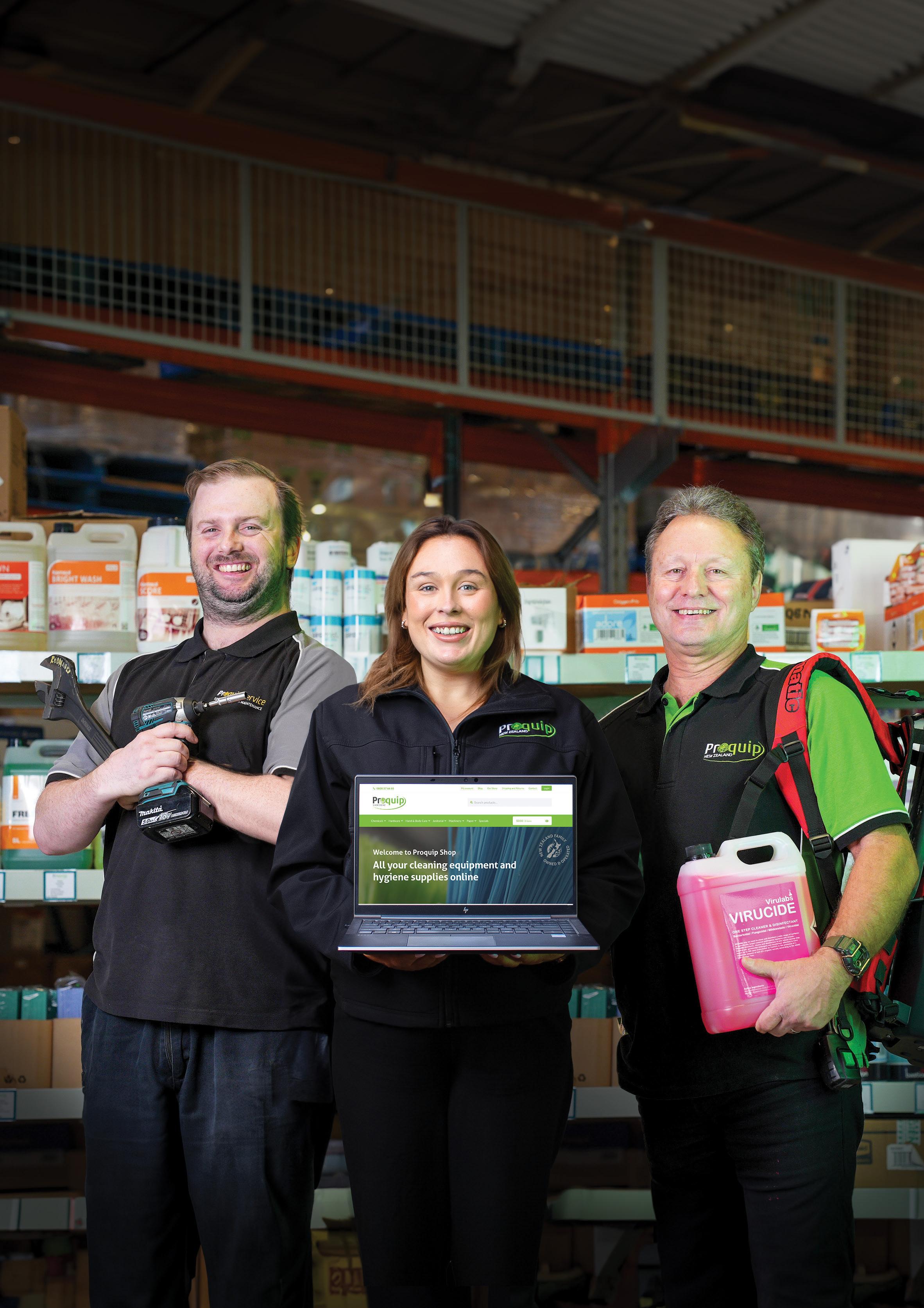

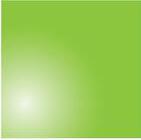
The D.Zero² suction sweeper has been produced to the latest design and ergonomic concepts, with a small impact on the environment both for the reduced use of water and for the emission of dust and noise. The machine is characterised by a traction system and electric sweeping services supported by lithium iron phosphate batteries (LiFe PO4) designed and produced based on a Dulevo project.
INCLEAN NZ is published by The Intermedia Group Pty Ltd on behalf of ISSA – The Worldwide Cleaning Industry Association. 41 Bridge Road, Glebe NSW 2037 Australia
PUBLISHER:
Simon Cooper
MANAGING EDITOR:
Claire Hibbit
E: chibbit@incleanmag.com.au
P: +61 2 8586 6140
ADVERTISING MANAGER:
Samantha Ewart
E: sewart@incleanmag.com.au
P: +61 2 8586 6106
PRODUCTION MANAGER:
Jacqui Cooper
PRODUCTION ASSISTANT:
Natasha Jara
ART DIRECTOR:
Chris Papaspiros
NEW ZEALAND SUBSCRIPTION RATE:
12 months (4 issues) – NZD $44.00 (inc GST)
To subscribe call +61 1800 651 422
E: subscriptions@intermedia.com.au
The countdown is on for the 2023 ISSA Cleaning & Hygiene Expo taking place on Wednesday, 1 November and Thursday, 2 November at the Melbourne Convention and Exhibition Centre (MCEC).
This year, the event is set to be bigger and better than ever after securing a larger space at the MCEC to accommodate the growing number of participants. In addition to the expanded space, the expo will also feature a range of interactive activities and educational sessions, allowing visitors to learn about the latest industry trends and technologies. Check out what’s on in our show preview on page 18.
Also in this issue, we look at the growing rise of AI-powered robotics. Despite being the subject of criticism in years past, a new breed of autonomous cleaning machines is being rolled out in New Zealand and Australia as building services contractors and facility managers seek to save time and achieve better cleaning and hygiene efficiencies.
In fact, the demand for cleaning robots is only getting bigger with research suggesting the international market will reach US$24 billion by 2026, achieving 22.9 per cent compound annual growth rate (CAGR).
INCLEAN NZ is owned by ISSA
ABN: 44 617 407 020
P: +61 2 9890 4951
A: Suite 1, Level 1, 52 O’Connell Street, Parramatta, NSW, 2150 W: www.issa.com
DISCLAIMER: This publication is published by The Intermedia Group Ltd (the “Publisher”). Materials in this publication have been created by a variety of different entities and, to the extent permitted by law, the Publisher accepts no liability for materials created by others. All materials should be considered protected by New Zealand and international intellectual property laws. Unless you are authorised by law or the copyright owner to do so, you may not copy any of the materials. The mention of a product or service, person or company in this publication does not indicate the Publisher’s endorsement. The views expressed in this publication do not necessarily represent the opinion of the Publisher, its agents, company officers or employees. Any use of the information contained in this publication is at the sole risk of the person using that information. The user should make independent enquiries as to the accuracy of the information before relying on that information. All express or implied terms, conditions, warranties, statements, assurances and representations in relation to the Publisher, its publications and its services are expressly excluded. To the extent permitted by law, the Publisher will not be liable for any damages including special, exemplary, punitive or consequential damages (including but not limited to economic loss or loss of profit or revenue or loss of opportunity) or indirect loss or damage of any kind arising in contract, tort or otherwise, even if advised of the possibility of such loss of profits or damages. While we use our best endeavours to ensure accuracy of the materials we create, to the extent permitted by law, the Publisher excludes all liability for loss resulting from any inaccuracies or false or misleading statements that may appear in this publication.
Copyright © 2023 - The Intermedia Group Ltd
This trend is undoubtedly being driven by better technology, as well as rising labour costs, and the requirement for superior cleaning results in the wake of the pandemic.
Read how New Zealand building services and facility managers are exploring the ways cleaning robots can deliver quality, efficiency, and sustainability benefits in our automation feature on page 34.
In this issue we also turn our attention to employee burnout among first responders and front-line workers. Burnout has become an issue for many industries, including the cleaning, hygiene, and restoration sectors.
According to a global Future Forum Pulse survey of more than 10,000 respondents, burnout among employees is on the rise internationally, especially among women, young workers, and middle managers.
As a result, mounting pressure that is being placed on leaders to implement supportive workplace solutions.
We speak to experts on how employers can help play a key role in preventing employee burnout and improving wellbeing.
Happy reading!
Claire Hibbit Managing EditorCMS Berlin
19-22 September 2023
The international conference and exhibition will take place in Berlin www.cms-berlin.de
ISSA Cleaning & Hygiene Expo
1-2 November 2023
Australia’s premier trade event for the cleaning and hygiene industry will be held at the Melbourne Convention and Exhibition Centre (MCEC) www.issacleaninghygieneexpo.com
ISSA Show North America
13-16 November 2023
Vegas will play host to the industry’s largest event of the year www.issa.com
March 26-29, 2024
Expo
The flagship exhibition returns to Shanghai in 2024
www.chinacleanexpo.com
Interclean Amsterdam
14- 17 May 2024
Leading manufacturers and industry professionals to gather in Amsterdam www.intercleanshow.com/amsterdam/
www.incleanmag.co.nz
Solenis finalises purchase of Diversey for $4.6 billion Specialty chemical manufacturer Solenis, a portfolio company of Platinum Equity, completes acquisition of Diversey.
Health impacts of shift work exposed in new global survey
International study spanning 32 countries across six continents highlights the negative impact of shift work on the health and wellbeing of cleaners.
New research by World Vision New Zealand reveals many businesses are oblivious to the role of forced and child labour in their production processes.
ISS survey highlights need for positive workplace culture
While 69 per cent of workers feel a sense of belonging at work, half report feeling unable to share opinions freely and treated unfairly at the workplace.
OfficeMax to phase out petrol cars in latest sustainability initiative
OfficeMax New Zealand to phase out fleet of conventional cars by the end of the year, instead embracing electric and hybrid models.
Commission grants clearance for Henkel to acquire Earthwise brands
Commerce Commission grants clearance for Henkel New Zealand to acquire Earthwise brand and business from Earthwise Group Limited.
In a market full of choice, it’s important to know that you’re using high performance commercial cleaning equipment and consumables that will deliver under pressure, day after day. At Proquip, performance extends beyond their comprehensive product range. Find out more about Proquip’s market-leading services on page 14.
More than 90 local and international exhibitors showcasing their latest products, services and innovations
The education program will run over two days and feature 40 speakers, 16 freeto-attend speaker sessions, plus onsite workshops
Explore key topics such as technology and innovation, infection prevention, cleaning for health, supply chain, environmental and sustainability needs and workforce development
A 33% increase in the show floor making this the largest ISSA Cleaning and Hygiene Expo to date
An opportunity for companies to bring their teams to broaden industry knowledge and support employee development
Network with industry manufacturers, distributors and wholesalers at the exhibition hall or during informal networking events
Learn the best industry practices and uncover the latest innovations at the INCLEAN EXCELLENCE AWARDS 2023
Makita is committed to developing solutions for cleaning teams and facilities maintenance.
With over 100 years of motor engineering and more than 40 years of cordless innovation, Makita’s leading cordless technology offers freedom from the cord for maximum convenience, access to hard-to-reach spaces, and completing tasks quickly and easily. As a leader in cordless products, Makita offers more cordless solutions than the rest to get the job done.
Makita pride itself on purpose-built cordless solutions, conducted years of research and development to provide innovative cordless solutions. Each product is meticulously designed with intent and attention to detail to provide optimum efficiency, power and run time. Makita’s products are also engineered to provide superior ergonomics and less weight for a better user experience.
Makita’s unsurpassed quality drives down the cost of equipment ownership and maintenance. Cordless cleaning products allow users to easily navigate around busy offices, crowded stores, and tight stairwells without searching for outlets or creating trip hazards. Makita cordless cleaning products weigh less and are ergonomically designed to reduce operator fatigue and injury.
CLEAN MORE WITH THE ALL NEW LXT® BRUSHLESS ROBO CLEANER PRO
The 18V LXT® Brushless ROBO CLEANER PRO is a cordless solution that automatically cleans large flooring spaces in commercial environments.
The 18V LXT® Brushless ROBO CLEANER PRO is equipped with room mapping technology for improved cleaning
efficiency. Advanced control mapping, priority cleaning and remote-control functions can be used to clean targeted areas all from the special design Makita smartphone app.
The DRC300 features LiDAR sensor (2D) detects and memorizes the 2D shape of a room, with its built-in camera sensor that detects the shape of walls and obstructions, gives the ROBO CLEANER PRO the ability to map out and memorize the most optimal route for efficient cleaning of up to 5 rooms at a size of up to 10,000m² per a room.
A purposely built smartphone app, gives the user the ability to view a complete cleaning history, such dates and times of cleaning, percentage of area cleaned by the DRC300 and the ability to manually adjust the cleaning map to target areas missed or high traffic area that need to be prioritised by the unit.
User can use the app to remote control the ROBO CLEANER PRO as well as selecting areas that are not required by the DRC300.
