
9 minute read
What does it take to
Q&A: Svein Vatland Energy Focus talks with Svein Vatland, Vice President of Subsea Technology Programmes at ABB
How did the Subsea Power Joint Industry Project start? In 2011, ABB was awarded a contract from Equinor to provide power for the world’s fi rst subsea compression system to Asgard gas fi eld. In the absence of any power distribution on the seabed, each compressor initially had a cable tied back to the fl oating facility. This issue was subsequently addressed and all process equipment is now located on the seabed, powered by a singular cable with modular power distribution. In 2013, ABB, Equinor, Chevron and Total formed a JIP to develop this concept further, with a power solution for transmission and distribution of electrical power up to 100MW, over a distance up to 600km and to depths of up to 3,000m for 30 years. It targets greater recovery rates, reduced production costs and further development of deep-water production. Power will be supplied with a single cable, instead of one for each load. All equipment for medium voltage distribution, power conversion, automation and auxiliary power will be fi tted in subsea enclosures. A modular power distribution system on the seafl oor will drive pumps, compressors and other process plants.
What does it take to build a subsea power station?
How does the technology work? Subsea power technology and rocket science share similarities – both work in conditions for which fi xing anything is very diffi cult once the technology is installed. While satellites can get the small amounts of power they need from attached solar panels, the pumps and compressors located on the seafl oor require vast amounts of power and have to be plugged into a source of electricity.
The technology works the same way, in principle, as similar equipment on a topside or onshore. The diff erence is the harsh working conditions that the equipment is exposed to. The equipment is fi lled with oil and pressurised on the inside to compensate for the outside pressure from the water. Further, there is a lot of built-in redundancy to make the equipment extremely reliable. You would not do this to equipment situated in a location that is easily accessible.
While the control system is based on existing products, the technology had to be signifi cantly upgraded and modifi ed. The system also needed a completely new enclosure design. Though there are already subsea electronic modules for well-control applications, the control system designed will off er more advanced functionality, compared to existing solutions. The system is much more powerful than any state-of-the-art system used for subsea today.
How challenging was it to produce and maintain transmission and distribution of electrical power subsea? This has been a very challenging project – operational conditions are extremely harsh and reliability requirements are precise for pressure. The equipment needs to be able to operate at 3,000m water depth, which imposes a pressure on the equipment of 300 bar. Therefore, all the developed units are pressure compensated. As already mentioned, the units are oil-fi lled and pressurised from the inside to compensate for the pressure from the surrounding water– so all the electronics that go into the units must be able to operate in oil under extremely high pressures.

The equipment is designed for a 30-year lifetime. All the components need to be extremely reliable. A signifi cant challenge has been to capture the precise conditions that would lead to a test deviation, a change in device behaviour or component value, particularly when these deviations were intermittent and only apparent under the harshest of test conditions. This work was often carried out in specialist test facilities.
What role has rigorous
testing played during the past few years? With several hundred unique critical components and various stress conditions, a clear but pragmatic testing structure was required and devised to learn the behaviours and limits of diff erent designs. This helped mitigate the risk of failure before prequalifying for full-scale prototypes.
Starting with simulation and laboratory tests, materials, components, subassemblies and assemblies were all subjected to realistic stress levels in accordance with lifecycle profi les before the fi nal full-system shallow water test.
All tests were carried out in adherence to API17F Standard for Subsea Production Control Systems. Tests included temperature, vibration, pressure and accelerated lifetime. In 2019, the subsea power distribution system was brought together for the fi nal 3,000-hour shallow seawater test in a sheltered harbour. At the time of writing, the full power cell has been operating over more than 5,000 hours under pressure. All components, including the optical fi bres and their connectors, have performed fl awlessly.
Are autonomous subsea facilities powered by lower-carbon energy more likely to become a reality? Absolutely. Today, power supply and oil and gas processing power are based on installations on fi xed platforms or fl oaters. This topside set-up impacts the environment. The solution we have developed will enable more energy effi cient oil and gas production with fewer emissions. Our power distribution and conversion system are purely electrical, so there are lower overall CO2 emissions. Electrifi cation helps to increase system availability and control, and reduces component size and cost and environmental footprints, especially in deeper waters. As it is unmanned and remotely operated, humans are removed from a high-risk environment. The potential savings are considerable. For example, with eight diff erent loads, such as pumps or compressors, CAPEX savings could be about US$500m. Effi ciency will be signifi cantly improved, as the loads are closer to the well.
