BUYERS GUIDE 2025
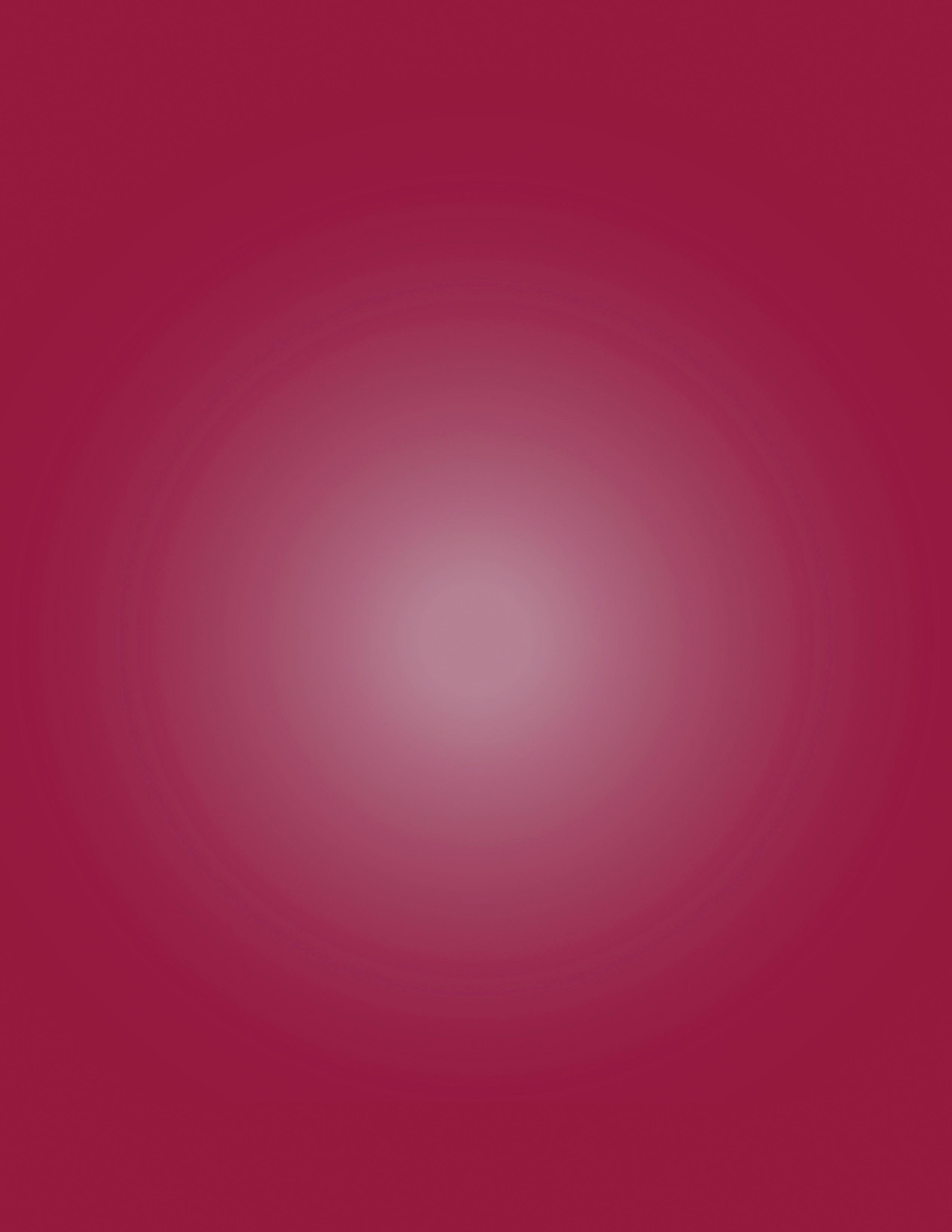
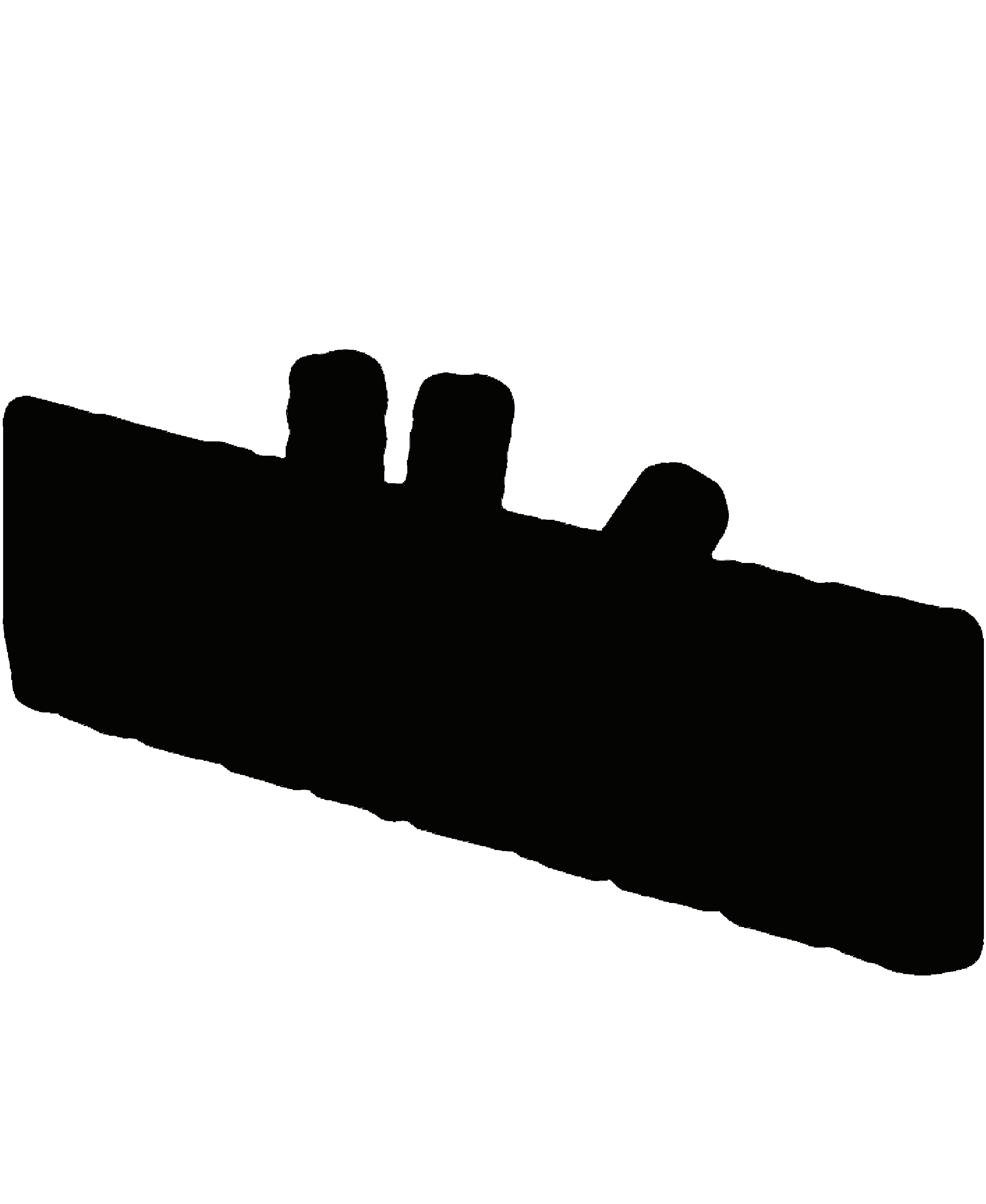
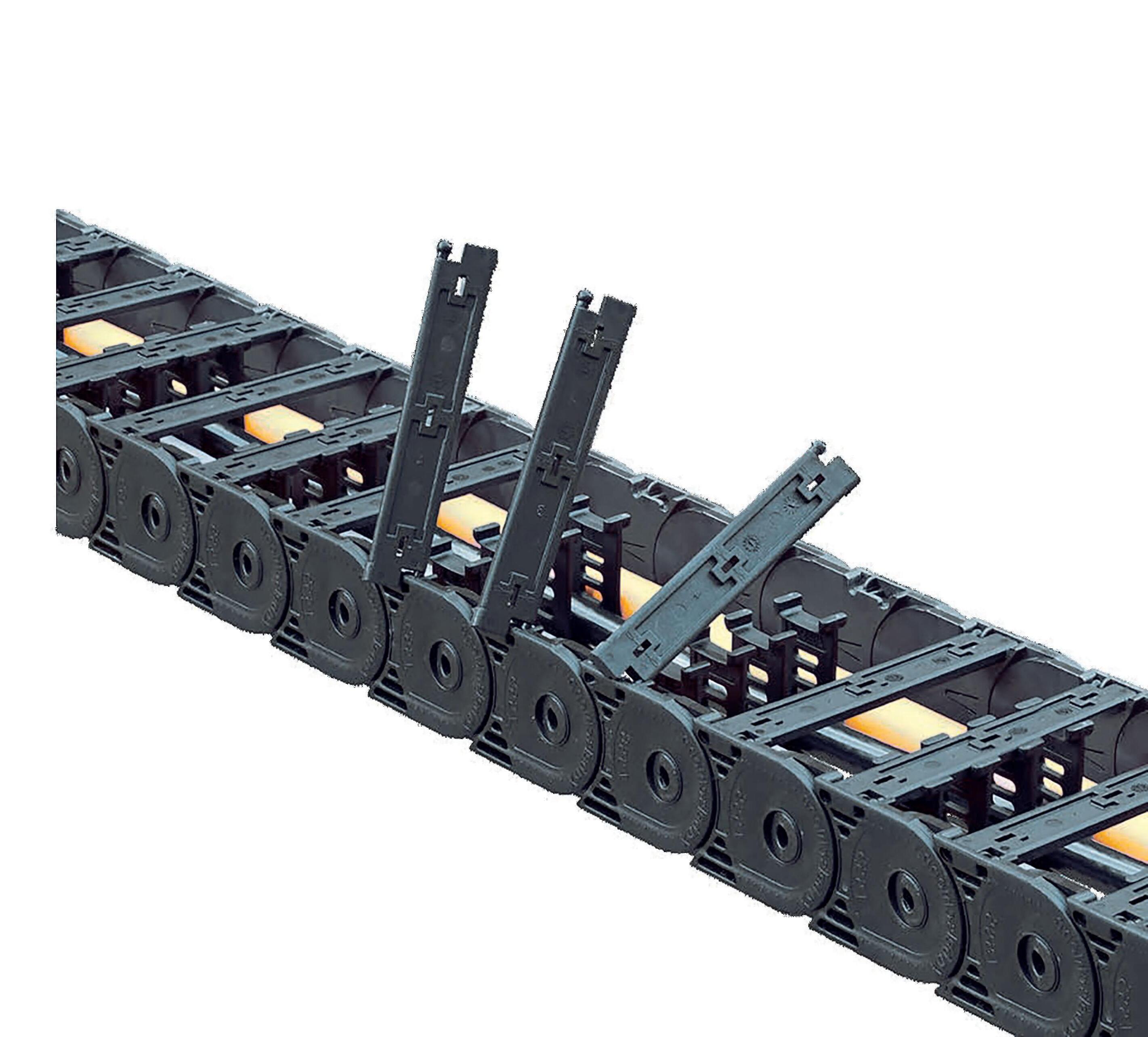
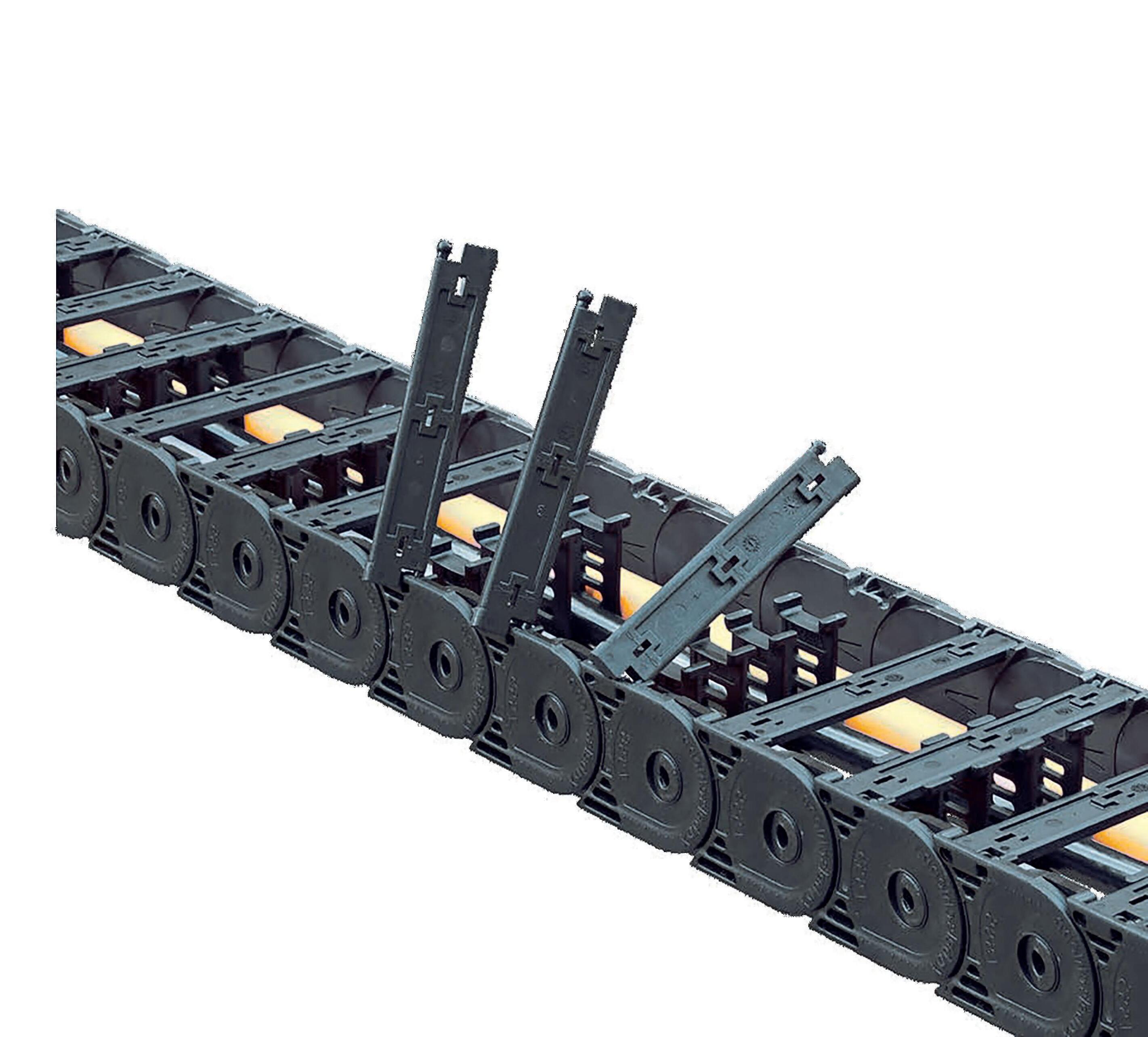
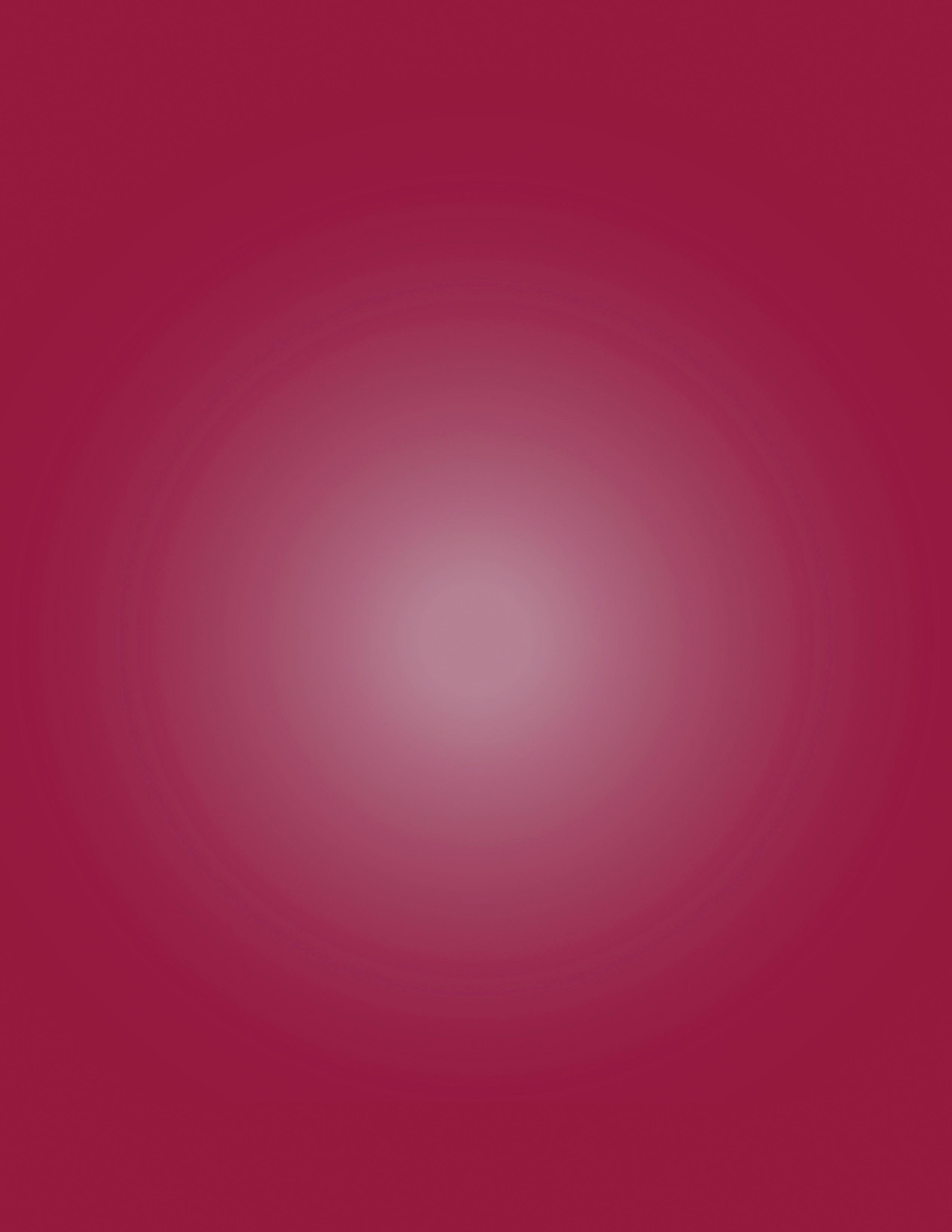
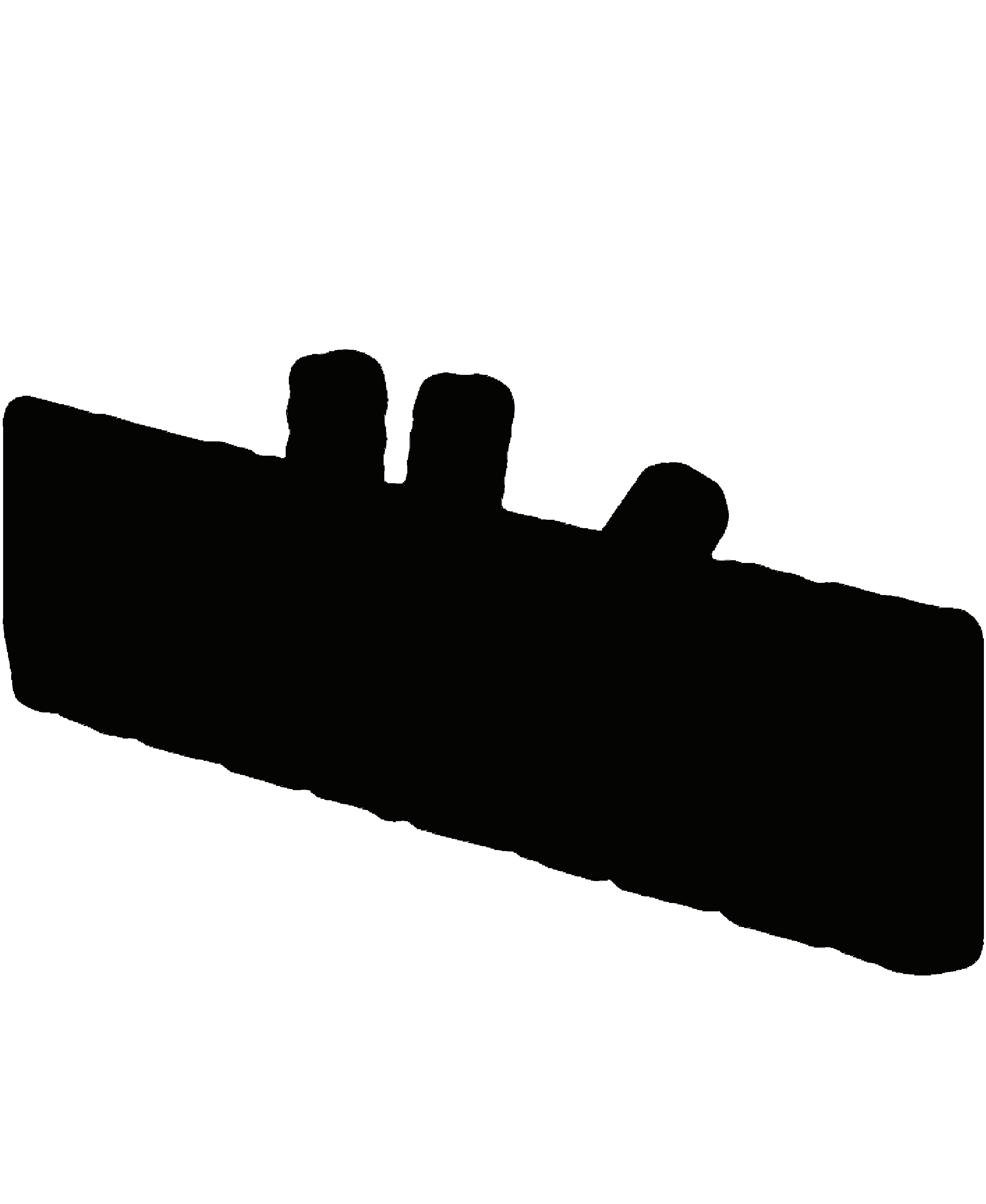
Hello and welcome to the 2025 TCT Buyers’ Guide.
Having just returned from an additive manufacturing trade (AM) show, it occurred to me once again how difficult such events must be for attendees as they look to identify their next – or first – AM investment.
AM technologies are varied in their material feedstock, printing processes, post-processing requirements; in the size of machinery and their purpose too. Finding the right technology for your business case, then, is no mean feat.
To step onto a trade show floor or into an OEM showroom can therefore be daunting. Hit with an overwhelming amount of information – and a side of salesperson persuasion – your note-taking hand will barely be able to keep up.
That, of course, is only one step of the decisionmaking process. Hours can be spent surfing the net and in meetings with decision makers before you reach out to the OEM.
To help you streamline that process, we have collated an array of leading 3D printing and postprocessing hardware – complete with their key specifications, features and capabilities – in this year’s Buyers’ Guide. This includes the size of the machinery, the volume of the build envelope, the speeds and precision the technologies can deliver, and the materials they can process.
