
7 minute read
Molson Open Day delivers a full range of site solutions
As the largest independent dealer in the UK, Molson Group recently put on an impressive showcase of its multi-brand machine and attachment offering, whilst also showcasing new technology and a big electric surprise. Construction Worx roving correspondent, Peter Haddock reports
Held at its Avonmouth facility earlier this year, the open day also allowed visitors to visit Bristol Ports and a special technology dig zone.
And for those visitors like myself who had never been to a Molson Group event before, it was like an industry tradeshow complete with hands on experiences, including a Sennebogen material handler basketball challenge and a Husqvarna remote control robot.
The event also saw the reveal of two very exciting innovations. The first being an electric powered 26-tonne Hyundai HX260e excavator, created in partnership with Dutch company Urban Mobility Solutions (UMS).
The big difference with this model was how it has been designed to work like a diesel machine with refuelling, in this case, delivered through exchangeable battery packs. These can be simply swapped out with fully charged units in under 10 minutes, ensuring the machine can keep operating throughout the day.
Talking about the partnership in its decarbonisation zone, MD Robin Powell said: "An excavator the size of the Hyundai HX260e consumes a lot of power, but with this machine, we have delivered the first battery powered solution that is fit for purpose in the UK. It will enable users to work in the same way they do when using a diesel equivalent. And, of course we will have trained engineers to look after the machine when it gets out to site."
As I walked around the depot with Robin, we passed rows of machines, including Kobelco and Hyundai excavators and earth carrying equipment from Thwaites, Hydrema and Rokbak, before discovering the latest Husqvarna remote control demolition robots.
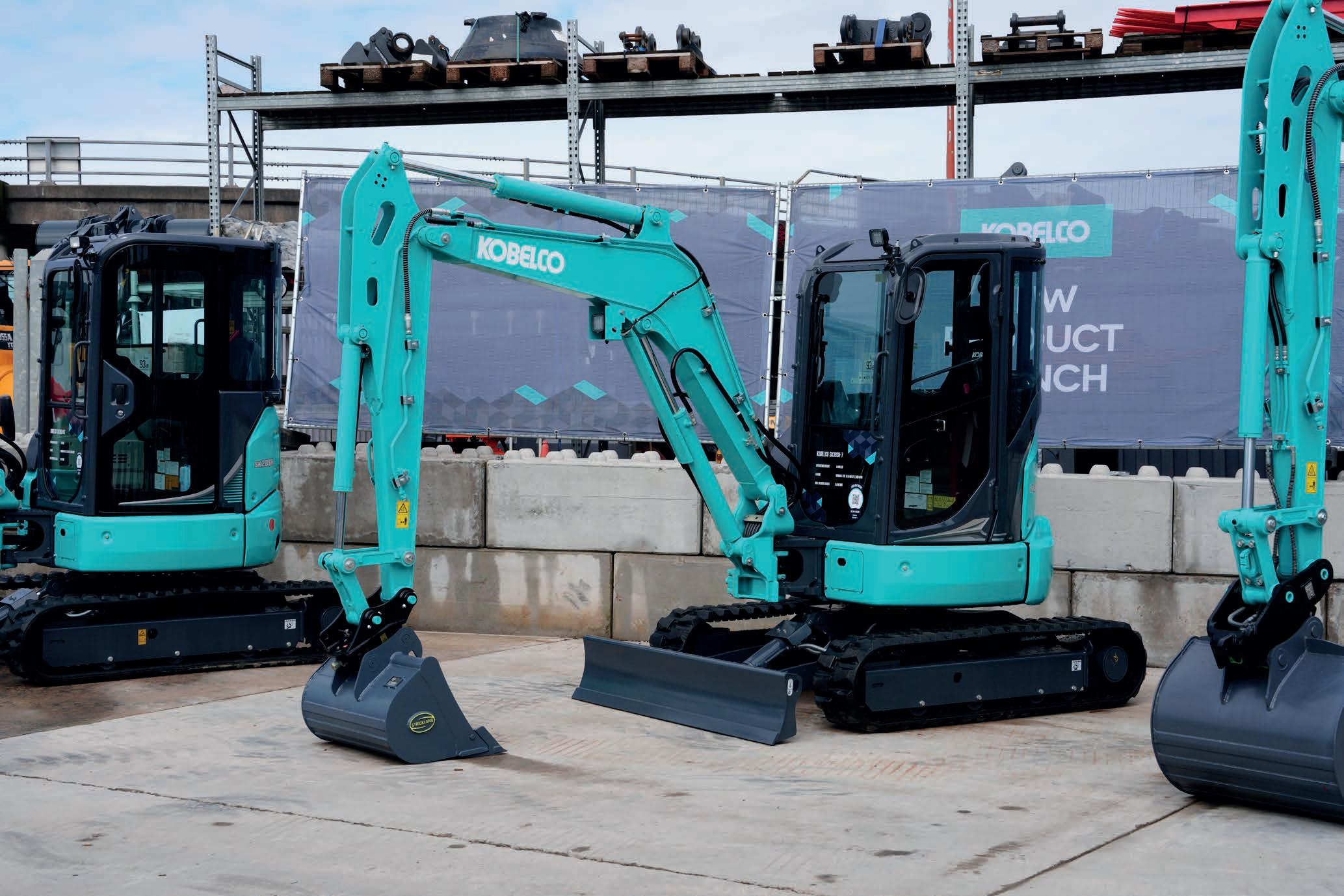
These electric powered machines have recently been added to the Molson Group offering, complete with a range of attachments. I caught up with product expert Fredrik Linnell to try out one of the machines and learn more about the range.
Donning a surprisingly comfortable shoulder strap mounted remote control, I was able to simply operate one of the robots, which was fitted with a grab and powered by an electric cable connection.
Explaining more about the machines, Fredrik added: "These robots are changing the way the demolition industry can work, and because they are electrically hydraulically driven, they are much better for the environment with no exhaust fumes to worry about.
"We have four products in the range, which can all be operated from a safe distance of up to 300m. Being small, they can fit through doors but are as powerful as an 8-tonne excavator. They are even agile enough to climb stairs."
