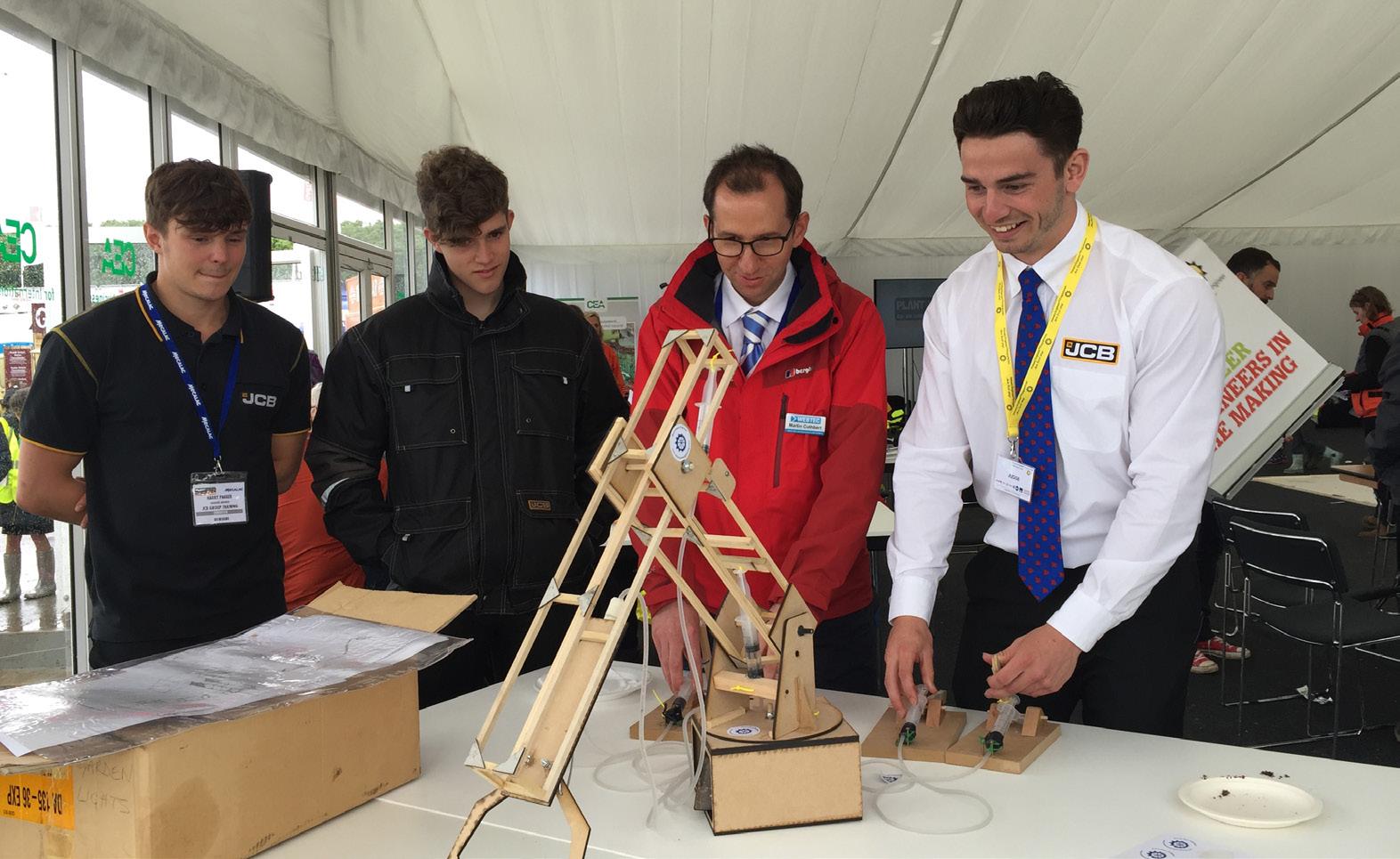
18 minute read
Upskilling the workforce
Training Our Future Engineers

Advertisement
Diego Cossio, development engineer at Webtec seen here presenting the Roy Cuthbert Scholarship to this year’s winner Ethan Green.
As a specialist manufacturer of hydraulic measurement and control products, helping to improve the productivity of construction machinery, Webtec have experienced first-hand the skills shortage in our industry. Their MD, Martin Cuthbert talks to Construction Worx about the company’s efforts to engage and retain apprentices and encourage our future engineers…
Webtec is committed to increase the knowledge and skills of its employees, customers and the wider community. From modern apprenticeship schemes to educating and encouraging the next generation of engineers the company believe in practicing what it preaches and sponsor programmes such as the Arkwright Scholarship Trust, Engineering Education Scheme and The Secondary Engineer® Fluid Power Challenge.
Martin said, “Each year we have openings for apprentices covering roles including engineering, manufacturing and sales. Each apprenticeship lasts around 3 ½ years and includes college day-release plus comprehensive in-house training with continuous assessment and a mentorship programme. We currently have four apprentices at various stages of their training, with another two successfully completing their apprenticeships and now fully working for the company in engineering roles. This number is set to increase as we are already looking for our intake of potential new recruits for this year.”
However, finding the right talent with an interest in engineering is not always easy, so to encourage youth into the industry Webtec take part in both local and national sponsorship and educational schemes. Martin added, “We have strong links with local schools and colleges and regularly attend job fairs and open days. We believe that local recruitment is important to nurture the talent available, but we often find ourselves competing with other more ‘fashionable’ professions. But times are changing with the importance now given to teaching STEM subjects at schools and national schemes such as ‘The Secondary Engineer® Fluid Power Challenge’, which are designed to attract secondary school pupils into engineering.”
Another scheme for young engineers is run by the Engineering Development Trust (EDT) called the ‘Engineering Education Scheme’ (EES) which links teams of 16/17 year old pupils and their teacher with local companies to work on real, scientific and technological problems. Webtec work with their local St Ivo Academy.
