




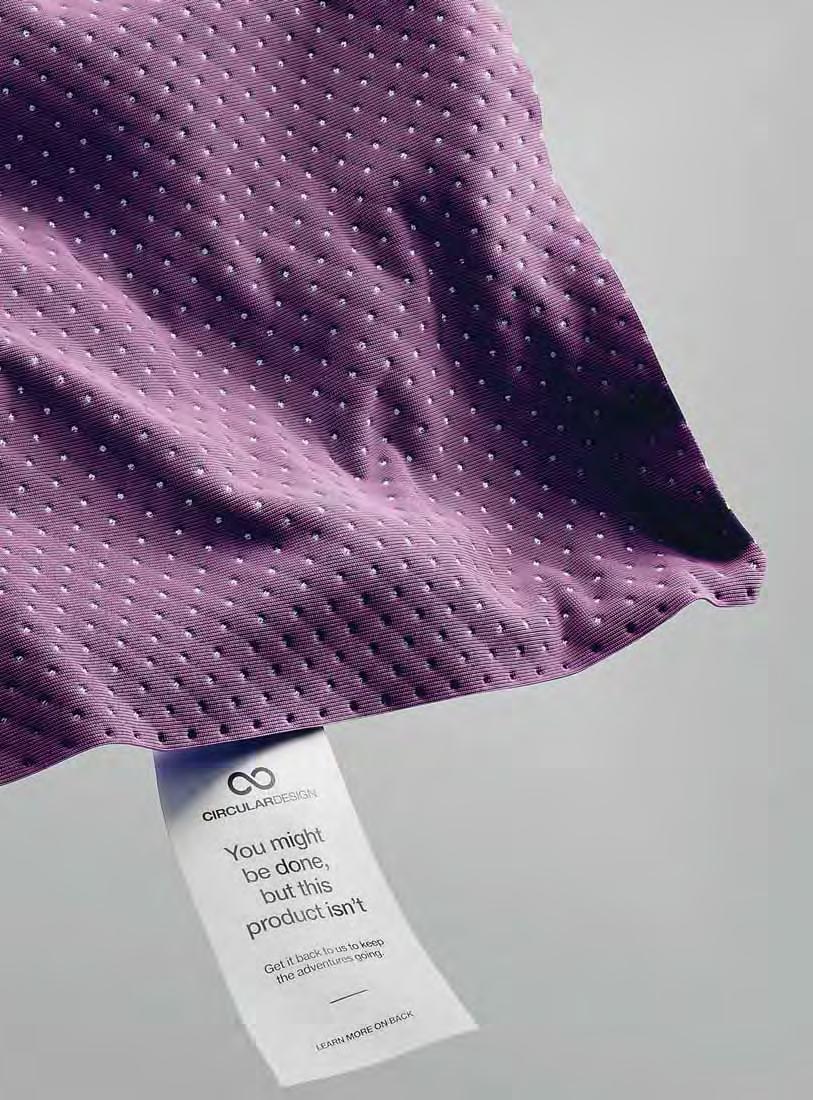

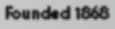
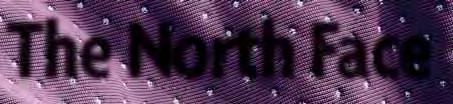
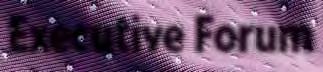




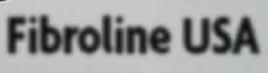

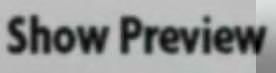



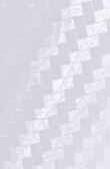
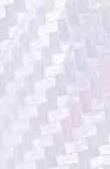
Representing a comprehensive range of product categories, find the latest in functional apparel textiles, including wearable smart textiles, new performance technologies, and much more!
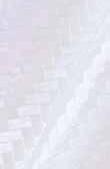
Representing a comprehensive range of product categories, find the latest in functional apparel textiles, including wearable smart textiles, new performance technologies, and much more!
Hundreds of leading exhibitors and knowledgesharing opportunities await. Don’t miss out on insights essential for thriving in today’s competitive textile landscape.
Register today for the 2025 edition of Techtextil North America!
MAY 6 – 8, 2025
ATLANTA, GEORGIA
Co-located withIncorporated with
Scan the QR code for more attendee information!
ON THE COVER:
The North Face is committed to innovation and performance, while also prioritizing sustainability and circular design principles. The company’s products, including the new DOTKNIT™ fabric, use recycled, renewable, and regeneratively grown materials when possible.
Industry Events Coverage
10 Techtextil North America/Texprocess Americas 2025
The collocated trade shows present an opportunity for the textile industry to gather at the Georgia World Congress Center in Atlanta.
12 Nonwovens & Filtration In Focus: IDEA®25/FiltXPO™
INDA’s collocated events offer in-person engagement opportunities across the nonwoven and filtration industries.
15 JEC World 2025: Pushing The Limits Of Composites:
JEC World 2025 marks the 60th anniversary of this trade show focused on composites innovations.
16 Executive Forum: The Next Chapter In Microfiber Pollution
Textile World spoke with Andrea Ferris, co-founder and CEOof Intrinsic Advanced Materials, and co-inventor of CiCLO® technology.
20 Harnessing Artificial Intelligence For Materials
Integrating AIinto R&D can accelerate materials development, and create sustainable, high-performance materials for the future.
52 FIMIC: Serving The Recycling Industry For Six Decades
FIMICtechnology provides solutions that eliminate impurities and lead to efficiently processed, high-quality recycled products.
55 Sustainable Upholstered Furniture: What Strategies & Technologies?
Lectra offers a roadmap for the upholstered furniture industry as it shifts towards more sustainable production practices.
26 The North Face:Pioneering Performance
The North Face recently introduced two new fabrics —DOTKNIT™ and FUTUREFLEECE™ —designed to work and perform together.
VOL. 175, No. 1 / TEXTILE WORLD (ISSN 0040-5213) is published bimonthly by Textile Industries Media Group, LLC, PO Box 683155, Marietta, GA 30068, and incorporates Modern Textiles, Textile Industries, Fiber World and Knitting/Apparel magazines, which remain the property of Textile Industries Media Group, LLC. Copyright 2025, Textile Industries Media Group, LLC Title registered with the U.S. Patent Office. All rights, including translation into other languages, reserved. Subscription rates for one year are: $65 (US); $85 (Canada and Mexico); $130 (Other International). Single copy rates are: $15 per copy. All prices are in U.S. dollars and all orders must be prepaid. Questions may be submitted to jdavis@textileworld.com. To obtain electronic copies of print articles, please contact ProQuest at www.proquest.com. To obtain microform copies, please contact NA Publishing at www.napubco.com.
POSTMASTERsend address changes to: Textile Industries Media Group, LLC, PO Box 683155, Marietta, GA 30068. Send Canadian address changes to: Textile World, c/o The Mail Group, P.O. Box 25542, London, ON N6C 6B2, Canada. Customer #7007632 Publications Agreement #40612608.
Samsara ECO: Commercializing Nylon 6,6, Recycling
Enzyme technology enables infinite recycling without degredation.
34 Molecular Fingerprinting Can Aid Textile Recycling
NIR-SORT, a new National Institute of Standards and Technology (NIST) database. can be used to identify and help sort textile waste.
37 INNEGRA ™ Fiber: Amplified Performance
Marketed under the tagline, “The Social Fiber,” INNEGRA™ works best when combined with other fibers to elevate product performance.
40 IACMI Celebrates A Decade Of Innovation
The Institute for Advanced Composites Manufacturing Innovation® (IACMI) has bolstered American manufacturing and national defense.
42 Cleaner Composite Fiber Recycling With DEECOM
Longworth and Cygnet Texkimp are partnering to commercialize DEECOM reclamation techology for the composites industry.
44 Medical Textiles With Infection Prevention
DITF and Heraeus are researching AGXX antimicrobial technology for use in medical textiles.
&
46 Fibroline & Navis TubeTex Open State-Of-The-Art Innovation Lab
Fibroline USAInnovation Lab introduces cutting-edge dry powder impregnation technology to North American market.
49 Color Accuracy, Supply Chain Certification Are Keys To A Strong Brand
Getting color right the first time reduces waste, saves time and offers value to customers.
2025QuarterlyVolumeI TextileWorld.com
Founded 1868
Quality Fabric: Reimagining Rest
Read about a luxury mattress ticking collaboration between Culp Home Fashions, Suedwolle Group and Lenzing AG
NEXT ISSUE:
• State Of The Industry
• Sustainability Focus
• Weaving Technology
EDITOR IN CHIEF
James M. Borneman
EXECUTIVE EDITOR
Rachael S. Davis
TECHNICAL EDITORS
Dr. Lisa Parillo Chapman
Dr. Peter J. Hauser
Dr. Trevor J. Little
Dr. William Oxenham
Dr. Behnam Pourdeyhimi
Dr. Abdel-Fattah Seyam
Dr. Andre West
CONTRIBUTING EDITORS
Jim Kaufmann
INTERNET CONTENT EDITOR
Rachael S. Davis
CIRCULATION MANAGER
Julie K. Brown-Davis
ADVERTISING BUSINESS MANAGER
Denise Buchalter
ART & PRODUCTION MANAGER
Julie K. Brown-Davis
OWNER/PUBLISHER
James M. Borneman
ADVERTISING REPRESENTATIVES
UNITED STATES & CANADA Turner Marketing &Media, LLC +864-594-0921 sturner@textileworld.com
EUROPE (except ITALY) Sabine Dussey +49-171-5473990 sabine.dussey@dussey.de
ITALY
Ferruccio & Filippo Silvera +39-022-846716 info@silvera.it
ASIA
James M. Borneman +678-483-6102 jborneman@textileworld.com
MEXICO, CENTRAL & SOUTH AMERICA
Virgilio L. González +58-412-622-2648 vlgonzalezp@gmail.com
INTERNET & CLASSIFIEDS Julie Davis +678-522-0404 jdavis@textileworld.com
PO Box 683155 | Marietta, GA 30068, USA Telephone +678-483-6102 | www.TextileWorld.com
Non-contact precision spray technology and plasma treatment for sustainable finish applications.
Providing jet, jigger, beam and cold pad batch dyeing machines with IR lab dyeing equipment. Continuous scouring, bleaching, mercerizing and singeing ranges.
Finishing and coating lines for woven and knit fabrics, technical textiles and nonwovens.
Detwisting, opening and web guiding for all fabric constructions.
Textile calenders for softening, lustre change, embossing and recalipering of textile substrates.
Foam generators, in line chemical mixing and blending systems.
Water treatment and water recovery plants in textile facilities.
Fabric surface finishing equipment: napping, sueding and shearing.
Circular knitting machines for apparel, mattress, home furnishings and footwear markets.
Turbotex Scrim Fabric machine.
In-line vision systems for weaving and warp knitting machines, tenter frames, compactors, coating/laminating ranges.
Slitting, spooling and rewinding machines. Ultrasonic slitting for loom state and finished fabrics.
Automatic dispensing of powder dyestuffs and liquid chemicals for laboratory, and bulk textile production.
Automated inspection and packaging systems for rolled goods.
Textile Coating ranges, digital, flat bed and rotary screen printing and loop steamers.
For additional information on these companies contact Ian Mills at imills@fi-tech.com.
IIt’s great to have a strong economic headline to start a year that holds such promise, despite facing a stormy international business undercurrent.
The first of the year Institute for Supply Management“Manufacturing ISM® Report On Business® ”reported a Manufacturing Purchasing Managers Index (PMI®) of 50.9 percent — great news for U.S.manufacturers.
Even better is the fact that the textile mills sector led the charge of manufacturing sectors reporting expansion.Any Manufacturing PMI report at 50-percent or above signals expansion and this is the first report at that level after 26 consecutive months of contraction.
Eight manufacturing sectors reported growth in January — all good company at the industrial core of U.S.manufacturing.
That said,the strength and impact of a stormy international business undercurrent caused by the new administration’s bold tariff rhetoric is the great unknown.
The Global Port Tracker report released by the National Retail Federation and Hackett Associates described the uncertainty without alarm. “At this stage,the situation is fluid,and it’s too early to know if the tariffs will be implemented, removed or further delayed,”said Hackett Associates Founder Ben Hackett.“As such, our view of North American imports has not changed significantly for the next six months.”
No sooner had President Donald J.Trump announced 25 percent tariffs on Canadian and Mexican imports,they were paused for one month based on Canadian and Mexican support for assistance with illegal immigration and fentanyl interdiction at the respective borders.
It would seem at this writing that China is also facing increased tariffs and the suspension the de minimis exemption for shipments originating from China.Also on the block is the $800 duty-free threshold for Chinese imports.It would appear that all goods from
China,regardless of value,will be subject to formal customs processing and tariffs.Aside from that,a new 10 percent tariff looks like it will be imposed on all Chinese imports,in addition to existing duties.
This is a big swing in international commerce that could carry significant impacts on a broad range of businesses,including textiles.
Without getting in the weeds,the de minimis exemption was a customs accommodation for small packages,of little value,shipped internationally into the United States.An individual could receive a bottle of Scotch from an aunt in Scotland at Christmas without clearing customs and paying duty.Unfortunately,that accommodation became a loophole,then expanded to a loophole-based industry.
National Council of Textile Organizations (NCTO) President and CEO Kim Glas has been extremely active in supporting closing the de minimis exemption loophole.In mid-January she stated in a press release,“We have long called on the administration to use its existing authorities to mitigate the damage to our industry created by de minimis,which has functioned as a massive tariff loophole for lowcost,subsidized,and unethical Chinese imports.
“The U.S.textile industry … is experiencing severe demand destruction fueled by 4 million de minimis shipments a day flooding our market with cheap,often illegal imports because of this outdated trade provision that rewards Chinese e-commerce platforms, importers and tariff cheaters with an open door to the U.S.market.”
What a way to kick off 2025.Hold tight, the positive,stormy ride just started!
James M. Borneman jborneman@TextileWorld.com
Experience impactful education, innovations from hundreds of exhibitors, and unlimited networking.
Join the premier event for sewn products, designed for manufacturers and innovators in apparel, footwear, home furnishings, and more.
Register now for the 2025 Edition of Texprocess Americas!
MAY 6 – 8, 2025
ATLANTA, GEORGIA
Scan the QR code to get registered today!
Co-located with Co-produced by
MMI Textiles Inc.,Cleveland,recently acquired Jason Mills LLC,a Milltown,N.J.-based manufacturer of high-performance knit textiles.This acquisition significantly expands MMI’s product offerings across markets such as recreational trade,occupational safety,aeronautical, automotive and marine, healthcare,and filtration.
“This acquisition marks an exciting milestone as we continue to grow and strengthen our position in the textile industry,”said Amy Bircher Bruyn,MMI Textiles’founder and CEO. “We are eager to integrate their expertise,resources, and innovation to better serve our customers and address the evolving needs of the market.”
Jason Mills will continue providing innovative textile solutions under MMI’s umbrella.Michael Lavroff, CEO of Jason Mills, emphasized the company’s commitment to quality and customer service in this next chapter.
PezTex Consulting assisted in the deal,and has plans to explore further acquisition opportunities in the textile industry for MMI.
Greensboro,N.C.-based UNIFI Inc.has announced the consolidation of its Madison,N.C.,yarn production facility into other UNIFI locations across
North and Central America, with plans to sell the Madison property in 2025. The move aims to optimize the company’s manufacturingfootprint,aligning operations with its growing customer base while enhancing cost efficiency and strengthening the balance sheet.
Employees affected by the transition will be offered opportunities at other UNIFI facilities in North Carolina.The company emphasized that this shift will not disrupt its ability to meet market demands or impact strategic initiatives related to innovation,the REPREVE® portfolio,or financial performance.
“This move,which involves relocating some machinery to other manufacturing locations,will enhance our cost structure and strengthen our balance sheet,”said Eddie Ingle, UNIFI CEO.“We look forward to transitioning to a more robust operating profile,revitalizing our Americas businesses and creating a more sustainable future for all our stakeholders.”
Wellford,S.C.-based Leigh Fibers has completed a restructuring plan to further integrate its operations with ReVive Fiber — formerly Martex Fiber — focusing on long-term growth and profitability.Key changes include consolidating the Wellford facility into ReVive Fiber’s Spartanburg,
Milliken & Company, Spartanburg,S.C.,has announced an investment and strategic partnership with Tidal Vision,a biomolecular technologies company specializing in chitosan-based biodegradable solutions.This collaboration will accelerate the introduction of biodegradable chemistries across Milliken’s markets.Tidal Vision’s proprietary technologies transform chitosan — a natural,biodegradable compound — into high-performance materials suitable for various applications.
“At Milliken,we invest with a long-term perspective, prioritizing partnerships that will drive meaningful growth,”said Halsey Cook, Milliken president and CEO.“Our approach is grounded in thorough research,strategic alignment with our core values,and a commitment to creating lasting value for our customers.”
In other company news, Milliken reports it has
S.C.,location,with a limited Wellford presence through 2026.The Brownsville,Texas,facility will remain unchanged,and no production capabilities will be lost.
The company will shift its focus to its core competencies — engineered fibers,global trading and sustainability efforts — idling its nonwovens line to strengthen leadership in post-consumer textile waste diversion.Streamlined
become the first textile manufacturer to offer non-per- and polyfluoroalkyl substances (non- PFAS) materials for all three layers of firefighter turnout gear — the outer shell,Horizon™; moisture barrier,Assure™; and thermal liner,Equinox™. The three products are layered together in a “composite”fabric that exceeds performance standards according to third-party testing.Milliken’s U.S.-based supply chain allows garment manufacturers to test the fabric as a system and maintain a complete chain of custody for faster delivery to firefighters, according to the company.
“Milliken is proud to be the only U.S.manufacturer offering non-PFAS fabric for every layer of turnout gear,but more importantly,we’re proud that these fabrics exceed performance standards,” said Marcio Manique, senior vice president of Protective Fabrics,Milliken.
operations will enhance efficiency and responsiveness to market demands.
“Between Leigh’s 100 years in business and ReVive’s 50,we wanted to make sure we maintained the best of both and rekindled the spirit and culture that made these companies great,”said John Peoples, president of Leigh Fibers and ReVive Fiber.“By making these moves,we’ve put ourselves in a position to quickly restore profita-
bility to the business and be able to make the investments necessary to support the needs of the market.”
San Francisco-based Rubi,a company focused on sustainable manufacturing, has secured a $969,961 Small Business Innovation Research (SBIR) Phase II grant from the National Science Foundation (NSF) to scale its carbon-to-cellulose platform.This technology uses cell-free biocatalysis to convert carbon dioxide into cellulose,aiming to replace traditional wood pulp,
reduce deforestation,and lower the environmental impact of textile production.
The grant will support Rubi’s path to commercialization,building on its successful Phase I grant completion in 2023.Key milestones include an $8.7 million seed round co-led by H&M Group and Patagonia,strategic partnerships with major fashion brands and Walmart,and the debut of the world’s first carbon dioxide-derived yarn with GANNI.
“This award is a testament to Rubi’s vision for a symbiotic manufacturing future and our ambition to lead the next era of sustainable industry,”said Neeka
Mashouf,co-founder and CEO of Rubi.“As we move into 2025,this grant will accelerate our efforts to scale CO2-derived, low-carbon cellulose for the textile industry ….”
Dallas-based RTCM Holdings Inc.,doing business as Reclaimed Cleaning Textiles and World Wear Project,has acquired United-Southern Waste Material Co.(USW), creating the largest textile recycler in North Texas. Founded in 1914,USW specializes in recycling and repurposing clothing and wiping rags,operating from
an 88,000-square-foot facility with more than 120 collection bins.Financial terms were not disclosed.
USW Co-Owner Mindi Levine Kahn,a third-generation family member,will remain with the company to ensure a smooth integration.The acquisition aims to support RTCM’s goal of diverting 100 million pounds of textiles from landfills annually,enhancing its capacity and long-term growth.
“USW’s operation will help us expand our capacity and drive essential longterm growth,”said Craig McAndrews,president and CEO of Reclaimed Cleaning Textiles. TW
textiles and nonwovens sectors under the following Product Categories: Research, Development, Planning, Consulting; Technology, Machinery, Accessories; Fibers & Yarns; Woven Fabrics, Laid Webs, Braiding, Knitted Fabrics; Nonwovens; Coated Textiles, Canvas Products; Composites; Bondtec; Functional Apparel Textiles; Associations; and Publications.
Techtextil North America and Texprocess Americas present an opportunity for the textile industry to gather at the Georgia World Congress Center in Atlanta this May.
TW Special Report
To further help visitors locate technologies at Techtextil North America exhibits are classified according to 12 application areas: Agrotech; Buildtech; Clothtech; Geotech; Hometech; Indutech; Medtech; Mobiltech; Oekotech; Packtech; Protech; and Sporttech.
TThe year 2025 sees Techtextil North America and Texprocess Americas gather the best of the U.S. technical textiles and sewn products industries in Atlanta. Now fully settled into its new odd year schedule, Techtextil North America and Texprocess Americas 2025 will return to the Georgia World Congress Center (GWCC), May 6-8, 2025.
Techtextil North America, incorporated with ATME-I, and Texprocess Americas are organized by Atlanta-based Messe Frankfurt Inc. Texprocess Americas is also coproduced by SPESA — the industry association for suppliers to the sewn products industry. Organizers expect more than 300 exhibitors and more than 6,000 visitors to participate in the collocated events.
Messe Frankfurt recognizes current challenges faced by the textile industry — from trade wars and price increases to geopolitical instability — and sees the show as a platform to open discussions, create partner-
ships, advance technologies and develop solutions to immediate industry concerns.
