

YOUR SUSTAINABILITY JOURNEY STARTS HERE.

Electric power is available across our range of bin-lifting systems.
Built
Wherever
Electric bin lift systems by Terberg

Welcome to our latest edition of Eagle Eye. Doesn’t time fly? It seems like only last week we were starting a new year and yet here we are half way through 2024. It’s been a busy few months for all of us at Dennis Eagle, with the European IFAT show in Munich, our US Dealer Conference, and Waste Expo in Las Vegas. It was good to see so many of our customers attending these events. The feedback and follow-up discussions we’ve had have been excellent.
This edition is packed full of interesting articles for you to enjoy. Special thanks to The City of Edinburgh team for highlighting the benefits of our powerful narrow Elite+ chassis combined with the narrow Olympus
body and Terberg bin lift. This package comes into its own when negotiating the narrow hilly streets of Edinburgh. It’s fantastic to see our customers benefiting from our unique products, which specifically focus on refuse industry requirements.
In other articles you’ll get an insight into the competitive spot and contract hire markets supported by our customers, where product reliability and ease of use is of paramount importance. There is a focus on the continuous improvement culture within our training team where we are constantly looking for new ways to meet customer needs, from eLearning for Vehicle Operator Training to offering easier ways to access user manual content.
Enjoy the read and please pop in to say hello whenever you’re in the Warwick area. It’s always good to talk.
Keith Day Managing Director
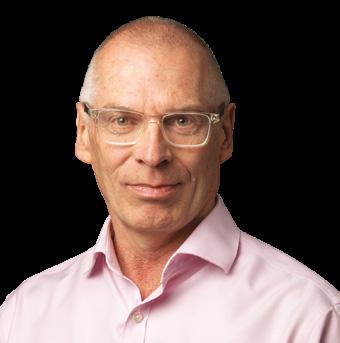
REGULARS
Fleet renewal, Dennis to the rescue, Stateside roundup
IN FOCUS
Meet new HR Director Jen Booker
THE CUSTOMER
Emma Cheeseman of Fiveways
EAGLE EYED
A selection of winning photos from our community
FEATURES
CAPITAL INVESTS
Edinburgh purchases 69 new trucks
08 12 06 10 14 20
contact Editor Amelia Jordan:
FOOD WASTE
The key to hitting 2035 target
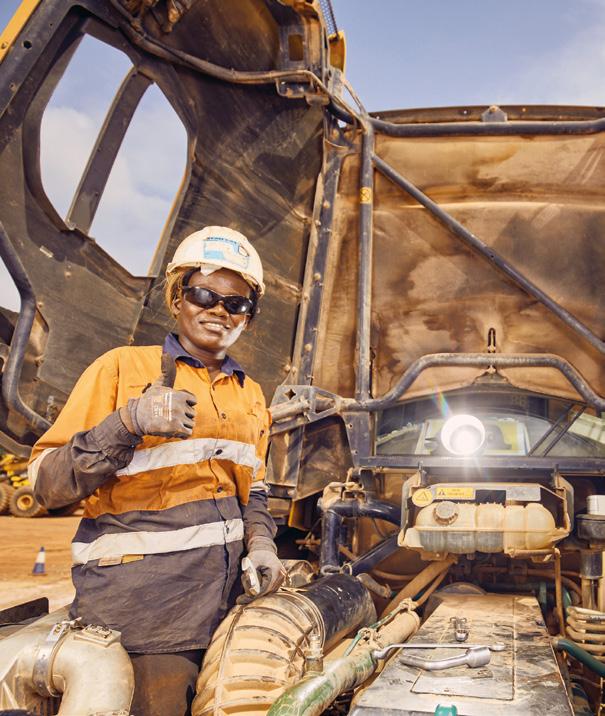
Further expansion of dedicated customer programme
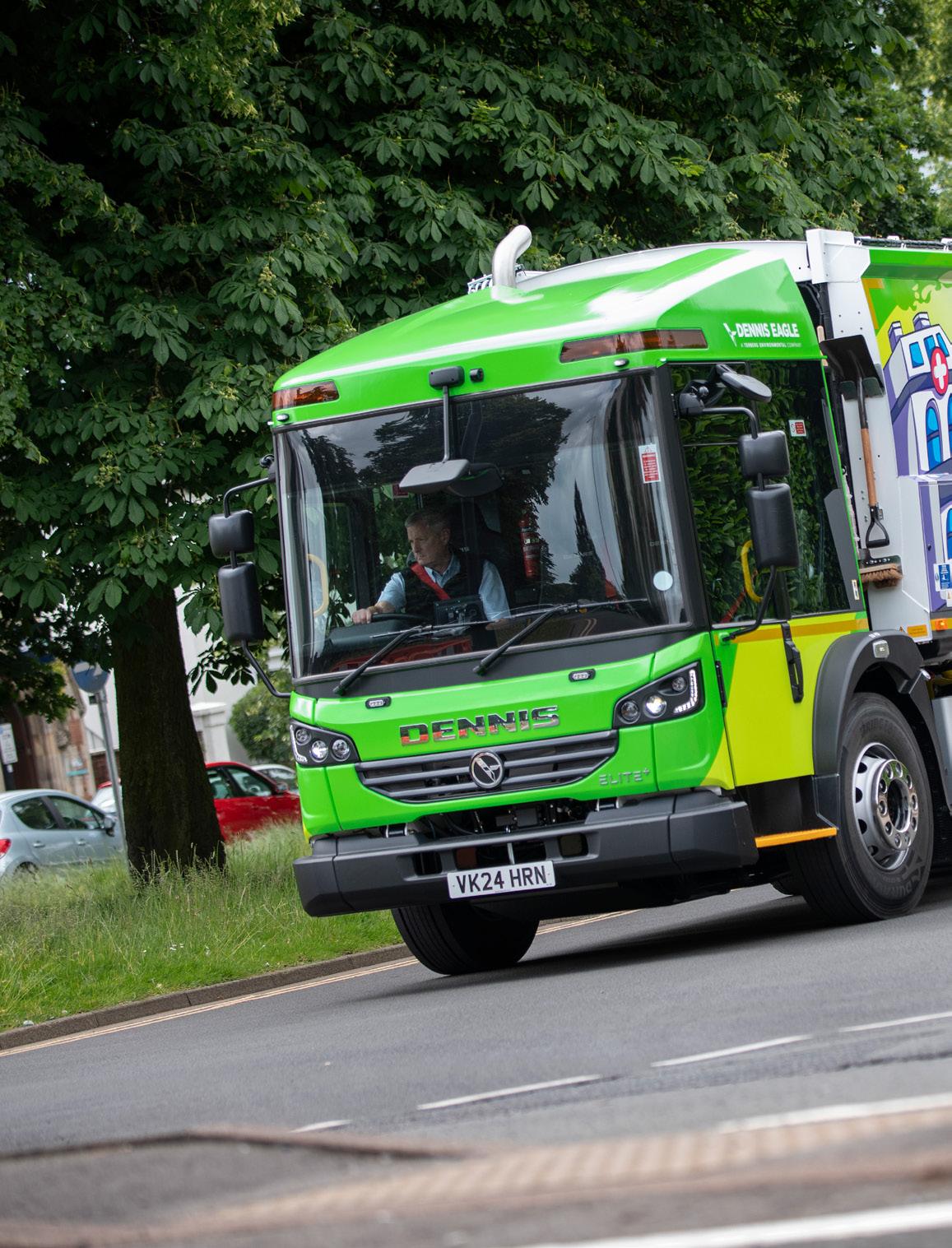
Expanding the fleet
From July we'll have three new demonstration vehicles on the road. If you see them, take a picture and upload to our socials for a chance to win prizes!
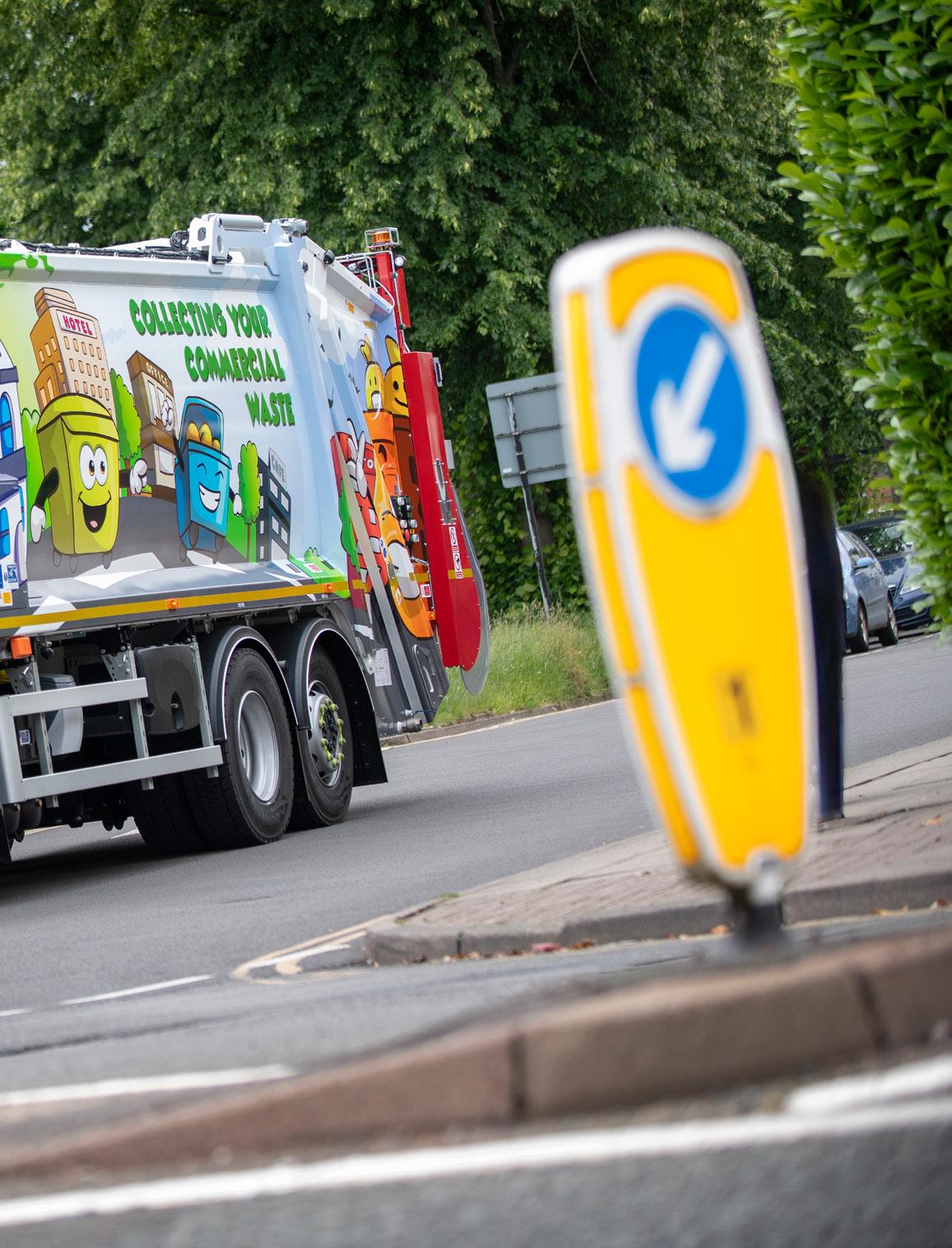
City of Edinburgh Council invests in the future
Edinburgh chooses Dennis Eagle to support its commitment to improving residential refuse collection.
