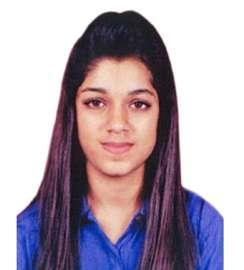
24 minute read
HEMP by Aishwarya Patil SUSTAINABLE FIBRE
HEMP
AISHWARYA PATIL
Advertisement
Department of Textile Design, Sophia Polytechnic, Mumbai
Hemp is obtained from the Cannabis sativa plant, the hemp filaments are notable for their solidness and toughness. In their crude state hemp strands are profound earthy colored to yellowish dark. Hemp was one of the first and most regular plants to be made into texture around 10,000 years prior.
Harvesting of Hemp fiber
Hemp fiber is grown in a calm environment. It needs three and a half months with 10-12 crawls of precipitation to develop sufficiently. Hemp plants are additionally thermophilic and heliotropic, implying that they need a decent measure of warmth and sun, without which seed creation and biomass are settled. Beginning in Central Asia, it is presently cultivated in various nations from the USA, Italy, Canada, Germany, France, Philippines, and India.
The plant-developed fibers are thickly planted and grow up to 2-3 meters tall. They are collected after their development. These seeds can be utilized for additional harvests and sold as food.
The hemp plant helps in recovering and detoxifying the soil. Apart from the normal advantages, falling leaves renew the soil with nutrients, oxygen, nitrogen. The underlying foundations of the hemp plant disperse and retain the energy of downpour, which keeps the seeds in place, and likewise ensures and treats the soil.
The base advantage of a hemp crop is as a turn crop. Hemp improves and balances out the soil where ranchers develop the harvests and provide them with weed-free farms.

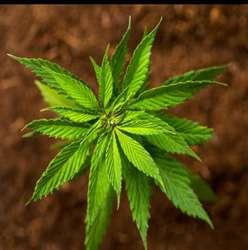
Figure 1: Hemp Plant
Hemp fiber handling
Hemp handling does not require numerous synthetics, however, may require other engineered filaments and gums relying upon the item that will be made. The fiber is produced using a stalk and goes through numerous cycles to foster good results.
Retting
Retting is a cycle that utilizes the activity of miniature life forms and dampness on plants to break up or decay away a large part of the cell tissues and gelatins encompassing bast-fiber groups, thus working with the partition of the fiber from the stem.
Field/dew retting is a kind of retting that should be possible on-ranch, while different varieties require a special service.
Water retting includes drenching the dry hemp stems in microorganismsfilled water tanks, lakes, or waterways. Compound retting utilizes acids and unique chemicals to separate the segments of the bast filaments. They are bubbled in medicines comprising of synthetic substances like Sodium Hydroxide, Sodium Chloride, Sodium Sulphite, Hydrochloric corrosive, and Oxalic corrosive.
Decortication
Hemp decortication is the cycle that eliminates the intense, woody inside of the hemp plant and isolates it from its delicate outside.
Hackling
Hackling is when short and mediumsized filaments are brushed out of the tail.
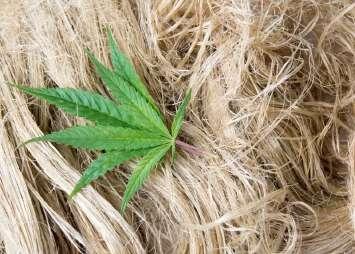
Spinning
To additionally treat the filaments for a better yarn, they are gone through a box of boiling water before being turned. This is known as wet turning. It mollifies the gelatin and considers further detachment of strands. Dry turning is additionally conceivable, yet the result is coarser. It is additionally less expensive.
Baling
Hemp filaments are at last baled for long-haul stockpiling or transportation. Enormous, round bunches work best as they take into consideration better drying. and the hemp isn't just about as firmly stuffed as in squares. They ought to be put away in a dry, less damp climate restricting any kind of water entrance to keep away from form. Utilizing plastic net wrap and twine would additionally guarantee its uprightness.
