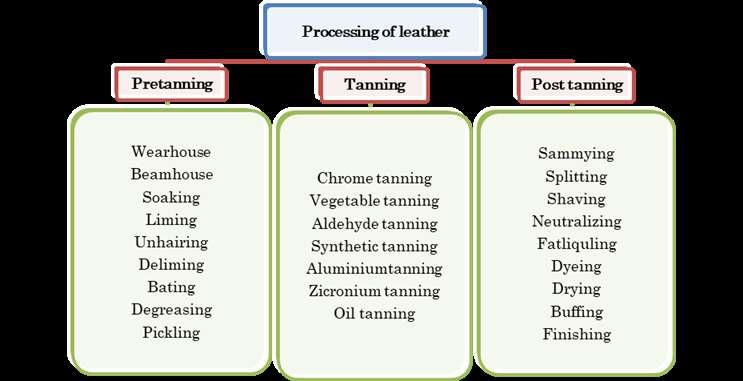
21 minute read
RECYCLING LEATHER by Ashwini Tarte and Dr. Suman D. Mundkur
RECYCLING LEATHER
ASHWINI TARTE DR. SUMAN D MUNDKUR
Advertisement
M.Tech Student
Visiting Faculty Department of Fibres and Textile Processing Technology, ICT Mumbai
Abstract
The leather industry is one of the leading industries in textiles. It produces large amounts of waste during the manufacturing process and after the use of leather fabric by consumers. This industry is one of the largest waste-producing industries. Almost 20% of worldwide waste from leather is generated in Asia. This can be very harmful to aquatic life. It occupies a large landfill space. The waste should be recycled to minimize the environmental impact. It produces solid waste and liquid waste during processing. There are a lot of studies done on leather recycling and reusing leather products. Some methods to recover energy from the heat and energy which is generated during leather processing. The restyling technique also helps reuse and reduce waste. Keywords: leather manufacturing, leather waste, leather recycling.
Introduction
Leather has been treated with chemicals to preserve and make it suitable for use as clothing, footwear, handbags, furniture, tools, and sports equipment. The consumption of leather products by humans is very commonly used. The primary raw material for any leather processing industry is derived from slaughterhouses and waste from the meat industry. This raw material is processed and converted into usable leather in tanneries. Hence, the tanning industry is considered as one of the primary leather processing units in the entire leather industry. The chemical treatment called tanning converts the otherwise perishable skin to a stable and non-decaying material. Tanning agents include vegetable tannins (from sources such as tree bark), mineral salts (such as chromium sulfate), and fish or animal oils. In this tanning process, maximum leather waste is generated; this waste is further used for generating heat and energy [1]. Process of modern leather Manufacting Leather production is a very lengthy process that involves several steps before tanning. The most important stages in converting the raw animal hide to leather are listed below [2][3]. The modern commercial leather-making process involves three basic phases:
Name of Chemical
Chromium sulphate
Chromium
Short chain chlorinated paraffin's (PBT)
Cobalt dichloride Use
Principal raw material used in the production of chrome tanning materials for the leather industry like Chrome-tanning salts
used for dyeing
Additive for the leather treatment (renders smoothness to leather), leather clothing and belts and as a leather oiling agent. Used in leather dyeing and finishing as well found in tanned leather Target organs
Blood, kidneys, heart, lungs, eyes and carcinogen
Kidney, CNS,
Liver, kidney, thyroid and carcinogen
Lungs, liver, kidney, heart, skin
Methyl isothiazolinone Biocide, microbiological protection Skin, eyes and carcinogen
Formaldehyde HCHO Heavy metals Arsenic Leather finishing Eyes, lungs and carcinogen
1. Preparation for tanning, 2. Tanning 3. Processing tanned leather [4]. No.1 lists down the different steps in the processing of leather.
