the tech scene in Toronto, Canada, is attempting to change the future of esports through 3D printing. The company offers parametrically designed 3D printed gaming mice that are designed specifically for each user, with the customer simply sending over a photo of their hand, which Formify then uses to analyze and collect measurements, before printing the bespoke product.
Co-Founders Will MacLaughlin, Alexander Chapman, Luke Morabito, Kenny MacLaughlin and Gianpaolo Pittis, each with their own expertise in different areas, started the company during the Covid-19 pandemic when they spotted a gap in the market for custom gaming peripherals.
Speaking to TCT, MacLaughlin said: “We were getting pretty into gaming at that time, and were looking at a lot of the different peripheral options that were available. One of the items we saw was the Azeron game pad, which was actually a 3D printed game pad. We thought, why aren’t they doing it parametric and making it bespoke for everyone? If you’re 3D printing it, mass customization is super easy, there’s just a really hard software problem. That’s the problem we set out to solve.”
MacLaughlin gave TCT the elevator pitch for the product, which included the line: “We think it’s ridiculous that in something as competitive as gaming, that everyone is using the same size chunk of plastic.”
Gamers in esports competitions are now often competing for millions in prize money, and Formify thinks that in such a competitive setting, they should have custom peripherals to give them the chance to perform at the highest level.
The software platform developed by Formify works by taking an image of the customer’s hand against an 11 by 8.5 inch piece of paper, which it analyzes to get the dimensions of the hand, the details of the bone structure and joint structure. This information is then put into a tech stack, which gives them a clean data set of the hand with a masking image.
The next step involves putting the data into an automation software which builds the full custom mesh of the mouse and adapts the parametric mechanical aspects that are needed to make it work. From that point, the design is exported in an STL file which can be sliced, and 3D printed. Formify uses multi-jet fusion (MJF) technology to print its products, which MacLaughlin said is the most compatible method to use with the file type. The final products can weigh as little as 55 grams depending on hand size, without sacrificing strength.
MacLaughlin told TCT about the process of deciding on the correct 3D printing technology to use for the Formify products: “We tried about every single one, and none of them went well. We do still use FDM for shape samples and optimization, we’ll use it to try out how different shapes feel. But FDM didn’t have the quality that we were looking for, even at really low layer heights. Then we tried SLA, but with SLA there is a bit of a balancing scale where if you need complete biocompatibility, you have to sacrifice some mechanical qualities, and if you need really good mechanical qualities then you sacrifice some biocompatibility, then you need to try and get the surface finish which can turn into a whole mess.
“So we made some failed prototypes with SLA, and eventually we tried SLS which we were quite happy with, especially with a vapor finish, but we found in the end it was more cost effective and even gave a less porous finish when using MJF, so that’s what we settled on.”
Formify typically uses 3D printing marketplace Hubs to manufacture the products. The relationship began when Formify was using Hubs for one off manufacturing, and one of the production managers at the company reached out about the idea.
“They’ve been really helpful with design, they’ve given us design tips and feedback. And it’s a really great automated software. So, you can upload an STL and that’s pretty much it. You click one button and it’s at your house in a couple of weeks, which is pretty powerful,” added MacLaughlin.
Speaking about what the future holds for Formify, MacLaughlin said that the company hopes to launch its crowdfunding campaign at some point in 2023, as well as looking into developing other types of gaming peripherals, such as custom keyboards.
MacLaughlin said: “We’ve taken a look at some other products. We’ve talked about keyboards, but there’s a different set of challenges that come with keyboards, as the switch location would essentially need to be wired as typically keyboards are just one PCB, and its very hard to parametrically design PCBs.”
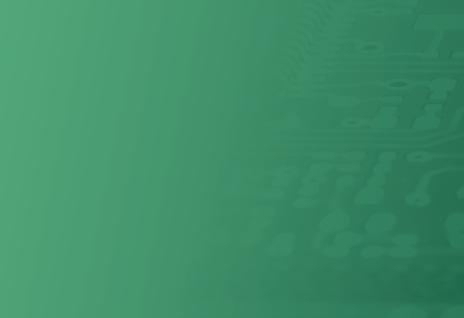
The main focus for the company for the time being is the gaming mice, with MacLaughlin saying that the team is working on optimizing to get the best performance and cutting down ‘target acquisition time’ for gamers, as well as increasing their comfort. MacLaughlin said that the company has made leaps in the past few months with the lightweighting aspect of the Formify products.
