
11 minute read
Busted Knuckle
Matt Myrick, left, joins Jake Burkey in his Busted Knuckle crawler at the King of the Hammers races in California.
Busted
Advertisement
Knuckle
A common love and a common ‘drive’ led two young men into a unique business
Story and photos By David Moore
Three factors bond Matt Myrick and Jake Burkey.
Both love driving extreme off-road buggies and challenging ridiculously steep rocks and hills.
Both love building these wild machines.
And both love it that they quit “normal” jobs to make a living doing something they truly love – owning and running Busted Knuckle Off Road. They’re in their fourth year as partners in the growing company located at a shop atop the hill four miles southwest of Dodge City on Ala. 69. Jake does design and engineering. Matt handles marketing, the gear they sell and films.
They fabricate and build limited-production off-road buggies (think Polaris RZRs on mega-steroids) that are basically large, precision-engineered roll cages riding on 43-inch tires driven by a 376 Corvette engine that gallops with 530 horses.
Sound wild? Wait until you rip up and down outrageous mountain trails and climb ridiculously steep rocks, or race one across the desert.
You can get a “roller” and finish it out yourself for around $20,000. But want a really wild ride? Matt, Jake and their team of 13 quality-driven employees will build you an extreme Busted
Matt Myrick and his Busted Knuckle buggy climb through a deep, muddy creek bed, showing the wide range of flexibility designed into these extreme off road machines.
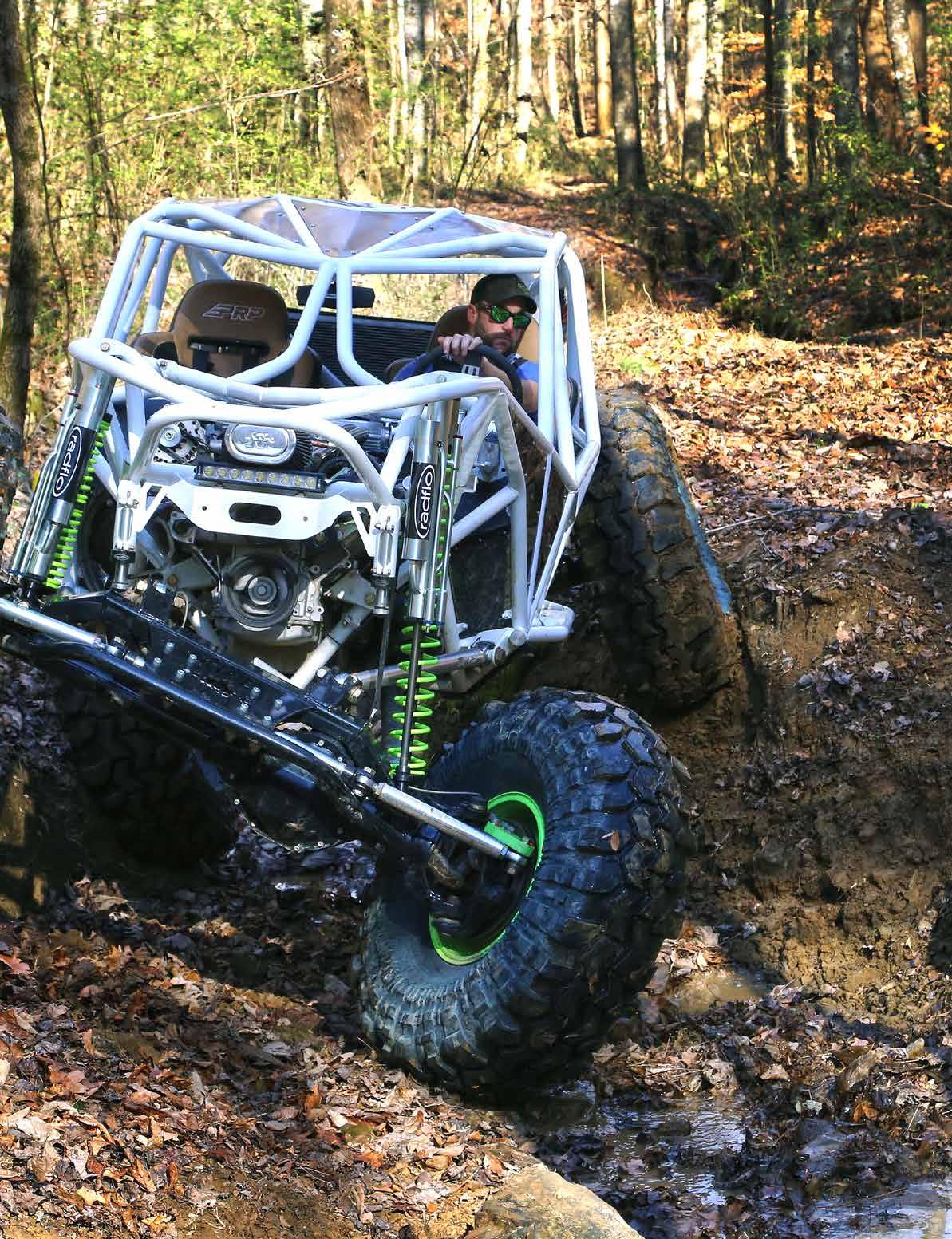
Knuckle bouncer with a 427 super-charged LS engine that churns out 1,000 hp. They start at about $85,000, turn-key and ready to rock with a one-year warranty.