We don’t expect that, having flicked through these pages, you’ll be immediately ready to make your next AM investment. But you will have narrowed your search, filtered out what won’t work for your business, and armed yourself with the right questions to ask as you engage with the relevant OEMs.
It will expedite what can be an arduous effort to find the right technology for your applications. So, dive in and see what you find!
SAM DAVIES GROUP CONTENT MANAGER
UNIQUE DETAIL RESOLUTION AND HIGHEST PROCESS ACCURACY
The DMP 7x is a Micro Laser Sintering machine of the newest generation from 3D MicroPrint. Our machines deliver best results in terms of detail resolution, accuracy and surface finish for 3D printed micro metal parts by our micro laser sintering process. With this it is able to manufacture high precision micro parts from micro scaled powder. This machine solution merge the abilities of micro manufacturing with the advantages of 3D-printing for the first time. Inspired by and made for Industry our machines
satisfy a broad bandwidth of user requirements. Low running costs, availability of industrial standards like zero-point-clamping system, inert gas atmosphere including gas cleaning and remote service support ensure best technical and commercial results. The machine comes with the latest CAD-workstation for data preparation. Intuitive software and hardware assures an immediate readiness for use, directly after commissioning and training.
Stainless steel, Inconel® 718, Tungsten, Titanium, Copper, Precious metals
