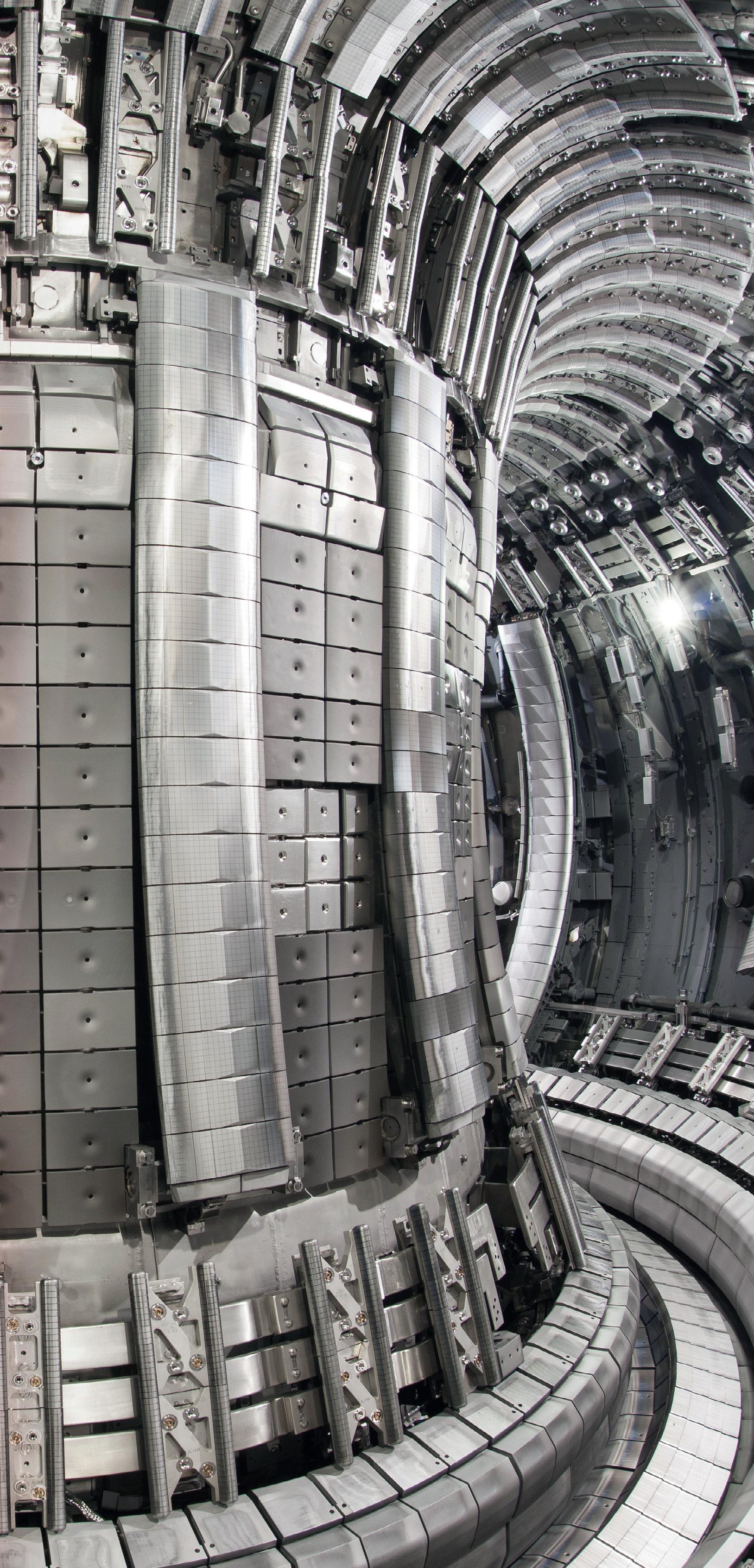
9 minute read
The future is fusion
Imagine a source of electricity where the fuel comes from water, fuel supplies will last for many thousands of years, the whole process is inherently safe and, most importantly of all, no carbon is produced. That is the promise of nuclear fusion – and it is turning from science fi ction to science fact.
Harnessing the power of the Sun The fusion of hydrogen to make helium is what makes the Sun shine – and it has long been mankind’s dream to harness this powder directly here on Earth. So why is fusion electricity not on the grid?
The simple answer is that it is very hard to do. The optimum fusion reaction fuses two isotopes of hydrogen (deuterium and tritium) to produce helium, a neutron and excess energy – but it requires the hot gas or ‘plasma’ of fuels to be heated to temperatures of around 150,000,000ºC. The most advanced approach is a device called a tokamak (fi rst developed in Russia in the 1960s), in which a powerful magnetic fi eld is used to hold the plasma inside a ring-shaped vessel. In future power plants, the fusion neutrons (which contain most of the excess energy) will be slowed down in so-called ‘blanket modules’ positioned around the vessel walls. These get very hot and can produce steam to drive turbines that make electricity.