Eco-friendly alternatives for the hazardous chemicals used in leather
processing
The consumer consciousness and strict regulations by worldwide authorities require leather products with the lowest possible risk for the environment. Instead of using chromium sulfate, we can use vegetable tannin like quebracho, chestnut, behra nuts in the tanning process, which gives a more stable leather and it is an eco-friendly method [6]. Nitrocellulose lacquer emulsions can be successfully replaced with castor oil, which maintains the typical lacquer emulsion properties like glossy touch, softness, and elasticity. Enzymes, amino acids, or oxazolidine can be used as an alternative in tanning processes. As an alternative for the solvent N-Methyl pyrrolidone high wear topcoat acrylics being free of solvents has been used. Formaldehyde in leather finishing is not only used as a crosslinker for cases in topcoats but also as a biocide. Finishing chemicals may contain formaldehyde even when no formaldehyde was used for the production, as many raw materials are preserved in a formaldehyde base. To overcome this problem use of formaldehyde scavengers can be adopted as in the case of some Wet End Chemicals Inorganic heavy metal pigments like lead chromate, cadmium sulfide and others can be replaced by organic pigments or pigments. We can use silver nanoparticles in the tanning process which improves the mechanical and physical properties. It can also be used as an antimicrobial and UV resistant application [5][7].
Waste management in the leather industry
Fig. No.2 below gives the volume of waste generated from the leather Industry. The largest amount of waste comes from the Asian Continent. The waste generated from the leather Industry from China alone contributes to 13% while, one-fourth of the global waste comes from the other Asian countries together.
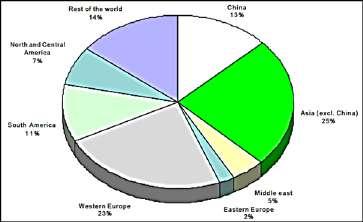
Two types of waste generated in the leather industry
1. Post-consumer waste: It is also called household waste and dirty waste. Any worn out, damaged, and out of fashion apparel and textile products, which are discarded and no longer in use by the wearer. They are sometimes given to charities but more typically are disposed of into the trash and end 2. Pre-consumer waste: is waste generated during the manufacturing process. Waste originates from all stages of leather making process, such as fine leather particles, residues from various chemical discharges, and reagents from different waste liquors (Effluent), comprising of large pieces of leather cuttings, trimmings, and gross shavings, fleshing residues, solid hair debris and remnants of paper bags. Out of 1000 kg of rawhide, nearly 850 kg is generated as solid wastes in leather processing. Only 150 Kg of the raw material is converted to leather [9]. Over 80 % of the organic pollution load in BOD terms comes from the pre-tanning process this mainly comes from degraded skin and hair matter. During the tanning process at least 300 kg of chemicals are added per ton of hides. Excess of non-used salts will appear in the wastewater [8]. A large amount of waste generated by tanneries is discharged in natural water bodies directly or indirectly through two open drains without any treatment. The water in developing countries, like India and Bangladesh, is polluted to such a degree, that it has become unsuitable for public use. In summer, when the rate of decomposition of the waste is higher, serious air pollution is caused in residential areas by producing intolerable obnoxious odors [10]. Tannery wastewater and solid wastes often find their way into surface water, where toxins are carried downstream water. Chromium waste can also leak into the soil and contaminate groundwater systems [9].
Steps to improve the waste management in the leather industry
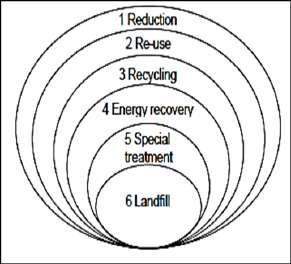
1. Reduce: We should buy only what we need because a better way to reduce waste is by not creating it. Reducing the amount of buying is the most significant of all the options to manage waste. The key is to only purchase goods that we need and in the right amount. If we generate an excess of products in the first place, we do not have to extract raw resources, manufacture goods from scratch, come up with shipping materials, utilize additional resources for shipping, and then devise ways to dispose of them [12]. 2. Reuse: If we have to acquire goods, try getting used ones or obtaining substitutes. Waste, after all, is in the eye of the beholder. One person’s trash is another person’s treasure. If we look at things we are throwing away, we can learn to see them as materials that can be reused to solve everyday problems and satisfy everyday needs. Most of us, however, have not even begun to exploit the resources in our trash. Once you have made up your mind to use trash for positive uses, you can begin to brainstorm and generate ideas. Reusing saves money, conserves resources, and satisfies the human urge to be creative [12]. 3. Recycle: When we discard waste, find ways to recycle it instead of letting it go to landfills [12][13].
Old leather recycling
1. Take gently worn leather goods to be fixed professionally. General shoe and bag repair shops often have the equipment to make repairs including patching, stitching, and stretching, and can restore your leather goods to extend their life. Do not buy new, fix your favorites instead as a sustainable option. 2. Take leather scraps to a recycling outlet for resale. It is a good option of taking leather scraps to be resold to others for many purposes including craft projects. Some industrial level companies also recycle leather to be used again in their products. 3. Donate worn leather shoes to a local charity. Many non-profit organizations will collect used footwear and pass it on to those in need in the community. Before giving away, we should carefully inspect and clean our shoes to appraise their quality for reuse. 4. Donate clothes and bags. Use the internet to find a collector in your neighborhood and give back to your community [14].
