
5 minute read
Maşini-unelte Trecerea la transformarea digitală (9)
Fabricația inteligentă este un proces care optimizează procedurile de prelucrare prin automatizare, analiza volumelor mari de date (Big Data) și comanda computerizată, care diminuează costurile și maximizează productivitatea. Prin combinarea datelor de la sistemele IT și sistemele operaționale (administrarea duratei de viață a produsului și sistemele ERP) permite producătorilor să răspundă rapid și eficient schimbărilor la nivelul secției și în întregul lanț de valori.
Care sunt beneficiile activităţii fabricaţiei inteligente?
Advertisement
Aceasta permite efectuarea continuă a îmbunătăţirilor, crescând productivitatea și diminuând costurile. Automonitorizarea și întreţinerea preventivă posibilă prin învăţare automată (machine learning) diminuează timpii de oprire și costurile reparaţiilor. Și informarea în timp real a stării echipamentului de producţie și a materiilor prime face mai ușoară satisfacerea necesităţilor beneficiarului, produse în serie personalizate și dezvoltarea de noi produse și servicii. [286]
Stimulată de big data, cloud și AI, Industry 4.0 va face posibilă crearea fabricilor inteligente, în care sisteme inteligente, interconectate comunică cu mașini și produse (ca și cu oamenii) în întregul lanţ de valori.
Tehnologiile Industry 4.0 transformă procesele lean pentru a aduce progresul întreprinderii. În timp ce principiile lean au fost folosite de mult timp în fabricaţie pentru a stimula eficienţa și diminua deșeurile, adăugând tehnologiile digitale sistemului lean se poate aduce o întreprindere la o frontieră complet nouă.
Principiile lean au jucat un rol semnificativ în stimularea eficienţei în întreaga organizaţie prin accentuarea diminuării costului, concentrarea pe eliminarea deșeurilor și bazarea pe acceptarea proceselor motivate de solicitările beneficiarului. Deși lean își are originile în fabricaţie, principiile sale de bază sunt întâlnite în multe tipuri de întreprinderi și aplicate în diferite moduri. Lean poate opera în orice domeniu în care este aplicat, pentru că oferă o abordare bazată pe date pentru elaborarea deciziilor, accentuând traseul cauzelor de bază. Lean este considerat adesea optim pentru identificarea problemelor ascunse și accentuarea continuei îmbunătăţiri. Dar lean, așa cum îl înţelegem astăzi, a fost concentrat într-un set de principii, care au transformat fabricaţia.
Mai recent, tehnologiile fizice și digitale Industry 4.0 au făcut posibile noi realizări privind viteza,
Corneliu GORNIC
Inginer, specialitatea Maşini-Unelte şi Scule, promoţia 1968
Activitate: n cercetare maşini-unelte din 1968 până în 1992, de la simplu inginer la cercetător ştiinţific principal gr. I şi director ştiinţific, în cadrul Institutului de Cercetări şi Proiectări Maşini-Unelte (ICPMUA, ICSIT-TITAN, acum SIMTEX); n marketing, AQ, CTC, proiectare (fostul ARMUS); n dezvoltare, tehnologii de montaj şi reglaj, încercări şi diagnoză, tehnologii de prelucrare (PROFEX CONSULT) coeziunea, flexibilitatea și automatizarea care au modificat pentru totdeauna aspectul producţiei. Progresele din robotică, materiale și AI sunt gata să fie avangarda viitoare a fabricaţiei și nu numai. Apariţia acestei noi ere solicită noi probleme: cum susţin tehnologiile fizice și digitale ale Industry 4.0 fabricaţia? Ce principii ale lean manufacturing rămân relevante astăzi, vor fi relevante în viitor și se aplică companiilor, îmbrăţișând digital lean? Care sunt beneficiile digital lean - și capcanele generale pe care trebuie să le evite specialiștii? Cum trebuie să abordeze tema un specialist?