3D MicroPrint GmbH manufactures high precision micro metal components by using Micro Laser Sinter technology. Since the company was founded in 2013, the additive manufacturing process for micro parts has been further developed and adapted for industrial production. Today, we offer our
• Minimum wall thickness: 30 μm
• Ra: 2 - 3 μm (as-built)
• Part density: > 99.5 %
customers the entire portfolio from design consulting for additive manufacturing, feasibility studies and part production to our own 3D MicroPrint Micro Laser Sintering system. In addition, 3D MicroPrint offers material development for exclusive technologies upon request.
DMP MACHINE 7X
• IR Fiber Laser 50 / 200 W
• Laser spot size ≤ 30 µm
• Optical accuracy 5 µm
• Layer thickness 1 µm to 15 µm
• Purified Argon atmosphere
• Integrated vacuum cleaner
• Powder containment
• Air locks and rapid transfer ports
• Zero-point clamping system
More than 35 years ago, 3D Systems brought the innovation of 3D printing to the manufacturing industry. Today, as the leading additive manufacturing solutions partner, we bring innovation, performance, and reliability to every interaction — empowering our customers to create products and business models never before possible. Thanks to our unique offering of hardware, software, materials, and services, each applicationspecific solution is powered by the expertise of our application engineers who collaborate with customers to transform how they deliver their products and services.
3D Systems’ solutions address a variety of advanced applications in healthcare and industrial markets such as medical and dental, aerospace & defense, automotive, and durable goods.