Dennis Eagle is powering the biggest vehicle investment the City of Edinburgh has ever made as its council commits to improving services across Scotland’s capital.
The City of Edinburgh Council has invested in a major fleet-replacement strategy, which sees 17 new Dennis Eagle vehicles being delivered now, and 52 more to come later in the year. The new narrow width trucks are part of the council’s continued programme to deliver a seamless waste collection operation to residents.
The perfect
fit
Residential refuse collection is quite the operation in Edinburgh. Home to over half a million people, the council’s refuse teams will typically lift up to 1,900 bins on each route per day, collecting over 15 tonnes of waste. Not only does the populous nature of the city make refuse collecting a significant task, but the steep,
medieval streets of Edinburgh pose a number of headaches when operating large vehicles.
It is because of these conditions that the council ordered 59 26-tonne vehicles and 15 18-tonne narrow RCVs from Dennis Eagle.
A positive relationship
Our vehicles have been helping to keep Edinburgh’s streets clean for two decades and Dennis Eagle accounts for around 90% of the city’s 100-strong refuse vehicle fleet. This relationship has endured because of the consistently positive feedback the vehicles receive from those who operate them.
As with any good relationship, both parties are looking to the future. Edinburgh Council entered five of our eCollect eRCVs into service last November, with funding provided by Zero Waste Scotland. As the path towards net-zero becomes more critical
with each passing year, electric vehicles are a step towards a greener future.
Cllr Scott Arthur, Environment Convener, said: “We’re committed to investing in our fleet and where possible we’re going electric.
The feedback from staff using the five electric refuse collection vehicles shows they are making a real difference to our residents, operating a quieter service, and improving air quality - already saving over 100 tonnes of carbon emissions.
“The new vehicles have also improved visibility for our drivers and have cycle safety features, making them safer for vulnerable road users as well as protecting our staff.
“All of the waste vehicles we purchased are narrow-bodied and shorter, which really works in Edinburgh and gives our drivers more flexibility in narrow streets with tight areas.”
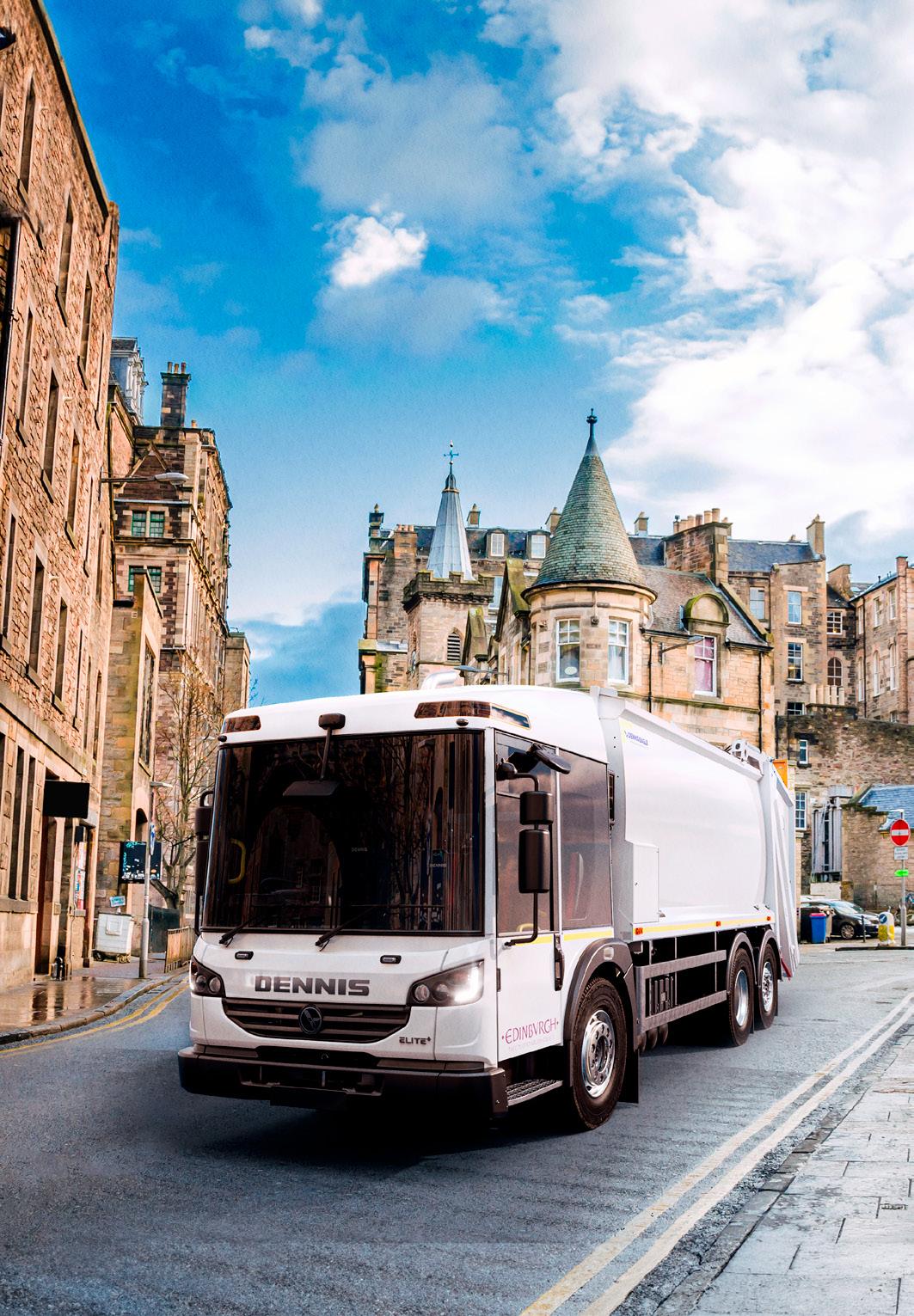
All of the waste vehicles we purchased are narrow-bodied and shorter, which really works in Edinburgh and gives our drivers more flexibility in narrow streets with tight areas.

Lincolnshire’s West Lindsey District Council renews 12-year relationship with Dennis Eagle
Part of a four-year framework that allows authorities within Lincolnshire to utilise the same purchasing route, West Lindsey’s four new Dennis Eagle vehicles will join its 16-strong RCVs fleet, which are all Dennis vehicles. The fleet is primarily made up of 26-tonne narrow-width vehicles, but the council also operates two 16-tonne vehicles.
West Lindsey covers 460 square miles of Lincolnshire. Predominantly rural, it encompasses the Lincolnshire Wolds, an official Area of Outstanding Natural Beauty. Its biggest urban area is Gainsborough, a town of 23,000 residents (and the capital of England and Denmark for five weeks in 1013!).
West Lindsey’s residential waste
collection operation serves 45,000 properties every week, from town to country. “While Gainsborough’s our main town, a high proportion of our area is extremely rural,” says Rob Gilliot, Operational Services Manager at West Lindsey District Council. “We use the smaller vehicles for the really tight areas around Gainsborough, and the bigger vehicles work across the rural areas.
“Our bin collections range from 700 a day to 2,000 a day, and we’re averaging around 100 miles a day per vehicle due to the rural nature of the operation.”
Dennis Eagle has been supplying RCVs to West Lindsey since 2012 through a procurement process led
by Lincolnshire County Council. “It’s a nice easy process for us as a local authority to use,” says Rob. “It’s a bit like being at a restaurant – we get a menu from the council’s purchasing team and our rep from Dennis Eagle of the different vehicle sizes, the types of bin lift, and the bolt-ons such as cameras, safety equipment, etc. We make our selection, and the vehicles are delivered fully branded with all the equipment fitted.”
West Lindsey avoids having to refresh its fleet all at once by making two to four new RCV purchases every couple of years. “This means we never have a lorry over six years old, which is important with the amount of miles they have to cover every week.”
Stateside Roundup
Our US Dealer Conference 2024, held at our North American headquarters in Summerville, South Carolina, at the start of March, was a great success. It was a fantastic opportunity for US dealers to discuss innovative ideas, exchange insights, and look ahead to the future with confidence. The conference theme was ‘Energising together with mutual growth’, celebrating strong growth across many areas of our North American operations over the last 12 months. This has included investing in aftermarket functions, enabling us to hire expert factory technicians and establish a dedicated technical help desk that supports our dealer network.