“The textile industry is at a crossroads, facing both immense challenges and unprecedented opportunities,” said Kristy Meade, vice president, Technical Shows, Messe Frankfurt Inc. “Techtextil North America 2025 is where we come together as a global community to address these challenges, exchange ideas, and create the solutions that will drive our industry forward. From sustainability to automation and supply chain resilience, this event provides the knowledge, resources, and connections that every textile professional needs to succeed.”
This biennial event gathers the textile value chain in one location. Visitors enjoy access to products, technologies and solutions for virtually any textile application.
Techtextil North America showcases the value-add chain in the technical
Texprocess Americas is promoted as the largest North American trade show displaying equipment and technology for the development, sourcing and production of sewn products. Product groups and services covered include: design, product development and automation technology; contract manufacturing/sourcing; production preparation and organization; cutting room and automation technology; fabrics/materials; manufacturer; fusing, setting and manufacturing preparation; textile machinery; textile finishing; knitting technology; embroidery technology; stitching, joining and fastening technology, automation technology; stitching, joining and fastening materials, automation accessories for garment, house and home textiles; product processing and finishing; energy, air conditioning, disposal and recycling; quality control; internal material flow; textile logistics; information technology; services, consultancy and training; and research and development.
Messe Frankfurt places an emphasis on education and this year is no exception. Badge holders can take advantage of both the Techtextil North America and Texprocess Americas symposiums over the three days. Subject matter experts will present sessions on a variety of subjects and attendees can register for the
sessions for an extra fee (See Table 1). The show floor pass is included with all symposium registrations.
Additional complimentary education options exist on the show floor. Tech Talks, Techtextil North America’s exhibit floor education sessions, will be hosted in a designated area. Topics will include technical advances, trade issues and the latest in applications, among other subjects.
Students also have the opportunity to showcase their research via the Student Research Poster Program. Show attendees can see the scientific research taking place at universities across the globe at both the undergraduate and graduate levels. The program also offers students a chance to engage with the industry, sharing their research findings and meeting potential employers and/or sponsors. Some students also may be selected to present their research during a Tech Talk.
The GWCC is located in downtown Atlanta, which offers many hotels, restaurants and entertainment options in close proximity to the trade show. Show hours are from 10 a.m. until 5 p.m. Tuesday and Wednesday, and from 10 a.m. until 3 p.m. on Thursday.
Visitors need only purchase an exhibit hall badge for one of the shows to gain access to both Techtextil North America and Texprocess Americas. Opening night reception tickets and symposium packages are available during registration. All pricing and deadlines, as well as hotel and transportation information, are available on the events’ respective websites. Visitors are strongly advised to register in advance to take advantage of pricing discounts and ease of entry during the open hours.
“Techtextil North America 2025 will be a must-attend event for professionals across the technical textiles supply chain,” Meade said. “Whether you’re a manufacturer, researcher or end-user, this is the
Tuesday, May 6
Exhibit Hall Open .
Emerging Technologies in Nonwovens: Innovations in Machinery, Materials and Sustainability
The Reality of Recycled Materials
Reusability of Textiles in Healthcare
Developments in Carbon and Ceramic Fibers
Wednesday, May 7
Exhibit Hall Open
Textile Engineering for Extreme Environments: Material Innovation in Aerospace Applications
LCA and Circular Economy: A Pathway to Sustainable Business Practices
Trade, Tariffs and the Textile Industry.
Thursday, May 8
Exhibit Hall Open
Transforming Materials Design through Machine Learning.
Bioplastics and the Supply Chain: Navigating the Future of Sustainable Materials.
10:00 a.m.-5:00 p.m.
8:00 a.m.-9:15 a.m.
9:30 a.m.-10:45 a.m.
1:15 p.m.-2:30 p.m.
2:45 p.m.-4:00 p.m.
10:00 a.m.-5:00 p.m.
. 8:00 a.m.-9:15 a.m.
9:30 a.m.-10:45 a.m.
2:45 p.m.-4:00 p.m.
10:00 a.m.-3:00 p.m.
. 8:00 a.m.-9:15 a.m.
9:30 a.m.-10:45 a.m.
Texprocess Americas Symposium Sessions
Tuesday, May 6
Exhibit Hall Open
Unlocking the Power of Simplicity: How AI Streamlines Production of Sewn Products
A Market How-To: From Strategy to Content to Close. .
A Guide to Financing Your Shop Floor
Under the Banyan Tree: Buyers and Suppliers in Fashion | A Conversation on Industry Transition
Wednesday, May 7
Exhibit Hall Open
Made in America | A Conversation Across the Domestic Supply Chain
The Reality of Recycled Materials
Maximizing Efficiency Under Pressure: A Live Strategy Showcase.
Thursday, May 8
Exhibit Hall Open .
10:00 a.m.-5:00 p.m.
8:00 a.m.-9:15 a.m.
. . 9:30 a.m.-10:45 a.m.
1:15 p.m.-2:30 p.m.
2:45 p.m.-4:00 p.m.
10:00 a.m.-5:00 p.m.
8:00 a.m.-9:15 a.m.
9:30 a.m.-10:45 a.m.
2:45 p.m.-4:00 p.m.
10:00 a.m.-3:00 p.m.
Table 1 Information accurate as of TW ’s press time
premier platform to explore new opportunities, connect with industry leaders, and discover the innovations transforming textiles. We look for-
ward to welcoming the global textile community to Atlanta for three days of learning, networking and business growth.” TW
For more information about Techtextil North America and Texprocess Americas 2025, please visit techtextil-north-america.us.messfrankfurt.com and texprocessamericas.us.messefrankfurt.com.
IDEA® 2025, the flagship event for the North American nonwovens industry hosted by the Association of the Nonwoven Fabrics Industry (INDA), returns to Miami Beach April 29-May 1, 2025, for the 22nd iteration of the trade show and conference. IDEA will again collocate with INDA’s FiltXPO™ International Filtration Exhibition and Conference to provide added value for exhibiting companies and attendees alike. The two events will take place at the Miami Beach Convention Center (MBCC) in Miami Beach, Fla.
“IDEA25 highlights the industry’s leading innovators, including those making strategic investments toward eco-friendly engineered material solutions,” said INDA President and CEO Tony Fragnito. “Attendees can learn and explore alternative production methods including the developments and incorporation of bioderived, recycled and biodegradable components. This event showcases the industry’s commitment to innovation and environmental responsibility in its operations and products.”
The last edition of IDEA attracted approximately 5,000 participants. Visitors to IDEA come from all sectors of the nonwovens market
INDA’s IDEA®and FiltXPO™trade events will collocate in Miami Beach, offering in-person engagement opportunities across the nonwoven and filtration industries.
TW Special Report
including wipes, apparel, geosynthetics, filtration, and medical and surgical sectors, among other sectors. Job titles for attendees run the gamut from senior leadership to research and development personnel to purchasing executives.
INDA is hoping for robust attendance in 2025 and has confirmed more than 600 exhibitors will participate.
A reception on Tuesday, April 29, from 5 p.m. to 7 p.m., will officially welcome guests to the three-day event. The exhibit floor is open Tuesday and Wednesday from 9 a.m. until 5 p.m. and on Thursday from 9 a.m. to 3 p.m.
IDEA will include a Sustainability in Nonwovens multi-day conference
portion that attendees may participate in for an additional fee. There will be a total of between 20 and 24 sessions, which includes two to three panel discussions. As of TW ’s press time, the conference agenda was not available, but session topics will tentatively cover:
•U.S., European Union and United Nations regulation;
•Start-of-Life: Materials Sourcing and Natural Fibers, among other topics;
•Product/Process Innovations;
•End-of-Life: Advances in Biodegradability/Compostability; and
•Next Life:Fiber-to-Nonwoven Recycling, Advanced Recycling, extended producer responsibility.
At the 2025 edition of the event, product promo talks —held previously during the conference — will be hosted at INDA’s in-booth lightning talks, and regional market overview sessions will occur at INDA’s in-booth sessions.
IDEA25 also offers a series of short courses to be taught on Monday, April 28, one day ahead of the show floor opening. Topics cover the essentials of nonwovens and market focused areas and are designed for newcomers and seasoned professionals alike. Courses
include Nonwovens 101, Baby & Adult Care Absorbent Hygiene Systems, Period Products Innovation Workshop and Wet Wipes 101.
The courses will be taught by James “Jim” Robinson, principal with Absorbent Hygiene Insights LLC; Heidi Beatty, CEO, Crown Abbey LLC; and INDA’s own Director of Education and Technical Affairs Dr. Matt O’Sickey.
“With over twenty years of attending IDEA, it was consistently the busiest and most productive week of my year as I was able to meet with all of my suppliers and all of my customers,” said Dr. O’Sickey.“It’s incredibly exciting now, as I am part of INDA, the hosting organization for IDEA and FiltXPO, to provide more ways to make the week even more valuable and efficient to our members with training courses, enhanced on-site meeting room options, and the inaugural multiday Sustainability in Nonwovens and Advances in Filtration Conferences.”
Attendees register for courses individually and may choose all courses or just one depending on budget and learning needs.
INDA confers the IDEA Achievement Awards in conjunction with the trade show. Presented by INDA in partnership with Nonwovens Industry magazine, the awards recognize leading companies, individuals and new products in the global nonwovens and engineered fabrics industry who have contributed to the industry since the last IDEA show.
Awards will be presented in the following six categories:
•IDEA Equipment Achievement Award;
•IDEA Raw Material Achievement Award;
•IDEA Short-Life Product Achievement Award;
•IDEA Long-Life Product Achievement Award;
•IDEA Sustainability Achievement Award; and
•IDEA Nonwoven Achievement Award.
Monday,April 28
Registration Open.
Training Courses:
Filter Media Training Course
Nonwovens 101 : Matt O’Sickey, Ph.D., Director of Education &Technical Affairs, INDA. .
Period Products Innovation Workshop : Heidi Beatty, CEO, Crown Abbey, LLC
— 5:00 p.m.
8:00 a.m. — 5:00 p.m.
8:00 a.m. — 12:00 p.m.
. 8:00 a.m. — 12:00 p.m.
Baby & Adult Care Absorbent Systems : James Robinson, Principal, Absorbent Hygiene Insights, LLC
Wet Wipes 101 : Heidi Beatty
Tuesday,April 29
Registration Open.
1:00 p.m. — 5:00 p.m.
1:00 p.m. — 5:00 p.m.
8:00 a.m. — 5:00 p.m. Opening Ceremony.
Conference Sessions.
Exhibit Hall Open
Training Course: Filter Media Training Course
Welcome Reception.
Wednesday,April 30
Registration Open.
Conference Sessions.
Exhibit Hall Open
Thursday,May 1
Registration Open.
Exhibit Hall Open
Three finalists are selected in each category by INDA’s Technical Advisory Board. Then, industry professionals vote on the winners at the Nonwovens Industry website.
IDEA is highly regarded by the nonwovens industry as a place to network, develop new business strategies and learn new things. INDA also continues to place a priority on sustainability encouraging the exploration of biomaterials and
9:00 a.m. — 9:15 a.m.
9:00 a.m. — 5:00 p.m.
9:00 a.m. — 5:00 p.m.
8:00 a.m. — 5:00 p.m.
5:00 p.m. — 7:00 p.m.
8:00 a.m. — 5:00 p.m.
9:00 a.m. — 5:00 p.m.
9:00 a.m. — 5:00 p.m.
8:00 a.m. — 5:00 p.m.
9:00 a.m. — 3:00 p.m.
healthier ecosystems as well as circular economies and innovative nonwoven materials.
“IDEA may be the single best opportunity in the Nonwovens industry to engage with other businesses and move our agenda forward,” said Neil Johnson, president, AJ Nonwovens. “We have been able to develop relationships, open sales channels, share innovation, solve supply challenges, and increase brand awareness. I’m not aware of a better opportunity to accomplish all
of this in one place. We are looking forward to more at IDEA25!”
“IDEA25 is the place for any organization working toward a future ripe with low carbon, biobased solutions,” noted Koen Bastiaens, Strategic Market manager, Hygiene & Nonwovens, NatureWorks. “Leading organizations across the industry gather at the event to showcase the latest technologies and innovations toward a more circular, sustainable economy. NatureWorks is proud to be part of this event that propels solutions that are critical to mitigating climate change.”
FiltXPO™Details
FiltXPO, is a newer INDA event focused on filtration technologies and innovations, and organized on an 18month schedule meaning every other year it is collocated with IDEA. FiltXPO includes an exhibit floor, Advances in Filtration Conference, two-day training Filter Media Short Course and FiltXPO Innovation Awards, among other features.
FiltXPO™Education
This year, the Advances in Filtration Conference is co-organized by INDA and the American Filtration & Separations Society (AFS). Five key topics will be highlighted: nonwovens and filtration for healthy buildings; nonwovens and filtration for data centers; nonwovens and filtration for e-mobility; sustainability and circularity in filtration; and innova-
tions meeting the current challenges of filtration. The conference will include plenary talks, panel discussions, and technical posters presented by subject matter experts as well as research institutes.
The Filter Media Short Course focuses on nonwovens and their applications in air and liquid filtration. The course —taught by Dr. Behnam Pourdeyhimi, NC State University professor and executive director of The Nonwovens Institute (NWI); Dr. Benoit Maze, NWI’s director of Education & Administration; and Dr. Hooman Tafreshi, NC State professor, Mechanical and Aerospace Engineering, and NWI’s director of research — is perfect for personnel in research and development, product development, marketing and product management, technical sales, technical support, and testing and quality control.
FiltXpo recognizes innovation within the filtration value chain with a particular focus on nonwoven fabrics and technologies with its FiltXPO Innovation Awards. Innovations are recognized in three categories —Air/Gas Filtration Media, Water/Liquid Filtration Media, and Filtration Equipment including converting equipment, filtration systems using nonwoven filter media, and testing equipment, among other technologies.
Similar to the IDEA Innovation Awards, the FiltXPO Innovation
Awards finalist are selected by INDA’s Technical Advisory Board. The industry then votes for the winners via a link on the International Filtration News magazine website.
“FiltXPO is something you don’t want to miss,” said Tom Justice, proprietor and owner, Zene Filtration. “It’s more important now than ever that you stay ahead of this rapidly evolving industry — being able to identify shifts in customer demands could determine whether your company will exist in three years.”
“Being there, you are directly engaged,” said Doug Huntley, senior global R&D leader, Home Environment Markets, 3M. “There is nothing that replaces that. Having healthier air clearly has an impact in the world. The challenges are only increasing in terms of air quality. That’s why we need to really step up our game in terms of delivering those solutions.”
Indeed, there is nothing that replaces that in person engagement and business networking opportunity offered by a trade show. As INDA focuses on preparing and fine-tuning details for IDEA and FiltXPO, the organization looks forward to bringing the learning and networking opportunities to the nonwovens and filtration industries this April. TW
For more information about IDEA ® and FiltXPO ™ and to register, visit idea show.org. and filtXPO.com.
JEC World 2025 marks the 60th anniversary of this trade show focused on composites innovations.
TW
Special Report
JJEC World 2025 is an international trade show for the composites industry that will take place March 4-6, 2025, at the Paris Nord Villepinte Exhibition Centre located just outside Paris. It is organized by Paris-based JEC Group, a non-profit entity devoted to promoting composite materials and fostering adoption of the materials.
The 2025 edition of the event marks 60 years of JEC World and organizers are celebrating this milestone under the motto and unifying theme “Pushing the Limits.”
The annual event gathers the entire value chain of composite materials, attracting more than 1,300 exhibitors, 43,500 professional visitors, and participants from 100-plus countries for its 2024 edition. JEC World serves as a global hub for business, networking and innovation in the composites industry.
There is no shortage of ways to get involved and learn about composites, network and connect at JEC World.
Highlights at JEC World 2025 include:
• The Exhibition Floor —showcasing cutting-edge innovations for a myriad of composite markets including automotive and road transportation; aerospace; renew-
able energy; sport, leisure & recreation; and building and civil engineering, among other sectors.
• Conferences and Panels —JEC hosts its own extensive composites conference program in two rooms over the three days. In addition, SAMPE Global will host a separate one-day conference focused on materials and process engineering led by global experts. JEC World also features “Composites Exchange” sessions highlighting presentations by JEC clients and exhibitors; as well as “Country On Stage” sessions discussing the composites industry in specific countries and regions.
• Innovation Awards —The JEC Composites Innovation Awards will be bestowed on cutting-edge, creative projects featuring composite materials.
• Startup Booster —a competition open to entrepreneurs, startups, small to medium-sized enterprises and academic spinoffs building innovative projects in the fields of composites and advanced materials.
• A Live Demo Area —Returning for its second year, these real-time presentations showcase composite parts manufacturing processes.
• Business Meetings —JEC World’s program that connects qualified business partners to facilitate net-
working and foster partnerships.
This year, JEC also will introduce Investor Day, a day-long event created in partnership with Catalysium and Sesamers, designed for organizations investing in advanced materials and composites.
JEC World places an emphasis on a more sustainable future encouraging the advancement of the nine R’s of circularity —Refuse, Rethink, Reduce, Reuse, Repair, Refurbish, Remanufacture, Repurpose and Recycle. Sustainable themes are central to the event including natural fibers and biobased materials, recycling, and Life Cycle Assessment roadmaps, according to organizers.
JEC World 2025 is open March 4-5 from 9 a.m. to 6 p.m. and on March 6 from 9 a.m. to 5 p.m.
In addition, at 6 p.m. on March 5, JEC World will host a networking cocktail party to celebrate its 60th anniversary.
Registration is simple with one badge providing access to all JEC World events.
Make plans to join the composites industry in Paris for this “Festival of Composites.” TW
For more information about JEC World 2025, please visit jec-world.events.
Textile World recently caught up with CiCLO’s Andrea Ferris to talk about CiCLO technology, government mandates and sustainability goals, among other topics.
TW Special Report
TTextile World last spoke with Andrea Ferris — co-founder and CEO of Intrinsic Advanced Materials,and co-inventor of CiCLO® technology — several years ago,about microplastics, CiCLO technology,and Intrinsic Advanced Materials,a joint venture company with Parkdale, Gastonia,N.C. (See “CiCLO ®: Just One Arrow In The Microfiber Pollution Solution Quiver”, TW , September/October 2022).
Ferris and her CiCLO biodegradable chemistry co-inventor Alan McIntosh recognized the performance characteristics inherent in polymers such as polyester and nylon and understood that they have an important role in the textile industry and cannot just be replaced by an environmentally friendlier fiber. But they also recognized the issues with polyester and nylon products at the end of their lifetime and their contributions to textile and microplastic pollution.Rather than focusing on recycling and circular systems as a solution,the pair instead zeroed in on a
way to make the synthetic fibers biodegradable.
CiCLO technology is blended with conventional or recycled polyester and nylon during melt extrusion as the fiber is manufactured becoming permanently embedded in the fiber.
This additive creates countless biodegradable spots throughout the matrix of the fabric that allow microbes to breakdown fibers when they inevitably end up in the environment.CiCLO technology only biodegrades the polymer under the right conditions — in the presence of moisture and microbes over an extended period of time — and therefore doesn’t impact the performance of the polyester or nylon products during their useful lifetime. But once the garment or other textile product treated with CiCLO biodegradable chemistry ends up in the environment,it will biodegrade similar to a natural or inherently biodegradable material.
TW recently had the opportunity to catch up with Ferris to talk about
the latest CiCLO technology developments and the next era of sustainability.
TW : We last chatted in 2022 about CiCLO technology and Intrinsic Advanced Materials. Are there any significant company updates you’d like to talk about?
Ferris : The brand has experienced remarkable growth since 2022! Mid-2024 we hit a major milestone,producing more than 100 million pounds of biodegradable fiber using CiCLO technology. More than 50 brands and retailers now use CiCLO polyester,including Billabong,Oakley,Target, McDonald’s,Bloomingdale’s, Landau,and more,to mitigate the environmental impacts of synthetic microplastic pollution.
At the end of 2023,we were part of Champion’s Eco-Future collection launch,introducing an updated version of the brand’s hero Reverse Weave sweatsuits made with CiCLO fibers.Building on this momentum, in early 2024,we worked with Uwila Warrior to
introduce the market’s first line of biodegradable undergarments.
Bass Pro Shops launched its first World Wide Sportsman Nylon Angler shirt with CiCLO nylon this week.We have more exciting adoptions launching in 2025 and 2026 from world-known brands.We’re so grateful that more brands and consumers are becoming aware that while synthetics offer tremendous performance benefits,they inevitably contribute to microplastic pollution, and are seeking solutions that are available now, like CiCLO technology.
TW : There is no doubt sustainability is one of the most important issues facing the textile industry today.The development of CiCLO technology focuses on biodegradability versus recycling.How do you make the case for biodegradable materials versus recycled?
Ferris : We don’t see it as biodegradable versus recyclable; biodegradability complements circularity. Synthetic fibers and fabrics
made with CiCLO technology remain durable and recyclable,maintaining performance during wash, wear and care.At the same time,any synthetic fibers shed from fabrics made with CiCLO technology can biodegrade at greatly accelerated rates if they end up as microplastic pollutants.We’re huge supporters of textile recycling and thrilled that extended producer responsibility (EPR) legislation will help fast-track an infrastructure to scale it.Many of our customers use recycled polyester made from bottles today and see that transitioning to polyester made from textile waste in the coming years.However,almost all synthetic fabrics shed, whether made from virgin or recycled materials,so circularity won’t solve the microplastic issue.CiCLO technology can be blended with virgin or recycled polyester from bottles or textile waste.
TW : How do limited government sustainability expectations impact progress and the pace of development for plastic pollution solutions?