Other features of the 18V LXT® Brushless ROBO CLEANER PRO include a three-litre dust box, LED filter maintenance warning light and large side brushes that enable to clean alongside walls, around obstacles or tight corners.
As a leader in cordless products, Makita offers more cordless solutions than the rest to get the job done.
Get increased productivity with Makita LXT Cordless Vacuums. With a Rapid Optimum Charger, LXT Batteries charge fast, keeping users moving through a job with less downtime.
Makita LXT is a complete system with proven battery technology, innovative brushless motor engineering, and exclusive communication technology that allows the tool and battery to communicate during use, for maximum cordless performance.
Makita-built brushless motors efficiently use energy to provide cordless products with longer run times.
Makita is aware of the increasing demand in cleaning teams wanting more battery-powered cleaning options for a more demanding jobsite and we are meeting this demand with an expansive line of vacuums, in our 40V | 80V max XGT System. XGT® outpowers, outsmarts, and outlasts the rest.
Through Makita’s innovative engineering, the technology within XGT® will lead to creating the equipment and tools of the future. The 40V | 80V max XGT® system is engineered for high-demand applications with 40V max and 80V max XGT® Products, pros can fully experience a battery-powered job site. ■
To find out more visit: www.makita.co.nz
“
Makita cordless cleaning products weigh less and are ergonomically designed to reduce operator fatigue and injury. ”
Diversey ANZ has announced the appointment of Michelle Miles as Australian and New Zealand Country Lead.
Miles has been part of the Diversey team for more than 12 years working in multiple countries including South Africa and New Zealand, and is excited to take on this new role, her appointment will primarily require her to lead the Australian team.
Miles said she was looking forward to moving the Diversey ANZ business into the future.
“Leadership is my passion and I believe in the attributes of being decisive, forthright, results orientated and an empowerment advocate,” Miles said.
“In Australia we have expanded our operations with the new plant in Victoria to better serve our key markets. After the pandemic we remain focused on serving the needs of our customers with better solutions and products that will help them win in the marketplace. I am thrilled by the opportunity to lead the business.”
Diversey is a global provider of commercial cleaning, sanitation, and hygiene solutions. The company employs approximately 9000 people globally, generating annual net sales of approximately $2.7 billion.
CrestClean has launched its own healthcare cleaning standard, to meet a gap in the New Zealand market.
The ‘HealthClean’ standard is a comprehensive set of systems, processes, and standards that enable CrestClean franchise teams to clean effectively in healthcare environments.
It was introduced to endorse CrestClean’s specialist healthcare cleaning training, for medical centres, private hospitals. and other healthcare facilities.
Liezl Foxcroft, who heads the commercial cleaning company’s training organisation, the Master Cleaners Training Institute, explains that New Zealand does not have an industry body that ‘governs’ cleaning.
Cleaners on healthcare sites tend to get trained by hospital nurses, infection prevention specialists or nurse educators, with an emphasis on the reprocessing and steralisation of medical equipment, however, there is not always the time and resources to cover the cleaning of general surfaces and spaces that are closely associated with sterile areas, says Liezl.
“New Zealand Qualifications Authority (NZQA) training is provided through Careerforce, but it takes 11 months to complete the basic cleaning qualification, and then you add on infection prevention and control as a separate qualification. In a lot of cases, cleaners change employers before they
finish the qualification, and the funding to complete it doesn’t follow them.”
Developed by a cleaning standard working group of infection prevention and control experts, HealthClean is based on the South Australian Cleaning Standard for Healthcare Facilities 2021, which is adhered to by many of New Zealand’s private hospitals.
CrestClean has always trained its franchisees in the basics of infection prevention and control, but the new standard and training provides an added layer of protection for healthcare customers and their patients, says Foxcroft.
“Cleaning is like a three-legged stool, the three legs being chemicals, equipment and training. If one leg is missing, the stool falls over. CrestClean has always kept this stool balanced and will continue to do so through our dedication to research and implementation of the latest procedures.
“We were the first cleaning company in New Zealand to put our hand up during Covid, to say we could safely clean spaces where infectious people had been. And, once again, we are being proactive, by developing HealthClean. There are a growing number of antibiotic-resistant, infectious bacteria and diseases coming to our shores — Candida Auris is one — and therefore we need to be on top of our game in cleaning for health and keeping people safe.”
New Zealand’s Deputy Prime Minister Carmel Sepuloni has announced the introduction of new modern slavery legislation that requires organisations and businesses to be transparent about their operations and supply chains through a new public register.
Under the proposed legislation, which is expected to take around six months, organisations with more than $20 million in revenue will be required to report and outline the actions they take to address exploitation risks in their operations and supply chains.
“We’re taking action to address modern slavery and eliminate exploitation in our supply chains. It’s vital we bring modern slavery practices out of the shadows and into the daylight so we can ensure workers are safe and treated with dignity,” Sepuloni said.
The International Labour Organization and Walk Free now estimates that 50 million people are in modern slavery on any given day, compared to an estimated 40 million in 2016.
“During consultation we heard clearly from business that this legislation is crucial. We already know some businesses are ensuring they don’t have modern slavery in their supply chains, and this will help level the playing field.
“The changes will mean that conscious Kiwi consumers will have more transparency about the products and services they consume. World Vision estimates Kiwi households inadvertently pay an average of $34 each week to industries whose products are implicated in modern slavery,” Sepuloni said.
“We have commitments in our Free Trade Agreements with the United Kingdom and the EU to take steps to prevent modern slavery in our supply chains and promote responsible business conduct. A lack of action will be detrimental to our trading relationships.
“It’s important we continue to bolster New Zealand’s transparent and ethical reputation within our export markets and on the global stage. Now, more
than ever, is the time to put steps into place to prevent these horrible practices from occurring.
“Our focus on larger organisations strikes an appropriate balance, by encouraging those most able to influence their more extensive supply chains, and not overburdening small businesses.
Chair of the Modern Slavery Leadership Advisory Group, Rob Fyfe said the changes are a positive step forward for kiwi business as more and more consumers demand transparency on the products they buy.
“The challenge consumers currently have, is that there is no easy way to find out what’s going on in the supply chains. There is no way to know what went into making the clothes they’re wearing. This reporting system will help bring this information to the fore.
“These important changes bring us in to step with a number of our key trading partners the growing expectations of our domestic and international consumers.”
In a market full of choice, it’s important to know that you’re using highperformance commercial cleaning equipment and consumables that will deliver under pressure, day after day. At Proquip, performance extends beyond our comprehensive, market-leading product range. Service is in our DNA, and it’s the people at Proquip who make the difference.
From humble beginnings as Waiwhetu Distributors in 1978, to today, Proquip continues to deliver the same exceptional Kiwi service that has set the business apart over 4 decades. No other cleaning solutions provider comes close to the level of understanding of the local industry we have built over the last 45 years. And when experience, expertise and market-leading service all combine, that’s performance you can depend on.
To complement the in-depth product training our expert team will provide you at time of purchase, we have developed a comprehensive online tool to support the ongoing training of additional staff in your business. The Learning Centre [TLC] is available to all Proquip customers to better understand and maintain their equipment. And just like people, all professional cleaning equipment loves a bit of TLC from time to time.
Our Proquip Service team are experts in preventative maintenance, servicing and repairs - passionate about helping you continue to get the best out of your cleaning equipment. As well as our own dedicated in-house Proquip techs in Auckland and Wellington, we have a trusted network of nationwide service partners to ensure our customers are fully supported at all times.
If you can’t make it in to one of our nationwide locations we’ve got you covered with the entire Proquip range of commercial cleaning equipment and consumables now online!
Proquip Shop has been developed to put the power in your hands, when it comes to making ongoing product orders easy and pain-free. From setting up favourites lists for repeat purchases, through to setting roles and permissions for staff across multiple sites, you decide what is right for your business.
Owner e.g. Head Office/National Procurement
Owner has full Administrator permissions with access to monitoring and reporting of company-wide spending.
Manager e.g. Regional Manager/Master Franchisee
Manager monitors Operator purchasing, can define contents of favourites lists and has access to reporting.
Operator e.g franchisee
Operator has basic ordering access only. They can review own purchasing history but cannot alter favourites as set by the Manager or Owner.
Advanced Specialized Equipment has been appointed master distributor for Dri-Eaz, Prorestore, Prochem and Chemspec across Australia and New Zealand, effective immediately.
The agreement includes Legend Brands Restoration (Dri-Eaz) and its brands of chemicals which covers, Pro Restore, Chemspec, Prochem, OdorX and Unsmoke.
Grant Hickey, GM, Advanced Specialized Equipment, said the new partnership will provide Australia and New Zealand with more industry leading equipment, chemicals, and technologies.
“Like any business we are always looking at doing things better. We see this new partnership as a huge benefit to Legend Brands Restoration, which already provides great levels of service and sales to the Australian and New Zealand network,” said Hickey.
“As master distributor, we will be able to further enhance this relationship by having better stock levels available, improved consistency of supply, as well as newer and more stable products coming to market. We will also be increasing our marketing and visual presence of these brands into the market.”
According to Hickey, while there is no view to increase the number of distributors or altering the leading distributors that are currently serving the market, Advanced Specialized Equipment will look at other geographical areas that the brands can be utilised in, such as the Pacific and Asia.
“There has always been a mutual respect by all the distributors in Australia and New Zealand and we expect that to continue going forward and hope to enhance this relationship between all parties.
“This new partnership will give the industry more class leading equipment and chemicals, as well as introduced new technologies to the market, such as Command Hub, which I believe will change the restoration industry.
“We look forward to the future of Legend Brands in Australia and New Zealand.”
An international study spanning 32 countries across six continents has highlighted the negative impact of shift work on the health and wellbeing of cleaners.
With more than 2500 participants, the survey, commissioned by UNI Global Union, exposes the significant challenges faced by cleaning professionals who work irregular and unsocial hours.
The survey found that cleaners who work shifts other than the day shift experience a range of adverse effects including isolation, difficulties maintaining relationships, strained social lives, poor sleep schedules, exhaustion and adverse impacts on physical and mental health.
“We have long advocated for a transition to daytime work in the cleaning sector, recognising the negative consequences of irregular and unsocial shifts on workers,” said Eddy Stam, UNI Global Union’s head of property services.
“This survey reinforces the urgent need for the industry to address scheduling issues and prioritise the physical and mental health of cleaners.”
The majority of cleaners surveyed work non-day shifts due to limited
operations or economic pressures, with many employers not offering day shifts. Moreover, non-daytime shifts often come with higher wages, acting as an incentive for workers struggling with cost-of-living pressures.
Key findings include:
Shift disadvantage: Approximately half of the cleaners surveyed work shifts outside of the regular day shift.
Sleep deprivation: Nearly 70 per cent of night-shift cleaners and over half of early morning and evening shift cleaners report not getting enough sleep.
Safety concerns: Around 45 per cent of female cleaners working the night shift express feeling unsafe at work. A significant number of them have experienced harassment at work and during their commute, with over a third reporting incidents of harassment. Social and family life conflict: Evening and night-shift workers face higher rates of conflict between their work schedules and their social and family lives compared to their counterparts on the day shift.
Lack of choice: Seven in 10 cleaners working shifts other than the day shift do so because they have no alternative.
Numatic’s NX300 36V battery technology delivers market-leading runtime, and consistent, powerful cleaning, giving you more time to get the job done. Made for the long haul, the NX300 Battery won’t let you down, engineered and tested for commercial use delivering up to 2500 charge cycles.
30 Power-cell configuration delivers 300W of energy
Off-board 1 hour fast charge Integrated Battery Health Monitoring system
The NX300 battery packs can be used across the growing Numatic Pro Cordless Range. The convenience, safety and power of Pro Cordless with reduced costs and lower maintenance from a single battery and charger system.
All Pro Cordless products are available with 1, 2 or 3 NX300 batteries and a dual battery charger will soon be available.
Introducing the WBV370NX Pro Cordless Wet Vacuum – the newest addition to the Numatic Pro Cordless Network.
Delivering a continuous 40 minutes of cordless freedom in a compact, convenient and versatile design, the WBV370NX is perfect for quickly and effectively clearing up spillages, leaving floors clean, dry and safe.
The NX Quick Charge Station recharges to 80% in just 1 hour for unstoppable cordless cleaning. A simple LCD battery charge indicator shows precisely how much charge is remaining.
Powerful 400W Digital Motor
The specially developed digital motor for the NX300 Pro Cordless range delivers greater airflow and energy efficiency, bringing users enhanced cleaning performance and extended runtimes.
The highly anticipated ISSA Cleaning & Hygiene Expo returns to Melbourne in November
The highly anticipated ISSA Cleaning & Hygiene Expo will return to the Melbourne Convention & Exhibition Centre (MCEC) on Wednesday 1 November 2023 and Thursday 2 November 2023.
The two-day, free-to-attend event is the only show in the southern hemisphere that is dedicated to the cleaning and hygiene industry, and will bring together leading experts, innovators, and cleaning professionals.