We have also announced new processes and systems that will further enhance our trucks and our dealer support. We are implementing new sales and service system portals, introducing Terberg Connect telematics on all trucks, with the capability to flash updates remotely, and launching next-generation Parts EPC, which includes full ecommerce capability and end-user configuration to drive sales directly into dealers.
Our exciting partnership with global NGO ‘Together for Safer Roads’ was also on the agenda, with a discussion with the organisation’s executive director, Peter Goldwasser. Road safety is of paramount importance to us, and we firmly believe our ProView chassis makes a hugely positive impact on improving safety on the roads of North America and Canada.
Changing behaviour through education
Dennis the Dustcart has been helping the Year 3 children at Ruskin Junior School to explore the importance of recycling. Our sustainable school programme supports the children in understanding how to recycle and the importance of recycling.
Through their learning the children in the three Year 3 classes discovered how materials that are recycled are collected, sorted and reused. One class, produced a class assembly based upon the journey of a plastic bottle after it was picked up by a seagull and dropped into the River Thames.
The children followed the bottle to see the impact it had on the environment and they shared the importance of reducing plastic waste in our environment and sea. Amelia Musty-Jackson, year 3 teacher commented, “Dennis’s wonderful resources have really supported our in class work and the children have a deeper understanding of the three Rs.”
The only low-entry, high-visibility cab designed for safetyfocused waste operators, the ProView, was on display at WasteExpo 2024 at the Las Vegas Convention Center in May. North America’s largest solid waste, recycling, organics, food waste recovery, and sustainability tradeshow, WasteExpo, was a fantastic opportunity to show off why the ProView has made waves in the low-entry chassis market in the US.
A huge thank you to everyone who stopped by the Dennis Eagle Booth to chat. We loved meeting everyone and discussing ProView's unique qualities for the North American market.

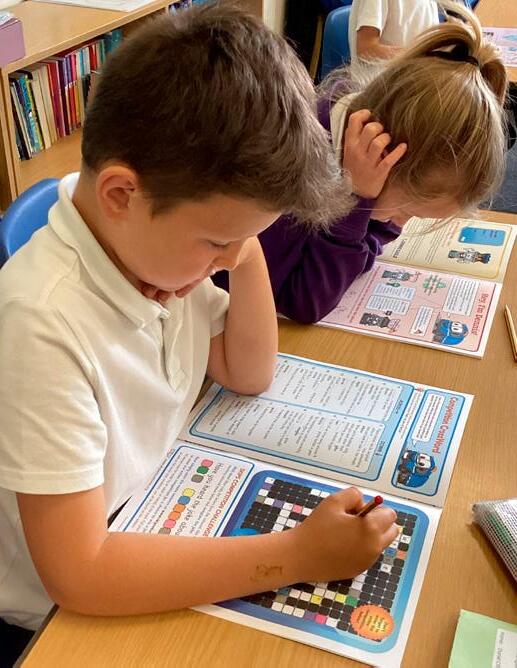
Border International have recently taken delivery of their new pickup, complete with Dennis Eagle livery!
Food waste could hold key to UK hitting recycling target
With household recycling rates continuing to plateau at around 45% the potential to increase food waste recycling will be vital if the UK is to meet its target recycling rate of 65% by 2035.
Last year, the UK government announced its ‘Simpler Recycling’ campaign to improve recycling rates through the streamlining of the recycling process for households and businesses, and by putting an end to potential confusion over what can and can’t be recycled.
Under the new requirements, all local authorities in England must collect the same recyclable waste streams from households. These include paper and card, plastic, glass, metal, food waste, and garden waste. In addition, all non-household municipal premises in England (such as businesses, schools and hospitals), must arrange to have the same set of recyclable materials (with the exception of garden waste)
collected for recycling or composting.
Whilst Simpler Recycling will hopefully serve to make things easier for people at home or work, it will definitely present some challenges for the local authorities and business charged with collecting and recycling it. This is certainly the case when it comes to food waste, with only around half of English local authorities currently providing a dedicated food waste collection service. Whilst food can be effectively recycled, its collection does present some challenges. Unlike other waste streams it cannot be commingled with other materials. If it were to be mixed, it would contaminate the other materials destroying their commercial and environmental value. It is also virtually impossible to separate out food from other materials during any form of waste processing. The only exception to this might be the potential to commingle food with green/garden waste but this would significantly
limit the recycling options available. It has also been shown to yield smaller amounts of food waste than when it is collected on its own.
As a result, it is likely that most local authorities and waste collection companies will have to rethink and potentially revamp their whole recycling collection setup. How they do this will depend on how they believe they can most effectively collect the required waste streams. This might include the need to run more vehicles in order to collect waste streams separately or utilising more multi compartment vehicles capable of collecting several waste types on a single round. These decisions will be based on a host of variables such as waste volumes, types of housing and vitally the waste processing facilities that are available.
The next and perhaps the most obvious challenge to implementing food waste recycling for all is the
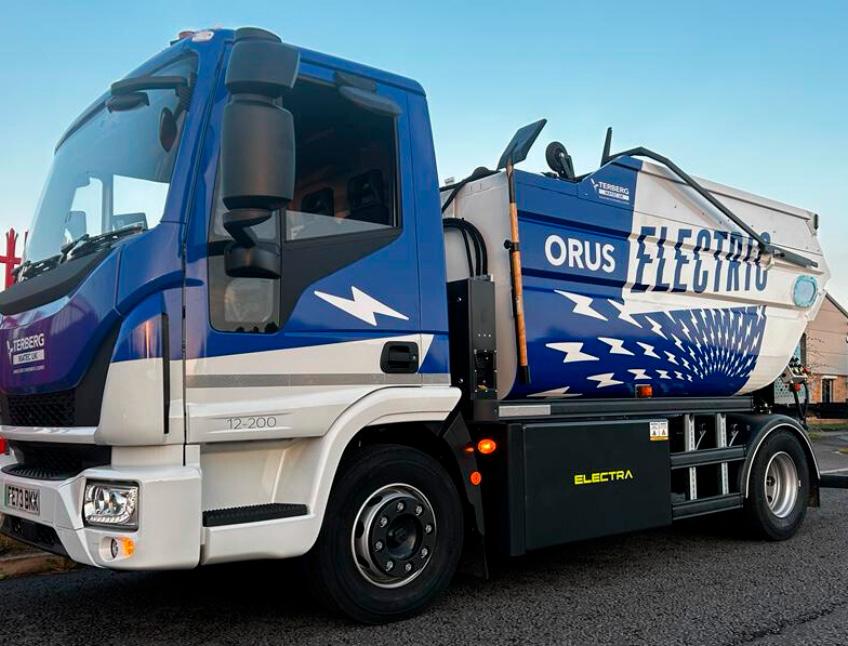
funding. The government recently announced that councils in England will be supported with up to £295 million in funding to introduce weekly collections. This is intended to cover new food waste containers for homes and specialist collection vehicles and will be targeted at local authorities that have yet to fully put a food waste service in place. There is however a significant question mark as to whether this will be enough.
Given the relatively short timescales it is also easy to envisage issues around the procurement and supply of vehicles and other infrastructure need to shift all households to a weekly food waste collection.
Another factor which needs to be considered is the government’s announcement that local authorities will also be required to provide at least a fortnightly collection for residual waste alongside a weekly food waste collection. This stance on
restricting options of residual waste collection frequency is slightly baffling given the overwhelming evidence that exists about how restricting residual waste collections reduces costs and increases recycling. And the fact that 80% of respondents to the government consultation disagreed with the proposal. The requirement for weekly food waste collections for households will also reduce the likelihood of any issues resulting from residual waste that is not collected meaning the frequency could in principle be lowered. This decision will put additional pressure on collection fleets and prevent vehicles being freed up to support additional recycling collections.
So in summary, while the next few years look set to be challenging they will also provide the opportunity to realise a genuine step change in the way we manage these valuable resources and the move to a world beyond waste.

Feature courtesy of Lee Marshall, Director of Innovation and Technical Service, CIWM.
Meet Jen Booker, Dennis Eagle’s new HR Director
With just under 1000 staff, more than 20 sites across the UK and some exciting developments planned to build, nurture and develop the team in 2024, it’s set to be a significant year for the growing HR Department.
How has your own career progressed at Dennis Eagle?
I joined the company back in 2009. At that time, there were just three of us in HR for the 550 staff. Like so many of us, I’ve had the fortunate opportunity to develop, learn and progress – as well as putting my own stamp on things. My latest move is to take on the role of HR Director. So much has changed since 2009, but the one constant is the group of fantastic people we have that put their all into this business day in, day out.
What’s been a key highlight during your time?
There are so many great things the team has achieved but one that we are particularly proud of is our wellbeing and mental health programme. In the past, mental health didn’t always get the appropriate focus, especially in manufacturing environments. We’ve really embraced it, through specific training for managers, mental health first aiders, counselling services and dedicated ‘absence and wellbeing’ staff in HR. It’s been such a positive experience for all of us. Another great achievement for the business that we have supported is the achievement
of the Investors in People Silver Level Accreditation for the whole UK business in 2022. This demonstrates our commitment to developing and supporting our people and to strive for improvement year on year.
What’s coming next?
Lots! In 2024, we’ll be focussing on leadership development for our people leaders to ensure colleagues and customers continue to receive the support and quality they love about Dennis Eagle. With the constantly changing world, we’ve also got to adapt our strategies for recruitment with a greater emphasis on making it simpler to apply, encouraging more diversity and promoting inclusivity – as well as all the benefits such an approach offers. Colleague retention is such an important part of our 2024 ambitions too, so expect to see us asking for more feedback from our people, highlighting and building on the various benefits we offer as well as further publishing career progression opportunities at Dennis Eagle. These positions are open to everyone and we really do want to encourage internal mobility across sites and departments for those that are looking for new challenges.