Ferris: With anticipated deregulation under the new U.S.administration, scaling sustainable solutions that are already available today is more critical than ever.While I’m an optimistic environmentalist myself,I’m also pragmatic. I hope any potential deregulation makes it easier for businesses to innovate and grow without impacting our environment.Based on hundreds of meetings with
brands and retailers over the last several years,I recognize that organizations are simply teams of people trying to do the right thing and improve responsible manufacturing.If the government doesn’t require specific standards, brands should embrace it as an opportunity to take even more initiative to lead their sector and assert themselves as the gold standard.People frequently ask why governments don’t yet mandate that synthetics be biodegradable since the technology exists. I think a more appropriate question to ask as industry innovators,manufacturers, and consumers is“Why should we wait for government to mandate that we do the right thing instead of just doing it?”
TW : The European Union is adopting a variety of durability mandates — with the Strategy for Circular and Sustainable Textiles and the Green Claims Directive just two among many pieces of legislation that address durability and extended producer responsibility that will impact the textile industry.How do you think these regulations will reshape design and production practices,and how should brands prepare for the changes?
Ferris: The upcoming EU textile durability standards are more than another regulatory requirement — they’ll reshape the entire approach to design and manufacturing.We’re likely going to see brands integrate durability testing into development processes,
Brands can choose to use hangtags to educate consumers about the CiCLO®technology. (Image courtesy of CiCLO)
with a particular focus on fiber selection and construction techniques. Companies that view these regulations as an opportunity rather than a burden will gain a competitive edge,especially as consumers increasingly demand quality and transparency in their clothing purchases.
These design requirements will help curb fast fashion in the long run by reducing the excessive amount of products that flood the market today and raising consumer awareness about the environmental and social impacts of the mass disposal of textiles. Even so,due to the accessibility,affordability,and durability of synthetics like polyester and nylon,they will remain a preferred material for many brands. According to Textile Exchange [a non-profit organization driving beneficial impacts on climate and nature in the fashion and textile industry],the use of polyester alone may reach 90 million metric tons annually by 2030,which will drive the need for solu-
tions that enable their use in a more responsible way.
TW : Polyester recycling remains a major focus of the textile industry as a method to tackle plastic pollution.Do you envision a shift from recycled polyester (rPET) and what does the future look like without the scaled infrastructure for an alternative?
Ferris: Many brands continue to use rPET as part of their sustainability goals,but some are also exploring alternative materials to complement its use.This shift is driven by factors like the rising cost of rPET,challenges in sourcing high-quality bottle flake for performance applications,and the desire to keep plastic bottles within the established recycling infrastructure for maximum circularity. While rPET remains a key material in many sustainability strategies,it is not without challenges — most notably,the microfibers it sheds,which are a leading source of microplastic pollution in natural environments.
This is where innovations like CiCLO technology come in,offering an act-now solution to address the environmental impact of microplastic shedding.By incorporating CiCLO technology,brands can continue using rPET fabrics while helping to ensure that any fibers that shed and end up as microplastic pollution won’t persist in the environment indefinitely.
As rPET is unlikely to disappear from the industry,CiCLO technology provides a crucial pathway for minimizing its impact and supporting a more sustainable future.
We know scalability is a significant hindrance to the adoption of sustainable solutions.When developing CiCLO technology, we focused on making the technology easy to integrate into supply chains and scalable for growing sustainability programs.We’re proud to lead in affordable, accessible,and scalable solutions for synthetics.
uate SKU volumes to align cost efficiency with reduced environmental impact, ensuring the two considerations work together rather than compete.
TW : How are brands weighing the balance between cost and environmental impact?
Ferris: Cost is a consideration for any product redesign or manufacturing process change.However, failing to make the updates required to manufacture more responsibly poses separate cost risks down the line — regulatory risks should new legislation require it,reputation damage as consumers are more aware and concerned about sustainability,loss of competitiveness,and supply chain vulnerabilities. Everyone pays in some way for the accumulating environmental impacts our society is causing.
Many brands are now taking a more long-term approach to their sustainability goals,which is a positive shift.They’re focusing on affordable,scalable, and logistically practical solutions,starting with steps that significantly impact their goals.When cost is a concern,brands can re-engineer designs or eval-
As a supplier of biodegradable technology, our mission is to provide brands and retailers with efficient supply chains where they need it.Unlike many new materials innovators who start small with capsule collections and hope to scale later,we’ve spent years building a global infrastructure to support the world’s largest brands.Our platform solution for biodegradable synthetics is designed to integrate seamlessly into existing processes and pricing structures.Rather than forcing brands to choose between cost and environmental impact,we aim to provide solutions that align the two,proving that sustainability and affordability can work hand in hand.
TW: Through your work with brands including Champion,Target,and Billabong,what trends or practices have emerged that seem to be effective in advancingsustainability goals?
Ferris: I cannot speak to any specific brand’s strategy,but I can share some things we see happening within organizations that effectively drive sincere change.
For one,it’s helpful when sustainability is a part of everyone’s jobs. Good ideas come from everywhere,and each person knows an area or thing well.Teams closest to product development,for
example,are probably the ones who can determine the most feasible improvements to design specs. At the same time,sourcing might have the best ideas for tier 3 supplier improvements,for example.The best and most solutions will materialize when everyone is encouraged to contribute.
When we work with large brands or retailers, we partner with one or many“champions”in the organization who help us navigate how to integrate CiCLO technology into their synthetics.They have varying responsibilities, but the common thread is that they are an environmentalist at heart and want to do good because it’s right.Today we met with one of those champions whose formal role is around assured supply for mostly non-textiles categories.We thanked her for helping us even though it’s“not her job”and she replied,“Well,I know how to make it happen and I care,so I guess,why shouldn’t it be my job?”
Another way we see goals being advanced is by setting achievable initiatives that don’t break the bank.Designing for durability and recyclability are top of mind for the industry moving forward and both can be tackled with strategic product design,often requiring zero dollars.Addressing synthetic textiles that shed microplastics also remains an important issue,and the industry is looking to solve it with solutions ranging from improved yarn and fabric construction to
recommending improved wastewater and laundering filtration to prioritizing biodegradable fibers.
TW : How do you see consumer awareness and behavior influencing the adoption of sustainable practices? What role does consumer education play in driving demand for truly sustainable products?
Ferris: Consumer awareness plays a massive role in brands’adoption of sustainable practices.As shoppers become more aware of the impact of their purchases,their shopping behaviors have evolved, with many consumers intentionally seeking out the most sustainable options for whatever is on their shopping list.Gen-Z has been at the forefront of consumer education and the changes in buyer priorities,largely thanks to brands educating consumers on social media.
In 2023,PDI’s Business of Sustainability Index reported that 91 percent of Gen-Z want to buy from sustainable companies.1 Recent financial stressors across markets have impacted short-term buying behavior, but even though buying behaviors might temporarily be in opposition to shoppers’values,their perspectives aren’t changing.When financial circumstances change,values will undoubtedly be reflected by purchase decisions.
Embracing sustainability is critical for brands’ long-term success and, most importantly,for building consumer trust that transcends economic fluctuations or trends.
TW : What does the next era of sustainability look like,in your opinion?
Ferris: The next era of sustainability is going to go beyond what some have referred to as“carbon tunnel syndrome.”For the past few years,the conversation has been narrowly focused on reducing carbon emissions through modifications to manufacturing and logistics processes or material choices,for example. Efforts to reduce and control carbon emissions will remain a priority,but this next era is ushering in EPR and the infrastructure to support truly circular textiles.We will see a massive reduction in the amount of textile waste that goes to landfill,which will instead be sorted and funneled to appropriate recycling facilities.Resalable items will remain in circulation and the second-hand market will boom.EPR schemes will prioritize repair,reuse and resale above recycling into new fibers.The use of recycled and lower impact materials will also be incentivized,and while I don’t know exactly how, it could be done through reduced“ecomodulated fees”charged to manufacturers in EPR plans.Lastly, there will be much more transparency to consumers about where and how their products were made,what chemicals were used,and expectations for durability. Even just five years ago,it was hard to imagine that the global textiles industry could mobilize towards a circular economy.Now with EPR moving forward in the EU and California, the world’s fifth largest
Reverse weave apparel in Champion’s Eco Future collection feature CiCLO®technology. (Image courtesy of Champion)
economy,we’re going to see these efforts ripple throughout the world.
TW : Are there any emerging technologies or innovations that you believe have the potential to significantly transform sustainability in the textile industry over the next decade?
Ferris: Well,I’d be remiss not to start with mentioning that CiCLO technology can significantly transform sustainability over the next decade.We believe that within the next five years a significant portion of polyester will transition to a combination of both virgin and recycled CiCLO polyester,which is durable, recyclable and also biodegradable.Within 10 years,at least half of the polyester produced around the world will be CiCLO polyester and a large percentage will be made from recycled textile waste. More research comes out weekly on the topic of synthetic microfiber pollution; it is the most prolific form of microplastic pollution found all over
the globe … and it doesn’t need to be.CiCLO technology is a vetted, affordable and scaled solution that is available now.
Textile sorting technologies also have the potential to significantly transform the industry.Sorting has been a very manual process,but several companies are working on super-fast materials identification for proper sorting.This is not only important for mechanical and chemical recyclers who will make new fiber or things like insulation or rags,but for the secondhand market.Advanced technology could do things like scan items for quality, amount of wear,brand,for example,quickly set an appropriate price and list it for sale online.The resale marketplace for secondhand could explode and will be serious competition for brands making new products.
I don’t have a crystal ball,but I do know the future looks bright and exciting. TW
References 1 https://pditechnologies.com/blog/ tracking-gen-z-consumer-trendssustainability/
Integrating AI into research and development can accelerate materials development, and create sustainable, high-performance materials for the future.
By Rishi Gurnani
These advantages — the preservation of knowledge, high-dimensional learning and personalized search — are fundamental in overcoming traditional challenges in material design and manufacturing.
Preservation of Knowledge: One of the most significant benefits of AI is its ability to preserve and retain existing knowledge. Consider ChatGPT, an AI model trained on vast amounts of internet data, embodying a large portion of recorded human knowledge. When you ask ChatGPT a question, it draws upon the collective wisdom of experts embedded within its training data. Extending this concept to a corporate environment, AI can capture and retain the expertise of departing employees, ensuring that valuable institutional knowledge is not lost. Traditionally, when a valued coworker leaves, their expertise vanishes with them, forcing organizations to re-run experiments, train new hires from scratch, or accept the loss of critical insights. AI mitigates this by preserving knowledge within its models, providing continuity and reducing the costs associated with knowledge loss.
IIn the rapidly evolving landscape of materials science, artificial intelligence (AI) stands out as a transformative force with the potential to revolutionize industries ranging from energy storage to nonwovens and fibers. Atlanta-based Matmerize Inc. — an early-stage company spun out of the Atlantabased Georgia Institute of Technology — is on a mission to harness the power of AI to accelerate materials design and manufacturing.
AI is not merely a technological trend; it represents a paradigm shift in how materials science may be approached. By leveraging AI, vast datasets can be analyzed, material properties can be predicted with high precision, and complex processes that were previously reliant on laborious trial-and-error methods can be automated. To fully grasp
AI’s potential, it’s useful to draw parallels with other historical technological breakthroughs, shown in Figure 1, that have reshaped industries. The steam engine, introduced in 1712, revolutionized manufacturing and transportation by providing a reliable and portable power source. The light bulb extended productive hours beyond daylight, significantly enhancing productivity and quality of life. More recently, the internet has transformed communication and information dissemination, fostering unprecedented global connectivity and collaboration. Similarly, AI is poised to leave an indelible mark on the materials and nonwovens industries, driving advancements that were once thought unattainable.
AI offers several unique advantages that make it particularly suited for advancing materials science.
High-Dimensional Learning : AI excels in generating new knowledge, especially when dealing with high-dimensional problems that are beyond human cognitive capacities. High-dimensional learning refers to the ability of AI systems to process and analyze data with numerous variables and complex interdependencies. Historical examples like DeepBlue and AlphaGo illustrate AI’s prowess in mastering intricate domains such as chess and Go, where AI systems have surpassed human champions. In materials science, this capability translates to understanding and predicting the behavior of complex materials with numerous interacting components. AI can uncover patterns and relationships within high-dimensional datasets that humans might overlook, leading to the discovery of novel materials and optimized manufacturing processes that drive innovation forward.
Personalized Search : AI also revolutionizes the way we conduct searches by enabling personalized search capabilities. Unlike traditional search engines like Google, which provide generic results based on broad queries, AI can tailor search outputs to specific contexts and individual needs.
As an example, picture planning a surprise getaway for a loved one while juggling budget, interests and time constraints. Today’s AI tools can provide a personalize itinerary that captures a unique vision, transforming an overwhelming task into a heartwarming experience. Before, such detailed, bespoke planning often meant endless research across impersonal travel sites.
Similarly, in materials science, personalized search capabilities enable researchers to input highly specific requirements into AI models — reaction constraints, chemical inventories and supplier lists as just a few examples — receiving customized insights and recommendations that precisely match project goals and constraints.
The integration of AI into materials science has given rise to a specialized subfield known as materials informatics. This interdisciplinary approach combines machine learning, data analytics and materials science to develop structure-property models that predict material behaviors based on their chemical and physical structures. The genesis of materials informatics can be traced back to decades-old work in drug discovery, where AI models were employed to predict drug-related properties from molecular structures. This methodology has been successfully adapted to polymers and other complex materials, enabling researchers to forecast properties like glass-transition temperature (Tg), mechanical strength and dielectric constants with remarkable accuracy.
1831
Electric Generator Provided a foundation for electrification, enabling modern factories and urban infrastructure.
1712
Steam Engine Enabled mechanized production, by means of a reliable and portable power source.
1798
Interchangeable Parts
Standardized manufacturing and reduced costs in industries like firearms and machinery
1879
1908
1956
Containerized Shipping
Standardized global trade, reducing shipping costs and accelerating globalization.
Assembly Line Mass production reduced costs and made automobiles accessible to the masses.
1928
Penicillin
Extended human lifespan and workforce productivity.
1969
Light Bulb
Extended working hours, increasing productivity and enabling 24/7 business operations.
At the heart of materials informatics are structure-property models. These models serve as predictive tools that estimate material properties based on structural characteristics. For polymers, this involves converting chemical structures into numerical vectors through so-called “fingerprinting” techniques. These numerical vectors are then fed into machine learning algorithms to forecast properties without the need for physical experiments. This capability significantly reduces both the time and financial investment traditionally required for material development. For instance, accurately predicting Tg can inform decisions about polymer selection and processing conditions, thereby streamlining the development cycle.
Developing reliable structureproperty models necessitates sophisticated AI techniques, particularly when dealing with high-dimensional data and limited datasets — a com-
2007
Smartphone Merged computing and connectivity, fueling mobile commerce, remote work, and app-based businesses.
1980
Personal Computer
Made computing power more accessible, transforming the ability to access the internet.
1994
Enterprise Resource Planning (ERP) Systems Integrated business processes, optimizing efficiency and decision-making.
Today
Internet
Transformed communication and information dissemination, fostering unprecedented global connectivity and collaboration.
Generative AI Automates creative and analytical tasks, transforming productivity, R&D, and customer interactions.
mon challenge in materials science. Three advanced approaches address these challenges:
1. Active Learning : This iterative process begins with training an initial model on a small dataset. The model then identifies and designs new candidate materials, which are experimentally validated. The newly acquired data is added to the dataset, and the model is retrained, progressively refining its predictive capabilities. This method optimizes the learning process, ensuring that each experimental trial provides maximum informational value.
2. Multi-Task Learning : Instead of developing separate models for each property, multi-task learning integrates datasets for multiple correlated properties and trains a single model. This approach leverages the interdependencies among different material properties, enhancing overall model accuracy and enabling more comprehensive material design. For example, a single model could simultaneously predict both Tg and melting temperature, uncovering underlying correlations that improve predictive performance.
Traditional AI models often neglect established physical laws governing material behavior. Physics-informed learning integrates these laws into machine learning models, ensuring that predictions adhere to known physical principles. This hybrid approach marries the strengths of AI with the rigor of scientific theories, resulting in models that are not only accurate but also interpretable and reliable.
While AI offers unparalleled potential, its traditional implementation has been hindered by the need for specialized expertise. Matmerize aims to democratize AI in materials science by eliminating these barriers. Its software platform is designed to connect non-experts with advanced AI tools through an intuitive no-code interface, transforming raw experimental data into
predictive models. This accessibility allows researchers to focus on innovation rather than the complexities of data management and model development.
The Matmerize software was developed with several key capabilities in mind:
• Hierarchical Structure-Property Modeling — Matmerize employs state-of-the-art algorithms to build hierarchical structure-property models that capture relationships across different physical length scales using proprietary fingerprinting techniques. In polymer science, for instance, models incorporate atomic triples, block-level descriptors, and chain-level features to predict properties like Tg with high accuracy. This multi-scale approach not only enhances prediction precision but also facilitates the exploration of complex materials such as copolymers, blends and crosslinked systems. By understanding how molecular structures influence macroscopic properties, researchers
Discovering HighPerformance Dialectrics for Energy Storage
Designing NextGeneration 6G Materials with Resonac
Energy storage (Defense, Aerospace, EVs, Consumer Electronics)
Telecommunications (6G Development)
AI models screened thousands of polymer candidates to identify materials with superior dielectric properties at high temperatures.
AI-driven strucureproperty models optimized material design for electromagnetic applications.
Developing Biodegradable Polymers for Kimberly Clark
Streamlining Mechanical
Recycling with Predictive Modeling
Sustainability (Plastics & Nonwovens)
AI software screened 20,000+ biopolymer candidates, identifying sustainable alternatives with strong mechanical properties.
Recycling & Circular Economy
AI-based predictive modeling forecasted pass/fail outcomes for recycled multilayer films, reducing costly experimental trials.
can design materials with tailored functionalities.
• User-Friendly Interface and Automation — The Matmerize platform is built with user experience at its core. The intuitive interface allows R&D teams to seamlessly navigate through data processing, model training, and prediction tasks. Automation features minimize the need for manual intervention, enabling researchers to generate predictive models in minutes rather than weeks. This efficiency accelerates the pace of innovation, allowing teams to iterate quickly and explore a broader array of material possibilities without being bogged down by technical complexities.
Discovered new polymers like PONB-2Me5CI achieving record-breaking energy densities at 200oC, surpassing conventional BOPP-based capacitors.
Resonac validated AI models against thirdparty alternatives, finding superior predictive accuracy. Enabled a streamlined material design process, reducing time and resource costs.
Selected a dozen+ promising biopolymers, currently undergoing evaluation. AI-driven approach fosters eco-friendly material innovation.
Client significantly reduced the number of lab trials, optimizing film composition for APR certification and accelerating the approval process.
Figure 2: AI-driven innovations in materials science: Case studies at Matmerize
• Active Learning and Model Refinement — Matmerize incorporates active learning cycles to continuously improve model accuracy. The software suggests new experiments based on model predictions, which are then validated and added to the dataset. This iterative process ensures that models evolve with the latest data, maintaining their relevance and precision over time, even as key employees leave the organization. By facilitating continuous improvement, Matmerize helps organizations stay at the forefront of materials innovation.
The following case studies illustrate the practical impact of AI in materials science and highlight how AI can facilitate significant advancements.
Case Study 1: Using AI To Discover High-Performance Dielectrics For Energy Storage Materials
Energy storage is a pivotal area with applications spanning defense, aerospace, transportation, and consumer electronics. Electrostatic capacitors, prized for their high-power densities, are integral components in these applications. Traditionally,
materials like biaxially oriented polypropylene (BOPP) have been used as dielectrics in capacitors due to their favorable properties, including high breakdown field, low energy loss and cost-effectiveness. However, BOPP’s relatively low dielectric constant limits the energy density of capacitors, especially at elevated temperatures.
Using AI models, Matmerize screened thousands of polymer candidates to identify materials with superior dielectric properties at high temperatures. These models predicted the energy density of polymers based on their structural features, enabling the prioritization of candidates with the highest potential. This targeted approach led to the discovery of new polymers, such as PONB-2Me5Cl, which achieved record-breaking energy densities at 200°C, a critical metric for aerospace and electric vehicle applications.1 These advancements demonstrate AI’s ability to help surpass conventional technologies.
Case Study 2:
Designing Next-Generation 6G
Materials With Resonac
As the telecommunications industry advances toward 6G technology, the demand for materials with specific electromagnetic properties has intensified. Tokyo-based Resonac, formerly Showa Denko, partnered with Matmerize2 to design materials optimized for 6G applications, where traditional design methods were proving inadequate in meeting stringent performance criteria.
Matmerize specializes in developing structure-property models that predict material behaviors with exceptional accuracy. Resonac evaluated Matmerize’s models against three third-party alternatives and found that its solutions provided superior predictive capabilities tailored to their specific needs. The enhanced accuracy of Matmerize’s AI-driven models enabled Resonac to streamline their material design process, reducing both the time and resources typically required for such specialized applications.
•In change of data management; infrastructure; collation; chaining; etc.
•Converts clear data into ML models
•Domain experts
•Query the models
•Analyze the queries to plan next experiment
•Automatic conversion of raw data into structured data
•Makes the job of the AIchampions easier
•Examples Bumbling, Les Anchiles, Labgram
•Conduct planned experiments
•Generate data
•Pass data back to AI champions
•Automating conversion of structured data into models
•Automating model gauging
•Makes the job of both AIchampions and AIcustomers easier
•Examples: Mararian, Celtrus, Multiple Technologies
•Equips the culture organization with the knowledge to effectively use AI tools and interpret their outputs
•Examples: Linked In, Learning, Udaty, Fourth Brain
Impressed by the performance of the models, Resonac formed a strategic partnership with Matmerize to collaboratively design and develop new materials specifically for nextgeneration 6G technologies.
Case Study 3:
Developing Biodegradable
Polymers For Kimberly Clark
Sustainability is a paramount concern in the materials and nonwovens industries. Kimberly Clark, Irving, Texas, aimed to develop biodegradable polymers to replace conventional plastics, thereby reducing environmental impact without compromising performance.