New technology and data-driven insights
Following on from my remote-control experience, I met with Henry Moore, Commercial Director for Molson, for its big technology reveals. The first was a new system called InVu that it has worked on with a supplier to the automotive industry. Together, they have developed the technology for the construction industry that has been tried and tested in Formula One.
This is an AI based safety solution that was demonstrated on a Kobelco excavator. Using clever technology and cameras around the machine, the solution detects the human form, alerting operators when anyone comes into the exclusion zone around the machine.
Henry: "Our customers not only want us to supply equipment and attachments, they are now looking for technology solutions that can be fitted at the point of purchase in our depots or retrofitted in the field.
"The InVu solution itself is made up of green, amber and red zones with audio and visual prompts for the operator and audio alerts for people around the machines. The technology also pushes real time alerts into our cloud-based platform, sending information to those responsible for safety. We are still adding new features to InVu and plan to launch it to our customers in Q4 of 2023."
With technology now playing an important role in keeping equipment operating and uptime levels high, the event also saw the launch of a new fleet solution called fleetCMD. This uses telemetry data to connect the machine through the cloud to an online platform that can give owners and plant managers a complete view of the fleet from any connected device.
It connects machine data from the API's provided by OEMs to monitor a whole range of information from operating hours and performance to CO2 emissions and machine health. It also links seamlessly to its online Molson Parts solution, ensuring that the right parts can be purchased for any machine purchased from Molson on the fleet.
Built into the system is the ability to create reports for a whole range of stakeholders, from customers to site managers and plant maintenance teams to engineers. This gives customers one version of the truth for all equipment, enabling better planning and reporting.
Henry Moore added: "We have made fleetCMD a cross industry platform that can accept information from a whole range of OEMs, some of which we don't sell. This ultimately helps customers understand what is going on and get aggregated data from all the machines onsite to monitor performance and uptime.
"For the brands we sell, additional information will be available to enable us to work with them to manage fleet health, with the information being specific to each machine. This also allows us to service their equipment more effectively, supporting the overall availability of machines."
