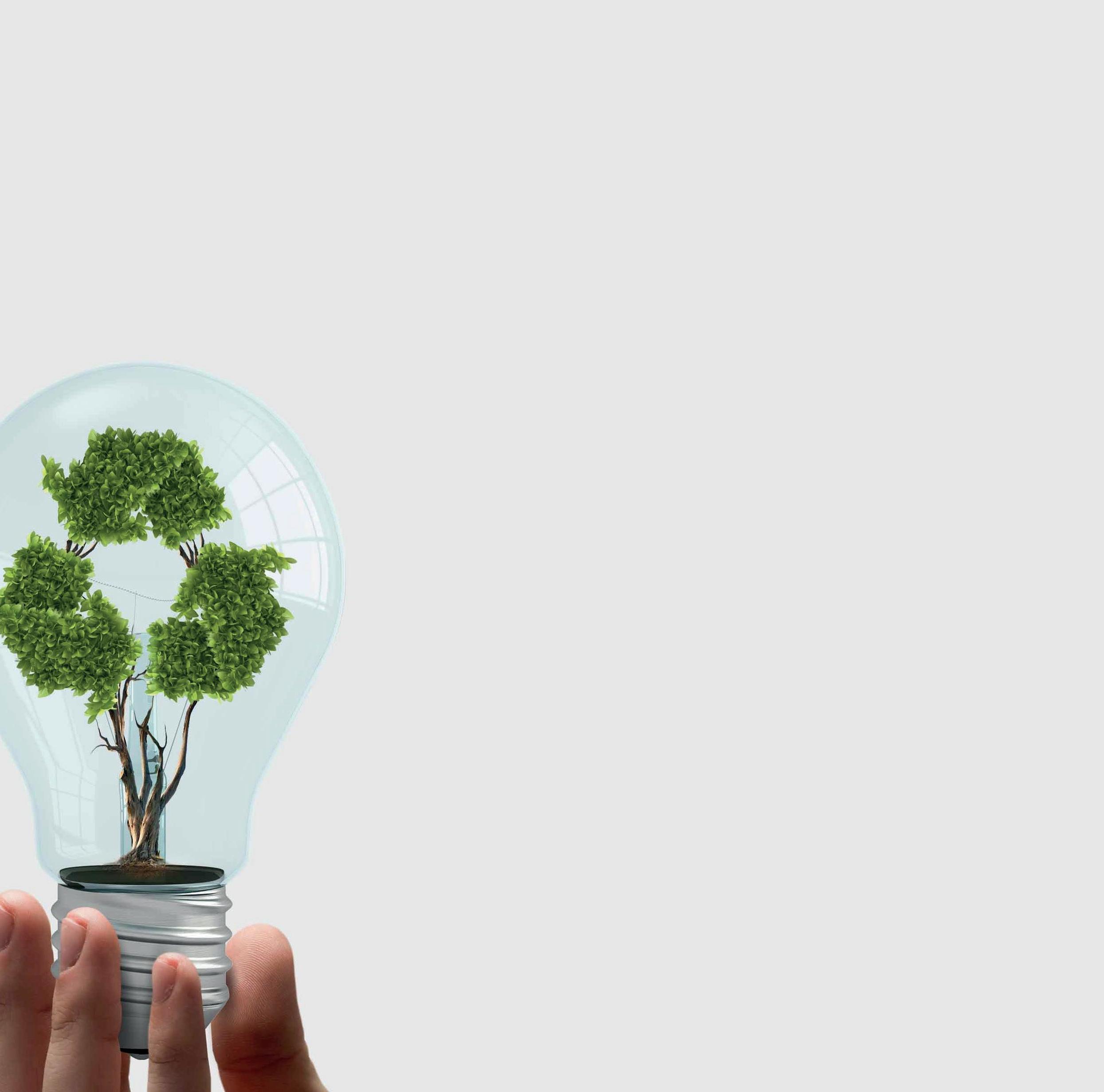
6 minute read
x SERVICE ECONOMY?
SERVICE ECONOMY?
Lighting has come a long way in terms of recycling and reuse, but there is still much that needs to improve across all electrical industries. Lighting as a service and product leasing schemes may all, for example, need to become more commonplace in the future
By Bryony Light and Alex Brothwood
This coming November the UK will host the 2021 United Nations Climate Change Conference, which new US climate envoy John Kerry has called the world’s ‘last best chance’ to avert climate catastrophe.
A key, and increasingly urgent, part of the climate change discussion is resource depletion. This is an area where it is vital all of us within the lighting industry work to achieve and maintain standards of compliance; that we prioritise responsible conservation of the environment, ensure less plastic is used, that rare materials are not lost, and that as much as possible is recycled or reused.
INDO Lighting is committed to manufacturing products that are more sustainable, using high-quality materials and components, making them much easier to recycle at treatment facilities and allowing better quality ‘recyclets’ to be recovered and sold back into the supply chain.