Matmerize’s software enabled Kimberly Clark to screen more than 20,000 biopolymer candidates, identifying more than a dozen promising chemistries with desirable mechanical properties. The AI models evaluated both the chemical structures and processing conditions, optimizing for performance metrics such as tensile strength and flexibility. The identified polymers currently are undergoing rigorous evaluation to ensure they meet Kimberly Clark’s sustainability and performance standards. This project highlights AI’s
potential to drive sustainable innovation, enabling companies to develop eco-friendly materials that align with environmental goals.
Case Study 4:
Streamlining Mechanical Recycling With Predictive Modeling
Mechanical recycling of plastics involves reprocessing materials into new products, a process that demands precise control over film composition and processing parameters to ensure both quality and consistency. Companies striving to align their recycled products with stringent government regulations must rigorously test their materials against the guidelines set forth by the Association of Plastic Recyclers (APR). Achieving certification from the APR is a formidable challenge, as it requires extensive and costly trials to validate that recycled films meet the high property standards necessary for certification.
Matmerize developed a predictive model for a client aiming to produce multilayer films certified by the APR. Its AI model could predict pass/fail outcomes based on film composition and processing parameters, significantly reducing the number of required experimental trials. By accu-
rately forecasting which formulations would meet certification standards, the client could bypass tens or hundreds of expensive lab trials, saving both time and resources. Initial results have been promising, with the client benchmarking our model against internal expert predictions and observing outstanding performance.
Integrating AI into research and development (R&D) is not merely a technological matter; it requires alignment at the cultural and organizational level (See Figure 3). Successful AI implementation hinges on robust data management, dedicated roles and strategic investments in key areas. In interactions with numerous companies, several critical elements emerge as essential for building an AI-ready R&D organization.
Data is the cornerstone of all AI models. Effective data management involves collecting, organizing, and maintaining high-quality datasets that accurately represent the materials and processes under study. Common challenges include disparate data sources, inconsistent formats, and incomplete records. To address these issues, organizations should:
• Centralize Data Storage : Implement centralized databases
or data lakes that consolidate information from various sources, ensuring easy access and consistency; and
• Establish Data Governance Policies : Define clear protocols for data collection, storage, and sharing to maintain data quality and compliance with industry standards.
Building a competent AI-driven R&D team involves delineating specific roles that align with the organization’s AI objectives. Three primary roles are crucial:
1. AI Champions: These individuals are responsible for managing and structuring data, ensuring that it is ready for model training and analysis. They bridge the gap between raw data and actionable insights, making them indispensable for AI initiatives.
2. AI Consumers : These team members utilize the predictive models to inform decision-making processes. They leverage AI-generated insights to plan simulations, design experiments, and drive innovation.
3. AI Actors : These are the handson researchers and technicians who execute planned experiments. They generate new data, feeding into the AI models and enabling continuous improvement.
To fully harness AI’s potential, organizations must equip their AI Champions, Consumers, and Actors with key tools and training programs:
• Electronic Lab Notebooks: The tools automatically convert raw data into structured data, easing the burden on AI champions.
• Modeling Software : Tools like Matmerize’s platform automatically convert structured data into easyto-use models, easing the burden on AI champions and AI consumers.
• Training and Education: Provide comprehensive training programs to equip team members with the necessary skills and knowledge to effectively use AI tools and interpret their outputs. This ensures that all stakeholders can contribute to and benefit from AI initiatives.
By enabling faster, more accurate material discovery and optimization, AI is driving innovation, reducing costs and fostering sustainability. As the industry continues to evolve, embracing AI will be essential for organizations seeking to maintain a competitive edge and address emerging challenges. The integration of AI into R&D processes not only accelerates material development but also opens new avenues for sustainable and high-performance materials that meet the demands of the future. TW
References:
1https://www.nature.com/articles/s41578-024-00708-8 2https://www.resonac.com/news/2023/09/22/2672.html
Editor’s Note: Matmerize Director of Software Rishi Gurnani leads the development of AI-driven solutions for materials design and manufacturing. With a Ph.D. in Materials Science and deep expertise in artificial intelligence, he has collaborated with clients across various industries, including energy storage and nonwovens, to solve complex materials challenges using cutting-edge AI technologies. To learn more about the company, visit matmerize.com.
TWINTEX, a Portugal-based clothing manufacturer specializing in medium-to-high-end and luxury garments, has implemented the Hänel Lean-Lift automated vertical warehouse from VRC Warehouse Technologies, Portugal, to optimize its logistics operations. This system enhances real-time stock management, reduces manual tasks, and improves process efficiency, enabling operators to quickly access and organize materials with greater accuracy, according to the manufacturer.
The installation has led to a 40-percent reduction in space usage, improved employee safety by eliminating the need for ladders, and minimized physical strain, according to the company.
“With VRC Warehouse Technologies’ equipment, an operator can, in just a few steps, retrieve and organize all the necessary materials, while stock management is updated by the day, hour, and minute, significantly enhancing performance in an impressive way,” said Mico Mineiro, COO of Twintex.
Japan-based Teijin Frontier Co. Ltd. has developed a next-generation comfort material for active and functional apparel, combining contact cooling functionality with sweat stickiness prevention. The dual-layer, knit structure alternates hydrophobic and hydrophilic WAVERON™ yarns, where the hydrophilic yarn absorbs perspiration, and the hydrophobic yarn keeps skin dry. The outer layer disperses moisture, enhancing comfort during physical activity.
Targeted for the 2026 spring/ summer sports and outdoor apparel season, Teijin aims to sell 100,000
meters initially, expanding to 1 million meters annually by 2028, including applications in functional fashion. The fabric is made from 100-percent recycled polyester and uses per- and polyfluoroalkyl (PFAS)-free water-repellent technology, supporting sustainability goals.
Spain-based textile design software company Penelope CAD has joined Italy-based Textile Solutions Group (TSG), parent company of Datatex. The acquisition aims to create an integrated ecosystem that bridges creative design and technical production, combining Penelope CAD’s advanced design and simulation tools with TSG’s expertise in production planning, management and optimization.
The collaboration will offer businesses a seamless workflow from design to production, boosting efficiency and innovation. Datatex will play an active role in integrating Penelope CAD’s software with its proven enterprise resource planning and supply chain solutions, providing clients with comprehensive tools to optimize their textile operations.
Italy-based Tonello S.r.l. recently unveiled Denim Renaissance, a collection celebrating the elegance of Italian craftsmanship, innovation, and aesthetics, at Kingpins New York. More than just a collection, Denim Renaissance pays tribute to Italy’s art, architecture, and cultural legacy, transforming denim into a sophisticated canvas.
The collection features jeans, skirts, dresses, gilets, and jackets, blending modern style with timeless luxury. At its core, Denim Renaissance emphasizes sustainability, crafted
Wales-based DeSL has announced a partnership with Browzwear to integrate advanced digital product development technology directly within DeSL’s Product Lifecycle Management (PLM) software. This collaboration allows users to visualize design variations in color and materials, reducing the need for physical prototypes and accelerating product line creation through DeSL’s Digital Planning Boards. Key benefits include real-time 3D model annotation, enhancing collaboration between vendors and internal teams, speeding up approvals, and reducing miscommunication. This streamlined digital workflow supports faster, more sustainable product development.
“We are excited to be partnering with DeSL to integrate our digital product development technology with their comprehensive PLM solution,” said Greg Hanson, CEO of Browzwear.
“This collaboration is an important step forward in achieving our core mission of helping brands innovate faster, and meet their sustainability and business goals.”
DeSL also reports that Patagonia, Ventura, Calif., has adopted its Discover e-Solutions Color Lifecycle Management (CLM) software for automated, simplified color management.
“With DeSL’s CLM solution, we’ve seen significant improvements in our color management workflow,” said Matt Swartz, senior Color & Surface Design manager, Patagonia.
using Tonello’s advanced technologies to reduce environmental impact, redefining luxury as both exquisite and mindful. TW
Never Stop Exploring™,” is a phrase well-known to outdoor enthusiasts. The North Face, founded in the 1960s by avid climber Doug Tompkins, adopted this mantra in relation to its customers and their love for exploring outside. Beginning with backpacks, The North Face has innovated outdoor clothing and equipment for its customers to support their love of the great outdoors where environments can be hot and sunny, cold, wet or snowy, or variable.
The North Face mantra is also applicable to the company’s own drive to explore and innovate when it comes to its products. Over the decades, The North Face has expanded its product line to include clothing, shoes, bags, tents and other gear for hiking, camping, running, climbing and skiing. It was one of the first companies to create a backpack with a lightweight internal frame. The North Face also was an early
The North Face recently introduced two new fabric technologies —DOTKNIT™ and FUTUREFLEECE™ — designed to work and perform together, and as part of the Advanced Mountain Kit™ clothing layering system.
By Rachael S. Davis, Executive Editor
adopter of Gore-Tex™ technologies in the 1970s. Today, the company has a full suite of waterproof, breathable product offerings that includes FUTURELIGHT ™ and DryVent ™ technologies; as well as Ventrix™, an insulation technology that keeps your body warm without overheating, among other The North Face branded innovations.
The North Face’s DOTKNIT™ Thermal Full-Zip Hoodie (far left) and Summit Series FUTUREFLEECE™ Full-Zip Hoodie.
The company also maintains a focus on responsible products and circular design principles. By 2025, The North Face aims to have “100 percent of our leading apparel fabrics originate from recycled, responsibly sourced renewable or regeneratively grown sources.” It focuses on using recycled, biobased and regeneratively grown materials, as well as responsibly sourced down. The North Face also eliminated per- and polyfluoroalkyl substances (PFAS) chemicals from the manufacturing of its consumer products in 2024.
“In 2024, more than 90 percent of our polyester was recycled,” said Carol Shu, senior manager, Global Sustainability. “Additionally, we’re utilizing circular design principles across key product lines so that once those products reach the end of their usable life span, they can be properly disposed of and recycled or utilized
to make future products. We’ll continue to make great strides in 2025 to inch closer to our end goal.”
The brand’s suppliers are instrumental in helping The North Face bring technologies to market, but innovations are tailored for The North Face consumers internally.
According to Forrest Cannon, Materials manager, Innovation Development, the company focuses on a three-step process for technology development:
•Research and validation;
•True technology development; and
•Deployment of technology.
“This approach allows our team to thoroughly understand the key characteristics of a technology influencing performance, to develop it into essential styles and applications that best serve our consumers, and to strategically incorporate the technology into our product line in a meaningful way,” Cannon said.
“Our process always begins with a problem to solve,” said Kyle Parker, product director, Apparel Innovation. “The team constantly meets with athletes, consumers and internal teams who provide inspiration in many ways —a new project in the mountains, a ‘perfect layer’ solution that may not exist, or even a simple idea about the way they’d like a material or garment to feel or perform. All of these serve as inputs that we brainstorm and consider in our design process, looking beyond existing solutions from our supply chain for inspiration for our starting point.”
New Introductions
DOTKNIT™ and FUTUREFLEECE™ are two new fabric innovations recently introduced to the market by The North Face.
“DotKnit technology was born as a solution for managing moisture in the mountains,” Parker said. “In high alpine environments, moisture trapped next to the skin can cause hypothermia. As a result, athletes will moderate
DOTKNIT™ fabric’s textured, double-knit structure and engineered holes allow for increased air flow and sweat evaporation.
FUTUREFLEECE™ features a grid pattern alternating between areas of looped yarns and flat knit areas. The high/low areas trap heat, increasing warmth and helping to regulate body temperature.
their exertion to manage their sweat rate as a function of safety.”
DotKnit material is a lightweight, double-knit fabric featuring a textured dot pattern. The fabric was designed to pull moisture from the skin and transport it to the outside of the fabric away from the body to reduce the risk of hypothermia. The trick is in the yarn choices. Two polyester yarns are used —the inner yarn is modified to be hydrophobic, and the outer yarn is hydrophilic. The yarns plus the engineered “holes” in the knit construction create a conduit to move moisture from the skin and through the fabric. The knit construction also contributes to increased airflow to help with sweat evaporation.
DotKnit garments —mostly tees and tops —are designed as a first layer to be worn directly next to the skin under a midlayer or an insulating layer.
DotKnit fabric’s construction focuses on moving the moisture directionally away from the body according to Cannon. “In a DotKnit fabric, the majority of evaporative cooling will occur away from the skin, which allows our athletes and consumers to stay drier and warmer in high aerobic, cold weather activities,” Cannon said.
Internal testing laboratories at The North Face test for one-way moisture transport, evaporative resistance and air permeability to
ensure the fabric meets the needed moisture and thermal benefits required for the application.
“A key point of difference between DotKnit technology and other ‘standard’ baselayers is that it actively moves moisture from the body,” Cannon noted. “Standard wicking tests only quantify how far the moisture has spread across a fabric, but not directionally from one side to another, which we test for with DotKnit fabric. Additionally, we have our world-class athletes testing our materials through a variety of climates and activities. They do a great job making sure we can stand behind our motto of ‘Athlete-Tested, Expedition-Proven!’”
DotKnit fabrics, used broadly across the product line, form part of The North Face’s Advanced Mountain Kit™, its alpine climbing system comprised of five technologies designed for layering. The North Face plans new silhouettes and material variations for several seasons to come, according to Parker.
FutureFleece fabric is another new technology that is part of the Advanced Mountain Kit. “Designed to be worn as a first layer over a
baselayer, like DotKnit garments, or as a next-to-skin solution in cold conditions, FutureFleece fabric efficiently regulates the microclimate of the wearer,” Parker said about this fabric innovation.
The knit fabric features a grid pattern alternating between areas of looped yarns and flat knit areas. The pattern with high/low areas traps heat within the non-looped areas, increasing warmth and helping to regulate body temperature all in a fabric with an optimized warmth-toweight ratio. The full-loop construction also results in a soft next-to-skin feel.
“FutureFleece fabric is a very unique knit construction that does not require brushing like traditional fleece products,” Cannon said. “Our engineers and designers are always thinking about how to improve the performance of our technologies. In FutureFleece fabric, the incremental pile against the skin allows us to reduce weight and increase air permeability on a highly insulative fabric.”
FutureFleece technology also utilizes an octagonal-shaped “octayarn,” which is instrumental in the fabric’s performance, according to Cannon. “This highly engineered fiber features both a hollow core and an eight-fin surface structure,” Cannon explained. “The hollow core component helps boost the warmth within the fiber, while the eight-fin structure creates additional insulative air pockets within the yarn and further boosts the warmth without an increase in weight.”
To test the thermal resistance of the fabric, The North Face team used its internal lab’s Sweating Guarded hot plate. “FutureFleece fabric has shown to have the highest warmthto-weight ratio out of the fabrics we’ve tested,” Cannon shared.
This warmth-to-weight property of FutureFleece fabric makes it the athlete’s most used layer across the entire range of activities and geographies, according to Parker. The fabric currently is featured in several silhouettes and material weights across The North Face’s Summit Series, from quarter zip
crew neck styles to full-zip hoodies. “This offering covers the needs across a wide variety of activity use cases,” Parker said. “We will continue to expand FutureFleece fabrics into Hike and Trail run in the seasons to come.”
DotKnit and FutureFleece technologies pair well together and have a purpose within The North Face’s Advanced Mountain Kit layering system. “When DotKnit fabric is combined with FutureFleece fabric and Futurelight — our most advanced, breathable waterproof solution — sweat is able to move and evaporate efficiently through the entire clothing system,” Parker shared.
As The North Face was developing the DotKnit and FutureFleece fabrics, the company’s sustainability goals and responsible materials choices were fully considered. “DotKnit fabric is made with recycled polyester and the garments meets our EXPLORATION WITHOUT COMPROMISE™ criteria,” Senior Global Sustainability Manager Shu reported. “FutureFleece fabric currently has 37percent recycled content and hasn’t reached the Exploration Without Compromise criteria; however, in a future season, this fabric will be converted to 100-percent recycled content and the garments will meet Exploration Without Compromise.”
As The North Face looks to the future, its commitment to innovation, sustainability, and performance remains unwavering. By continually pushing the boundaries of material technology and embracing circular design principles, the company not only supports outdoor enthusiasts in their adventures but also protects the environments they cherish. With a legacy rooted in exploration and a vision focused on responsible growth, The North Face is poised to lead the way in creating products that inspire, perform, and preserve for generations to come. TW
Circ®,Danville,Va.,has launched Fiber Club,a collaborative initiative with Fashion for Good and Canopy aimed at accelerating the adoption of recycled materials in the fashion industry.The program enables brands to validate and integrate recycled fibers through a four-phase process, reducing costs and complexity by streamlining supplier engagement and combining brand volumes.The inaugural focus is on Circ’s staple lyocell fiber,with plans to expand to more materials.
Partners include supply chain leaders Birla Cellulose,Arvind,and Foshan Chicley,alongside brands like Bestseller,Eileen Fisher,Everlane,and Zalando.This collective effort facilitates the scaling of Next Gen materials through simplified supply chain integration and bulk pricing strategies.
“By collaborating with brands and streamlining supply chain integration,we’re making it easier than ever to adopt recycled and Next Gen materials at scale — starting with our Circ Lyocell,” said Circ CEO Peter Majeranowski.
Austria-based Lenzing Group has expanded its LENZING™ Lyocell Fill portfolio within the TENCEL™ family, introducing a finer fiber variant with various cut lengths tailored for home textiles and apparel.According to the company,the new fibers enhance thermal comfort,moisture control, and form-keeping properties,while offering greater design versatility. Suitable for carding and blow-fill technologies,the fibers blend well with materials like polyester and down,catering to applications such as pillows,comforters and stuffed toys. Produced from responsibly sourced wood,the fibers are EU
Eco- and ClimatePartner-certified, supporting sustainability by reducing reliance on fossil-based materials.
Los Angeles-based Ambercycle and Shenghong Holding Group, China,have formed a strategic partnership to scale the production of regenerated filament yarns made using cycora® material.This collaboration integrates cycora into China’s value chain,supporting global demand for circular solutions in the apparel industry.Leveraging Shenghong’s advanced yarn manufacturing and Ambercycle’s circular materials expertise,the partnership aims to accelerate the transition to a circular economy, reducing reliance on virgin materials.
“Our partnership with Shenghong underscores our shared vision for a circular future,”said Shay Sethi, co-founder and CEO at Ambercycle. “Together,we’re not just scaling production; we’re driving the adoption of circular materials across the apparel industry at the pace necessary to meet the growing demand.”
Universal Fibers®,Bristol,Va.,is strengthening its investment in nylon 6,6 capabilities to support customers following Ascend’s exit from the bulked continuous fiber (BCF) business.This move ensures continued access to nylon 6,6 offerings,backed by capital investments in new spinning capacity for solution dyed nylon (SDN) and natural yarns. The company aims to meet evolving market demands while reinforcing its commitment to product innovation and customer satisfaction.
“Universal Fibers is excited to capitalize on this opportunity,”said Marc Ammen,CEO of Universal
Oerlikon Barmag, Evonik Partner On Chemical PET Recycling
Oerlikon Barmag and Evonik,both based in Germany, have announced a strategic partnership to advance chemical recycling of polyethylene terephthalate (PET) waste. The collaboration focuses on developing efficient depolymerization and purification technologies,integrated with repolymerization processes and scalable Engineering,Procurement and Construction (EPC) business models.This joint effort aims to commercialize a cuttingedge PET recycling technology by the end of the decade, fostering a global network of development partners.
Oerlikon Barmag brings expertise in polymer processing for fibers and packaging,while Evonik contributes innovative catalytic processes to enhance recycling efficiency.The technology will allow seamless integration into existing PET production, handling contaminated and mixed PET waste that currently ends up in landfills or incinerators.
“Our new catalytic processes and chemical technologies will complement the current mechanical recycling approach enabling high recycled PET content from heavily contaminated and mixed PET waste that would otherwise be incinerated or landfilled,”said Max Preisenberger,head of Catalysts at Evonik.
Fiber Systems.“We are confident that the addition of these resources will complement our existing product offerings and further underpin our commitment to product innovation,customer satisfaction and long-term growth.” TW
COMPANY PROFILE
Breakthrough enzyme technology company Samsara Eco’s Co-Founder Vanessa Vongsouthi (right) with Founder and CEO Paul Riley .
and put his 30 years of experience in venture capital and private equity business development to work.
Scaling Samsara Eco’s technology enables infinite recycling without quality degradation and eliminates the need for creating new plastics from fossil fuels.
TW Special Report
Commercializing Co-Founders Spence and Vongsouthi’s research would allow for infinite recycling without quality degradation and eliminate the need for creating new plastics from fossil fuels or plants.
Samsara Eco was launched with the backing of Main Sequence — Australia’s “deep tech” investment fund — and Woolworths Group, and in partnership with ANU, all drawn to Samsara’s mission to “decouple fossil fuels from plastics manufacturing, by delivering new plastics comprised of 100-percent recycled material — with no virgin plastics supplementation needed.”
RRecycling textiles and plastic waste has been top-of-mind among many leaders in the textile industry under the guise of sustainability for some time now.
Thought leaders have led the charge, conferences have been held, and no shortage of articles have been written on this very hot topic. And in time, real investments, innovations, and products have come to market. But there is still much work to be done to achieve a serious level of circularity in the textile industry.
Mixed waste often consists of various plastics, contaminants, dyes and other components presenting a conventional recycling nightmare that necessitates sorting and often some degree of cleaning prior to further processing.
There is something to be said for a more efficient recycling process but regrettably, meeting the challenge is no simple task.
Founded in 2021, Australia-based Samsara Eco has made strides in
mixed waste recycling with a continuous enzymatic approach that alleviates waste sorting, breaks both polyester and nylon 6,6 waste down to their respective monomer building blocks, and doesn’t gobble up a lot of energy in the process.