Upcycling Leather Items Creatively
1. We can use old belts to make a ‘shelf’. Once we have finished wearing a belt, we can still use it in a variety of handy ways around the home, including creating a unique hanging shelf. It’s easy, cheap, and saves space in your room. 2. We can create funky new handles for a handbag from leather waste. 3. We can make a set of new napkin rings for your dining room table. 4. Also of kind rug for the living room can be made from leather waste. If we have enough scraps, we can make a large rug for the living room [14].
4. Energy Recovery UASB technology
The heat and energy generation can be achieved by treating the wastewater effluent using Upflow Anaerobic Sludge Blanket Technology (UASB) with Sulfur Recovery Plant. The UASB technology has been well-known for treating wastewater primarily because of its low sludge production. The major advantage of this technology is that it provides a potential possibility to generate energy, rather than consuming the same while treating the wastewater using this technology for treating tannery wastewater. Because of the high sulfate content, it results in the generation of methane gas, contaminated with hydrogen sulfide. An improved system has, therefore, been developed whereby the sulfate is completely removed as elemental sulfur. This also reduces the COD by 60% and TDS by 90% UASB uses an anaerobic process while forming a blanket of granular sludge which is suspended in the tank. Wastewater flows upward through the blanket and is processed by the anaerobic microorganism, eventually aggregates form into dense compact biofilms referred to as granules and Biogas with a high concentration of methane is produced as a by-product, and this may be used as an energy source, to generate electricity [11].
Biomethanation for Solid Waste Disposal of leather
Solid wastes generated by the leather processing industry are posing a major challenge. Tannery, fleshings, which are the major solid wastes emanating from the beam house of a tannery, are subjected to biomethanation. It is a process whereby the fleshing is liquified completely biologically. The resulting liquefied fleshing is treated in anaerobic reactors to produce biogas. Any anaerobic reactor like the UASB reactor can be used for this purpose. Biomethanation is a process by which organic material is microbiologically converted under anaerobic conditions to biogas. Three main physiological groups of microorganisms are involved in fermenting bacteria, organic acid oxidizing bacteria, and methanogenic archaea. Microorganisms degrade organic matter to methane and carbon dioxide. Biomethanation has strong potential for the production of energy from organic residues and wastes. It will help to reduce the use of fossil fuels and thus reduce CO2 emissions [11].
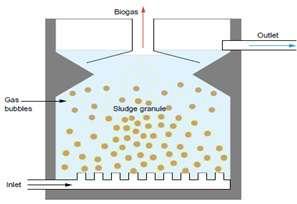
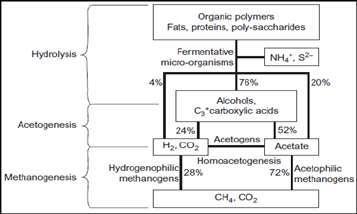
Fig. No. 5 Process Flow of Bio methanation process [11]
5. Special treatment Regenerated leather (RGL)
Preparation of leather-like material, regenerated leather from finished leather wastes is economical and helps in reducing the environmental pollu-
tion. Incorporating plant fibers into RGL enhances its mechanical properties. Plant fibers are exploited as reinforcement materials owing to their low cost, fairly good mechanical properties, high specific strength, non-abrasive, eco-friendly, and bio-degradability characteristics. Fiberized leather wastes and PFs were mixed in various proportions to prepare regenerated leather composites. Plant fibers like coconut, sugarcane, banana, and corn silk were used for a study, regenerated leather composites prepared using leather waste and coconut fiber (50:40 ratio) proved to be a better composite with potent properties. Regenerated leather composites are promising for the preparation of leather goods and footwear materials in addition to their cost-effectiveness and environmental pollution abatement [16].
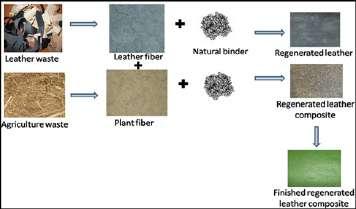
Fig. No. 6 Regenerated leather processing [16]
Benefits of recycling
Reduce, Reuse, and Recycling decreases the landfill space requirements. This will result in pollution avoidance, reduced consumption of energy, chemicals, and water. There will be a reduced demand for dyes. Overall, reducing the need for processing virgin materials [15][17].