It sounds like a very busy 2024, so what’s planned outside of work?
The pandemic offered an opportunity for me to explore new hobbies and interests. One I have kept up with for the past few years is running (slowly!)
and trying to keep fit. I’m planning to do my second 10K in July and hopefully a half marathon in October – now it’s in Eagle Eye, I know you’ll keep me to it! 2024 is about travel too as we’ve bought a campervan, so there are some big adventures with the family that are being cooked up!
#VanLife
One thing your colleagues might not know about you…
Speaking of ‘cooking up’, we are big foodies at home and create and share plant based recipes in our online recipe book called VeganEat. I am passionate about trying to make more sustainable choices for the future of our beautiful planet, and making plant based eating accessible for people, is a fun part of this.
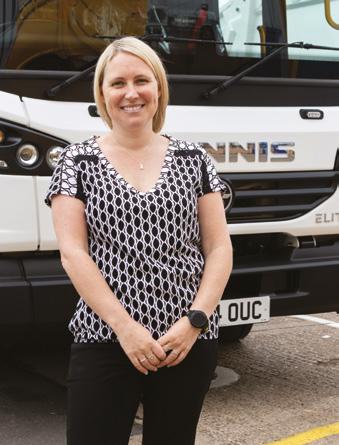
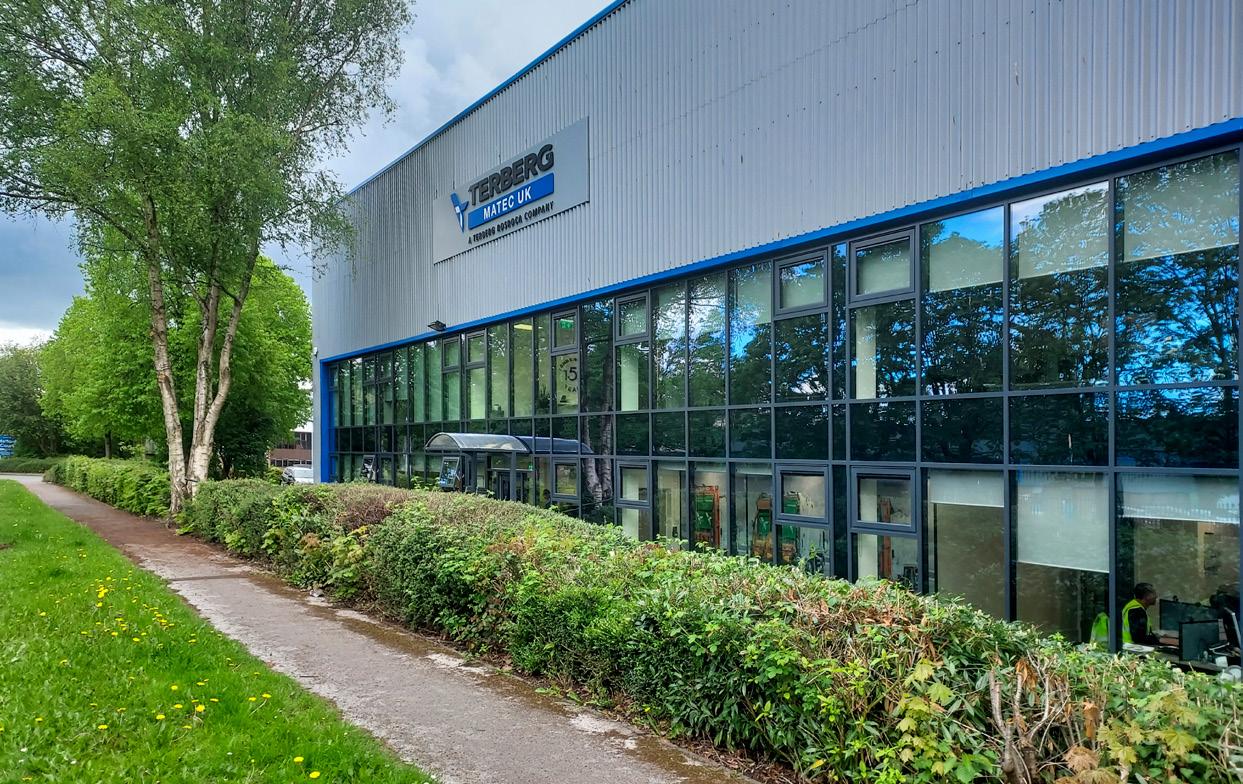
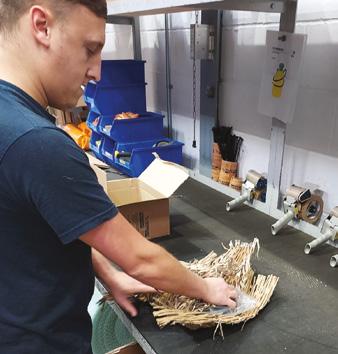
In June 2022, Terberg Matec UK started its journey towards implementing the holy grail of Environmental Management System (EMS) standards: ISO 14001. In October 2023, the hard work was worth it, with approval gained.
Terberg’s main focus was repurposing suitable cardboard waste as void-fill packaging, and a cardboard shredder was purchased. “The results have been quite astonishing,” says Mick Bullock, Parts & Quality Manager at Terberg Warrington.
“Almost 5.5 tonnes of cardboard waste have been repurposed in the last 12 months, we do not use polystyrene packaging pellets in the packing
Terberg drive sustainability improvements
process at all, and we have reduced bubble wrap consumption by 400kg.”
The CO2 emissions associated with waste collection and packaging delivery have been halved, while the initiative has resulted in a 70% saving on bubble wrap and a 100% saving on polystyrene. In addition to sustainability improvements, these changes have delivered a substantial financial saving.
A culture of collaboration and open discussion has led to further improvements, including correctly disposing of items that fall under the scope of Waste Electrical and Electronic Equipment (WEEE) and migrating to cordless tools.
“The cost to charge a cordless battery is minuscule compared to running a compressor all day,” says Bullock.
Terberg has also introduced reusable tote boxes to supply spare parts to the workshop. Historically, they had been packed into a cardboard box that was usually disposed of, and this simple but effective idea has delivered further cost savings reduced cardboard waste.
“Gaining ISO 14001 accreditation was a great achievement that was only possible with the help of all staff,” says Bullock. “Of course, the journey did not stop there. In fact, it was just the beginning, and by following the key principles, we strive to continually improve year on year.”
Dennis Eagle invests in the future of vehicle training
Dennis Eagle’s dedicated customer training programme is growing from strength to strength. Having recently expanded the team Dennis Eagle also has plans to launch a new eLearning element to complement its in-person offering later this year.
Last year, Dennis Eagle trained over 700 customers. This year, there are a few remaining dates available to customers keen to expand their knowledge of operating, repairing, and maintaining their refuse vehicles.
“We’re always working really hard to deliver a great relationship with our customers, and our training programme is part of creating that customer-first culture,” says Alice McCabe, Learning & Development Officer at Dennis Eagle.
Training options
Dennis Eagle’s training programme, which has been running since the early 80s, is split into three categories: Vehicle Operator Training, Technical Training, and Electric Vehicle & HV Systems training. All courses are created and delivered by a team of dedicated Dennis Eagle trainers, with more being recruited to meet demand.
Vehicle Operator Training is carried
out at customers’ sites when they take delivery of a new vehicle. The training demonstrates the key functions and new features of the vehicle, and includes instruction on loading and tipping procedures, driving controls, and in-cab options. Technical Training has six courses: Elite+ Chassis, Olympus Body, Electronic Truck Steering, Olympus Twin Pack, Beta 2 Bin Lift, and Toolbox Training. Each course provides delegates with the skills and experience to recognise faults and carry out repairs and maintenance.
“Technical training is at our Service Centre in Aldridge in Walsall throughout the year,” says Alice. “However, we can be flexible, so if a customer can’t come to us, we can go to their site instead.”
For Electric Vehicle & HV Systems training, Level 2 and Level 3 courses are available. Level 2 is online, while Level 3 is a four-day course at Aldridge, run in partnership with industry specialists, Autotech Training. For all courses at Aldridge, Dennis Eagle can help customers book hotels if needed, and lunch is provided.
Looking to the future
While Dennis Eagle receives overwhelmingly positive feedback
from customers, that doesn’t mean it's resting on its laurels. “We work hard to deliver an even better training experience by constantly looking for new ways to meet customer needs,” says Alice.
This includes building a Digital Training Academy for Vehicle Operator Training, which will be showcased at RWM in September. Customers will receive the eLearning programme at the point of vehicle delivery. “We believe it will be more efficient for customers because they won’t have to take their workforce off refuse collection rounds,” says Alice. “Customers will also have the option of requesting a trainer to visit their site to deliver further operator training if needed. It’s about providing more time efficient and cost effective offerings as possible.”
Dennis Eagle are excited to be able to provide their customers with the platform to allow them access to “in the moment of need” information.