“Most of our buggies come in about $100,000,” says Matt, referring to the addition of options such as heated seats, larger shocks, rear steering, rock lights underneath the chassis or perhaps a nightvision back-up camera. One enthusiastic customer maxed out with “the baddest of the bad,” buying a $135,000 buggy that included – because he wanted it – a $1,000 siren.
“We’re the Ferrari of off road,” Jake says. “That could be a slogan for us.”
Actually, a fourth factor bonds them: both are sticklers for excellence and aren’t afraid to work.
Matt and Jake have been off road – literally, if not figuratively – since they were kids.
Matt graduated from Sparkman High in Huntsville and went to Auburn University to study construction management and business/marketing as a minor. While there, he bought a Sony Discman Handycam.
“I had been off road since I was 13 or younger, riding four-wheelers and everything you could imagine,” he says. “I started filming folks while we were out riding and made a DVD just for fun. People started asking me for copies of it. That’s how my business was born.”
That was in 2007, and he named the business Busted Knuckle Films. (Today, it’s the marketing arm of Busted Knuckle Off Road.)
Graduating in 2008, he continued living in Auburn while working as project engineer at a major development at Fort Benning, Georgia. Weekends were his to travel to offroad events and races … so his and Jake’s paths were almost gunning to cross.
Hailing from Columbia, Tenn., and driven by the drive to tinker, Jake graduated in 2008 from Tennessee Tech University, his degree in mechanical engineering.
“Ever since I was a kid that’s all I ever did – tinker, build off-road buggies. That’s just kind of my thing,” Jake says.
He got a job as a project manager at Alvin W. Vogtle Electric Generating Plant and actually lived in a two-bay storage unit he converted into a one-bedroom apartment. That rather extreme step allowed him to immerse himself in his extreme hobby of modifying, building, riding and later racing extreme rock bouncers and off-road buggies.
“I bought a chassis and finished it out,” he says. “I tweaked it and learned how things should be built.”
It would prove to be a great thing to know … as would knowing Matt.
Looking back, Matt and Jake realize their paths crossed at several off-road events, such as River Rock in Georgia, and Golden Mountain Park in Tennessee. Though they didn’t know or meet each other, they later recalled common incidents.
Golden Mountain stands out for what happened there in the 2011 Dixie Run.