Challenges with Recycling
Although the recycling of materials creates a circular economy and therefore increases sustainability, there are potential challenges to recycling leather. Theoretically, offcuts of leather created within the leather manufacturing process are more easily recycled than final products at the end of their life. However, with a potential lack of market for offcuts, this product is often disposed of in the tannery. Although some brands are making use of offcuts or combining leather offcuts with other materials to create a combination material, this is not currently widespread and often this material is used for certain products only. There is an extra cost to recycling goods. If the market is not willing to pay the increased cost for a recycled product, it is unlikely that companies will invest [18].
Conclusion
As the amount of use of leather increases, the waste generated from the leather is inevitable. Research Institutes and Industries are keen to search for various textile waste recycling opportunities at the industrial level for both economic and environmental reasons. The waste generated during the tanning process of leather manufacturing contains harmful chemicals which pollute the groundwater and is a hazard to living organisms. To overcome this problem, there are alternative chemicals that can be used in the tanning process. These alternatives give better results, are safe for living beings, and sustainable. Some Research Institutes have developed new technologies related to heat and energy generation from toxic solid and liquid waste that is generated in the leather industry. With the help modern technology, leather goods can be recycled more efficiently with minimum waste products.
References
1. Dr. Shilpa Goel ‘An in-depth study of India’s leather industry with special reference to export prospects of leather products’ International Journal of Advanced Research in Management and Social Sciences, January 2014.
2. Karanam Sai Bhavya Raji P, Jenifer Selvarani A ‘Leather Processing, Its Effects on Environment and Alternatives of Chrome Tanning’ International Journal of Advanced Research in Engineering and Technology (IJARET) Volume 10, Issue 6, November-December 2019, pp. 69-79.
3. Moses A Ollengo and Esther W Nthiga Peter Maina, (2019), ‘Trends in leather processing’: A Review, International Journal of Scientific and Research Publications, 9 (12).
4. Sumita Dixit, Ashish Yadav, Premendra D. Dwivedi, Mukul
Das ‘Journal Toxic hazards of leather industry and technologies to combat threat: a review’ Journal of Cleaner Production (2015) 39-49.
5. M. Seggiani, M. Puccini, S. Vitolo, C. Chiappe, C. S. Pomelli & D Castiello ‘Eco-friendly titanium tanning for the manufacture of bovine upper leathers: Pilot scale studies’ Clean Technologies and Environmental Policy volume 16, pages1795–1803 (2014).
6. ‘Leather processing, its effects on environment and alternatives of chrome tanning’ laeme publication international journal of advanced research in engineering and technology (ijaret) volume 10, issue 6, november-december 2019, pp. 69-79, article
7. F.R. Souza, and M. Gutterres, ‘Application of enzyme in leather processing,A comparison between chemical and coenzyme processes’. Brazilian Journal of Chemical Engineering, 29(3), 2012, 473-481.
8. J. Hidalgo Ruiz, ‘Wastes generated in the leather products industry’ fourteenth session of the leather and leather products industry Panel Zlin, Czech Republic 13-15 December 2000.
9. Agarwal, R., Sharan, M. (2015). ‘Municipal textile waste and its management’, Research journal of Family, Community and Consumer Sciences. Vol. 3 (1).
10. Ozgunay H, Colak S, Mutlu MM, Akyuz F, ‘Characterization of leather industry waste’. Pol J Environ Stud 6:867–873, (2015).
11. N.M. Sivaram and Debabrata Barik, ‘Toxic Waste From
Leather Industries’ Department of Mechanical Engineering, National Institute of Technology Pondicherry, Karaikal, U.T. n book: Energy from Toxic Organic Waste for Heat and Power Generation (pp.55-67).
12. Fahzy Abdul-Rahman, ‘Reduce, Reuse, Recycle: Alternatives for Waste Management’ Guide G-314, N.M State Uuniversity, Florida Cooperative Extension Service publication HE 3157. January 2014.
13. Rick leblanc ‘The Basics of Textile Recycling’ Growth of Textile Recycling Promises to Divert More Material from Landfills’. Updated December 30, 2020 https://www.thebalancesmb.com/the-basics-of-recycling-clothing-andother-textiles-2877780.