“They will be able to log on from their laptop or mobile and click on bitesize chunks of learning content including videos and reference guides” says Alice. “This means they will no longer have to flick through a physical user manual, allowing quicker access to information needed”
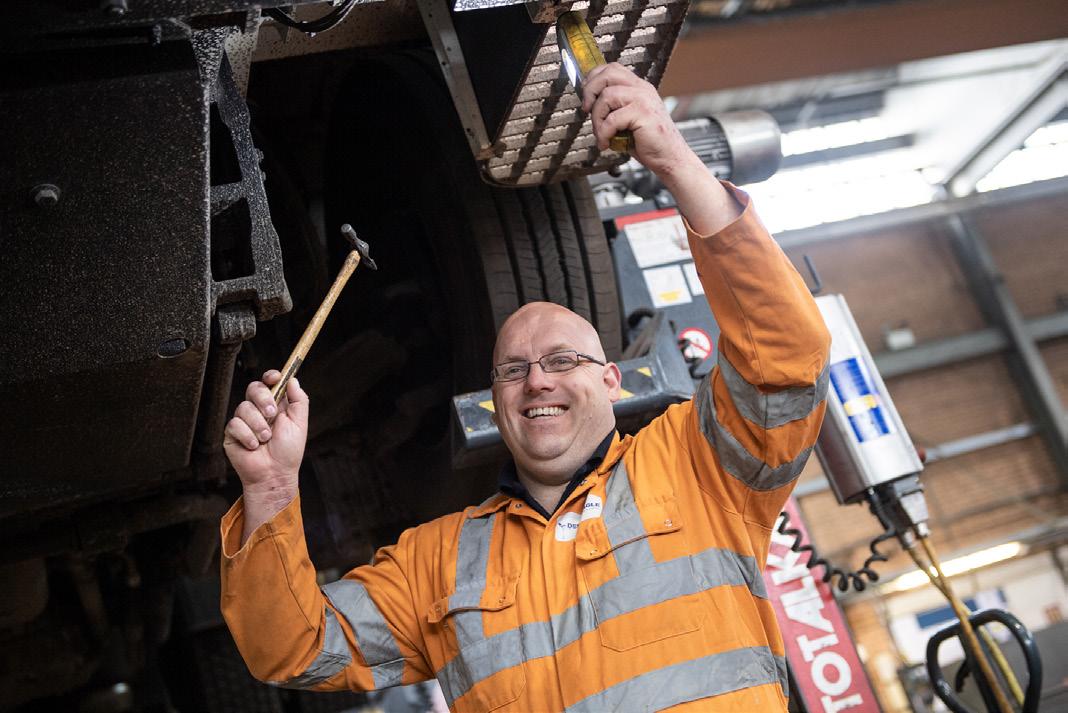

Get booked in
Dennis Eagle has a number of available dates remaining this year for its Technical Training courses at Aldridge:
Elite+ Chassis (Available July, August, September, October, November, December)
Olympus Body (Available August, October, November, December)
Olympus Twin Pack (Available September)
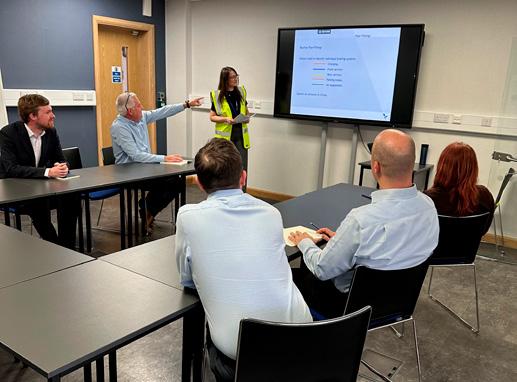
Beta 2 Bin Lift (Available August, November)
Level 3 EV Training (DE eCollect) Master Tech Qualification (Available July, August, September, October, November, December)
To book a training course, visit here. If you have any questions, please contact our Dennis Eagle Training team directly on customertraining@ dennis-eagle.co.uk, call 01926 458 500, or visit https://dennis-eagle.eventbrite.com
New cybersecurity measures bring extra peace of mind
Dennis Eagle secures UNECE R155 certification
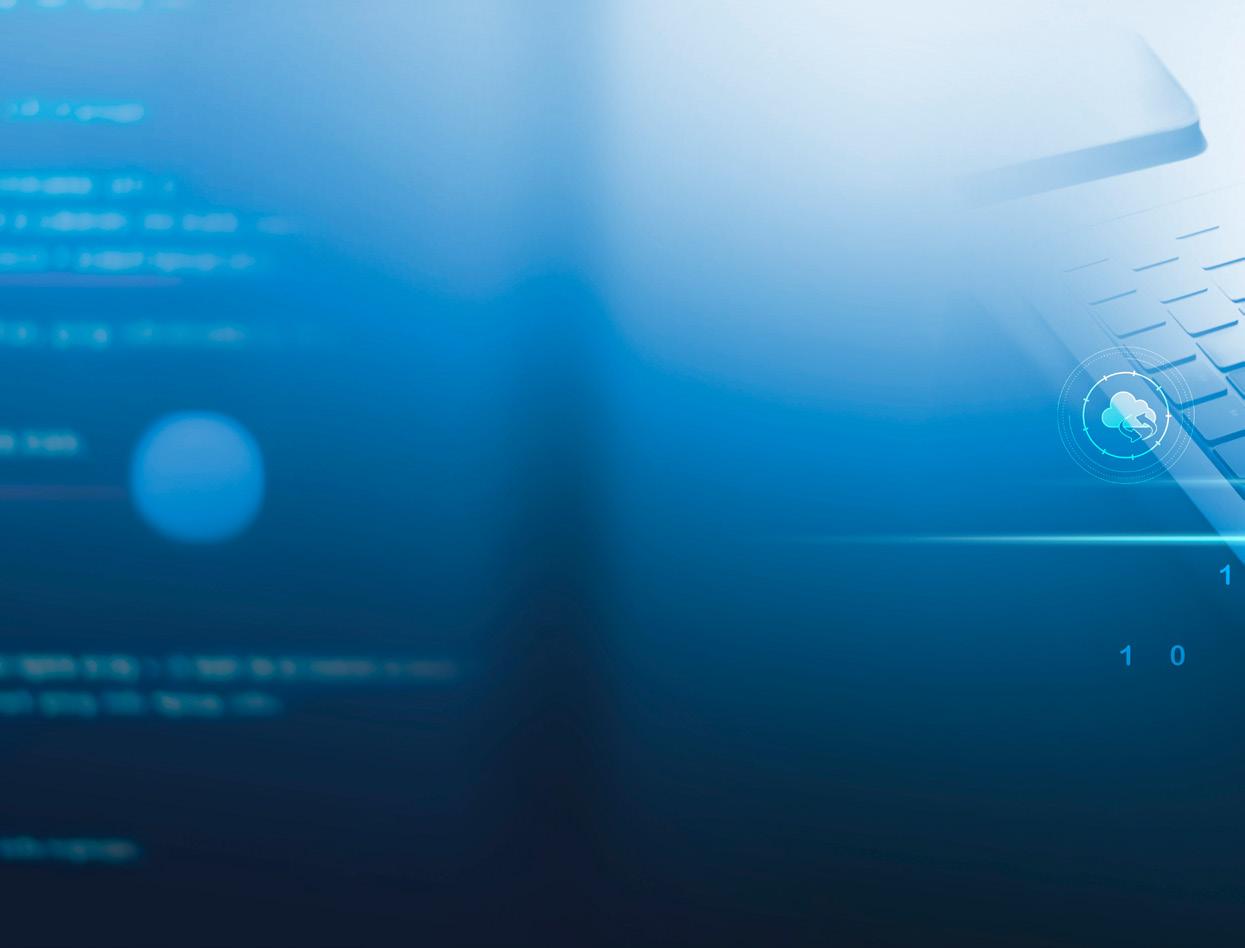
With the increasing adoption of digital technologies in vehicles that rely on networked software and data exchange, cybersecurity is a growing threat globally. Dennis Eagle has just completed a vital step in helping to protect its customers – and there’s more to come..
The predominant cybersecurity risk to be addressed by vehicle manufacturers is the potential for the remote control of vehicles by hackers, from scammers to state-level terrorists. Once control is taken – the most likely entry point into the vehicle being the telematics – this can lead to ransom demands affecting a fleet’s ability to collect refuse for a period of time, or much more seriously, for the vehicle to be used as a weapon in a public space. Whatever the motive, there is a considerable growing financial and reputational threat to
businesses and authorities.
A new regulation, UNECE R155, is designed to protect vehicle operators and the public from the cybersecurity risk. This regulation affects the entire automotive industry and compliance is compulsory. UNECE R155 covers product security as well as the people, processes and technology required to implement a Cybersecurity Management System (CSMS).
At Dennis Eagle, achieving UNECE R155 certification has been a dedicated project overseen by Head of Vehicle Cybersecurity, Manu Gowda. Manu has been working across almost every organisational function within the company since April 2023 to introduce new measures, systems and processes and he was delighted to receive Dennis Eagle’s UNECE R155 certificate last month.
“You can view a Dennis Eagle vehicle as being a collection of many computers, each of which could potentially be vulnerable to attack. An average refuse truck contains 35 to 40 electronic control units (ECUs) from brake and steering control units, to motor control and battery control units,” explains Gowda.
“The key part of the legislation is that it requires these ECUs to be cyber secure. Cyber secure means that ECUs identified as being critical must have a firewall installed. So, in the past 18 months, we have been working with our suppliers to undertake this exercise, which involves setting a risk threshold, then evaluating and mitigating the risks of the component or system, documenting our processes with the Vehicle Certification Agency (VCA) who audited us for five weeks,” continues Gowda.