How will distributing electricity underwater revolutionise the way we live and work? The vision is for a subsea facility: using
digital solutions to enable intelligent remote and unmanned operations. This would further reduce CAPEX and OPEX, while increasing recovery rates, improving safety, enhancing reliability, raising productivity and minimising environmental impact. Using this concept, practically all the world’s known oil and gas resources can be reached. However, this is only the beginning. With 75% of the world’s surface under water, we believe not only in the power that electrifi cation can bring to the off shore industry, but also in the potential it could off er far beyond oil and gas.
How possible is it for the
technology to synchronise with renewable energy resources? Connecting hydro, wind or solar power to maintenance-free subsea transformer stations both on and off shore is very much the plan and increases project viability. Studies with our partners show this approach could reduce costs by 30–40% in water depths deeper than 60–70m, and even more in water depths beyond 100m. Less steel is needed, and subsea cooling is provided for free by the surrounding seawater.
We have a track record of delivering off shore substations to off shore wind farms. Now, with our subsea power distribution technology, we can deliver a visionary step-change with seabed-based substations for fl oating off shore wind farms. These new wind parks could also support next-generation, entirely unmanned, entirely subsea off shore oil and gas production facilities with 80–110MW of power, via a single cable, using ABB’s modular and scalable subsea power distribution solutions. Any excess power can still be exported to market, using the same system, and any future new power sources can easily be added and used by off shore power users.
Operators would be able to reduce cable requirements, especially dynamic export cable requirements, which are a costly element. They would also reduce their maintenance needs and environmental footprint, waste less energy in transmission, reduce human exposure to risk, and reduce emissions. Today, equipment ranging from multi-megawatt seafl oor compressors to subsea resident vehicles or off shore fi sh farm operations can tap into this new power source.
How critical was the collaborative eff ort of the joint project between ABB and its partners? It has been a great asset to have continuous close collaboration with our partners. This means that we have had access to a vast base