Hosted by ISSA, the worldwide cleaning industry association, the ISSA Cleaning & Hygiene Expo, now in its fifth edition, is set to showcase the latest products, services, and innovations from more than 90 exhibitors.
“The 2022 show was an enormous success for both exhibitors and attendees with many stating it was ‘the best expo to date’,” said Lauren Micallef, ISSA Oceania Manager.
“As a result, our members have asked us to keep the momentum going and already the
2023 show is set to be the largest event to date. This will be the first show in four years held in Melbourne and the industry is excited for its return.”
Earlier this year, ISSA acquired additional hall space to meet the growing demand which included a mix of new exhibitors as well as past participants taking up bigger and grander stands.
Visitors are set to benefit from the 33 per cent increase in hall space, as they will be able to explore a wider range of products and services and engage with even more industry experts and professionals.
“Where else in Australia can you meet with so many leading manufacturers, distributors and wholesalers in one location, demonstrating their innovations and sharing their industry insight,” said Stuart Nicol, ISSA Oceania Advisory Council Chair.
“The ISSA Cleaning & Hygiene Expo allows for the opportunity to meet face-to-face and get a feel for what a supplier is really proposing in a more hands on environment.”
Craig Dowell, Director Sales, and Marketing ABCO Products, said: “We look forward to the show returning to Melbourne and being able to provide technical advice and support on products and services that will empower not only the cleaners and companies but also the community.”
Last year saw a 25 per cent growth in ISSA Cleaning & Hygiene Expo attendees with visitors stemming from more than 20 countries. This year the show anticipates more than 3000 attendees from both national and international markets.
“It has been great to see the local growth of the event, but also the traction and awareness from an international perspective,” said Micallef.
“This only helps to broaden the product offerings to our audience as well expand potential business markets for our exhibitors.”
Adam Baker, National Marketing Manager of Makita Australia, platinum sponsor of the event, said the show provides a unique opportunity for the entire market to connect, foster relationships and uncover the latest innovations and insights.
“As a returning platinum sponsor, we have seen the great value and importance that comes from showcasing our brand and products at this important industry event, and we look forward to continuing the relationship in the years to come.”
The expo’s education program will take place over two days and feature 40 speakers, 16 free to attend speaker sessions, plus onsite workshops.
It will cover a variety of topics that have been designed to provide attendees with the knowledge and tools to grow their business, develop their staff, and remain up to date with industry trends and emerging developments.
More broadly, the education program will ensure visitors from all areas of the cleaning and hygiene industry can receive practical advice from industry experts.
A variety of panel discussions between industry thought leaders and stakeholders will expand the number of professionals that the audience can tap into on topics such as cleaning for health, infection prevention, technology and innovation, environmental and sustainability needs, supply chain, and workforce development.
For those attendees looking for a deeper dive into technical training and industry standards, onsite workshops and breakfasts sessions will be taking place throughout the two-day event.
This year, the Facility Management Association’s (FMA) Victorian Chapter will host a technical breakfast and industry standard session on Thursday, 2 November.
“We are excited to collaborate with the ISSA Cleaning & Hygiene Expo and provide members with the opportunity to engage with fellow attendees and leading suppliers within the industry. It’s an opportunity to network and uncover the latest innovations that will benefit the facilities management sector,” said Matt Marsh, Managing Director, Sebastian Group.
The expo workshop program will also delve deeper into indoor air quality, carpet containment, and cross contamination topics. Property and facility managers focused on supporting the health of their occupants are highly encouraged to register.
“Businesses that move quickly to adopt these latest trends and insights will have a competitive edge in their markets,” said Micallef.
Dr. Gavin Macgregor-Skinner, Senior Director, Global Biorisk Advisory Council (GBAC), a division of ISSA, highlights that a key trend in the market is ‘cleaning for health’ and that he expects it be significant discussion point throughout the show and one he will be addressing throughout the education program, including his workshop.
“Cleanliness is not just an aesthetic quality,” he notes. “It is a foundational pillar of infection prevention and occupant safety. It’s about being able to use cleaning and disinfecting equipment, tools, processes, and chemistries to battle the invisible infectious disease-causing agents, contaminants, and pollutants.”
Last year saw a 25 per cent growth in ISSA Cleaning & Hygiene Expo attendees with visitors stemming from more than 20 countries. This year the show anticipates more than 3000 attendees from both national and international markets.
In addition, to the exhibition and education program, the expo will also feature the 2023 INCLEAN Excellence Awards which will be announced at the networking event at the conclusion of the first day.
“Last year the awards received the largest number of entries to date, and we are expecting 2023 to be even bigger,” said Micallef.
These awards celebrate the latest innovations and recognise outstanding achievements of people who work in the industry.
“Participating in the 2023 INCLEAN Excellence Awards allows you to highlight your outstanding achievements, biggest successes, and most creative initiatives and innovations.”
Lisa Michalson, Director of Cleanstar/ XPOWER, said it was an honour to be a winner at the 2022 INCLEAN Excellence Awards.
“We found the benefits and recognition from the industry to be profound. The awards provided a great platform for us to showcase our latest products and innovations. We highly encourage other organisations to participate and in doing so continuing to raise the recognition of the industry,” she said.
Awards finalists will showcase their products in the Innovation Zone on the show floor of the ISSA Cleaning &Hygiene Expo, allowing visitors to view the products and uncover more about these innovations.
“This year’s event is a must-attend for anyone interested in advancing their knowledge and expertise in the cleaning sector. Attendees can connect with their peers, learn from experts, and discover the latest trends and innovations that are shaping the future of the industry,” said Micallef.
“The ISSA Cleaning & Hygiene Expo is an event not to be missed! Events like these would not be possible without the support and effort from our exhibitors and sponsors. They help to raise the profile of the industry and demonstrate its credibility, value, and importance.
“This year, we welcome our returning platinum sponsor Makita, and our returning gold sponsor and sanitising station sponsor, Dettol Pro Solutions. Thanks to our returning silver sponsors Oates (Freudenberg) and ACCO Brands, as well as new sponsors GURR, Brain Corp, EcoPower, and Spillz. We would also like to thank returning coffee cart sponsor, RapidClean; returning business lounge sponsor, Pacvac; returning product placement sponsor, Tennant; and returning lanyard sponsor, Cleanstar. We would also like to welcome ice cream cart sponsor, Symbio.” ■
To register for the ISSA Cleaning & Hygiene Expo in Melbourne, visit www.issacleaninghygieneexpo.com
The Kärcher KIRA B 50 cleaning robot is a practical addition to any cleaning team. Intelligent and autonomous, this innovative floor scrubber delivers maximum efficiency, and consistent cleaning results.
The perception around autonomous machines changes daily. With the advancement in technology, autonomous machines are becoming more frequent in daily living, like self-driving vehicles and delivery robots.
The pandemic has fast-tracked the use of automation, with the cleaning industry no exception, and it is now ready for the adoption of advanced, robotic cleaning machines like the KIRA B 50.
Kärcher’s new KIRA B 50 cleaning robot provides efficient cleaning with every use and offers
cost savings in areas such as labour, detergents and water.
The KIRA B 50 delivers, with consistently outstanding cleaning results within a predeterminable time frame.
The water volume, detergent dosing and speed of cleaning can be pre-set. This allows you to accurately calculate the consumption of resources and costs for each cleaning process.
The KIRA B 50 scrubber dryer cleans floor areas independently and fully autonomously. This reduces labour and enables cleaning tasks to be performed in parallel.
As the machine cleans floors without any decrease in quality, this significantly frees up
team member time which can then be spent performing more challenging tasks in other locations.
In this way, people and machines can work productively together, ensuring that cost-effectiveness is significantly higher for floor cleaning than it’s ever been.
Thanks to its easy operation, setting up the machine for your intended purpose is a breeze and can be done without needing expert knowledge.
Whether it be cleaning large areas or quick use as a manual scrubber dryer, the intelligent concept allows for both options and everything in between.
Partial areas can also be cleaned individually instead of entire surfaces, and cleaning sequences can be adapted to current, day-to-day needs.
All the settings on the KIRA B 50 are easy to use thanks to an intuitive menu, user guidance, and straightforward set-up.
The interface offers various languages that can be selected via a large, central touch screen display.
Clear instructions and straightforward illustrations ensure that operation is simple, whether you are setting up the machine for autonomous or manual cleaning tasks.
1. Efficiency: cleaners no longer have to perform monotonous tasks, instead taking on more complex work.
2. Cost-effectiveness: the ability to perform cleaning tasks in parallel saves time and increases productivity.
3. Intuitive Operation: easy to configure, operate and maintain via the easy to use touch display.
4. Safety: safety certified for public areas thanks to the excellent perception of the environment.
5. Autonomy: the docking station facilitates the fully autonomous replenishment of resources.
When in autonomous mode, the environment detected by the sensors can be visualised using a multi-sensor system during set-up. This allows you to see precisely what the cleaning robot detects and where it has already cleaned.
Cleaning professionals in areas such as airports, supermarkets, or manufacturing, know that floor cleaning is a labour and time intensive task with a number of associated risks and high costs.
Often, qualified cleaners are called on to carry out simple floor cleaning tasks, diverting them away from doing more complex cleaning tasks.
Cleaning floor areas autonomously using the KIRA B 50 cleaning robot means that the cleaning team no longer have to perform monotonous tasks, which increases productivity.
The contra rotating twin roller brush system, with a pre-sweeping function for coarse dirt and a side brush for cleaning up to the edge, ensures excellent cleaning results every time.
The intelligent docking station enables fully autonomous resource replenishment. What’s needed? Connections for fresh water and electricity at the planned docking station site, plus a floor drain.
As needed, the KIRA B 50 docks at the docking station, and everything else happens autonomously – from emptying the dirty water and rinsing the dirty water tank, to refilling the freshwater tank and charging the lithium-ion battery.
Several docking stations can also be used to optimise processes for cleaning very large areas.
The KIRA B 50 offers a comprehensive range of standard features including a high-performance lithium-ion battery. A time-saving auto-fill function and automatic dirty water tank rinsing system maximise water efficiency. The speeddependent dosage system is designed to conserve water and detergent, further increasing productivity and cost efficiencies.
The compact, manoeuvrable scrubber dryer robot is impressive in environments
where space is limited or the area is large. This makes it ideal for floor cleaning in the transport sector (airports, stations, logistics warehouses), retail and shopping centres, healthcare settings (hospitals, care facilities), public buildings (schools, universities, museums, sports halls) or for manufacturing areas.
Safety is paramount. That is why the KIRA B 50’s environment perception system is designed for optimal navigation, with a particular focus on guaranteeing the safety of people in the area.
Integrated laser scanners plus 3D and ultrasound sensors help ensure optimal 360° detection of the working environment.
The sensors reliably detect environmental changes, even transparent obstacles such as glass doors, allowing for avoidance manoeuvres where necessary. Thanks to intelligent recovery manoeuvres, the KIRA B 50 quickly finds its own navigation solutions, even in tricky situations such as dead ends. Integrated warning lights safely inform people in the area that the robot is changing direction.
Kärcher’s KIRA B 50 is safety certified to
CSA_22.2 No. 336-17 and IEC 63327 for use in public areas. Several user profiles with different authorisation levels can be assigned which means you decide who can access and adapt settings for added security.
Full visibility and control of your fleet of cleaning machines is extremely important. The KIRA web portal details information regarding the device cleaning reports, notification logs and machine status at any point in time. This way you can have
full transparency and proof of cleaning, knowing immediately when the robot has finished it’s tasks or needs support.
No matter what the industry or the size of the space, the KIRA B 50 is up for the task. It provides fully automated, efficient, wellthought-out cleaning from start to finish. ■
Kärcher offers a wide range of products and services. For more information, visit: karcher.co.nz
The spotlight is firmly on better practices around infection control as cleaning specialists and aged care and healthcare services seek to protect their employees and customers, but challenges remain.
Words Cameron Cooper
Health management expert Nicola Turner recalls days past when it was not unknown for hospitality staff in aged care and healthcare facilities to flip between cleaning duties and food service for residents.
With 30 years’ experience in health service management, Turner is now the chief operating officer for aged services provider Presbyterian Support Central (PSC) in Wellington. In her current job, she plays a key role in overseeing the group’s infection prevention initiatives.
“Many years ago, we realised when we had one home that had recurring gastro outbreaks that the hospitality staff were mixing up the shift,” she says.
“They could be in and out of the kitchen and in and out of cleaning roles. We had people who were in the middle of cleaning who then stopped to deliver food.”
With more than 900 staff and about 350 volunteers across the group, PSC is a notfor-profit organisation providing services in Taranaki, Whanganui, Horowhenua, Manawatu, Wairarapa and the greater Wellington region. Under the Enliven brand, it runs aged care services that deliver day-to-day support and clinical care across the lower North Island, including in eight retirement villages and 14 care homes.
Turner says the group has long since imposed stricter protocols around cleaning and hygiene, as well as introducing rigorous training programs to ensure best-practice infection prevention at its facilities. It has also engaged with Careerforce – the Industry Training Organisation for the health, wellbeing, social and community sectors in New Zealand – to complete the National Certificate in Cleaning and Caretaking (Level 2) accreditation.
