
7 minute read
Orealizare inginerească imposibilă a devenit acum posibilă
Combinarea lucrărilor lui Michelangelo, Rodin, Kollwitz, Kotaro şi Savage cu expertiza Sandvik Coromant
Realizarea de lucrări de artă din metal nu reprezintă o noutate. Mulţi dintre noi s-ar gândi imediat la Statuia Libertăţii sau la Turnul Eiffel, în timp ce cunoscătorii de artă contemporană s-ar putea gândi la Chicago Picasso sau la Îngerul Nordului realizată de Sir Anthony Gormley. Dar cum ar fi combinarea câtorva lucrări de artă faimoase, folosind oţel inoxidabil şi inteligenţa artificială (AI) pentru a crea un nou tip de capodoperă modernă? Atunci când Henrik Loikkanen şi Jakob Pettersson, ingineri de la Sandvik Coromant, au primit sarcina de a crea o sinteză din oţel inoxidabil generată prin AI a unora dintre cele mai faimoase lucrări de artă din istorie, competenţele lor în domeniul aşchierii metalului au fost supuse testului suprem.
Advertisement
În parteneriat cu Grupul Sandvik, Sandvik Coromant a realizat o statuie care va rămâne în istorie. Fabricată folosind sistemele de modelare controlate cu AI şi soluţii de fabricaţie de ultimă generaţie, sculptura combină poziţiile dinamice ale lucrărilor lui Michelangelo, iscusinţa realizării musculaturii specifice lui Auguste Rodin, tonurile sumbre ale lui Käthe Kollwitz, influenţa japoneză a lui Takamura Kotaro şi sfidarea inspiraţională a Augustei Savage, reunindu-i pe unii dintre cei mai cunoscuţi artişti din istorie, dintr-o perioadă care se întinde pe 500 de ani.
Având o greu-tate de 500 de kilograme şi o înălţime de 150 de centimetri, Statuia imposibilă a fost inaugurată oficial la Tekniska Museet, Muzeul Naţional de Ştiinţă şi Tehnologie din Suedia, în luna aprilie 2023. Acest procedeu de construcţie a unei statui nu a mai fost implementat niciodată până acum. Dar cum au reuşit Loikkanen, Pettersson şi echipa lor să creeze acest melanj de artă şi ştiinţă, de trecut şi viitor?
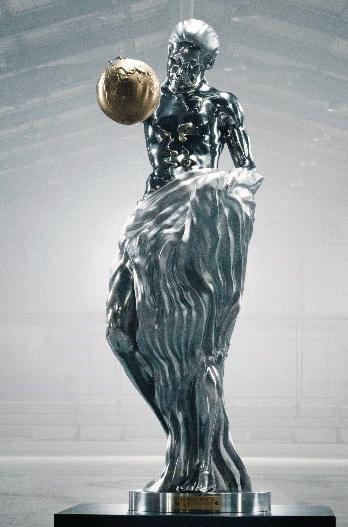
Atunci când inteligenţa artificială se intersectează cu arta
AI este utilizată de ceva timp, maşinile inteligente fiind însărcinate să îndeplinească activităţi care, în mod normal, presupun inteligenţă umană, cum ar fi percepţia vizuală, recunoaşterea vorbirii, luarea de decizii, traducerea limbilor şi rezolvarea de probleme. Conceptul său are mai multe zeci de ani vechime, cel mai timpuriu program fiind scris în 1951 de Christopher Strachey, care ulterior a devenit director al Grupului de Cercetare pentru Programare la Universitatea din Oxford. Însă apariţia unor programe de AI noi, conversaţionale, precum Bard şi ChatGPT de la Google, deschid calea pentru şi mai multe aplicaţii în domeniul tehnologiei.
În prezent, realizările AI par aproape nelimitate — aceasta poate chiar şi să creeze lucrări de artă.
După stabilirea unui model 2D care a reunit stilurile celor cinci artişti, Sandvik a început transpunerea modelului într-o imagine 3D completă. Folosind estimatori ai adâncimii pentru a realiza modelul 3D, estimatori ai poziţiei umane pentru rafinarea corpului, algoritmi de jocuri video pentru a genera ţesături realiste şi AI specializată pentru a reintroduce detalii fine care fuseseră omise în cadrul etapelor anterioare, Sandvik a fost gata să transforme modelul în realitate. Cu ajutorul software-ului Mastercam, a fost creat un model pentru o statuie cu peste şase milioane de suprafeţe şi detalii complexe.