Hemp Fiber Properties
It is exceptionally impervious to hurtful UV beams and willnot blur in the daylight. It is speedy drying and forestalls the development of microscopic organisms and buildup, making it hostile to microbial. Hemp withstands washing – each time it is washed, the strands become gentler and better. It additionally sheds an infinitesimal layer that abstains from ruining and uncovered a new surface. The actual texture is completely biodegradable and recyclable, adding to manageability. Even though it is difficult to blanch the normally dim shade of hemp fiber, it tends to be colored in splendid or more obscure shadings and does not blur without any problem. The elasticity of hemp fiber is more prominent than other vegetal strands and twice that of cotton. This demonstrates that it is undeniably more solid and can be utilized for mechanical items requiring a sturdier texture. The hemp strands have minute recesses, making them incredibly breathable and retentive. The texture assists one with remaining cool in blistering climate and warm in cool climate due to the catacombic development, which permits air caught in the strands to be warmed by the body. The fiber has low versatility, so items made with hemp textures hold their shape.
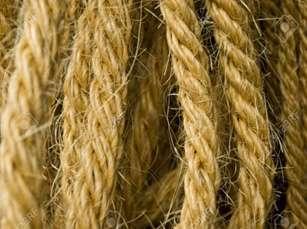
Figure 4: Hemp Ropes and Cords
Uses of Hemp fiber
Attire and Textiles - Hemp fiber has been utilized for millennia to make cloth for garments and materials. The material has various profitable properties like UV security and its microbial/ hypo-allergenic advantages make it ideal for delicate skin.
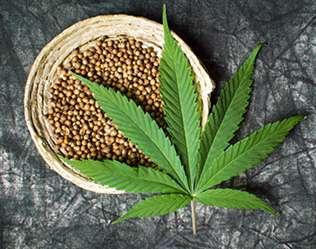
Shoes - Hemp has additionally been utilized to make shoes that are agreeable and durable rather than cowhide. Calfskin can be costly; however, hemp fiber is much less expensive, not as tedious, and does not hurt creatures. Paper - The most widely recognized and old utilization of hemp fiber is for paper. It can be a fill-in for wood fiber in mash and paper creation. It offers 4-5 times longer fiber and higher elasticity, adding to higher tear opposition. Ropes and Cords - Hemp is perhaps the best fiber to make ropes and ropes because of its toughness and is more grounded than jute, material, and cotton. It was likewise utilized for sail apparatus and anchor strings. The flexibility of Hemp adds to its yearly development pace of over 30%. It will just keep on expanding as individuals roll out the improvement to feasible, eco-accommodating items with little mischief to the climate. From the different properties of hemp, we can conclude that hemp is a material with a fantastic extent of supportability. It is not just natural but is also climate well disposed and modest in every aspect. Hemp is eco-accommodating and likewise benefits the soil and air where it is developed.
References
• https://www.the-sustainable-fashioncollective.com/2014/12/02/hemp-fibre-fabric-eco-benefit/
• https://www.nugistics.io/hemp-fiberextraction-processing-properties/
Image source
• https://arc-anglerfish-arc2-prod-pmn. s3.amazonaws.com/public/KB2HJM-
SUEFGHLO2EDE7P6WRJEY.jpg
• https://www.ksre.k-state.edu/news/ images/news-stories/2019/ag-naturalresources/ukhempharvest%20web.jpg
• https://njaes.rutgers.edu/fs1312/fs1312main-1.jpg
• https://www.unnatisilks.com/blog/wpcontent/uploads/2019/06/Group-2-2. jpg
• https://static.wixstatic.com/media/e4039a_531d48f0b94340799e 5bdb0a4641127d~mv2.jpg/v1/fit/ w_320%2Ch_600%2Cal_c%2Cq_80/file. jpg
• https://previews.123rf.com/im ages/mahroch/mahroch1007/ mahroch100700050/7468070-detailof-the-rope-made-of-natural-fibres-ofhemp.jpg

YARN EXPORT MAINTAINS TEMPO IN APRIL, COTTON TAKES LEAD
TEXTILE BEACON
Basic textiles comprising fibers spun and filament yarns shipment were worth US$1,053 million or INR7.730 crore, accounting for about 3.4% of total merchandise exported from India during the month. We have intentionally refrained from analyzing year-onyear comparison (April 2021 with April 2020) since April 2020 was an abnormal month with values abysmally low and outliers to the trend.
