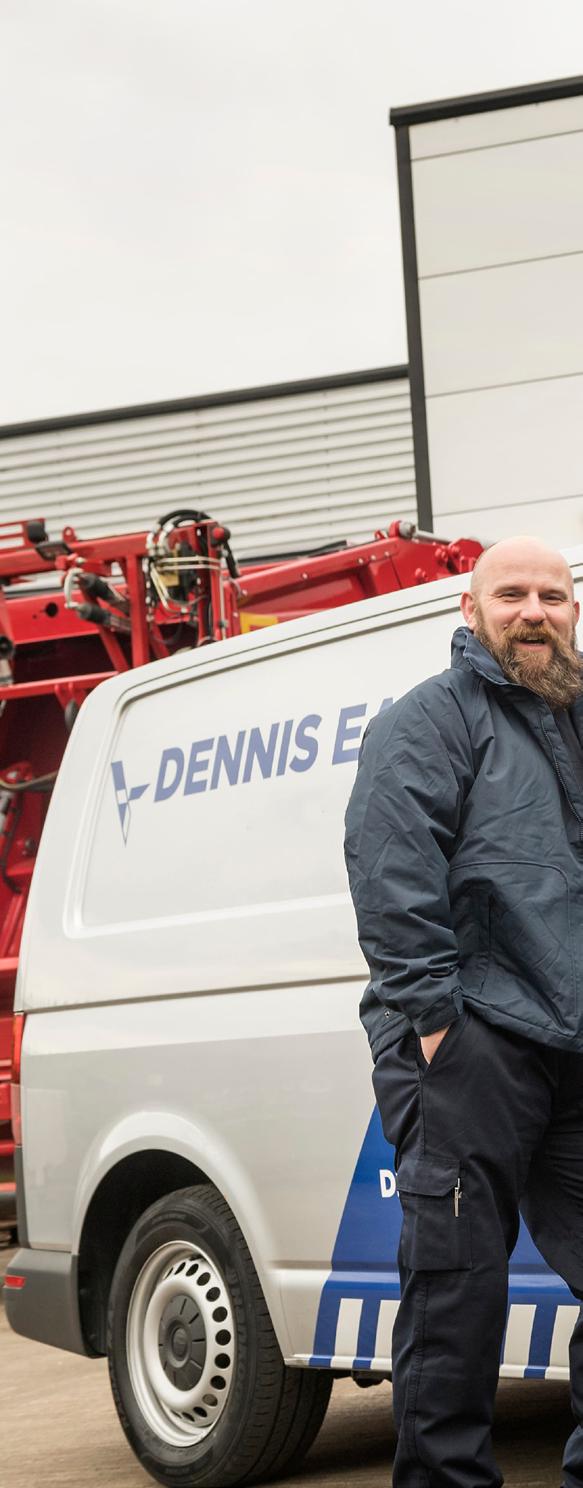
6 minute read
Aftermarket support based on efficiency
They also operate the telematics system DE-Connect which provides accurate and timely insights into the performance and needs of individual vehicles as well as fleet operations.
All these functions are based on efficiency.
Our Aftermarket teams aim to ensure vehicles are always available for their daily schedules and always safe, roadworthy and operationally efficient. To this end, we aim to minimise travelling times and distances of vehicles coming to our premises and get replacement parts delivered via our mobile engineers as quickly as possible.
In order to achieve this we have the biggest network of service centres in the UK industry, each well stocked with spare parts and the biggest network of Field Service Engineers. And our Repair and Maintenance contracts mean we have engineers permanently working fully fitted workshops on customers’ locations.
Our approach to repairing vehicles is also unique in the UK industry in that we routinely send our engineers to customers’ premises and to vehicles broken-down on the road in order to carry out repairs, rather than requiring the vehicles to come to us. This both saves time and reduces the carbon footprint of these operations.
Highly trained staff
Our staff are the best trained in the industry. In addition to the training and induction processes provided by the Dennis Eagle HR Team, all our staff receive specific training for their roles.
A detailed document created in early 2022 – Marginal Gains – described precisely what those roles entailed and set the standards expected in roles as diverse as Service Controllers, Workshop Administrators, Parts Advisors, Contract Engineers, Field Service Engineers and all managers.