Making fusion work The UK leads the world in developing this transformative technology, with the UK Atomic Energy Authority’s (UKAEA) work at Culham Science Centre in Oxfordshire at the forefront. For example, UKAEA operates the world’s largest and most advanced tokamak – JET – on behalf of European fusion researchers. JET is the only tokamak in the
The STEP programme is a staged programme to design and build the world’s fi rst compact fusion reactor by 2040
The future is fusion
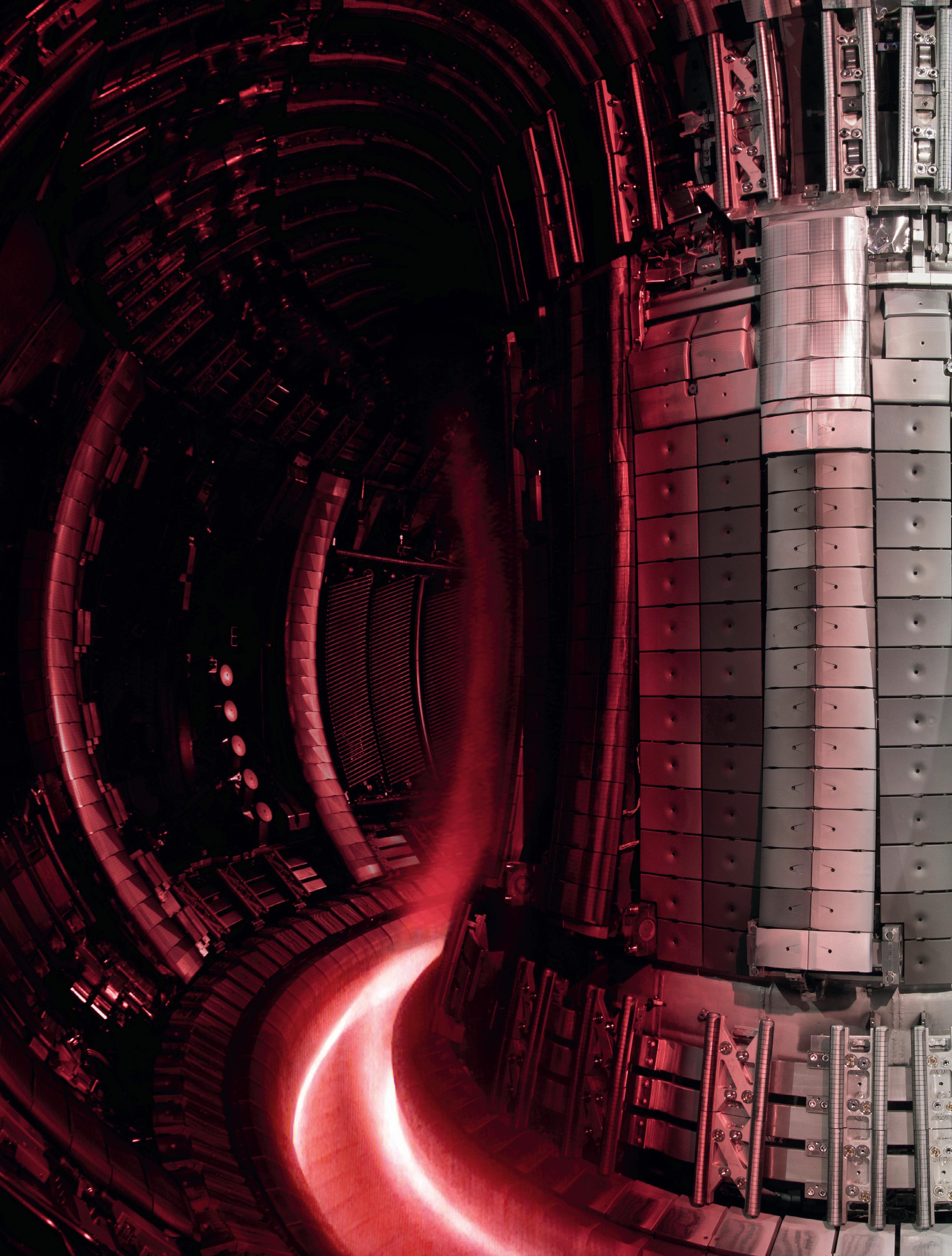
As the quest for clean, limitless energy heats up, nuclear fusion is a question of ‘when, not if’, says Professor Ian Chapman at the UK Atomic Energy Authority
world that can use both deuterium and tritium, boasting an advanced remote handling maintenance system. It holds the world record for fusion power of 16MW. Recent JET experiments are all focused on preparing operations for ITER – a €20bn international tokamak, under construction in Cadarache, France. After it is switched on in 2025, ITER will aim to produce 500MW of fusion power, and answer key plasma physics and technology questions for the fi rst fl eets of commercially viable power stations. Indeed, most of the ITER partners (Europe, the US, Japan, South Korea, China, Russia and India) have ambitious demonstration power plant design programmes.