Jake, driving a Jeep he modified and reinforced, and a friend riding shotgun, made a run at Bounty Hill. The trail is a wide, slab boulder jutting up about 12 feet at a 60-degree angle; there it breaks onto
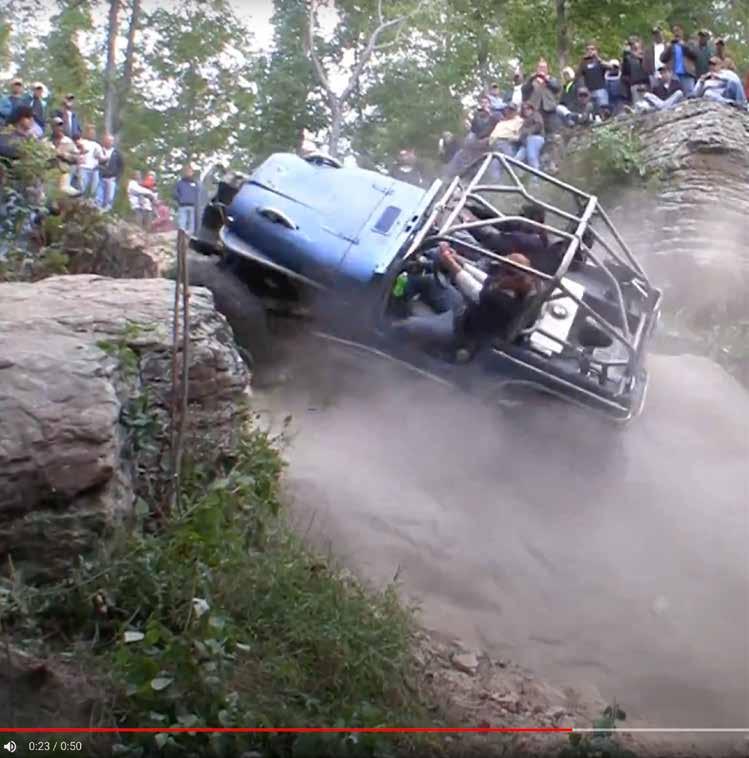
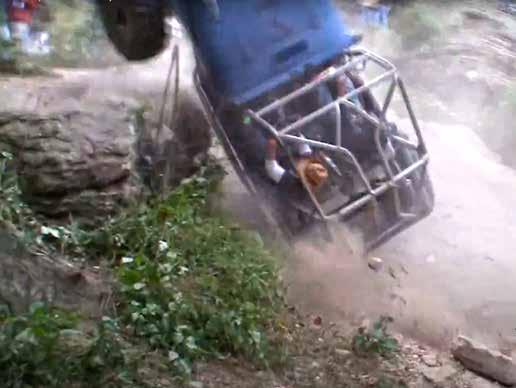
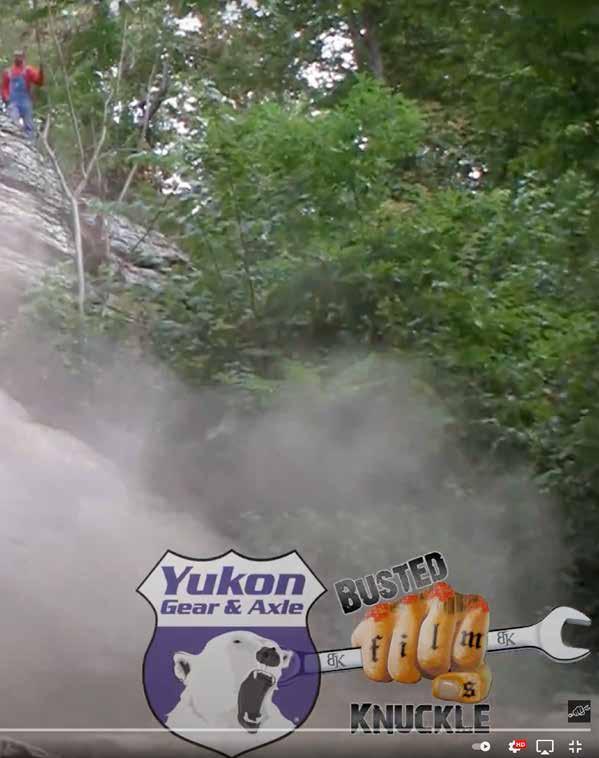
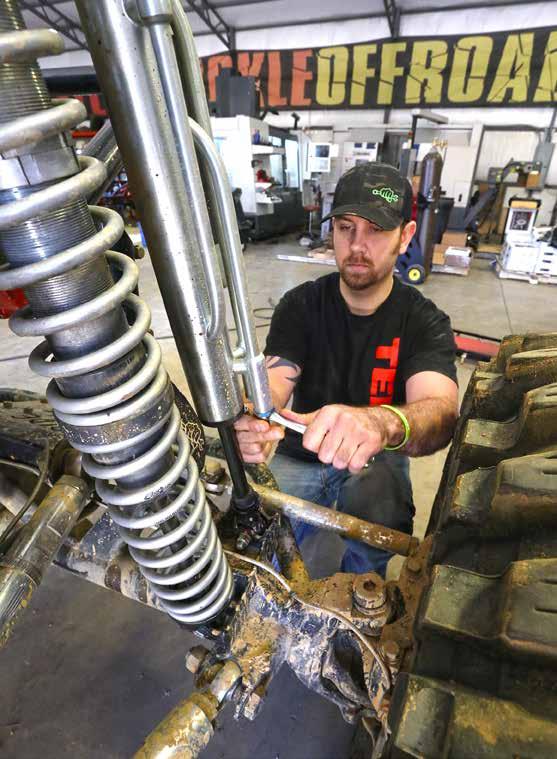
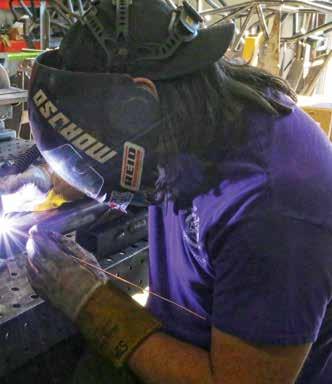
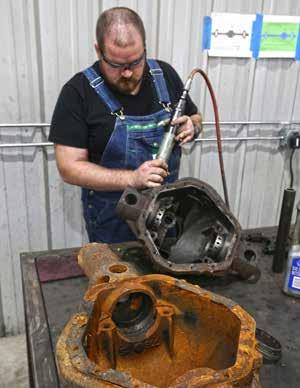
Jake Burkey, upper and lower left, vertically rolls his old Jeep crawler on an extreme climb in 2011. His now business partner, Matt Myrick recorded the stunning spectacle and posted it to Youtube, from which these screen grabs came. Above, Jake, the company’s design engineer, fine tunes the front suspension on his Busted Knuckle rock crawler at their assembly shop west of Dodge City. The crawlers, or buggies, are designed and built tough, the latter a factor of their dedicated and knowledgeable team of 13 employees. Center left, Austin Moore welds a stainless steel driveshaft. Left, Russell Meeks, stripping an axle housing, says he’s not been challenged so much by any job in ages.
a narrow shelf before climbing another 12 rugged feet or more. Calling this a trail takes a lot of imagination, even for a rock crawler.
At the base of the hill, Jake guns his Jeep. It lunges up the slab, landing with the front tires on the shelf. He’s still gunning it as they careen crazily left. Onlookers scatter as the Jeep bounces further left before flipping over backward, downhill, onto its rollbars. As designed, the Jeep rolls all the way over on its side in clouds of dust before finally landing upright on all fours.
Onlookers cheer and clap. Jake throws up his arms: touchdown. Amazingly, in addition to Jake, his rider and onlookers are unharmed, and Jake’s Mountain Dew bottle remains unspilt in its dashboard holder.
This whole time, Matt is mere feet away, filming the entire escapade. They met and talked briefly at the time. Matt was, seemingly, just another photographer to Jake, but that would change.
A few months later, at Hooters in Augusta, Jake was fortunate that he didn’t choke on a wing or a beer when he glanced at a large-screen television on the wall – and saw himself.
“I’m sitting there, and this clip comes up, and it’s me flipping over,” Jake laughs. “That was wild.”