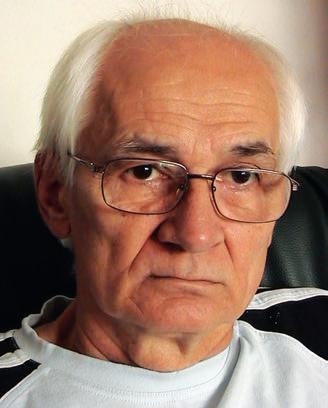
Se încearcă să se răspundă acestor întrebări, dar și altora, prin explorarea modului în care Industry 4.0 permite companiilor să devină digital lean. [287]
,,Primul pas în Industry 4.0 sau fabrica inteligentă este eliminarea instrucţiunilor pe hârtie și punerea în aplicare în procesul de asamblare. De aici se trece la corectarea erorilor și achiziţia de date. Pași simpli. Probabil că este la fel de simplu ca operaţia pe care o face un operator când citește un cod de bare al unei piese dintr-un container, atunci când obișnuiţi să luaţi de bună piesa corectă pentru a fi asamblată în produse corecte. Sau un control mai riguros al procesului de strângere, care iniţial a fost un proces cu buclă deschisă. A fost surprinzător cât de puţin a fost controlat procesul pe liniile de asamblare. După ce muncitorii de la asamblare au asimilat instrucţiunile de lucru digitale, eliminarea erorilor și achiziţia de date, pot face pasul următor pentru o mai mare integrare a pachetului software. Aceasta este baza alfabetului pentru harware și software – PLC, SCADA (Supervisory Control and Data Aquisition=control de supraveghere și achiziţie de date), MES (sistem de executare a prelucrării) și ERP – care administrează fabricile de montaj moderne. Sistemul ERP poate fi achiziţionat sau folosit cel existent, cu posibile adaptări. Fiecare tip de software poate fi achiziţionat independent, dar asamblarea lor ar putea pune probleme. Se recomandă cumpărarea unui pachet software care acoperă toate problemele, de la un singur furnizor.
Ceea ce este cel mai important nu este sensul din care derivă necesitatea introducerii Industry 4.0, ci cultura companiei. „Totul depinde de nivelul de maturitate digitală a organizaţiei. Dar la fel de important pentru organizaţie este să aibă o cultură lean, flexibilă, care este adoptată de la vârf până la muncitorul obișnuit. Atunci când o organizaţie generează puţine proiecte de îmbunătăţire continuă, acestea conduc, adesea, la soluţii extinse. Nu există soluţie de tip glonţ de argint (soluţie simplă și magică pentru rezolvarea unei probleme) pentru crearea unei fabrici digitale; există o serie de curse de viteză flexibile. Se pot verifica teorii, dar se învaţă din cele mai bune soluţii proprii", declară Rodney RUSK. El a lucrat în ultimii cinci ani la aplicarea tehnologiei IIoT la BOSCH Group: Am învăţat multe prin încercări și erori. Acum oferim și altora multe din acele cunoștinţe.
