
4 minute read
Billingham Construction
TOWNHOUSES IN CLARKSON Family Dream
Photos Andrew Pritchard / Gary Boulos
Advertisement
First Major Project in Perth after Life-Changing Move from the UK
Lee and Louise Billingham were seemingly destined to end up in the Western Australia building industry. After Louise graduated from university in the UK with an honours degree in business, she and Lee – a carpenter since his teens and at the time a construction site manager – headed off to backpack around the world.
Their travels took them to Perth, to visit family, and they immediately realised they would love to live in Western Australia.
Nevertheless, for the time being, they returned home to Manchester and started their own commercial joinery business. While Lee managed the company, Louise worked in the sales industry as a regional account manager. “We have both always been driven,” notes Louise. “The rest is history, as they say!”
That history, eight years ago, finally brought them back to Perth, specifically Mindarie, where Lee studied and became a registered builder and the couple set up Billingham Construction.
“Many years ago it was Lee's dream to build houses,” recalls Louise, “but we never thought it would come to fruition. Lee is very creative, patient and hands-on with all of his jobs, which is in his nature. He nurtures the jobs to completion – he just can't help himself. Clients get to know and deal with us both on a personal level.” Louise’s own role within Billingham Construction is operations manager. “I do everything, other than build on site.”
Professional Milestone At first, Billingham Construction focused on private builds, as well as renovations, extensions and granny flats in Perth, all of which they continue to work on for their growing portfolio of clients. Then last year they secured the commission for their first multiple housing project: 11 double-storey townhouses in Clarkson.
The day they were offered the contract remains delightedly etched in their memories, and they are especially proud of their achievement in building the first detached, three-bedroom, double-garage home in 16 weeks. Furthermore, before this show house was completed, eight of the 11 homes had been sold for the client.
THE TEAM

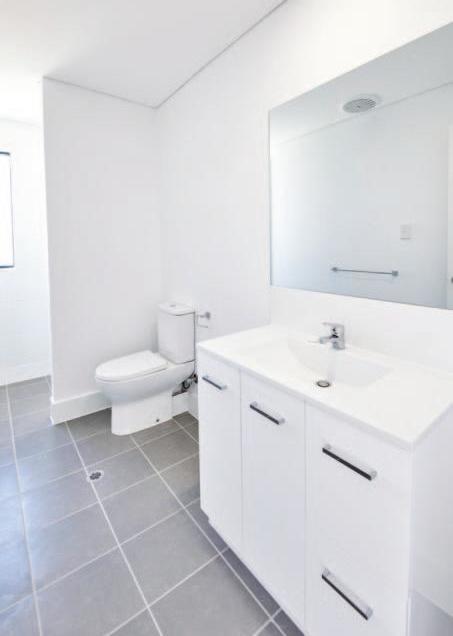
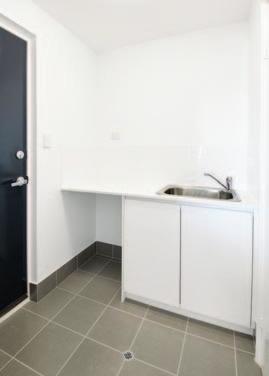

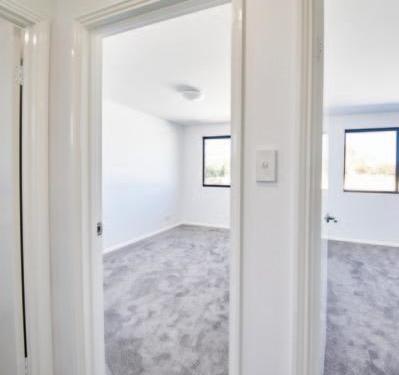
The whole townhouse project, which is part of a mixed-use development in the area, is due to be completed in 12 months subject to weather. It has generated employment for more than 40 sub-contractors, and Billingham Construction has worked mostly with local contractors and suppliers. The quick building turnaround also benefits the new owners, ensuring lower rental costs while waiting for their homes to be built, as well as resulting in minimal interest payments for investors.
Quality Homes for Affordable Living Billingham Construction had worked alongside Straight Edge Steel Framed Homes (Scott Elsley) and Smart Steel for several years on different projects. They were approached by Scott to collaborate on the Clarkson project, with the objective of providing affordable living.
To that end, according to Lee Billingham, one of the main priorities was to use the land efficiently – hence the double-storey layout.
As there was a 30-millimetre clearance between the adjoining walls of each property, accuracy in the building works was paramount. Double-cavity brick works were used on the ground floor, for ease of construction; while steel-framed walls and steel joist steel truss systems were used for the upper floor construction.
“Steel is strong, durable and lightweight,” explains Lee. “It doesn't twist, shrink, rot or warp over time, and termites can't eat it! It's quick to install, it won't catch fire and it has versatility within it's design. The Truecore (Bluescope) steel we use has a high strength-to-weight ratio and is precisely engineered, thus ensuring walls are straight and true. Floor space gains can be achieved by using steel, combined with external cladding construction. It arrives on site pre-fabricated, and we saved valuable time with the quick installation.”
Steel is also ideal for environmentally-conscious clients, as it avoids the use of insecticide (unless specified by NCC), minimises waste material and enhances thermal values.
One of the main challenges was dealing with the rocky limestone ground. Even though the land was prepared by a civils company beforehand, a lot of the limestone rock had not been removed, so Billingham Construction had to finish that task before completing all the foundation works.
“Wild winter weather has had an impact,” says Lee, “but we have remained focused on and mindful of our time frames and our capabilities.”
There have also been some complications sourcing materials. “With the current housing/building boom in Western Australia due to a buoyant economy and government building grants, there's demand for materials from other builders, which leads to manufacturing delays in getting them to site. This has not affected us, as we have been pro-active ordering materials, so our program of works remains on track.”
Away from the building site, another challenge faced by the Billinghams – and many other people working in the industry – is ensuring the right family balance is maintained. Billingham Construction is a solidly family-run business, and Lee and Louise have four young children. ”Juggling family life and a successful business model takes organisation,” says Louise. Happily for the Billinghams, that life is now in the new land of their dreams.