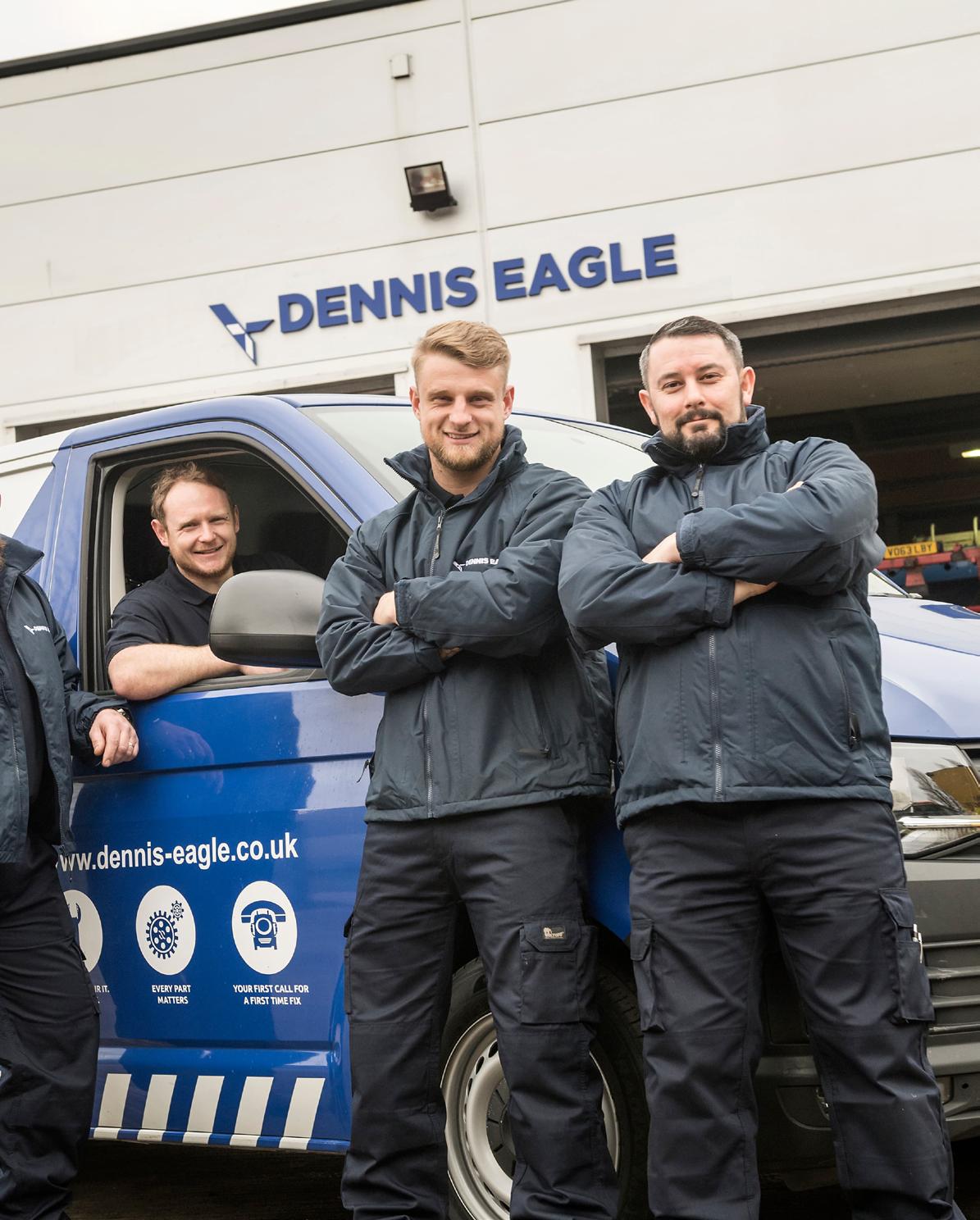
This enabled us to identify any further training needed while raising the standards of our customer service.
Our staff resource is also outstanding in its scale. We have over 60 service managers in the Aftermarket team and 61 Field Service Engineers – far more than anyone else in the UK industry. A key aspect of their work is visiting customers’ sites and building strong relationships.
Industry leading coverage
Our network has 10 Dennis Eagle Service Centres across the UK and six other facilities offering support through dealership partners and manufacturing centres. The scale of the network reduces both time and distance between customers, vehicles, engineers and parts and minimises ‘vehicle-off-road’ time.
They are equipped with workshops, stores, admin, meeting and training facilities. Some are purpose built to modern building standards, others converted to meet the required standards.
