
38 minute read
i‘CE’ THE DIFFERENCE
‘CE’ THE DIFFERENCE
Brexit and the UK’s departure from the European Union mean significant changes to the use and application of the CE mark as well as energy efficiency labelling. But the good news is it’s not happening all at once
The ILP has linked up with the International Nighttime Design Initiative to launch a new resource for ILP members, the ‘Write, Light, Night’ booklist designed to raise awareness of books to help lighting professionals think about and reflect on night-time design. A launch event also delved into our changing perceptions of night, shade and dark By Allan Howard
By Nic Paton
Most lighting professionals will be very familiar with the CE mark. The CE mark is the symbol applied to products to indicate their conformity with the essential requirements of the relevant European Union (EU) directives regarding health and safety or environmental protection.
The letters ‘CE’ are an abbreviation and come from the French phrase ‘Conformité Européene’, which literally means ‘European Conformity’. The CE mark is mandatory for specific products that are sold in the European Economic Area (EEA).
Now, with Brexit completed and the UK out of the European Union, including the customs union, the EEA and single market, this article intends to look at how our changed status in relation to Europe will also mean changes for the lighting industry when it comes to the use and application of the CE mark and, as we shall see, its post-Brexit replacement.
THE CE MARK AND THE ‘CHINA EXPORT’ ‘CE’ MARK
The first point to make clear in all this is, in fact, not about Europe and the EU at all, but confusion with similar marks.
This is because it is important not to confuse the EU’s CE mark with what has become termed the ‘China Export’ mark (and so which can potentially also be shortened to ‘CE’). To confuse matters even further, the logos for the two marks are similar in design (see figure 1 opposite).
This similarity in design means the two marks can often be confused and thus a product considered safe for use when it should not be. Products with the “China Export” CE mark will not have had the relevant risk assessment, safety evaluation or testing and as such are not certified against the relevant EU CE standards.
Bear in mind, too, that products bearing the ‘China Export’ mark can vary from being acceptable to highly dangerous.
If we look again more closely at figure 1, it may help to compare the two marks side by side; as you see the characters are not exactly the same. In particular, it is the spacing between them that distinguishes the difference.
The correct EU CE mark also has the ‘E’ starting on the circle profile drawn out by the ‘C’ character. Nevertheless, it pays to be vigilant!
THE POST-BREXIT UKCA MARK
The UKCA mark (UK Conformity Assessed) is the replacement for CE marking in Great Britain (in other words, England, Scotland and Wales) post Brexit. It serves the same purpose as the CE mark, but just recognising the fact that Great Britain is no longer a member of the European Union.
The regulations and directives that created the legal structure for the CE marking have been adopted into UK law and updated to change the terminology and to bring them within the control of the UK government. The UKCA is therefore applicable wherever the CE mark was previously required.
APRIL 2021 LIGHTING JOURNAL 29
Lighting, Brexit and the European Union
Figure 1. The EU’s CE mark (left) and the ‘China Export’ CE mark. The logos are, unfortunately, quite similar in design, something that can lead to confusion. However, when examined side by side, there are clear differences
Figure 2. The logo for the new UKCA (UK Conformity Assessed) mark. The post-Brexit mark came into effect in January, but there is a transition period until January 2022
The UKCA mark came into effect on 01 January 2021 but to allow businesses time to adjust to the new requirements the old EU CE mark is still valid until 01 January 2022.
However, the UKCA mark is not recognised within the EEA and products for sale within the EU still require the CE mark.
Products will be able to display both marks unless and until the rules for those products diverge between the UK and EU, although it is not currently expected that any divergence will happen in the near future.
It can only be hoped that overseas manufacturers consider the UK market is sufficient that they look to use the UKCA mark.
In this new landscape, it is important for lighting professions to become familiar with this new mark. So the image above (figure 2) is what the UKCA mark looks like.
NORTHERN IRELAND EXEMPTION
It is also important to recognise that the UKCA is not applicable in Northern Ireland, where a new ‘UKNI’ mark has been adopted but only for products where thirdparty certification by a notified body is mandatory.
There are very few lighting products that fall into this category, but those for use in explosive environments is one. Ordinarily, Northern Ireland will still require the CE mark for all self-declared products.
THE EU ENERGY LABEL
Beyond the CE mark, another change that has come about because of Brexit is to the EU energy label. This was first introduced in 1992 and has become a familiar sight on many goods and products. The absolute performance criteria were defined for different types of appliances to determine the energy class of each appliance sold within the EU.
These ranged from A (best energy performance) to G (worse energy performance). After a number of years and progress of technology, most appliances were being classed in the highest rating and to manage this in 2011 the EU maintained the criteria but introduced A+ to A+++.
We are now at a stage where the problem exists once again and the existing labels are considered confusing to the end user, so the energy labels are being redefined.
From last month (in other words March 2021), the labels are set to be rescaled and revert to an A to G grading. In addition, they will contain a QR code allowing the end user to access information on the product.
For light sources, the rescaling means that A+++ becomes C with A and B currently unattainable. However – and this is important – also bear in mind that this switch will happen from September for light sources covered by Regulation (EU) 2019/20150.
The transition to this new approach for energy labelling will enable consumers to distinguish more clearly between the most energy efficient products. At the same time, it is meant to encourage manufacturers to continue research and innovation into more energy efficient technologies.
The light source label is still being developed. But, to provide an idea of the sort of differences to expect, figure 3 above shows the existing and future labels for a refrigerator.
Figure 3. The existing (left) and future energy labels for a fridge. This example has been taken from the European Commission’s guidance [1]
p A cut-out CE mark on a product

GOVERNMENT CONSULTATION
Between November and January, the Department for Business, Energy & Industrial Strategy (BEIS) carried out a consultation process with the lighting industry in regard to the energy labelling issues discussed above [2].