MacLaughlin, who oversees Management and Software Development for Formify, has a background in Aerospace Engineering, studying at Ryerson University. Alexander Chapman is the head of Operations and Business Development, with a bachelor’s degree in commerce, specializing in Global Management, also from Ryerson University. Fellow co-founder Luke Morabito heads up the Technical Development and Marketing and has an Honours Mechatronics Engineering qualification from the University of Waterloo, with previous product development experience at
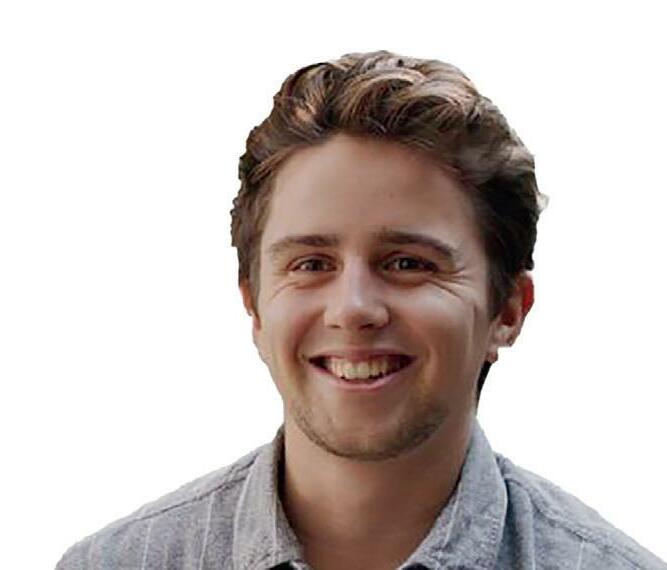