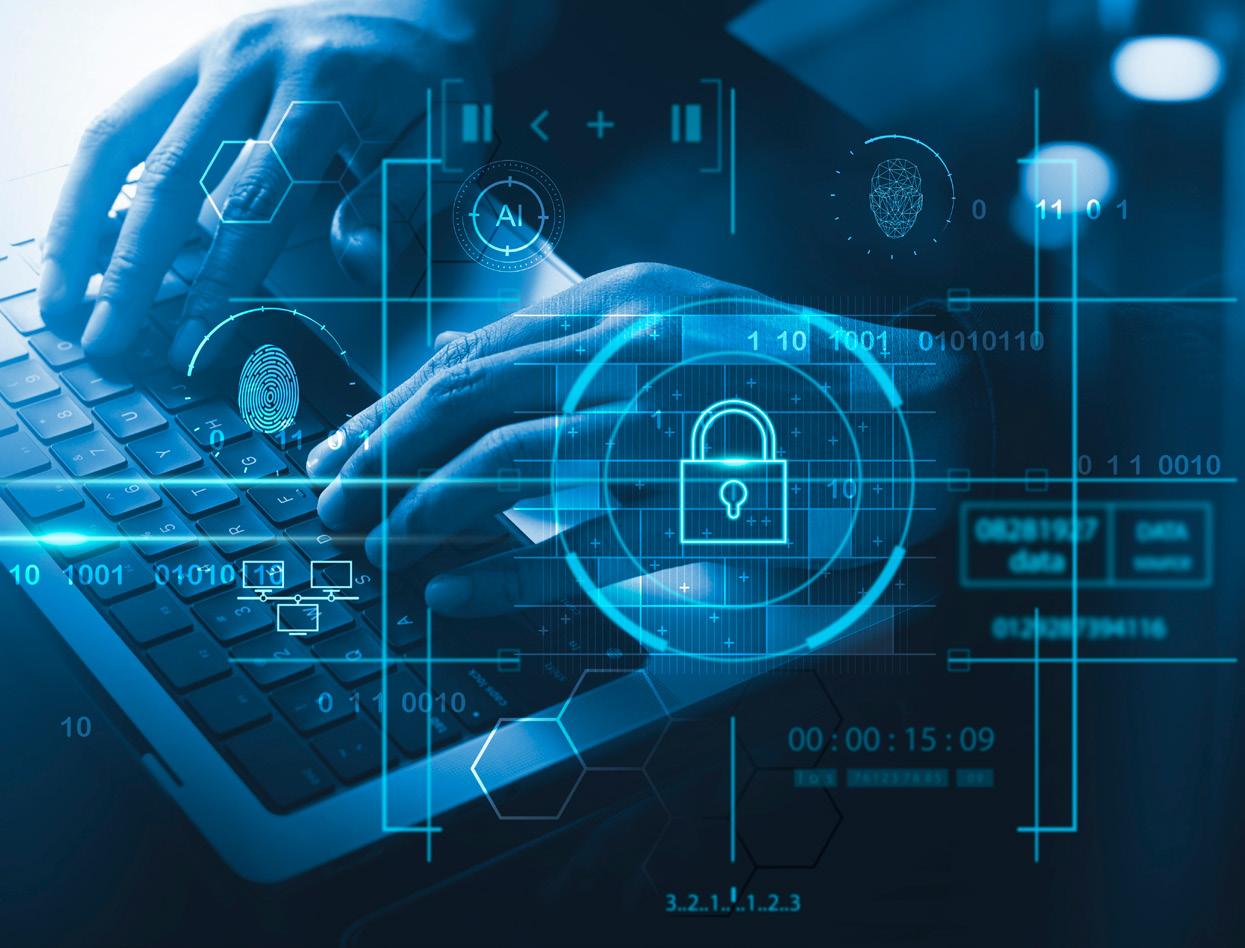
“The process has involved a lot of cross-functional working: an indirect team of 15 colleagues in purchasing, sales, aftermarket, engineering, quality and HR has been working together. We received some positive comments about our way of working from the VCA. We must also credit our suppliers who share our serious approach to cybersecurity. Between us, we have generated thousands of pages of documentation covering threat assessment and remediation analysis.”
Hackers are determined of course and will persevere to find workarounds to cybersecurity measures. That is why a manufacturer’s R155 certification only lasts for 18 months, why manufacturers are continually audited and why another regulation, UNECE 156, has also been introduced. UNECE 156 ensures that any software updates to control units need to be securely updated and
come from a trusted source. Dennis Eagle vehicles will be compliant with UNECE 156 during 2025, in line with the regulatory timeline.
“Cybersecurity is certainly not a one-time exercise; it’s an infinite game,” says Jon Sayers, Engineering Director at Dennis Eagle. “The legislation requires OEMs to continue to demonstrate they understand the evolving risks and have a plan in place to continue to address them.
“Dennis Eagle is committed to continuous improvement. We will keep updating the firewalls to keep a step ahead of the criminals. As such, our customers can have confidence that our new vehicles, whether diesels or EVs, are more secure than ever and that we are doing everything we can to protect them and their customers,” concludes Sayers.

Manu Gowda, Head of Vehicle Cybersecurity.
Fiveways looks to the future
A fleet of 25 new Dennis Eagle vehicles is playing a pivotal role in Fiveways’ spot hire growth
When Fiveways decided to expand its UK-wide spot hire operations, it turned to Dennis Eagle to boost its fleet of RCVs. An order of 25 Elite+ vehicles continues a fruitful relationship between Fiveways and Dennis Eagle that stretches back 20 years. Over the last five years, Fiveways has purchased over 200 vehicles from Dennis Eagle and this new order complements the existing fleet.
“We have almost all of our vehicles out on spot hire at all times, and with the utilisation rate so high, it felt like the right time to expand the fleet,” says Emma Cheesman, Head
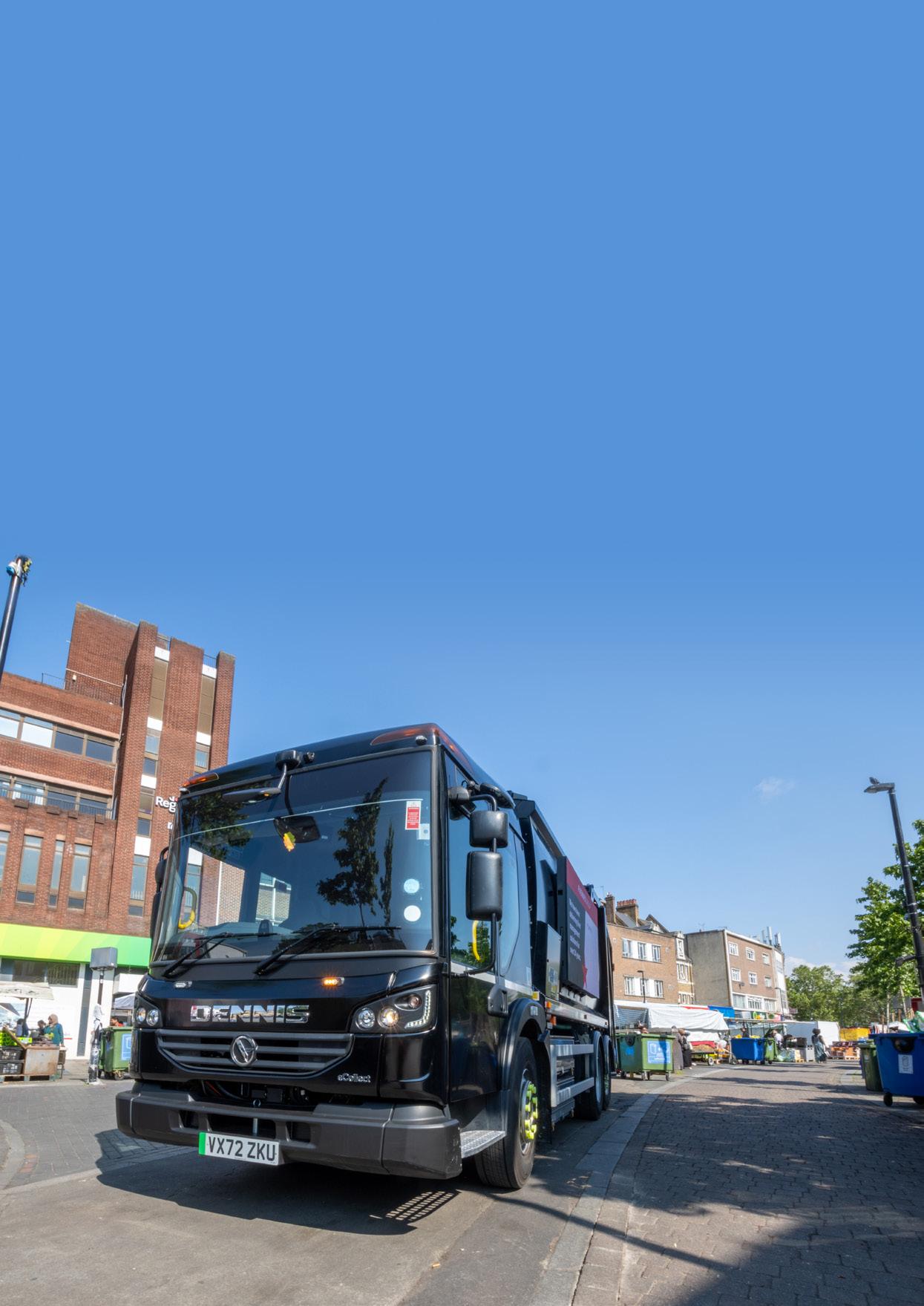
of Development at Fiveways. “Many of our spot hire customers specify that they want Dennis Eagle, so it was perfect for us to work with them again.”
Nationwide growth
Founded 25 years ago, Fiveways has grown from strength to strength and has become a respected leader in the industry. Employing a dedicated team of professionals, its base is in Essex, but its spot and contract hire service is growing nationwide. Spot hire makes up 70% of its operations, with customers in the private and public sectors.
“We pride ourselves on our customerfocussed approach, which is often the deciding factor for businesses choosing to work with us,” says Emma.