This included all members of the UK Lighting Liaison Group (LLG), which consists of representatives from all UK professional organisations interested in light and lighting. We await to hear the government’s conclusions from this.
Finally, while this all may feel like a lot of change all coming at once, it is important to emphasise that, in general, the approach by the UK is to adopt the current EU regulations and labelling, so as to minimise the change needed. And this was broadly supported by those active in the consultation process.
[1] ‘In focus: A new generation of EU energy labels’, European Commission, August 2020, https://ec.europa.eu/info/news/focus-new-generation-eu-energy-labels2020-aug-13_en [2] ‘Consultation: Draft Ecodesign and Energy Labelling Regulations (Lighting Products) 2021’, Department for Business, Energy & Industrial Strategy, November 2020, https://www.gov.uk/government/consultations/draft-ecodesign-and-energy-labelling-regulations-lighting-sources-2021 Allan Howard BEng(Hons) CEng FILP FSLL is director for lighting at WSP
MINE CRAFT
Mining is one of the most challenging industrial environments in the world, and lighting is an absolutely critical component in keeping workers safe, facilities running smoothly and product flowing. Yet choosing, specifying, installing and maintaining lighting in this context is anything but straightforward
By Simone Rossi
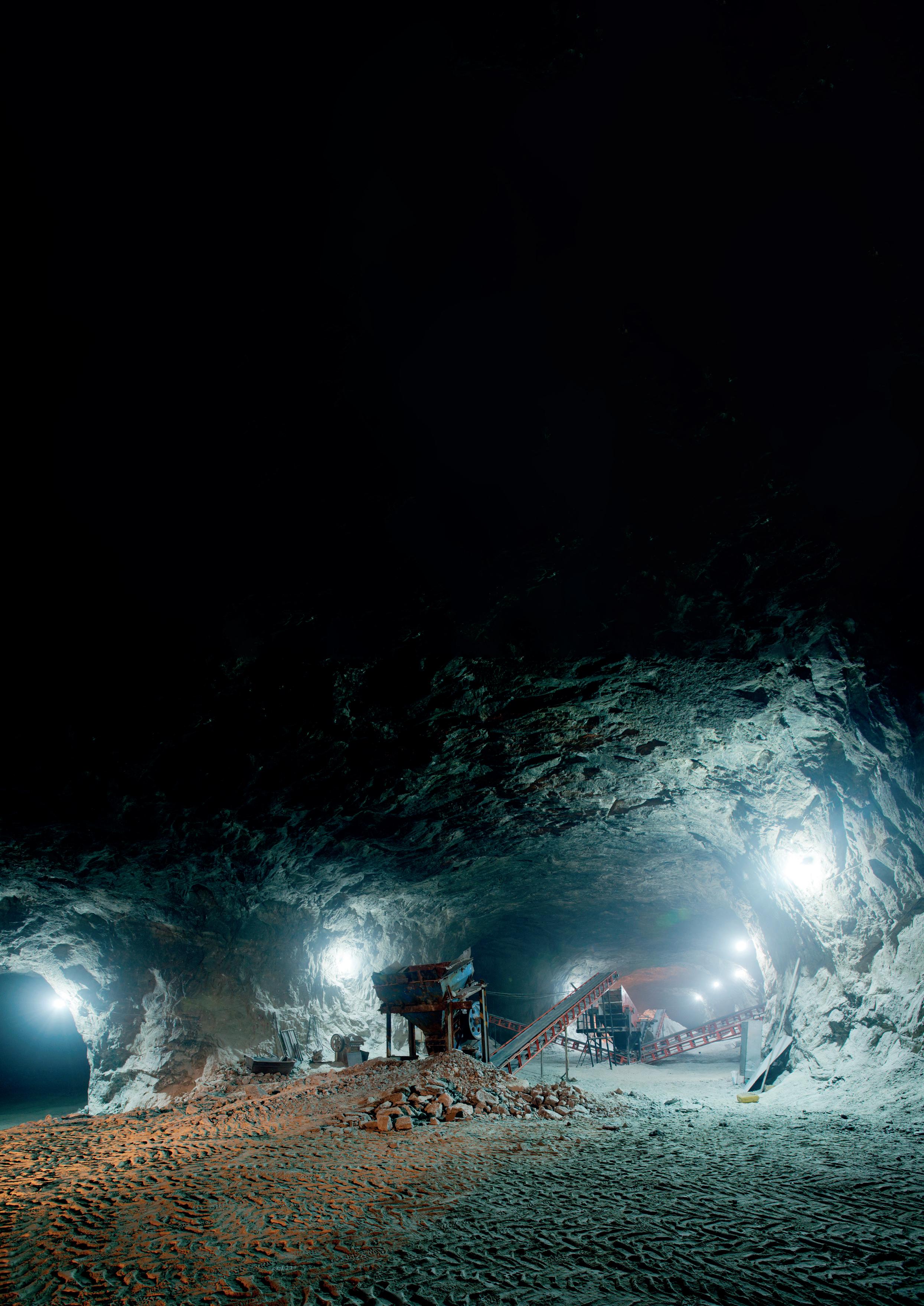
APRIL 2021 LIGHTING JOURNAL 31
Lighting harsh environments
Arguably one of the harshest and most challenging industrial environments, the mining industry plays a pivotal role in the global economy. With operators around the world continuously balancing production output, cost efficiency and employee safety, proper lighting is critical equipment in both underground and above ground extraction.
That is why mining operators depend on advanced lighting innovations and optimised lighting designs to keep their employees safe, facilities running smoothly and product flowing. But, for lighting designers, creating a plan to maximise visibility with reliable, efficient lighting can be extremely challenging.
