
7 minute read
Tech-Driven transformation - South West's housebuilding and infrastructure revolution
Join Construction Worx roving reporter, Peter Haddock, as he embarks on a journey through the South West, exploring the groundbreaking advancements brought about by Leica technology in the realms of housebuilding and infrastructure.
From Devon to Cornwall, the last four years have seen earthworks contractors in high demand for housing, holiday homes and the infrastructure needed to support them. Fast forward to today, and contractors large and small are using technology to deliver even the most complex of projects.
Touring around the region, I caught up with operators and engineers to see just how the delivery of earthworks projects has been changed using 3D models and Leica Geosystems machine control.
I was joined on the tour by Lee Knowles of local dealer One Point Survey Equipment who has been working with businesses to retrofit excavators and dozers with the technology, whilst supporting engineers with the surveying equipment needed to create the earthworks models the machines require.
For Courtney King, owner of Courtney King Plant Hire and Groundworks, adopting machine control has led to the largest project the business has undertaken to date, a major new road outside Newquay. It's a key part of a major new house building project also currently under construction.
Courtney: "I originally started using machine control when I was an owner operator, and now it's enabled us to expand the business with the addition of more excavators and a Cat dozer.
There is no room for error on a job like this as on this section in particular, we have to carefully place and compact material from a local quarry, building up the road base to meet a new bridge.
"So, it's a project we could only deliver by working to a model using 3D machine control on our Doosan 225 excavator and Caterpillar D5 dozer. With support from the team at One Point Survey, we have managed to get all of the equipment fitted in time to start work whilst also upskilling the team who are delivering it.
"This has involved training on how to operate the dozer and excavator for the whole team, including myself. We have also gone through the learning curve when it comes to the model design working with our local engineer. We have even involved the client in the process, which has been important to the management of the job.
"They now have direct access to the model and can see our 'as dug and dozed' progress each day, which is a great management tool.
"And if any changes to the model are needed, these can now be sent straight to the machine over the GPS network by our engineer, who doesn't even need to be onsite.
"It has literally changed how we work, and I have already added Leica onto two of our smaller excavators used mainly on our house building projects."
Where Courtney and his team have more recently built machine control into their projects,
Cornish earthworks contractor KHC Groundworks & Civil Engineering was one of the first users to adopt the technology.
I met with the team over four years ago at a dig day, so I was pleased to see the business has continued to invest with a new Hyundai HX220Al excavator and SMT tiltrotator greeting me at a complex house building project in St Erth, Cornwall.
The excavator was joined by a Liebherr PR 716 dozer, also using machine control operated by Darryl, who first stepped into its original Hyundai machine four years ago using the Leica Geosystems CoPilot system to operate the machine and tiltrotator.
Darryl, who is also a site manager, updated me on the company's progress: "We now have five connected machines working on different projects across Cornwall, and we continue to invest in the fleet. This is because the technology helps us to do so much more, allowing us to take on bigger, more complex projects."