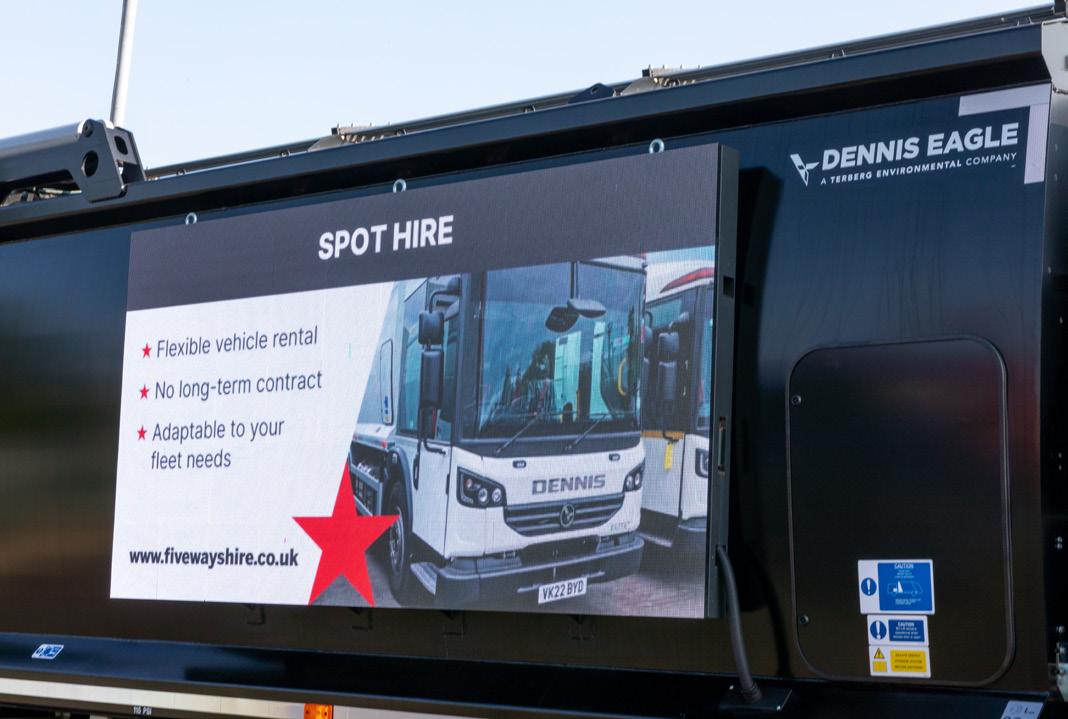
“We’re incredibly responsive, for example, if we get a call late afternoon for a spot hire, we’ll ensure the vehicle gets out to our customer, having been fully inspected, the following morning before service delivery. We are able to offer this service as we have a fully equipped vehicle maintenance facility that offers not only service inspections but also tacho calibration and MOTs.”
Providing best-in-class vehicles
Fiveways’ reputation for quality is built on its commitment to supply best-in-class vehicles to its customers. This is why 80% of its RCV fleet is manufactured by Dennis Eagle. With many of its customers hiring RCVs, Fiveways knows it can rely on Dennis Eagle’s specialist knowledge and experience in the waste management industry.
“Most local authorities operate Dennis Eagle vehicles, so naturally, when they
need spot hire vehicles, that’s what they want because their drivers and operators are familiar with Dennis,” says Emma. “They are the vehicle of choice and is very popular in the market.”
Emma says customers like the ergonomics of the Elite+ cab, and the regular updates with additional features. “The nice thing about Dennis Eagle is that they’re constantly looking at improving their products,” she says. “If you look at the Elite and the newer Elite+ cab, improvements have been made to the overall comfort for the driver and the crew, along with even better direct vision.
A critical element of spot hire is ensuring the vehicles are always on the road. Having vehicles in the yard means lost revenue and is damaging to brand reputation.
“It’s rare there’s a problem with any Dennis vehicle because they’re so
reliable, but the very few times there is, the care you get from the service department is really good,” says Emma. “They are very responsive and also excel at parts availability.”
Future-proofing growth
Fiveways’ expansion will be built on reliability. That means reliable customer service, reliable costs, and reliable vehicles.
Fiveways is also innovating to stay ahead of the game. It is launching new patented LED screens that can be mounted onto the side of its refuse vehicles. “It allows our customers to continuously advertise their messages - whether that’s recycling rates or service changes, for example. It is an innovative way for businesses and local authorities to engage with their customers and wider communities.”
Three is the magic number
The Narrow, Trade and Food Waste vehicles are added to Dennis Eagle’s fleet.


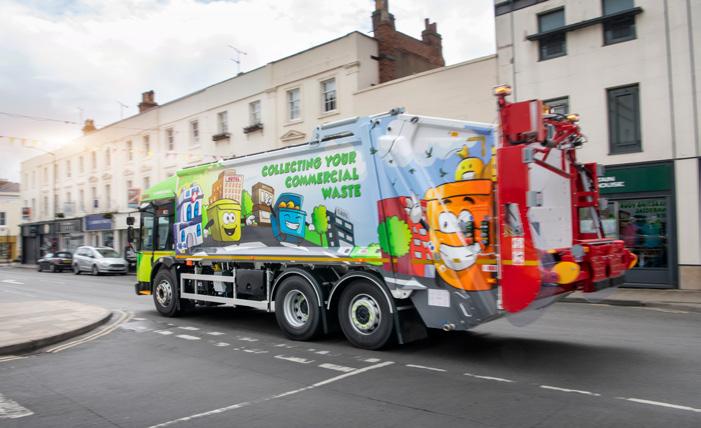
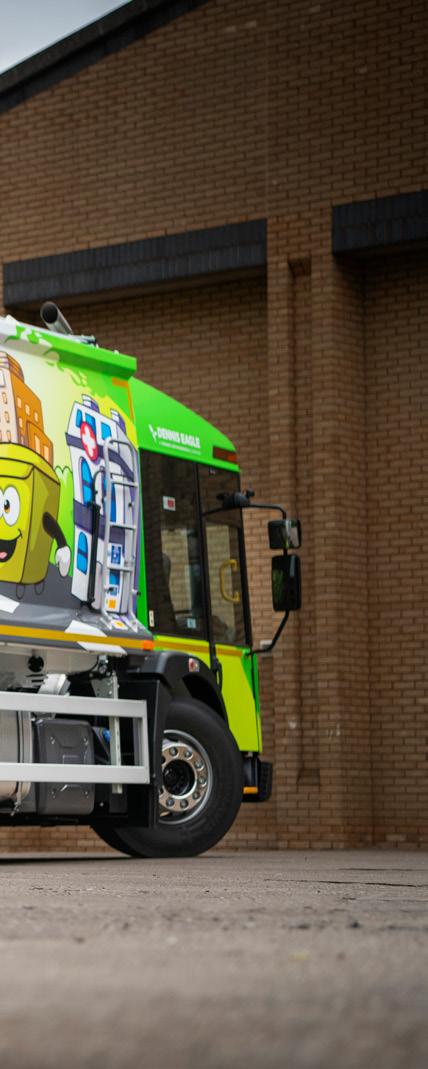
Dennis Eagle is delighted to welcome three new demo vehicles to our fleet, available to be tested, tried and assessed ahead of making any purchasing decisions.
The Narrow, Trade and Food Waste vehicles are all part of our Elite + range, designed for the full spectrum of operational needs. All three are 6x2 rear-steer vehicles with exceptional manoeuvrability. The OL19N and OL14N offer a narrow chassis, and the OL23W has a wide chassis.
Based on its well-respected predecessor the Elite 6, the Elite+ is an upgrade in comfort, practicality, efficiency and safety, creating an outstanding workstation for drivers and a safe vehicle for serving the community.
Let’s take a look at the three new vehicles, and their variety of bin lifts. Want to find out more about our three new vehicles? Please contact your local Dennis Eagle Regional Sales Manager, or email adele.pearl@dennis-eagle. co.uk for further information or to book a demonstrator.
OL19N
With a wheelbase of 5,250mm and a Volvo 280bhp engine, the OL19N comes with a Terberg OmniDEL Hydraulic bin lift. Terberg’s bestselling low-level fully automatic bin lift solution offers a sturdy build, minimal maintenance, and a safe operation system. It has a twin split chair capable of lift 2 wheel and 4 wheel containers, with cycle times of 6-7 seconds and 10-12 seconds, respectively.
The OL19N also comes with a LoadSense underbody weighing system and has a fixed displacement pump on the left-hand side.
OL23W
With a wheelbase of 5,650mm and a Volvo 320bhp engine, the OL23W is a robust and versatile vehicle. It comes with a Dennis Eagle Beta 2 bin lift, which simply bolts onto an Olympus tailgate. Up to 30% lighter than most split bin lifts, the Beta 2 delivers a payload advantage with a shorter rear overhang that reduces the real axle load. Lifting up to 500kg, the Beta 2 can be supplied as a lip lifter for wheeled bins or DIN arms.
The OL23W comes with a LoadSense underbody weighing system and is prepped for Bin Weighing.
OL14N
With a wheelbase of 5,500mm and a Volvo 280bhp engine, the OL14N comes with an electrically powered bin lift. The electric sibling of the Terberg OmniDEL, the OL14N requires only a 24v connection and, unsurprisingly, has a very low noise rating of just <56dB(A). The result? A super quiet, fuel-saving vehicle appreciated by the community and collections crews.
The OL14N comes with a PM underbody weighing system and is prepped for Terberg Bin Weighing technology and a top discharge pod for food waste collection.
Strengthening our dynamic weighing portfilio
Terberg Matec UK (TMUK) has increased its range of dynamic weighing software integrations through a partnership with Waste Logics. Waste Logics has become the 10th waste management software company to align with Terberg Matec’s TMDW9020 dynamic weighing system, offering commercial waste customers a significant range of options. The technology uses in-cab data sent via Bluetooth to record the weights of individual bins and different waste streams in real-time.
“I firmly believe that Terberg has the best technology and the most reliable system for integrated dynamic weighing,” says Ian Warren, Weighing & Data Manager at TMUK. “Our ability to seamlessly marry with so many waste management software solutions is a real plus point for waste operators.”
This applies to Fresh Start Waste Services, based in the North-West of England, and was the first business to take delivery of vehicles using the Waste Logics integration, Fresh Start has an existing relationship with Waste Logics. “It was desirable to us that the software works in unison with Terberg bin lift products,” says Ben Entwistle, Head of Operations at Fresh Start. “We’re really pleased with our purchase.”
