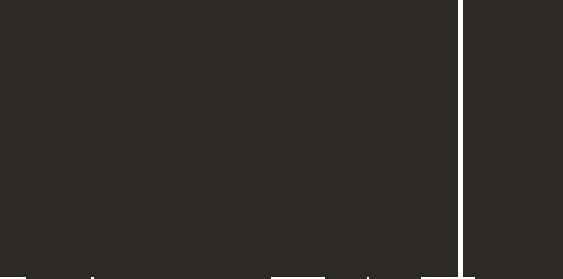
11 minute read
Application of Coir Fibre Reinforced Green Composite
from AUGUST 2020
Mr. DEBJIT BISWAS
INTERN AT TEXTILE VALUE CHAIN
Advertisement
ABSTRACT
With the rise in pollution and degradation of the environment researches are more focusing on the use of natural fibers such as jute, coir, sisal, etc. This has resulted in creating an awareness of using natural fiber reinforced biodegradable composites to replace the traditional fiber reinforced plastic composites. The objective of the paper is to develop a led incorporated biodegradable composite to add a product range in the field of home accessories. Coir fiber is selected as the reinforce material as it is ecological, non-toxic and biodegradable. Other than that Coir fibers have properties that help to improve strength, stiffness and make the product lightweight. There are many natural cellulose fibers but coir is used for being coarse, thick and is the most resistant to other commercial fiber. It is extracted from the outer shell of the coconut. Coir fiber is rich in lignin, making it even suitable for the products where slow degradability is required. The paper also briefs about composites, natural fiber different properties of coir fiber, polymer matrices and totally renewable composites.
According to Kelly[1] composites are not regarded as a simple combination of two materials. Instead it is a unique combination of its own distinctive properties such as resistance to heat and other desirable qualities. The definition by Van Suchetclan [2] says that composites are homogeneous material as any portion of it will carry the same property. It can also be considered as heterogeneous material with two or more solid phases in contact on a microscopic scale.The history says that the use of composite has increased in a varied field where the strength and stiffness properties are hugely required. Over the era, the use of composite has rapidly increased because of its quality of high structural performance at low cost and compliance with the environment. The material majorly used to make composites were glass fiber, carbon fiber and aramid fiber reinforced with epoxy and unsaturated polyester for high mechanical strength. However, the major issue that arises is the non-biodegradability of these materials. With the rise of environmental consciousness and demand of legislative authority for their recycling, it becomes ethically though to continue using these materials. The Composites consists of matrices which function to disperse the fibers, it’s orientation and spacing. It avoids catastrophic propagation of cracks by transferring the obtained stress by the load on the composite, to the fibers by adhesion or friction across the fiber-matrix interface.[3] They can be further classified on the basis of matrix such as Metal matrix composites , Ceramics matrix composites and Polymer matrix composites. The synthetic polymer composites are petroleum based products. With growing awareness to reduce the carbon footprint and to preserve the petrochemical resources, alternatives are being searched by the researchers to replace the petroleum based composites [4]. The synthetic polymers produce a huge plastic waste which is non-biodegradable. A lot of energy in the form of
heat and pressure is required to fabricate the composites. The Limitation of the reserves of petroleum is the major problem for synthetic polymers [5]. Due to these rising issues researchers are looking forward to polymers synthesised by sustainable and eco friendly raw materials. This led to use of natural fiber along with polymer matrices. According to recent research, the energy required in production of natural fibres is more than half of the energy needed for the synthesis of synthetic fibres. Natural fibres are light in weight, , non-irritating, non-abrasive non-toxic, combustible, and biodegradable[6]. Natural fibers are classified on the basis of their content i.e cellulose, protein and mineral[7]. The other fibres used are Coir (Coconut), Bamboo , Pineapple , Ramie Advantages of green composites are less expensive, light weight, flexible, renewable resource, good sound insulator and also helps in thermal recycling. The cellulose are further classified on the basis of their origin i.e leaf, bast, seed, stalk and grass. The Fibres from seeds are single cellular and are referred as fibers while those of the bast, stem and leaf are organised as bundles thus, called fibre bundles [8].Natural fibres mainly made compose of cellulose, lignin and hemicellulose. The Cellulose in the fiber are responsible for the inherent strength and stability of the natural fibre, while hemicellulose gives structure of the natural fibre. Thus the natural fibers contribute to green composites. Ecological concerns have resulted in recyclability and environmental safety. Green composites are being introduced due to its biodegradability, they are decomposed by the action of microorganisms when dumped. When decomposed they get converted into H2O and CO2, which are readily absorbed by the plant systems. Green composites are classified on the basis of the type of reinforcement and polymer materials. Totally renewable composites are those in which the matrix and reinforce material are composed of renewable resources. Partly renewable composites are those in which the matrix is obtained from renewable resources and reinforced material is synthetic. Partly renewable composites are those which are composed of synthetic matrix and natural biopolymers as reinforced material [9]. Coir Fiber