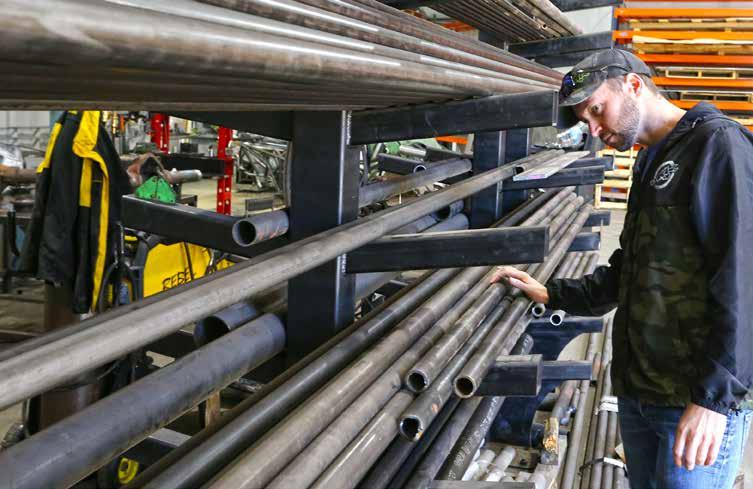
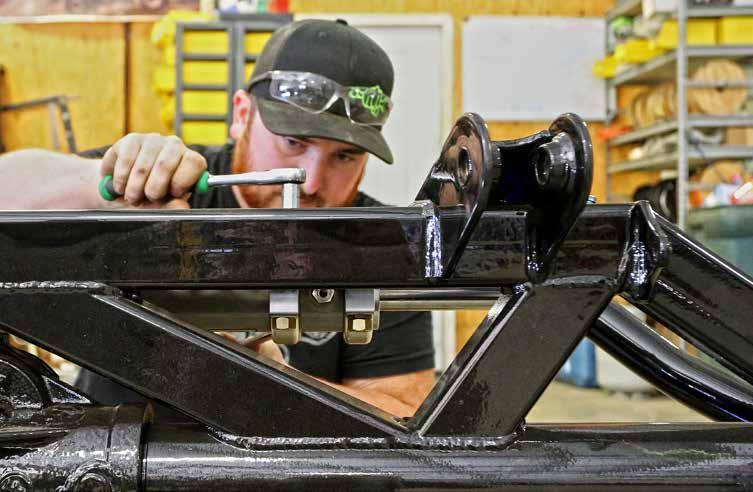
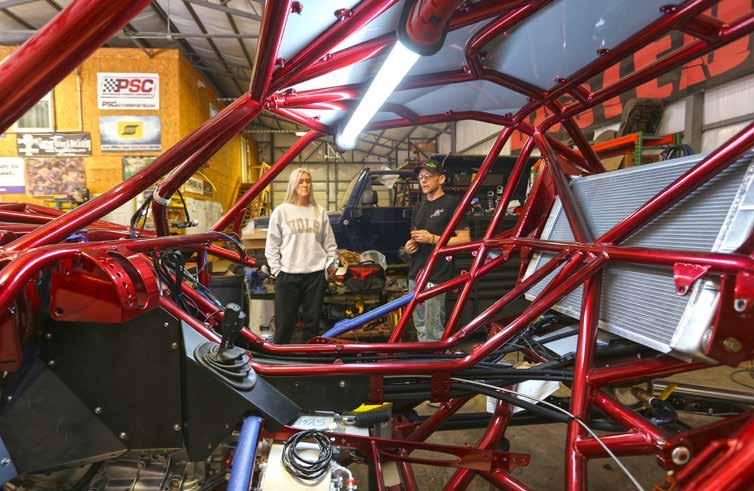
Matt had sold the rollover and other clips from YouTube to a TV show called “Dumbest Stuff on Wheels.”
“What’s crazy,” Matt laughs, “is that after he flipped, Jake went right back to try that hill again, only this time they wore helmets.”
What’s not crazy is seeing how Matt’s work impressed Jake. After that, he communicated more and more with Matt.
At that time, Matt lived in a house he’d built on the Jasper side of Smith Lake.
Loving the off road and filming, and fed up with clock-punching at Fort Benning, Matt quit his job in 2011.
What finally led to his quitting his old job was a visit to California to shoot a huge event known as King of the Hammers. It has developed into multiple days of offroading, including a 14-hour event covering 165 miles where custom fabricated and souped-up racers fly at 100+ miles per hour across deserts and gear way down to conquer extreme rock crawling sections. The races draw 50,000 spectators and serious money machines.
“I saw how big the off road sports industry is,” Matt says. “If there was a time to get into it, this was it.”
So Matt quit his job and began using his four-wheeler to chase racers and rock riders, capitalizing on his knowledge of business and marketing to live off his camera craft.
As for Jake, by 2013 he was off-road racing, far more costly than just wild rides and events. In addition to his “real” job near Augusta, he sold off-road parts online through www.burkeyracing.com.
Besides the states, racing took him to Puerto Rico, Italy, Spain and Portugal.