Rob Colby TMUK Commercial Director commented, “It is a privilege to team up with Fresh Start Waste Services and their chosen software partner, Waste Logistics. The collaborative approach on this project has delivered a very smooth development & implementation process. We are thrilled to be in a position to expand our reach and link up with additional software experts such as Waste Logistics. I have no doubt that this combination will enhance the
experience for both Fresh Start and their customer base.”
Fresh Start Waste Services is a carbon-conscious waste and recycling service provider, and Terberg Matec’s Dynamic Weighing System supports these environmental goals in providing accurate data about each and every bin collected. In addition to reporting load weight for billing purposes, it provides a very accurate measurement of under- or over-loaded vehicles. “If we can see data that says we only empty one bin worth of weight every four visits, we can review the collection frequency and potentially save the customer some money, as well as reducing the carbon impact of more frequent visits, this allows us to maximise the payload when we come
to collect the bins, in this instance we reduce the number of visits to empty a bin by 75%, which is in line with our environmental goals,” says Ben.
In addition to delivering its OmniTrade bin lifts to Fresh Start, the integration with Waste Logics has led to new business with Lavelle, a waste services company based near Manchester. Lavelle has placed orders for EuroTRADE bin lifts for later this year.
Full list of waste management solution companies Terberg Matec’s Dynamic Weighing System can integrate with: The Access Group, AMCS Group, Bartec, Biffa, Dataset, Select Interventions, VWS Purgo, Waste Logics, Webaspx, Whitespace.

Eagle Eyed
Spot a Dennis Eagle RCV and take a pic
We asked our Facebook community to get creative and take a snap of our RCV's in action. Here's a selection of the best so far.
If you'd like the chance to win some cool Dennis Eagle merch, just take a pic of our trucks, wherever you are in the world and send it to us via our Facebook page. Good Luck!
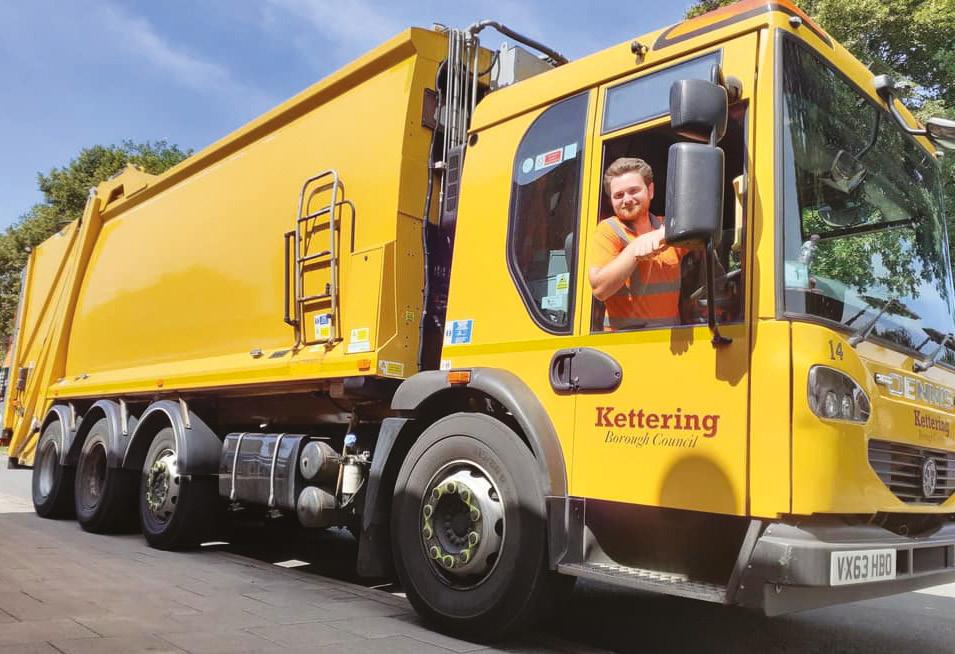
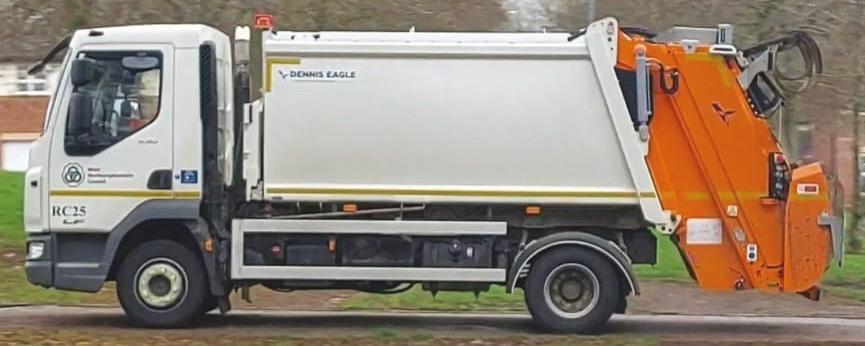
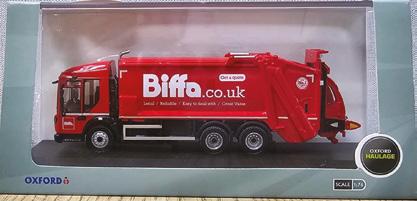
WINNER: James Chapman (top left)
RUNNERS UP: (clockwise from top right)
Martyn Clarke
David Nicholls
Ashley Lovering
Fin Burke
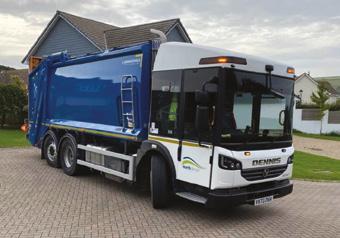
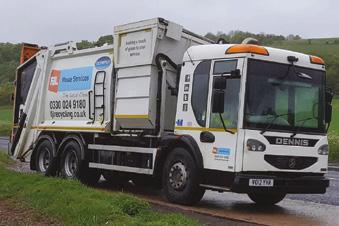

Reader competition:
For your chance to WIN a limited edition BIFFA OXFORD model RCV please send photos of unusual places where you have taken your copy of Eagle Eye, this could include holiday destinations, or at work, the more unusual the better!
Send your entries to contact.us@dennis-eagle.co.uk
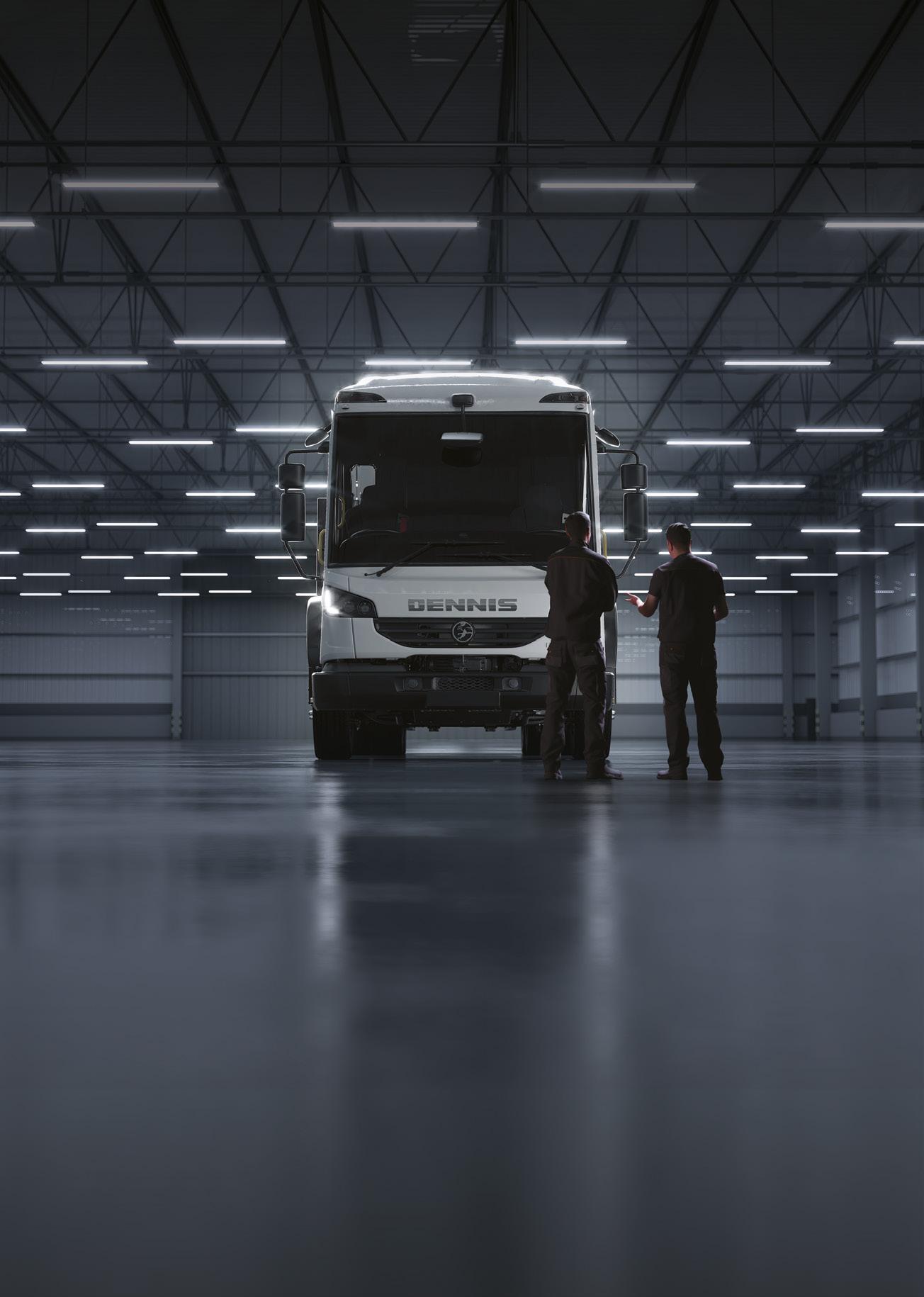