Low-energy lighting and energy-efficient heating systems, fans and other fittings are the norm. A programme of modernisation in recent years has ensured our they are not only operating to the highest environmental standards available but that our Service Centres also provide a comfortable working environment for both staff and visitors.
Our workshops are fitted with modern efficient equipment which is well maintained and regularly serviced. Safety is our priority in all workshops and across our sites as a whole and our safe working practices often go beyond what is required by legislation.
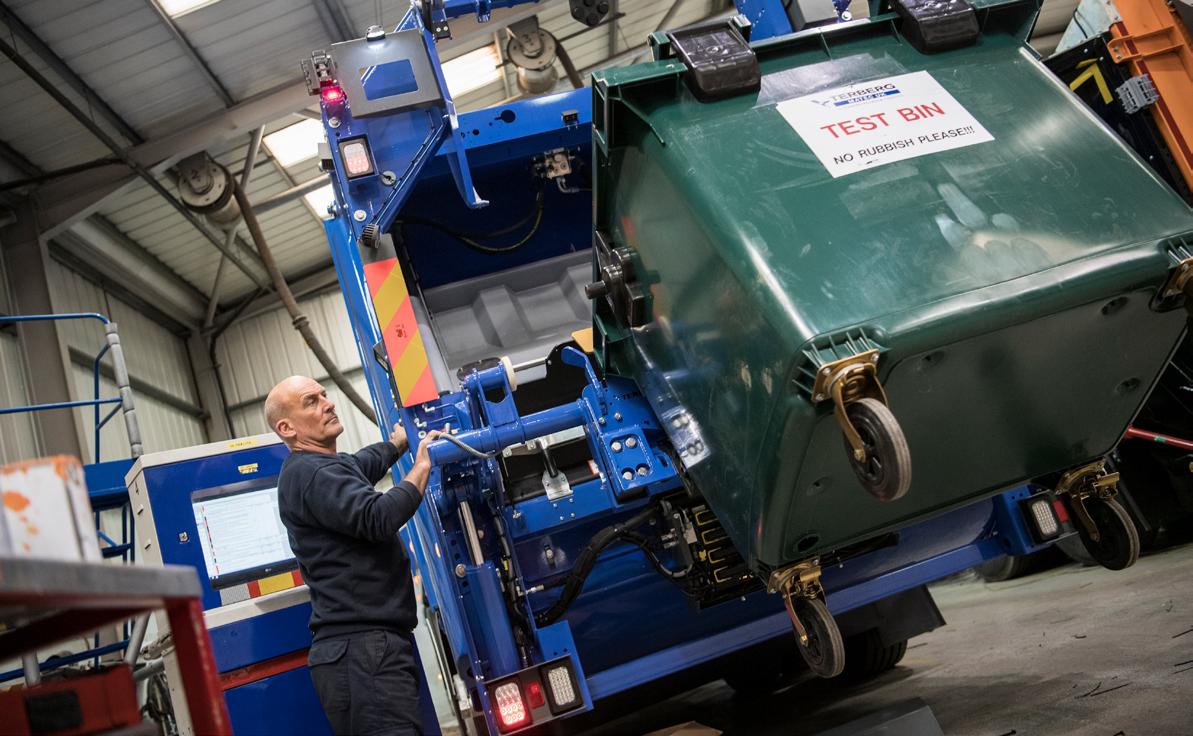
The routine services we offer in our Service Centres includes preparing vehicles for MoTs. Here, we have an outstanding record of 98.9% first time pass rate in 2022.
Outstanding parts service
Our parts system is set up for maximum efficiency in terms of time and movement. We have a Central Stores facility in the North-West England which stocks all parts for our vehicles.
Our Service Centres also carry most stock and our Field Service Engineers carry the most routinely needed parts with them.
All parts can be quickly and easily ordered through our Electronic Parts Catalogue (EPC) which includes diagrams specific for individual vehicles for quick, easy and certain identification. Customers with accounts are trained to use this facility, as are Dennis Eagle engineers.
Orders can be despatched immediately and delivered across the UK by our round-the-clock delivery service. Customers and Dennis Eagle engineers can also pick up parts in person from Central Stores and Service Centres if that is more convenient.
We have the highest levels of first-time selection for parts in our industry. Figures are routinely published. The average in 2022 was 96%.
96% 98.9%
98.9% first time MoT pass rate in our Service Centres in 2022.
