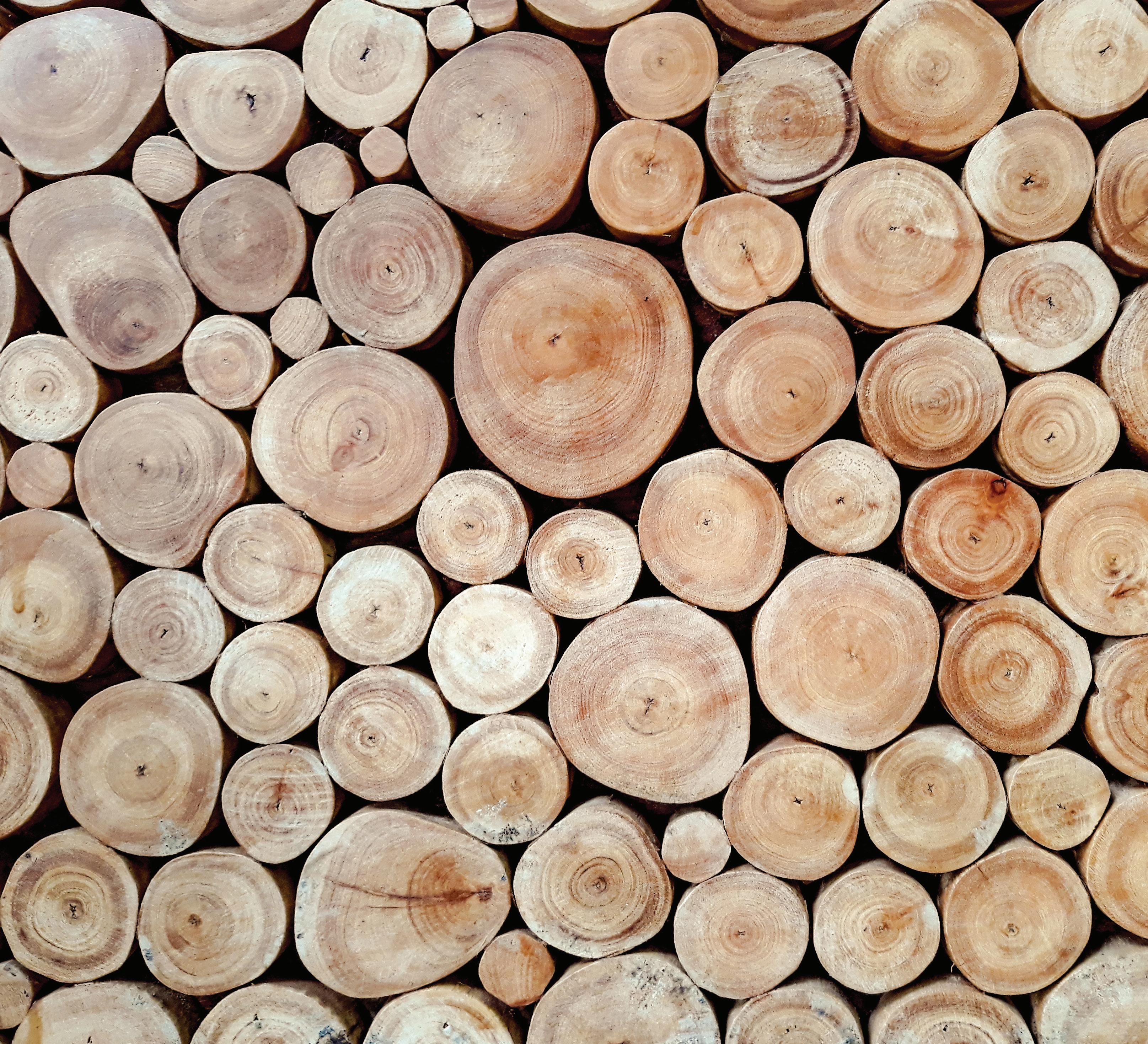
3 minute read
THE CIRCULAR ECONOMY
Asif Din
The concept known as Circular Economy uses the lens of material management to make sure that resources are not used indiscriminately. As a starting point, the goal is for the minimization of waste produced across all life cycle stages of a building material, as well as looking to maintain material value through reuse. A wide range of strategies are used to ensure that materials are fit for reuse and do not end up in a landfill. Earth’s resources are finite and cannot be infinitely replenished. In recent years, the amount of human-made mass has exceeded all living biomass.* It is paramount, therefore, that we do everything we can to maximize the viable lifespans of our building materials. The longer our materials last, and the more times they can be reused, the less new material must be made.
The circular economy has two main classifications of material components: technological items – which need to be kept at their highest value in the system as long as possible –and biological materials that can be returned to the earth for decomposition.
Many new regulations have been implemented that focus on reducing waste taken to landfill in the process of construction. This is beneficial for increasing material resources – the less we waste, the less we have to produce – but it does not do much to help retain material value. Material value is often defined in two ways – functionally, and financially. Another way to think of this is as usefulness - if a product can retain its functional or financial usefulness, more care will be taken to reuse it rather than discard it.Currently, when the term “recycling” is used, it does not refer to a closed loop system, wherein 100% of the recycled material is reused. Far from it, only a small fraction of the existing “recycled” materials are used in a new product.
An example of circular design can be seen at the new hospital in St Pancras, London, in which an adaptable façade has been designed to accommodate internal programmatic changes. As the interior layout of the building may change to adapt tovarious needs or uses, so too can the modules of the façade be moved to suit. Likewise, the mechanical and electrical systems within the building also follow a modular design, allowing the building to be easily converted (with suitable module replacement of the façade) into a commercial or residential usage in the future.