British innovation In hosting and operating JET together with a network of academic and industrial partners, UKAEA has acquired unique knowledge, experience and capability. In a conscious drive to build on this leading position, the UK government has funded a thriving UKAEA technology programme in areas that are crucial for economically viable future fusion power stations. Key areas include: remote and robotic maintenance; resilient nuclear materials that can withstand the energetic and damaging fusion neutrons; systems to breed, store and recover radioactive tritium fuel; and fusion reactor component testing and validation facilities. With support – including from the UK Engineering and Physical Sciences Research Council (EPSRC) – this programme now comprises a range of new UKAEA facilities that underpin the commercialisation of fusion energy. These include:
The Remote Applications in Challenging Environments (RACE) facility, opened three years ago at Culham and successfully working with UK industry to design and test systems for ITER and beyond to the fi rst power plant.
The Materials Research Facility has also been open for three years, and tests fusion candidate material strength at microscope scale, including after irradiation. A new fuel research centre, H3AT, will open in 2021, to study the breeding, storage and recovery of fusion fuels
Additional new Fusion Technology Facilities will also open at Culham and a new site in Rotherham, Yorkshire. These will work with industry to test, validate and

qualify components and equipment in fusion-relevant conditions.
In addition to this activity, UKAEA also has its own tokamak for studying the viability of fusion at a reduced scale and cost – the Mega Amp Spherical Tokamak, or MAST. Through confi ning the plasma in a much tighter, more spherical shape, MAST has shown a potential route to smaller, cheaper and more effi cient power plant designs. There is a major obstacle to this approach, however: plasma exhaust. Sitting at 150,000,000ºC, a fusion plasma is one of the most intense heat sources on Earth. Finding a way to exhaust the byproducts (such as the helium) and excess heat is essential.
STEP is not only about designing and building an electricity-producing fusion reactor – it is also focused on making sure there are the skills and supply chain required to deliver the reactor to market.
To enable this to happen, the STEP team is a growing partnership that involves national laboratories, institutes, industry and universities, all harnessing their combined capabilities and creating growth opportunities that further strengthen national capability. The development of our supply chain will be increasingly important as we design for manufacture and look to roll out the fi rst fl eet of commercial power stations. STEP
44 energyfocus | www.the-eic.com An upgrade to MAST has just been completed, funded by EPSRC. When the new MAST Upgrade device starts up during 2020, it will test a new exhaust system that is expected to reduce power loading by a factor of 10-20 – potentially solving one of the big challenges for future fusion power stations.
UK steps closer to fusion on the grid An ambitious new programme will give the UK an opportunity to build on all of its knowledge and capability, to design and build a compact prototype fusion power station called Spherical Tokamak for Energy Production (STEP). Following construction by 2040, STEP aims to produce net electricity in the region of 100MW. It is a programme that is packed with adventure, drawing on the combined expertise of UKAEA, the wider fusion industry and academia. UKAEA has been awarded £222m to work with partners to undertake an initial, conceptual STEP design by 2024, fi nally aff ording scientists and engineers the chance to deliver their ultimate goal – to build an electricityproducing fusion power station.
One of fusion’s forefathers – the Russian physicist Lev Artsimovich – once famously said that fusion would be ready ‘when society needs it’. Society needs fusion as soon as possible – and STEP aims to deliver.