Spun yarns shipment totaled 138 million kg worth US$491 million or INR3,600 crore. The unit value realization of all types of spun yarn averaged US$2.3.55 per kg. Bangladesh was the largest market for spun yarns, topping both in terms of volume and value. China followed by 14% of the total value. Cotton yarn export was 110 million kg worth US$408 million (INR2,997 crore). These were destined to 79 countries at an average price of US$3.70 a kg, up to US cents 25 from the previous month. Bangladesh was the top imported of cotton yarn, China, Portugal, Vietnam, and Egypt. 100% man-made fiber yarn exports were at 8.8 million kg, comprising 1.7 million kg of acrylic yarn, 3.3 million kg of viscose yarn, and 3.6 million kg of polyester yarn. Viscose yarn was worth US$11.5 million or INR85 crore, exported at an average price of US$3.48 per kg in April to 29 countries. Of these, the major market was Turkey, followed by Bangladesh and Belgium. Polyester spun yarns export was worth US$8.6 million exported to 41 countries at an average unit price of US$2.37 a kg. Turkey was the largest importer of polyester yarn, followed by the USA and Brazil.
Blended spun yarns worth US$6.6 million were exported in April, including 1.6 million kg of PC yarns and 0.5 million kg of PV yarns. Bangladesh was the largest importers of PC yarn from India followed by Brazil while Iran was the single largest importer of PV yarns from India followed by Turkey. All kinds of filament yarns shipment totaled just 8 million kg, valued at US$11 million or INR85 crore. Cotton shipment in April was 11.6 lakh bales worth INR2,800 crore or US$382 million. This takes the total export to 78 lakh bales worth US$16,867 crore or US$2,322 million in the first eight months of the 2020-21 marketing season. China was the largest market for Indian cotton export during April, followed by Bangladesh, Vietnam, and Indonesia.

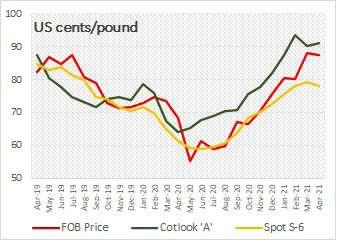
Export price realization for cotton averaged INR142 a kg or US cents 87.56 per pound during April. This was much below Cot look A index, the global spot price benchmark, and higher than domestic spot price for benchmark Gujarat Shankar-6. During the month, Cotlook averaged US$91.15 per pound while Shankar-6 was at US cents 78.22 per pound, which implied Indian cotton was still competitive in the global market.
FIBRE PRICES EASE IN MAY ENTERING LULL DEMAND SEASON
TEXTILE BEACON
Polyester
Polyester staple fibre prices eased in China and declined in Pakistan but were up in India during May. In Jiangsu and Zhejiang, the market saw offers and discussions falling in the first half of the month but recovered partially towards the end. Trading prices were below offers, indicating a discount in firm deals were under negotiation. In Fujian, nominations marched down and discussions trended lower. Offers for 1.4D direct-melt PSF were lowered to 6.65-6.80 Yuan a kg (US$1.03-1.06 a kg, down US cent 1) in Jiangsu and Zhejiang while the same in Fujian and Shandong were down similarly at US$1.04-1.07 a kg. In Taiwan, offer for 1.4D were down US cents 4 at US$1.10 a kg FOB. In Pakistan, polyester fibre market was mostly shut after the country returned to lockdown amid Eid holidays. No change was reported in prices in Karachi market during the month after offers were lowered by PakRa5 in the last week of April. Thus, 1.4D PSF offers averaged at PakRs.200-202 a kg (US$1.31-1.32 a kg, down US cents 5). In India, producers kept their offers stable for May seeing downstream markets hard hit by restrictions to contain the second wave of the Covid-19. Offers for H2 April were lowered and thus May average were down compared to April at INR96.75 a kg (US$1.32 a kg) for 1.2D and at INR96 a kg (US$1.31 a kg) for 1.4D. With India and Pakistan continuing with lockdown, although partially and China entering a seasonal low, demand will remain depressed in coming month.
Nylon
Nylon-6 staple fiber offers were raised 7% in China in May as upstream caprolactum as well as polyamide or nylon chip cost were raised. producers reported breakeven business, despite weak demand. Prices were down at lower end for high-end values goods woollike grade items closing May. 1.5D offers averaged 16.18-16.75 Yuan a kg (US$2.51-2.60 a kg, up US cents 14 on the month).
Acrylic
Acrylic staple fibre prices tumbled in China and India during May but gained somehow in Pakistan. Offers for Taiwan origin 1.5D acrylic fibre stayed frozen month on month to average US$2.95-3.10 a kg FOB Taiwan. In China, reference prices of cottontype staple fiber, tow and top were down 11% during the month. Althoguh there were limited orders from spun yarn producers, demand was moderate. More than half of all acrylic fibre capacities have been offline after acrylonitrile prices went up at a higher speed in March. The industrial run rate reached a low of 55% this week.