The Arkwright Engineering Scholarship Trust acts as a beacon to the
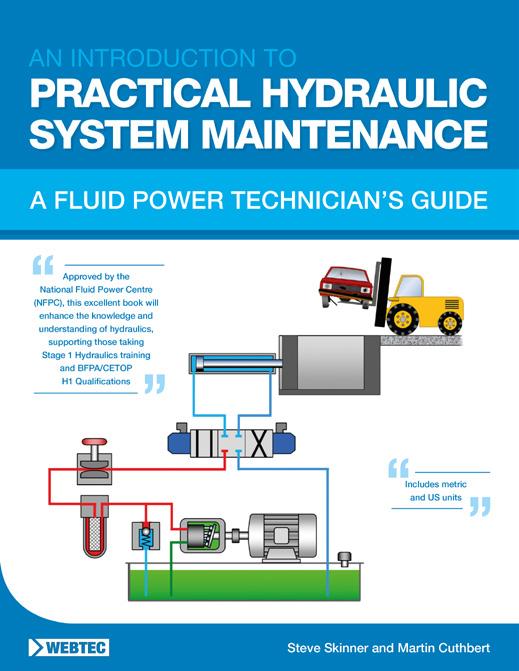
most talented STEM students in UK schools and who aim to ensure that high-potential young people, in the critical 16 to 18 age range, stay engaged in the engineering careers pipeline.
Martin said, “For the past six years we have sponsored the Roy Cuthbert Scholarship, part of this award scheme, which was named after Webtec’s founder, a passionate engineer and entrepreneur who passed away in 2013. Knowledge and education go hand in hand and as such we wanted to find a way to share our vast experience and information with a wider audience. After many months in preparation we launched ‘An Introduction to Practical Hydraulic System Maintenance’, a guide for all fluid power technicians. Co-authored by industry expert Steve Skinner and myself we believe that this is an invaluable tool aimed to help educate technicians and engineers new to hydraulic fluid power maintenance and hydraulic engineers embarking on a career in this industry.”
The guide is available via Amazon and Kindle, and has been reviewed and endorsed by several organisations including the British Fluid Power Association, Institution of Mechanical Engineers, National Fluid Power Centre, British Valve and Actuator Association and the Construction Equipment Association. All profits made from the book will be donated to support STEM programmes. Webtec also has a dedicated ‘Education’ resource section on their website where specific product and educational guides can be downloaded for free – see https://www.webtec.com/ education/.
Martin concluded, “As a company proud of its heritage, we are committed to inspiring others to enjoy the challenges that engineering brings.” ■
I am Woman hear me roar!
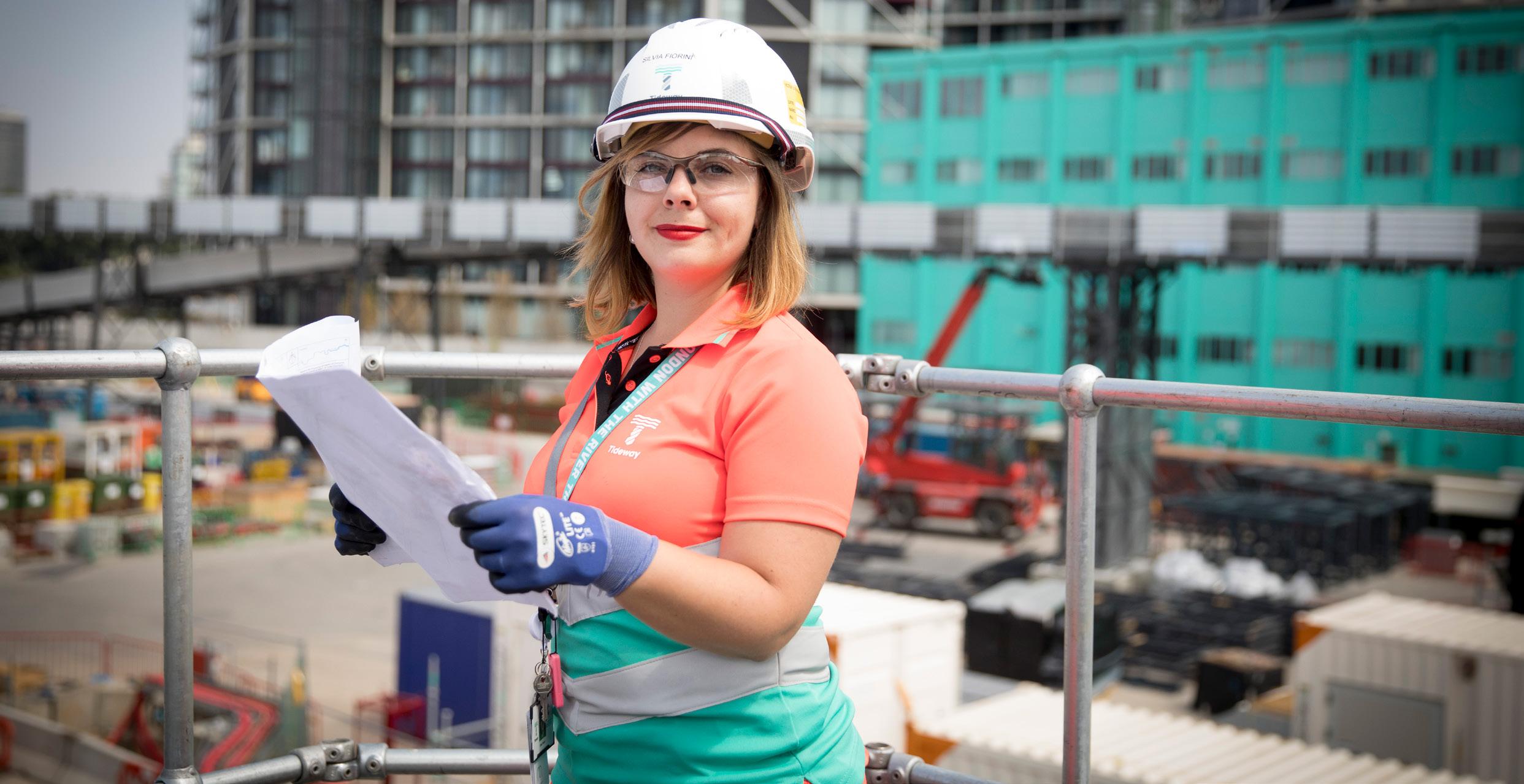
Support for women looking to move up the construction career ladder – Construction Worx explores the fantastic work the Women into Construction organisation has been working on in order to drive a better gender balance in the construction sector.