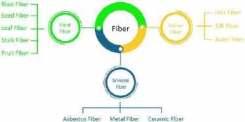
Natural fibers are broadly classified into three segments i.e Plant fiber, Animal fiber and Mineral fiber. The plant fiber is subdivided into blast, seed leaf stalk and fruit fiber. The animal fiber is subdivided into hair, silk and avian fiber. Similarly the mineral fiber is divided into asbestos, metal and ceramic fiber. The classification is explained in Fig. 1 Among the natural fibers, Coir is abundantly available in India, making a position of second largest in the world. It is extracted from the outer husk of coconut. The husk contains a corky tissue called firth along with water, fibres and soluble solids. Coir contains lignin which make it suitable in terms of durability. The chemical composition of coir is mentioned in Fig 2. Natural fibers consist of cellulose, hemicelluloses, lignin, pectin, water soluble substances and waxes. The composition differs from the obtained conditions and test methods. Cellulose are polysaccharide composed of D-glucopyranose units linked together by -(1-4)-glucosidic bonds. {10] Cellulose consists of a huge amount of hydroxyl group that gives the fiber hydrophilic properties.[11] Hemi cellulose has a lower molecular weight than cellulose. They are bonded to the fibrils of cellulose with hydrogen bond. It consists of many hydroxyl and acetyl groups due to its open structure, therefore they are semi soluble in water and hygroscopic[12] Lignis have the least water sorption than the other natural fiber component. They are aromatic, amorphous and polymers of phenyl propane units[11]. Due to the hydrophilic nature of the natural fibers they often result in weak interfacial properties of fiber and polymer. Thus the matrice reduce its potential as reinforce agent. Chemical modifications are done to activate the hydroxyl group and interlock it with the matrix to enhance its properties. Such chemical coupling agents functions to react with the hydroxyl group and further react with the functional groups of the matrix.
The coir fiber has been used as reinforced material to make composites. Aireddy et al [13] researched on coir dust reinforced epoxy resin to test the abbersive properties. The result reveals under normal load the abrasion property increases with increase in the load and decrease with increase in coir dust concentration. S.mazan et al. [14] studied sound absorption panels. The research included the viability of coir fibre reinforced composites in it. The composites were composed of reinforced coir fiber and polyurethane as resin. To investigate the acoustic properties of the material, two microphone methods were used. The result showed excellent acoustic properties of the composites and proves the property of the coir fiber reinforced composites. Li et al. [15] worked on coconut fibres of length 20 and 40 mm which were untreated and alkalized respectively. Cementitious composites as reinforcement materials were used. Impactful results were achieved on adding a low percentage of coconut fibres along with the chemical agents in the cementitious matrix. Reis [16] researched on the mechanical characterization toughness of epoxy polymer reinforced with different natural fibres. The result proves that the coconut fibre reinforced polymer had higher fracture toughness and fracture energy than that of other fibres reinforced polymer concrete.
3. Material and methodology
After reaching on different parameters of coir fiber done by different researchers, a research gap was found that elaborates on amalgamation of Led lights with coir fiber reinforced polymer composite. The research aims to create a totally renewable composite restaurant tray. As there is a fusion of Led with the composite, the product fits for Restaurants having dim light arrangement The material used is Coir fiber due to its mechanical and chemical properties, resin made of derivatives of Cellulose, starch and lactic acid, a led stripe of 12 volts and a opaque acrylic sheet. There are many methods to create Green composites. For example filament winding, lay up methods, resin transfer moulding, injection moulding and autoclave bonding[17]. The method incorporated in this research is Lay up method/ hand lay up method. Initially a mould is created with metal. The dimension used for making the tray is 380 mm x 255 mm. A mould releasing agent is treated to the surface of the mould. Further the led stripe is added and the border of the composite and a thin gel coating is applied all over the surface of the mould. When the gels set, the first layer of resin or matrix material is applied. After that, the coir fiber or sheet is added on the top of the resin layer. Finally a thin layer of resin is equally added on the top of the coir fibers/ sheet layer. As shown in Fig 3. When the obtained composite becomes fully hardened, it is removed from the mould. A border of acrylic sheet is incorporated above the led, in the composite. The addition of acrylic aims to give an aesthetic look and visual impact when the light from led passes and scatters through the Acrylic sheet.