PSC’s vigilance comes at a time when the focus on infection control, including healthcare-acquired infections (HAIs), has never been stronger in the cleaning, aged care and healthcare sectors.
A new report from the World Health Organisation (WHO) shows just how critical such infection-control programs can be, with its research indicating that when good hand hygiene and other cost-effective practices are followed, 70 per cent of such infections can be prevented.
Peter Teska provides technical support in the United States for healthcare offerings at Diversey, a provider of cleaning and hygiene products in countries around the world, including New Zealand.
He agrees that the key to stopping infections is to stick to the fundamentals, especially in aged care and healthcare facilities. That means promoting vaccinations, insisting on regular hand washing, and encouraging people to wear face masks, when appropriate.
“We saw a general increase in HAI rates during COVID because people became so focused on the pandemic and they stopped doing the basic things they should have been doing to protect patients,” he says.
The other imperative to minimise HAIs Teska notes, is to disinfect and clean surfaces properly and regularly. Skipping cleaning of a bedrail or light switch in a resident’s room for just a day or two can increase the risk of transmission of pathogens, which can lead to patient infections elsewhere in a facility.
Dr Greg Whiteley urges all aged care and healthcare facilities to stay attentive in the face of multiple infection threats.
In addition to COVID-19 and influenza, he warns of the rise in healthcare settings of CPE (carbapenemase-producing enterobacterales), a type of superbug that lives in the gut and which is highly resistant to antibiotics. While it is normally harmless, the bug can be deadly if it enters the bloodstream through a wound of a patient who is already sick or frail.
“They are resistant to most frontline antibiotics, including some now very commonly used antibiotics,” says Dr Whiteley, the executive director of Whiteley, a manufacturer of sterilants, disinfectants and professional cleaning technologies that are distributed in New Zealand and other countries.
“The risk is that if you don’t dispose of things like your bed pans properly in healthcare, those bugs can end up in splashes around sinks and taps. Then those surfaces get touched by hands and the bugs can move from place to place. So, the importance of cleaning surfaces and washing hands cannot be overstated.”
Dr Whiteley acknowledges that implementing cleaning and disinfecting strategies in a hectic healthcare workplace is complicated. However, with a bad flu season in New Zealand and a continuing threat from COVID-19, there is no room for complacency. His concern is that many facilities continue to underestimate the importance of proper, hygienic glove use.
“We still see a lot of people using gloves as though they’re some sort of invisible force shield, but you should also be changing your gloves regularly.”
Peter Newman, regional manager of PSC, says in addition to wanting to do the right thing for its residents, the group understands that its brand reputation is tied to protecting the health of its staff and residents. “It’s a huge focus for me and the group,” he says.
“A lot of cleaning and infection control practices have shifted, and it’s absolutely critical for our homes and our people that we maintain a really clean space.”
He adds that two recent awards in the New Zealand Aged Care Association Excellence in Care Awards suggests that PSC is getting it right.
The ongoing challenge for many healthcare and aged care facilities is the high turnover of nursing and cleaning staff in the wake of the pandemic.
Teska says high levels of work-related stress during COVID-19 led to many nurses and carers quitting the sector or switching to become ‘travelling nurses’ who are contracted to facilities for a limited period. This complicates efforts to roll out effective infection control training and processes.
“
A new report from the World Health Organisation shows just how critical such infection-control programs can be, with its research indicating that when good hand hygiene and other cost-effective practices are followed, 70 per cent of such infections can be prevented. ”
“People who are not permanent employees will typically not receive the full breadth of training. This creates knock-on effects because those staff may not be following the practices that you have adopted for your hospital or healthcare facility.”
Teska concedes it is difficult to lift pay rates significantly without affecting other aspects of service delivery, while he adds that high turnover rates also result in staff filling gaps in rosters that make it even more difficult for them to allocate time for training programs. “As a result, it becomes a vicious circle.”
Lauren Micallef, ISSA Oceania manager, says an emphasis on training of cleaners and healthcare professionals should never be compromised.
“Now is not the time to cut back on training,” she says.
“It’s key. If you’ve got staff shortages, you need to be adapting, you need to be changing and making sure that people are ahead of the game.”
Micallef adds that contractors and facilities should be conscious of planning for the future and putting in place strategies to retain their best staff.
“You need to hold on to them,” she says.
Such a sentiment resonates strongly with PSC. Turner says staff turnover has been stable “because we invest in our employees”. Whether it is through training, or paying competitive wages, she says the group is building a culture in which cleaning staff are highly valued.
Diversey’s global infection prevention expert Peter Teska has contributed to three recent peer-reviewed scientific articles on infection prevention – one in the American Journal of Infection Control on automated floor cleaning disinfection, another evaluating the hygiene outcomes of manual floor mopping methods, and a third examining the efficacies of disinfectant towelettes against Candida auris, a drug-resistant fungus.
The floor studies are designed to examine how proper hygiene and disinfection practices can stop pathogens such as Staphylococcus aureus transferring from contaminated floors to other highcontact areas, potentially contributing to healthcare-associated infections (HAIs).
In the former study, the researchers tested and compared efficacies of five US Environmental Protection Agencyregistered disinfectants and one neutral cleaner using a floor-cleaning machine. They found that hydrogen peroxide and quaternary ammonium compounds were more efficacious against S. aureus than the neutral cleaner.
In the latter study, a 2m2 vinyl floor contaminated with S. aureus was used to test the efficacies of five floor hygiene products using three different mops. The researchers found that there were significant differences among product types used, with a neutral cleaner having the most average log densities recovered compared
with hydrogen peroxide or quaternary ammonium compounds-based disinfectant products. They added that “more crosscontamination was observed when cotton mops were used, while the area cleaned or disinfected had no significant differences among average log densities recovered”. Teska believes the research will contribute to a view that the use of a biocide to destroy harmful organisms will become accepted practice with floor cleaning. “Now whether or not clinically that’s necessary is still open, but as far as a step further in our understanding of potential pathogen transmission from floors, we feel very strongly that, all things being equal, if you can use the biocidal product, you’re probably better off to do that because it will lower the level of pathogens on the floors.”
With the C. auris study on the use of disinfectant towelettes on hard, nonporous surfaces, the findings suggest that healthcare facilities wanting the best hygiene outcomes should use disinfectants with an EPA-approved label claim against C. auris and should ensure the surface is kept wet for the contact time listed on the label. “If you’re not doing that, you’re likely not able to kill some of these pathogens, and Candida is harder to kill,” Teska says. “You want a disinfectant that’s been tested against it, or at least has been shown to be efficacious against it because it’s definitely an environmentally acquired pathogen.”
“
The ongoing challenge for many healthcare and aged care facilities is the high turnover of nursing and cleaning staff in the wake of the pandemic.
PSC’s Nicola Turner says two key initiatives have helped her organisation improve its infection control and hygiene outcomes. First, she advises making sure that handhygiene practices extend to all areas of a facility or organisation. “We realised that we had always concentrated on hand-washing and hygiene for staff, but not so much on the aged care residents,” she says. “But residents may forget to wash their hands and they get sick and they touch things, including their walking frames.” PSC has now addressed this issue with a greater focus on hand hygiene for residents.
Second, PSC allocates a significant budget for deep cleaning of carpets and furniture – two areas that can be overlooked in some facilities – in addition to doing regular servicing and maintenance of cleaning equipment. “It’s not just infection control that’s important,” Turner says. “Cleaning has to be handled properly on all levels.”
“Their role is just so critical. We have a very flat structure and everyone wears the same uniform. When we first introduced this policy, some staff, especially the nurses, didn’t like it because they thought they were being demeaned,” Turner explains.
“But when we talked to the residents, they made the point that everyone has a really important role in keeping the homes ticking over. The cleaners are just as important as everybody else. They have a relationship with the residents and their families and they’re often the ones who notice when a resident’s not well. So, they’re very much part of the whole team and that’s probably why they stay.”
As he reflects on the impact of COVID-19 on hygiene practices and infection control, Teska says it is clear that cleaning and hygiene experts
CrestClean are leaders in healthcare cleaning. We understand the particularities of providing effective cleaning for the healthcare sector.
As part of the supply chain for DHBs, we are accountable for the delivery of cleaning services to many surgeries and clinics throughout New Zealand, including multi-site facilities.
Our cleaning services meet the strict environmental criteria set by Environmental Choice NZ. This helps to improve the sustainability of our cleaning services and allows our customers to verify sustainable procurement.
W: 185mm x H: 90mm
have to keep debunking myths and informed opinion.
“There was this assumption that if we had a public health emergency, everyone would listen to the experts,” he says. “Well, we now have to revisit that notion.”
Despite evidence to the contrary, Teska says many conspiracy theorists continue to downplay the risks associated with COVID-19, while even some healthcare workers have refused to be vaccinated.
“The idea that you can read something on Facebook or Google and that this somehow makes you an expert in it, I think is very problematic,” Teska says.
“The medical leadership globally sees this as an important challenge and hasn’t really come up with an effective way of addressing it. But we do need to make it clear that just because someone has an opinion, it doesn’t mean it’s an informed opinion and that it should not necessarily translate into actions that increase the risk of negative health outcomes for other people.” ■
Find out more at crestclean.co.nz/healthcare
Facility budget cuts often mean a decline in the quality of cleaning within offices, schools, hospitals, and other buildings. However, cleaning is essential for creating a safe and healthy environment, maintaining occupant satisfaction, and keeping a facility looking its best.
Rather than eliminating cleaning practices from a facility, organisations can instead implement a variety of cost-cutting cleaning methods and new technologies to make cleaning more efficient and affordable.
1. Day cleaning: Instead of late-night work, shifting cleaning tasks to daytime hours helps reduce cost and improve sustainability by taking advantage of more productive hours. Day cleaners are more productive per square foot because they have better visibility of soiled areas and can establish relationships with occupants so that messes are cleaned up as they occur. Buildings can also lower their energy bills by turning down lights and adjusting HVAC settings at earlier hours, rather than keeping them running at night for cleaning crews.
2. Dilution control: Dilution control solutions dispense the correct chemical dose so that employees don’t have to manually dilute them. By implementing this solution, facilities can avoid switching to lower quality chemicals to cut costs, which typically require employees to use more chemical to achieve the same results. Properly diluted chemicals and cleaning practices will also help protect the investment made in the facility’s floors, equipment, and other assets. Dilution control solutions also reduce hazards and error by ensuring that employees avoid
contact with concentrated chemicals and that solutions are not mistakenly mixed or improperly diluted. Many dilution control systems are easy to use, and employees can be quickly trained on proper use.
3. Controlled dosing: Traditional floor care machines continue to dispense chemical solution when machines slow down and turn. Advanced floor care machines now offer speed-dependent dosing systems that apply the chemical to the floor based on the machine’s speed rather than the amount of time that has elapsed, reducing solution waste. By using an advanced dosing system, facilities can reduce cleaning solution waste by up to 30 per cent. These machines also allow operators to vary the level of dilution/solution and in some cases, turn off chemical dispensing to clean floors based on the level of soil. These machines also increase productivity because employees don’t have to empty and refill tanks as often.
They can also reduce downtime after cleaning because they leave very little moisture behind.
4. Customisable workstations: These workstations can be configured based on the user’s preferences. These workstations improve productivity because items are strategically placed for workers. Studies have shown that efficiency increases by 20 per bcent or more when using workstations designed
TASKI AERO vacuum cleaners are highly efficient with a 585W whisper quiet motor which delivers the same cleaning performance as 900W, this is achieved through an ingenious airflow system and as a result saves significant levels of energy and reduces CO2 emissions without compromise.
for a specific cleaning task versus fixed solution workstations. These customisable workstations allow cleaning to be completed more quickly, thereby reducing labour costs. They also reduce ergonomic strain for workers, limiting potential injuries, time away from work and workers’ compensation claims.
When facility managers face budget cuts, the ideal solution is to adjust cleaning programs, rather than cut out resources completely or switch to cheaper options that yield less impressive results. Innovative technology, chemicals, and equipment can make cleaning more efficient and cost-effective by reducing energy, chemical and water consumption and improving productivity.■
If you have questions about any aspect of Diversey New Zealand’s hygiene programs, services or products visit our website at diversey.co.nz or call 0800 803 615 to speak to our friendly customer service to and find out more.
Rather than eliminating cleaning practices from a facility, organisations can instead implement a variety of cost-cutting cleaning methods and new technologies to make cleaning more efficient and affordable.
Sustainability has been on the agenda for some years but how many businesses have truly embraced it by changing their processes to deliver the triple bottom line of people, planet, and profit?
When it comes to sustainability, some customers will be content to switch to products they consider to be more “environmentally friendly.”
Sustainability is such an all-embracing subject that simply switching formulations can only ever deliver some of the potential benefits. Many teams will want to go much further and embed sustainability into their business by changing the way they work
and integrating more of their processes.