For over a decade Women into Construction (WiC) have been addressing the staggering imbalance of gender representation in the UK construction industry, which currently sees women making up just 14% of the work force. Their programmes offer bespoke support and guidance for women wishing to work in the sector. The not-for-profit organisation has trained over 1,600 women, with over half of those moving into sustainable employment, in what continues to be a male dominated industry.
This small, dedicated team, led by Kath Moore MBE, are running entry work programmes across London, Birmingham, Essex and Cambridge, continuing to promote gender equality, support women and assist contractors to recruit motivated and trained women - creating a more gender-equal work force.
However, as more and more women join the industry, it has become clear that the gender pay gap continues to lay wide open for those already working in the sector. In recent published statistics, the construction industry has been shown to have the highest gender pay gap of all industries in the UK, with an average pay gap of 23.6% against the UK average median of 9.8%. The ten largest companies (by turnover) are still reporting an average of a 30% gap.
With support from the CITB, Trust for London and BAM Nuttall, WiC launched ‘WiC Moving On Up’, a pioneering programme, set to provide career progression training and one to one mentoring to support low-paid female construction workers, to progress into better paid and more secure employment within the sector. It identifies barriers and challenges employers’ working practices to support women to progress in their careers and narrow the gender pay gap.
Talking about WiC Moving on Up, Kath Moore said, “This programme, which has no cost to companies or individuals, will pave the way for the diversity that is key to the construction industry’s future. It comes at a time when the industry is struggling to recruit yet falls at the first hurdle as it struggles with employing, training and promoting suitable, qualified and talented women.” Her comments were echoed by Sarah Beale, CITB’s chief executive, saying “CITB welcomes the opportunity to support companies in developing strategies to tackle the gender pay gap, assisting them to recruit and retain more women within the workforce, and to support their supervisors with being effective mentors/sponsors. We will also be supporting women already within construction with career progression.”