Atunci când se iau decizii privind investiţii în mijloace de producţie în era Industry 4.0, se recomandă producătorilor să întrebe mai mult decât „ce se va face pe această linie?" și să pună o altă întrebare „cum se va potrivi această linie întregului ecosistem existent?" La efectuarea unui salt la Industry 4.0, producătorii nu trebuie să se teamă de eșec. Nu sunteţi pe punctul de a obţine chiar 100% din timp. [288]
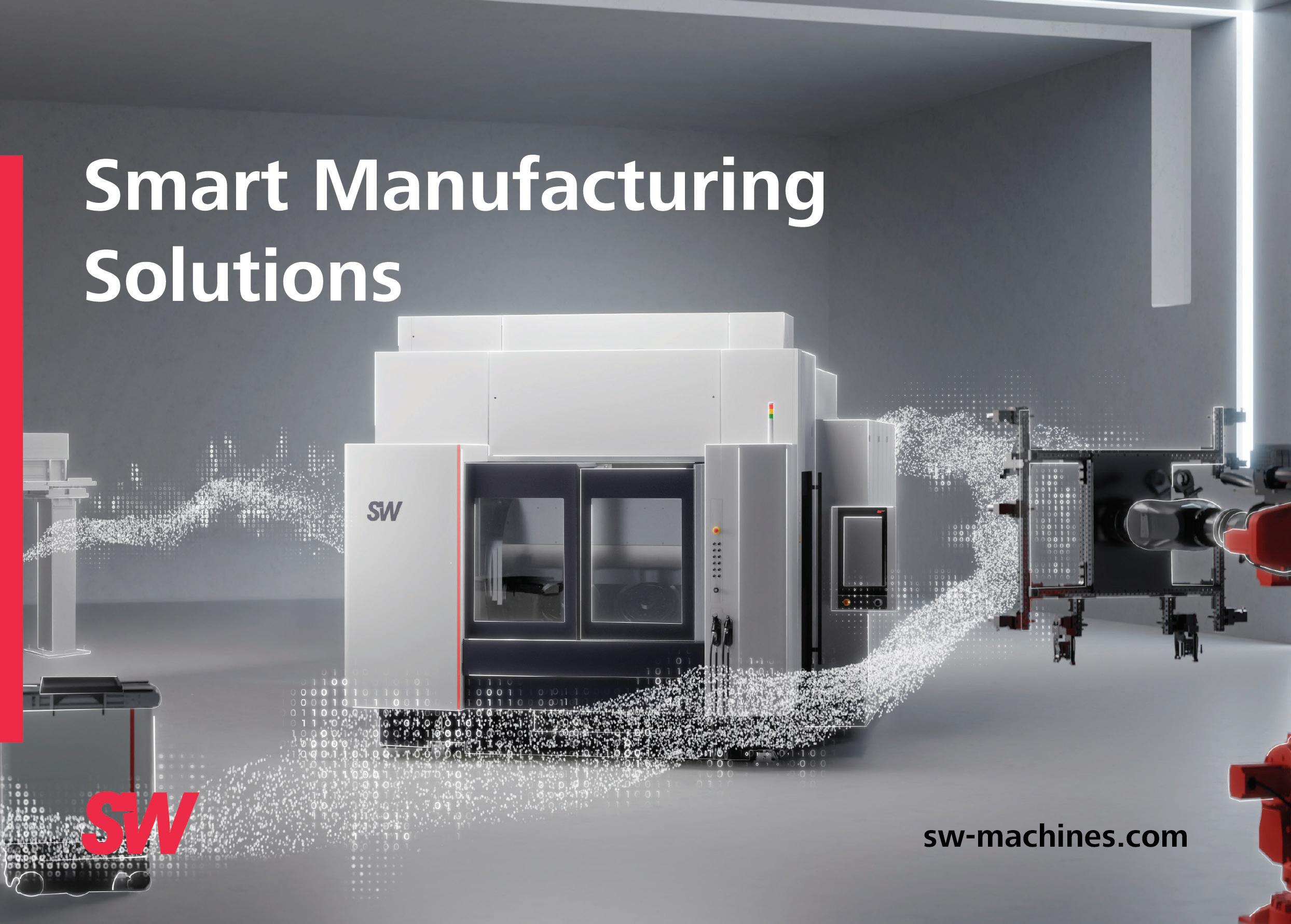
Producţia industrială a viitorului este conectată. Conectivitatea mașinilor-unelte este cheia afirmaţiei. Trebuie satisfăcută o serie de cerinţe înainte ca interconectarea în reţea să fie ori posibilă, ori utilizabilă. C.O.R.E. (Customer Oriented REvolution) asigură aceste cerinţe. Noul tip de hardware și arhitectura software deschid posibilităţi remarcabile pentru interconectarea, controlul și monitorizarea proceselor de producţie și, de asemenea, optimizarea acestora. În plus, C.O.R.E. oferă experienţa operatorilor în lumea telefoanelor inteligente.
Interconectivitatea asigură un schimb de date între oameni, mașini și mediul de producţie, creând o bază pentru funcţionarea aplicaţiilor moderne ale IoT. A fost posibilă o funcţionare intuitivă pentru a face munca mai ușoară pentru reglorii, operatorii mașinilor și personalul de întreţinere. C.O.R.E. a transformat viziunea în realitate – în mod revoluţionar.
Viitorul digital începe cu C.O.R.E. – Stephan NELL.
Graţie unui chip personalizat, profilul utilizatorului individual poate fi încărcat automat. Se permite astfel înregistrarea și deconectarea mai ușoară, dar și semnificativ mai sigură. Un profil este stocat pentru fiecare utilizator, fiind posibilă accesarea informaţiilor relevante. Se diminuează complexitatea și se diminuează erorile. Ecranul C.O.R.E. nu are taste. Există un comutator rotativ pentru suprareglarea avansului, permiţând reglarea axelor cu o simplă rotire.
Folosirea panoului C.O.R.E. la orice marcă de mașină simplifică operarea mașinii și ușurarea școlarizării.
Panoul este doar partea vizibilă a tehnologiei. C.O.R.E. OS este un sistem de operare complet, instalat pe un PC industrial de înaltă performanţă. El servește ca poartă IoT și este gazda aplicaţiilor software. Sistemul este compatibil cu toate echipamentele CNC folosite de firma producătoare a sistemului. În procesul de dezvoltare, care a durat câţiva ani, au colaborat experţi (din companie și utilizatori), care au transferat experienţa lor arhitecturii unice a software-ului.