Adopting super concentrated cleaning products is a good example. Water is added at the point of use rather than at the factory, which means the amount of product required for a specific number of cleaning tasks is less than corresponding bulk and ready-to-use alternatives.
More chemical and less water is carried on vehicles, which reduces the total road miles and carbon footprint of deliveries. Another benefit is that less packaging is required, which means fewer raw materials are consumed and less waste is generated. Ideally the packaging will be fully recyclable.
This equipment removes the guesswork when preparing solutions to deliver consistency, eliminate waste and reduce costs.
Further gains are made because solutions prepared consistently to the manufacturer’s specification reduce the need for expensive and timeconsuming rewashes.
The J-fill system is a good example of one of the Diversey platforms designed to deliver super concentrates in a safe, simple, and reliable way.
The J-fill platform is the most innovative and versatile chemical dispensing platform in our industry today.
• Metering tip in every bottle
Prevents misuse, guarantees cost and eliminates clogged metered tips
• Spill-Tite packaging
Significantly reduces the risk for chemical spillage and chemical exposure
• Super and hyper concentrated solutions
Delivers best-in-class product performance cost
• Full product portfolio
J-Fill offers a wide product range
• The J-Fill bottle can be used in a variety of unique
One bottle can be used in multiple dispensers to fit the need of any customer situation
4 Superior efficacy
4 Lowest toxicity profile
4 No rinsing required
This is a four-product water valve operated dispensing unit that uses eductor-based technology. The J-Fill dispenser and the J-Fill packaging is a fully enclosed system with Spill-Tite technology that virtually eliminates the user from coming in contact with liquid concentrate.
4 Low odour issues
4 Superior safety profile
4 No PPE required in use
4 Reduced cross contamination
4 Short contact time required
4 Latest technology
Quattro Select is a lockable unit which stores four super-concentrated chemicals simultaneously, simply turn the smart valve selector to the desired product and begin filling. The unit offers two flow rates to make bucket and trigger filling easy.
As autonomous technology and robotics rapidly improve, New Zealand building services and facility managers are exploring how cleaning robots can deliver quality, efficiency and sustainability benefits.
Words Cameron Cooper
You can’t keep a good robot down. Despite being the subject of criticism in years past because of glitchy technology and frustrating operational issues, a new breed of autonomous cleaning machines is being rolled out in New Zealand and Australia as building services contractors and facility managers seek to save time and achieve better cleaning and hygiene efficiencies.
Automated technology and robotics are advancing quickly and can have a positive impact in large commercial and industrial spaces at a time when cleaning workforces are thin on the ground.
Conrad Pearson, sales director for robotic floor cleaning equipment manufacturer Tennant in Australia and New Zealand, says while robots are getting smarter and smarter, the focus should always be on meeting the
expectations of customers with machine rollouts, rather than offering technology for technology’s sake.
“It’s really about trying to match people’s desires, rather than saying, ‘We’ve got a great machine, do you want it?’”
The demand for cleaning robots is big and getting bigger, with findings from KBV Research suggesting the international market will reach US$24 billion by 2026, achieving 22.9 per cent compound annual growth rate (CAGR).
This trend is undoubtedly being driven by better technology, as well as rising labour costs and the requirement for superior cleaning results in the wake of COVID-19. What is clear is that the pandemic has changed people’s expectations of cleanliness, health and safety in public spaces and workplaces.
This is where artificial intelligence comes to the fore. AI-powered robotics are producing faster and more consistent results. They assist with safety in so much as they undertake repetitive tasks that can result in injuries for humans. They also use less water and energy, thereby contributing to sustainability goals.
In this environment, a wide range of new automated robotics in the commercial cleaning industry is emerging. Predominantly designed to clean floors, the best machines can now work autonomously with minimal human intervention on different surfaces and across any facility.
Superior battery technology has also been at the core of better robotics performance. Japanese company Makita is using the battery technology innovation from its power tool range – offering long run times and longer life – to improve the performance of robotics equipment.
It unveiled the DRC300 brushless robotic floor cleaner for commercial and industrial use in the New Zealand market late last year. The 18V LXT battery can provide continuous cleaning power of up to 240 minutes over 600m2 area when used with two 18V 6.0Ah batteries in parallel. It uses LiDAR sensor technology and a front camera sensor that helps to map cleaning areas, with the cordless machine also connecting to a smartphone through an app.
Ben Fuller, key account manager for Makita New Zealand, says better batteries are crucial to the high performance of machines such as the DRC300.
“Luckily for us, we’ve had our battery technology for a long time, so we’ve always been strong on that side. Now we’re also focusing on the smartness of the robotics, being able to link it to your phone, having more control, and being able to maximise what you want to use it for.”
Fuller says robotics technology is constantly evolving and getting more intelligent.
“We see the DRC300 being especially useful in commercial and industrial areas where a production guy at the moment is having to jump off his line to do a clean-up and then jump back on a machine. It’s all about getting the robot to do that cleaning for them.”
He adds that it is also ideal for ongoing cleaning maintenance in high-traffic areas in between visits from regular cleaners.
Following its release, Fuller says the DRC300 has enjoyed quick take-up.
“It’s obviously a big outlay in terms of cost, but when customers weigh that against what they’re saving in the long run, it’s definitely well worth it.”
Cleaning is without doubt one of the largest costs in building management. Therefore, it makes sense for facility service providers and building managers to consider robotics as a way of driving down long-term costs and addressing chronic labour shortages that have been a feature of the New Zealand workforce since the outbreak of COVID-19.
Pearson confirms that the worker shortage is a very real challenge for New Zealand, as a labour drain to Australia is exacerbating an already significant shortage of workers.
That is making robotics all the more appealing for supermarket distribution warehouses and industrial sites where the emphasis is firmly on clean, safe and healthy working environments.
As those labour woes continue, an earlier reluctance to embrace robotics is breaking down through necessity. In the past, there were fears that robots would replace human workers, while the
“
Automated technology and robotics are advancing quickly and can have a positive impact in large commercial and industrial spaces at a time when cleaning workforces are thin on the ground. ”
upfront expense of the technology put off some potential buyers.
Now, many businesses simply want a solution to help address the labour crisis, and better technology is making autonomous cleaning machines a more viable option.
Kärcher, for one, is responding to this need. The German cleaning equipment giant has just released into the New Zealand market its KIRA B 50 cleaning robot, an autonomous floor-cleaning scrubber dryer that is designed to clean large facilities such as airports, logistics warehouses, shopping centres, hospitals, and educational facilities.
KIRA is powered by a 160Ah lithium-ion battery and uses a roller brush technique with a pre-sweeping function with a 55cm working width.
Ryan de Goede, national key account manager for Kärcher Professional in New Zealand, says while KIRA can perform the tasks of a conventional floor scrubber, it does not need human intervention. This allows cleaning teams to use their time to focus on higher-value tasks.
“It’s new to this region and it’s very impressive, and we’re now in a position where we are ready to do some trials and demonstrations on live customer sites,” he says.
In line with advancing technology that is making such autonomous machines more valuable, KIRA has a docking station where it can automatically refill and recharge. It is equipped with 2D and 3D
cameras that help it navigate and map cleaning environments. The machine also connects directly to a web portal, which can display critical machine data instantly from any location. Water volumes, detergent dosing and the speed of cleaning can all be preset.
De Goede says a ‘teach and repeat’ function allows users to target areas for ongoing cleaning.
“You can do it yourself, which means there is very little after-sales support that we need to do in terms of the physical mapping of the customer’s site.
“They can take control of that process.”
He makes the point that lithium-ion batteries are “probably the bare minimum now in terms of floor care”.
“What that enables the machine to do is, number one, run for longer, but it also enables the machine to charge intermittently – to top it up without the battery being damaged. With conventional batteries, you can’t do that.”
Better batteries aside, Kärcher is also aiming to introduce a fast-charger towards the end of the year.
“There’s advances coming all the time from our factory with this machine,” de Goede says. “So it’s pretty exciting.”
The emphasis now for many cleaners and facility managers will be ensuring they have the right technology for the right spaces.
Pearson says after an initial spike in
robotics uptake in the North American retail sector by big-name retailers such as Walmart and Kroger, there was an expectation that this trend would flow through automatically to other countries such as New Zealand and Australia.
“But I think we’ve realised that the rest of the globe is not necessarily the same as North America,” Pearson says.
“The store footprints are not as big here and the way stores are cleaned is different.”
He observes, too, that some of the major retailers in Australasia have not been early adopters of the latest robotic cleaning technology, partly because of their market dominance.
This has prompted Tennant to target the industrial sector in the knowledge that the sector has already embraced technology to ‘pick’ goods and streamline material handling in distribution warehouses.
“A lot of industrial businesses are ready for the robotics model, and they understand why it’s important and that it’s not just a gimmick – it’s actually something that’s giving them a return on investment, it’s improving efficiency, it’s improving performance,” Pearson says.
On the flip side, he notes that adoption of robotics has been somewhat hit and miss in the healthcare space. After reasonable uptake during COVID-19, Pearson says facility managers have been “backing off” more recently as they again focus on cost cutting.
To overcome the perception of robots being too expensive, Kärcher will offer an operating lease model in New Zealand that will include full servicing of KIRA. De Goede says the move is designed to give customers “peace of mind for a fixed fee every month”.
“We’ve got local support teams up and down the country, so we try to make our offer as attractive as possible to customers.”
As it contributes to a cleaning world where robots and cordless machines become the norm, Makita is also doing its bit to promote sustainability.
For the past 30 years it has embraced efforts to recycle rechargeable batteries, with the aim being to keep batteries out of the waste stream.
“The battery is a big part of our business now, and factors such as recycling of batteries are very important to us,” Fuller says.
Whether it is batteries, AI or other innovations, ongoing technology advances will only heighten the imperative for cleaning contractors and facility managers to support robotics.
At the same time, de Goede says there is no intention to get rid of human cleaners.
“We’re not replacing people,” he says.
“We’re redeploying people so that you can give your cleaning team a bit more time to free them up to go and do the smaller detail stuff. It’s all about working more efficiently and more productively.”
He points out that robots are not only smart, but hard-working.
“They’re not going to take sick days or leave. They’re going to clean consistently the same way every single day, from Monday to Friday. As long as there’s power and they’re plugged in, they’re going to do their thing.” ■
“
AI-powered robotics are producing faster and more consistent results. They assist with safety in so much as they undertake repetitive tasks that can result in injuries for humans. They also use less water and energy, thereby contributing to sustainability goals.
Escalating employee burnout among first responders and front-line workers is putting pressure on leaders within cleaning and restoration businesses to implement supportive workplace solutions.
Words Cameron Cooper
The numbers are in – and, without question, burnout has become an issue for many industries, including the cleaning, hygiene and restoration sectors.
According to a global Future Forum Pulse survey of 10,243 respondents, burnout among employees is on the rise internationally, especially among women, younger workers and middle managers.
Although employees with work flexibility report higher scores for productivity, connection, and company culture, 42 per cent of people overall say they are experiencing burnout.
For companies, business leaders, and their employees, the question now is how to respond to an insidious burnout trend that can result in employees suffering from chronic stress that often causes physical and emotional exhaustion, low self-esteem, reduced productivity and detachment from their peers.
Kerrie Dale, general manager at Workplace Rehabilitation Management, is not surprised at the rise of burnout, noting that first responders and front-line workers in high-stress environments have experienced a string of confronting challenges in recent years.
“We have seen fires, multiple COVID lockdowns, and then floods,” she says.
“So, it has resulted in a situation where people such as first responders have simultaneously become service providers and victims. And no one has really had the chance to process any of that.”
In addition, Dale says many work-from-home employees have had to deal with added strains and anxiety related to changing family scenarios, the adoption of new technology platforms, and isolation from their colleagues.
“People have had to cope with a lot of change.”
Restoration professionals are among the cohort of workers that has observed the most harrowing of scenes in recent years stemming from natural disasters. They have had to watch on and interact with people who have lost their loved ones, homes and businesses to fires and floods, in particular.
Lorraine Rogic, a cleaning industry expert and managing director of Logic Business Resources, says restorers and cleaners often experience distressing workplace circumstances.
“In the restoration business, it’s not just about floods – it could be cleaning up bodily fluids and things like that,” she says.
“It’s always been confronting, and some people may just leave the industry as opposed to being given the support they need.”
Although the cleaning and restoration industries have evolved from times when workers were assessed as “either being built for the work, or not”, Rogic believes management can still do much more to aid workers.
As a starting point, leaders should acknowledge that technology has made workers “more available than ever” and insist on policies that give them genuine time away from the office.
They should also resist the temptation to load up high-performing workers with more tasks at a time when recruitment is tough.
“There’s no such thing as multi-tasking,” Rogic says. “We really can achieve more when we do one thing at a time.”
Melissa Behrend, a director at HR on Call, says the merging of people’s lives between work and home as a result of the pandemic has added extra layers of duties, complexity and anxiety for many employees. For those onboarded during COVID-19, they were often given task-focused jobs.
Now, they may have to be recalibrated to work in a mainstream office when they would prefer to keep working from home.