14. ‘How to Recycle Leather’ Co-authored by wikiHow Staff Last Updated: March 29, 2019 https://www.wikihow.com/ Recycle-Leather#References
15. Bairagi, N. ‘Recycling of textiles in India’. Department of Knit wear Design, National Institute of Fashion Technology, Bengaluru, India, Textile Science and Engineering, (2014).
16. Rethinam, Senthil, Tiruchirapalli, Sivagnanam, Uma, Bhabendra Nath Das & Thotapalli Parvathaleswara Sastry ’Recycling of finished leather wastes: a novel approach’
17. Islam, M.M., Khan, M.M.R. (2014). ‘Environmental sustainability evaluation of apparel product: A Case study of knitted T-shirts. Journal of Textiles, Hindawi Publishing Corporation, Article id 643080, 6 pages
18. Clean Technologies and Environmental Policy, (2015), Volume 17, pages187–197.
MONPA HANDMADE PAPER OF ARUNACHAL PRADESH
SHIPRA YADAV
Department of Fashion Technology, National Institute of Fashion Technology, Patna
Revival of 1000 Years old Paper
Traditional art and craft, practiced by various skill-societies in the country are the evidence of Indian cultural heritage. For this, a positive development has been made in the state of Arunachal Pradesh where an extinct 1000-years-old ancient paper mill has been revived by the Khadi and Village Industrial Commission (KVIC). This optimistic approach has welcomed opportunities in bringing the employment for the people of the state of Arunachal Pradesh and also play a vital role to boost the Indian economy. The paper has great historic and religious significance as it is the paper used for writing Buddhist scriptures and hymns in monasteries. The Monpa handmade paper, made from the bark of a local tree called Shugu Sheng, has medicinal values too. Monpa paper craft is made by tawang scheduled tribe people, known as monpa. They were the early people to practice this handmade paper. Slowly and gradually this art become an integral part of the local custom and their source of earning livelihoods. Monpa paper become famous and started being produced in large amount, which was exported in nearby places like Bhutan, Tibet, Thailand and Japan. Because at that time there was no proper paper making industry existed in those countries. Thus, the people of Tawang got the benefit.
The Monpa
The monpas are the major tribes of Arunachal Pradesh in northern India and the believed to be only nomadic tribe in north east India. They completely depend upon animals’ live sheep, cow, yak, goats and horses. Monpas share a close affinity with the sharchops of Bhutan.
About Tawang
This Tawang not only known for handmade paper but also handmade pottery and handmade furniture as with the passage of time it was also get extinct. It also famous amoung tourists for the mountain motorbikes. Tawang shares it bordering region with Tibet and Bhutan.
Over time, the local industry of Arunachal Pradesh began declining and the indigenous handmade paper was taken over by the inferior Chinese paper. After this declination, in 1994, there was an attempt made for the revival of Monpa paper industry but failed due to various geographical challenges in Tawang due to its tough geographical region, with high mountains, daunting terrains which makes industrial developed a complicated to established.
Process of Making Monpa Handmade Paper
Monpa paper is made from the bark of tree Shugu Sheng, grown locally in Tawang. To make Mon Shugu, the inner fibrous bark of the Shugu Sheng shrub is dried, boiled with a solution of ash, made into pulp and then cut into sheets of paper. The process of making this paper is entirely organic with no chemical additives. This naturally processed paper possesses strong tensile strength and is durable. Initially the paper industry engaged 9 artisans, who can produced 500-600 sheets of monpa handmade paper per day. For which each artisan was earning Rs. 400/-.
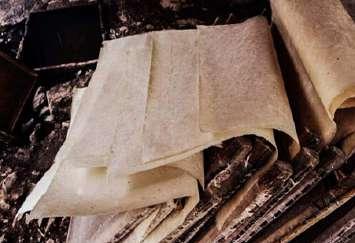
The Arunachal Pradesh government lent support to the project and offered a building on a nominal rent to set up the unit. A team of scientist and officials of The Kumarappa National Handmade Paper Institute (KNHPI) Jaipur were deployed at tawang by the instruction of KVIC.
Challenged faced: The most challenging task for KVIC officials was to transport the machines to Twang owing to its difficult mountainous terrain and inclement weather conditions.
Findings
Monpa handmade paper making unit in Tawang which not only aimed at reviving the art but also engaging the local youths with this art professionally and earn.