By Professor Ian Chapman, CEO, UK Atomic Energy Authority and Head of Culham Centre for Fusion Energy
STEP needs further skills development across both science and engineering during the next fi ve-10 years. There are solid foundations in place via, for example, the EPSRC’s facilitation of co-ordinated training programmes through its Centres for Doctoral Training. These need to be enhanced, and apprenticeship schemes in the nuclear industry expanded, to create a strong fusion education programme that will provide the skills necessary to meet the needs of the STEP programme. For more details on STEP, including procurement opportunities, please visit ccfe.ukaea.uk/research/step
lb/cf

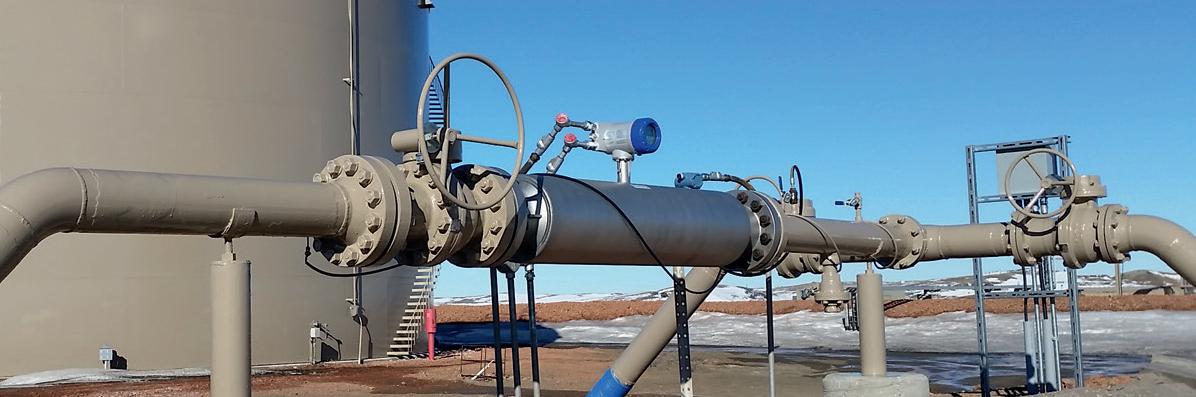
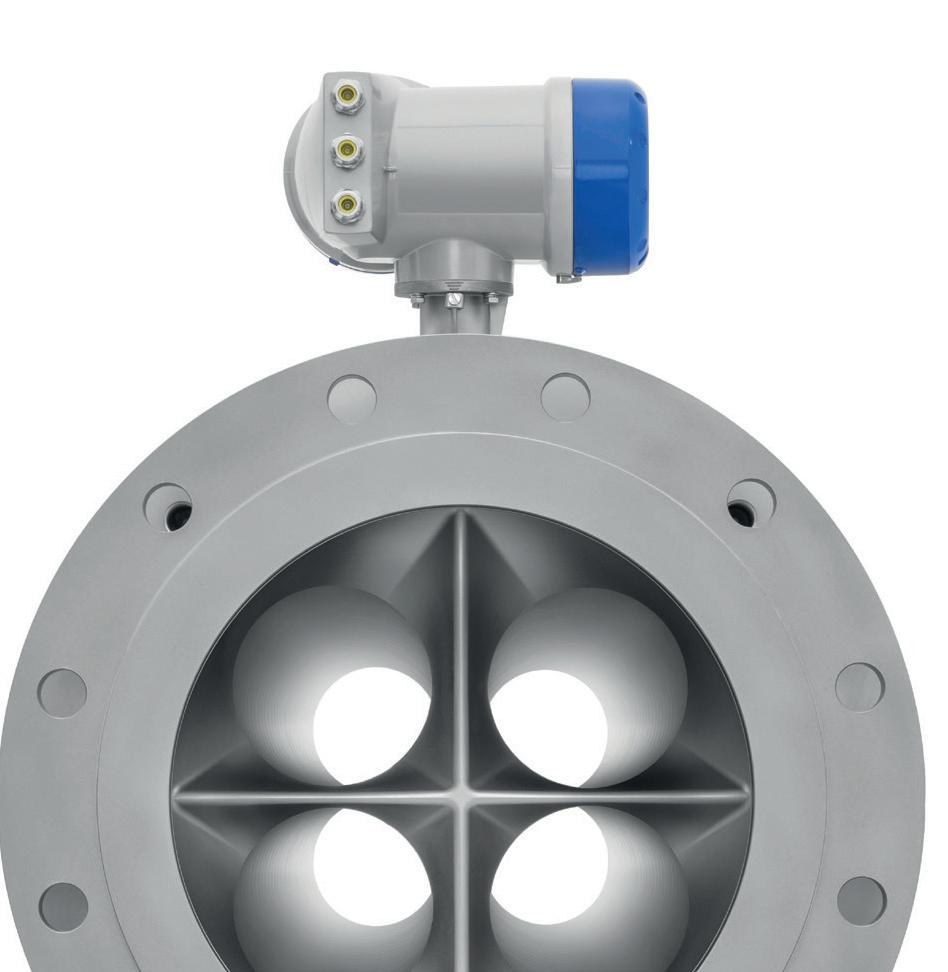


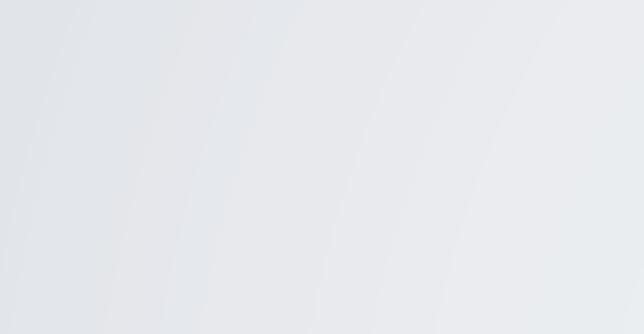
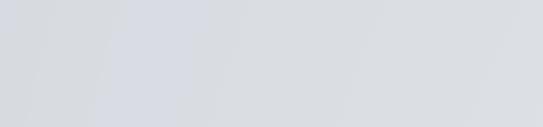


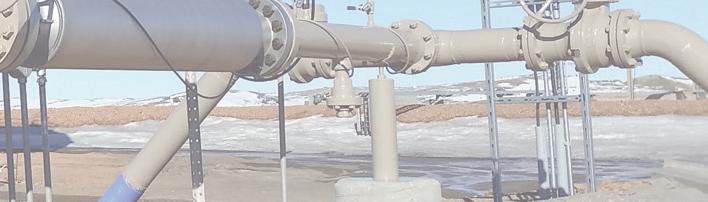

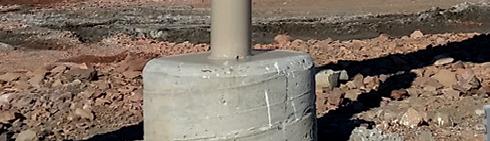
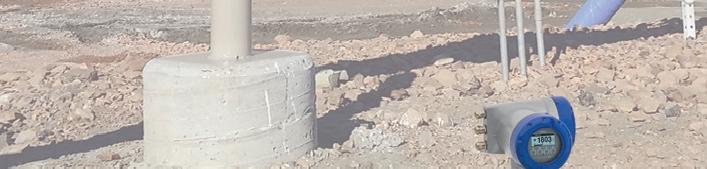



fact
bbl/h
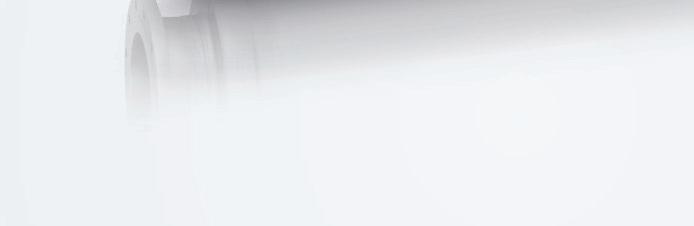