“They’re trying to learn social niceties and norms in a vacuum,” Behrend says. “And then if you overlay issues such as floods and COVID, they’re suffering additional stress on top of that.”
The result is a group of workers who may be overwhelmed and mentally and physically spent.
Dr Melissa Marot, an organisational psychologist and clinical neuropsychologist at The Mind Room, says leaders, managers and HR personnel should be on the alert for possible signs of employee burnout. This could include mental and physical exhaustion, lethargy, mood swings, social withdrawal and lower job satisfaction and productivity.
Formerly punctual employees may start turning up late for work or appear to be less motivated than in the past. They may seem disengaged from other team members and self-isolate at lunch or have standoffs with other workers with whom they previously got on well.
Likewise, Dr Marot says employees should be conscious of burnout risks. If they find that they are getting more irritable, or if they are exhausted and finding less joy at work, they should treat it as a wake-up call.
“
Leaders, managers, and HR personnel should be on the alert for possible signs of employee burnout. This could include mental and physical exhaustion, lethargy, mood swings, social withdrawal and lower job satisfaction and productivity.
“And if your friends and family are saying, ‘Hey, you’re different than what you were six months ago,’ you need to be aware of that,” she says.
“It often happens bit by bit. That’s the issue with burnout – often it isn’t really noticeable at first. It does creep up on you.”
Dale also urges workers to take responsibility for some factors that can be controlled at an individual level – sleep more, drink less and eat better.
Crucially, she says employers should create a workplace environment in which staff feel supported and not “victim blamed”.
“Don’t make someone who is already in a vulnerable position feel bad that they haven’t done some of the things they were meant to do.”
Rogic has no doubt that employers can play a key role in preventing employee burnout and improving wellbeing. For example, providing employee assistance programs is a smart way to assist staff. This could include offering access to financial
counselling services that could be a life-changer for staff.
Whatever they do, Rogic agrees it is essential for bosses to create a culture in which staff feel comfortable to bring up any burnout concerns with senior peers.
“Give them permission and encourage them to approach their manager and say, ‘Look, this is happening and that’s happening’ and then for the manager to be seen to be actually doing something about it. Culturally, things will shift if employees talk more to their managers about what’s going on.”
Staff need to know, adds Rogic, that they will not be reprimanded or branded as a lazy worker if they raise concerns about personal burnout.
Behrend agrees that employment assistance programs can be invaluable. She also suggests conducting an employee survey to identify any workplace pain points.
“In some cases, one employee may leave the business and another worker
Although working from home can have many benefits for employees, it can also lead to greater isolation and an unhealthy around-the-clock focus on work.
HR on Call’s Melissa Behrend says this reality makes it crucial for employers to get home-based staff to come into the office for team days, or to just regularly catch up with other staff.
“It’s important for them to connect,” she says.
“It’s also important for a team leader or manager to do their check-ins with staff without always talking about tasks and what they have done with regard to work. Make sure you understand your team members, their intrinsic motivations and their personal circumstances. Ask them about their weekend and find out something about that person to create a relationship because that’s often lost with the square box that we look in.”
“
Employees should be conscious of burnout risks. If they find that they are getting more irritable, or if they are exhausted and finding less joy at work, they should treat it as a wake-up call.
The following actions can be circuit-breakers for people who are experiencing burnout.
1. Talk to a supportive person –whether it is a trained therapist, a boss, a family member or a friend, it is important to speak to trusted peers about your issues and to start to address them.
2. Embrace meditation and mindfulness – such practices allow you to check in with your body and have been shown to significantly reduce stress and anxiety.
3. Up the ante with daily exercise – being active through running, walking, swimming, yoga or other forms of exercise can boost your endorphins and distract you from the worries and pressures of the office.
4. Focus on a healthy diet – in tough times we often turn to fast food and alcohol for relief, but healthy food options can be part of the lifestyle changes you need to make to get back to your best.
5. Be intentional about disconnecting from work – make a point of catching up with friends and seeking entertainment away from the job to give your mind a break and provide some life context to any career concerns.
Dr Melissa Marot says one of the worst responses to burnout is to ignore it, especially among first responders or those who are exposed to high-risk scenarios at work.
“A lot of people tend to just push on because that’s what you do,” she says. “They respond to emergencies, so they just keep on pushing and pushing and pushing. Being aware that such a response may not be the best way to go is a good thing.”
She also encourages under-pressure workers to seek professional help.
“Go and see a psychologist – they can be really helpful and you don’t need to have many sessions. You can just have a few just for some good tips, tricks and strategies.”
gets three jobs piled on to them. So, it’s about understanding those issues and knowing that people may have days where other factors are impacting their performance. It’s just so important for leaders and managers to recognise signs and symptoms of burnout. Even co-workers can check in to ask ‘are you okay?’ and to be aware of the wellbeing resources that you can point staff to. You don’t have to be an expert in it, you just have to be there and point them in the right direction and recognise that, maybe, someone’s not okay.”
Burnout is an issue that will not just fade away. A new study of 1400 employed Australians from the University of Melbourne and YouGov reveals that, in the aftermath of the pandemic, Australian workers across all ages and stages are in poorer physical and mental health.
So-called prime-aged workers – those between 25 and 55 – are reporting the greatest burnout, while about 40 per cent of respondents feel less motivated about their work than before the pandemic. Worryingly, 33 per cent of this prime-aged workforce is thinking about quitting.
Such findings make it clear that leaders in the cleaning sector cannot afford to be complacent.
Behrend says bosses needed to be proactive if they see those signs of
people struggling and not just let them push through those issues.
Rather than ignoring signs of trouble, she urges leaders to embrace responses such as mental health first aid.
As all organisations grapple with their response to burnout, Dr Marot says leaders and managers should never ignore the importance of genuine, two-way communication with their staff.
“Communication needs to go both ways,” she says. “But it’s important that the employer encourages a culture where that communication is possible. “It’s really important that the leaders in the organisation, right down to line supervisors, not just encourage communication but really listen to their employees and take action.”
Rogic agrees that actions speak louder than words.
“If a manager stands there and says, ‘We want to support you, we want to help you’ and then doesn’t provide any support or any help, that speaks volumes, regardless of what you discuss in your team meetings.”
She says the truth is that there was not enough support for first responders, restorers and other workers in highstress roles before COVID-19. The pandemic provides pause for thought and a chance to rectify that situation.
“I hope that one of the positives out of COVID is that there’s more leadership around burnout and there is more assistance and support for those who are most vulnerable.” ■
The built environment is all structures built by humans, including our homes, workplaces, schools, planes, trains, buses, and cars.
These are the spaces where we spend most of our time. We spend 90 per cent of our life in these spaces, so if we live to 80 years old, then 72 of those years have been spent in the built environment.
As in any place on earth, microorganisms (bacteria, viruses, fungi) have been found in every part of the built environment that has been studied.
They exist in the air, on surfaces, and on building materials, usually dispersed by humans, animals, and outdoor sources.
Microbial communities and their metabolites can be good or bad – they can cause (or exacerbate) and prevent (or mitigate) human disease.
Words Dr Gavin MacGregor-SkinnerAll cleaning professionals should understand the field of microbiology of the built environment, how our built environments affect human health, and what actions they can take to ensure they are cleaning for health.
Throughout history, if we build something, we have sought to control germs and eradicate causative agents of disease. It is well documented that humans understand that unclean indoor environments can adversely affect health. This has dominated the cleaning industry for centuries. But what are some other key discoveries for our industry:
• In 1890, Koch’s postulates stated the four criteria as guidelines for establishing that microbes cause specific diseases. Then came the ability to separately
count bacteria and fungi using a microscope from samples collected on culture media.
• By the early 1900s, research began to demonstrate how overcrowding, poor ventilation, and contamination of buildings by microorganisms and organic matter can lead to infection and disease.
• In the 1950s, we could identify specific bacteria and fungi from a sample using selective culture media.
• Research accelerated in the 1960s to understand the sources, survival, and how to control germs in the built environment. Associations between fungal spores in air and dust and allergy symptoms were established and quantified. Rates and mechanisms of germ emissions when humans cough, sneeze, and breathe, showed
how communicable respiratory diseases spread.
• Since the 1960s, culture-based investigations have dominated studies of germs in the built environment and continue to dominate industrial hygiene sampling.
• Throughout the 2000s, RNA sequencing has enabled the identification of previously unculturable microorganisms and a deeper understanding of microbial ecology.
Assessing germ contamination in the built environment is critical in determining threats to public health.
We have existing tools and recent technologies that will significantly impact the cleaning industry and become part of our toolbox.
They will allow us to visualise the invisible germs and help determine how to clean and what products to use.
We can start with ATP detection, routinely used to measure surface cleanliness but cannot specify which microorganisms are present.
There are other tools that you may not be aware of that can distinguish the living from the dead microorganisms, such as dye-based screening techniques, ethidium monoazide (EMA), propidium monoazide (PMA), quantitative polymerase chain reaction (qPCR), isotope probing, or bioorthogonal noncanonical amino acid tagging (BONCAT)—a powerful tool for analysing microbial communities.
Studies have been conducted to characterise patterns, associations, and drivers of microbial communities in built environments.
Many of these studies have demonstrated that most bacterial microorganisms found on surfaces in buildings originated from human skin and the mouth (talking, breathing, coughing, vomiting) and nose (breathing, sneezing).
These studies suggest that humans are the primary source of microorganisms found in the built environment.
Studies in hospitals, public transport, and homes have found humanassociated microorganisms, including common potential pathogens (that
cause disease) such as Pseudomonas spp., Acinetobacter spp., Staphylococcus spp., and Streptococcus spp., as well as common commensals (that live in harmony with humans) such as Anaerococcus spp., Prevotella spp., Corynebacterium spp., and Neisseria spp.
A study that quantified the abundance of bacteria and fungi emitted by a person indoors estimated the total particles to be 31 milligrams per hour, with approximately 37 million bacteria and 7 million fungi per hour being dispersed.
It is estimated that a cough produces approximately 3,000 droplets, whereas a sneeze releases 40,000 droplets, and each droplet may contain as many as 200 million virus particles.
Particles from your sneeze can travel up to 26 feet, coughing up to 6 feet, and breathing up to 3 feet. A toilet flush sneeze without the lid closed can travel up to 8 feet away.
People inhale a considerable volume of indoor air daily, on average 16,000 litres or 4,200 gallons for adults.
Therefore, it stands to reason that the interactions between humans and buildings that facilitate microbial exposure will profoundly impact human health.
Cleaning professionals need to know that culture studies suggest that the most common microorganisms associated with indoor surfaces belong to the fungal genera Cladosporium, Penicillium, Aspergillus, and Stachybotrys (in damp buildings) and the bacterial taxa Corynebacterium, Staphylococcus, Lactobacillus, Streptococcus, Enterobacteriaceae, Acinetobacter, Sphingomonas, Mycobacterium, Methylobacterium, Bacillus, and Pseudomonas.
However, the growth potential of these organisms is determined by water activity (a measure of water availability in a material), chemical composition, pH, and the physical properties of surfaces.
Keeping building materials dry, that is, with a water activity below 0.9 for bacteria and 0.6 for fungi, ultimately limits growth on most materials.
• Temperature affects both water activity and microbial growth. Warmer temperatures promote rapid growth and many bacteria can still flourish at lower temperatures.
• Sunlight, both UV and visible light, has been shown to alter the survival
of microorganisms surviving in the built environment.
• Moisture is one of the most potent contributors to microbial survival in air and on surfaces.
• Low relative humidity (20-30 per cent) increases the ability of microorganisms to become aerosolised from surfaces and suspended due to occupant traffic or disturbance.
• High relative humidity (>80 per cent) contributes to microbial survival and activity on surfaces.
• Surface material is also critical; although all surfaces can function as a physical substrate, the chemical composition of the material provides a food source for the colonising microorganisms and potentially selects for different species. Studies have demonstrated that cellulose-based surface materials, such as, for example, wood, can stimulate microbial growth more rapidly than inorganic materials, such as gypsum, mortar, and concrete.
• pH is also important, as many metabolic processes are more energetically favorable at neutral pH; therefore, materials with an alkaline or acid pH can retard microbial growth.
• Physical composition of the surface material will affect which organisms can access the surface. Even the surface roughness, porosity, and position in the environment (for example, the ceiling or the floor) can influence the dynamics of microbial colonisation and growth. However, how these variables affect microbial metabolism and fungal–bacterial interactions remains to be elucidated and is an active area of research.
• Biofilms can form on built environment surfaces, especially in moist areas such as sinks and bathroom
“
Assessing germ contamination in the built environment is critical in determining threats to public health.
showers, facilitating transfer through everyday activities.
• Microenvironments within carpets can create pockets of high relative humidity that can aid in the growth, prolonged survival, and transfer of microorganisms to people.
How should the cleaning industry deal with large variability in local environmental conditions, including local weather, building materials, humidity, temperature, and indoor activities?
The viability of microorganisms that exist in indoor environments is an area of great interest for the cleaning industry.