Figure 4™ Standalone 3D Printer
426 x 489 x 971 mm
124.8 x 70.2 x 196 mm
Figure 4™ Modular 3D Printer Configuration dependent 124.8 x 70.2 x 346 mm
Figure 4™ Production 3D Printer
NextDent™ 5100 Dental 3D Printer
dependent 124.8 x 70.2 x 346 mm
x 489 x
x
ProJet® MJP 2500 Plus Plastic 3D Printer 1120 x 740 x 1070 mm 295 x 211 x 142 mm
x
Tough-GRY 10, Tough-GRY 15, Eggshell-AMB 10
Flex-BLK 20, Hi-Temp 150C FR Black, Hi-Temp 300 AMB, JCast-GRN 20, Jewel Master GRY, Med-AMB 10, Med-WHT 10, PRO-BLK 10, Rigid Gray, Rigid White, Rubber-65A BLK, Rubber-BLK 10 Tough 60C White, Tough 65C Black, Tough 75C FR Black, Tough-BLK 20, Tough Clear, Tough FR V0 Black, Rigid Composite White
Tough-GRY 10, Tough-GRY 15, Eggshell-AMB 10. Flex-BLK 20, Hi-Temp 150C FR Black, Hi-Temp 300 AMB, JCast-GRN 20, Jewel Master GRY, Med-AMB 10, Med-WHT 10, PRO-BLK 10, Rigid Gray, Rigid White, Rubber-65A BLK, Rubber-BLK 10, Tough 60C White, Tough 65C Black, Tough 75C FR Black Tough-BLK 20, Tough Clear, Tough FR V0 Black, Rigid Composite White
Tough-GRY 10, Tough-GRY 15, Eggshell-AMB 10, Flex-BLK 20, Hi-Temp 150C FR Black, Hi-Temp 300 AMB, JCast-GRN 20, Jewel Master GRY, Med-AMB 10, Med-WHT 10, PRO-BLK 10, Rigid Gray, Rigid White, Rubber-65A BLK, Rubber-BLK 10, Tough 60C White, Tough 65C Black, Tough 75C FR Black. Tough-BLK 20, Tough Clear, Tough FR V0 Black
ProJet® MJP 2500W RealWax™ 3D Printer
x
x
ProJet® MJP 2500 IC
3D Printer 1120 x 740 x 1070 mm 294 x 211 x 144 mm
VisiJet ProFlex M2G-DUR, VisiJet Armor Max M2G-JF engineering plastics VisiJet Crystal M2P-CST, VisiJet M2R-WT, M2R-BK, M2R-CL, M2R-GRY, M2R-TN, M2S-HT90, M2S-HT250 rigid plastics VisiJet M2 EBK, M2 ENT, M2E-BK70 elastomeric materials Melt away support
VisiJet® M2 CAST - wax material
VisiJet® Wax Jewel Red
VisiJet® Wax Jewel Ruby
VisiJet® M2 Cast
VisiJet® Wax Jewel Red VisiJet® Wax Jewel Ruby
VisiJet® M2 ICast -
ABS, ASA, PETG, PLA, PP, TPE 25 Shore A, TPU 40 Shore A, TPU 85 Shore A, ABS CF10, ABS CF20, PP CF15, PP GF30, PC CF20, Nylon CF5, Nylon CF10, Nylon CF35, PEI CF20, PEI GF20, PEKK GF30, and more
x
x
EXT 1270 Titan Pellet
x 3048mm x 3048mm
x 1270mm x 1829mm
ABS, ASA, PETG, PLA, PP, TPE 25 Shore A, TPU 40 Shore A, TPU 85 Shore A, ABS CF10, ABS CF20, PP CF15, PP GF30, PC CF20, Nylon CF5, Nylon CF10, Nylon CF35, PEI CF20, PEI GF20, PEKK GF30, and more
6.0mm
-
to 14kg/ hour (with
ABS, ASA, PETG, PLA, PP, TPE 25 Shore A, TPU 40 Shore A, TPU 85 Shore A, ABS CF10, ABS CF20, PP CF15, PP GF30, PC CF20, Nylon CF5, Nylon CF10, Nylon CF35, PEI CF20, PEI GF20, PEKK GF30, and more
- 6mm
(with 9mm nozzle)
270 710 x 730 x 1830 mm 242 x 265 x 300 mm
ProJet® MJP 5600 Multi-Material 3D Printer 1700 x 900 x 1620 mm 518 x 381 x 300 mm
ProJet® 7000 HD SLA 3D Printer 984 x 854 x 1829 mm Up to 380 x 380 x 250 mm
PRO BLK 10, Rigid Gray, Rigid White, FLX BLK 20, Tough FR VO BLK, Rigid Composite White, Tough 60C White, Model Ortho Orange, HT 300 AMB Eggshell AMB 10
to 150 microns (material dependent) Up to 38mm per hr. (material dependent)
VisiJet® CR-CL 200, CR-WT 200, CR-BK; CE-BK, CE-NT Composite Multi-Material Printing 13μ to 16μ
Accura 25, Accura ABS Black, Accura AMX Durable Natural, Accura AMX High Temp 300C, Accura AMX Rigid Black, Accura AMX Tough FR V0 Black, Accura CastPro, Accura ClearVue, Accura Fidelity, Accura Phoenix, Accura Sapphire. Accura Xtreme, Accura Xtreme White 200
SLA 750 and SLA 750 Dual 1370 x 1539 x 2255 mm 750 x 750 x 550 mm
ProX® 950 SLA 3D Printer 2200 x 1600 x 2260 mm
x
x 550 mm
Accura 25, Accura 55, Accura 60, Accura ABS Black, Accura AMX Durable Natural, Accura AMX High Temp 300C, Accura AMX Rigid Black, Accura AMX Tough FR V0 Black, Accura Bluestone, Accura CastPro, Accura ClearVue, Accura Composite PIV, Accura Fidelity, Accura HPC, Accura PEAK, Accura Xtreme, Accura Xtreme White 200, Accura AMX Rigid Composite White
0.050 to 0.125 mm
Accura® plastics and composites (widest range, simulating ABS, PP and PC, high temp., for casting patterns and other specialty materials)
DuraForm ProX PA, DuraForm PA12 Black, DuraForm PA11 Natural, DuraForm PA11 Black, DuraForm PA CF, DuraForm PAx Natural, DuraForm PAx Black, DuraForm ProX HST, DuraForm ProX GF, DuraForm TPU 90A, DuraForm FR-106 0.08 to 0.15 mm sPro™
DuraForm® plastics and composites (powders)
DMP Flex 200 Metal 3D Printer
x
x 1950 mm
x
x
DMP Flex 350 and DMP Factory 350 Metal 3D Printers Model dependent 275 x 275 x 420 mm
Ready-to-run LaserForm CoCr (B), Ti Gr.23 (A), Ti Gr.5 (A) and 316L (B) with extensively developed print parameters. Custom material parameter development available with optional software package.
μm - 120 μm. Preset: 30 μm
Wide choice of ready-to-run metal alloys with extensively developed print parameters, including LaserForm Ti Gr. 1 (A), Gr.5 (A) and Gr.23 (A), CoCrF75 (A), 316L (A), 17-4 (A), Ni718 (A), Ni625 (A), AlSi10Mg (A), AlSi7Mg0.6 (A) and Maraging Steel (A). as well as Certified CuCr2.4 (A), CuCr1Zr (A), HX (A), CuNi30 (A), GRCop-42 (A), M789 (A), A6061-Ram2 (A) and Tungsten (A). Custom material parameter development available with optional software package. in build speed section for the 350, add comment: Dependent on number of lasers
DMP Factory 500 Metal 3D Printer
Configuration dependent 500 x 500 x 500 mm
LaserForm materials Ti Gr.23 , Ni718, HX
Adjustable, min. 2 μm, max.200 μm, typ. 60-120 μm
With over 80 years of cross-industry knowhow, Rösler is among the worldwide leading suppliers of innovative solutions in the field of surface finishing. In recent years, we have been increasingly dealing with requests for the surface finishing of 3D printed parts. In this sense, we have concluded quickly that, compared to traditional manufacturing processes, additive manufacturing poses entirely new challenges for post processing. Often, these are still solved manually, but this has a negative impact on costeffectiveness and reproducibility.
To meet these requirements in the best possible way, we founded the brand AM Solutions - 3D post processing technology, which will be responsible for developing and offering tailormade equipment, process technologies, and consumables for the automated post processing of 3D printed components. Regardless of material, printing process or production volume, we will find the best quality and most economical solution for your post processing requirements. For this purpose, we also gladly advise you already during the design phase of your parts.
WE OFFER TAILORED EQUIPMENT FOR:
• Unpacking of work pieces
• Removal of support structures
• Removal of loose and sintered powder from the component surface
• Smoothing and cleaning of internal passages
• Surface cleaning
• Surface homogenization, surface grinding & smoothing and (high gloss) polishing
• Surface preparation for subsequent manufacturing steps, e.g. coating and painting
AS QUALIFIED PARTNER WE OFFER:
• Decades of experience in the processing and finishing of surfaces for a wide range of industries
• Broad portfolio of machines for surface processing/finishing specially developed and adapted for AM
• Individually adapted process development for every workpiece and every process step
• > 80,000 m2 production and development at the German site
• > 400 m2 Customer Experience Center at the German site
• Many years of experience in automation / process interlinking
• Competent after sales support and worldwide subsidiaries as direct local contacts
ABOVE: S1: The smart multi-talent for cleaning, smoothing, and homogenizing
LEFT: C1 Max: Designed for the efficient cleaning of 3D printed SLA parts up to 750 x 750 x 550 mm (W x D x H)
SELECTION FROM OUR PRODUCT PORTFOLIO:
Additionally we offer a range of equipment and services provided by our commercial partners.
RIGHT: 400 sqm state-ofthe-art Customer Experience Center at our German site
LEFT: AM Solutions – 3D post processing technology, a brand of the Rösler Group, at the German site with > 80,000 sqm production and development area
AON3D’s new platform leverages artificial intelligence, hardware automation, and in-process monitoring to deliver quality-verified parts, up to 85% stronger, with just a few clicks.
Founded in 2015, AON3D is a North American manufacturer of Industrial 3D Printers and software, whose solutions drive innovation for hundreds of businesses in 25+ countries worldwide, ranging from small businesses to multinational Fortune 500 companies.
Print PEEK, PEKK, ULTEMTM, and open market materials — larger, faster, stronger, and easier.
AON3D HyloTM, one of the largest and fastest high temperature industrial 3D printers on the market, combines end-to-end automation and in-process monitoring to deliver new levels of part performance, reliably and repeatably.
AON3D BasisTM, Hylo’s accompanying additive software, leverages AI to run ultra-fast thermal simulations, emulating the 3D printing process, and integrating polymer physics into the slicing process to create geometry- and materialspecific print settings, mm by mm — maximizing part quality, performance, and throughput.
In addition, Basis unlocks new methods of nondestructive part examination. By consolidating Hylo’s sensor data into digital twins, users can identify hidden defects and verify printed part quality in real-time.
Open Material – ABS, ASA, Nylon (PA 6, 6/66, 12), PAEK, PC, PEBA, PEEK, PEI (ULTEM™ 9085, 1010), TPI, PEKK, PETG, PLA, POM, PP, PPSU, PSU, PVDF, TPE, TPU, and more.
Plus, Carbon fiber, glass fiber, Kevlar®, and ESD safe variants of the above.
Step 1: Simulate & Optimze
Basis simulates the 3D printing process and creates dynamic print settings, mm by mm, to maximize part properties and minimize potential defects.
Step 2: Print
Hylo’s automation and advanced process control ensure accurate and repeatable results.
Step 3: Qualify
Digital twins created from Hylo’s sensor data enable real-time hidden defect detection and part quality verification.
The German family-owned company ARBURG is one of the world‘s leading manufacturers of plastic processing machines. ARBURGadditive was founded in 2021 in order to bundle together activities in the additive manufacturing area. The product portfolio comprises the freeformers from ARBURG and the 3D-printers from innovatiQ, an ARBURG family member.