Between environmental factors, strict regulatory standards and client protocol, lighting designers have a lot of hurdles to address, which this article intends to consider.
TOP CHALLENGES FOR MINE LIGHTING
1. Environmental hazards. Dust and airborne particles can be a dangerous source of ignition in the presence of heat or spark, especially in confined places with little ventilation and where the concentration of explosive compounds may be higher.
In such environments, any piece of equipment that may cause a spark or excessive heat would represent a hazard. These hazards can cause spontaneous combustion of both airborne particles and accumulated material on fixtures or explosions.
The risks vary depending on the type of ignition source, their concentration and the temperature at which combustion occurs. A classification of hazardous situations is provided by IEC standards and by the European Union’s ATEX Directive 2014/34/EU [1]. The IEC/EN 60079 series provide a list of types of protection manufacturers may adopt to ensure their fixtures are suitable for each class of hazardous location [2].
The most relevant kinds of protection for lighting and related components are:
• Flameproofing – preventing any explosion inside the fitting and its associated gases from reaching the outside. • Durability – improving the robustness of the fixture and thusly increasing safety. • Encapsulation – using resin, sand, powder or quartz depending on requirements. • Smart design – organising the internal components to prevent arcing or to make them non-incendiary. Designers must keep these hazards in mind, as well as other factors like humidity, the presence of chemical compounds and even coastal/caustic conditions that can cause corrosion.
2. Physical hazards. From forklifts and bulldozers through to longwall mining machines and conveyor systems, moving equipment can wreak havoc on lighting fixtures, damaging the housing or chassis from impact.
This can cause either catastrophic failure or enough damage to compromise components or damage gaskets that prevent material ingress, creating the risk of fire or explosion. For designers, robust fixture selection plays a key role in reducing these risks.
3. Accessibility. Luminaire placement can be a challenge in mining facilities. Often, where the light needs to be for ideal illumination is difficult to access – directly overtop process equipment, for example – which makes installation and maintenance difficult. Many facilities also rely on high-voltage power supplies to run equipment, which is too much for lighting. Designers have to be mindful of both accessibility and infrastructure when designing for these conditions.
4. Safety. Clear visibility is critical for keeping workers safe and preventing incidents like slip, trip and fall hazards from turning into lost time accidents, or worse. In the US alone from 2009-2018, the mining industry suffered nearly 63,000 injuries at a cost of $2.1bn (£1.5bn), and 365 fatalities, costing $373m (£273m) [3]. Better illumination has been proven to decrease workplace accident rates by as much as 60% [4].
Designers must ensure minimum luminance and uniformity requirements for the task to be performed in each location. Any vertical illumination needs must also be accounted for, along with emergency lighting. The design must take into account whether emergency lighting is to be supplied by backup generators, central battery storage or batteries integral to the luminaire in order to specify the right fixtures and layout.
5. The human element. Too often in industrial settings, we forget that humans are part of the equation. In an environment where workers put in long shifts, work overnight and perform repetitive tasks, poor lighting can impact mood and energy levels, contributing to fatigue and drowsiness, which are key factors in accidents and injuries [5].
In addition, the lighting must be comfortable on the eyes with low glare and take into account the performance and wellbeing of the people who go to work there every day.
High-quality industrial LED lighting has proven to be a robust solution, enhancing workers’ alertness and reducing fatigue [6]. And with proper design and light placement, it can produce the most vibrant, comfortable, low-glare environment.
6. Customer communication. Often, because of proprietary equipment and operational data, customers are reluctant to share all of the files and information required to produce a high-quality lighting design. This can put the designer at a disadvantage, leaving them unable fully to account for all the conditions and forcing multiple design revisions. Sometimes customers will remove files from the drawing package because they’re unsure exactly what’s necessary.
Designers must therefore be able to clarify and ask for exactly what’s needed and explain how this data is critical to the success of the project, while also being sensitive to the customers’ confidentiality concerns.
While the situation may sound daunting, there is substantial opportunity for lighting designers to positively impact mine safety, productivity and profitability through innovative lighting design and technology.
This is particularly important now, as the global mining industry works quickly to adapt to Covid-19 economic challenges and remain resilient [7].
Industrial LED lighting has become the most efficient, economic and durable lighting solution for mining applications, maximising facility safety, productivity and cost-effective operations.
Not only is it the most efficient lighting source on the market, it is also the most resilient and long lasting, providing a safer, high-performance alternative to conventional HID lighting.
But specifying industrial LED fixtures is only part of the equation. The lighting design, product selection and manufacturer you choose can have a substantial impact on project success and long-term customer satisfaction.
CONFIGURING MINING LIGHTING
When configuring industrial LED lighting designs for mining applications, designers should keep the following in mind.
1. Ask for the right information. Along with requesting all available amendable layout drawing and pictures from site, when designing for explosive environments the
Lighting harsh environments

Figure 1. Illustration of the required electrical equipment labelling for hazardous areas. The key works as follows: (1) name of manufacturer; (2) product type code; (3) address of manufacturer; (4) year of manufacture; (5) marking in accordance with directive 2014/34/EU II 2 GD – group II location, category 2 equipment, for gas and dust hazards; (6) marking in accordance with European standards – built and tested to European standards, type of protection, explosion group, temperature class; (7) CE marking, together with notified body registration number; (8) notified testing body and reference number; (9) serial number; (10) technical data; and (11) ingress protection
client should provide all details about the hazards which may be encountered on site and how they are classified in compliance with standards and regulations.
Lighting designers are not expected to be ATEX experts and the client should provide specialist advice on the type of hazards recorded on site. This also applies to emergency lighting, where applicable; the client should provide workplace emergency plans produced by a competent professional based on which the designer may make informed decisions on the type and location of lighting. If the customer is reluctant to share proprietary data, offer to sign a non-disclosure agreement to ensure that anything shared remains confidential. Starting off with thorough information can make the entire project go much smoother.