Realizarea modelului statuii a presupus o serie de provocări unice.
Am avut nevoie de o simulare digitală fenomenal de precisă pentru a putea prelucra statuia. Producţia digitală înseamnă că putem testa în prealabil întregul proces complex de prelucrare. Prin urmare, unicul interval de timp pe care l-am petrecut lucrând cu maşinile a fost timpul de producţie propriu-zis. De asemenea, nu am fabricat nici măcar o singură componentă care să fie rebutată pe durata desfăşurării proiectului.
Henrik LOIKKANEN, Manager de tehnologie, Sandvik Coromant
Prelucrarea imposibilului
După finalizarea modelului statuii cu ajutorul AI şi simulând virtual modalităţile optime de fabricare a statuii folosind tehnica geamănului digital, venise timpul începerii operaţiunilor de prelucrare. „Ne-am raportat la producerea statuii aşa cum ne-am fi raportat la prelucrarea unor piese complexe, ultraspecializate, precum cele din industria aerospaţială”, a continuat Loikkanen. „O provocare suplimentară a provenit de la materialul ales pentru statuie — oţel inoxidabil de la Alleima — deoarece materialele ISO M sunt recunoscute pentru cât sunt de greu de prelucrat. Grupa de materiale se caracterizează prin vitezele mari de călire şi proprietăţilor slabe de rupere a aşchiilor în timpul prelucrării. Aşadar, trebuia acordată o atenţie deosebită sculelor selectate pentru prelucrarea materialului.”
Sandvik Coromant a ales câteva scule pentru a facilita sculptarea fiecărei piese complicate din componenţa statuii. A fost utilizată interfaţa de prelucrare Coromant Capto® pentru conectarea braţului şi capului la trunchiul statuii, au fost utilizate scule monobloc circulare din familiile CoroMill® Plura şi Dura pentru finisarea tuturor suprafeţelor şi caracteristicilor statuii, iar CoroMill® MH20, o freză cu avans mare lansată în 2021, a fost utilizată pentru prelucrarea corpului de oţel inoxidabil îndepărtat de pe piesă.
Avem peste 10.000 de produse standard care acoperă domeniile găuririi, frezării, lărgirii şi filetării în catalogul nostru. Însă nu am fi putut selecta o sculă oarecare pentru a crea Statuia imposibilă. Pentru o asemenea provocare, a trebuit să facem o selecţie cu o precizie de laser. A trebuit să analizăm îndelung selectarea metodei şi sculelor, pentru a reduce la minimum operaţiunile de prelucrare şi pentru a limita, astfel, generarea de deşeuri.
Prelucrarea de degroşare a statuii a fost efectuată cu o combinaţie de freze cilindro-frontale din carbură monobloc din familiile CoroMill® Plura şi Dura. Profilarea de degroşare a formei finale a trebuit să fie efectuată cu scule destul de lungi. În acest caz, combinaţia de freze MH20 cu avans mare montate pe cozi din metal greu a fost soluţia perfectă. Utilizarea frezelor cilindro-frontale din gama noastră de scule monobloc circulare a accelerat semnificativ procesul şi a redus consumul de energie.
Jakob PETTERSSON, Specialist în CAM şi prelucrare, Sandvik Coromant
Datorită capacităţii sale de prelucrare la lungimi mari în consolă, freza CoroMill® MH20 este foarte avantajoasă pentru industria aerospaţială. Aceasta a fost proiectată avându-se în vedere componentele dificil de prelucrat şi, în contrast cu conceptul convenţional de freză cu plăcuţă cu patru muchii, MH20 este prevăzută cu o plăcuţă cu două muchii. Acest lucru este deosebit de avantajos deoarece cea mai slabă secţiune a plăcuţei se află departe de zona principală de aşchiere, asigurând o fiabilitate sporită şi protecţie împotriva uzurii. De asemenea, prelucrarea într-un colţ sau pe un perete nu are un impact asupra muchiei următoare sau a colţului anterior, garantând o performanţă uniformă per muchie.