of domain expertise and experience, where new ideas quickly can get a reality check. To develop the technology in close collaboration with leading energy companies such as Equinor, Total and Chevron has been pivotal for a successful outcome, to ensure that the technology is fi t for purpose. We have also maximised our expertise and knowledge in-house, with colleagues across ABB collaborating across teams and countries to innovate and advance our research and development eff orts. More than 200 expert ABB engineers, physicists and chemists in test facilities and research centres around the world have been involved in developing this next-generation technology for subsea power.
What’s the ultimate goal?
The ultimate goal is to do as much subsea oil and gas production and power generation as possible. This can lead to unmanned production facilities operated from shore and avoid transporting people and goods (by helicopter and boat), keeping people safe on shore.
The potential reach of ABB’s subsea power technology is vast, across regions and countries covering anywhere with extreme long step out distance and subsea tiebacks for existing facilities.
Our subsea power distribution system can and will have a major impact on how oil and gas production will be done in the future. Subsea power is a key enabler for the ultimate vision of a subsea facility. As a digital technology leader, we are excited and honored to be contributing to today’s energy transition for tomorrow’s world.
Continuing to invest in EIC members
DATABASES
2014
1X CAPEX - EICDATASTREAM

2020
3X CAPEX, OPEX AND SUPPLY CHAIN EICDATASTREAM, EICASSETMAP AND EICSUPPLYMAP
EICSupplyMap is our brand new, members only, database that tracks UK supply chain companies and their capabilities
NATIONAL AWARDS DINNER
2014 0 AWARDS
8
INSPIRING GROWTH CATEGORY AWARDS
12020
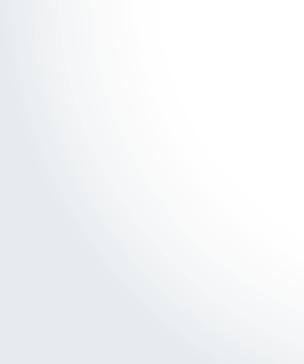
1
COMPANY OF THE YEAR AWARD EIC-RGU RISING STAR MBA AWARD
MARKET RESEARCH TEAM
...LOCATED IN EIC’S WORLDWIDE OFFICES
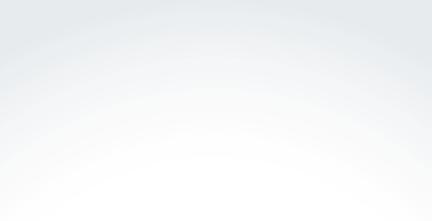
ANALYSTS 12
ANALYSTS 22
2014 2020
77 years 700 members 130 events per year 12 UK pavilions 10 overseas delegations 7 global offi ces
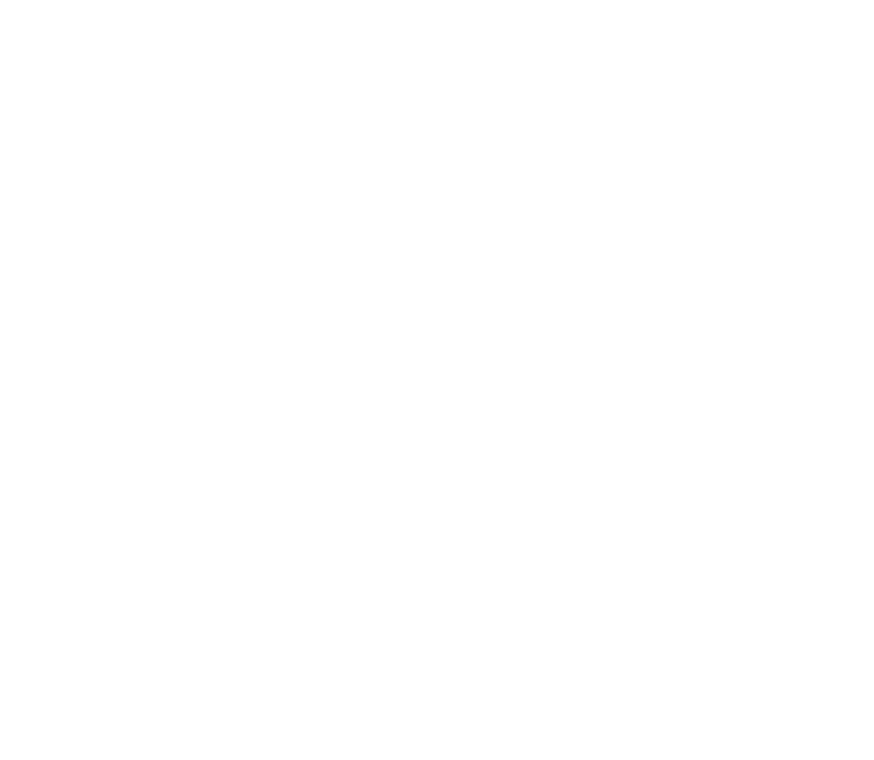
MEMBERSHIP CATEGORIES
2014
2
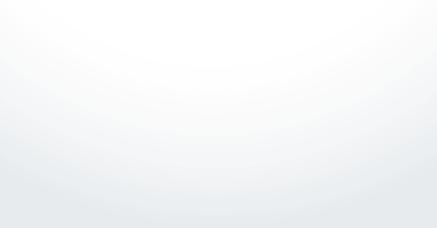
categories of Primary or Global
2020
categories to match your business needs, including Global, 3x Primary, 5x Local, Renewable and Operator 11
INSIGHT REPORTS
2014
SECTOR REPORTS PRODUCED 3
2020
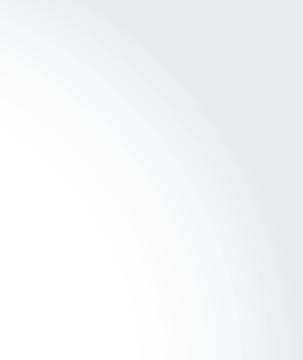
SECTOR AND COUNTRY REPORTS PRODUCED 14
Including CCUS, downstream, energy from waste, LNG, Mexico, Norway, off shore wind, OPEX reviews, Saudi Arabia, Survive and thrive and upstream decommissioning
FLAGSHIP CONFERENCES
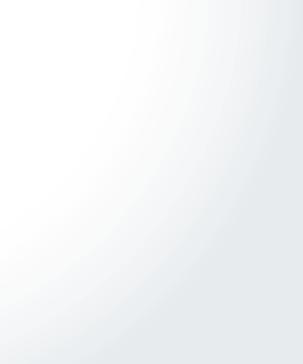
Energy Exports Conference and EIC Connect run in Bahrain, Benelux, Brazil, China, Indonesia, Mexico, Saudi Arabia, UK and US - each is the largest supply chain energy event connecting you with project opportunities and key contacts EVENTS 11 2020 ...in the UK & UAE EVENTS 2 2014