2. Specify ATEX-certified products.
Because of the airborne dust, gases and other particulate matter, mining operations require hazardous location-certified fixtures to reduce the risk of explosion or combustion.
Be sure that you understand the risk in each specific area to be lit and specify products accordingly. This is a critical safety issue, and there’s absolutely no room for compromise in this area.
Designers should ensure that the products they intend to specify are fitted with the required electrical equipment meant for hazardous areas and labelled containing the information shown in figure 1.
3. Choose durable products. Replacing damaged or burned-out fixtures often requires a production shutdown, which directly impacts profitability.
When creating a design therefore, choose fixtures that are known for their resistance to shock and vibration and proven to perform well in harsh industrial applications.
Many products carry a five-year warranty but the most durable are covered for ten years. While a more robust fixture may cost more initially, it will save the customer money and hassle by not having to replace a cheaper fixture more often.
4. Choose a specialised manufac-
turer. Because of the harsh environment and need for low-maintenance, high-durability fixtures, no off-the-shelf fixture will suffice.
Many LED fixtures are not designed or equipped to withstand volatile conditions, making them prone to premature failure, ultimately costing more in the long run.
Instead, choose specialised products from a manufacturer with a strong track record of durability in mining applications.
5. Design around emergency/egress lighting, where required. Emergency evacuation paths must be well lit at all times, so the fixtures you specify must perform well in unexpected conditions.
Consider how fixtures will be powered in the event of an outage and the maximum time of operation in those circumstances. Choosing the most efficient fixtures will ensure the longest possible operation, allowing safe exit for personnel.
7. Maximise light efficacy. Design a plan that leverages both light output (in lumens per watt) and optics for precise light placement to minimise the quantity of fixtures required. While you don’t want to skimp, obviously fewer fixtures will mean greater energy efficiency, lower upfront costs and less maintenance down the road.
CONCLUSION
Without a doubt, mine sites can be some of the most challenging industrial facilities and lighting them can be even more of a hurdle. Industrial LED lighting has become the technology of choice in mining for its durability, energy efficiency and low total cost of ownership.
But before choosing just any LED fixture for mining applications, designers must be cautious to consider the durability, safety and longevity of fixtures and select high-quality products from a manufacturer with proven reliability in mining applications.
Simone Rossi is a senior lighting designer at Dialight Europe and is an affiliate member of the ILP
[1] Equipment for potentially explosive atmospheres (ATEX), European Commission, https://ec.europa.eu/growth/sectors/mechanical-engineering/atex_en [2] Standards documentation for purchase, International Electrotechnical Commission System for Certification to Standards Relating to Equipment for Use in Explosive Atmospheres, https://www.iecex.com/publications/standards/ [3] US Bureau of Labor Statistics, National Safety Council, from an internal analysis for Dialight Europe [4] Abdou O (1997). ‘Effects of Luminous Environment on Worker Productivity in Building Spaces’, Journal of Architectural Engineering, vol 3, issue 3, September 1997, available online at https://ascelibrary.org/doi/10.1061/%28ASCE%2910760431%281997%293%3A3%28124%29 [5] Edwards L and Torcellini P (2002). ‘A Literature Review of the Effects of Natural Light on Building Occupants’, Technical Report, National Renewable Energy Laboratory, July 2002. Available online at: https:// www.nrel.gov/docs/fy02osti/30769.pdf [6] Falchi F et al (2011). ‘Limiting the impact of light pollution on human health, environment and stellar visibility’, Journal of Environmental Management, vol 92, issue 10, October 2011, pages 2714-2722. Available online at: https://www.sciencedirect.com/science/article/pii/S030147971100226X [7] Mine 2020. Resilient and resourceful: PwC’s 17th annual review of global trends in the mining industry, PwC, https://www.pwc.com/gx/en/ industries/energy-utilities-resources/publications/mine.html
DISTILLING

YOUR SOLUTION
When we think of ‘Ex lighting’, or explosion-proof lighting, we might imagine it being for an offshore oil rig or petrochemical site. But a distillery can be an equally hazardous environment, as well as often open to the visiting public, making it imperative to be specifying and considering the right lighting solutions
By Emily Faulkner
APRIL 2021 LIGHTING JOURNAL 35
Lighting for hazardous environments
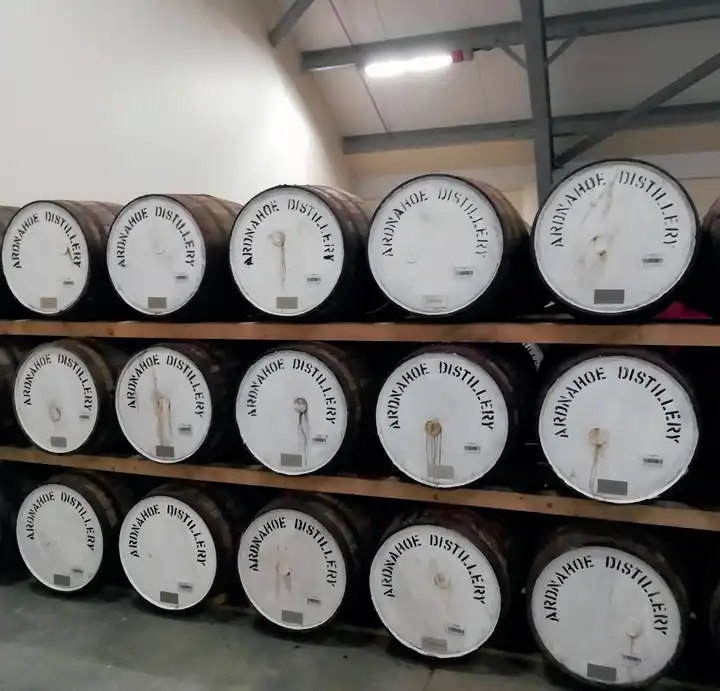
If you’re familiar with lighting for hazardous areas, you’ll know the luminaires for use in such environments are specially designed and certified for use in applications where there is a risk of explosion because of the presence of gas or dust.