LEGAL RECYCLING OBLIGATION
Furthermore, INDO products are ‘Direct Drive’, which means there is no driver. This results in units that not only are easier to treat and recycle but means end-users don’t need to pay for the replacement of expired drivers midway through a unit’s lifetime or oversee an additional waste obligation.
As most lighting professionals will probably be aware, there is also a legal obligation here. The lighting supply chain must ensure all lighting is treated and disposed of correctly by approved recycling facilities. Manufacturers placing more than five tonnes of electronic goods on the market per year have to join a producer compliance scheme (PCS) to manage this obligation on their behalf.
Within UK street lighting, Lumicom is the largest PCS operating, and has the majority of manufacturers in the UK as active members.
The scheme is well-established in the
APRIL 2021 LIGHTING JOURNAL 51
Lighting and recycling
market, with the team working in partnership with contractors, street lighting manufacturers and their recycling partners to provide an end-to-end, fully traceable, recycling service. Importantly, by using a PCS, manufacturers can have peace of mind that they have the correct paperwork in place to be compliant under ISO 14001 and the Waste Directive 2011.
However, this kind of ‘bread and butter’ recycling, while important, is just part of the wider environmental conversations we now need to be having within the industry.
As was highlighted in Lighting Journal last month (‘Green governance’, vol 86 no 3), the government plans later this year to consult on reforms to the WEEE waste and recycling regulations. The likelihood is this will close some of the loopholes (for example products sold through online marketplaces) and opt-outs that some businesses are currently able to take advantage of.
USE OF ‘FOREVER CHEMICALS’
So, the landscape is already changing. Within this, there is a further issue in lighting manufacture around the use of persistent organic pollutants (POPs). POPs are sometimes known as ‘forever chemicals’, and are organic compounds resistant to environmental degradation and are classified as hazardous waste.
In street lighting, POPs waste is seen in the form of brominated flame-retardant plastic (which is used in a lot of electronic equipment). Bromine doesn’t break down naturally and has to be removed from the supply chain completely.
However, the track record of the industry when it comes to POPs is actually very positive. Lumicom has researched and tested 75 variants of luminaire dating back from the 1970s to the modern day and found bromine levels well below the threshold limit (1,000 parts per kilo) across all samples.
To that end, Lumicom was instrumental in alerting the government to this fact and having street lighting reclassified as non-hazardous’. It is in fact the only electrical category (other than refrigerators) to be so classified.
Declassifying street lighting waste as hazardous in this way offers the practical benefit of reducing the cost of collections. Collecting POPs waste is significantly more expensive to transport, and subsequently treat, per tonne. On collection alone, for example, hazardous transport permits are required in addition to a hazardous waste consignment note for each load, which can cost up to £60 per collection. This would be a considerable cost that would have to be passed back to the producer.
As was also recently highlighted in Lighting Journal, (‘Squaring the circular’, January
2021, vol 86, no 1), the idea of the ‘circular economy’ is gaining traction, and widescale acceptance, within the industry.
Ideally, recycling through a waste stream should be the last option when a product reaches the end of its useful life, after remanufacturing, reusing and repurposing parts; be that for upgrades to the same product or as components for new products or new markets.

NEW ‘TAKE-BACK’ SCHEMES?
Moving to a more circular economy at the moment, however, is a stage that is currently missing for many within the industry, and something that needs added focus, discussion and action if we all want to move forward to effect real environmental change.
As time goes on, and debate in this area intensifies, there will be pressure on public spending to incorporate additional steps into product design, client specifications and asset management plans to reflect these changes.
Ultimately, more product will need to come back to the manufacturer to reuse and repurpose the parts, quite possibly under various ‘take-back’ schemes such as offering lighting as a service, or a product leasing business model.
We’re already seeing this evolution happen in other industries and sectors. For example, broadcaster Sky leases its box rather than selling it to the customer. This way Sky retains ownership and can easily manage refurbishment, reuse, parts-harvesting or recycling.
Or, similarly, HP’s ‘Instant Ink’ subscription service allows for new print cartridges to be sent out and old ones returned by Freepost to be reused or taken down to component parts. The likelihood is that a similar evolution may start to be seen in lighting and lighting manufacture.
CONCLUSIONS
Technological and regulatory shifts within this space are, it is clear, imminent. Lighting has come a long way in terms of recycling, but there is still much that needs to improve across all electrical industries.
This is an area where you can never afford to sit still. For example, at INDO we are currently reviewing the recycling position for our horticultural lighting business, as we recognise this is a commercial lighting sector that needs to address these critical issues as we head into a new era of using LED lighting for more sustainable food production.
With climate change and environmental responsibility becoming so critical for future generations, it is essential that manufacturing companies – lighting manufacturers included – change their mindset and be more consistent about reuse, repurposing, harvesting, recycling and waste. We all need to accept and account for this change within our business, just like any other ‘cost of sales’ entry on the profit and loss statement.
Bryony Light is marketing manager at INDO Lighting and Alex Brothwood is business manager at Lumicom