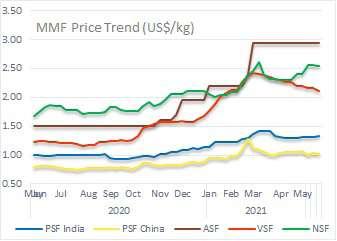
Prices for medium-length and cottontype acrylic fibre 1.5D and 3D tow averaged 17.12-17.62 Yuan a kg (US$2.662.74 a kg, down US cents 33). In Pakistan, overseas offers for acrylic fibre jumped 30% in Karachi market during May. 1.2D ASF offers averaged PakRs.452.50 a kg (US$2.95 a kg). In India, producers lowered their offer by about 7% as acrylonitrile cost fell 11% in May month on month. Offers in May averaged INR232.50 a kg (US$3.17-3.20 a kg, down US cents 16).
Viscose staple fibre prices were lowered in China and Pakistan during May, in line with weak demand from spinners and lower spun yarn prices, while they were rolled over in India. In China, producers offered large discounts, so transaction volumes increased somewhat. Downstream mills made massive procurement at low price levels, so inventory pressure on fibre producers eased somewhat. Prices for both medium-end and high-end goods were pegged lower while spot prices were pegged lower than offers. In spot, average prices fell US cents 8 with 1.5D at 13.90 Yuan a kg (US$2.16 a kg) and 1.2D to 14.48 Yuan a kg (US$2.25 a kg). In Taiwan, offers for 1.5D were raised, in contrast by US cents 4 to US$2.10 a kg FOB, citing costlier raw material pulp cost. In Pakistan, producers’ offers were lowered in the last week of April as lockdown and Eid holidays did not see any trading activity. Offers were maintained stable in May in expectation that recovery in demand will pick up after the Eid holidays, whereas the Covid crisis appear to have weakened. Offers for 1.5D VSF in Karachi averaged PakRs340-345 a kg (US$2.222.25 a kg, down US cents 13-15). In India, producers’ offers for 1.2-1.5D remained unchanged at INR195-197 a kg (US$2.67-2.70 a kg). Overall, viscose fibre prices are expected to remain soft amid with bearish expectation in June.
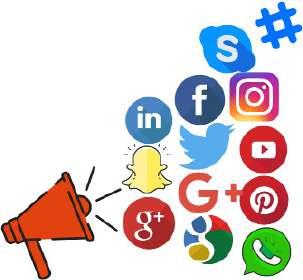
Digital Promotion In Textile Value Chain Media Promote Your Business Online
Banner On Home Page Social Media Promotion TVC E-Newsletter Banner Customised Email Marketing
Visit Our Platforms To Know More :
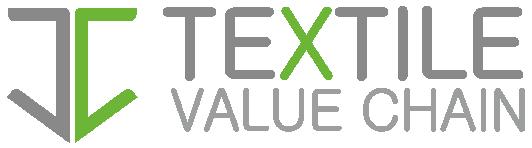
GO DIGITAL
All You Need Is... A Digital Push!
Social Media Agency Handling Of Upto Four Social Media Three Post Per Week Designing Of Posts Competitor Analysis Follower Increase Activity Monthly Performance Report
Our Clients :
Chur Textiles Mechtex Engineers Textile Courses Online
For Enquiry: Mr. Mohammad Tanweer Mail: sales@textilevaluechain.com Phone: +91 9167986305
A REPORT ON SDC EC INDIA WEBINAR END TO END: PROCESSING AND WASTE MANAGEMENT
Event Sponsors: AMA Herbal Group Companies, Britacel Silicones Ltd., Archroma Ltd., Ion Exchange (I) Ltd, and DR. JD
The attendees were welcomed by Dr. Vishaka Karnad, Hon. Trustee, SDC EC who briefed the audience on SDC and introduced the Moderators of the two Panel Discussions.
PANEL DISCUSSION 1. Wet Processing Technologies and Methods
Moderator: Mr. Anjani Prasad
Managing Director & Member of Global Leadership Team, Archroma Pvt. Ltd.