By engineering plastic degrading enzymes that can break down plastics to their most basic building blocks — from polymers to monomers — the Samsara platform streamlines the mixed waste recycling process.
The very definition of samsara is the “cyclicity of all life, matter, and existence”.
As Ph.D. students at the Australian National University (ANU), Matthew Spence and Vanessa Vongsouthi focused on engineering plastic-degrading enzymes. Their work formed the foundation of Samsara Eco’s infinite plastic recycling technology platform.
Paul Riley, who saw the technology’s potential, founded Samsara Eco to address global plastic pollution
Riley, founder and CEO of Samsara Eco, explained: “I had been searching for a solution to the plastic crisis for nearly a year when a serendipitous moment led me to the research at ANU. The moment I saw it, I knew it could change everything. It had the potential to tackle both the waste and carbon problems associated with plastics.
“As we’ve scaled the technology and run trials with brands and partners, we’ve witnessed how this potential can become a reality. And, while there’s still a long way to go in solving the plastic crisis, our progress over the past four years — advancing the ability to recycle even the most challenging plastics, including mixed plastics and textile blends — offers real hope for a fossil-fuel, waste-free future.”
Samsara’s enzyme platform has broad capabilities that can depolymerize polyethylene terephthalate (PET) and polyester plastics; nylon 6,6, including dyed and spandex blended textiles; and hard-to-recycle plastics.
Moving the technology forward, the Samsara team created the brand EosEco™ to signify its patented recycling technology and the combination of biophysics, chemistry, biology, and computer science, including AI, used in creating its plastic-eating enzymes.
The Samsara Eco team has taken scaling enzymatic recycling seriously from the get-go.
Starting with a lab scale model in 2021, it created a pilot line in 2022 followed by a prototype of two batch lines — for polyester and nylon 6,6 — in 2023 and 2024 respectively.
Two, larger scale commercial proof of concept R&D lines will come online during 2025, and the team has sights set on delivering a 20-kiloton commercial plant in 2027.
“Textile-to-textile recycling is becoming increasingly important as minimum recycled content mandates and extender producer responsibility regulations come into force in the EU and elsewhere around the world,” said Samsara Eco Chief Commercial Officer and COO Sarah Cook.
“Brands are having to rethink their entire global supply chains with these regulations in mind, and it’s placing a greater need for solutions like ours.
“We help brands take control of the entire lifecycle of their products, while also helping reduce scope emissions. That’s a really appealing proposition for companies,” Cook added.
Regarding the company’s ability to recycle nylon 6,6 and its recently announced enzyme capable of recycling nylon 6, Cook said: “There are really limited solutions for recycling nylon so our ability to recycle nylon 6,6, nylon 6 and polyester is a significant advantage. The broader industry’s recent focus tends to be on recycling pure polyester textiles largely because polyester accounts for approximately 57 percent of global fiber production. However, for a huge
segment of the market, particularly sports and outdoor wear, athleisure, intimates, hosiery and even automotives, nylon is widely used, and they need a solve to handle their waste and excess. We are uniquely positioned to help them fill this gap.
“We are working with a range of potential feedstock partners including the brands, mills, existing collectors and other potential sources within the nylon 6,6 supply chain,” Cook continued. “The feedstock will be both post-industrial and postconsumer waste that will go through our enzymatic recycling technology.”
Developing a process from bench chemistry to a full-blown plant is one thing, but developing industry partnerships and gaining acceptance takes significant effort as well.
In February 2024 Vancouver, British Columbia-based brand lululemon announced: “Using recycled
lululemon’s iconic Swiftly Tech Long-Sleeve Top created with Samsara Eco’s recycled nylon 6,6.
This is an incredibly significant moment for the future of sustainable fashion and circularity.”
lululemon also noted that, “This milestone in lululemon’s multi-year collaboration with Samsara Eco is
nylon 6,6 made with Samsara Eco’s technology, lululemon has created samples of its iconic Swiftly Tech Long-Sleeve Top, representing the first time this type of nylon has been recycled in this way.”
Riley said at the time: “Our work with lululemon represents a groundbreaking step forward in tackling the challenge of textile waste and demonstrates the potential to create a fully circular ecosystem for apparel.
“We’ve started with nylon 6,6, but this sets the trajectory of what’s possible for recycling across a range of industries as we continue expanding our library of plastic-eating enzymes.
one way lululemon is advancing its goal to make 100 percent of products with preferred materials and end of use solutions by 2030.”
In August 2024, Samsara signed a memorandum of understanding (MoU) for apparel with Israel-based nylon 6,6 producer NILIT. Regarding the MoU, Ilana Melamed, NILIT general manager, explained: “NILIT’s partnership with Samsara Eco is a critical step in our multi-pronged strategy to provide the apparel market with premium nylon 6,6 products that have lower environmental impact.
“Implementing textile-to-textile recycling solutions will substantially decrease global carbon emissions and reduce the 92 million tons of textile waste added to landfills annually. Together, NILIT and Samsara Eco have the potential to produce infinitely recycled nylon 6,6 that delivers outstanding fabric quality and performance while benefitting the planet.”
In September 2024, Samsara Eco received an “ITMF Sustainability & Innovation Award” presented by the Zurich-based International Textile Manufacturers Federation (ITMF) at its annual conference held in Samarkand, Uzbekistan.
ITMF Awards recognize outstanding achievements by actors in the global textile industry in two categories — Sustainability & Innovation and International Cooperation. According to ITMF, these awards highlight the textile industry’s commitment to sustainability and global cooperation, showcasing innovation and collaborative efforts that are driving progress towards a more sustainable future.
The ITMF Sustainability & Innovation Award was presented in honor of Samsara’s development described
as, “Endless Plastic Recycling: A Solution for Textiles Out of Use.”
In June 2024, Samsara Eco raised $100 million Australian dollars ($65 million) in a Series A+ funding round. According to ESG Today — a website dedicated to covering environmental, social and governance (ESG) issues for investors — the funding was led by Temasek and Main Sequence, with participation
from investors including Wollemi Capital, lululemon, Hitachi Ventures, Titanium Ventures and DCVC.
It has also been reported that the funding will be used for facilities across Southeast Asia.
Regarding the investment, Cook stated: “Our latest funding will facilitate the development of two major recycling facilities — one for nylon and another for polyester. We expect these facilities to commence commercial operations during 2027 and will be established as joint ventures with leading plastic polymerization companies.”
Vongsouthi serves as head of Science Operations & Research founder and is focused on optimization of the company’s enzymes. She has often stated: “All the plastic we’ll ever need has already been produced. With infinite plastic recycling, we can view waste as a valuable resource and put a ‘full stop’ to the production of virgin plastic from fossil fuels.”
Accomplishing the company’s mission to divert plastic from landfills and oceans while creating a truly circular economy for plastics has become more than Riley’s vision for Samsara Eco — it’s reality. TW
Researcher Amanda Forster examining near-infrared spectroscopy data obtained from clothing and textile samples.
(Images
NIR-SORT, a new National Institute of Standards and Technology (NIST) database, can be used to identify and help sort textile waste.
TW Special Report
PPicture this: You have a bag of heavily used clothes that can no longer be donated taking up space in your closet, so you drop it off at your local recycling center. But what happens to that bag of clothes? You might assume that the clothes would get broken down and reused to make new products.
However, according to the Environmental Protection Agency (EPA), in 2018 around 85 percent of used clothes and textiles headed to landfills and incinerators1, wasting precious resources and polluting the environment. One reason is that recycling can be more expensive than landfilling, so companies have little incentive to recycle.
To help solve this problem, researchers at the National Institute of Standards and Technology (NIST), Gaithersburg, Md., have developed a database that contains the molecular “fingerprints” of different kinds of textile fibers that can enable more
rapid, efficient sorting of fabrics at recycling centers.
“This reference data will help improve sorting algorithms and unlock the potential for highthroughput sorting, which requires less manual labor,” said Amanda Forster, a NIST materials research engineer. Forster leads the NIST project focused on keeping end-of-life textiles in the economy, a process called textile circularity. “That should reduce costs and increase efficiency, making textile recycling more economically viable.”
The problem of textile waste has been growing in recent years. One reason is fast fashion, a business model that has companies churning out large volumes of inexpensive, trendy clothes that are often quickly discarded. New types of textiles, blended textiles, and incomplete or inaccurate labeling also pose significant challenges when it comes to sorting textiles at recycling centers.
At those centers, workers sort clothing using handheld devices that shine near-infrared light. Those devices measure how much of the light passes through or scatters off the fabric, producing a unique pattern — a sort of fingerprint that can identify the type of fibers in the clothing. This technique, called near-infrared (NIR) spectroscopy, can also be used in automated conveyor belt systems. However, current techniques still require a lot of manual labor.
In recent years, recycling equipment manufacturers have increasingly used machine learning and artificial intelligence to improve their sorting algorithms. To train these algorithms, they need high-quality reference data.
That’s where NIST’s database comes in. Called the Near-Infrared Spectra of Origin-defined and Realworld Textiles, or NIR-SORT, it contains 64 different fabric types along with the NIR fingerprints they produce. The database includes single fiber types, such as cotton and polyester; blended fiber types including spandex blends; and real-world fabrics taken from thrift stores. Manufacturers of NIR scanner systems can use this database to train and test
A clothing sample is analyzed using an analytical lab technique called near-infrared spectroscopy. The method measures how much of the light passes through or scatters off the fabric, producing a unique pattern — a sort of “fingerprint” that can identify the types of fibers found in clothing.
their sorting algorithms and improve the performance of their products.
“The difficulty comes in when fibers are similar, like cotton or hemp,” noted NIST research chemist Katarina Goodge, who led the development of the database. “That means that the near-infrared signal is similar. The same is true with a cotton and polyester blend. Is this a new fiber or a blend of two or more
NIST researchers have developed a database that contains the molecular “fingerprints” of different kinds of fabrics using clothing and textile samples as shown.
fibers? AI can help make the decision-making process more accurate.”
Because NIST is the nation’s measurement institute, it has the equipment and expertise to fill this database with very high-quality spectra. This hopefully means fewer errors when identifying fabrics, which will lead to more textiles recycled.
This research stems from a key initiative of a report by NIST 2 in which experts recommended the development of better technology for identifying and sorting textiles and clothing. These efforts are part of NIST’s Circular Economy Program 3 , which develops measurement science and methods to support an economy where materials are designed to retain their value through repeated reuse, repair and recycling, with disposal as a last resort. TW
References:
1https://www.epa.gov/facts-and-figures-about-materialswaste-and-recycling/textiles-material-specific-data
2https://nvlpubs.nist.gov/nistpubs/SpecialPublications/ NIST.SP.1500-207.pdf
3https://www.nist.gov/circular-economy
Editor’s Note: The database is free and available to download from NIST’s Public Data Repository: https://data.nist.gov/od/ id/mds2-3325
Austria-based ANDRITZ recently commissioned a state-of-the-art teXline bast fiber line at Ekolution’s new factory in Malmö, Sweden, boosting the company’s capacity to produce hemp fibers and nonwoven felts made using industrial hemp. The installation includes equipment for hemp decortication, refining, and a neXline airlay flexiloft+ line, capable of producing up to 1.5 tons of nonwoven felt per hour for various applications. The materials are used to produce Ekolution’s bio-based, sustainable building materials.
In other company news, ANDRITZ supplied and commissioned two new teXline bast fiber lines for France-based Van Robaeys, enhancing the company’s production of cottonized flax fibers. These customized lines can process up to 800 kilograms per hour and meet growing demand in France for natural, high-quality textile fibers. This marks Van Robaeys’ seventh and eighth ANDRITZ cottonizing lines, with the first in operation for 50 years.
Tex-Tech Industries Inc., Kernersville, N.C., has completed the acquisition of Fiber Materials Inc. (FMI) from Spirit AeroSystems Inc., expanding its portfolio of hightemperature materials and reinforced composites. FMI, based in Biddeford, Maine, and Woonsocket, R.I., specializes in carbon/carbon composites used in thermal protection systems, re-entry vehicle nose tips, and rocket motor components, with products featured in NASA programs like Stardust, Mars Curiosity, Orion and Mars 2020.
FMI’s 400 employees and senior management team will remain in their current roles, ensuring continuity in operations.
“FMI’s unique capabilities will allow us to better service the rigorous material requirements in the rapidly growing space and defense industry,” said Scott Burkhart, CEO of Tex-Tech.
Piana Technology, a 442-year-old Italy-based textile company, has achieved net-zero energy consumption at its Nonwovens facility in Cartersville, Ga., by fully offsetting its energy use through an expanded solar panel system. The photovoltaic system adds more than 1.24 million kilowatt-hours annually to the facility’s production capability, helping the company avoid 920 tons of carbon dioxide emissions per year — equivalent to the carbon sequestration of 250 acres of trees.
Excess solar energy is fed back into the city’s grid, contributing to the local power supply. This milestone aligns with Piana’s broader sustainability goals and sets a benchmark for other manufacturers.
“This is an exciting milestone for our ongoing sustainability goals, and it will set a new high bar for all of our manufacturing facilities,” said Andrea Piana, CEO of Piana Technology. “This is the future. You can do it better and do it greener.”
Acme Mills Co., Detroit, has launched Natura, a new line of bio-based polylactic acid (PLA) fabrics designed to replace petroleum-based textiles like polyester, polypropylene and nylon. Made using renewable resources such as corn starch and sugarcane, Natura fabrics are biodegradable under industrial composting conditions and reduce greenhouse gas emissions by up to 75 percent compared to traditional plastics.
Brooklyn, N.Y.-based Loomia and Advanced Functional Fabrics of America (AFFOA), Cambridge, Mass., have introduced the Gentoo Flexible Heater, a thermoplastic polyurethane-based resistive heater engineered for ultra-cold environments as low as -60°C. Designed for seamless integration into textiles, it combines comfort, breathability, and four-way stretchability, making it ideal for both commercial and military applications.
The Gentoo Heater maintains consistent performance even after 20 wash cycles, with minimal resistance changes, and can be laminated into a variety of fabrics, offering versatility across industries like outdoor gear and specialized coldweather equipment, according to the developers.
“Heating technology like the Gentoo Heater will play a major role in the future of highperformance textiles to protect warfighters and civilians in extreme temperatures,” said Sasha Stolyarov, CEO of AFFOA.
The product range includes spunbond nonwovens, needled felts, hydroentangled and meltblown textiles, serving industries like food and beverage, automotive, packaging, furniture and healthcare. Supported by a global supply chain across Europe and North America, Natura reflects Acme Mills’ mission to deliver eco-friendly, high-performance textile solutions worldwide.
“Natura is more than just a product line; it’s a testament to our commitment to innovation and sustainability,” said Matt Utley, chief of Strategy at Acme Mills. TW
Solution-dyed INNEGRA™ increases the possible end-uses for the fiber.
Marketed under the tagline, “The Social Fiber,” INNEGRA™ works best when combined with other fibers to enhance and elevate product performance.
TW Special Report
FFibers for highly technical applications are subjected to demands where often failure is not an option. Over the years, fibers have been engineered to meet stringent technical specifications whether it be for aerospace, energy, medical, filtration, construction or automotive applications, as well as protective gear. Fibers are pushed to be lighter, stronger and perform better —all at the lowest cost.
A newer high-tech fiber on the market is INNEGRA™, a high modulus polypropylene (HMPP) fiber available from Colfax, N.C.-based Quantum™ Materials LLC (see sidebar on page 39). Innegra may be used on its own in a high-tech application. However, the most interesting thing about Innegra is that the fiber performs at its best when it is blended with other fiber types.
Recognizing this attribute, Quantum coined the phrase “The Social Fiber” to describe the unique benefits of Innegra and its ability to “play well” with other fiber types. “We like to say it performs best when it is combined with other materials where they can bring out the best in each
other,” said Jen Hanna, director of Innegra sales, Quantum Materials.
“While it cannot carry a load like carbon, it can protect those structural fibers and provide something carbon cannot. It’s the Swiss army knife of fibers, packing a lot of versatility into a lightweight package.”
For a newer fiber, Innegra has a pretty involved origin story. Originally created between 2004 and 2008 in Greenville, S.C., the fiber was first introduced to the market in 2009 by Innegrity LLC. Initially produced in Greenville and Germany at facilities where the capabilities existed, the technology was acquired in 2011 by CCH, which changed its name to Innegra Technologies. In 2014, 100percent of the production was moved to Quantum’s production facilities, and in 2023, Quantum purchased Innegra Technologies outright.
While Quantum did not play a role in the fiber’s initial creation, the company has worked to improve the manufacturing process to in turn improve the fiber quality since it began manufacturing the fiber in 2014.
Innegra has some unique and in some cases, unexplained, properties that set it apart from other technical fibers. The fiber is manufactured using a melt spun process with quench, followed by a high draw. The finished fiber is highly crystalline and porous, which results in an ultralightweight fiber with high modulus. In fact, the fiber is the lightest synthetic fiber that is commercially available.
Innegra also has a unique surface structure and cross section that feature micro voids and nanofiber bridges (See Figure 1). It is suspected that these nanofiber bridges act as shock absorbers of a sort, although this has yet to be tested and verified.
According to Quantum, other inherent characteristics of the fiber include excellent dielectric properties, low creep, density and elongation; high sonic velocity; and cold temperature stability.
Innegra also is hydrophobic — therefore performance is not impacted by moisture or water — and is chemically inert. When subjected to more than 25 different
chemicals —including acids, bases and organic solvents, as well as hydraulic fluids and oils, among other chemicals —test results showed either no effect on the breaking strength of the fiber or only a slight effect, where Quantum defines no effect as less than 10 percent and slight as between 10 and 20 percent.
Innegra has a double melt point between 162 and 164°C with the melt onset occurring above 150°C, or approximately 302°F. The fiber’s unique characteristics remain intact and continue to perform up to 150°C.
The fiber properties compared to those of a regular PP fiber are shown in Table 1.
When hybridized with other fibers, Innegra enhances perfor-
mance. “As a material that works best with other fibers, Innegra truly is an enhancer or amplifier to a product as a whole, elevating performance when combined with other materials,” Hanna reinforced.
The fiber:
• Is Tough and Durable —It can prevent fracture propagation or catastrophic failure because it is ductile and has the ability to dissipate energy;
• Dampens Vibration —Innegra dissipates energy helping to reduce vibration for enhanced protection or performance;
• Is Flexible —The fiber maintains excellent flex fatigue and does not break after many cycles of bending and flexing;
• Maintains Shape —It exhibits excellent shape retention after
Density0.91(polymer)0.91g/cc 0.84(fiber)
Tenacity(specificstrength)9.05.0g/denier 667300-400MPa
ElasticModulus200g/denier 153GPa
Elongation9.520%
long-term use and its low creep and recoil reduction extends a product’s lifespan;
• Is Fusible —Innegra maintains performance characteristics when fused and compacted into solid shapes;
• Is Impact Resistant —The fiber will quickly dissipate a tremendous amount of energy in high impact applications; and
• Is Ductile —Innegra is pliable, not brittle —even in cold temperatures —and does not lose toughness when deformed during application.
Innegra is found in a wide variety of applications including military ropes, puncture resistant insoles for firefighter boots and military jungle boots, webbing, ballistic fabrics, and lacrosse and other sports netting.
However, Innegra is used most widely in composite applications where it supports high modulus fibers to increase toughness, durability and damping, while also reducing weight. Such applications include sporting goods, automotive applications, radomes, luggage and prosthetics. For example, Innegra is combined with carbon fiber to produce tennis racquets where it reduces weight, improves impact resistance and reduces vibration. When blended with carbon and basalt fiber in hockey goalie masks, Innegra reduces the weight and vibration, and increases impact resistance. Blends comprised of Innegra, glass basalt and carbon fiber reduce weight, increase damage tolerance and increase impact resistance when used in canoes and kayaks. Innegra also can be combined with aramids and ceramic fibers in ballistic applications for weight reduction, energy dissipation, and chemical resistance, among other benefits.
It also can be combined with natural fibers. “Hybridizing Innegra with natural fibers is another area to explore that could prove to be beneficial,” Hanna mused.
“Innegra can be used in an effort to reduce over engineering,” Hanna said. “Sometimes, when products are designed, extra layers are factored in for safety as an insurance policy. Instead of overengineering with heavier or more costly materials, Innegra may be used to provide increased durability and protection without the added weight or extra cost.”
Brands currently using Innegra fiber include East Coast Dyes (ECD) for lacrosse mesh, Head, Bauer, Shimano, Swift Canoe, Nova Craft and Allied Cycle.
A Germany-based university also researched using Innegra fiber as a component in a fly bag — a textile bag designed to mitigate the risk of a blast from bomb located in passenger luggage stored in the cargo area of an airplane. The bag was designed to absorb shockwaves, contain fragments of the explosion and contain the fire. “The design was proven to perform,” Hanna said.
Innegra also offers excellent value per pound of fiber, according to the company. Compared to other highperformance fibers on the market, Innegra is competitive in price. “Innegra is a specialty fiber that aims to bring higher performance,” Hanna said. “With higher performing fibers, price tends to increase. However, keep in mind when talking per pound pricing, Innegra is 60-percent lighter than glass, 50-percent lighter than carbon and 40-percent lighter than aramids. A pound of Innegra goes a long way!”
“Quantum Materials is committed to pushing the boundaries of innovation,” Hanna noted. “As we expand into emerging markets, like composites, we continue to focus on developing advanced materials and high-performance solutions that address the most challenging technical demands.”
Originally established as a manufacturer of high-performance elastomericbased suspension fabrics, Colfax, N.C.-based Quantum Materials LLC is today a vertically integrated manufacturer with the ability to convert resin into finished fabrics all under one roof. Its 150,000-square-foot facility supports three core areas of Quantum’s business —Quantum Suspension Fabrics, Quantum Technical & Industrial Yarns and Textiles, and INNEGRA™ Quantum processes polyester, nylon, polypropylene, copolyester, and recycled and biobased materials. Yarn capabilities include monoand multifilament yarn extrusion, fully drawn yarn, yarn coating, air-jet texturing and twisting. The company also has the ability to impart a variety of additives and offers a variety of fiber cross-section options.