Typical applications that spring to mind here include offshore oil rigs or petrochemical sites. Another interesting and challenging application that is less often thought of, however, is the use of hazardous area lighting in distilleries.
Nevertheless, the production of spirits, especially whiskey (or, in Scotland, whisky), involves several processes that can result in a potentially explosive atmosphere, including the release of vapour during distillation and storage. The correct selection of Ex lighting (or explosion-proof lighting) is therefore imperative to ensure site safety at the distillery.
Distilleries are often found in older, quirky buildings which can, in turn, present a challenge. Furthermore, and perhaps unique among hazardous area environments, distilleries have a dual role. They are both a production area for the manufacture of spirits but also often a visitor attraction. When considering the requirements for lighting, distilleries must therefore do this with both uses in mind.
Typical areas around a distillery requiring hazardous area lighting will normally include (but are not limited to):
• Grain warehouses. Within grain warehouses and silos there is always air, and the stored grain deposits layers of dust across surfaces. During loading and unloading operations, these layers can generate a dust cloud as particles are sucked up by the circulating air meaning they are commonly designated as a ‘Zone 21’ hazardous area.
This is an area in which an explosive dust atmosphere is likely to occur in normal operation [1]. • Distillation areas. The production of alcohol uses heats of up to 70degC, and the vapour it gives off mean that distillation areas around the stills and mash tuns are designated as a ‘Zone 1’ hazardous area. This is an area in which an explosive gas atmosphere is likely to occur in normal operation. • Barrell storage areas. Vapour can also be present in barrel storage, where the whiskey is stored and allowed to mature. These areas are commonly classified as a ‘Zone 2’ hazardous area. This is an area in which an explosive gas atmosphere is not likely to occur in normal operation, but if it does occur, will only exist for a short time. It stands to reason that all luminaires installed on site must comply to the classification of each area. This makes it imperative to specify the correct and most appropriate lighting in each instance.
SPECIFYING LIGHTING FOR DISTILLERIES 1. Consider LED
The benefits of LED over older lighting technologies are well-documented but are especially relevant for distillery applications. This is for three reasons, all again very well-recognised within the industry, but nevertheless worth reiterating within the very specific environmental constraints of distilleries.
• Lifetime and maintenance. Providing it uses effective thermal management, an LED luminaire can offer a lifetime of 100,000+ operating hours.
With many distilleries facing the challenge of maintaining their required levels of production, balanced with frequent visitor tours, reducing the level and frequency of maintenance is major benefit. • Energy costs. Reducing running costs is a common goal for most businesses, and LED luminaires help reduce energy costs by running far more efficiently than conventional lighting. This is beneficial to distilleries of all sizes but especially to smaller, independent distilleries. Production of whiskey is often considered to be a seasonal business, one where keeping costs down in the slower months is imperative. • Quality of light. Choosing an LED luminaire allows light quality to be improved, with LEDs capable of providing improved CRI and higher colour temperatures than conventional lighting, so drastically improving working conditions.
With many distilleries also being used as a visitor attraction, LED luminaires also provide greater flexibility in tailoring the light for each area, depending on its use. While higher colour temperatures may be ideal for production areas, warmer colour temperatures may be better suited for areas of the distillery which are used as part of the visitor tours.
2. Consider aesthetics
With distilleries often doubling up as tourist attractions, the general aesthetics of lighting in these environments is also important. This is both in terms of how the luminaire fits in with its environment and in the quality and visual impact of its light output. There are two key considerations to be thinking about here.
Lighting for hazardous environments

Raytec Zone 1 and Zone 2 ‘SPARTAN’ linear luminaires were installed throughout Torabhaig distillery on the Isle of Skye. The luminaires were given a bespoke white paint job to help them blend in with the aesthetics of the white panelled ceiling
• Physical appearance. Installing a luminaire that fits in with the architecture and design of the building is important to many distilleries, given that the overall look and feel of the building can represent the distillery’s brand image to those who visit it. The option to have the luminaires painted in bespoke colours can help them to blend in and be less intrusive, again adding to the aesthetics of the distillery/branding. A good example of this where we at Raytec have been involved is the Torabhaig distillery on the Isle of Skye, where we installed our
‘SPARTAN’ range of luminaires, but also colour-matched them to the wood panelling within the distillery. • Light output. As well as lighting playing an important functional role in the running of the distillery, it can also be used to draw attention to architectural features, or to add to the experience of visitors during tours of the distilleries. The iconic copper stills, for example, are often a focal point for many distilleries, so using warmer colour temperatures, or even coloured lenses, can help to add a deeper glow to the colour of the stills.
Warmer colour temperatures can also make areas of the distillery more aesthetically pleasing for visitors. While it depends on the personal preference of each distillery, many therefore opt for luminaires with a lower Kelvin rating in some areas, such as barrel storage or tasting rooms, to make them more inviting (while of course still being compliant with the hazardous area classification).
Selecting a luminaire that provides this level of flexibility is an important consideration when specifying lighting for a distillery.
3. Consider ease of maintenance
Specifying LED luminaires can help in reducing the frequency of maintenance required. But the way in which a manufacturer has designed the luminaire has a large impact on how easily maintenance can be carried out if it is required. There are again, two key considerations here.