The freeformer using ARBURG Plastic Freeforming (APF) is an open system, which operates on the basis of standard pellets. The APF process opens up completely new applications.
It enables the processing of three components to produce raus complex functional parts in a hard/soft combination. A new addition to the range is the freeformer 750-3X, whose part carrier of 750 cm² is around 2.5 times larger than that of the freeformer 300-3X.
With the 300-3X and freeformer 750-3X for two or three components, ARBURG covers a wide range of applications. Custom-made plastic
parts for consumer goods, medical implants and spare parts made from the original material are only three of the many areas for which the freeformer is predestined.
The open system offers great geometric and material freedom. Users can apply their own original materials and optimise droplet size as well as process regulation. The ARBURG material database documents qualified standard granulates as well as food-safe, biocompatible, flame-retardant, soft materials up to Shore 28A and special plastics for the aerospace industry. These include high-temperature plastics like ULTEM or PEEK. The range of qualified materials is continuously being expanded.
Machine Name
freeformer 300-3X 2-3
234 x 134 x 230 (x, y, z) max. mm
freeformer 750-3X 2-3 330 x 230 x 230 (x, y, z) max. mm
APF is an open system, that offers great freedom in terms of materials. It is based on qualified original plastics in the form of standard granulates (e.g. ABS, PA10, PC, PP, TPE, PMMA, Ultem) , soft materials TPU, SEBS e.g. 30 shore
The freeformers are in great demand for applications in medical technology, including for use within the human body. They are suitable for additive manufacturing of individual orthotics, implants made from original biocompatible material and models for surgical preparation. The system can process for example medical PLLA (Purasorb PL18), very soft TPE (Medalist MD 12130H) or Resomer LR 706 that imitates human bone to produce implants (Evonik).
(water soluble support, e.g. Armat 11, 12)
break away support
In the ARBURG Prototyping Center (APC) at the German headquarters in Lossburg, several freeformers produce benchmark parts for prospective customers. Further machines are used for the same purpose at the company‘s subsidiaries throughout the world. Preliminary trials can be conducted to determine whether the freeformer is actually suitable for the desired part, material and application.
Axtra3D is transforming additive manufacturing by addressing its most significant challenges. At the core of the company’s approach is the seamless integration of technology, materials, and business models, delivering unmatched performance and flexibility for industrial applications.
At the heart of Axtra3D’s innovation is Hi-Speed SLA, a groundbreaking technology powered by the company’s patented Hybrid PhotoSynthesis (HPS) and TruLayer advancements. Hi-Speed SLA eliminates trade-offs between speed, surface finish, precision, and throughput. HPS combines the strengths of SLA and DLP processes, achieving superior surface quality and dimensional accuracy at high throughput. TruLayer enhances this process by optimizing layer-by-layer
control, ensuring reliability and reducing errors. Together, these innovations enable the Lumia X1 printers to produce intricate, high-quality parts with consistent precision, making them ideal for applications demanding structural integrity and fine details.
Axtra3D collaborates with leading material manufacturers to provide a robust portfolio of resins engineered for industrial applications. These materials support a wide range of needs, from general prototyping and high-strength components to micro-detail and medical-grade solutions. The flexibility to switch between materials on a single machine allows users to tackle diverse applications efficiently, minimizing the need for additional equipment investments.
Axtra3D offers flexible business models to meet the unique needs of its customers. Whether relying on the company’s curated material portfolio or experimenting with third-party materials, users are given the freedom to innovate. Additionally, accessibility to Axtra3D’s technology is enhanced through direct purchases, reseller partnerships, and collaborations with service bureaus, ensuring availability in global markets.
Axtra3D’s solutions are utilized across industries such as aerospace, automotive, healthcare, and consumer goods. Applications include injection mold tooling, precision connectors, and low-volume production parts. By delivering high-resolution detail, scalable batch production, and exceptional reliability, Axtra3D enables businesses to streamline workflows and reduce costs.
Axtra3D has redefined additive manufacturing by focusing on advanced technology, material flexibility, and adaptable business models. The company empowers industries to embrace the full potential of 3D printing without compromise.
Carbon provides industry-leading digital manufacturing solutions that empower companies to create high-performance 3D-printed products at scale. Based in Silicon Valley, Carbon’s idea-toproduction platform joins groundbreaking technology, engineering-grade resins, and innovative design software with world-class expertise-- helping companies turn ideas into reality with digital manufacturing.
With Carbon, you can bring a printer in-house to drive your own development or work directly with an extensive network of experienced application engineers and partners in the Carbon Production Network to bring your product to market.
Design: Carbon Design Engine empowers designers to make precisely tuned, high-performance latticed products. Design Engine can help you find the right lattice and material combination to meet mechanical, performance, and aesthetic requirements.
Print: Integrated printing software powers Carbon printers and offers powerful, flexible print preparation, fleet management, and production process integration.
Automate: Automatically customize parts and seamlessly prepare them for printing to produce custom applications at scale with Carbon Custom Production Software.
Materials
Carbon materials combined with the Carbon DLS™ process offer the potential to produce engineeringgrade parts with predictable mechanical responses, enabling you to seamlessly transition from design to functional prototyping and end-use production, all on the same platform.
Premium
Unlock a wide range of mechanical responses in your products made with EPU resins by latticing product designs with Carbon Design Engine. Carbon’s portfolio of durable elastomeric materials can be tuned for stiffness, energy return and absorption, haptics and colors.
Meet the performance needs of your product with Carbon’s engineering-grade rigid materials, suitable for applications across medtech, automotive, industrial, and consumer markets.
Hardware
The evolution of the Carbon Digital Light Synthesis™ technology process offers a new baseline for innovation and part quality. Next-gen oxygen permeable optics, closed-loop control of force and temperature, and built-in IR-based resin heating opens up more possible part orientations and increases printability with DLS technology.
M3
M3 Max
Offers faster printing, simpler print experience, expanded design space, consistent surface finish
Experience the benefits of next-gen DLS printing with a true 4K light engine, enabling double the build area with the same pixel size and density
L1 Large format printer that delivers consistent, highvolume production of large parts of many small parts
EOS is the world’s leading technology supplier in the field of industrial 3D printing of metals and polymers, with a focus on responsible and sustainable manufacturing. Connecting high quality production efficiency with its pioneering innovation and sustainable practices, the independent company formed in 1989 is shaping the future of manufacturing through its innovative and comprehensive solutions. Its product portfolio of EOS systems, materials, and process parameters gives customers a crucial competitive advantage in terms of product quality and the long-term economic sustainability of their manufacturing processes. Supported by its broader ecosystem, EOS facilitates customized manufacturing solutions across the entire value chain – from the initial idea to design and engineering, production, post-processing and ultimately the finished part.
Today, industrial production is in the throes of a fundamental change. EOS is certain the future belongs to digital manufacturing, with industrial 3D Printing being one of the key drivers. At the same time, additive manufacturing can play an important role in overcoming the limitations of current manufacturing techniques that are restrictive, wasteful, and inefficient. EOS is leading the way in AM techniques such as metal support-free part printing and creating production workflows that enable easy integration with existing production lines, while accelerating the part design process.
As a market leader, EOS wants to lead by example on sustainability. This has for a long time been part of its company DNA, with a strong focus on customers and their applications. EOS nurtures an ecosystem, actively engages its community, and network, and empowers its people to strive for results that increase energy efficiency, reduce
ABOVE: Support-free hip replacement (source: EOS)
waste, and use resources conscientiously at every step of the process. All with the very clear intention of establishing Responsible Manufacturing as the ‘new normal’ – and to support customers in achieving their own sustainability goals.
EOS, its customer YOU MAWO, and Fraunhofer EMI partnered up for a comparative lifecycle analysis. The result: eyewear 3D printed on EOS technology shows up to 58 percent lower carbon footprint than conventional eyewear. As the technology enables the design and manufacturing of highly individualized eyewear, it also helps to avoid overproduction, minimizes supply chains, and enables on demand production where it’s needed.
100% Support-free 3D printing: This metal printed Titanium (Ti64) hip replacement exceeding neck fatigue testing ISO 72606 was produced on an EOS M 300-4 and EOS M 290 and integrated into a traditional production workflow. By shifting to supportfree 3D printing, the AM process was improved economically and environmentally. Not needing to construct supports during the build means less of the material in the powder bed will be melted, which cuts down production time and saves post-processing resources. This results in a lower level of material waste and reduced energy expenditure.
AMCM, an EOS company that provides customized machines, enables new levels of part performance. Customers like ThyssenKrupp can produce highly efficient copper components thanks to the AMCM M 290 system with 1 kW infrared fiber laser. The new inductor design generates an optimized magnetic field, which leads to a more efficient process. The cost saving is an impressive 60% when the inductor is manufactured using the additive process. The inductor has 2.5 times longer service life and, in addition, the power consumption during the heating process can be reduced by 50%.
ABOVE: Dual function inductor (source: thyssenkrupp)
1,320 x 1,067 x 2,204 mm (51.97 x 42.01 x 86.77 in) 200 x 250 x 330 mm (7.9 x 9.8 x 13 in)
2,030 x 1,270 x 2,100 mm (79.9 x 50.0 x 82.7 in) system incl. switchgear cabinet 340 x 340 x 600 mm (13.4 x 13.4. x 23.6 in)
Nylon 11: white, natural, black, climate neutral
Nylon 12: white, natural, carbon reduced, glass-filled, aluminum-filled Thermoplastic Polyurethane: unfilled
3,400 x 2,100 x 2,100 mm (133.9 x 82.7 x 82.7 in)
Nylon 11: natural, climate neutral
Nylon 12: white, natural, black, highly reusable, carbon reduced, glass-filled, flame-retardant hal.