An average of 96% of first time selection for parts in 2022.
R&M contracts for ultimate support
We offer full Repair and Maintenance contracts for customers who wish to outsource this function. At the end of 2022, we had 25 such contracts on-going.
The scope of these varies but may involve us either identifying and renting suitable premises or working from customers’ existing workshops. In both cases, new, highly efficient tools and equipment is fitted to meet our exacting standards.
Existing staff are usually TUPEd to become Dennis Eagle staff and thoroughly trained to our requirements.
RCV fleets are then totally managed by our engineers. They are checked before they leave the depot in the morning and when they return. All vehicles must be fit and safe to work before they can be used.
Routine servicing, maintenance and most repairs are done on site. Staff routinely work on the vehicles until they are fit and safe for operations.
We defined electric RCV safety
Service and maintenance of electric vehicles requires a unique approach. As the first Original Equipment Manufacturer (OEM) in our industry to introduce eRCVs, it fell to us to devise and implement rigorous safety regulations and best practices.
We have shared these with competitors and customers alike who wish to service and maintain eRCVs themselves.
Our approach is thorough. Training in safety around electric vehicles was provided to ALL Dennis Eagle staff across the UK and visitors to our premises are given clear safety briefings and shown awareness videos.
Only engineers trained in repairing electric vehicles can work on them in any capacity. eRCVs are routinely fenced off to keep unqualified staff away from them. Safety equipment for HV electrical systems is prominently displayed in workshops and staff trained to use it.
We offer full service, maintenance and repair services to all our eRCV customers at our premises. Every Service Centre has engineers trained to the highest standard to maintain them.
Special projects for ultra sustainability
For commercial efficiency, slack time in our workshops is often filled with repairs and maintenance of third-party vehicles and equipment.
Some Service Centres take on specialist projects. Among them are repowering vehicles. This involves taking a customer’s existing diesel asset and converting it to an all-electric eCollect. Depending on the age and condition of the original vehicle, this can be cost-effective route to reducing emissions for some operators.
We also offer full refurbishment of suitable RCVs. Our experienced and trained staff provide detailed assessments of vehicles and costings for customers.
And we also provide an Approved Used service, buying back suitable vehicles and refurbishing them for resale. Suitable parts from all these vehicles are also refurbished and sold to customers as Approved Used.
All come with full warranty.
Satisfaction is key
At the heart of our extensive operations is customer satisfaction and a culture of constant improvement has been developed among Aftermarket staff.
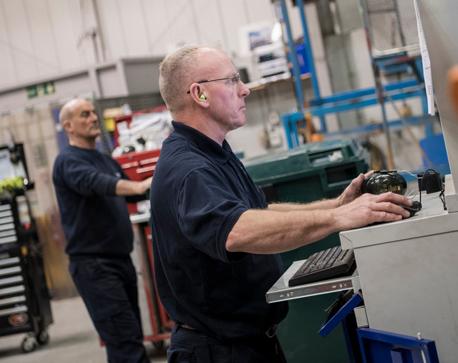
We need customer feedback to ensure this is happening and to identify opportunities for improvement. To this end, customers are all approached in a timely fashion for formal feedback and their responses are logged. Staff have monthly targets to achieve this. Answers are qualitative but while the responses are overwhelmingly positive, work is underway to analyse their patterns to identify areas in which we can improve.
Our staff and communities
Staff engagement is also crucial to our operation. The core elements of this are outlined in the HR section of this report but in addition to this, managers hold weekly meetings with their teams at which any issues can be raised and feedback garnered.
Our engagement goes beyond our immediate employees and customers and onto our suppliers and to the communities in which we have a presence. Local suppliers are used wherever possible to further benefit the local community. These typically include consumables and non-Dennis Eagle equipment.
Total compliance
With safety paramount in both ours and our customers’ operations, compliance and enforcement of compliance are essential. We take a strict and unyielding approach to this in all our workshops and depots: our vehicles can not go into operation unless they are totally compliant.
The emphasis we put on this and our culture of continuous improvement led us to create a dedicated role of Aftermarket Compliance Manager, a position we recruited for in summer 2021. Their sole role is to improve safety across all of our Aftermarket sites.
We have a similar approach to other legal aspects of our operations. A good example of this is data protection as our telematics system DE-Connect generates vast quantities of customers’ data. Data security is fundamentally important in all our dealings.