Advances in techniques to visualise microorganisms in the air, in water, or on surfaces, and then also to be able to determine their viability and activity will significantly change how we clean.
Are the bacteria multiplying, fungi or mould growing, or are the viruses surviving? Are the bacteria and fungi producing microbial volatile organic compounds (MVOCs) that can influence human health outcomes? Knowing the answers will help us ensure with what and how we clean has the least negative health consequences.
For example, dust is a rich, heterogeneous mixture of materials, providing plentiful substrate for microbial growth. When exposed to moisture, the resulting germination of fungal and bacterial spores or dormant cells leads to an increase in metabolic products, which can include chlorinated hydrocarbons, amines, terpenes, alcohols, aldehydes, and ketones, as well as sulfuric and aromatic compounds.
We know that microbial metabolic products can affect human health and cause nasopharyngeal inflammation, wheezing, cough, shortness of breath, onset and exacerbation of asthma, bronchitis, respiratory infections, allergic rhinitis, eczema, and other allergies.
Everyone who enters built spaces has extensive interactions with the air and surfaces.
These interactions have traditionally been examined only regarding the transmission of potential diseasecausing germs.
Microbial transmission between occupants and the built environment is reciprocal. For example, bacterial pathogens such as Bacillus anthracis, Legionella pneumophila, and Mycobacterium tuberculosis; fungal pathogens such as Cryptococcus neoformans, Histoplasma capsulatum, and Aspergillus fumigatus; and pathogenic viruses such as rhinovirus and influenza virus, can be transmitted by direct inhalation.
Other pathogens, such as Clostridium difficile, Staphylococcus aureus, Pseudomonas aeruginosa, Pseudomonas putida, and Enterococcus faecalis, as well as norovirus and influenza virus, can be transmitted through surface contact. As people move throughout the built environment, microorganisms are constantly transferred.
Throughout history, most efforts to determine the influence of indoor microorganisms on health have focused primarily on the negative impact of disease and allergies.
How would the way we clean change if we could shift our understanding of the microbiology of the built environment from a purely negative role (that is, causing disease) to combining a positive role (that is, protective or preventive)?
The physical and chemical properties of buildings and the surface materials
encountered by microorganisms in the built environment are quite different from materials and surfaces in the natural environment.
Wood surfaces are often treated with chemicals to preserve them. Gypsum, fiberboard, drywall, synthetic carpets, and surface lacquers create environments unlike any other.
Genomic sequencing and culture studies show that different surface chemistries and physical structures promote the growth of various germs. For example, shower curtains are mainly colonised by bacteria associated with Sphingomonas and Methylobacterium. Physical surfaces in buildings have been shown to be primary sites for bacterial adhesion and biofilm formation.
The cleaning industry has a significant role in improving human health outcomes by cleaning for health. There is an immediate need by the cleaning industry to improve the measurement of cleanliness.
The COVID-19 pandemic led to a rapid expansion and the use of real-time sensors for indoor air quality. We need the development of real-time microbial sensors to detect exposures for individuals within the built environment that can be correlated with health and disease metrics. Our default approach is to attempt to make the built environment as hostile to microbial life as possible to prevent microbial infections.
Buildings are not isolation chambers. If we spend 90 per cent of our life indoors, then there is a need to better understand why, when, and how microorganisms transfer from the built environment to occupants, when these transfers lead to disease, and when these interactions are beneficial to built environment occupants. ■
Dr. Gavin Macgregor-Skinner is the senior director of the Global Biorisk Advisory Council (GBAC), a division of ISSA. Dr. Macgregor-Skinner will be presenting at the ISSA Cleaning & Hygiene Expo in Melbourne.
1 Gilbert, J. A. How do we make indoor environments and healthcare settings healthier? Microbial Biotechnology 10, 11–13 (2017).
2 Kirjavainen, P. V. et al. Microbial secondary metabolites in homes in association with moisture damage and asthma. Indoor Air 26, 448–456 (2016).
3 Lax, S. et al. Longitudinal analysis of microbial interaction between humans and the indoor environment. Science 345, 1048–1052 (2014).
4 National Academies of Sciences, Engineering, and Medicine. Microbiomes of the Built Environment: A Research Agenda for Indoor Microbiology, Human Health, and Buildings. Washington, DC: The National Academies Press. (2017)
5 Nazaroff WW. Embracing microbes in exposure science. Journal of Exposure Science & Environmental Epidemiology 29:1–10 (2019)
6 Meadow JF, Altrichter AE, Kembel SW, Moriyama M, O’Connor TK, Womack AM, et al. Bacterial communities on classroom surfaces vary with human contact. Microbiome 2:7 (2014)
COMPLIMENTARY RESOURCES FOR YOUR BUSINESS
Enjoy complimentary tools like Product Cost & Usage Calculator, Workloading & Bidding Tool, The Value of Clean Toolkit to take your business to the next level.
LOCAL
FOUNDATION
Share in our vision, mission, values and goals. Together we can change the way the world views cleaning.
MEMBER
Get featured in the online listing of all members which attracts over 15,000 clicks per month and provides access to all company profiles.
The
team is working with
number
local service providers to provide members with exclusive discounts to relevant services.
TRENDS
Gain valuable market analysis both regionally and globally.
GLOBAL
Whether you’re an environmental services worker in a hospital or a custodian in a school or office, the first piece of personal protective equipment (PPE) you most likely reach for is a pair of disposable gloves.
In industries such as cleaning, food service, industrial or health care, disposable gloves are used to protect people from processes and to protect processes from people.
Trends in personal safety have increased the demand for single-use gloves.
Statistics from 2022 found the global market for disposable gloves accounted for US$13.6 billion in 2021 and is expected to reach $27 billion by 2030, a compound annual growth rate (CAGR) of 7.9 per cent, according to Acumen Research and Consulting.
Despite their popularity, disposable gloves are often an improperly used asset. Some of the most common mistakes users make include:
• Not properly washing their hands prior to wearing gloves. This can lead to contamination of the gloves and defeat the purpose of wearing them in the first place.
• Touching their face or other surfaces with their gloved hands. This action also could lead to contamination and potential risk to the user and others.
• Not changing gloves frequently enough. Gloves can become contaminated over time, so it’s important to change them regularly. Replace your gloves whenever they become soiled or damaged, or when you move from one task to another.
• Reusing disposable gloves. Disposable gloves are designed for single use only and should be discarded after each use.
• Not disposing of the gloves properly. It’s important to dispose of them in a designated
• waste receptacle, as opposed to throwing them on the floor or in a sink.
Even if you follow proper procedures, your gloves won’t offer protection if they’re the wrong glove for you or your job. When choosing disposable gloves, always consider fit, form, and function.
Properly fitting gloves allow for dexterity and help prevent tearing. Make sure you’re wearing a glove that is snug but not constricting. Too tight of a glove creates hand fatigue, while too loose of a glove will compromise dexterity and make tasks harder to perform.
A glove’s form, or properties, are important in choosing the appropriate material for any potential risks, such as chemicals or biohazards. Consider the
level of protection needed and remember that glove thickness doesn’t always equal strength.
Vinyl or nitrile gloves are best for regular cleaning tasks such as dusting, mopping, and wiping, as they provide a good barrier against cleaning chemicals and are durable enough to withstand frequent use. As a rule of thumb, for short duration and mild chemical exposure, use vinyl. For harsh chemicals, extended use, or when tactile feel is more important, choose nitrile.
Latex gloves are puncture resistance and offer excellent hand dexterity. However, make sure your workers are not allergic to latex before choosing them.
As workers are more likely to use gloves that are easy to don, consider gloves that are treated with powder coating (such as cornstarch), which helps the glove slide more easily over one’s hand.
Finally, determine what function the gloves need to provide. Will they need to protect workers from chemicals or bodily fluids? Will users need extreme grip or finger dexterity while wearing them? Chemical resistance charts and glove application selection tools can provide advice regarding the best glove for specific jobs.
To ensure gloves meet their purpose, choose a quality pair from a reputable brand, and inspect them for any defects before use, and check if they have been found to meet quality standards.
For tasks where you need more protection, such as handling sharps (containers for used needles) or materials that might contain bloodborne pathogens, it’s important to use gloves specifically designed for those risks.
In critical environments, refer to safety data sheets (SDS), manufacturers’ recommendations, and facility standard operating procedures (SOPs) to ensure that you are using the proper PPE.
Common recommendations for these scenarios include using an exam-grade product of a specific material type (such as nitrile), a specific thickness, or even specific certifications (e.g., a chemotherapy rating or a fentanyl rating).
For tasks that involve handling materials that could contain bloodborne pathogens, such as those found in a hospital or a restroom, suitable PPE would include not only gloves, but also gowns, masks, and eye protection.
Properly fitting gloves allow for dexterity and help prevent tearing.
Perhaps one of the biggest mistakes glove users make is putting them on (donning) and removing them (doffing) incorrectly. Follow the correct procedures to ensure that the user, the cleaning process, and the environment are not compromised using disposable gloves.
To properly don disposable gloves:
• Take the gloves out of the packaging and ensure that they are the correct size and
• free from defects
• Hold the glove by the cuff and slide your fingers into the glove, making sure it
• is fully extended over your hand and fingers
• With your fingers in the glove, use the opposite thumb to insert and pull the glove
• from the inside palm to fully extend the glove to appropriate cuff length
• To ensure a snug fit, smooth out any wrinkles or air bubbles in the glove
• Repeat this process with the second glove.
To properly doff disposable gloves:
• With one hand, pull the opposing hand cuff and pull the glove away from the
• body, turning it inside out as you do so
• Hold the inside-out glove in the palm of the other gloved hand and gently pull from
• the inside of the cuff and away from the body, turning inside and out, which also
• secures two gloves
• Discard the gloves in a designated waste container
• Wash your hands or put on hand sanitiser immediately after removing gloves
Expansions in the nitrile category, including material thickness, are among the newest developments in the disposable glove market. As manufacturing has become more sophisticated, products have realised greater material consistency.
The market for natural rubber disposable products has decreased, replaced by a demand for nitrile products. The global nitrile gloves market is expected to grow from $9.2 billion in 2021 to $15.6 billion by 2030, a CAGR of 6.1 per cent, according to a report published by Spherical Insights & Consulting. In response, manufacturing facilities have expanded the nitrile glove category, offering new developments in thickness, texture, color, and certification standards.
Over the last several years, the disposable glove market has seen a significant amount of volatility due to demand fluctuations, as well as unpredictable international transportation of goods.
The COVID-19 pandemic forced the industry to focus on limited options that were the most cost-effective solutions to meet the increase in demand for PPE. Blended substrates and thinner gloves were the byproduct of these market fluctuations. Unfortunately, some of these new products lacked the quality needed for specific applications.
In addition, new entrants into the market from traditionally nonglove importers fueled rapid price increases. Quality suppliers of imported gloves have focused on making sure inventory is readily available for all types of disposable gloves and ensuring customers get the best glove for its intended application. This is a mature industry with end users who are cost conscious, which means innovation is limited. However, users are delighted to see greater availability from quality suppliers who can offer a full line with multiple colors, sizes, and thicknesses at affordable prices. ■
Eric Phipps is vice president of sales for Tradex International. This article was first published by CMM has been republished with permission.
“
Replace your gloves whenever they become soiled or damaged, or when you move from one task to another.
An industry body plays a key role in bringing people of an industry together, being the voice of that industry, and championing the priorities of its members.
To ensure BSCNZ understand and prioritise member needs we conducted a member research survey. The top priority and reason why members join the BSCNZ is to ensure our industry voice is heard by policy makers and government officials. Over the past several years BSCNZ has made significant connections within government to relay our industry voice.
With the election pending, the messaging from the BSCNZ needs to be clear and not just resonate across this current government but also a potential new government. Given the significance, and size of our industry, it is critical that our voice is heard.
BSCNZ members have very strong views on the challenges facing our industry and businesses in general. The key area of significance is an increase in the cost of doing business; 96 per cent of BSCNZ members have experienced an increase in their costs over the past few years. Seventy per cent have seen an increase in tax compliance. Other expenses are labour, insurance, fuel, and the cost of immigration.
Seventy per cent of survey respondents believe personal tax rates should be lowered, while 52 per cent believe corporate tax rates should remain the same. Sixty-five per cent of members do not agree with “windfall” taxes on profitable businesses. Members do not see this current government as capably handling key economic disruptions such as COVID-19 and recent flooding events, with 91 per cent agreeing that there is a lack of coordinated planning.
Immigration settings are another area of concern, with ninety per cent of BSCNZ members stating that they do not have confidence in current immigration settings.
There seems to be a disconnect between business and government when it comes to the government’s programme to deliver a “pipeline of talent”. Thirty-nine per cent of members said “no, the programme isn’t working”, while another 43 per cent were unaware of any ‘pipeline’.
When reviewing the Accredited Employer Assisted Visa system, 43 per cent of members believe this has made employing immigrants more difficult.