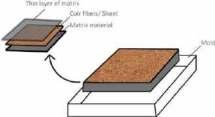
1. Final tray
Fig. 4 Design of the tray
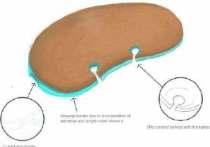
Future Scope and Conclusion
The present research has been done, with an objective to explore the properties and potential of the Coir fiber polymer composites. The research includes different reports of the use of Coir fibers, as reinforcements in the polymer matrix. It aims at providing knowledge to enhance further research in the area of coir reinforced composite. The result obtained has excellent strength and toughness of the composite . The motive was to replace glass fiber composites. Instead of it use the natural fiber composites with good mechanical properties. Currently, it can be said that one of the most important natural fibers is coir, due to its properties and abundance. The obtained coir reinforced polymer composites can have a wide area of application. The lignin content of the coir makes its application suitable in the areas where slow degradability is required. Thus, it
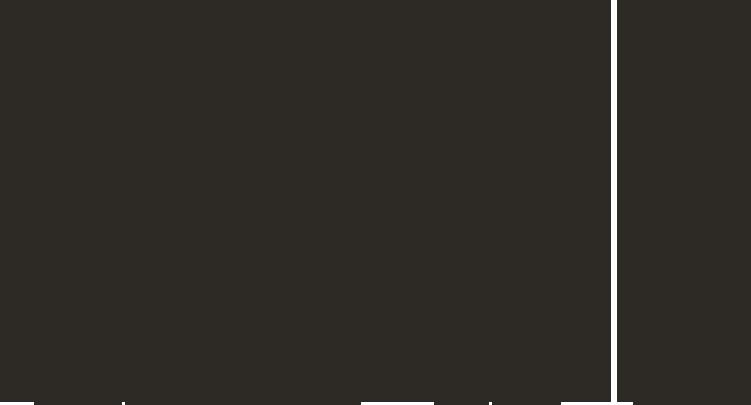
SUSTAINABLE FIBRE 41 can be concluded that the future of coir fiber com[2] Suchetclan Van; Philips Research Reports. 27 (1972) 28 posites are quite promising. [3] Mathews, F. L, Rawlings R .D, Engineering Composites 1 sI ed. Chapman and Hall, London, (1994) Future Scope and Conclusion [4] Julia Cigasova, Nadezda Stevulova, Alena Sicakova, Jozef Junak, Some Aspects of Lightweight Composites Durability, Chemical EnThe present research has been done, with an obgineering Transactions, vol 32,2013 2526 jective to explore the properties and potential of [5] Giuseppe Cristaldi, Alberta Latteri, Giuseppe Recca and Gianluca the Coir fiber polymer composites. The research Cicala Composites Based on Natural Fibre Fabrics, Woven Fabric includes different reports of the use of Coir fibers, Engineering, 2014 as reinforcements in the polymer matrix. It aims at [6] Olusegun David Samuel, Stephen Agbo, Timothy Adesoye Adekaproviding knowledge to enhance further research nye, Assessing Mechanical Properties of Natural Fibre Reinforced in the area of coir reinforced composite. The result Composites for Engineering Applications, Journal of Minerals and obtained has excellent strength and toughness of Materials Characterization and Engineering, 2012, 11, 780-784 the composite . The motive was to replace glass [7] Eustathios Petinakis, Long Yu, George Simon and Katherine Dean fiber composites. Instead of it use the natural fiber Natural Fibre Bio-Composites Incorporating Poly(Lactic Acid), Fiber composites with good mechanical properties. CurReinforced Polymers - The Technology Applied for Concrete Repair, rently, it can be said that one of the most impor2013 tant natural fibers is coir, due to its properties and [8] Mwaikambo, L. Y. REVIEW OF THE HISTORY, PROPERTIES AND APabundance. The obtained coir reinforced polymer PLICATION OF PLANT FIBRES, African Journal of Science and Techcomposites can have a wide area of application. nology (AJST),Science and Engineering Series Vol. 7, No. 2, pp. 120 The lignin content of the coir makes its application – 133 suitable in the areas where slow degradability is re[9] International Journal For Technological Research In Engineering quired. Thus, it can be concluded that the future of (IJTRE) Volume 2, Issue 7, March-2015 coir fiber composites are quite promising. [10] Rowell, R.M, Young, R.A, Rowell J.K, Paper and composites Reference from agro-based resources, CRC Lewis Publishers, Boca Ra[1] Kelly, A.,The nature of Composite Material, Sci. Amer. Mag. 217 (B) (1967) ton RL, (1997) 301-336 161 &KHTXHV''DUH)DYRXULQJ 7R,QQYRDWLYH0HGLD <HDU ,VVXH $QG <HDU ,VVXH ,QIRUPDWLRQ&RPSDQ\ <HDU ,VVXH 3D\DEOH$W0XPEDL ,VVXH <HDU 3/($6(127(:('2127*8$5$17((7+('(/,9(5<2) &23,(6%<1250$/%22.3267 1DPH &RQWDFW3HUVRQ $GGUHVV 3KRQH1R 0RELOH1R (PDLOΖG :HEVLWH | AUGUST2020