Panelists:
Mr. Arindam Choudhuri (Business Head – Global, Britacel Silicones Ltd.) Mr. Yawar Ali Shah (Co-Founder & CEO, AMA Herbal Group Companies) Mr. Klaus Bergmann (MD of Erbatech India PVT. LTD., Director Sales & Director Textile Technology of Erbatech GmbH Germany) Mr. Anjani Prasad introduced all the panelists and the theme of wet processing technologies and methods. The
Day: Friday, 14th MAY 2021 Time: 5:30 PM to 7:30 pm Online Platform Virtual Panel
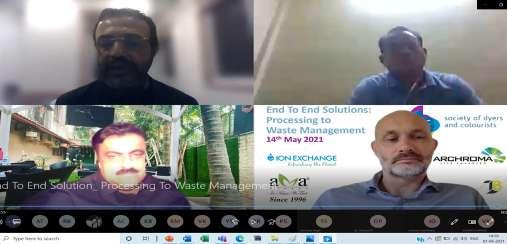
Discussions MS Teams
Participants: 227
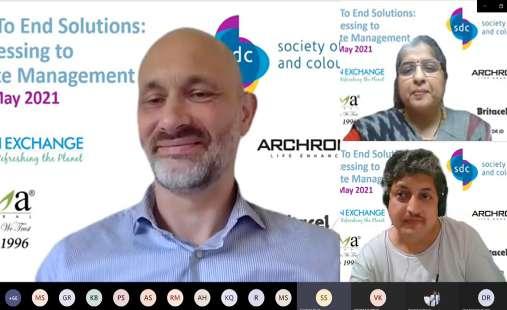
safety he said was of prime importance - safe purchase, safe process, and safe disposal. It is important to take care of chemical management. Check for RSL, MRSL at the starting point, if inputs are right only then, the output will be right. It is important to make the right choices for purchasing dyes and chemicals and we make the right processes. Inappropriate choices can have a hazardous impact on life and the environment. He suggested that the discussion would be around the solutions to processing both improving efficiency and process enhancement. It is important to consider if the Plant is being used for more enhanced features and efficiency to get the right values on the ecological and social aspects of sustainability. There are a lot of areas to improve on namely to improve productivity and efficiency ratios, to have reduced lead times for value generation of products, of the company with sustainability along with enhanced functionality features. All this considering enhanced social economics as the goal. With this, he posted some questions to the panelists. Mr. Arindam Choudhuri stressed the importance of adopting efficient machinery and new technologies saving water and energy voluntarily by Companies. He suggested the move towards continuous process rather than discontinu-
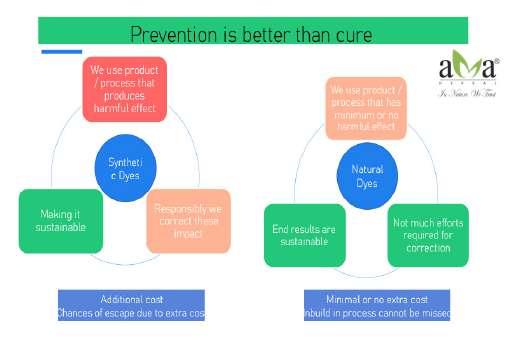
ous process, ZLD or water harvesting or recycling, installation of the solar system across the free space inside dye house to save natural energy, design dye house premises efficiently to save daylight, process optimization to reduce the machine run time, reduce the inorganic chemical use in the process, reduce the sludge after ETP, or concentrated chemical use to reduce petrochemical base packing material and air pollution while transporting the chemicals. Non-PVA/Non-Synthetic (Acrylic /Resin/Binder) base Sizing agent, use of hot water to de-size natural starch which can easily be removed from fabric in PTR washing range (without enzymatic de-sizing) saving on one process/hold time 8 – 12 hours, electrical rotation cost & labor man-hour, etc. He suggested Pad–Steam de-size over Pad–batch de-size for regular/conventional sizing process. In the Pad batch, you need rotation that leads to an increase in lead time, electrical energy consumption, and wastage of water. Caledon Vat pigment dyeing system for light and pastel shades over CPB/PDPS System with no washing required, in Caledon dyeing, Hydrose and Soda Ash replacement by chemicals, Low temperature, Soaping, Bleaching, RT de-size/bio-polish, Resin. Avoid Sanforize/Calendar whichever possible so that extra mechanical process can be avoided and energy cost reduced. Purchase and concentrated chemicals to avoid unnecessary packing material wastage, limit the transport of chemicals, saving on utility/energy/raw material.