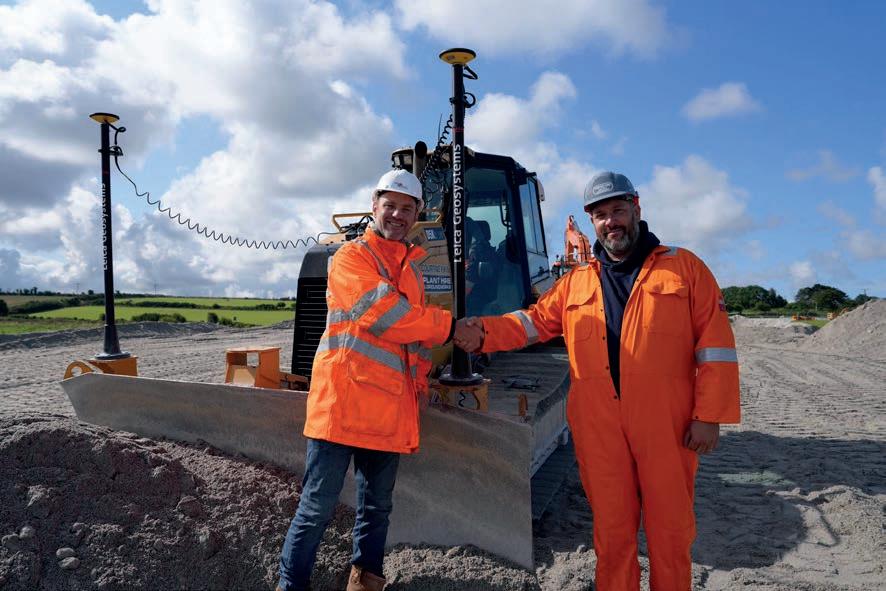

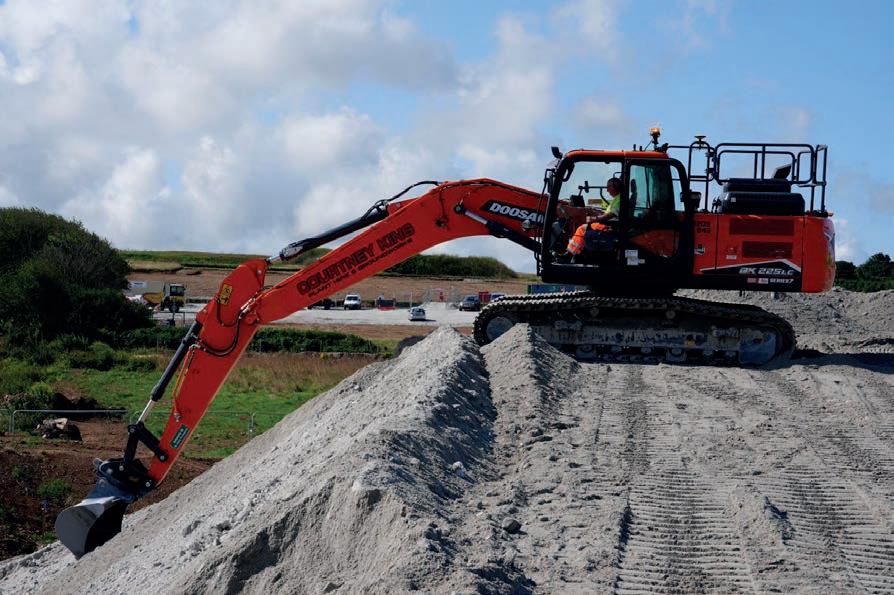
"This site we are on is a great example as it was originally on quite a steep slope, which we have had to cut and fill for the plots as well as digging trenches to install new drainage and utilities.
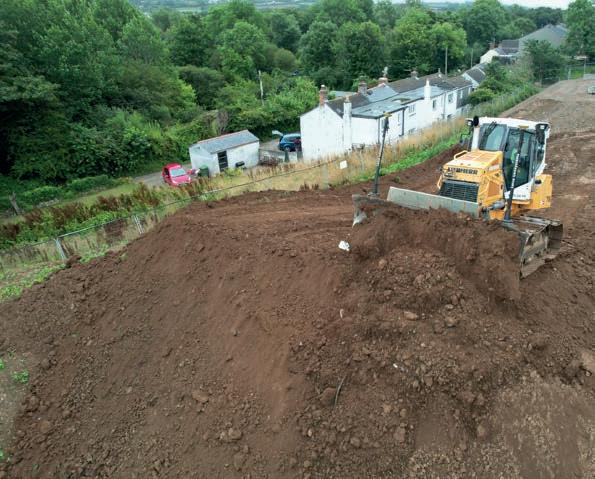
"With all work needed to be completed in a very tight timescale, this is a job we just couldn't do without combining 3D models with machine control."
Having combined tiltrotators with machine control for the last four years, I was keen to understand from Darryl what key impacts it has had on the business.
Darryl: "With the tiltrotator, you can sit the excavator in one place and don't have to move the tracks around so much. You can also quickly change buckets and work in different ways, thanks to the 360 capability, digging to high levels of accuracy.
"And the most important thing is you remove people from working around the machine. So, no one is in a trench, and all you need is a banksman.
When I visited newly machine control trained operator Darren was in the seat of the new Hyundai and shared his experience: "I went into panic mode when they said I was going to be using machine control, but to be honest, I got used to it, and now I wouldn't go back.
"In previous roles, I would have to wait for an engineer to come to the site and set out the plots, and I would often be waiting around if I finished the job. Now I can just move to the next plot as the model is on the machine."

It was finding out more about 3D model making that was part of my next site visit in Exeter, where earthworks for the construction of a new supermarket were well underway thanks to Pavilion Construction. Here I met with engineer Lee Butler, who was creating models needed for the site infrastructure.
Lee: "Since we adopted machine control, we have seen a number of changes in the way we work. The first is the ability to create and dig more complex models, which couldn't be achieved using more traditional methods.
"And the second is the speed in which we can go from the original design to the 'ready to dig' model, which can also be changed and loaded up to the relevant machine very quickly.
"This allows our operators to have a complete and up to date site model on their machine, so they can move from one task to the next.
"I can even upload changes remotely and log into the model to see the progress that has been made every day. It's changed the way I work as I no longer put stakes in the ground, and with my Leica Geosystems rover I can check levels onsite in a matter of minutes.
"I can also see what the operator sees on their tablet, so if there are any questions, I can login remotely and talk them through changes like adding offsets.
"This saves so much time, and once you have worked with an operator hand in hand, they pick up the system very quickly. We can now deliver more complex jobs and even share our progress with clients, which helps to manage the projects we work on and ultimately helps us deliver them on time."
With summer traffic making travel chaotic on the roads in the South West, it was great to see that time wasn't being wasted and that the teams could keep digging with models sent over the GPS network.
It was also clear that the relationships between operators and engineers have changed with more interaction between both of them as they work together to deliver projects.
It just goes to show how far the industry has come in the last four years and how many more projects have been completed with less fuel burnt and a big reduction in idle time. And what's more, it has given the businesses making the investment in technology a real competitive advantage.