BPD
Highest capacity Coriolis flowmeter on the market
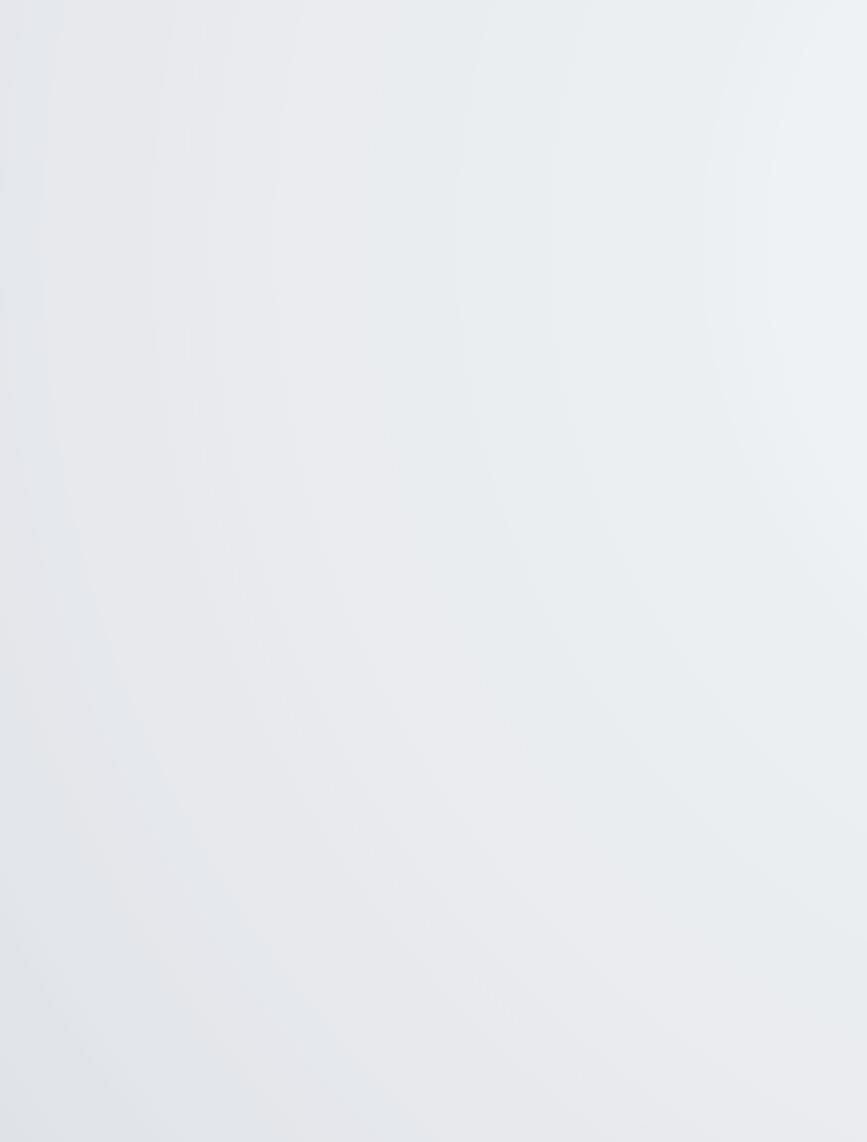
OPTIMASS 2400 – technology driven by KROHNE
• Multiple straight tube Coriolis flowmeter in sizes DN100…400 / 4…16”
• Mass flow measurement up to 4600 t/h MCNJO
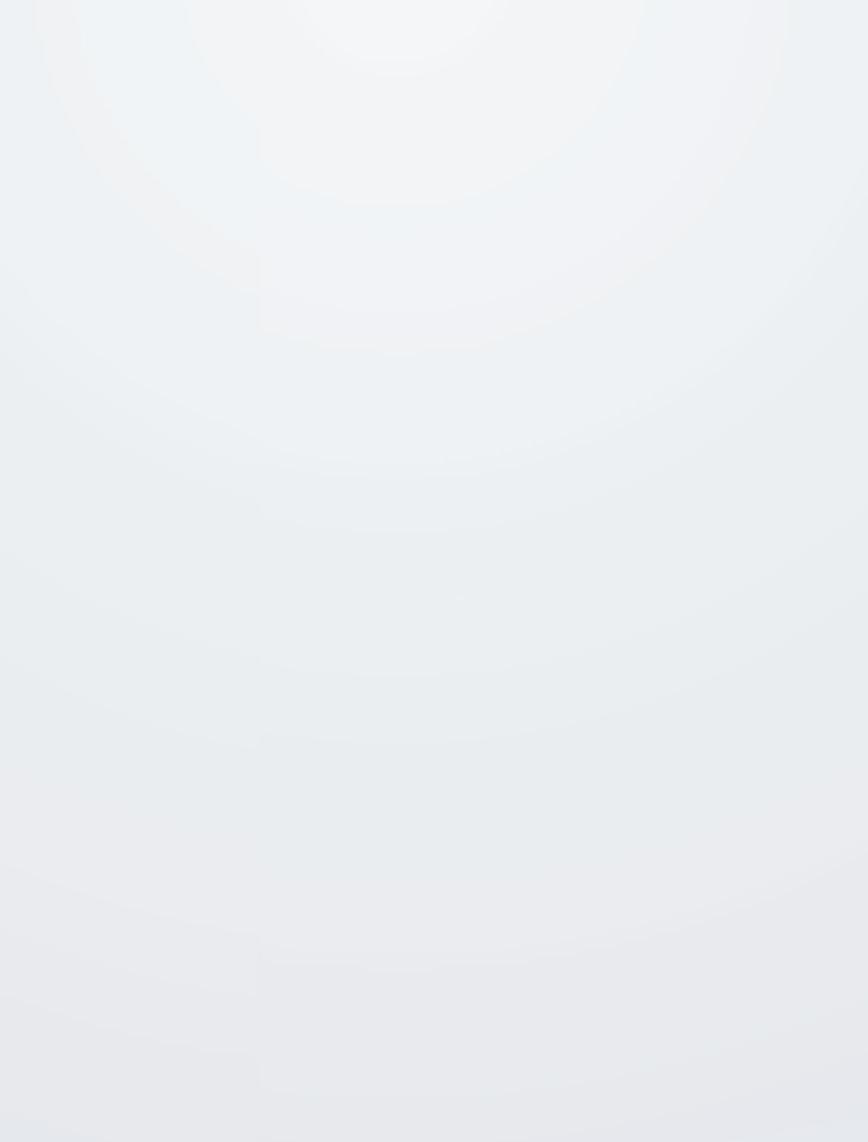
• Entrained Gas Management (EGM TM ): reliable indication of gas entrainments, maintaining operation at all times
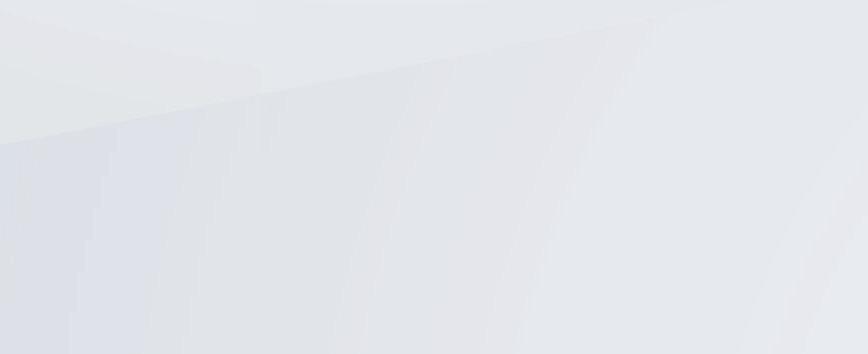