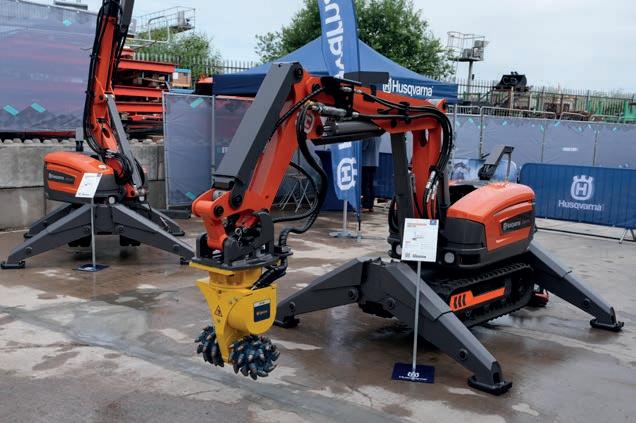
Rolling out more electric and unloading ships at Bristol Ports
In addition to the Hyundai HX260e, Molson also revealed a smaller HX85A fully battery powered excavator converted by UMS and Amman showcased its new compact double drum electric roller, the eARX.
Jo Adam from Ammann was on hand to explain the key features: "Being powered by an all-electric drive, the eARX 26-2 is very quiet compared to the same diesel equivalent, and it offers the same performance. It can also be charged with our portable, fast charger from zero to full in around 3 hours.
"For additional charging options, we have added a standard Type 2 charger to the machine like you would find on an electric car, making it easy to charge, particularly on sites using other electric vehicles. And with more construction sites setting up this charging infrastructure, you can charge this roller and a car side by side.
"Like other electric vehicles, we have added regenerative features, so the roller will put energy back into the battery when braking. When it comes to general operation, the ��ARX 26-2 can put ina full shift, and of course, there is no idling, so it won't use any battery power when stationary."
Even with some very large machines at the event, including Terex crushers and screeners, the highlight of the day was just a short drive away. This was because Molson had just completed the build of a new Sennebogen 870 specialist port material handler at Bristol Ports.
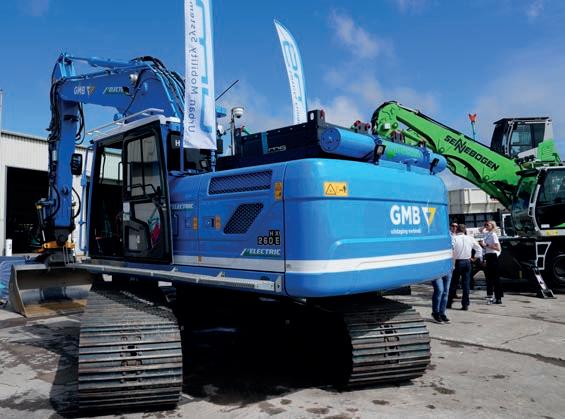
The huge machine that took three weeks to assemble is set to slash material discharge times by up to 50%. It will be joined shortly by a second machine, and together, they will help Bristol Ports increase productivity and reduce the time ships need to spend in the port itself. This particular configuration has a 24m reach and was supplied with an 8-tonne capacity grab bucket.
The whole event was certainly an eye opener, and Robin left me with a final comment when looking at the extensive attachment range from brands like Geith, Strickland and SMT. Robin: "For attachments in particular, our customers want us to supply an option for them so they know they get the right support. And this is why we continue to expand our attachment range, as it just makes sense."
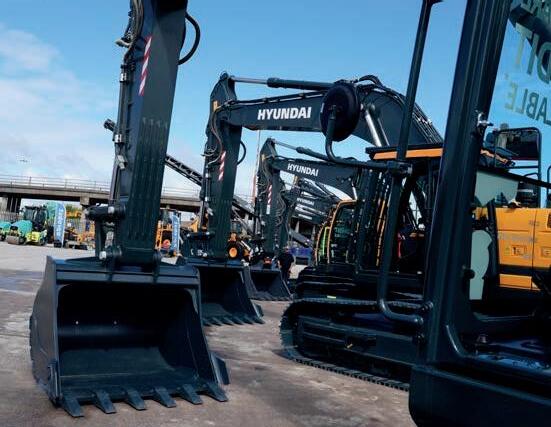