All respondents agreed that immigration settings need to be streamlined and simplified. Members want to see it made easier to obtain approval for work visa, and the renewal process simplified. Many members would welcome a more industry orientated approach towards developing solutions to skill gaps and labour market constraints.
In June, the Ministry of Business, Innovation and Employment (MBIE) was open to receiving submissions as they are currently reviewing the immigration Green List. Based upon our members’ feedback, BSCNZ forwarded a submission to request facility managers, sustainability managers, commercial cleaning site specialist, building exterior cleaners, window cleaners, hard floor specialist cleaners, and supervisors be added to this list.
If added to the Green List, it will allow immigrants in these roles to apply for citizenship and continue to work and live in New Zealand permanently. Results of this submission will be made available to members in due course.
In June, the MBIE CEO approved Fair Pay Agreements (FPA) for commercial cleaners. Eighty-seven per cent of BSCNZ members see FPA’s as having a negative
effect on our industry. Like many industry bodies we lobbied against FPA legislation coming into law but were ignored.
Seventy per cent of BSCNZ members actively work with clients to support the implementation of the living wage, but this is always client dependant. Given the current economic climate, it is impossible for some clients to agree to the Living Wage, and many of those are government funded departments with limited budgets.
BSCNZ members have always supported fair pay and appropriate working conditions, this is reflected in having the longest standing collective agreement in New Zealand. We do not see that it is the government’s place to force bargaining, but this is the situation our industry, and many others, currently face.
In line with the BSCNZ values and member ethos we will celebrate our industry workers again this year. Thank Your Cleaner Day will be celebrated on Wednesday, 18 October 2023. Please get in touch or go to www. thankyourcleanerday.co.nz for more information on how to get involved. ■
Include
Natural disasters might be a rare occurrence and, subsequently, a very low risk for most facilities—but that doesn’t mean you shouldn’t prepare for one.
It takes just one natural disaster, such as a flash flood, to severely damage a facility. Buildings can be compromised or inoperable for days, weeks, or even months. In addition to structural damage, natural disasters can cause significant financial losses.
Identify which natural disasters pose the greatest threat to your facility. If you are in a high-risk zone – prone to disasters – it’s even more important to be cautious. You should assess other potential risks as well, including bushfires and severe storms.
The most successful natural disaster management systems are comprehensive with a risk-focused strategy. The following advice can help you be prepared if a natural disaster strikes.
You can’t be prepared for a natural disaster without having details about your facility at hand. It’s necessary to have detailed blueprints of the entire site, including
important infrastructure like hazardous installations of chemical processes and equipment, gas pipelines, and drainage systems. Knowing the location of all drainage systems can help redirect floodwaters, and understanding which pipelines might have been damaged during an earthquake can aid in postdisaster management.
Take particular care to identify areas that could pose more significant problems, such as those containing hazardous machinery or chemicals, or equipment that is crucial for the facility’s operation. Also, it’s important to know the location of all designated confined spaces. This information can be critical in determining where workers might become trapped during a disaster or to prevent potential risks, such as toxic gas build-up.
Consider using building information modelling (BIM) to gather information about your facility. BIM is not just a tool for designing and constructing buildings. Its 3D facility representations can provide a comprehensive database of a building’s maintenance history and physical assets. Asset information is critical for understanding the physical layout and infrastructure of your facility.
Once your site knowledge is well established, you’re ready to put a comprehensive natural disaster risk management plan in place. This plan should be a part of your safety management system and include measures to be taken in the following four phases, as outlined in an article on crisis and disasters risk management published in Ethics, Medicine & Public Health.
Preparedness: Actions taken prior to an emergency to facilitate response and promote readiness
Response: Actions taken during an emergency to save lives, property, and the environment
Recovery: Actions taken after an emergency to restore and resume normal operations
Mitigation: Efforts to reduce the effects or risks associated with hazards. You can also take the following threepart approach to natural disaster management, as outlined in an article on emergency disaster response by the British Geological Survey: Pre-disaster: This stage involves taking a risk assessment of your facility, setting up preventative measures, and seeking participation from all building residents.
It also involves setting up a warning system and an evacuation plan.
Disaster: At this stage, you will be focusing on providing immediate assistance to those directly affected by the disaster. The next priorities include assessing damage, providing ongoing assistance, and restoring infrastructure.
Post-disaster: The stage immediately after the disaster involves reconstruction, the process of economic and social recovery, and ongoing development.
Once you have your natural disaster response plan in place, it’s important to do the following:
Check your emergency equipment, such as sirens, bells, and digital alerts. Make sure they are working properly and can be easily heard or seen.
Include hypothetical natural disasters in your emergency drills. This will help you determine how quickly your employees can respond and evacuate.
Inquire about the response times of local, state, and federal agencies. This is especially important if your facility contains hazardous materials or equipment. It’s a good idea to establish communication channels with these agencies before you need them in an actual emergency.
Employee buy-in is crucial to your facility’s natural emergency planning. To achieve this, establish a team of employee representatives from the entire facility to coordinate planning and respond to natural disasters. Also involve employees in your facility’s disaster risk management process. Don’t fall into the trap of making risk assessments the sole domain of management.
Your emergency response planning should entail training employees in your facility’s natural disaster response. Ensure that all employees receive appropriate training based on the facility’s natural disaster risk profile.
When preparing for natural disasters, prioritize safety over assets. Your main focus should be ensuring your employees’ wellbeing—79 per cent of them consider their health and safety a top priority, according to the 2022 State of Employee Safety Report.
Safety works best as a proactive process. For example, your facility could invest in disaster-resilient architecture. However, it’s important to consider
the drawbacks of this approach. While materials like concrete, glazed bricks, and steel hardware can minimize flood damage, they can be hazardous during an earthquake. Conduct a cost-benefit analysis (CBA) before making any decisions regarding safety measures.
Can a facility and its employees ever be 100 per cent prepared and protected for a natural disaster? The short answer is, no, not a chance. Natural disasters are simply too unpredictable. Any risk management professional will tell you that claiming 100 per cent protection from natural disasters is foolish.
As natural disasters are inherently dangerous and unforeseeable, it can be tempting to do nothing in the hopes that your facility will never be struck by disaster. But despite the uncertainties, being as prepared as possible is the most effective way to mitigate the risks of a natural disaster or an extreme weather event. ■
Bryan Christiansen is the founder and CEO of Limble CMMS. He can be reached at bryan@limblecmms.com
“
Natural disasters might be a rare occurrence and, subsequently, a very low risk for most facilities—but that doesn’t mean you shouldn’t prepare for one.
Following extensive research, listening to both distributors, customers, and end users, Livi has developed an all-new website. The new online platform is easier than ever to use, and helps users create quality away from home experiences for customers and staff. The new website features a host of upgrades that can help find what you need quickly and easily. The website is now live www.livi.co.nz
Livi
www.livi.co.nz
Suma Bio-Floor Plus Cleaner is a new cleaner and deodoriser that soaks into grout and tile pores and eats the grease. Bacteriaenhanced cleaning power that continues long after you put away the mop.Suma Bio-Floor Plus contains armies of self-replicating, nonpathogenic bacteria that attack and remove the soil build-ups in the grout & tile pore, making the floors safer to walk on.Formulated with five strains of bacteria, simultaneously producing different classes of enzymes:
· Lipase – to digest fats, greases, and oils
· Protease – to digest proteins
· Amylase – to digest starch
· Cellulase – to digest plant and vegetable matter
Bacteria digest the entire soil by releasing vast quantities of enzymes. Bacteria work progressively, moving from one type of soil to another, releasing different types of enzymes, one after the other. Once working, the bacteria can reproduce for hours or days, continuing to clean when mopping stops. Suma Bio-Floor Plus Cleaner does not need rinsing, saving time and water.
Diversey
The Learning Centre (TLC) was established with the purpose of empowering you and your team to optimise the ongoing performance of your professional cleaning equipment. Through the TLC portal, cleaning staff (whether new or existing) gain access to comprehensive product training. This includes quickstart guides, easy maintenance instructions, and best-practice tips, all on one convenient website. Enrolment is free and participants are issued certificates to recognise successful course completion. Equip your team with the skills and knowledge needed to maximise the performance, cost-effectiveness, and lifespan of your equipment at The Learning Centre - powered by Proquip. The Learning Centre
0800 277 678
thelearningcentre.proquipnz.co.nz
Mr Bean is a commercial-grade disinfectant, air freshener, and multipurpose cleaner. It is designed for use in commercial and residential environments and is safe to use on benchtops, walls, floors, air fresheners, and high touch points.
• Long-lasting residual action
• General purpose cleaner
• Pleasant tutti-frutti fragrance Whiteley Corporation
1800 833 566 marketing@whiteley.co.nz
Multi-Clean offers a range of high-performance commercial cleaning chemicals and floor maintenance products for the commercial cleaning industry. The Multi-Clean Multi-Purpose Citrus Solvent Cleaner/Degreaser is a dilutable, adhesive remover, that can also remove rubber tire marks.
The Multi-Clean Carpet Spotter is an all-purpose spotter formulated with detergents and fortified with solvents for removing a variety of common stains. It loosens spots for quick removal and does not leave a sticky residue behind. Use on greasy traffic smudges, shoe polish, India ink, fruit juices, oily stains.
The Multi-Clean Eliminator Spray ‘n Wipe power cleaner is stronger than general purpose cleaners, attacks and lifts everyday grease and grime on hundreds of surfaces. Simply spray and wipe surfaces clean.
NZ Cleaning Supplies
info@cleaningsupplies.net.nz
www.cleaningsupplies.net.nz
The future of Rapid Scrubbing is here. The RapidClean RC1 Scrubber has a 360o swivel point for exceptional manoeuvrability and control fitted with a heavy-duty by-pass vacuum motor providing effortless cleaning in all applications. RC1’s smart mounted dashboard clearly displays power and battery usage and allows you to independently control water, vacuum and speed settings.
RapidClean New Zealand
0508 727 433 sales@rapidclean.co.nz www.rapidclean.co.nz
Sanitol Jade is a uniquely formulated antibacterial hand sanitiser designed to prevent the spread of harmful germs. Sanitol Jade has a rapidly acting formula that kills 99.99 per cent of germs – protecting you against a range of potentially unsafe microorganisms. Sanitol Jade is an effective component of a personal hygiene program, and its scientifically advanced formula is gentle on all skin types.
Benefits:
• Contains natural emollients to replenish the skin’s lipids – leaves hands feeling soft, smooth and revitalised
• Natural skin conditioners and light pleasant fragrance – ideal for all ages to use
• A refreshing gel that kills germs without the need for water
Whiteley Corporation
1800 833 566
marketing@whiteley.co.nz
More than 70 per cent of vacuuming is undertaken in daytime hours leading to noise issues creating customer/guest disturbance. Diversey has the answer to reduce noise levels!
TASKI AERO 8 Plus tub vacuum cleaner with whisper quiet technology. The TASKI AERO 8 Plus vacuum combines patented ultra-silent, whisper technology with an airflow system which delivers reliable and efficient cleaning at a peak noise rating of 53db(A), making it an ideal choice for both daytime and night-time cleaning. The efficient state-of-the-art 585W motor delivers the same cleaning result as a motor with more than 900W, achieved through the ingenious patent airflow system which also works to reduce energy costs and CO2. TASKI AERO 8 Plus features include dust bag indicator and optional HEPA filters, an ‘Eco mode’ button - just one press and noise emission fall to 50db (A) with an energy consumption decrease of roughly 50 percent to 300 watts.
Diversey New Zealand
0800 803 615
www.diversey.co.nz
The unique formula of V-Wipes disinfectant wipes is proven to kill a broad variety of bacteria and viruses, including SARSCoV-2 (COVID-19) Virus which is killed in 60 seconds. The formulation is pH neutral, and they feature a high-quality apertured fabric perfect for fast, effective cleaning and disinfection of all surfaces within the healthcare environment. V-Wipes is an Instrument Grade Disinfectant – low level and can be used on environmental surfaces and non-critical medical devices such as hospital beds and theatre trolleys. Class IIb Instrument Grade Disinfectant – LowLevel Wipes.
• pH neutral – safe for use on most surfaces and equipment
• Highly absorbent apertured fabric
• Leaves surfaces streak free
Whiteley Corporation
1800 833 566
marketing@whiteley.co.nz
Introducing Kärcher’s KIRA B 50 cleaning robot - the ideal solution for cleaning floors in medium to large sized areas. With the latest technology and multi-sensor system, this fully autonomous scrubber dryer robot can efficiently clean designated areas, freeing up your cleaning team to focus on more complex tasks. With roller brush technology and a side brush for edge cleaning, the KIRA B 50 ensures excellent cleaning results while reducing the need for manual prep and follow-up work. Plus, with its intuitive touch display and web portal connectivity, you can easily manage and monitor your cleaning robot from anywhere. Kärcher’s commitment to safety and data protection is validated by independent bodies, making KIRA B 50 the perfect addition to any cleaning team.
Kärcher New Zealand
+64 9 274 4603
customerservice@karcher.co.nz
karcher.co.nz