Monpa handmade paper has high commercial value that can be harnessed to create local employment. By
increasing production of Monpa handmade paper, it can be exported to other countries. This is a local product with great global potential, which is aligned with the Mantra of "Local to Global" given by the Prime Minister.
The Government has tried to implement schemes for the people of Arunachal Pradesh like intra-state transmission and distribution infrastructure in the state by providing the states grid connectivity to remote areas.
Producing paper from Non-Timber Forest Products (NTFPs) and nonwood fibres help in reducing the need to procure pulpwood from natural forests and to minimize deforestation. These products are vital sources of income, nutrition and sustenance for many forest-based communities around the world.
With increasing population, paper consumption has also been increasing which demand large number of raw materials from different sources, such as wood, non-wood fibre and nontimber forest products to increase the production. With the strong resolve of the higher management of KVIC, the unit was successfully established despite many challenges. The 1000-year-old heritage art the monpa handmade paper of Arunachal Pradesh which was driven to extinction has come to life once again with the committed efforts of KVIC.The revival of this paper industry brings an encouragement to the art and heritage to the people of Tawang. This initiative not only brings the revival but the employment to the people of Arunachal Pradesh making it a part of their livelihood by the prime minister mantra “local to global”. The making process of monpa handmade paper is eco-friendly and the product is biodegradable which made from non-timber forest product. It also encourages the value of monpa (scheduled tribe) to the world recognition. Not only this revives the Indian heritage but also play a vital role to boost the Indian economy.
References
[1] PIB Delhi (2021, February 04). Press Information Bureau, Government of India, Ministry of Micro, Small & Medium Enterprises; Article. People Patronize Monpa Handmade Paper of Tawang after PM’s push in Mann Ki Baat.Retrieved from https://pib.gov.in/Pressreleaseshare.aspx?PRID=1695156
Figure [1] [3]- PIB (2020) Monpa Handmade Paper [Photograph] Arunachal revives 1,000-year-old handmade paper industry https://acumenias.in/uploads/ affair/Monpa%20Handmade%20Pa per20201230070138.jpg
Figure [2] PIB (2020 December 28). monpa handmade paper[photograph]. https://vajiramandravi.s3.us-east-1.amazonaws.com/ media/2020/12/28/10/12/4/jjjjj.jpg
Figure [4][5] Holiday Scout (2017, 04 June) Tawang Focus – The Art of Making Paper. [Photograph] https://theholidayscout.com/ indigenous-knowledge/arts-and-crafts/tawang-focus-the-art-of-making-paper/
Figure [6] Sentinel Digital Desk (2020 28 Dec). KVIC revives Monpa handmade paper industry, historic event for the locals of Tawang. [photograph]. https://www.sentinelassam.com/north-east-india-news/ arunachal-news/kvic-revives-monpa-handmade-paper-industry-historic-event-for-thelocals-of-tawang-518374
LENZING CLAIM TO FAME FILAMENTS TO BE PRODUCED USING MATERIAL WASTE
NEWS
Lenzing and Södra are expecting to transform a yearly 25,000 tons of material waste into the new item by 2025. Lenzing is collaborating with mash maker Södra, settled in Växjö, Sweden, on the further improvement of OnceMore Pulp created from material waste.
The arrangement includes the exchange of information between the two organizations which have been proactively driving the roundabout economy numerous years and following joint turn of events and a limit extension, OnceMore Pulp will be utilized as a crude material for the creation of Lenzing's Tencel x Refibra marked forte strands. The two organizations are intending to turn a yearly 25,000 tons of material waste each year into the new item by 2025. The OnceMore cycle joins wood cellulose with up to half material waste substance to make an unadulterated, excellent dissolving mash which can be utilized to create new attire and other material items.
"The participation with Södra is a significant achievement towards accomplishing our yearning environment and manageability objectives. We are pleased to have the option to go this route with a capable accomplice. "One organization alone can't address the major problem of material waste," said Christian Skilich, individual from the overseeing leading group of Lenzing. "It is proactive organizations like this one that will empower us to push ahead and achieve genuine fundamental change." "With OnceMore mash, Södra has made an internationally one of a kind answer for putting together materials with respect to a reused source," added Lotta Lyrå, President and CEO of Södra. By uniting with Lenzing, we will carry a-list reusing to the material worth chain. Through another speculation, we will likewise build our creation limit with regards to OnceMore mash ten times during 2022 and have a more significant level of reused material substance. These are significant strides towards our drawn out focus of making a round material industry."