WiC ‘Moving On Up’ successfully rolled out the first cohort with 98% engagement from companies, with the second cohort launched this February. Project manager Ripha Begum said, “This is an amazing opportunity to unite industry leaders in developing best practice to support women working in construction to develop their careers and potentially progress within their companies. This also allows a platform to network, engage and encourage cultural change in attitudes to diversity, fairness and respect within our workplace.”
With the CITB reporting that 33,000 new recruits are needed between now and 2023 to meet demand it’s safe to say that the work of Women into Construction is not over as continued support is needed for women to gain entry into the industry if companies are to diversify their work force and tackle these skills shortages. Retention also plays a key role and women deserve access to equal opportunities once they are in the industry too. With programmes like ‘WiC Moving On Up’ leading the way, there will be an increased representation of higher paid, successful women in the sector who will become role models for a new generation of women in construction. ■
For more information about Women into Construction contact: Website www.women-into-construction.org Email: info@women-into-construction.org Tel: 07480 856802
WHY DIG LIKE THIS... ...WHEN YOU CAN DIG LIKE THIS?
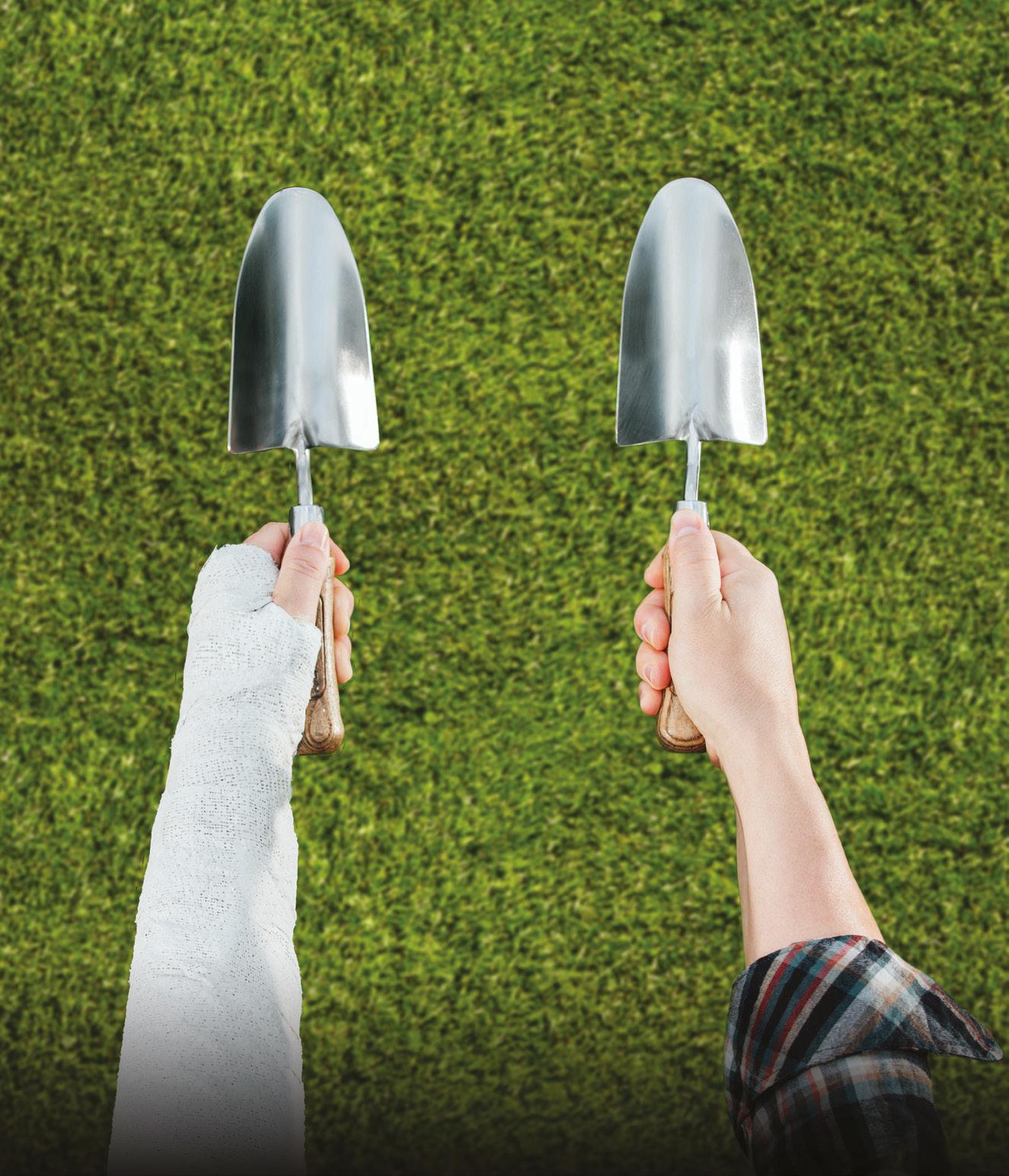

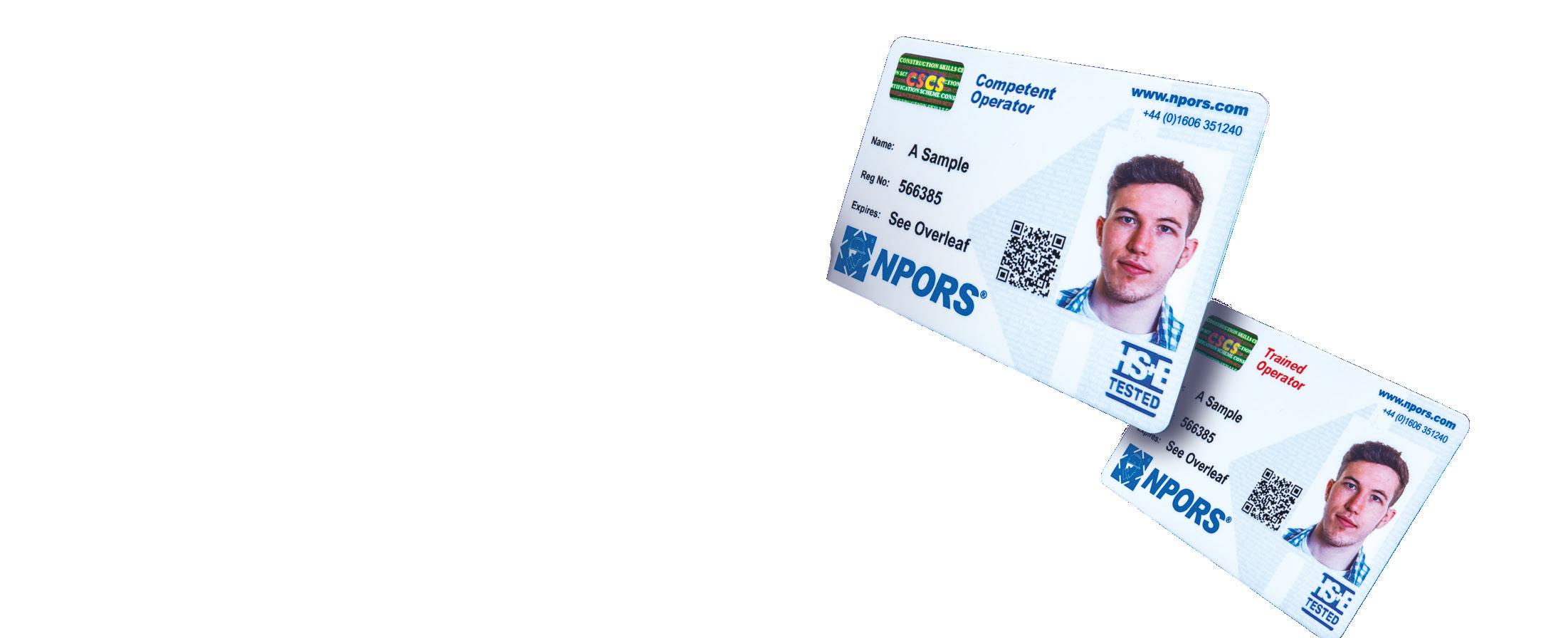
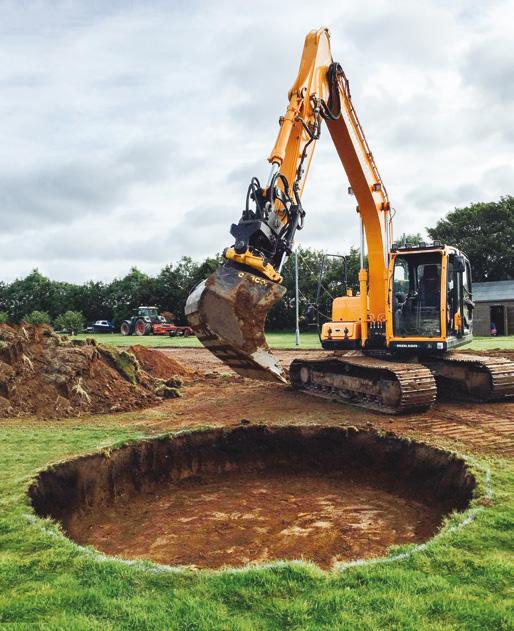
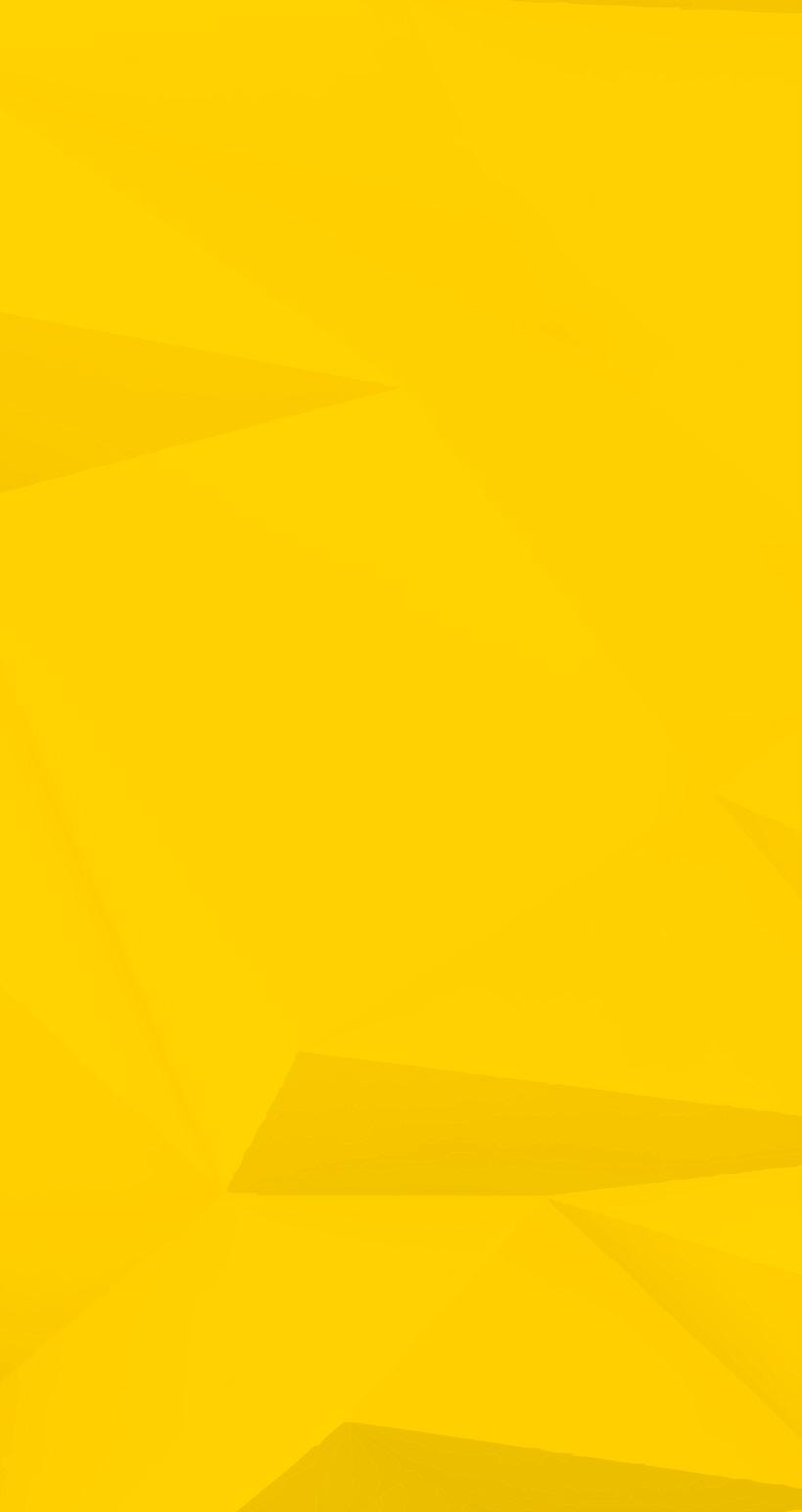
DIGGING WITH AN ENGCON TILTROTATOR IS LIKE REMOVING THE PLASTER CAST FROM YOUR EXCAVATOR’S ARM Call us on 01684 297168 for a demonstration If you’re the kind of excavator owner that likes to have total control over every aspect of your digging, then we would like to talk to you. Free up your mind and free up your excavator – fit an engcon.
Building Skills for Offsite Construction


The call for offsite and modern methods of construction to be utilised across all areas of construction is growing. It has the great potential for use in the housing, social and commercial sectors with further opportunities to upscale adoption in large-scale infrastructure projects, which can be seen in projects like HS2 and Hinkley Point.
These revolutionary new ways of delivering both small- and large-scale projects can mean a reduction in costs and delivery timescales while realising an increase in productivity, quality, and whole-life value. However, the industry is reporting that training in these new areas is not keeping pace with demand.