Matt Myrick, top, looks over some of the steel tubing Busted Knuckle uses to construct its wild machines. Center, Brendan Trump mounts a hydraulic steering ram to a front axle. Below, Jasmine Davidson, Jake’s girlfriend who’s in charge of shipping orders, talks with Mick Walker, who fits on body pieces, does wiring and oversees some of the quality control. Each piece of the chassis and roll-cage body has to be precisely bent and welded. BK also sells many of the specialty parts it manufactures at the plant.
He often met up with Matt who was “working” the races. Other participants wouldn’t dare go trail-riding before a race, but Jake would, and Matt would join him in his own bouncer.
“We would trail ride until 2 am the day of the race,” Matt says. “Jake would break something, and we’d stay up and fix it so he could race.”
“Sometimes we would fix it,” Jake shrugs, “sometimes we couldn’t.”
Ever the engineer, Jake began tinkering with his own racer designs.
“I took my knowledge from racing and made sketches on paper,” he says. “I was actually able to make a racing buggy using a CAD (computerassisted design) program.”
Meanwhile, Matt, had moved to the Cold Springs area on Cullman County’s side of Smith Lake. He delighted in teasing Jake about having a regular job as opposed to, say, them starting their own business.
“I’d send him a picture of me wakeboarding on a Wednesday afternoon and say, ‘Hey Jake, what’s going on? You quit your job yet?’”
“It took me about four years to get up the courage to do it,” Jake says. “Those last two years, I hated work. I knew I was leaving. I just couldn’t take it anymore.”
So in 2017 he left the nuclear power plant, moved to Cullman County and went into business with Matt. They sold their buggies for capital.
Initially, they planned to sell parts online and, with Jake now known as an off-road sports guru, they’d also make tech videos and capitalize on his abilities and status.
After Matt moved to Cullman County, his parents, Larry and Teresa Myrick, relocated here. It was Larry who spotted a shop for rent on a big hill between Dodge City and Stony Lonesome OHV Park. At the time, Stony Lonesome still hosted off-road buggy races, so the location was perfect and not only had room to stock parts but to build buggies as well. And that was a good thing.
Right after Jake quit his job, he was contacted by an Italian racer who said forget the price, just build him a high-quality, extreme buggy. Not really interested, Jake quoted him a price of $180,000, hoping to scare off the guy. It didn’t work.
So, with two guys they hired, plus Jasmine Davison, Jake’s girlfriend who moved with him from Augusta, they custom fabricated the buggy in their shop. It took nine months to build the main components, which they took to Italy for final assembly.
Still selling parts, both their own brand and others, the next year Busted Knuckle produced two custom buggies, one with an attention grabbing 1,600 hp engine. But custom builds were not what they needed to do.
“The R&D is very expensive for a onetime shot,” said research and development
designer Jake. “Every single part of those buggies, I had to have my hands on it.” “There was no way for us to grow if Jake had to have his hands on every single part of a build,” Matt says. They decided instead to offer various options on several limitedproduction models. By 2021, their second year of taking production buggy orders, Busted Knuckle rolled out 10 of the quality-built extreme machines. They’d also built a large extension onto the shop, and their employment had grown to 15. “Manufacturing has taken us to another level,” says Matt, who churns out a lot of promotional videos and built a following of 2.5 million on For trial runs and test drives, Busted Knuckle incorporates trails through their Facebook page the woods and up and down the small but steep mountainside behind alone. “People see our the shop. In this photo, Matt guns his still new rock crawler up the vehicles. If they can’t mountain, bound for the sun and other great things. afford the buggy, they want our R-and-D-ed parts for their own machine.” Busted Knuckle’s gross on buggies was only 5 percent of its total gross last year, he adds. That’s because it takes three months to produce a turnkey buggy, and on a given day they might sell two $15,000 axles they fabricated in-house.
By mid-January, Busted Knuckle already had six turnkey orders lined up, and demand for parts is strong. Those dream machines and parts are going to some of the growing number of enthusiasts who love extreme off road sports. “We want someone to have the best time they can off-roading,” says Matt. “We want to see the sport grow. It was probably a dream,” he adds of the business. “But never did I dream this would be the reality.” “If we had full-time jobs, we’d be doing this for fun,” Jake grins. “Now we’re doing that same thing, just making money doing it.” Good Life Magazine
