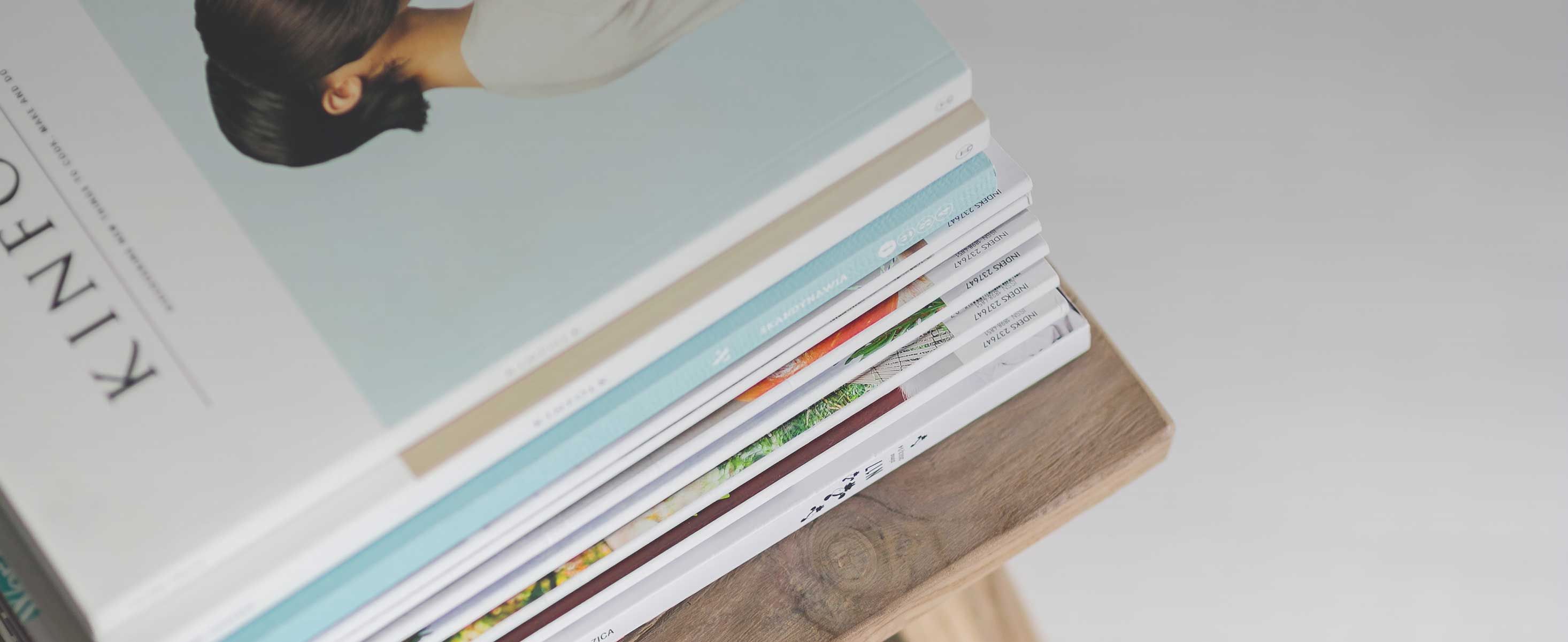
4 minute read
BIM Fabrication & Empowering Design and Construction for Health Care Industry| Tejjy Inc.
from BIM Fabrication & Empowering Design and Construction for Health Care Industry| Tejjy Inc.
by Tejjy Inc
The COVID-19 outbreak epitomizes an unprecedented test for the global healthcare system. Dealing with the epidemic and saving human lives depends to a great extent on the availability of medical supplies along with the capability of the hospitals. The United States stands at around only 2.8 beds per thousand people. The sheer pace of the epidemic enhances the question of how to expand healthcare infrastructure.
BIM Prefabrication Prospect
Advertisement
Under normal situations, the creation of large-scale hospital infrastructure takes several years to complete. Conventional construction methods aren’t designed to meet the high demand. Healthcare construction tends to be project-centric, using various stakeholders to learn about the process of working together.
BIM Prefabrication helps in manufacturing building elements off-site. Rather than a conventional linear build, where every process depends upon the next, BIM (Building Information Modeling) prefabrication technique moves in a synchronized way, leading to cost efficiency and schedule reduction. Prefabrication helps to improve safety and enhance productivity for hospitals, causing less disruption to operating campuses, adjacent areas, and the general patient experience.