Over the last decade output per UK worker in the construction sector has remained largely constant, whereas the service sector has improved just over 30% and output in manufacturing has rocketed by more than 50%.
CITB released its 2017 report, ‘Faster, Smarter, More Efficient: Building Skills for Offsite Construction’ which showed that 42% of construction industry employers with over 100 staff expect to use offsite methods in five years’ time. It also showed that nearly 50% of construction industry clients expect the use of offsite construction to increase over the next five years. This is supported by the Infrastructure Projects Authority Transforming Infrastructure Performance report, through which five Government Departments committed to apply a presumption in favour of offsite construction by 2019.
However, a number of issues with training and qualifications were highlighted as acting as barriers to delivering the skills needed to upskill the workforce for this demand, notably: ● Limited training and qualifications that are specific to offsite construction/manufacturing, rather than traditional construction; ● Training that is available does not typically include coverage of relevant ‘softer skills’, including behaviours and attitudes for offsite, even though these are very important for the holistic nature of offsite work; ● There is a shortage of skilled tutors and assessors with relevant and sufficient knowledge of offsite to be able to deliver highquality training; ● Where relevant training and qualifications are available, most employers are not aware of them, or are unable to access them because few providers offer the courses or because they are not able to release employees to attend training; and ● The tendency among employers to assume relevant training does not exist and to train in-house instead. As a result, this suggests to training providers there is limited demand. CITB is investing £1.2m in projects aimed at increasing the skills capacity to support offsite manufacturing and construction. As part of this the Manufacturing Technology Centre (MTC) is developing a set of high-quality resources to upskill trainers in education and industry. This includes creating: ● A set of standardised training materials that are freely available to approved trainers. ● Upskilling of existing trainers and creating new trainers in offsite manufacturing knowledge and competence ● Providing employers with quality assurance evidence that the current provision has the adequate knowledge and competence in modern methods of construction and lean manufacturing.