Knits Continuous bleaching and CPB dyeing to avoid salt/time/energy consumption. He touched on the Green chemistry concept for textile finishes and the usage of Sustainable Certified chemicals. He mentioned the advantages of Chemical Fission that were found to yield uniform particle size, better finish batch to batch, equal surface preparation, reduction in silicone consumption, and ease of crosslinking with organic molecules. Textile finishes need to be sourced from renewable, natural raw materials, that achieve high levels of textile performance while radically lowering carbon emissions. The activation of silicone openchain polymer emulsion yields component that is readily reactive with easy penetration, giving durable finish, low consumption, and uniform softness. Mr. Yawar Ali Shah said that there are millions of dollars spent on sustainability. We are responsible enough to make textile processing sustainable. We need to plan the Exhaust method in garment dyeing, planning that is necessary, as prevention is better than cure. To illustrate, he compared the process of Natural Dyeing as compared to re-
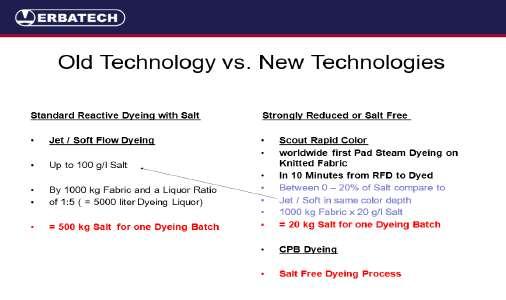
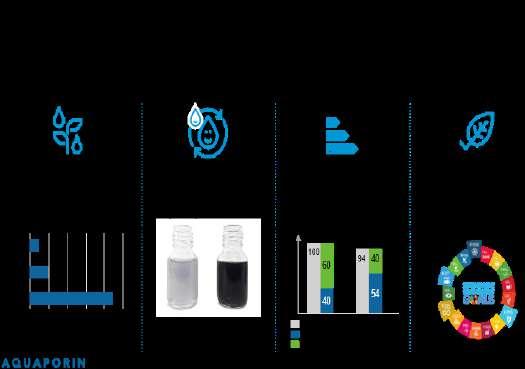
active dyeing. He proved from R&D studies that the saving of auxiliaries, dyeing time, and dyeing at room temperature, clearly directed to zero consumption of energy, saving the time of dyeing and remarkable reduction of BOD, COD, TDS, and pH values with no serious modifications. Mr. Klaus Bergmann emphasized the need for salt-free dyeing or strongly reduced salt dyeing. As the textile industry faces the problem of water. He spoke on the key advantages of the continuous dyeing process with low production costs, easy reproducibility, no enzymatic treatment for hairiness, and no salt in the effluent. It is important to go ahead in adopting safe technologies. He compared the consumption values of continuous dyeing and discontinuous dyeing with a 60% reduction in water 52% steam and 45% electricity consumption. There is a potential demand for new technologies, strongly reduced or salt-free dyeing of knitted as compared to the Jet/Soft Flow dyeing of Standard Reactive dyeing which requires (was 100g/lt salt was too much) five times the amount of salt.
Mr. Arindam recommended bio-elimination. He suggested that people from the fashion and processing houses must shorten the material to liquor ratio and improve chemi-
cal efficiency for old machines by using modern technologies. Mr. Anjani Prasad added that safe selection of products and check on MSDS. OECD can be checked for biodegradability. OECD can be checked whether it will biodegrade on its own. In reality jet technology leads to 2-5%/kg fiber loss which is not sustainable. Solvent-based or acid-based processes are not beneficial. Bio polishing process can be avoided. Mr. Yawar Ali Shah added that brands are recycling 20-30% recycled with fresh. This sustainable concept not only saves energy costs and reduces landfill space. Upcycling of garments has a lot of scopes. Mr. Anjani Prasad gave an example of stripping or shredding waste for regeneration for Viscose, paper, nonwovens, nitrocellulose for construction, etc. Yawar Ali Shah said that what is a waste for one is considered as a resource by another e.g., pomegranate rind considered as waste is a source of dye. He gave an example of the extraction of Ethyl alcohol from Sugarcane for sanitizer. Waste from any source has utility and has to be renewed as a resource.
PANEL DISCUSSION 2: End of pipeline solutions and waste management solutions Moderator: Mr. Ajay Popat, President, Ion Exchange (I) Ltd. Panelists:
Dr. K. Ramesh, Tamilnadu Water Investment Company Limited, Tirupur, Tamil Nadu. Mr. Soren Robenhagen, Sales Director, Industrial Water, Aquaporin, Denmark. Dr. Jaideep Dudhbhate, Textile Consultant, Pune, India.