• Reducing downtime. It is self-evident that minimising downtime is crucial to the financial viability of distilleries. If the lighting fails, certain parts of the production process may be unable take place because to the health and safety risks to the workers and the visiting general public.
This could have a detrimental impact on both the volume of production and the number of visitors the distillery can receive. Having a lighting solution that allows maintenance to be carried out quickly and easily on site ensures downtime is kept to a minimum.
The key to this is to specify a luminaire that has a modular design and allows maintenance to be carried out onsite. If the luminaire is sealed, however, any on site maintenance will not be possible. • Making easier access. Choosing an
LED luminaire with a removable power supply unit (PSU) can help to make access for maintenance much easier. Luminaires such as, again, our
SPARTAN high-power flood and highpower bay allow the PSU to be removed.
This, in turn, means all the wiring and serviceable parts can be positioned in easy-to-access locations. It’s not hard to see the benefit of this in the context of a common application within larger distilleries: grain storage areas.
These areas will usually have high bay luminaires mounted to (or suspended from) the ceiling of the storage building. With non-modular lighting installed, gaining access to the luminaire may require the grain to be removed before maintenance is carried out. This is, of course, a slow and costly process.
On top of this, even if the luminaire can be accessed without needing to remove the grain, carrying out maintenance with the grain still below is risky; it could lead to it becoming contaminated if anything falls while maintenance is being carried out.
In contrast, being able to mount the PSUs remotely means maintenance can be carried out at ground level (with no risk of contamination), and the grain does not have to be removed. Ultimately this means maintenance can be done quicker, at a lower cost and risk.
Lighting for hazardous environments
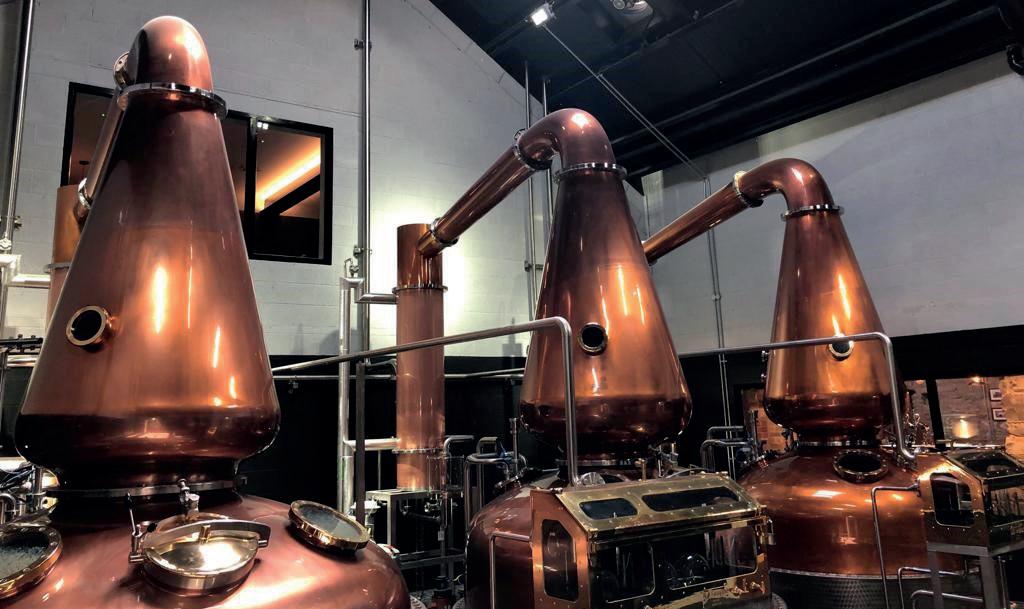
A distillery’s iconic copper stills can be enhanced by using LED lighting around the still areas. Here, Raytec ‘SPARTAN’ linear luminaires can be seen at Teelings distillery in Ireland and (main image page 34) at Ardnahoe distillery on the Isle of Islay
4. Consider emergency lighting
Clean fresh water contributes to each whiskey’s flavour. It is an essential ingredient of the distillation process and means distilleries are often located in hard-to-access locations, such as remote Hebridean islands where power cuts and longer outages can be more frequent.
This, naturally, makes emergency back-up lighting an absolute necessity to maintain the safety of everyone on site and to provide back-up illumination in the event of a power outage. This is especially important to any distillery that is also open to the public. There are two main considerations to be thinking about here.
• Duration and output. To ensure an emergency luminaire will provide back-up illumination for the required length of time, it is important to check the emergency duration when specifying.
Consideration should be given to the level of light output the luminaire provides while operating in emergency mode. This is usually expressed as a percentage of the luminaire’s output in normal operation, and it is common for output to drop significantly when in emergency mode.
To use our SPARTAN range again as an example, the emergency luminaires in this range provide 25% light output for three hours as standard but can also offer up to 100% output for a shorter duration if required.
The duration and intensity of output is often specific to individual applications, so this flexibility can be an important benefit. • Automated testing. Some manufacturers are now providing emergency luminaires that increase safety and reliability of emergency systems.
These ‘intelligent’ systems provide emergency luminaires with a self-testing function that automatically cycles the emergency battery.
This, in turn, helps to maintain the battery’s health and also measures its capacity to ensure the luminaire is operating at its optimum. This functionality reduces the requirement for manual intervention, while the inspection of emergency luminaires is also made easier. An LED indicator is used to communicate when the unit is going through a testing procedure and highlights the overall health status of the luminaire.
5. Consider lighting design
Lighting design is another essential part of specifying lighting within distilleries. The nature of distilleries means walkways between hot stills need to be well lit and any pipes or other distillation equipment need to be clearly illuminated to maintain the safety of workers and the visiting public.