Why does the Construction training industry need to get involved? ● This represents a significant opportunity for providers and employers to get ahead of the game in developing new capability at no cost – the project is funded by CITB; ● Employers are seeking training organisations that can demonstrate an understanding of offsite manufacturing and construction; without this they’ll go elsewhere for training provision. [At Offsite Expo concern was expressed that providers and employers are not keeping pace.] ● Providers and employers stand to gain competitive edge by having trainers approved as capable of delivering offsite knowledge
What’s the commitment? ● Undertake an on-line diagnostic (1-hour average of your trainer’s time) ● Undertake a five day train the trainer programme at MTC in Coventry
Offsite also represents a slightly different perspective of the industry. Research shows it can present a new image and opportunities to people coming into the industry. It offers different working conditions in a factory and roles like digital design, data analysis, robotics and factory production managers may appeal to a slightly different cohort
Your Invitation
compared to traditional construction roles.
Not only is the Training industry needed to back this initiative but also the construction sector as a whole. Staff training and development should form an important part of any company’s employee retention strategy. Research has shown that employers who have a strong training and development plan allowing their staff to learn new skills or upskill in existing areas keep staff for longer, reducing recruitment and onboarding costs. There is no doubt that the industry is going through significant change. Action taken now will help alleviate the current skills gap challenges and ensure the provision of a workforce fit for the needs of a transformed industry.
Steve Radley, CITB strategy and policy director, said: “Offsite construction creates a range of exciting new skills needs and opportunities, including in assembly, digital technologies and installation. We’re looking to build these into training at both entry level and also to enable upskilling within the industry, because getting this right can mean a more multi-skilled, diverse and productive workforce.” MTC construction skills manager, Ian Buckingham, said that developing offsite construction capability is a key priority to address poor productivity in the sector and also to meet government housing targets.”
For more information on the CITB/MTC project, contact Ian Buckingham, construction skills manager, ian.buckingham@themtc.org. Visit http://www.the-mtc.org/ for more information on the Manufacturing Technology Centre. ■
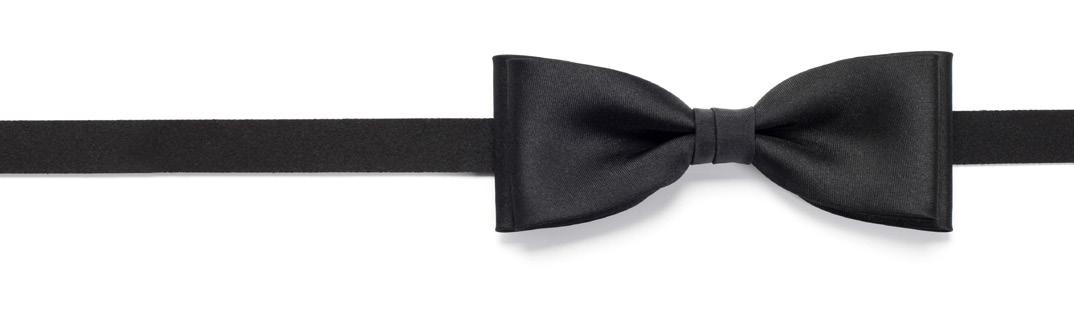
Thursday 11th June 2020
East of England Events Centre, Peterborough, PE2 6HE

A sparkling black tie event where the construction industry meets. Take a table and bring your customers. Unparalleled networking over pre dinner drinks, dinner and the CEA Awards for Excellence in association with Plantworx. Celebrity host Shaun Williamson. Eastenders' Barry, actor and quiz supremo.
TICKETS FROM £89 CEA Members: £89 pp - table of 8 £675. Others: £99 pp - table of 8 £775. Visit www.thecea.org.uk or contact claire.kelly@admin.co.uk for further details.
Constructing skills for industry – investing in the future
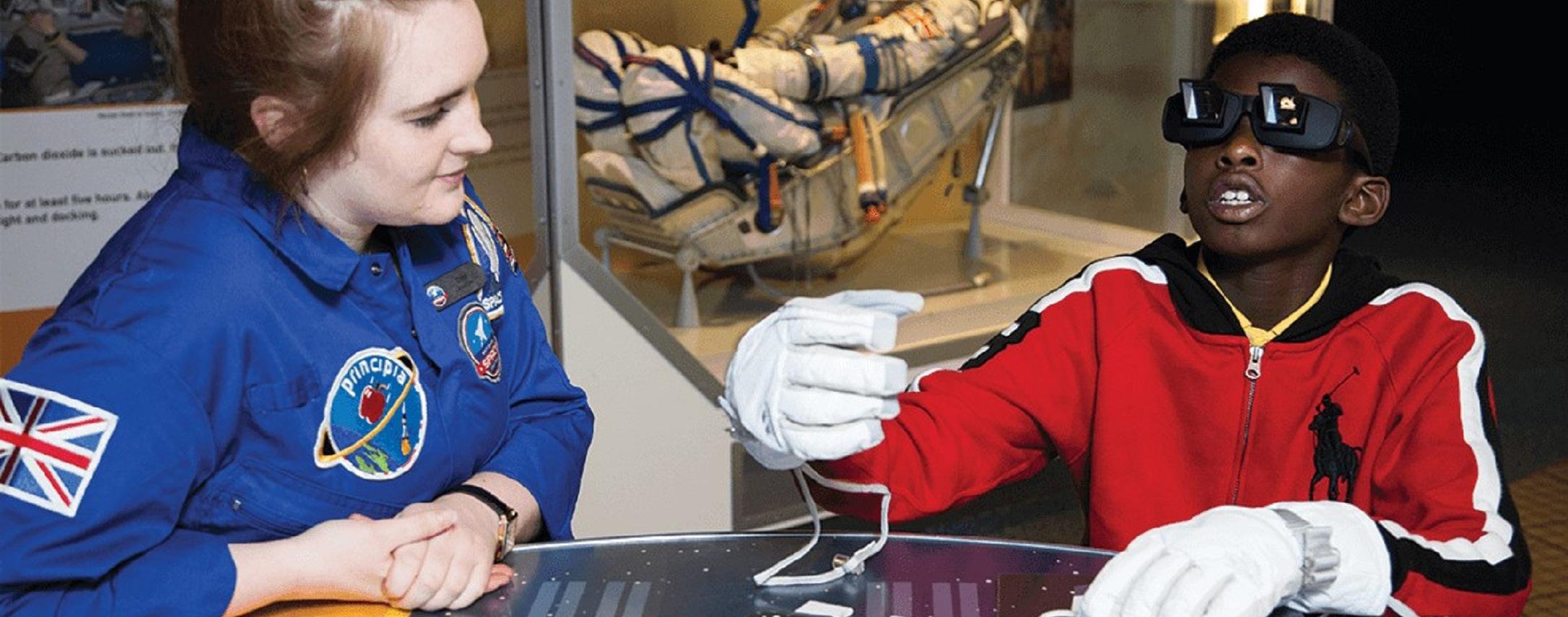
Advanced Polymer designer and manufacturer Nylacast, place people development at the top of its agenda through delivering award-winning educational programmes across its business. The company regard its workforce as its most valuable asset and have invested a great deal in nurturing the next generation of talent and upskilling its current staff.