Waterloo Formula Electric and Tesla. Kenny MacLaughlin is responsible for Marketing and Design at Formify and received a bachelor’s degree in Film and Media from Humber College. He has previously worked for the Toronto Raptors. Gianpaolo Pittis works in Technical and Software Development at the company and has an Honours Mechanical Engineering qualification from the University of Waterloo, and previously worked in Data and Failure Analysis at Apple.
Formify says that when competitors in esports are using the same size mouse, they are leaving performance and comfort on the table, and that’s where its product comes in.
3D Printing
• Designed for PBF (powder bed fusion) metal 3D printing
• Parts printed on the 3D-EZ-Release™ print plate can be released in seconds
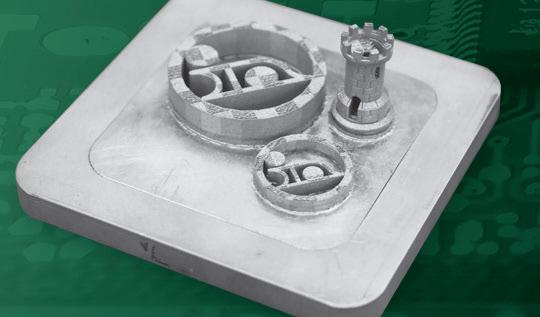
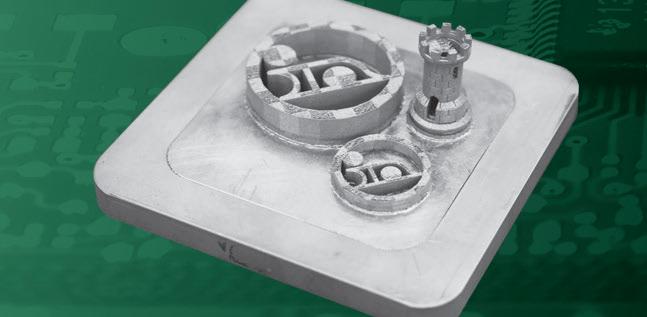
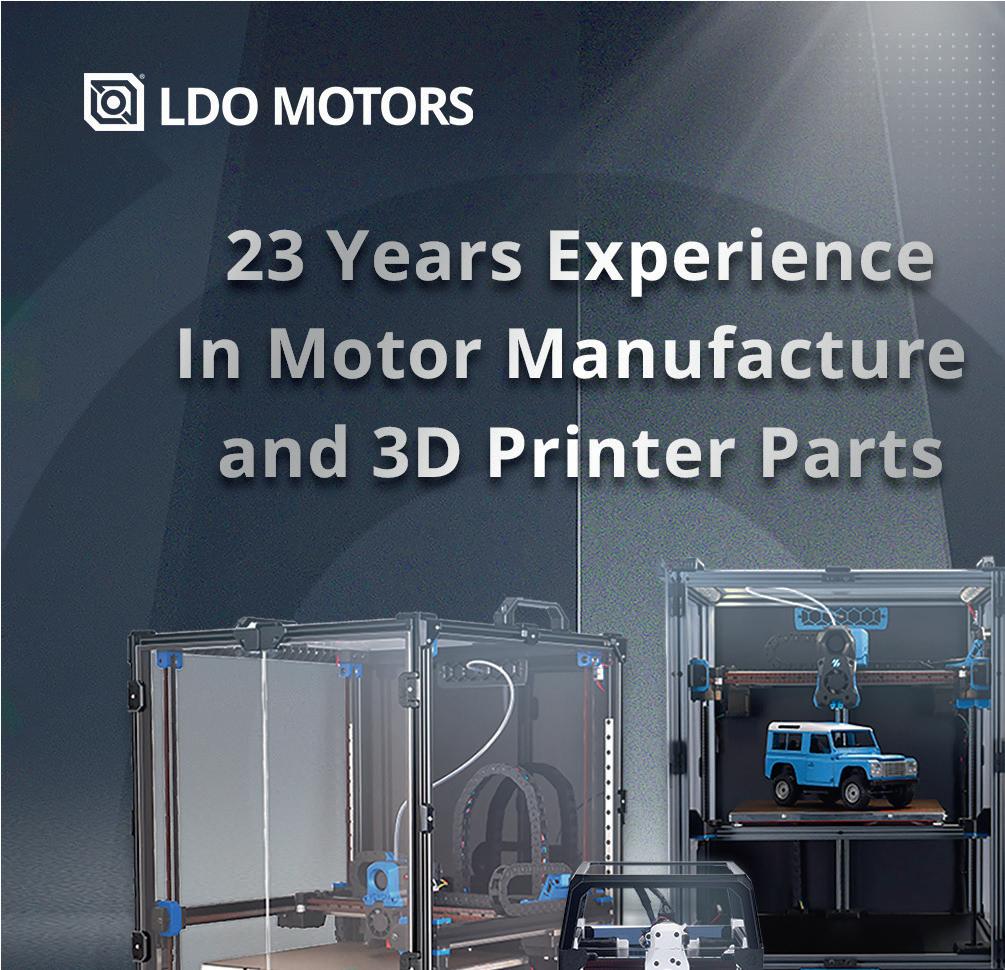
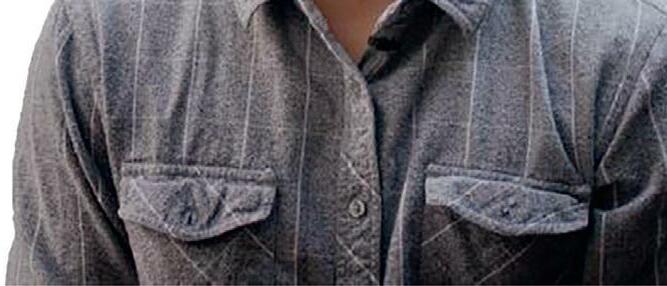
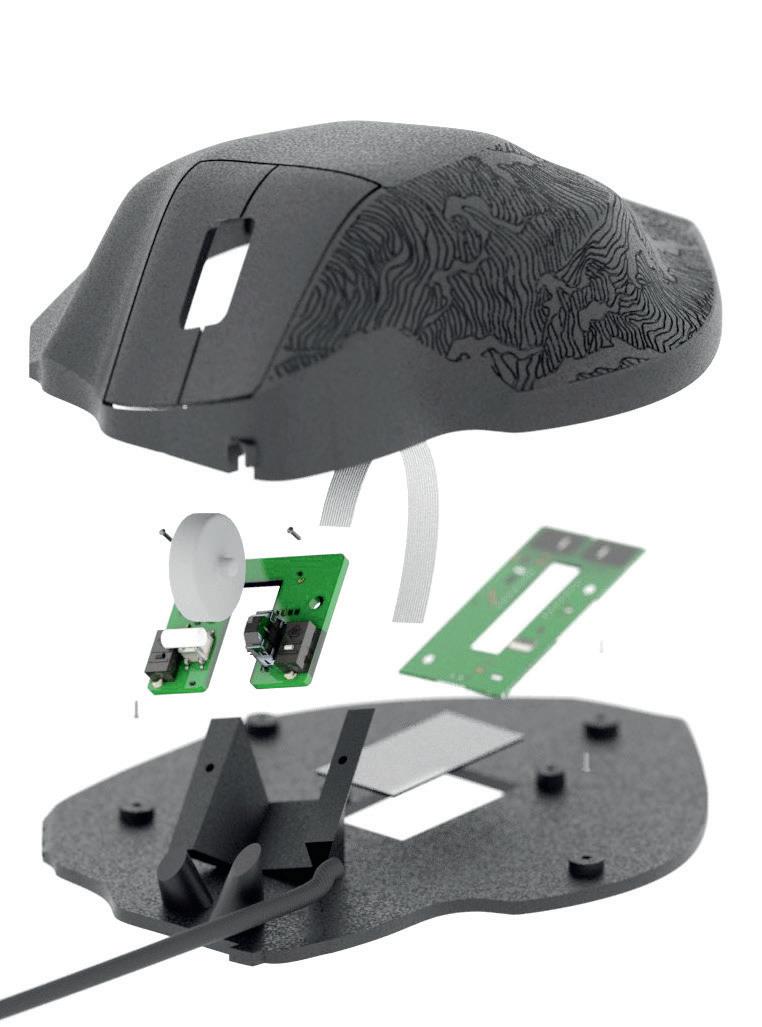
• No EDM wire or other cutting saw is needed to remove the printed parts from the build plate

• Separation is achieved by heating on a hot plate, or in a standard oven set to 200°C
• Current 3D-EZ-Release plate size is 3.5" – larger sizes are in development
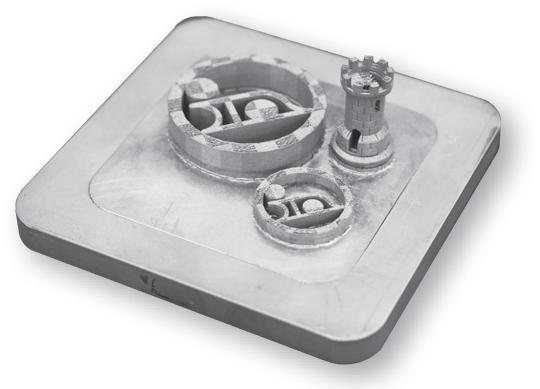
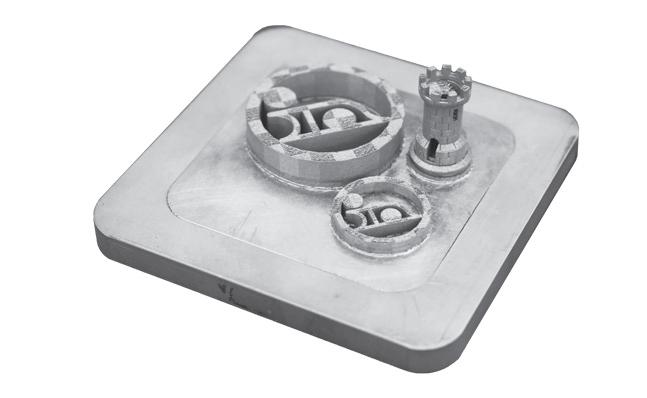
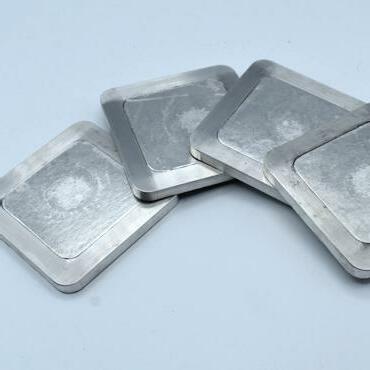