CoroMill® Plura HD este prima opţiune de la Sandvik Coromant în cazul soluţiilor pentru aplicaţii dificile în oţel şi oţel inoxidabil, asigurând procese sigure şi eficiente de prelucrare cu frezele cilindro-frontale monobloc. Acum, datorită stratului de acoperire Zertivo™ 2.0 dezvoltat de echipa de cercetare şi dezvoltare de la Sandvik Coromant, scula oferă un avantaj suplimentar care asigură un plus de siguranţă şi productivitate a procesului. Frezele CoroMill® Dura reprezintă o soluţie universală de prelucrare. Frezele cilindro-frontale pot fi utilizate în cadrul tuturor proceselor de fabricare a unei componente ― inclusiv degroşare, finisare, semifinisare şi prelucrare în plan înclinat.
O capodoperă din domeniul producţiei
Bineînţeles că prelucrarea imposibilului nu a fost lipsită de provocări, iar echipa a trebuit să realizeze câteva adaptări ale strategiei de prelucrare. „Modelul 3D iniţial nu a fost tipul de model cu care sistemele CAD/CAM pot să lucreze”, a afirmat Loikkanen. „Acesta a trebuit să fie convertit dintr-un model 3D de tip reţea care este, în esenţă, un înveliş din poligoane de suprafaţă, care este utilizat, de obicei, în studiourile de realizare a animaţiilor 3D, într-un model 3D solid, cu densitate, iar acest proces a fost destul de dificil. Odată terminat, modelul a fost secţionat în 17 piese, iar toate suprafeţele de secţionare dintre acestea au trebuit să fie modelate cu un ajustaj strâns, pentru a ascunde intersecţiile în momentul în care piesele urmau să fie asamblate. A durat ceva timp până când totul a fost perfect.”
„De asemenea, în timpul prelucrării de degroşare, am întâmpinat o serie de provocări din cauza dimensiunii componentei în raport cu maşinile”, a adăugat Pettersson. „Acestea au fost soluţionate prin simularea codului NC şi identificarea tuturor zonelor în care am fi putut atinge limita incintei de lucru a maşinii şi prin modificarea secvenţei CAM.”
În cele din urmă, realizarea unei statui care combină în mod unitar lucrările a cinci artişti a devenit posibilă. Însă crearea unei statui absolut inedite nu a fost singura realizare notabilă pentru Sandvik Coromant. „Pe parcursul procesului, am implementat mai multe tehnici care pot fi aplicate în viitoarele proiecte de prelucrare digitală”, a afirmat Loikkanen. „Datorită muncii colosale de programare, realizarea statuii nu ar fi fost posibilă fără geamănul digital. Întregul proces de testare a fost efectuat digital, ceea ce a asigurat economii enorme de timp şi a eliminat necesitatea efectuării de teste de încercare şi eroare. Acesta este cu siguranţă un lucru pe care îl putem aplica în proiecte viitoare pentru a economisi timp şi pentru a reduce numărul de componente rebutate.”
„Procesul de programare şi simulare a devenit tot mai rapid cu fiecare componentă”, a adăugat Pettersson. „Prelucrarea a avut aproximativ aceeaşi durată pe toată durata procesului, mai ales deoarece regimul de aşchiere şi selecţia de scule nu s-au schimbat foarte mult. Acest aspect m-a făcut să trag o concluzie: Datele ample despre produse şi recomandările pe care le oferim sunt precise şi pot fi obţinute uşor fie de pe site-ul nostru web, din ghidul de scule, din biblioteca de scule sau chiar direct din sistemele CAM în care sunt integrate. Acest lucru este, cu siguranţă, foarte valoros pentru clienţii noştri şi încheie una dintre cele mai intense sarcini de lucru prin închiderea buclei digitale în jurul programării CAM.”
Fiind acum expusă pentru a fi admirată deopotrivă de iubitorii de artă şi de tehnică, statuia are rolul de a reaminti creativitatea care poate fi atinsă de instrumentele digitale şi de sculele fizice de fabricare. „Sunt extraordinar de mândru că am reuşit să ducem la bun sfârşit acest lucru”, a concluzionat Loikkanen. „Sper că persoanele care vor vizita Tekniska Museet şi oricine altcineva care va vedea această statuie să o aprecieze ca pe o operă de artă unică.”