• Highest safety factor with optional pressure rating 180 bar / 2,610 psi, PED approved secondary containment up to 150 bar / 2,175 psi • NACE compliant with Duplex or Super Duplex as wetted material • ATEX, IECEx, CSA, FM, NEPSI, MID, OIML, API & AGA compliant

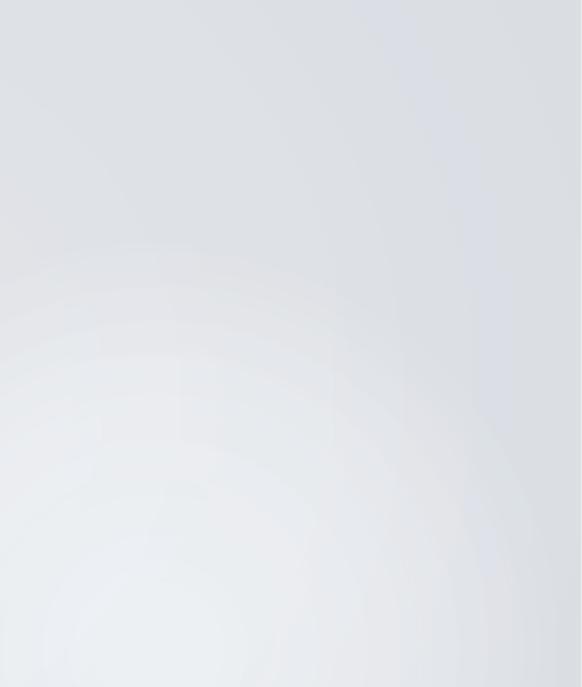
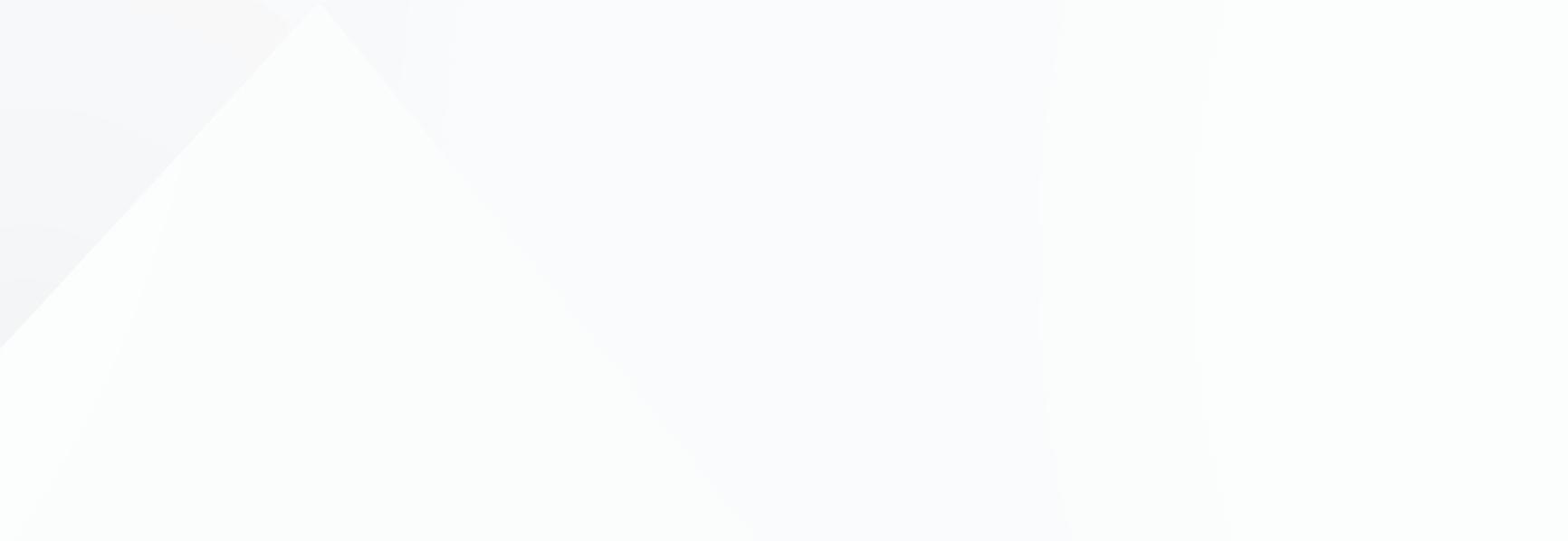
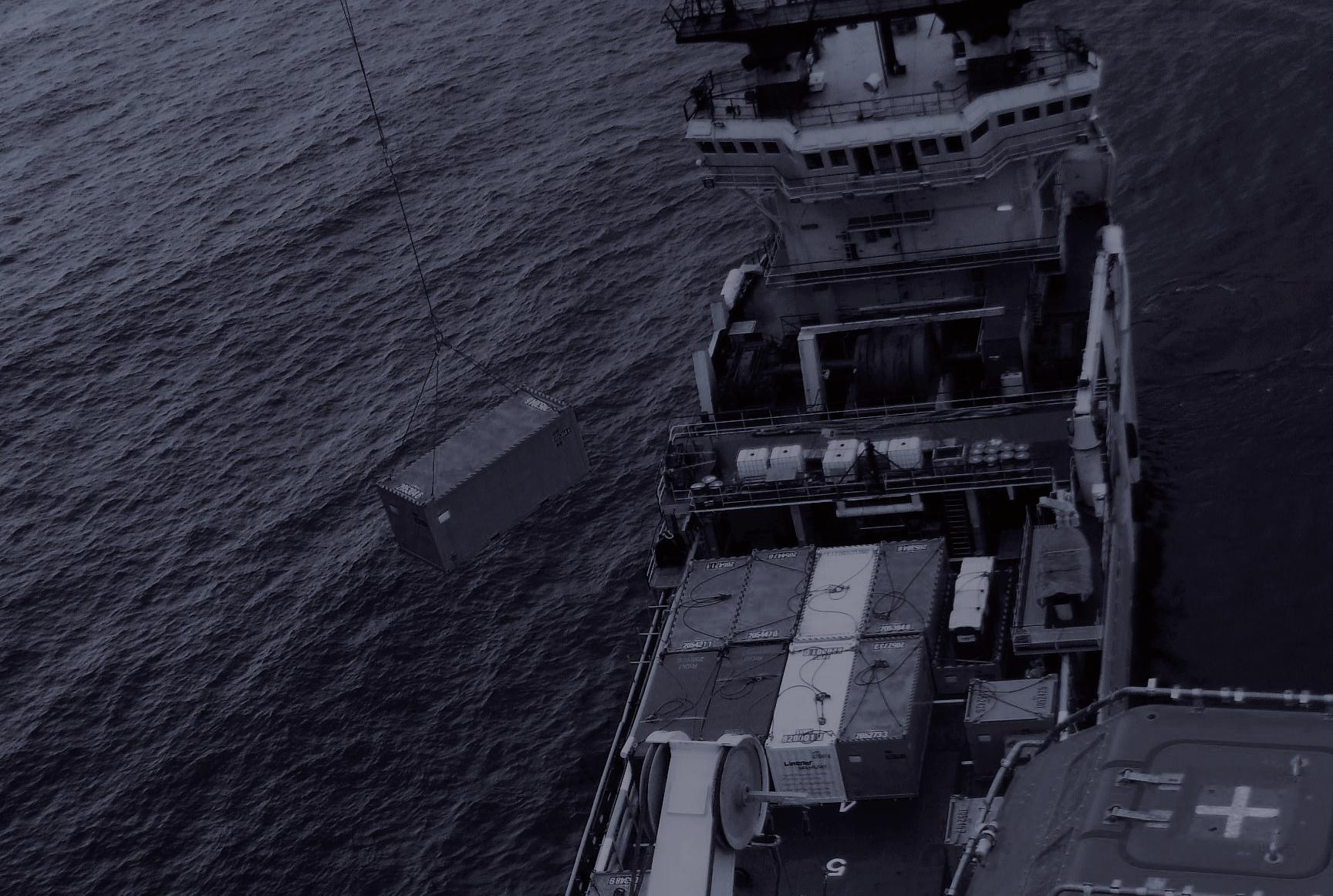





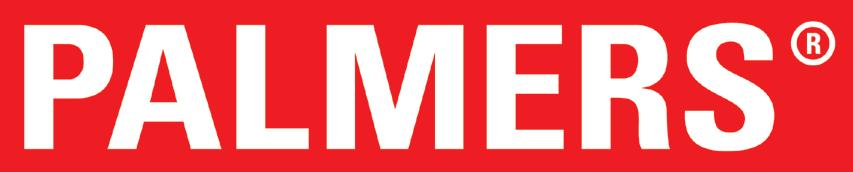
Palmers Scaffolding UK Ltd. is one of the industry’s leading access, scaffolding and related industrial services providers. Since 1880, our people have made a difference using their skill, experience and dedication – providing creative solutions to the most complex issues of our clients.
We offer bespoke scaffolding & special access solutions for the following industries:


■ Petrochemical ■ Power Generation ■ Construction ■ Steel Manufacture ■ Rail ■ Airports Infrastructure ■ Industrial ■ Marine

Palmers Scaffolding UK Ltd. // 331 Charles Street, Glasgow, G21 2QA, UK // P +44 141 553 4040 // F +44 141 552 6463 // info@palmersgroup.co.uk // palmersgroup.co.uk