• Mr. Ajay Popat introduced each of the topics and speakers and the topic of waste management. Textile
Waste Water- Current Limitations of conventional effluent treatment processes. The discussion, therefore, focused on the New technologies / Drivers listed here: Recovery of salts, dyes, energy and water, Automation & Digitalization, Remote Sensing, Monitoring Control, Optimize OPEX, Sustainable Treatment Technologies, Biological processes with lower,
Energy Footprint, Sludge generation, Advanced
Oxidation, Electrocoagulation, Non-vortex cavitation, PCO, Affordable ZLD- AMBC and OARO / FO.
Pollution and increased demand have made good quality water-scarce and expensive due to stringent discharge norms. • ZLD is mandated in textile units having effluent discharge more than 25 m3/day & also for all textile units in clusters irrespective of their wastewater discharge
Textile units face the folloing limitations for ZLD implementation : • Capital expenditure of INR 8-9 crore /MLD excluding land cost Operating cost of approximately INR 225/m3 • Cost of Electricity from 3000-15000 kW/day
ZLD Increases the cost of production by 25-30 % • Generation of quantum of hazardous solid waste & increase in disposal costs • High Carbon footprint with power consumption from 8-10 kW/m3, Thermal evaporators require 20-40 kW/ m3
• Inefficient functioning of Primary & Secondary involving Biological treatment units leading to choking & scaling of membrane & evaporators which increases expenditure due to repair/replacement. Mr. Ajay shared the TERI Analysis Report and indicated the technologies and drivers to resolve the limitations and problems of the industry. Dr. K. Ramesh presented a Case study on Waste Mixed Salt minimization Technique in ZLD Process. The Waste salt generation from RO brine Management system comprised of Mechanical Vapor Recompression (MVR) type Evaporator, Multiple Effect Evaporator (MEE), and Agitated Thin Film Dryer (ATFD). He spoke on the high waste mixed salt generation due to crystallization of salt from RO brine, generation and disposal issues of considerable amounts of fly ash from boiler due to salt crystallization. 80% salt recovered from the wastewater can be reused in the dyeing process. No fresh salt is required. The remaining salt (20%) is waste mixed salt with contaminants and is being stored. He suggested the Treated brine Reuse Technology to reduce waste mixed salt generation. In another Case study, on Salt Separation and Purification in ZLD Process using Membrane Technology. The improved brine reuse technology with NF, Membrane Distillation (MD) is based on Solar thermal energy for Zero Liquid Discharge (ZLD) with Zero Waste Salt (ZWS) generation. Solid waste reduction techniques and disposal methods. Sludge reduction techniques in ZLD Process/Water recycling Plants. Elimination of primary chemical treatment and treating of combined wastewater (TDS < 10g/L) directly through Aerobic biological treatment (Extended Aeration). For Hardness reduction, WAC resin can be implemented instead of Lime-Soda Softening(LSS) treatment. The quantity of Chemicals required to treat the WAC’s sidestream waste is very minimal than the LSS. Disposal and utilization methods were discussed where, the Bio-sludge was stored, mixed with biomass briquettes for burning in boilers. The Chemical sludge for new plants, manufacturing of fly ash brick (from the Captive Power Plant/Boiler) with the lime sludge was proposed. Currently, Chemical sludge lime is being sent to nearby cement industries for Co-processing. Integration of Solar Energy for brine management to eliminate ash generation and disposal issues. Brine Management using solar energy to eliminate ash generation from the boiler. Application of Membrane Distillation (MD) system instead of MEE and use of a solar thermal system to generate hot water (at 90oC) which can be used as a heating medium instead of steam. Advanced Oxidation Process (AOP) is a Sludge-less