„Tehnicile pe care le-am utilizat şi metodele pe care le-am folosit arată de ce este într-adevăr în stare Sandvik Coromant”, a adăugat Pettersson. „Ne pricepem cu adevărat la aşchierea metalului şi putem aborda chiar şi provocări pe care nimeni nu le-a mai întâmpinat.”
Pentru a afla mai multe despre Statuia imposibilă realizată de Sandvik şi pentru a viziona un clip video de prezentare a desfăşurării proiectului, accesaţi home.sandvik. A
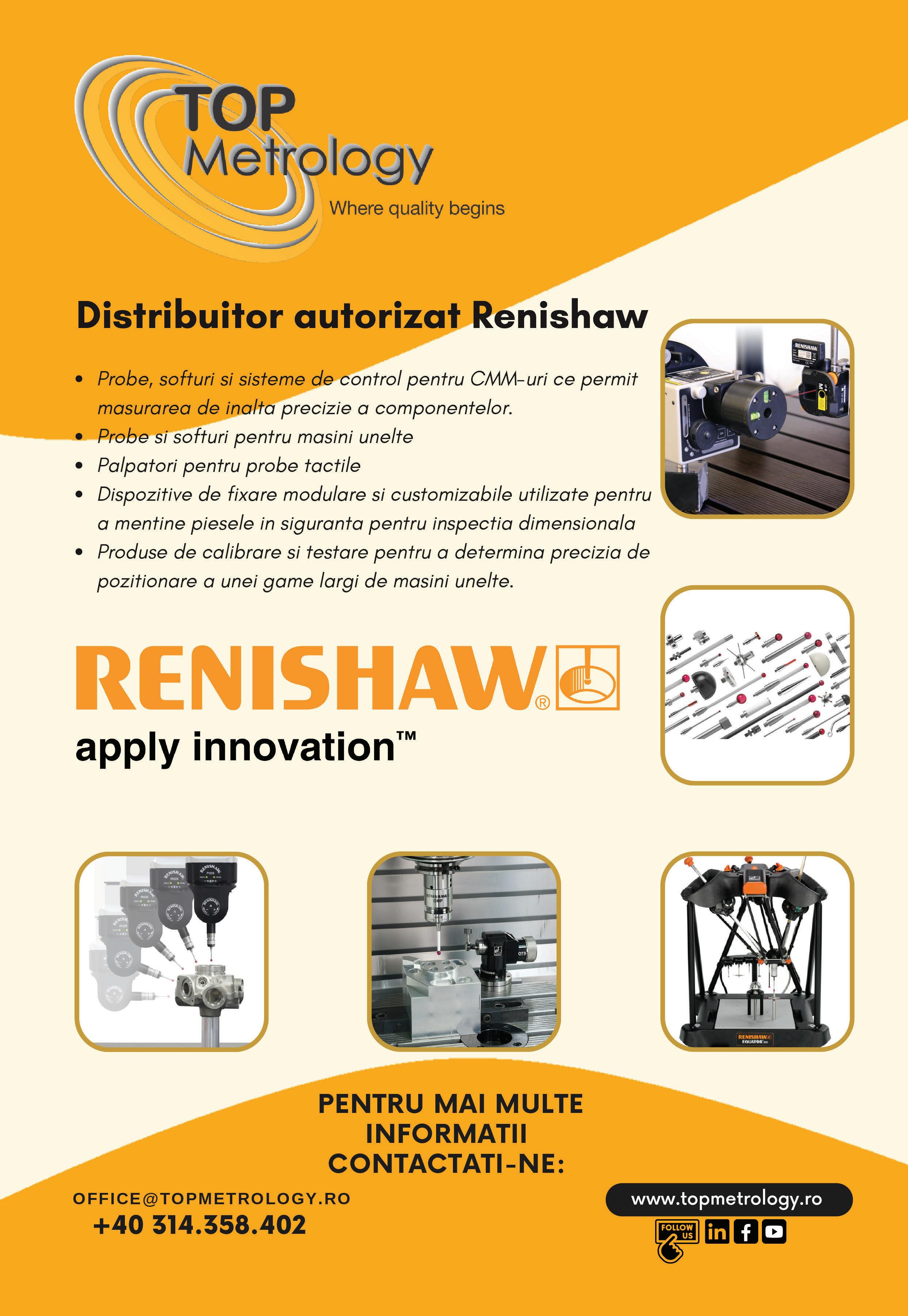
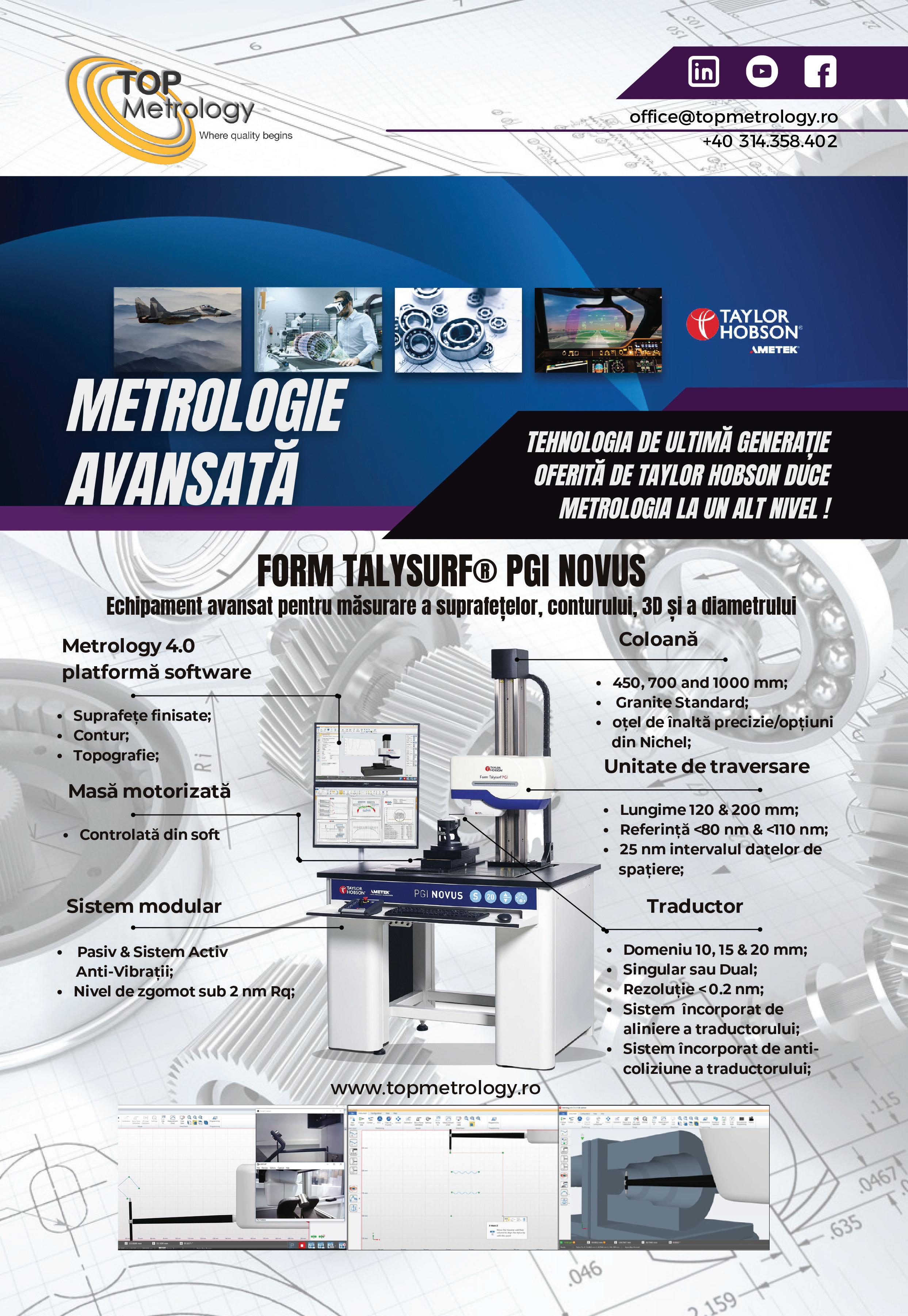