Quantum has more recently added solution-dyed Innegra to its portfolio, which offers greater customization options to customers. “Often times Innegra is used in the laminate where you cannot see it after production,” Hanna said. “However, there are many applications where it is visible and the solution-dyed expanded the options beyond natural or black.”
Quantum also offers a variety of coated Innegra yarns to meet the demands of different applications from ultraviolet to weather resistance and beyond. In addition, the company has experimented with a glow-in-thedark version that needs some fine tuning, but will be developed further if a good-fit application is discovered.
Hanna also noted that a new product, PROTECC, is positioned to enter the thermoplastic market this year. Protecc is a blend of Innegra and the company’s proprietary Quantum Fusion Technology. “Protecc comes in two versions, coated Innegra or Innegra hybridized fabrics, or fabrics
In weaving, Quantum has warping capacity, and can produce 2- and 4way stretch fabrics, as well as bonded and non-bonded stretch wovens.
The company prides itself on quick turn production cycles and research and development. It has in-house designers on staff and also dedicated resources for new product development initiatives. Quantum’s smaller team of approximately dedicated 90 employees is agile and adaptable, as well as focused on technical excellence, operational efficiency and rapid customer response. The company has been a trusted supplier to global companies for more than 30 years, and Quantum continues to leverage its technical expertise to overcome complex challenges while delivering high-performance solutions.
combined with a low melt adhesive yarn.” Hanna explained. “Combined with the low melt adhesive yarn, Protecc can be processed using heat and pressure —which shortens cycle times and improves efficiencies —to create high-performing durable parts.
“Today, Innegra is used in a variety of markets including sporting goods, transportation, radomes, military, protective, industrial applications,” Hanna said. “The potential is really untapped between thermoplastic composites and textiles. These are two areas we are just beginning to explore.”
The company will participate in trade shows such as JECWorld, Techtextil North America and CAMX to build awareness for the fiber and its unique opportunities.
Quantum’s continuous development of Innegra positions the company at the forefront of advanced material innovation. The Innegra journey has just begun, and the potential is as limitless as the products Quantum aims to transform. TW
Established by the Department of Energy in 2015, the Institute for Advanced Composites Manufacturing Innovation® (IACMI) has emerged as a leader in advanced composites and workforce solutions, bolstering American manufacturing and national defense.
TW Special Report
Active IACMI Members
>70%
Industrial Members Are SMEs
4,500 Professionals convened from industry supply chain
IACMI’s Impact: Collaborative efforts are tackling the industry’s toughest challenges.
TThe Institute for Advanced Composites Manufacturing Innovation ® (IACMI), also known as IACMI–The Composites Institute®, recently celebrated a decade of revitalizing American manufacturing and strengthening the nation’s defense industrial base. Established by the Department of Energy (DOE), IACMI was announced as the fifth of now 18 Manufacturing USA® institutes on January 9, 2015. The Advanced Functional Fabrics of America (AFFOA) is also a Manufacturing USA institute.
The institute comprises more than 170 members —including those from industry, universities, national laboratories and government agencies — that work together to accelerate the development and adoption of advanced composites and innovative manufacturing technologies. Its collaborative work through public-private partnerships drives domestic production capacity, strengthens U.S. manufacturing competitiveness and elevates domestic job creation.
IACMI is managed by the Collaborative Composites Solutions Corp.
(CCS), a not-for-profit organization established by the University of Tennessee Research Foundation. IACMI is supported by the U.S. Department of Energy’s Advanced Materials and Manufacturing Technologies Office, and the U.S. Department of Defense (DoD) Industrial Base and Sustainment (IBAS) Program from the Innovation and Capability and Modernization (ICAM) office, as well as key state and industry partners.
For 10 years, IACMI has played a pivotal role in America’s reindustrialization, aiming to secure its position as a global leader in manufacturing innovation and workforce development. Reshoring initiatives have been key to bolstering U.S. economic and national security. Through multiple national workforce programs sponsored by DOE and the DoD, IACMI has been inspiring, educating, and training a skilled workforce to help address the projected 4.6 million open manufacturing jobs in the coming decade.
IACMI’s impact for economic growth has been clear in four primary ways:
• Public-Private Collaborations — Convening more than 170 members and 4,500 professionals from industry, academia, and federal labs to tackle the composites industry’s toughest challenges in automotive, aerospace, wind, infrastructure and the circular economy.
• Technical Innovation — Connecting more than 90 of its members to conduct 60-plus industry-led R&D projects that helped commercialize dozens of products; advance the Technology Readiness Level (TRL) of numerous technologies; and create hundreds of design, engineering, and manufacturing jobs.
• Workforce Development Catalyzing IACMI, Americas Cutting Edge (ACE), and Metallurgical Engineering Trades Apprenticeships & Learning (METAL) programs to enable: —More than 100 internships with industry collaboration,
resulting in 100-percent placement in industry jobs or higher education;
—18,300-plus STEM outreach engagements;
—More than 12,400 trained online across 50 states in CNC machining;
—5,100-plus trained in-person in composites, CNC, metrology, and metallurgy; and
—40 machine tool training centers in 14 states.
• Leveraging Resources — Providing open access to more than $400 million in scale up facilities across eight states has led to an additional $220 million-plus for companies, universities, national labs and workforce initiatives.
“For 10 years, IACMI has harnessed the power of public-private partnerships to improve products, processes, and people’s lives through composites innovation and workforce solutions that secure America as a global leader in advanced manufacturing,” said Chad Duty, IACMI’s CEO. “With steadfast investment and support from industry and government partners, notably DOE and DoD, IACMI has empowered domestic manufacturers to accelerate design and commercialization, fostering a more reliable, secure, and competitive U.S. economy.”
Since 2015, IACMI, the DOE, and state economic development organizations have invested in a shared infrastructure that collectively delivers a breadth and scale of open-access advanced composites manufacturing R&D capabilities that stand unmatched in the U.S. These facility and infrastructure investments have been led by IACMI’s core innovation partners in Colorado, Indiana, Michigan, Ohio and Tennessee. Today, these capabilities uniquely position IACMI to build on past achievements, de-risk future research, and accelerate onshoring efforts in the United States.
Examples of state-of-the-art scale-up facilities include:
Value of scale up facilities
Additional leveraged funds
IACMI’s Impact: Open access to facilities led to additional funding for initiatives.
•Manufacturing Demonstration Facility (MDF) at Oak Ridge National Laboratory (ORNL), Oak Ridge, Tenn.;
•Carbon Fiber Technology Facility (CFTF) at ORNL;
•Fibers and Composites Manufacturing Facility (FCMF) at University of Tennessee, Knoxville, Tenn.;
•Laboratory for Systems Integrity and Reliability (LASIR) at Vanderbilt University, Nashville, Tenn.;
•The Composites Laboratory at the University of Dayton Research Institute, Dayton, Ohio;
•The Composites Manufacturing & Simulation Center (CMSC) at Purdue University, West Lafayette, Ind.;
•The IACMI Scale-Up Research Facility (SuRF) in Detroit; and
•The Composites Manufacturing Education and Technology Facility (CoMET) at National Renewable Energy Laboratory (NREL), Applewood, Colo.
IACMI has leveraged these facilities to undertake transformational R&D, in nation-critical industries including energy, transportation, aerospace, and infrastructure & construction. An IACMI-sponsored project team helped Volkswagen (VW) of America redesign and validate a composite liftgate for SUVs, reducing the weight by 35 percent and lowering its
recurring cost by 9 percent compared with steel. Technological advances from this research are now being used across multiple VW platforms, including the new VW ID Buzz EV.
The scaling, manufacture and testing of novel thermoplastic wind turbine blades that are recyclable and lower in cost has also been demonstrated. Further research in automating finishing processes for wind blades aims to reshore wind manufacturing jobs. Simulation and modeling work to develop a virtual twin for additive manufacturing is revolutionizing the production of tooling.
Today, these capabilities uniquely position IACMI to build on past achievements, de-risk future research, and accelerate onshoring efforts in the United States.Duty predicts, “Over the next few years, IACMI and its partners will leverage their full-scale facilities and equipment and significantly expand programs,” Duty said. “IACMI will continue to convene, connect, and catalyze the U.S. composites community by attracting startups and small enterprises while creating opportunities with large companies, national labs, and universities.Our ecosystem of innovation is ready to advance American manufacturing.” TW
To learn more about IACMI, visit IACMI.org.
DDuring a recent ceremony held in London, England-based B&M Longworth claimed the Make UK National Award in the Energy and Sustainability category for its development of DEECOM technology.
Longworth has a long history in the manufacture and supply of specialized cleaning and waste-reduction technologies for the polymer and coating industries and its DEECOM system exploits pressurized steam in a process called pressolysis to successfully separate and reclaim fibers and polymers from composite parts for reuse.
Enabling true circularity for materials, DEECOM completely eliminates the need for traditional dirty processes involving solvents, chemicals, burning or mechanical grinding.
Using a combination of compression and decompression cycles or
Longworth and Cygnet Texkimp are partnering to commercialize DEECOM reclamation technology for the composites industry.
By Adrian Wilson
“pressure swings,” it can gently remove a range of resins from composite fibers, effectively reversing the bond between the fiber and the matrix. The process takes place in a pressure vessel filled with superheated steam.
Depending on the polymer type, temperatures above 200°C (392°F) will melt or soften the polymer and a degree of hydrolysis will occur. When at pressure, the steam penetrates fissures in the polymer where it condenses, before it boils on
decompression, causing an instant physical fracturing of the polymer chain and carrying away monomers and oligomers along with polymer fragments from the outer faces.
Since the process interacts with the resins, it can reclaim the format, length and structure of fibers from post-industrial or end-of-life waste composites, whether cured or uncured.
“The pressolysis process enables the high-yield reclamation of highquality, clean, reusable fibers that are free from residues and have a retained length and properties akin to virgin materials,” explained B&M Longworth Director Jen Hill.
Longworth and its partners in the Emphasizing Project — EMSChemie, Ford Motor Company, Gen2plank, Gestamp, TWI and the Brunel Composites Centre at Brunel University in London — have already
Clockwise from top left: A DEECOM fiber reclamation unit has been installed at the Henry Royce Institute in Manchester, England; A B&M Longworth DEECOM fiber reclamation unit; and Cygnet carbon converting equipment at the UK’s Advanced Manufacturing Research Centre (AMRC) in Sheffield, England. (Image courtesy of Cygnet Texkimp)
received the JEC World 2024 Innovation Award in the Circularity and Recycling category.
This has focused on the reclamation of materials from end-of-life wind blades, their resizing and subsequent remanufacture into mass production car parts.
This resized material is based on DEECOM-recovered glass fibers that are treated with various chemistries to retain performance properties.
“The aim is to find several use cases for the reclaimed and/or resized material, and for the industry to gain access to a brand new, low impact advanced material at a low cost,” Hill said.
The technology is now being commercialized for the composites industry in a partnership between Longworth and England-based Cygnet Texkimp. A first DEECOM reclamation unit has recently been
installed at the Henry Royce Institute in Manchester.
Royce is bringing together nine leading institutes in a pioneering R&D program to fully investigate and commercialize new applications for reclaimed fibers.
Founded in 1974, Cygnet Texkimp, is a supplier of advanced handling and processing machinery to the advanced fibers and composites markets, with 80 percent of its machines exported to more than 30 countries. In particular, the company is a supplier of creels for unwinding high value composite fibers and tire cord at constant tension and at optimal speed into a range of downstream processes including weaving, prepregging, coating and beaming.
“It’s a time of unprecedented
growth for our company because in addition to DEECOM we are also busy with projects for the UK’s National Composites Centre and the Advanced Manufacturing Research Centre,” said Cygnet’s international sales manager Josh Ingham. “We currently have a healthy order book, especially in creels for aerospace industry suppliers, but we’re also excited about the new opportunities we believe DEECOM will open up for us.”
Both Longworth and Cygnet are members of the British Textile Machinery Association (BTMA). TW
Editor’s Note: Adrian Wilson is an England-based analyst and writer specializing in the technical textiles, nonwovens and composites industries. He is the owner of AWOL Media.
Dispersion of AGXX particles (Image courtesy of DITF)
DITF and Heraeus are researching AGXX antimicrobial technology for use in medical textiles.
TW Special Report
IIn collaboration with the Germany-based Heraeus Group, the German Institutes of Textile and Fiber Research (DITF) are developing fibers and textiles with a novel infection protection system. The basis is an antimicrobial mechanism of action licensed from Heraeus and marketed under the name AGXX. The goal of the collaboration is to optimally integrate the AGXX technology into textile finishes and coatings and to incorporate it into fiber-spinnable polymers to provide medical textiles with highly effective and long-lasting protection against microbial infections.
AGXX technology is based on an entirely new mechanism of action. It uses a catalytic redox reaction initiated by metallic AGXX particles consisting of silver and ruthenium. In interaction with humidity, reactive oxygen species such as peroxides are formed. These are oxygen-containing molecules with very high reactivity. They effectively kill microorganisms such as bacteria, fungi and algae and are equally effective against viruses.
The special feature of this mechanism of action is that the AGXX particles are not reduced and do not release any active ingredients. In established antimicrobial systems
based on the release of silver ions, the release of active ingredients has become a problem: the release of the silver ion concentration is difficult to control and many of the established systems do not meet the requirements of the European Chemicals Agency (ECHA). Such systems will disappear from the market in the medium term and must be replaced by alternatives.
In addition to permanent efficacy, the AGXX technology offers a particularly broad spectrum of protection against pathogens and prevents the formation of resistance.
Heraeus AGXX technology is used in various industries; and in general, the particles can easily be incorporated into various materials. However, textiles used in the medical sector are subject to more stringent requirements. The resistance of the antimicrobial protection mechanism must be high, as contaminated textiles can be a source of transmission of pathogens over a long period of time. Modification of the textile material, either by surface treatment —finishing or coating — or by incorporation of AGXX into filament yarns, should not adversely affect the physiology of the garment. This is because a reduction in textile properties is unlikely to be accepted by the wearers of the textiles.
The goal of the collaboration is not only to determine the optimal concentration of AGXX particles to provide the best possible protection against infection without compromising the mechanical properties of the textiles, but to also determine technical prerequisites for the development of suitable textile finishes and the compounding of polymer melts.
The resulting textile samples were tested for antimicrobial and antiviral activity in DITF’s laboratories where finishes and coatings for polyester and nylon fabrics showed convincing results. Compounding AGXX in the nylon 6 polymer melt enabled the production of filament fibers with consistently good fiber strength values.
The determination of textile mechanical parameters such as abrasion resistance, air permeability and dimensional change as a function of number of wash cycles is still in progress. However, it is becoming apparent that textiles modified with AGXX are consistently effective without having an excessive impact on the nature of the textile.
The results of the research are an important contribution to reducing the risk of infection from medical workwear. They form the basis for future industrial production of textiles for durable and reliable protection against infection. TW
For the first time,Techtextil Frankfurt 2026 will feature Textile Chemicals & Dyes as a separate product area,highlighting their growing importance in the global textile industry.This new segment will create a central hub for suppliers and users,fostering collaboration and streamlining communication across the value chain.Collocated with Fibers & Yarns and Performance Apparel Textiles,the setup aims to enhance industry synergies and accelerate solution development.
“Textile Chemicals & Dyes are becoming increasingly important for the production of technical and performance textiles,”said Sabine Scharrer,director,Brand Management, Technical Textiles & Textile Processing,Germany-based Messe Frankfurt. “At Techtextil,we will bring the players even closer together in future. In this way,we enable dialogue, comparability,and raise even more awareness for this promising sector.”
X-Rite Inc.,Grand Rapids,Mich., has launched the Judge LED light booth for precise visual color evaluation,designed to support industries transitioning from fluorescent to energy-efficient LED lighting.This new light booth,featuring seven distinct light sources,ensures color consistency across supply chains in sectors like textiles,automotive,and packaging, addressing the challenges posed by differing spectral power distributions between fluorescent and LED lights.Key features include instant warm-up,stabilized illuminants, energy efficiency,and compliance with ISO,ASTM,AATCC,and BSI standards.It also integrates with digital workflows,allowing
comparison between physical samples and digital material twins.
“Our custom-designed LEDs are optimized to offer the best SPD match for legacy fluorescent tubes,including U30,U35,CWF and TL84,ensuring a seamless integration into color workflows,”said Albert S.Laforet, director of Strategic Projects,X-Rite.
Singapore-based SHEIN increased its use of Cool Transfer Denim Printing by 90 percent in 2024, producing approximately 380,000 denim pieces with this resourceefficient technology,up from 200,000 in 2023.This innovation,developed in partnership with NTX®,reduces water usage by 70.5 percent compared to traditional denim methods — according to Bureau Veritas in October 2023 — saving more than 10,000 metric tons of water in 2024.
Cool Transfer Denim Printing uses reactive ink to digitally print designs onto transfer film,which is then applied to white denim fabric, replicating faded finishes without harmful chemicals like chlorine.
Konica Minolta,Japan,has launched the CM-3700A Plus,its latest spectrophotometer designed for industries requiring high-precision color measurement,including textiles and plastics,among others. Building on the success of the CM-3700A,the new model offers unmatched accuracy with an interinstrument agreement of ΔE*ab 0.08 or less,ensuring consistent color data across global supply chains.Key features include a built-in camera viewfinder for improved sample positioning,simultaneous SCI and SCE measurements that cut measurement time in half,and
The American Association of Textile Chemists & Colorists (AATCC),Durham,N.C.,has signed a Memorandum of Understanding (MOU) with The Textile Association (India) (TAI) to strengthen collaboration within the global textile industry. The MOU aims to promote communication,reduce duplication of efforts,support standards development,and create joint educational programs including conferences,seminars,and training.
Members of both organizations will receive a 30 percent discounted membership in the other,along with special introductory offers for TAI members.Additionally, Texas Tech University Professor Dr.Seshadri Ramkumar has been appointed as AATCC’s first Ambassador to India.
“The textile industry in India represents a robust and dynamic sector,”said AATCC President Christina Rapa.“… We eagerly anticipate supporting the Indian market with high-quality testing standards,comprehensive training programs,and valuable networking opportunities in the years ahead.”
In other AATCC news,the organization recently announced two new student chapters — at the University of Georgia,Athens , Ga.,with Faculty Advisor Suraj Sharma;and Bangladesh-based Ahsanullah University of Science and Technology (AUST) with Faculty Advisor Mohammad Tajul Islam.
environmental sensors for temperature and humidity monitoring. The device is also compatible with SpectraMagic™ NX2 software for advanced data management and supply chain communication. TW
A ribbon-cutting ceremony was held to officially open the new Fibroline USA Innovation Lab housed at the Navis TubeTex facility in Lexington, N.C.
Fibroline USAInnovation Lab introduces cutting-edge dry powder impregnation technologyto North American market.
By Jim Kaufmann, Contributing Editor
AAn advanced dry impregnation processing technology was formally introduced into the North American markets with a ribbon cutting ceremony held at Navis TubeTex in Lexington, N.C., The event marked the grand opening of the Fibroline USA Innovation Lab, which is the result of a strategic partnership between France-based Fibroline and finishing machinery manufacturer Navis TubeTex.
The new state-of-the-art innovation center showcases Fibroline’s cutting-edge technologies, and provides access for potential customers to conduct scalable trials for existing and developing applications in a wide array of market segments. According to Jerome Ville, Fibroline’s CEO, “This partnership with Navis TubeTex and the opening of this Innovation Center will help us to more effectively introduce and promote our unique technology’s capabilities to the North American markets.”
Fibroline was founded in 2003 focused on developing and engineering solutions for the global textile industry. The company owns more than 50 technology and application patents. Its dry powder impregnation technology evolved from these efforts, and since 2016, Fibroline has focused on creating strongly diversified, technology-driven applications. It has a research and development facility in France, which includes pilot lines for sampling and prototyping units for larger scale evaluations. Fibroline’s flexible business model focuses on developing performancebased applications and technologies that may be patented and subsequently licensed to interested companies on a royalty basis. The company employs manufacturing partners to produce full turnkey solutions in Europe, and now, given the partnership with Navis TubeTex, in North America as well.
In early 2024, Navis TubeTex entered into a manufacturing partnership with Fibroline after it was introduced to the Fibroline technology by Dr. Sanjay Patel, an advanced materials and process expert who consults for Navis TubeTex.
“I just felt this would be a good opportunity to introduce Fibroline’s technology to North America and open up new markets,” offered Dr. Patel. William Motchar, president and CEO of Navis TubeTex, saw the possibilities and extended an invitation to Fibroline to establish the Innovation Lab at the Navis TubeTex facility in Lexington.
“We anticipate the innovation center will become a hub for collaboration and ingenuity where we can assist our customers to explore, test and foster creative solutions to meet ever evolving market demands,” Motchar said.
The new innovation lab resides in an 800-square-foot segment of
the Navis TubeTex building with room to expand, where the company will also effectively manufacture and sell the Fibroline inspired equipment to North America customers. In addition, Navis TubeTex will provide machine engineering expertise as well as installation and after sales services.
Fibroline’s eco-friendly in-line technology is identified as a dry impregnation process, but the flexibility of the line along with its system of modular pieces that can be switched in or out depending on needs, offer up greater possibilities for both flexible and ridged composite materials. The best way to view this technology from a textile perspective is as a methodology to provide value-added performance attributes to potentially any textile material type to meet a wide selection of application needs.