For specifiers going through the initial design process with a clear brief in mind, a carefully thought-through lighting design will provide peace of mind that the final solution will achieve the required on site lighting goal, with no surprises at the point of commissioning.
Without wanting to end on too much of a ‘plug’, at Raytec, for example, we offer clients a free lighting design service alongside our manufacturing services.
This includes a 3D visual representation of the final lighting solution, with detailed lux levels and a true indication of lighting performance as well as one-to-one design support. In a challenging environment such as distillery lighting, we find this sort of end-to-end support is very much valued by clients.
Emily Faulkner is a marketing executive at Raytec
GETTING FIT

FOR THE FUTURE
What should have been a relatively straightforward LED upgrade of a leisure centre in Wales proved more complicated because of, you’ve guessed it, the country being plunged into lockdown last year. But the results nevertheless herald a (hopefully) more positive future all round
By Liz Hudson
APRIL 2021 LIGHTING JOURNAL 41
Sports and interior lighting
Plas Madoc is a leisure centre with a story. The centre began life as a council-run facility and, with its huge family-friendly offering, quickly cemented itself as an essential presence within the local community.
However, due to local government cuts and despite its popularity, the leisure centre was sentenced to closure in 2014. It was at this point that the community took matters into its own hands and formed a not-forprofit organisation to keep the leisure centre alive, and in December 2014 it was officially reopened by the Splash Community Trust, gifted to the community by Wrexham County Borough Council.
Since the transfer of ownership, Plas Madoc Leisure Centre has gone from strength to strength, winning ‘Social Enterprise of the Year’ in the 2018 Social Business Wales Awards. A core ongoing goal for the Splash Community Trust is continuously to find ways to drive down costs and improve efficiency, yet without compromising on service, facilities or quality.
This has seen it improving the heating systems and wave machines in the pool area but also working to upgrade its lighting.
It was to achieve this goal that the team turned to Carbon Reduction Technology, largely because of its acquisition in early 2019 of the Waveguide light injection luminaire range.
The leisure centre had installed several Waveguide luminaires at an earlier point in time and the team was keen to use the same technology throughout the rest of the building.
Light injection luminaires, which are ultra-uniform and low glare, are particularly well suited to this sort of environment, as leisure centres tend to be full of shiny floors and surfaces as well as areas that require extremely even, shadowless illumination, such as squash courts.
The client had three clear primary goals in mind at the outset of the project:
1. Streamline operating costs 2. Improve the aesthetic of the facility and the light quality in active areas 3. Reduce its carbon footprint
WORKING AROUND COVID-19
Coronavirus, naturally, threw a major spanner in the works, as it did for most UK businesses in 2020, causing operational problems and shutting down activity.
Lockdown landed smack bang in the middle of the Plas Madoc installation, halting forward progress while the centre closed to comply with government restrictions.
Installation had begun in February 2020 and, to mitigate the pandemic’s impact, the Carbon Trust offered an automatic extension to its usually rigorously strict 12-week installation requirement. In the event, however, the project was not officially completed until last September, making Plas Madoc CRT’s longest single installation!
Fortunately, we had already planned for the installation to be modular, with different zones inside the building being upgraded in a phased rollout. This was strategically designed to reduce as much impact on the day-to-day running of the centre as possible, which in normal times opens seven days a week.
As well as disruption from lockdown restrictions preventing personnel from attending sites to survey, install or maintain, the Covid-19 pandemic also caused major supply chain issues, affecting manufacture, component sourcing, air freight, sea freight and customs.
Following the first return-to-business last summer after the first lockdown, both the centre and CRT had some adjusting to do in order to continue to rollout the upgrade safely and in a legally compliant manner.
This began, as all things do, with a detailed risk assessment, action plan and policy documents. When we were ready to put the installation team back on site, Covid-safe procedures had to be followed to the letter to maintain the safety of the Plas Madoc staff, the general public and the install team.
Of course, every cloud has a silver lining. The pandemic did provide a rare opportunity for our photographer to capture a totally empty facility post installation. Observing, of course, all Covid-safe guidelines and laws.

The Plas Madoc team installed Waveguide luminaires throughout the centre following a successful trial in the sports hall. Opposite: custom blue filters were added to the luminaires lighting the pool area ceiling to give an outdoor feel
A MODULAR ROLLOUT
Despite the pandemic-related delays and pauses in installation once the centre was able to reopen its doors to members, there was no further forced closure before the project was completed.
Sports and interior lighting
The newly illuminated climbing wall. The sports centre is a community hub and offers a huge range of sports and activities

CRT approaches almost all installations in a modular manner – a tactic designed to allow our clients to continue to operate safely and with as much capacity as possible whilst the installation is in progress.
Unless a facility has regularly scheduled downtime sufficient to complete a retrofit, it’s usually unfeasible for a business to halt trading and shut down to accommodate a lighting upgrade.
This modular approach, in fact, proved ideal for adapting to a Covid-safe install strategy. The centre was divided into zones, which were isolated, closed and reopened one by one. This had the added benefit that, even with manufacturing and freight delays, we could continue to upgrade areas in full with the assets we had, leaving the original lighting temporarily in place in the zones affected by delays. This all ensured the lights stayed on and the leisure centre remained functional and safe for members.
SPOTLIGHT AREAS
The centre has an extensive range of facilities and spaces, including a soft play area, climbing wall, swimming pool, gym, sports hall, fitness class space, café, squash courts, offices, changing rooms, staff areas and common areas.
All interior spaces required a lighting refit, plus the exterior of the building using the pre-existing poles.
Leisure centres present a variety of lighting challenges and interesting or complex spaces, all of which require slightly different approaches to achieve the best results. We’ll look at some of these different areas in turn.