2,250 x 1,550 x 2,100 mm (88.6 x 61 x 82.7 in) 700 x 380 x 580 mm (27.6 x 15 x 22.9 in)
Nylon 11: white, natural, black, climate neutral Nylon 12: white, natural, carbon reduced, glass-filled, aluminum-filled, flame-retardant hal. & non-hal. Thermoplastic Polyurethane: unfilled
www.eos.info/responsible-manufacturing
EOS M 290
EOS M 290 1kW
EOS M 290-2
EOS M 300-4 1kW
EOS M 300-4
EOS M 400-4
Metal systems/Direct Metal Laser Sintering (DMLS): more under www.eos.info/metal
2,500 x 1,300 x 2,190 mm (98.4 x 51.2 x 86.2 in)
250 x 250 x 325 mm (9.85 x 9.85 x 12.8 in) incl. build platform
2,680 x 2,120 x 2,400 mm (105.5 x 83.5 x 94.5 in) 250 x 250 x 325 mm (9.85 x 9.85 x 12.8 in) incl. build platform
5,221 x 2,680 x 2,340 mm (205.6 x 105.5 x 92.1 in) 300 x 300 x 400 mm (11.8 x 11.8 x 15.8 in) excluding build plate
4,181 x 1,613 x 2,355 mm (164.6 x 63.5 x 92.7 in) 400 x 400 x 400 mm (15.8 x 15.8 x 15.8 in) including build plate
5,140 x 1,613 x 2,490 mm (202.3 x 63.5 x 98.0 in) 400 x 400 x 400 mm (15.8 x 15.8 x 15.8 in), including build plate
Cobalt chrome, titanium, stainless steel, maraging steel, tool steel, nickel alloys, aluminium, case hardening steel, copper
Cobalt chrome, titanium, stainless steel, maraging steel, tool steel, nickel alloys, aluminium, case hardening steel, copper
Cobalt chrome, aluminium, nickel alloys, stainless steel, titanium, maraging steel
Aluminium, cobalt chrome, copper, nickel alloys, stainless steel, tool steel, titanium
Aluminium, case hardening steel, copper, nickel alloys, stainless steel, maraging steel, titanium customized machines via AMCM
An extensive portfolio
We offer two-way flow AFM machines, MICROFLOW
low-viscosity variation, tooling, and specially engineered media to address your AM finishing needs.
The experience
The AFM inventor, Extrude Hone, delivers surface improvement for AM components across all industries.
Superior results
Partially sintered material removal, stress release, and improved roughness by up to 10 times.
MICROFLOW
Focus on small orifices.
VECTOR
SPECTRUM
Advanced process control to address more significant volume production and/or complex parts.
Designed to handle large parts with complex requirements.
250mm (10”) /
300mm ‘12”) /
400mm (16”) /
600mm (24”) /
(19.5”) 900mm (35.4”) X 500mm (19.7”)
780mm (32”) up to 16” model
1257mm ‘49.5”) for the 16” HP and 24” models
1016mm (40”) for 10” and 12” models 1270mm (50”) for 16” model 1384mm (54.5”) for 16”HP and 24” models Same for depth
Media Control with AUTOFLOW ( 16” and below) & temperature management
Media Control with AUTOFLOW ( except 24”) & temperature management
Hydraulic or manually operated swing arms. Manually operated tooling slide cart
For almost 100 years our company has been one of the global players in the development and manufacturing of machines and production lines. Our customers include the world`s most prestigious car manufacturers, their suppliers and many other renowned companies from various industries. With our production plants in Mindelheim (Germany), Bluffton, Ohio (USA), São Paulo (Brazil), Dalian (China), Pianezza (Italy) and Bangalore (India), and worldwide service and sales subsidiaries, we are represented around the globe. The GROB Group generates worldwide revenue of over 1.8 billion euros (BY 23/24) with a workforce of about 9,000 employees.
Our portfolio ranges from universal machining centers to highly-complex manufacturing systems with own automation function through to manual assembly stations and to fully-automated assembly lines. Furthermore, production plants for electric motors and assembly lines for battery and fuel cell technology are part of our product range. GROB engineers are delivering solutions for cutting high-strength turbine housings and machining structural and chassis components. With the GROB-NET4Industry software developed in-house for the digitalization and networking of production processes, production processes can be displayed digitally and transparently.
With the GMP300, GROB is offering its customers a manufacturing system for the first time for the near-net-shape production of Aluminum components in the field of additive manufacturing. At GROB, a pioneering, economical and flexible manufacturing process has been developed in the field of additive manufacturing that eliminates the disadvantages of traditional metal-processing additive manufacturing processes: liquid metal printing (LMP). With the GMP300, GROB is already offering its customers reliable, efficient and cost-conscious plant technology with maximum manufacturing flexibility for single-part and smallbatch production. GMP stands for GROB Metal Printing, and the 300 refers to the size of the work area, 300x300x300 mm³. The GMP300 is equipped with 3-axis kinematics and a maximum axis speed of 30 m/min. The inert atmosphere protects the component from oxidation, thus guaranteeing consistently good material properties.
HP 3D printing technologies are reinventing design and manufacturing by unleashing the full potential of 3D printing.
Our solutions bring together new systems, data intelligence, software, services, and materials innovations that enable customers to scale their 3D production to unprecedented levels.
Manufacturing predictability with high-quality parts, performing optimally at industry levels of efficiency, precision, and repeatability.
Offering the best economics in production environments, it provides greater flexibility, optimizes workflows, and simplifies the management of production systems.
Learn more at: https://www.hp.com/gb-en/printers/3d-printers.html
x 1268 x 1804 mm (87 x 50 x 71 in)
HP 3D HR PA12 White 11 hours HP Jet Fusion
x 1268 x 1804 mm (87 x
HP Metal Jet S100 3D Printing Solution 2937 x 1409 x 2478 mm 430 x 309 x 140 mm
HP 3D HR PA12, HP
3D HR PA12GB, HP
3D HR PP enabled by BASF, HP 3D HR PA11, BASF Ultrasint® TPU01 11.5 hours (balanced print mode) 9.5 hours (fast print mode)
HP Metal Jet SS 316L and HP Metal Jet SS 17-4PH 1990 cc/hr9*
* 9. In the case of a layer thickness of 50 microns, actual build speed is affected by build depth, materials, and processing parameter settings.
Capable of print speeds 15x faster than the nearest competitor, the CBAM 25 has and will change the way things are made by bringing the power of 3D printing to volume manufacturing.
Faster 3D Printing: The CBAM 25 prints 25 feet per minute and produces parts 15x faster than any other technology on the market.
Better Dimensional Accuracy: Long-carbon fibers are combined with 50 micron layers enabling the CBAM 25 to achieve tolerances up to 100 microns.
Higher Strength: As a true composite using high strength materials such as carbon fiber we achieve tensile strengths of 140 MPA which is 4x FDM and 3x MJF.
High Performance Materials: Using high strength carbon fiber and high performance plastics like PEEK we obtain higher strength and better chemical resistance than conventional 3D printing materials.
No Shrinkage or War-page: Because we use long fibers and consolidate under high pressure the is little to no shrinkage or warp-age in CBAM printed parts.
CBAM or Composite Based Additive Manufacturing uses high-speed printing methods to produce high-performance composite parts without tooling or messy resins.
Long-fiber sheets of carbon fiber or fiberglass are combined with PEEK and other high-performance polymer powders. Once the excess polymer powder is vacuumed from each individual sheet, they are stacked in the shape of the CAD bitmap file.
Next, the stack of sheets are heated and compressed to the melting point of the polymer and finally, the un-bonded portions of sheet fibers are removed through manual or automated bead blasting processes.
What is left is an advanced composite part with an excellent strength-to-weight ratio compared to aluminum.
Features and Benefits
Designed for Manufacturing Environments
Load and unload while run technology for powders, inks, and build blocks
• Roll fed substrate minimizes sheet handling errors and increases productivity
AI-based, in-situ process control to ensure stable and repeatable printing
Carbon Fiber High Performance
PEEK yield higher tensile strengths up to 140 MPA and better chemical resistance.
• Fiberglass and PA 12 yield better performance than FDM and at a much lower cost.
UL 94V-0 Certification
Real Time Defect Detection and Avoidance System
• Automatic print monitoring correction via Smart Yield Tech Minimizes scrap builds Improves productivity uptime and reduces costs environments
• CBAM 25 operates in standard industrial
Simple Operating Environment
• No hazardous waste or explosion risks
• No special material storage requirements
Operates with standard shop utilities (air, power)
High Dimensional Tolerance
• Bulk thermal processing eliminates warping, cracking and seams associated with other 3D processes
Typical accuracy 200 microns, up to 100 microns achievable with reprint
Sustainability Focused
Room temperature printing means no wasted powder
• Unfused fibers can be recycled
Specification
Fiberglass
Founded in 2016 by a team of engineers with extensive experience in precision equipment development and high-performance materials research, INTAMSYS has unequivocally emerged as a global leader in delivering cutting-edge solutions for industrial FFF 3D printing and direct additive manufacturing, propelling the industry standard forward.
Our dedication lies in harnessing industrial FFF technology to accelerate the integration of 3D printing into end-use part production. We’re actively transforming the limitations of traditional manufacturing, reinventing a more efficient and cost-effective manufacturing landscape.