In general terms, the dry impregnation begins with a powder “chemistry” that can be one specific powder, or possibly a mix of different chemistries related to the intended application. The powder chemistry is distributed onto the surface of the material to be impregnated using conventional powder processing means. As the powder-coated material passes through the machine, electrodes positioned above and below create alternating electric fields that evenly position the powder throughout the thickness of the material while fixing it to the fibers.
One limitation of this technology is that carbon fiber and other conductive materials cannot be treated because of the electric fields employed during the process. However, most any other man-made or natural material may be processed using the Fibroline technology.
It should also be noted that by controlling the current, dwell time and other machine settings, a gradient distribution of the powder may be made. For example, powder can be applied just on the surface of the
Fibroline’s facility in France features a pilot unit for scaling up trials.
material or located at specific levels throughout the thickness, including covering all fibers through the thickness. This technique allows for many unique possibilities in the impregnated structure, including surface treatments, fully encapsulated fibers, partially coated layers, thru the thickness powder coatings, consolidated thermoplastic composites, both flexible and rigid composites, to name just some of the possible configurations.
According to Fibroline, energy consumption during processing is very low compared to traditional systems. There is no rise in the temperature of the material during the impregnation process. In addition, there is no residual build-up of static electricity in the material at the end of the impregnation treatment, which makes it possible to process heat-sensitive chemistries. Also, Fibroline’s process does not require the use of any consumables. The impregnated material can then be fully cured separately or in-line using heat and pressure or whatever other means the application may require. This process does not require the use of solvents or any drying steps, and therefore the types of powders employed have very few limits. Thermoplastics, thermosets, medical additives, flame retardants, absorbents, and numerous other types of
Open house visitors were given a demonstration by Fibroline’s Sofien Bouzouita of the static lab unit, which can be used for preliminary trials.
chemistries can be utilized. It’s possible to process powders from 5 microns to 500 microns in size. Single or multiple chemistries can be applied during the same process. Theoretically, any powder or combination of powders can be applied. For example, a medical powder —a vitamin or pharmaceutical perhaps — could be combined with a biodegradable binder to create a time release platform or other chemistries. Colors may be employed together to produce multiple characteristics on the same material. Of course, there are sure to be limitations, but untold possibilities exist with this type of technology.
Powder
Porous Substrate
Plasma
Homogeneous Impregnation
Product and application development, chemistries evaluations, proof of concept or feasibility trials are also within the capabilities of this equipment. Larger product development and pilot validation trials can be performed at Fibroline’s R&D facility in France.
A variety of “porous structures” can be processed using the Fibroline dry impregnation process. These include nonwovens and foams along with most variations of woven and knit textiles as well as technical yarns, fiber roving, tapes, and assorted composite materials.
There currently are three different impregnation technologies to choose from depending on the intended applications. The “D-Preg” technology is more of a traditional inline process intended for large industrial
Filtration
• Odor capture
• VOC absorption
applications. The “S-Preg” technology is designed for applications requiring lower powder content and a high level of accuracy in powder distribution. The “Y-Preg” system has been developed specifically for processing yarn and unidirectional tapes and does allow for the processing of multiple bobbins in parallel.
The equipment installed at the Navis TubeTex innovation lab is in concert with the D-Preg technology, but downscaled and designed primarily for technology demonstrations.
Military
• CBRN protective suits
• Ballistic protection
• Helmets
• Water depollution Transportation
• Headliners
• Package trays
• Door panels
Medical
• Homeostatic patches
• Wound dressings
• Gauzes
Personal Care
• Sheet masks
• Skin care pads
• Wipes
Composite Tapes & Prepegs
• AFP tapes (GF, NC, Aramid...)
• Filament winding tapes
• Glass/natural fiber mats
Technical Yarns
• Rubber reinforcements
• Braided packings (seals)
• Racket strings
• Medical yarns
Fibroline’s dry powder impregnation technology may be used for a wide variety of applications across a diverse group of markets.
As suggested previously, the number of existing and potential applications for this technology is truly mind-boggling. During an introductory presentation and tour of the new innovation center, a variety of products and possibilities were discussed. Dr. Sofien Bouzouita, Fibroline’s Innovation manager highlighted examples of current applications including Ethizia ™ , a hemostatic sealing patch from Johnson and Johnson; wound dressings from Smith and Nephew; technology licensed to Depestele, Europe’s leading flax producer, for unidirectional tapes made from flax fiber; and automotive headliner technology licensed to foam manufacturer Howa Tramico that will be available in 2026.
Other applications in development with partners include rubber reinforcements to improve tire manufacturing and longevity, active air and water filtration systems, as well as active filtration systems designed for protection against chemical, biological, radiological and nuclear malicious-use agents. In addition, flame retardancy, thermal insulation and composites markets continue to find opportunities for this technology, not to mention all the others yet to be discovered.
Ultimately, given the nearly endless combinations of chemistries, substrates or materials impregnated, and the modular combinations of the processing technology, the beauty of this system is truly in the eyes and creative minds of its beholder. The employees and consultants at both Navis TubeTex and Fibroline are certainly willing and able to initiate the various conversations necessary to validate this technology and the numerous technologies that may follow. Here’s to its bright future! TW
Datacolor provides light booths that can simulate a variety of lighting conditions for color assessment.
Getting color right the first time reduces waste, saves time and offers value to customers.
By Basto Wong
TTo improve the value they provide to their customers, some industry-leading brands and major retail chains now require their suppliers to follow tighter quality and sustainability guidelines. These include mandates to use color specification and quality control (QC) technologies throughout their supply chains.
Companies hope to achieve multiple goals by specifying these technologies. First, they reduce the environmental impact caused by waste-producing color mistakes that can occur during manufacturing. In addition, they help provide universal
color consistency — a benefit at every stage of the supply chain and to customers as well.
Although many brands have been utilizing color management technology in their own facilities for years, these requirements are now being extended to current and would-be suppliers. The reasons are well justified. Color management systems can help reduce waste, save time, provide consistent color QC across multiple locations, and improve communication between brands and their suppliers.
Implementing the necessary hardware and software tools isn’t enough, however. To ensure supply chain
Many well-known brands utilize color management technologies to bring endto-end color solutions to their supply chains. Common packages include:
• Spectrophotometers : Highprecision benchtop instruments used for close-tolerance color measurement, ensuring uniform assessment of materials across the supply chain.
• Performance monitoring : A predictive measurement monitoring system that assists with the calibration of spectrophotometers and correlates to master instruments to ensure performance meets a brand’s requirements.
• Formulation software : Amplifies the accuracy of color development, improving QC and productivity. This can significantly reduce the need for physical matches and improve first-shot match rates, shortening formulation time.
• QC software : Enables objective analysis, reporting, communication
consistency and transparency, many vendors are also being required to prove they can meet color standards by participating in a color management verification program.
Quality-conscious brands take color consistency seriously. To ensure that their suppliers’ color programs and processes meet specified standards, many are increasingly turning to verification and certification processes. Experts recommend that each supplier be assessed by a third-party authority such as Datacolor Certify, a color assessment and lab audit program that also provides training services.
The auditor will check for conditions within the manufacturing process that can affect color quality, such as:
•Operator expertise, skill, knowledge, and ability to use color management software and technology properly;
and visualization of accurate color results.
• Industry-specific applications: Specialized software is available to meet the unique needs of certain industries, including textiles, apparel, home furnishings, paint and coatings, plastics, and other applications.
• Light booths : Viewing stations that simulate a variety of lighting conditions, including daylight, common light sources used in retail stores, typical home and office lighting, LED, ultraviolet, and more. This enables visual color assessments of inks, paints, plastics, textiles, paper, colorants and other materials. Calibrated light booths across the supply chain promote consistency in color decisions by ensuring that everyone evaluating samples views them under similar lighting conditions.
• Operator training : Remote or hands-on instruction provided by experts fluent in the operator’s local language.
•Overall equipment performance, condition and calibration; and
•Humidity, temperature and other environmental factors.
Assessments typically involve a combination of off-site and on-site inspections designed to ensure that the supplier is qualified and capable of meeting a brand’s color quality expectations. Inspections should ideally be performed annually to ensure that proper color developmental procedures are followed consistently over time.
By implementing regular color management assessments like this across their supply chains, brands can achieve multiple goals, including:
•Reducing the overall number of lab dips or samples;
•Reducing or eliminating shipments of physical color samples for approval;
•Easing the environmental impact of repeat production by minimizing color matching and formulation errors;
•Increasing speed to market;
•Verifying the color capabilities of suppliers;
•Empowering vendors to make decisions locally, eliminating delays waiting for guidance — especially from customers in distant time zones; and
•Ensuring consistent quality for end customers.
Although verification is typically required by brands or retailers, suppliers are often the primary beneficiaries when it comes to cost savings. For those in the apparel sector, for example, color approval processes that used to involve as many as six lab dip submissions can potentially be streamlined to only one or two. Those kinds of savings add up quickly because a single lab dip can cost more than $100. Lab dip samples also must be ferried back and forth between brands and suppliers, incurring additional costs and creating unnecessary carbon emissions. The savings in time, money and resources from these two benefits alone can easily justify the effort of verifying a color program, both for brands and suppliers.
Certification can empower qualified suppliers in other ways. Being able to self-approve samples that meet measurable specifications delivers increased production efficiency and opportunities to optimize the color developmental process. Suppliers can also reach more brands by showcasing their capabilities. A universal accreditation program is especially advantageous, because a single annual certification can satisfy the requirements of multiple brands.
Suppliers often become validated in response to mandates from their customers, but they can also benefit by seeking certification proactively. Certified suppliers are automatically more attractive to brands because
they’ve already proven their color management capabilities; the brand doesn’t have to worry about training or lag time. In addition, some certification providers maintain databases that brands can search when looking for suppliers to work with.
Brands benefit from the capability to respond to market demands faster, with the confidence that color quality from all their suppliers will meet their expectations.
Implementation across an entire supply chain can shave several weeks off color developmental and production processes while providing greater transparency. In cases where the same color is being utilized by multiple suppliers, brands can expect much greater consistency and fewer rejections. Partnership with a third-party validation authority also eliminates the time, administrative and travel costs needed to send knowledgeable team members overseas to certify suppliers.
In addition to improving the consistency and quality of products, partnership with a verification service can help support more sustainable supply chains. Wasted time, money, labor, materials and resources are
Color consistency within the every stage of the supply chain is critical to a brand’s success.
significant issues for all industries. Minimizing the unnecessary carbon emissions associated with shipping samples or transporting team members across continents are also relevant concerns.
Getting color right the first time is the best way to reduce all of these things. This commitment to sustainability aligns with broader corporate responsibility goals established by many organizations, whether for their own sake or in response to regulations.
An expert verification service can help a company achieve more ambitious color formulation, measurement and QC goals. Here are some key factors to consider when evaluating potential partners.
Start by looking for a vendor that also makes high-quality measurement tools themselves, rather than relying on hardware from a third party. Its instruments should be capable of adhering to the industry’s tightest color tolerance ranges and have high inter-instrument agreement. With proper usage, good instruments can prevent suppliers from accidentally shipping products with off shades.
It’s important to also make sure instruments have 100-percent backward compatibility. This will ensure that any valuable color data curated over the years won’t be lost because of incompatibility with newer instruments when it’s time to upgrade.
In addition to trusted and reliable products, look for a partner with an even more valuable asset — people. Hardware and software should be supported by experts who have experience working in the industries they serve — ideally, for many years. This will ensure that they’re not only proficient in their company’s products and services, but have a deep understanding of your industry’s unique needs and challenges.
Finally, make sure any investment in a solution is backed by a global team capable of providing guidance every step of the way, from choosing the right solutions through final installation and continued support thereafter. A partner should have a dedicated local support team that speaks regional languages and is ready to help should problems arise. TW
Editor’s Note: Basto Wong is the Service Project manager and head of Assessments at Lawrenceville, N.J.-based Datacolor.
Team FIMIC prides itself on working with passion, forward thinking and an innovation-based culture.
FIMIC technology provides solutions that eliminate impurities and lead to efficiently processed, high quality recycled products.
TW Special Report
FFIMIC S.r.l., a family-owned company based in northeastern Italy, has a rich history in recycling technology that spans over more than six decades. Located in Carmignano di Brenta — in the Veneto region of Italy about 30 miles northwest of Venice — FIMIC initially focused on manufacturing guillotines for cutting industrial waste bales and rolls. This initial focus was just the beginning of a long history assisting companies with innovative recycling technologies.
FIMIC’s early success manufacturing guillotines continues today, building on a reputation for robust, long-lasting, low maintenance machines that feature Italian crafts-
manship and technology that has reinforced its status as FIMIC’s “flagship” equipment.
Today, two lines of guillotines are available, focused on different kinds of materials and cuts necessary to meet customer’s specifications. According to the company, a significant feature is the level of customization — with virtually no two guillotines the same.
In 1996, FIMIC saw an opportunity to solve a problem in melt technology and further support the needs of not only its guillotine customers, but also the growing demand from plastics recyclers for an automatic filtration system. Melt filtration technologies available at the time were
improved with FIMIC’s development of the first FIMIC backflush filter.
A year later, FIMIC’s “scraping” system was added to further advance melt filtration technology.
With these innovations, FIMIC started to make history in the plastics recycling industry and became known as a specialist in automatic self-cleaning melt filters with an eye toward simplicity, optimization, flexibility, and performance.
FIMIC currently supplies five different types of filtration with five filter models. This offering provides a range of technology for the diverse needs of the industry.
According to the company, the RAS scraping filter system is known for its flexibility and strength. Using two blades, it can scrape very highly contaminated polymer flows and reprocess both, post-industrial and post-consumer materials with an adjustable discharge valve system.
The amount of waste produced by the melt filter can be adjusted through a special FIMIC valve, automatically opened when necessary, according to the level of melt contamination. As a result, the waste flow is proportional to the amount of contamination; in the event of a particularly clean melt, the valve will stay shut, and discharge just the little amount of waste filtered.
Following the development of the RAS filter, the ERA filter was introduced to address the needs of double filtration applications, conserving investment and consumption by performing the double filtration step in a single machine with two consecutive filtration chambers.
The RAS+REF melt filter that distinguishes FIMIC technology in the recycling field offers enhanced functionality with a backflush mode, and can operate in two different ways — in backflush mode or scraping mode. This provides clients who wish to process materials with mesh filters with more options.
The addition of the TEN model
Above: FIMIC guillotines feature a high level of customization.
Right: More than 500 RAS melt filter units are installed around the globe.
melt filter, which features the innovation of the first automatic screen changer allows, continuous filtration on woven mesh, eliminating material build-up and reduction of output with the additional option of adjusting the mesh output to ensure consistency and quality. The TEN doesn’t need the constant supervision of the operator simplifying the process.
In response to the considerable amount of material to be recycled today, and the demand for high-quality end products, FIMIC also designed a unique melt filter, representing the culmination of its technology and the expertise that made the company filtration specialists.
The GEM is a twin melt filter with an unmatched filtering surface that utilizes just two parallel filtering screens.
The GEM is proven as a leading technology in today’s market that is ideal for high-throughput recycling line applications, according to FIMIC.
FIMIC’s focus on designing and manufacturing self-cleaning, automatic melt filters that improve production line efficiency and output quality has been center stage for the company’s positioning in the marketplace.
FIMIC’s melt filters feature quick operation, with screen changes com-
FIMICfilters don’t require operator intervention, optimizing workflow while maintaining a high-quality product.
pleted by a single operator in less than 30 minutes. This efficiency minimizes production down time and can optimize workflow.
Pumping plastic materials in the recycling process can be a maintenance challenge for processors. Standard gear pumps are sensitive machines that can be easily damaged by contamination and demand significant maintenance and periodic gear replacement.
In addressing these issues, FIMIC developed the SPA screw pump — a pump that doesn’t need gear changes, operates at lower management costs and is not as sensitive to contaminated material.
According to the company, the SPA screw pump also can be used both before and after the filter and is appropriate for double filtration needs.
FIMIC says the SPA pump has a strong operating speed, is easy to operate, demands little maintenance and has a long service life.
Despite its long history focused on plastic recycling, FIMIC understands
the huge importance of recycling in the textile marketplace, as well as the wide variety of possible textile applications for its technologies.
In the current plastic/textile recycling environment, the focus is on two main applications — polyester (PET) fibers, polypropylene (PP) fibers and tapes. These very challenging applications require highquality, reliable technologies at every step of the way.
According to FIMIC, the PET fiber manufacturing market is facing serious market issues, one of them being the high prices of hot-washed PET flakes, now destined for higher-end applications like food contact thermoforming or bottling.
For this reason, fibers producers cannot use solely PET flakes as a raw material, but also need to use lowergrade PET waste such as lumps and waste fibers themselves. PET lumps can be highly contaminated which cannot logically be washed away in a washing line.
That’s where FIMIC’s filtration technology can help the most — to act as a pre-filter to remove the majority of contaminates and prepare a well-filtered melt to the following steps of the processing line.
With PP textiles, an extremely interesting application is in PP woven bags, or flexible intermediate bulk containers (FiBC), whose woven tapes are made of recycled polypropylene (rPP).
This is a very demanding application, especially starting from postconsumer PP woven bags, that often are heavily contaminated and need specialized machinery from experienced suppliers to complete the process.
FIMIC can contribute here with two technologies to improve the efficiency of such process
The guillotine — at the very beginning of the line — can be used to pre-cut the bales of PP wovenbags and prepare them to be fed to the subsequent washing steps.
Secondly, FIMIC’s Melt Filtration technology — single or double — may be used to remove many contaminants from the melt stream, hence helping to obtain a high-quality, unstressed polymer, and very well filtered melt that can be pelletized to be reused into rPP tapes production.
With a rich history serving recyclers needs for innovative solutions, FIMIC finds itself deeply ensconced in an industry of increasing demand. From humble beginnings focused on assisting in processing waste — the industry is no longer discarding waste but transforming it in a circular product environment. FIMIC has proven to be an effective partner in various stages of the recycling process, and its portfolio of equipment is recognized for its reliability and in its word “unbreakable.”
With the growing interest in recycled plastics and a need to process highly contaminated plastic waste, FIMIC technology provides solutions that eliminate impurities and lead to efficiently processed, high quality recycled products. As recycling continues to reman top of mind, FIMIC’s ability to contribute look more constructive than ever. TW
TW Special Report
Key components of this effort include addressing packaging and emissions, ensuring material health, minimizing environmental impact, and upholding social responsibility standards.
Sustainable Upholstered Furniture:
Sustainable Upholstered Furniture:
But for Nicola Coropulis, CEO of Poltrona Frau, an Italy-based company focused on providing global living solutions in a sustainable way for international customers: “Sustainability also means durability. The products are handcrafted to last generations, and we offer a dedicated service team to restore and reupholster items, with collection and delivery services available worldwide.”
ustainability has become a critical focus across industries, especially in home furnishings. According to the Sustainable Furnishings Council, sustainability in this sector refers to the design, production, sale, and use of furniture in ways that aim to minimize negative environmental, health, and social impacts. This approach prioritizes the long-term well-being of the planet and its inhabitants over short-term gains, integrating principles that promote ecological responsibility throughout a product’s entire life cycle.
But incorporating sustainability in upholstery or furniture design is not a new approach, at least not in the minds of some designers and manufacturers. In 1976, German designer Dieter Rams introduced his principles of good design, which included “Good design is long-lasting” and “Good design is environmentally friendly.”
A survey by the Center for Industrial Studies (CSIL) found 45 percent of its manufacturer respondents cited “environmental sustainability” as a top priority in all areas of their business strategies. 1 According to a recent Furniture Today survey, the furniture industry gave itself an average of a “C” grade on its sustainability efforts. Many noted the industry’s efforts but found the overall momentum lacking. Despite all this, 77 per-
cent of manufacturers believed sustainability should be a priority.2
“The meaning of sustainability is not only the certifications or sustainable products, it goes beyond. It needs to include also the business environment and the social levels, connecting everything to one place. And then we can call it a sustainable business,” explained Ovidijus Jalonskis, CEO Vilmers, a Scandinavian furniture company that is setting new standards for sustainability and customer-centric experiences.
But how can this be achieved? “By moving forward, upholstered furniture might be best served by defining sustainability as in this way: by connecting the manufacturing process from end to end and resulting in a sustainable business model,” Jalonskis shared. “Balancing the social, environmental, and economic aspects of sustainability in the upholstered furniture industry is indeed challenging, however a circular approach that emphasizes material recovery, longevity, and the responsible management of resources throughout a product’s life cycle can and will make a difference.”
Sustainability in the upholstered furniture sector is driven by a focus on reducing environmental and social impacts across the product life cycle.
Central to sustainable home furnishings is the promotion of ecofriendly manufacturing practices and sourcing. Some 36 percent of CSIL survey1 respondents chose “production process” as a key focus area for improving sustainability, and this can be achieved by adopting different manufacturing practices.
Reducing
On-demand manufacturing allows companies to eliminate overproduction because they only produce what’s needed and don’t have excess material or product inventory. Additionally, the need for shipping and storing components and raw materials in bulk is eliminated, further reducing a company’s environmental footprint. On-demand manufacturing is a more sustainable option, and it offers furniture makers the ability to adapt to market fluctuations and improve customization.
For instance, Poltrona Frau combines sustainability and customization in various ways. Its products are made to order and fully customizable, offering consumers an extensive selection of materials — including various types of sustainable materials and leather — Pelle Frau Impact Less, FSC-certified wood, or fabric, for example —and a choice of more than 100 colors for each individual product. Thanks to technology, customers can view their personalized product through the configurator available on the website.
Indoor air quality is becoming increasingly regulated, and sustainable products must be created using using non-toxic, safe materials
Reducing Waste —Highly precise, minimal buffer cutting and automated marker making ensure that manufacturers limit both waste and cost per cut part. The use of technology enables manufacturers to optimize nesting with minimal buffer, amounting to 3 percent in material savings that represents 15 percent of reduction waste. In terms of reducing waste, this applies not only to the manufacturing process but also to the shipping by using recyclable materials or cutting back on the amount used in packing and, ultimately, costing furniture businesses less.