1. Squash courts. Squash courts are a particularly interesting space to light, as a large area of the court – including the floor and most of the walls – is playable area and needs to be evenly lit to provide excellent visibility of the ball, which is only about 40mm in diameter and can move at well over 100 miles per hour!
As you might imagine, it’s also vital for squash court luminaires to be smash proof.
Fortunately, the structure of Waveguide luminaires is particularly well-suited to lighting a broad area, not just below the luminaire but to the sides and, to a degree, above where required.
The luminaire is projecting light to the sides and above the fitting, rather than just in a downwards direction. We turned the outer tubes in the fitting to project out and up.
Light is injected into flawless acrylic rods, which act as mixing chambers and project exceptionally low glare and uniform illumination. The shape and spread of the illumination is controlled by a precise reflective coating applied to the rod.
The luminaires are made up of multiple rods and, by twisting the outer rod in the luminaire, we were able effectively to light the upper walls and corners of the courts without the need to install additional lights fittings. 2. Swimming pool. Plas Madoc has a large pool area, complete with water slides. This area came with a special request to light the roof area blue, so as to simulate the sky and give the area a more outdoor feel. A high lighting standard is also critical in areas such as swimming pools to properly support safety.
The deep end of the swimming pool was the only area where we added a small number of additional luminaires, as the previous lighting design didn’t provide sufficient scope for us to achieve even enough lighting.
To achieve the required blue lighting effect, we adapted the luminaires with custom blue Perspex filters.
3. Spiral staircase. The centre has a spiral staircase in the reception area, which was added on to the project in a later stage. The staircase was originally lit with eight spotlights, running at 300w each.
During the course of the upgrade, these lights were removed, leaving gaps in the ceiling where the fixtures had been situated. Although the staircase was safely lit by the new lighting layout, CRT and the Plas Madoc team decided to put in new high-efficiency luminaires to showcase the staircase.
Eight new custom spotlights were therefore installed, running at 14w each, with the emphasis on aesthetic.
4. Emergency lighting. In addition to retrofitting the lighting throughout the entire Plas Madoc facility, we also
A Trading Division Of

We offer a wide range of services including structural analysis and non-destructive testing on lighting columns and structures.

Our services combine Fabrikat’s extensive knowledge within the engineering industry with the latest technology to provide you with superb services, tailored to your needs.
Collectively our team have over 100 years’ experience in the NDT and Streetlighting industries.
3D printing for rapid prototyping and on site 3D scanning are among some of our most recent advancements we can offer.

Neoterik® is a trading division of Fabrikat (Nottingham) Limited. Our core business is the provision of engineering services that include on-site testing of streetlighting infrastructure, asset data collection and surveying.
We employ a number of highly skilled engineers within our engineering services division who are members of the British institute of Non-Destructive testing, and hold a PCN Level 2 in accordance with EN ISO:9712. Introducing Our Innovative Purpose Built IOS And Android App

Testing In Accordance with GN22. Column Data And Attribute Collection
Easy Access Customer Portal
External Influence And Condition Analysis
Column Material Analysis
Sports and interior lighting
The gym area. The low glare light injection approach of Waveguide technology works well for these sort of high occupancy areas
installed a new emergency lighting system.
Emergency lighting is of course a legal requirement, and requires the installation of drivers and battery packs into luminaires at strategic points along escape routes. These are designed to trigger automatically in the event of an onsite power failure.

RESULTS
Let’s gauge the results for this project on three measures: performance, light quality and financial.
1. Performance. While the management team identified several key goals for the upgrade, the primary objective was to achieve a significant reduction in energy expenditure. To that end:
• Tonnes of CO2 saved per year: 36 tonnes • Sitewide energy saving: 78% • Energy saving in kwh: 127,000kwh (reduced from 163000kwh to 36000kwh) • Average reduction in wattage per luminaire: taken as an average across the whole site, we reduced power by 107w for every luminaire
2. Light quality. A key concern for Plas Madoc was improving the light quality and aesthetic. Generally speaking, a busier, more modular floorplan and part-time operating hours can reduce the savings potential when compared to, say, a manufacturing facility. For Plas Madoc, as a leisure centre, it was able to recoup some of these savings by opting for a high colour temperature, which is very much standard in the leisure industry.
The management team also opted not to have the lighting scheme layout altered for maximum efficiency, although we were still able to achieve a 9% reduction in lighting fixtures. The light quality changes were:
• Colour temperature: 5000K • Lux levels: Approximately a 30% improvement
3. Financial. Despite Plas Madoc having only part-time operating hours, the savings and paybacks have been impressive.
The centre is set to recoup the cost of the project through energy savings in just 34 months; as the payback term with the Carbon Trust is five years. This means Plas Madoc will see an immediate saving on its bottom line on a monthly basis, even with its finance commitment.
As we expect our luminaires to last in excess of 20 years, the leisure centre will be enjoying the financial benefits of its upgrade for a long time to come. In more detail, the savings amount to:
• Operating hours: eight to 12 hours per day, seven days per week • Payback: 34 months • Carbon Trust payback: five years
CONCLUSIONS
The Plas Madoc Leisure Centre and Splash Community Trust team were a genuine pleasure to work with, driven, as they are, by an extraordinary group of people with a strong sense of vision and a firm grasp on making energy efficiency work.
Coronavirus continues to make times feel turbulent and uncertain for most small and medium-sized businesses, but as we, hopefully, now start to come out of the pandemic, the government’s renewed commitments to cutting and neutralising carbon emissions means there will be an ever-greater imperative for businesses of all sizes to be finding ways to reduce carbon footprint, with more energy efficient lighting one important option.
Liz Hudson is head of marketing at EW Business Development & Marketing, and works with Carbon Reduction Technology