In 2014 Nylacast officially unveiled its Training Academy. Identifying a need to consolidate the company’s many educational activities under one roof, the engineering firm invested in a dedicated on-site facility to help bridge the much-debated engineering skills shortage faced in the UK. Following expansion of facilities and training teams, today the Nylacast Training Academy provides a wide variety of programmes to attract and nurture new talent in addition to upskilling and retaining the current workforce. Keen to promote careers in engineering, the Leicester-based company has developed close links with schools, colleges and universities across the UK and regularly participates in community initiatives to attract and develop future generations. This includes frequent visits to primary and secondary schools, to deliver careers talks and hold mock interview sessions.
The company also launched its own summer ‘Introneering’ programme which aims to deliver a one-week industry placement to students aged 14 to16, demonstrating the many career paths available within organisations. In addition, Nylacast facilitates five to ten-week student placements across all departments, providing access to skills, knowledge and experience within STEM related fields.
Located a stone’s throw away from the National Space Centre, Nylacast is also a proud sponsor of IGNITE, the National Space Centre’s Community Engagement programme, with a mission to get people excited about space and help develop the next generation of scientists and engineers.
Since starting its multi award-wining apprenticeship programme in conjunction with Leicester College, Nylacast has nurtured over forty students from fledgling apprentices into fully qualified professionals. The annual intake of apprentices at the company has grown from four to twelve in just a few years, with further apprenticeship opportunities now offered in non-engineering subjects including sales, marketing and business administration.
In addition to attracting and developing future generations, Nylacast run an annual review process to help identify the training needs and requirements of team members, this develops into a personalised training and development plan. As technology evolves the company also looks to identify potential future skills gaps across its business and further develop team members who want to advance their skills and knowledge.
The Nylacast Training Academy also focuses on the upskilling of the current workforce, helping to develop and retain talent within the engineering sector. Dedicating over 500 hours of in-house, classroombased engineering training per annum, the Training Academy and its CNC (computer numerical control) simulator facilities have trained and upskilled over 100 members of staff in CNC programming.
Recognising and nurturing talent, the engineering firm’s Training Academy has also helped more than fifty team members achieve NVQs in Leadership and Management through a programme developed in conjunction with Leicester College.
Operating within the manufacturing industry the company also delivers regular training and refresher courses on first aid and first response. More recently delivering a six-month ESOL course (English for Speakers of Other Languages) with a successful wave of graduates receiving their qualifications in December 2019.
Mental, physical health and well-being is also high on the company’s agenda, with dedicated events, initiatives and campaigns taking place on a monthly basis from Mental Health First Aid to health awareness workshops and yoga lessons which all prove very popular.