Healthcare is ahead of other segments in implementing prefabrication and extensive uptake helps the industry deliver the much-needed beds faster. General contractors like J.E. Dunn, BOLDT and Mortenson have acknowledged the benefits of prefabricated BIM and thus gotten ahead of the trend. Nevertheless, to make prefabrication BIM technologies a mainstay, reforms are essential across the construction ecosystem, involving the designers, contractors and the owners.
Design Alignment Facilitated through BIM
The architects and designers need to shift from the ‘stick-built design’ towards an element-centric design. Teams are required to determine the elements to be prefabricated – be it for the bathroom pods, the ceiling of an operating room, or an exterior wall panel. It’s also important to delineate whether they will go ahead with a step further and implement an utterly volumetric modular design.
Design teams of the construction projects can then work using Design for Manufacturing Assembly principles, emphasizing the way the prefabricated elements are designed for manufacturing and ease of assembly. All project stakeholders including the subcontractors, manufacturers and general contractors should be referred to as associates from the early stage of design optimization. Digital information-sharing platforms like BIM (Building Information Modeling) and Pre-fabrication & Modularization technologies facilitate real-time collaboration, acting as powerful tools during the entire construction workflow.
Making the changes makes a big shift for design teams with significant benefits. With less time spent on ‘standard’ elements to be prefabricated, architects can emphasize the signature and complex design areas that add more value to the construction project, providing more satisfaction to the project team members.
General Contractor Embracing Prefabrication
Strategically, a general contractor needs to amend specific methods for embracing prefabrication, beginning with estimation. Using conventional estimation models, it becomes difficult to compare
multi-trade prefabricated designs while asking for credits from subcontractors and that too at risk of losing the work. However, the adoption of prefabricated BIM helped to integrate the entire work process. BIM-enabled dynamic practice helps to associate with manufacturers or subcontracting firms for understanding their prefabrication design and manufacturing competencies and implementing element-centric target costing, which envisions the prefabricated elements through multi-trade subassemblies and modules.
Hence, the General Contractors or the GC should implement a new mindset for becoming the integrator throughout the construction phase, modernizing the processes from the construction schedule to site plan integration. General contractors also should work with new supply chain associates to move into competent manufacturing approaches and develop their fabrication shops.
Subcontractors Becoming Manufacturers with Prefabricated BIM
All types of elements can be manufactured through BIM prefabrication and modularization. Apart from volumetric modular buildings, there is a whole gamut of parts including elements such as medical headwalls, plant rooms, and elevators. In healthcare, simple spaces like the patient room can be created with prefabricated elements along with complex spaces like plant rooms & operating theatres.
Subcontractors in healthcare have started becoming manufacturers, combining skills with innovative manufacturing approaches. BIM supports sophisticated, data-rich designs that can be shared with other AEC project stakeholders. Subcontractors can capitalize on automation and sophisticated quality assurance practices to further enhance production.
Owners to Request BIM Pre-fabrication
Eventually, owners are required to request prefabrication and change their behaviors for empowering in the industry. It’s not just about cutting costs but gaining enhanced certainty over the schedule, budget and building outcome. Hence, owners are necessary to work collaboratively with General Contractors and other project stakeholders to reduce risk and hold realistic expectations.
The benefit of BIM Pre-fabrication is that healthcare owners should stand to gain a lot from prefabrication. Prefabrication provides owners the opportunity to commoditize individual elements of hospital buildings like the equipment inside these facilities. Owners can also ensure a consistent and satisfying experience for the end-user, supporting patients’ treatment.
BIM Prefabrication Supporting Healthcare
So, BIM prefabrication is facilitating everyone involved in the construction ecosystem with fast delivery. With off-site manufacturing, manifold building elements can be constructed simultaneously and assembled on the site. Building components can also be stored and reserved for expanding critical infrastructure at times of extraordinary demand. BIM prefabrication also reduces the disruption of operating healthcare campuses with minimized traffic, noise, and dust.
During the unprecedented time of COVID-19, healthcare is performing exceptionally by caring for those afflicted with the virus. By implementing BIM prefabrication and modularization there’s a prospect for design and construction to speed up healthcare construction in the future and deliver beds as and when required.
To know more about BIM pre-fabrication & modularization, call Tejjy Inc. at 202-465-4830 or email at info@tejjy.com to discuss your Prefabrication and Modularization requirements in the USA.