Technology, to reduce COD and Colour removal. In current treatment methods, Biological treatment is capable of removing COD and BOD but not color. Generally, chemical treatment and Polymeric resin (WBA) are extensively used to remove the color from the secondary treated effluent. High sludge generation from chemical treatment and liquid waste stream from WBA resin is difficult to handle and high Opex. Electrooxidation (EO) to replace WBA and Chemical treatment methods. Electrooxidation offers a good reduction in COD and Colour if implemented as a downstream treatment unit to the secondary treatment system. EO process can also be used as a standalone treatment unit to recycle the brine solution (Post hardness removal). Zero-Sludge from EO Process and hence no sludge handling and disposal issues. Mr. Soren Robenhagen spoke on Aquaporin’s sustainable re-use of water in industrial applications. He introduced Forward Osmosis and explained how it works. Forward osmosis uses natural energy in the form of osmotic pressure to transport water through a membrane. This process enables efficient extraction of water, leaving challenging contaminants behind and reducing effluent volume. The benefits of applying forward osmosis ered (20x concentration). Stable water flux at 8-10 LMH, >5 LMH from 90-95 %. Good membrane chemical and physical tolerance. Another Case Study on FO post RO in ZLD scheme with FO brine concentration. LD scheme with FO, which pre-concentrates the brine concentration up to 150,000 ppm and reduces the volume by up to 90 % before it is sent for evaporation. Dr. Jaideep Dudhbhate contributed to the topic on the end of the pipeline solutions for the reduction of wastes/ sludges generated in the wastewater treatment plants. He presented several case studies and pilot treatments for the reduction in color and chemical sludge quantity to 0.5-1 ton/d. Although lime-ferrous treatment is eliminated, tertiary treatment was needed. However biological sludge generation still takes place (excess bio sludge generation 0.25-0.35 Kg / Kg COD reduced). He explained the sludge-less biological process with a reduction of 90-95%. Some solutions in textile wastewater effluents were suggested tertiary decolorization after biological treatment. Low energy requirements–almost 50% power saving in COD reduction. When there is excess bio sludge along with less chemical sludge, less requirement for downstream sludge handling. The Panel Discussions ended with a Vote of Thanks by Mr. Sandeep Singh, Hon. Trustee, SDC EC. The chatbox had several questions that were answered in the Chat and few queries would be answered through the mail. A feedback form was administered and certificates were issued to participants and all the sponsors for their generous support extended through their sponsorship. Heartfelt thanks to the Sponsors of this Event and the SDC EC Team for making the program successful. Looking forward to furthering interactions and collaborations in our endeavors for learning and enrichment.
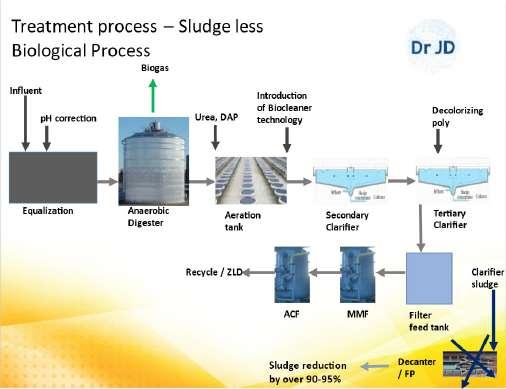
in textile wet-processing. Reduce water consumption for washing and rinsing operations. Recycle rinsing waters within the wet-processing or reuse the water for utilities. Reduce the effluent volume sent to the effluent treatment plant and evaporator to save costs. Recover chemicals (dyes/salts/metals) for reuse. The concentrated “draw solution” drives the FO process. Regeneration of the draw solution is often needed to maintain the driving force and to extract clean water as a product. Water is recovered from both upstream wet processing and downstream in ETP/ZLD. Cut energy consumption - reduce carbon footprint and operating costs. Presenting a Case Study on Wool & cotton dyehouse wastewater, Mr. Soren Robenhagen explained that water-saving and reuse allow for 6.7 EUR/m3 saving in bleaching and dying operations. 95 % clean water recov-
-DR. VISHAKA ASHISH KARNAD (CTEXT.FTI) Associate Professor, College of Home Science, Nirmala Niketan
Honorary Secretary, SDC EC & Hon. Secretary “Textiles” SIG TI
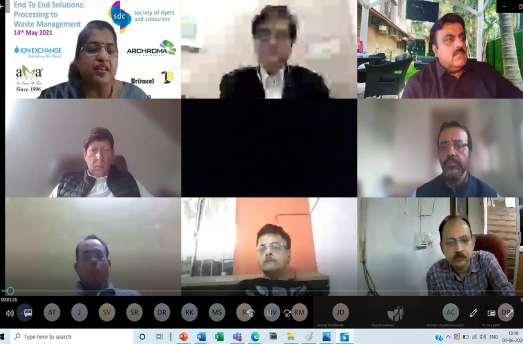