Nylacast’s group marketing manager, Junaid Makda, commented on the company’s passion for people, he said, “As a company with more than five decades of operations we are fortunate to have a huge talent pool stemming across multiple generations. it is our social responsibility as collective individuals to open our facilities and share our knowledge to create a platform and foundation for future engineers and leaders.”
Nylacast has proved that investing in its employees is the smartest business decision a company can make – in the words of leading entrepreneur Richard Branson, “Customers come second, employees first. It's a philosophy that brings unexpected benefits to both the company and its clients.” ■
Thumbs up from the CEA members
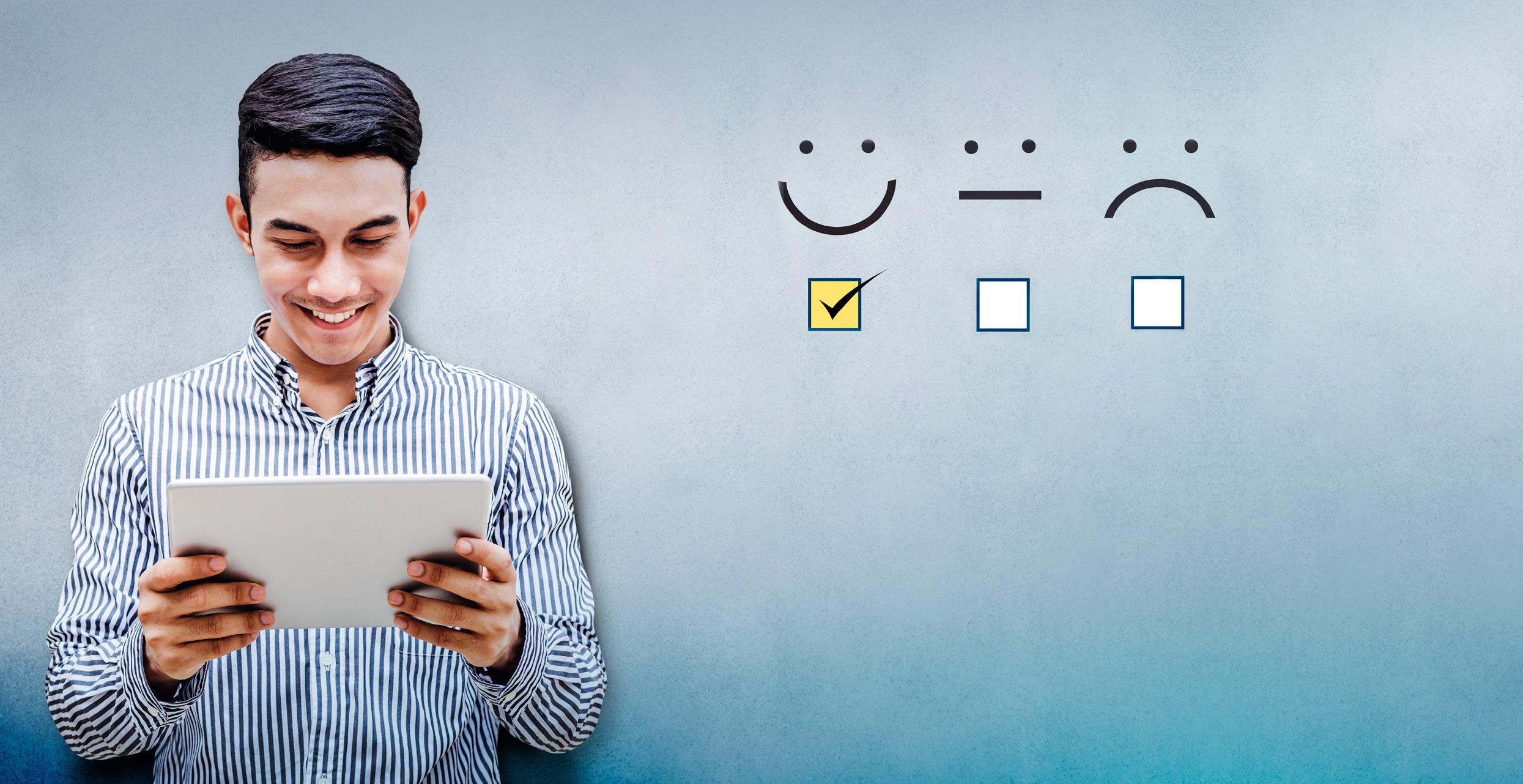
The results of the CEA’s latest membership survey show strong support and provide ideas for the future…
The CEA conducted a snapshot online survey of its members’ assessment of the main services provided by their Association. The purpose was to gather feedback to help with the planning of activities and priorities in 2020 and beyond. Billed as “The Five Minute Survey” it drew a healthy response rate.
The survey focused on asking members their views on how helpful the five main service area provided by the association are for them and their company. The areas were Lobbying activity, Technical services, Market information, Business promotion and International trade. The overall feedback on this was very positive, as shown in the chart below. This shows that 82% of the ratings recorded services as “Very helpful” (34%) or “Helpful” (48%).

Looking at the ratings for individual services, all five received an impressive level of “very helpful” and/or “helpful” responses. The chart below shows the split of the top two ratings between the service areas. Lobbying came out as the most valued service, followed by technical and regulatory services.
After rating how useful CEA services were to their company, members were also asked if they thought the services provided were good value. In response to this, 81% of respondents rated services as “Very good” or “Good” value, which provided further positive feedback on current CEA activities.
22 SPRING 2020 The rest of the survey invited members to provide comments on any additional services that they would like the association to provide. The results from this pointed towards the need to provide further development of existing services. More than half of the comments related to further development of the Market information and International trade services. Market information services have grown significantly under the management of specialist analyst, Paul Lyons. International trade services have been hampered by the scaling back of much of the funding available for overseas trade shows and trade missions by the Department for International Trade (DIT). As the UK enters the post-EU world, the CEA continues to press government on the importance of practical assistance in overseas markets.
The last question in the survey asked companies to identify if they were also members of other trade associations. This revealed that more than three quarters of the companies who responded to the survey were also members of other trade associations, and identified nearly forty other relevant associations. This was quite eye-opening, to illustrate how important trade association activities and services are to companies within the construction equipment sector. ■
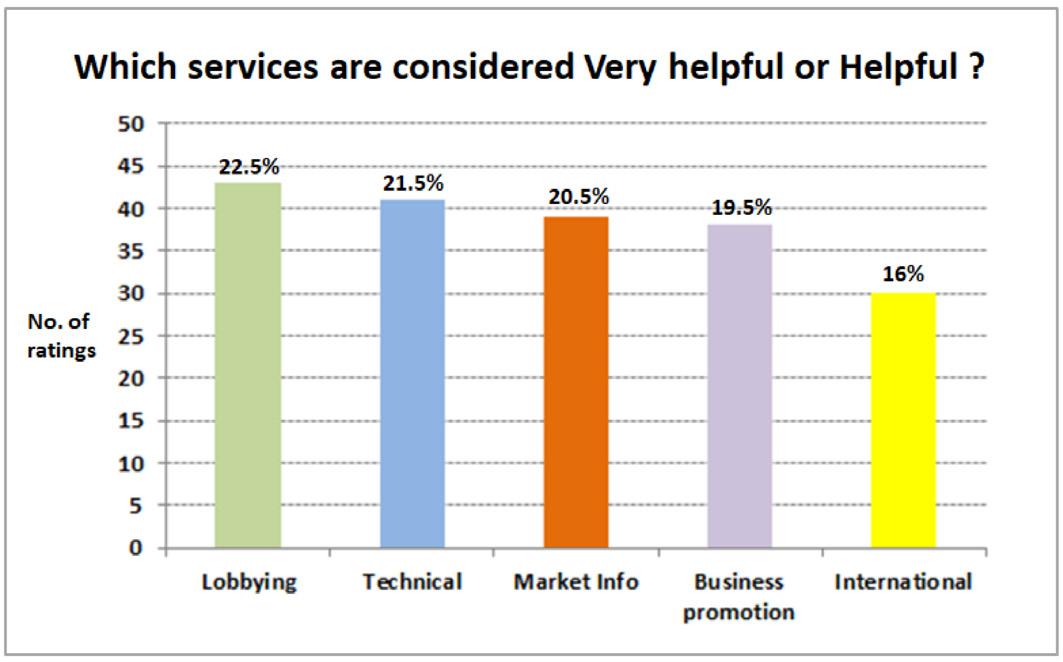
Membership of the CEA is open to all manufacturers and importers of construction equipment, component and accessory suppliers, distributors and relevant service providers. For further information contact Paul Lyons via paul.lyons@thecea.org.uk.