Industrial Performance
• Large-format, high performance material printing
• Superior surface finish of complex geometries
• High dimensional accuracy and enhanced mechanical properties
• Industrial-grade consistency and reliable repeatability
Production Efficiency
• High printing speed
• Unattended operation with intelligent design
• Additive manufacturing software platform for the production at scale
• Continuous production 24/7
• High reliability with minimized downtime
• Open material system offers cost-effectiveness
Accelerate Your Production with All-New FUNMAT PRO 310 NEO
Ideal for Small-Batch Manufacturing in Industrial Applications, the FUNMAT PRO 310 NEO empowers engineers and designers with industrial-grade performance and reliability, taking user experience to the next level. Its 100°C heated chamber, combined with a spacious 305 x 260 x 260 mm build volume, enables the full-size printing of larger models with no compromise.
New self-developed high-speed architecture ensures the superior surface finish and high dimensional precision, significantly enhances production efficiency.
Machine name Description
FUNMAT PRO 310 NEO
FUNMAT PRO 610HT
FUNMAT PRO 410
FUNMAT HT
Industrial HIgh
Speed 3D Printer
• Industrial Performance
• High-throughput Printing
• High Versatility
Large Build Volume Industrial 3D Printer
• Up to 300 °C Heated Chamber
• Large-Format
• Continuous
High Performance and Fiber Composite 3D Printer
• Industrial Grade
• PEEK Printing
• Intelligent Design
Designed for PEEK 3D Printing
• High Performance
• Desktop 3D Printer
• Cost-Effective
With 12+ types of material process packages for high-speed printing, the production capacity reaches 500g to 1000g per day
Industrial Performance
The active heated chamber maintains a consistent temperature up to 100°C, optimizing material properties and mechanical strength for a wide array of engineering plastics.
High Versatility
Capable of printing a wide range of materials such as engineering materials, fiber composite materials, flexible materials and high performance materials such as PC, PPA-CF, TPU, and PPS.
Intelligent Auto-Leveling
Enjoy effortless setup and printing with auto mesh leveling and Z-axis calibration. Precise and efficient.
Established in Tokyo in 1949, JEOL is a world leader in electron optics and analytical instrumentation and for high-end scientific and industrial research and development. Core product groups include SEM and TEM electron microscopes and e-beam lithography systems, as well as MS, NMR, and ESR analytical instruments.
In 2014 JEOL began development of our first Electron Beam Melting prototype AM machine for the additive manufacturing market, the culmination of more than 75 years in electron beam expertise. Today JEOL has the JAM5200EBM Metal 3D Printer, a production ready AM solution which has been demonstrated to achieve AMS7032 operational qualification
For more information about JEOL USA, Inc. or any JEOL products, visit our booth, our website at www.jeolusa.com, or call 978-535-5900
JAM-5200EBM
standards by exceeding the AMS7011 material requirements.
JEOL has over 180 field service support staff located across North America that can respond to any unexpected performance challenges with a median tenure of 17.5 years. Because of the size and experience of our team, customers can expect first contact within 2 business hours of the support request and, in most cases,
Ti6Al4V, Nickel Alloy 718, Tungsten, Copper, and many more 6000W
engineers on-site within 1-2 business days of the initial request.
JEOL USA, Inc., a wholly owned subsidiary of JEOL, Ltd., Japan, was incorporated in the United States in 1962. Our goal is to apply our unique technologies to leading edge, reliable products that empower our customers to meet their manufacturing targets. The company has 13 regional service centers that offer unlimited emergency service and support in N. America.
LULZBOT: THE PREMIER CHOICE IN USAMADE DESKTOP 3D PRINTERS
Hassle-free 3D printing, built on a foundation of unwavering reliability, repeatability, performance.
WHY LULZBOT?:
• USA-Made in Fargo, ND: Our products are built to stock and typically ship same or next day.
• Trusted Legacy Since 2011: Specializing in desktop 3D printing, LulzBot is a preferred choice for Fortune 500 companies, military branches, and top-tier educational institutions.
• Mastery in Flexible Materials: LulzBot machines are calibrated for optimal printing with flexible materials like TPU, credited to our direct drive extruders and 2.85mm filament diameter compatibility.
• Government Experience: We’re GSAlisted and have experience working with government agencies. Contract Number: 47QSMA22D08NT.
LULZBOT TAZ PRO PLATFORM: FOR THOSE WHO DEMAND THE BEST: When reliability, repeatability and performance matter, the TAZ Pro platform remains unrivaled.
• Complete Versatility: Whether it’s 1.75mm or 2.85mm filament, nuanced requirements of dual-material printing, or onboard backlash compensation, the TAZ Pro is engineered to meet your exact needs.
• Professional Endorsements: Leaders in the field vouch for the TAZ Pro Platform’s simple 3D printing integration and superior output.
• Multiple Build Volumes: Explore the range of LulzBot TAZ Pro machines tailored to fit unique requirements. [View table for details.]
• High Flow: Large layers and volumetric output available with tool heads featuring up to 2.4mm nozzles.
DELIVER RESULTS WITH A LULZBOT PRINT FARM:
Streamlined, high-speed 3D printing operations. That’s what LulzBot Print Farm delivers.
• Proven Expertise: We don’t just make 3D printers; we run a 300+ LulzBot 3D Print Farm daily.
• Operational Integration: Bring the power of LulzBot into your workflow. Centrally manage 64+ 3D printers.
• Robust Software: With AutoFarm 3D Software, expect streamlined job queuing, live data monitoring, and detailed ROI.
• Optimal Workspace Management: Our SlideNest™ Doors create a spacious work space, easily adaptable between open or enclosed 3D printing.
• Custom-Tailored Solutions: We work with you, ensuring the Print Farm aligns perfectly with your needs.
• Full-Service Installation: From setting up to handson training, our experts are with you at every step.
• Resilient Design: Perfect for high-intensity shop floors or calm office spaces.
Elevate your projects with our state-of-the-art 3D printing technology. Connect now to begin your journey.
Phone: 701-809-0800 x1 Email: sales@lulzbot.com
Renishaw designs and manufactures world-leading metal additive manufacturing systems for production of components in a variety of metals, using a process called metal powder bed fusion (or laser melting).
Renishaw is a global engineering and scientific technologies company with expertise in additive manufacturing (AM), precision measurement and process control, position and motion control, and healthcare.
Renishaw’s additive manufacturing solutions include metal AM systems, software, metal powders, ancillary equipment, accessories, and expert consultation and training. Renishaw can provide turnkey and optimised additive manufacturing solutions for a broad range of applications in the industrial and healthcare sectors.
Using its experience as a manufacturer and its expertise in process development, Renishaw
supports its AM customers as they explore how metal 3D printing could revolutionise how they design and make products.
From aerospace and medical to oil and gas, a wide range of customers use Renishaw’s advanced AM systems to fulfil a variety of industry applications where productivity, durability, customised parts and precision are key.
All AM components require a degree of finishing and inspection after they come off the build plate. Renishaw is the only company in the 3D printing industry to offer the technologies and expertise that provide both highly productive metal 3D printing AND control of finishing and downstream processes.
AM 500Q/S series* Height: 2,130 mm, width: 2,165, depth: 1,236 mm 250 × 250 × 350 mm
* RenAM 500Q/S are Renishaw’s multi-laser AM systems. The RenAM 500 series can be configured with one (S) or four (Q) high-power 500 W lasers, each able to access the whole powder bed surface simultaneously. Machine Name Machine Size
Titanium, Ti6Al4V, Aluminium, AlSi10Mg alloy, Cobalt chromium, CoCr, Stainless steel, 316L, Nickel alloys
Up to 150 cm³/hr
YOUR TRUSTED PARTNER FOR DEPOWDERING
Since 2015 Solukon is the pioneer and technical leader of automated depowdering in additive manufacturing. The company, located in Augsburg, Germany, has extensive experience in the development of AM systems and related peripheral equipment and offers a full range of industrial postprocessing systems. Solukon has installed depowdering systems in 27 countries and is the supplier of choice of the leading rocket manufacturers. The systems are approved for safe and reliable processing of powder materials, including tough-to-handle and reactive metal powders. Solukon provides four different systems, each of them optimized for your part size and application. The powder removal systems fit for every laser powder bed fusion manufacturing system on the market.
MARKET LEADER THROUGH INTELLIGENT AND DIGITAL FEATURES
Solukon not only manufactures the best depowdering equipment on the market, but also considers the digital integration of the equipment. For digital depowdering Solukon is the first manufacturer in the world to offer various unique tools.
SPR-Pathfinder® Software
The SPR Pathfinder® uses the build job’s CAD file to calculate the ideal motion sequence in the Solukon system.
Digital-Factory-Tool (DFT)
The DFT sets new standards for quality monitoring, depowdering automation and digital integration. It records all relevant depowdering process data and summarizes the values in a protocol file. New: it also tracks the carbon footprint of depowdering.
Maximum capacity
2,100 kg
600 x 600 x 1500 mm
820 x 820 x 1300 mm
Minimum footprint
SFM-AT350/-E
SFM-AT800-S
All reactive and/or non reactive metal powders
The entry level system for medical components / laboratory applications
All reactive and/or non reactive metal powders
The new standard for medium sized parts
All reactive and/or non reactive
The award winning flagship for complex geometries SFM-AT1000-S
SFM-AT1500-S
All reactive and/or non reactive metal powders
The pro version ideal for extraordinary large parts
All reactive and/or
The new titan for extraordinary large and heavy parts
Thermwood is a US based, multinational, diversified machinery manufacturer that markets its products through offices in 11 countries. Thermwood is the oldest manufacturer of highly flexible, 3 and 5 axis high-speed machining centers known as CNC routers. We primarily market to the aerospace, plastics, composites and woodworking industries, but have found applications in almost every major industry from medical to entertainment.