Jalonskis cites his company’s replacement of cardboard and plastic packages with 100-percent recycled packaging materials, improving the customers’ experience, and reducing the company’s additional tax burden. “In the end, we even saved money,” he said. “You can find that sustainability can help you to improve your business, and the customers don’t need to pay extra for that.”
Reducing Energy —Using renewable energy sources and optimizing manufacturing processes are efficient ways to reduce overall energy consumption. Adopting new and upgraded cutting solutions that have been eco-designed is vital. Energy consumption of the cutting equipment can be reduced 30 to 40 percent by making these investments. For instance, more efficient cutting machines with higher production capacity allow companies to produce more cut pieces within shorter periods, reducing the carbon dioxide emissions rate for each one.
One of the most critical concerns in upholstered furniture is the reduction of harmful emissions, particularly volatile organic compounds (VOCs). The healthiest upholstered furniture doesn’t add chemical flame retardants or stain-guard fabric coatings on its fabrics and should use natural latex or low-VOC certified foam in the cushions. Formaldehyde, commonly found in adhesives and particleboard, is a known irritant and carcinogen. Over the past 20 to 30 years, there has been a significant push towards limiting its use in furniture.
Historically, emissions regulations were minimal, with manufacturers rarely required to meet strict standards. However, with growing awareness of indoor air quality’s impact on health, regulatory bodies have implemented stricter guidelines. Today, compliance with standards is a crucial indicator of a product’s commitment to minimizing harmful emissions. Industry practices now include the use of low-emission adhesives and treatments.
The material health of upholstered furniture is another core component of sustainability. This focuses on using non-toxic, safe materials throughout the product’s construction. Regulatory frameworks, such as California’s Proposition 65 (Prop 65), have been influential in shaping industry practices by requiring manufacturers to disclose harmful chemicals in their products. A growing focus is on eliminating per- and polyfluoroalkyl sub-
stances (PFAS), often used for stain resistance. These “forever chemicals” are persistent in the environment and pose health risks. As a result, many manufacturers are now turning to non-toxic, water-based treatments and exploring safer, innovative materials like organic cotton, wool, and natural latex to meet health and safety standards without compromising product performance. Examples of non-PFAS coatings include coatings made from elements like silicon, oxygen, carbon, and hydrogen.
The environmental impact of furniture manufacturing extends beyond emissions and toxic chemicals. It significantly affects natural resources like water and contributes to climate change through deforestation and carbon emissions. In Europe, the EU Regulation against deforestation and forest degradation has impacted producers, who must ensure that the materials used do not come from deforested land. The industry has made strides in sourcing sustainable wood, focusing on certified options like to ensure practices that protect ecosystems and promote legal harvesting.
The concept of social responsibility in upholstered furniture is crucial, given the global nature of the supply chain. Around 40 to 50 percent of upholstered furniture is sourced from countries like China and Vietnam, where labor standards can be less stringent. This raises concerns about worker safety, fair wages, and ethical labor practices.
Brands play a critical role in verifying labor conditions, particularly in regions where local regulations may not adequately protect workers. In the United States, the Uyghur Forced Labor Prevention Act bans imports of Chinese products made using Uyghurs. Leading companies are increasingly implementing social compliance audits and working with third-party certifiers to ensure their suppliers meet ethical standards.
While voluntary efforts from industry leaders drive some progress, there is a growing call for regulatory frameworks to enforce minimum standards globally. Voluntary initiatives —such as adhering to the Fair Labor Association or the Ethical Trading Initiative — promote fair treatment of workers throughout the supply chain.
As global awareness of environmental impacts rises, companies worldwide are exploring new ways to reduce their ecological footprint. However, sustainability practices in upholstery manufacturing vary significantly across different regions, influenced by local regulations, consumer preferences, and economic factors.
Global supply chains in upholstery manufacturing have undergone significant shifts driven by demographic changes, geopolitical tensions, and disruptions from the COVID-19 pandemic. The demographic trend of aging populations in Europe and the United States has led to increased demand for durable, high-quality furniture that prioritizes comfort and longevity. This has driven manufacturers to focus on sustainable, long-lasting materials that cater to these preferences.
Geopolitical factors, such as trade wars and increasing tariffs, have prompted companies to reassess their reliance on Asian manufacturing hubs. Many businesses are exploring reshoring—moving production closer to their primary markets—to reduce dependence on international suppliers and mitigate risks associated with long supply chains. This shift has also been influenced by the need for better control over environmental standards and compliance with local sustainability regulations.
The pandemic exposed vulnerabilities in global supply chains, prompting manufacturers to adopt more resilient and sustainable practices. This transition has also highlighted the importance of digital technologies, such as AI and digital twin technology, in optimizing supply chains
for greater efficiency and sustainability through transparency.
The upholstered furniture industry faces increasing pressure to adopt sustainable practices. However, achieving sustainability in this sector has its challenges.
Upholstered furniture is notoriously difficult to recycle due to its composite materials. Typically made of a mix of wood, metal, foam, fabric, and adhesives, separating these components for recycling is labor intensive and costly. Foam poses a significant issue because it is often treated with fire retardants and chemicals, making it unsuitable for simple reuse.
Consequently, many pieces of upholstered furniture end up in landfills, highlighting the industry’s struggle with developing effective recycling solutions. The United States Environmental Protection Agency estimates that 9 million tons of furniture are thrown away every year. 3 And in Europe, 5 million tons of furniture is discarded every year, the majority of which is destined for either landfills or incineration.4
Costs Of Sustainability — Incorporating sustainable practices into the production of upholstered furniture can be expensive. Sourcing ecofriendly materials such as organic fabrics, responsibly harvested wood, and recyclable metal components significantly increases costs. For many manufacturers, especially smaller companies, the investment required to overhaul supply chains, implement sustainable practices, and meet certification standards can be prohibitive. As a result, these costs are often passed on to consumers, making sustainably produced furniture less accessible and competitive compared to traditional offerings.
Adopting sustainable manufacturing processes requires significant investment in technology and equipment. Shifting towards greener practices, such as using water-based adhesives or energy-efficient machinery, involves high up-front costs and ongoing maintenance expenses.
Uneven Playing Field —Sustainability standards and regulations vary widely across regions and markets, creating an uneven playing field for manufacturers. Companies operating in countries with strict environmental regulations face higher compliance costs, while those in regions with less stringent policies may continue using cheaper, nonsustainable materials.
This disparity makes it difficult for responsible manufacturers to compete on price, particularly in a global market where cost is a significant factor for consumers. But there is hope. A recent U.S. study shows that 76 percent of Americans are willing to pay a higher price tag for eco-friendly furniture.5
Labor Shortages — The furniture industry is grappling with labor shortages, which are exacerbated by the specialized skills needed for sustainable manufacturing. Skilled artisans capable of working with eco-friendly materials and techniques are in short supply. Steve
According to statista.com, 76-percent of Americans are willing to pay a higher price tag for eco-friendly furniture.
Kooy, Health & Sustainability director for BIFMA, finds this to be an issue of concerns for manufacturers.
This issue is particularly concerning for manufacturers based in rural areas, where the access to skilled workers is more limited. Additionally, the existing skilled labor is aging out and efforts to recruit and train new generations to replace this expertise have been unsuccessful. This has led to increased competition for talent and rising labor costs.
Supply Chain Disruptions And Near-Shoring —Global supply chain disruptions have prompted many furniture manufacturers to bring manufacturing back closer to home markets. It can reduce transportation delays but also increase labor costs, exacerbating the overall economic burden even as it reduces dependency on foreign suppliers. While nearshoring or reshoring can lead to improved quality control and shorter lead times, it also introduces new challenges, such as the need to rebuild domestic supply chains that support sustainable material sourcing. Finding local suppliers that meet high sustainability standards can be difficult and costly, further complicating the industry’s transition to greener practices.
Consumer Trends And Sustainability Marketing —Consumer demand for sustainable products is growing, but there is still a gap between interest and actual purchas-
ing behavior, mainly due to higher prices and limited availability.
Consumers care about sustainability, but they don’t want to pay anything extra for sustainability. They have doubts about the quality,” explained Kooy. For some, the real question is should the responsibility for promoting sustainable upholstery lie with the consumers or the manufacturers?
Furthermore, consumers may struggle to discern genuinely sustainable products from those that are merely marketed as such, due to a lack of standardized certification. This creates challenges for brands attempting to build trust and differentiate their offerings in an increasingly crowded market focused on sustainability claims.
There also is a generational shift in consumer habits, particularly among younger generations, suggests that materialism may be on the decline, affecting demand for new furniture.
Adopting sustainable practices in the upholstered furniture industry is no longer optional; it is essential for long-term business success and environmental responsibility. Technological innovations will continue to play a crucial role in enhancing sustainability and customization for upholstery manufacturers, however embracing a sustainable design philosophy is also vital.
“This means emphasizing longevity and timeless aesthetics to reduce the need for frequent replacements. Thoughtful design can lead to products that remain relevant and functional over time, minimizing waste,” Coropulis said.
There are key strategies that companies can implement to enhance sustainability including:
•Education and consumer awareness;
•Regulations and recognized sustainability certifications;
•Better use of Industry 4.0 technologies;
•Transportation, logistics and consumption patterns; and
•Emerging business models.
The future of sustainability in upholstery manufacturing will likely be driven by a combination of regulatory shifts, industry 4.0 technologies, innovations, and changing consumer preferences. As companies continue to adapt and evolve, those prioritizing sustainable practices are expected to gain a competitive edge, build stronger customer loyalty, and contribute positively to the environment. In summary, while the journey toward full sustainability in upholstered furniture is challenging, it is also filled with immense potential. The transition may be gradual, but the collective efforts of manufacturers, policymakers, and consumers hold the promise of a more sustainable future for the global furniture market. TW
References:
1CSIL survey among upholstered producers, 2021 2www.furnituretoday.com 3www.architecturaldigest.com 4eeb.org 5www1.eere.energy.gov
Editor’s note: This article was adapted from a white paper exploring the future of sustainability in the furniture industry published by the Lectra Observatory, a research initiative launched by Francebased Lectra. To read the full version of the white paper, which includes more on global perspectives and sustainablity strategies , please visit TextileWorld .com.
Finland-based Spinnova Oyj has joined the International Textile Manufacturers Federation (ITMF),Zurich,as a corporate member.
Lee® — the Greensboro, N.C.-based denim brand owned by Kontoor Brands —recently introduced the Lee X product platform.Designs were created with comfort and performance in mind.
Switzerland-based Archroma has joined the BioCircular Materials Alliance.Conceived by biomaterials company Spiber Inc.,the alliance encourages the wider adoption of biobased materials and chemical treatments.
Milliken & Company, Spartanburg,S.C.,has earned a gold rating on its 2024 EcoVadis assessment — a rating of sustainability. The gold rating puts Milliken & Company in the top 5 percent of all organizations rated and is the third consecutive year the company has achieved a gold rating from EcoVadis.
Burlington,N.C.-based Sunbrella has expanded its Sunbrella Plus® collection to include 17 color options.
New York City-based design house Schumacher has opened a new 4,000square-foot showroom in the New York Design Center.The space offers a curated selection of the brand’s portfolio including textured and solid fabrics, trims and wallpapers.
Montreal-based Gildan Activewear Inc. was included in the Dow Jones Sustainability™ North America Index for the 12th consecutive year. The company also donated $200,000 worth of American Apparel® and Gildan® garments to FireAid,a concert benefiting those affected by the recent wildfires in Los Angeles.
Designtex,New York City,reports the company is now 100-percent per- and polyfluoroalkyl substances (PFAS)-free having eliminated the
forever chemical in all of its products and inventory.
YKK Corp.,Tokyo, recently announced that the Science Based Targets initiative (SBTi) has validated that the company’s long-term goal of reaching net-zero greenhouse gas emissions by 2050 meets the SBTi Net-Zero Standard in the Textile,Apparel,Footwear and Luxury Goods category.
Office furniture manufacturer MillerKnoll,Zeeland, Mich.,announced it has eliminated the use of PFAS in its North American portfolio of products.
Denver-based workwear company Truewerk recently joined the Americas Apparel
Producers’ Network (AAPN),Atlanta.
New York City-based Carnegie has introduced Siltech Plus,a highperformance,biobased polyurethane coated upholstery product made using corn starch.The fabric,backed with a 100-percent post-consumer recycled polyester,comes with a 10-year warranty.
England-based Think Group recently won a National Flooring Innovation Award — which recognize businesses, products and services that are new and innovative in the United Kingdom flooring industry.Think Group’s SpringBond® Eco-Step 8mm,its latest introduction,was key in its win.
Germany-based A. Monforts Textilmaschinen GmbH & Co.KG reports two Monforts Montex tenter lines at its Advanced Technology Center (ATC) are now equipped with Texcoat™ G4 Digital Spraying Units from St.Louis-based Baldwin Technology Co. The lines are ready for customer trials. TW
Toronto-based Canada Goose recently named Judit Bankus senior vice president of Merchandising.
Laura Beachy has joined Italy-based Thermore as vice president of Global Marketing and Communications.
Cotton Incorporated, Cary, N.C., recently named William Kimbrell president and CEO.
Eric Haagen was named sales representative with responsibility for the North American market for testing solutions company emtec Electronic GmbH, Germany.
Applied mathematician and color scientist
John Seymour has joined Germanybased ColorLogic — a software brand and global provider of color management solutions — as the Color Science lead.
Craig Leffew has joined Piana Sleep —a division of Piana Technology, Cartersville, Ga. —as director of sales. He reports to Piana Sleep’s Vice President of Business Development Chris Henning
Haskell W. Beckham was honored with the 2024 Olney Medal from the American Association of Textile Chemists and Colorists (AATCC), Durham, N.C. Beckham is vice president of Innovation at Columbia Sportswear, Portland, Ore., and was recognized for his significant contributions to textile sciences.
Germanybased Lindauer DORNIER GmbH has appointed Dr. Holger Niemeier chief technology officer. He is responsible for research and development, production and digitalization with a focus on artificial intelligence.
Seattle-based outdoor clothing and accessories brand Filson, a Bedrock Manufacturing Co., has named Tim Bantle president.
Germany-based specialty chemical company Rudolf GmbH has appointed Marcos Furrer CEO, Dr. Gunther Duschek chief technology and operations officer, and Dr. Oliver Kusterle chief sustainability officer. In addition, Dr. Wolfgang A. Schumann was named chairman of the Board of Directors.
Emmanuelle Gmür was recently named chief human resources officer of the Rieter Group, Switzerland, as well as a member of the group’s executive committee. She succeeds Tom Ban who has left the company.
Moss Inc., Franklin Park, Ill., has promoted Elissa Decker to vice president, Global Procurement and Textile Development.
Sweden-based Circulose recently named Jonatan Janmark CEO. The company also appointed Helena Helmersson chairman of the board. In addition, Sara Diez Jauregui, with experience with leading fashion and apparel brands, and Kalyan Madabhushi, an Aditya Birla Group associate, have joined the board.
Helsinki-based Suominen Corp. has appointed Darryl Fournier COO. He reports to President and CEO Tommi Björnman. In addition, Mark Ushpol was named executive vice president, Americas business area, and member of Suominen’s executive management team.
Textile engineer Cathy Shao has joined eVent® Fabrics, Kansas City, Mo., as Innovation director.
Courtney Harold has joined Green Theme Technologies, Albuquerque, N.M., as head of marketing.
Cincinnati-based Michelman has named Wilma Beaty chief human resources officer. Beaty will lead the company’s global human resources operations, driving people engagement, organizational design and culture initiatives.
Apex Mills Corp. Inc., Inwood, N.Y., named Chris Rojas assistant plant manager for the company’s Aridyne facility in Graham, N.C. In other recent appointments, Marth Miller Hopkins has joined the Apex Mills’ Business Development team. In her new role, Miller Hopkins will drive growth of warp and circular knits, stretch and 3D spacer fabrics, and enhanced finishes and treatments for the activewear, shapewear, industrial and military markets, among other applications.
Dr. Eric D. Evans has joined the board at Advanced Functional Fabrics of America (AFFOA), Cambridge, Mass. He is director emeritus and fellow at the MIT Lincoln Laboratory and MIT professor of the practice. Evans also is the chair of the Defense Science board. TW
8-10 :EMITEX 2025,La Rual Trade Center,Buenos Aires,Argentina. Visit emitex.ar.messefrankfurt.com
8-11 :Americas Apparel Producers’ Network (AAPN) Carolina Mill Tour. Visit aapnetwork.net.
9 :Synthetic Yarn & Fabric Association (SYFA) Annual GolfTournament, Rocky River Golf Course,Concord,N.C. Visit thesyfa.org.
10-11 :SYFA 2025 Spring Conference,Sheraton Charlotte Airport Hotel,Charlotte,N.C. Visit thesyfa.org.
14-16 :Functional Fabric Fair Powered By Performance Days,Oregon Convention Center,Portland,Ore. Visit functionalfabricfair.com.
29-May 1 :IDEA® 2025,organized by the Association of the Nonwoven Fabrics Industry (INDA),Miami Beach Convention Center,Miami Beach,Fla. Visit ideashow.org.
29-May 1 :INDA’s FiltXPO™, Miami Beach Convention Center, Miami Beach,Fla.Visit filtxpo.com.
6-8 :Techtextil North America 2025, Georgia World Congress Center,
Atlanta.Visit techtextil-northamerica.us.messefrankfurt.com.
6-8 :Texprocess Americas 2025, Georgia World Congress Center, Atlanta.Visit texprocess-americas.us. messefrankfurt.com.
6-9 :FESPA Global Print Expo,Messe Berlin, Berlin.Visit fespaglobalprintexpo.com.
12-14 :AAPN’s 2025 pro:Americas Annual Conference,Marriott Harbor Beach,Fort Lauderdale,Fla. Visit aapnetwork.net.
19-22 :SAMPE 2025,Indiana Convention Center,Indianapolis. Visit 365.sampe.org/events.
By Rachael S. Davis, Executive Editor
For more information, visit suedwebs.com/ innovation/ elevatinghome-textiles/ Go online to TextileWorld.com for archived Quality Fabric articles.
Suedwolle Group recently worked with Lenzing and Culp Home Fashions to create a new luxury mattress ticking fabric.
CComing together and contributing expertise towards a shared goal, Germanybased worsted yarn spinner Suedwolle Group, Austria-based cellulosic fiber producer Lenzing AG and Stokesdale, N.C.based Culp Home Fashions (CHF) recently explored new ways to merge functionality and visual appeal in home textiles.
This cross-industry collaboration focused on improving sleep comfort while imparting a fresh design and color scheme to mattress fabrics.
The project began with Suedwolle Group’s Oakport yarn — a 50-percent wool/ 50-percent TENCEL™ Lyocell blend in a 36/1 Nm yarn count. The yarn is available in Suedwolle Group’s stock program. According to Suedwolle Group, this fiber blend offers practical benefits for home textiles. Wool has natural temperatureregulating and moisture-wicking properties, which is enhanced by the softness and moisture control of Lenzing’s TENCEL Lyocell. The blend also offers breathability and durability, as well as odor management. Originally established in 1976 as Culp Ticking, CHF is Culp Inc.’s mattress fabric division. For the collaboration, CHF’s design team set to create a fabric that differed from the blue and gray color combinations often used for mattress fabrics. They selected a warm and neutral color palette and went with a vintage-inspired patchwork pattern featuring angular shapes. The fabrics are available exclusively through CHF.
“Lenzing and Suedwolle Group recognized a void for a natural mattress ticking face that brought together the benefits of merino wool and TENCEL lyocell fibers,” reported Walter Bridgham, senior business development
manager, Lenzing Fibers, TENCEL brand, Americas Home Segment. “Culp was identified and approached as a partner that has a keen sense of design and outstanding production capabilities, and they brought this luxury mattress ticking fabric to reality.”
“The best part of the project was having the opportunity to work with industry leading fiber and yarn suppliers, said CHF President Tommy Bruno. Collaborating with industryleading fiber and yarn suppliers on this project has helped create an innovative and foundational fabric that will contribute to future product development. This collaboration allowed us to create a fabric that will ultimately stimulate conversation and inspire future product development with our customers.”
The fabrics made their debut at the recent Heimtextil trade show in Germany.
“Lenzing had the opportunity to show this fabric at the January Heimtextil fair in Frankfurt where we received very positive feedback on the innovative fabric,” Bridgham said. “Since Heimtextil, Lenzing has received interest to bring the fabric to market in the mattress ticking area.”
Reflecting on the collaboration, the companies agreed that a core color palette for the yarn presents future opportunities for elevated design, premium tiered options and enhanced creative possibilities.
“I am really excited on how the collaboration is being perceived after launch!” added Lukas Vogl, marketing specialist, Suedwolle Group.
“I think the real benefit that we have put forth for the collaboration between Suedwolle Group, Lenzing, and Culp is the exclusive marketing support for this innovation. We want to make sure that we make this development and the relationship very special.” TW
website / magazine / e-newsletter
Subscribe to Textile World for complete coverage of the U.S. and global textile manufacturing industry — the latest technologies, applications, regulations and trends.
Now you can receive your Textile World magazine anywhere you go.
Print advertisers receive additional reach and linking with free inclusion in Digital Editions.
read / share / engage
Stäubli TF series weaving machines are the answer to the continuously expanding areas of application for technical fabrics. Selectable configuration and flexible design give mills the adaptability they need to meet individual and changing requirements.
Do you produce reinforcing fabrics for lightweight applications, heavy industrial textiles, fabrics with carbon fibres, ceramic weaves for aircraft – or something brand new? With Stäubli TF you have an extremely flexible, technologically advanced production system.
www.staubli.com