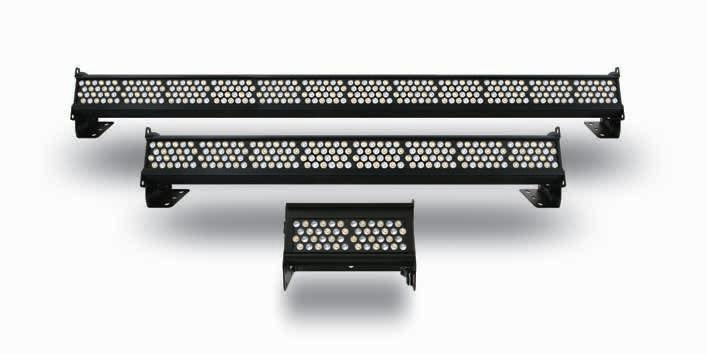
5 minute read
Tech Column
hey won’t be replacing those ARRIMAX M90s anytime soon, but LED lights are casting some bigger shadows on sets and studios. Ostensibly, they consume less energy, throw off less heat and have a longer lifecycle and are more robust than say, an HMI source, all of which combines to offset their initially higher costs. The devil, however, as always, is in the details.
First, a little history. LED – Light Emitting Diodes – have been around for more than half a century, though it’s only in the last decade or so they’ve become practical. The root science of LEDs goes back to circa 1907, with the discovery of electroluminescence. Work continued over the years to find a use for this phenomenon, and by 1963 the first red LED was created at General Electric. It took a decade before yellow LED came about at Monsanto. Still more work was done by more scientists and more companies before the first bright blue LED emerged in 1979. Still, it took until about 10 years ago for the technology to really start to break out of the lab and into wider use.

through a diode in combination with a specific material. Light is the result of interaction at the atomic particle level in the form of photons. There’s no filament to heat up and burn and nothing to break. Until recently, LEDs were restricted as staging lighting for live shows – either for theatres or live concerts – because they couldn’t pump out the lumens like tungsten or HMI lights.
Things are changing, and over the last couple of years, they’ve started to reach critical mass in niche settings on movie sets, in TV studios and in TV series production. Shows like Rookie Blue and Big Brother, along with CTV and other news shows in Toronto are using them for specific shots, and shows like Good Morning America, Jimmy Kimmel Live, The Late Show with David Letterman and The Tonight Show StarringJimmy Fallon have switched or are switching to at least some LEDs.
“They are also cutting their HVAC costs to cool down the studio,” notes Jean Francois Canuel, managing director at A.C. Lighting Inc. in Etobicoke, where the company has just moved into a 43,000-square-foot facility with
manufacturing, research and development, testing and administration under one roof. “In TV, for example, LED is also very welcome because those HD sensors are much more sensitive,” he says. “They used to shoot at 125 or 140 foot candles and can now shoot at 40. You can also do time of day lighting more easily because you can dial in what you want with RGBA fixtures.”
A.C. Lighting UK has been around for some 40 years and bought Spectrum Manufacturing in Canada 14 years ago. The company moved into LEDs two years later. Around the corner at William F. White, National Director Technical Support and Development Mike Harwood also says interest is picking up. “The biggest thing is internal controls, so instead of having to change a light – tungsten to HMI – you just change the settings,” he says. “We also have some lights with special effects built in so you can simulatelightning or police strobes at a crime scene.” Dialling a little blue or red into the lighting mix sets up a mood elegantly and easily, he adds, and it’s one of the reasons LED is finding a niche.
Still, size does matter, Harwood adds: “Our LEDs put out about 2,000 watts, but they’re at the limit where heat is becoming an issue. So you either baffle them and they get really big or you use fans, and of course as soon as the sound guys see fans, they panic.”
Looking ahead, some vendors have approached Whites with 6,000-watt space lighting for use overhead in sets, and he’s intrigued: “They say they’re equivalent to the 6K tungstens, though there are more fixtures. We’re doing some basic testing now.”
On set the crew likes them because they’re fairly easy to work with, and the talent likes them too. “The talent likes them because the heat doesn’t come off the front,” Harwood notes. “But the heat does come off the back so you have to be careful where you put them.”
Even with the advancing technology and growing acceptance, there are some roadblocks ahead, Canuel says. While LED fixtures might seem more expensive initially, they have come down in price and continue to fall, though there’s a wall to hit because the price of the components have firmed up. “If you do the math right it is even cheaper,” Canuel argues. “You can remove the dimmer, the copper to wire it up, the labour to wire it up, the extra HVAC, even maintenance. It’s competitive at the right level.”
As it stands now though, light level itself is the major hurdle: “Theoretically you can hit 260 lumens per watt in the lab, but that’s under controlled conditions and in the real world, maybe 100,” he says. “That’s about 80 or 90 lumens per watt, better than tungsten and about the same as fluorescent.”
As to the future, he shrugs. There are literally hundreds of scientists and researchers working on new configurations to boost output and efficiencies, but he suspects they may have already reached the limits of the current configuration and will need a new technology to break through again as it did in the early 1990s.
“There’s no Moore’s Law (named after the Intel founder who proclaimed integrated circuits would double in speed every 12 to 18 months and half in price) at play here,” he says. “I don’t see that 575 HMI disappearing soon.”
Ian Harvey is a veteran Toronto-based journalist who writes for a variety of publications and covers the technology sector. He welcomes feedback and eagerly solicits subject matter ideas at ian@ pitbullmedia.ca.
Previous page: Chroma-Q Studio Force V Range features variable white LED models. Above: Compact Studio Force LED light.

The Chroma-Q Studio Force V Phosphor, a variable white fixture using LED technologies.