Thermwood is also the technology leader in large scale additive manufacturing of thermoplastic composite molds, tooling, patterns and parts with its innovative line of LSAM (Large Scale Additive Manufacturing) machines that both 3D print and trim on the same machine. These are some of the largest and most capable additive manufacturing systems ever produced and are marketed to major companies in the aerospace, marine, automotive and foundry industries as well as military, government and defense contractors.
Thermwood has a strong ongoing research and development effort combined with core skills in diverse technical areas such as ultra high-performance control system design, real
time software development, CAD/CAM software development, advanced machine structure design, machine motion dynamics, thermal design and polymer science.
Thermwood was the first company to develop a CNC control system in the 1970s, and today our control has advanced to become one of the most powerful and capable available. It is highly regarded and used by major aerospace, automotive, government and defense contractors for some of their most demanding applications. Thermwood embraces all aspects of the essential technology, the machine, the control and the driving software. This better integrates all aspects of state-of-the-art technology into superb products to meet the most demanding customer requirements.
Thermwood machines are designed to operate in real production environments 24 hours a day, 7 days a week, 365 days a year with minimal maintenance. Many, if not most, customers go years without experiencing a technical issue.
Thermwood’s technical service is ready to help if ever needed. From highly innovative virtual service to the ability to ship almost any part of any machine overnight, to providing updates, upgrades and rebuilds of older machines, to indepth training both at the machine purchase and any time after. Thermwood service is available to anyone who owns a Thermwood machine whether it was purchased from us or on the used market.
Our key guiding principal is to insure that Thermwood users continue to profit as a result of their relationship with us.
x
(X - Y -
PSU, PESU, ABS (carbon fiber filled and glass filled), PEI/ULTEM, POLYCARBONATE, PPS, PETG, POLYETHEYLENE, POK
PSU, PESU, ABS (carbon fiber filled and glass filled), PEI/ULTEM, POLYCARBONATE, PPS, PETG, POLYETHEYLENE, POK
PSU, PESU, ABS (carbon fiber filled and glass filled), PEI/ULTEM, POLYCARBONATE, PPS, PETG, POLYETHEYLENE, POK
PSU, PESU, ABS (carbon fiber filled and glass filled), PEI/ULTEM, POLYCARBONATE, PPS, PETG, POLYETHEYLENE,
Deposition rates from 200 lbs per hour to 500 per hour depending on the melt core and polymer used.
Deposition rates from 200 lbs per hour to 500 per hour depending on the melt core and polymer used.
Deposition rates from 200 lbs per hour to 500 per hour depending on the melt core and polymer used.
Deposition rates from 200 lbs per hour to 500 per hour depending on the melt core and
www.trumpf.com/s/additivemanufacturing
THE RIGHT SOLUTION FOR EVERY METAL AM APPLICATION
From prototyping to industrial series production. As a pioneer in additive technologies and laser specialist since 1979, we offer the right technology for every application requirement: Laser Powder Bed Fusion or Laser Metal Deposition. Benefit from complete industrial solutions with intelligent monitoring and smart services from a leading high-tech mechanical engineering company worldwide.
Are you looking for an application that you would like to produce additively? Talk to our AM Consulting.
TRUPRINT 3000 - FIND YOUR FLEXIBLE METAL 3D PRINTING SOLUTION WITH MULTILASER OPTION
In addition to performance increase with fullfield Multilaser option, the focus of the TruPrint 3000 is improving process robustness and various operating scenarios. High process reliability due to newly developed gas flow and high part quality are proven with Melt Pool Monitoring.
The 3D printer can be tailored to your production process needs. Visit our AM showroom, live oder online: www.trumpf.info/am-showroom
Stainless steels, tool steels, aluminum, nickel-based, cobaltchrome, copper, titanium or precious metal alloys, amorphous
TruLaser Cell 3000
Also individual integration into your OEM solution Laser Metal Deposition (LMD): From coating to repair through to additive manufacturing
TruLaser Cell 7040
x 600 x 400 mm
x 1500/2000 x 750/1000 mm
Stainless steels, tool steels, aluminum, nickel-based, cobaltchrome, titanium or copper alloys, tungsten or titanium carbides
Unpacking: Internal
Monitoring: Condition, Powder Bed, Performance
New options: - Multiplate for 4 build plates printing without a stop - Preform for printing single abutments on pre-built base parts
Preheating:
Up to 200 °C
Unpacking: Internal under shielding gas
Periphery: Powder preparation station
Monitoring:
Condition, Powder Bed, Melt Pool, Performance
Preheating: Up to 200 °C
Unpacking: Internal under shielding gas or external with interchangeable cylinder in depowdering station (optional under shielding gas) or with unpacking station
Periphery:
Industrial part and powder management
Monitoring: Condition, Powder Bed, Melt Pool, Performance
Preheating: Up to 200 °C (basic machine), up to 500 °C (optional)
Automatic process start: Yes
Unpacking: External with interchangeable cylinder in depowdering station (optional under shielding gas) or with unpacking station
Periphery:
Industrial part and powder management
Monitoring: Condition, Powder Bed, Melt Pool, Performance
New option: Preform for hybrid manufacturing
DepositionLine technology package for LMD: Configurable solution from beam source, powder feeder, optics, and nozzle High-speed laser metal deposition for rotationally symmetric components
UltiMaker is a global leader in 3D printing, driving innovation across industries such as manufacturing, product development, and education. UltiMaker offers a comprehensive professional portfolio of advanced 3D printing solutions, including the S series, Method series, and the Factor series.
A versatile, high-performance 3D printer designed for professional environments, the UltiMaker S7 combines reliability with precision to produce numerous applications, from prototyping to end-use parts. With its automated bed leveling and seamless integration with UltiMaker’s software ecosystem, it ensures ease of use and exceptional print quality. The S7 has one of the widest portfolios of compatible 3D printing materials, from polymers to composites to metal.
Method XL is a larger-format 3D printer designed for high-performance applications, with a build volume that accommodates big, complex prints. Equipped with industrial-grade features, including heated print beds and an enclosed temperature-controlled chamber, it’s ideal for producing durable prototypes and
functional parts using advanced engineering materials such as ABS and carbon fiber.
Factor 4 represents UltiMaker’s next generation of 3D printing technology, combining industrialgrade features and precision. Built for production, it delivers exceptional throughput and quality for manufacturing environments, making it perfect for businesses looking to scale up their additive manufacturing capabilities. Factor 4 is compatible with over 200+ 3D printing materials, available through the UltiMaker Marketplace.
These systems offer unparalleled flexibility and performance for a variety of applications. The company’s powerful software platforms, Cura and Digital Factory, enable seamless integration and advanced workflows, streamlining the design-to-production process. UltiMaker Cura is a free, easy-to-use 3D printing software trusted by millions of users. Fine-tune 3D models with 400+ settings for the best slicing and printing results. UltiMaker Digital Factory is the gateway to seamless, efficient 3D printing, enabling users
to streamline processes, increase productivity, collaborate with colleagues, and unlock the full potential of UltiMaker printers. UltiMaker software empowers teams to scale 3D printing innovation across the organization, with a subscription plan for every need. The UltiMaker software platform follows the guidelines of ISO 27001.
These innovations empower customers to create high-quality prototypes, end-use parts, spare parts, and low-volume production runs with precision and reliability.
With a strong commitment to shaping the future of digital manufacturing, UltiMaker continues to push the boundaries of what’s possible, helping organizations enhance productivity, reduce costs, and accelerate innovation.
0330 229 0175
UnionTech 3D stands among the world’s largest and most trusted manufacturers of stereolithography (SLA) technology, renowned for delivering high-performance 3D printers with exceptionally large print bed volumes. Designed for businesses requiring precise, large-scale production, UnionTech’s advanced SLA machines empower manufacturers to achieve unmatched accuracy and scalability, solidifying their position as a global leader in industrial 3D printing.
10,000+
Printers Shipped
150+
Engineers + Scientists
2000
Company Established
60+
Global Reseller Alliance
251+
Issued patents 83 submitted and pending approval
700-800 Employees
60%+
Unit Marker Share in Industrial SLS segment
100%
Intellectual Property Self-implementation Conversion Rate
6
Offices in United States, Germany, Russia, Vietnam, Tianjin, Guangdong
A defining feature of UnionTech 3D printers is their open-source compatibility with resins. This flexibility allows users to choose from a vast array of material options, ensuring the best fit for their specific applications. By eliminating restrictions on resin selection, UnionTech provides customers with the freedom to optimize costs, performance, and outcomes without being tied to proprietary materials.
UnionTech’s SLA solutions cater to a wide range of industries. In investment casting, the printers produce highly detailed patterns with outstanding accuracy, while in the medical and dental sectors, they are trusted for creating surgical guides, dental models, and prosthetics. The footwear industry benefits from precise prototyping, while automotive and aerospace sectors leverage the technology for tooling, lightweight components, and functional prototypes. Additionally, UnionTech plays a pivotal role in design and engineering applications, offering groundbreaking solutions for prototyping and end-use production.
As a leader in SLA technology, UnionTech combines industry-leading large-volume printing capabilities with complete freedom of material choice. With their innovative approach and commitment to customer success, UnionTech continues to set the standard for precision, flexibility, and efficiency in 3D printing
Input
In a world that has had to rapidly adapt to on screen education there has never been a better time to invest in a TCT webinar.
Webinars offer a multi-layered marketing outcome, enabling you to tell your story to a global audience, define your organisation as a thought leader and simultaneously deliver a healthy number of leads for your sales team to get to work on.
We will help you with the whole process, with a dedicated project manager, content consultation and a multi-channel marketing campaign to drive attendance and views.
To discuss how you can leverage our audience and marketing channels with a Webinar contact our Sales team: Carol Cooper: +44 (0) 1244 952 386