To reuse the maximum number of materials already in existence, differing models have been put forward, such as “Buildings as Material Banks” and “Urban Mining”. These various models all essentially describe the same core concept – to reimagine our urban fabric and existing building stock as libraries of alreadymanufactured materials ready to be repurposed.
By examining embodied carbon and life cycle analyses (Module D of ISO 15978), we have been exploring how corporate interiors can benefit from a circular materials approach. In order to be most beneficial, this process should begin at the earliest opportunity in the design of the project, using design and procurement strategies to enable a circular future.

Addressing embodied carbon in interiors projects is crucial, as the embodied carbon of an office building’s interiors can quickly surpass the embodied carbon of the shell and core if replaced any more than once in 10 years.
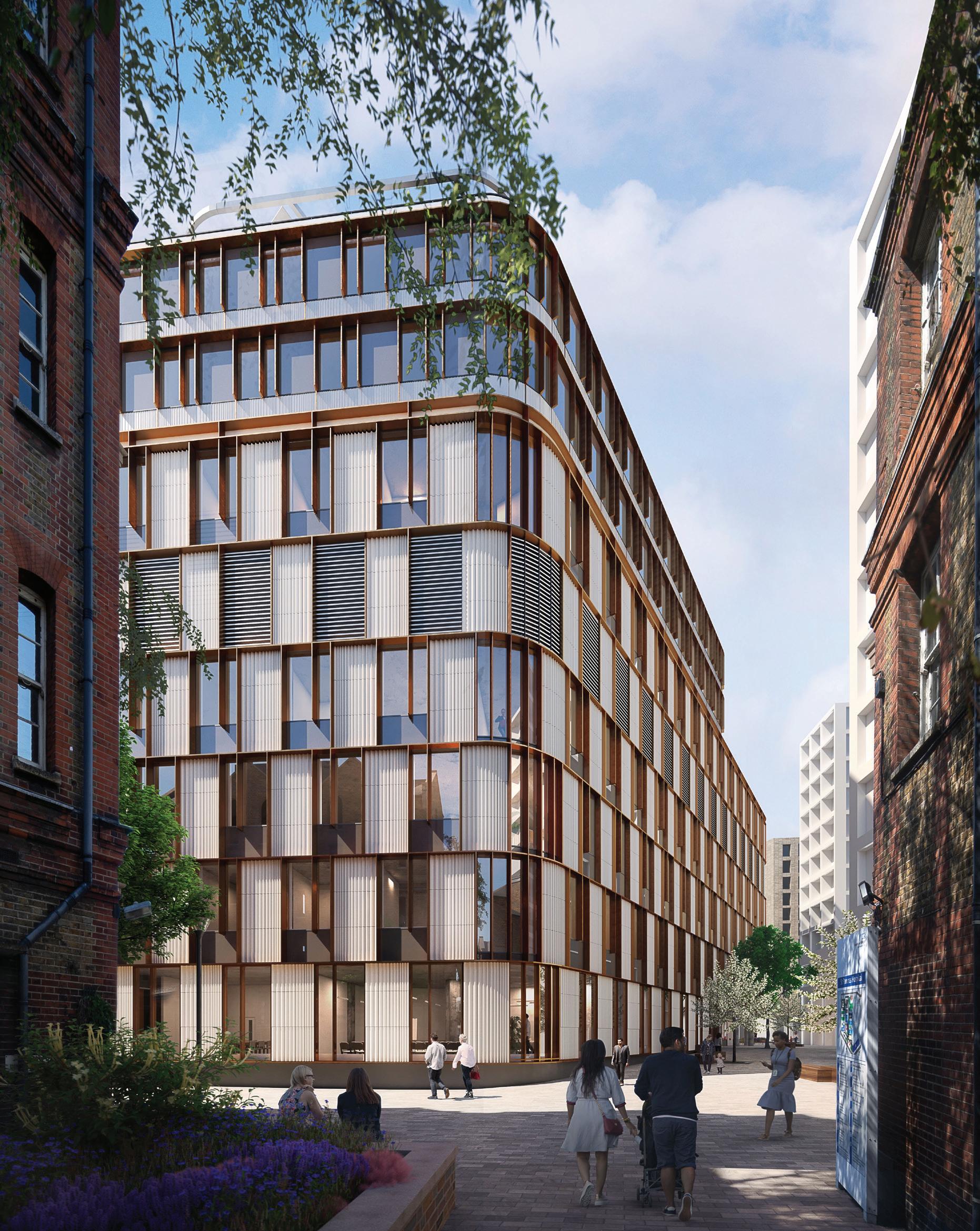
Life Cycle Loop
With the current turnover rate in office space, building interiors are often retrofit far more frequently than once every decade. As designers, we need to establish what we are responsible for specifying and make sure that these elements can be specified in the most circular method we can. As such, our process is dominated by the specification of interior furnishes and fittings.
Accounting for the initial embodied carbon of a new building’s interiors can be quickly optimized. However, quite often, much of an office building’s interiors are replaced long before the end of their service lifespan. This is a waste of materials, carbon, and money. Much greater accountability is needed to track interior retrofits across the industry, within company accounts through IFRS (International Financial Reporting Standards) and other accounting mechanisms.
It is important not to think solely about capital expenditure, but also to take into account the residual value that remains after the fit out cycle. This is a key part of thinking about circular design processes. However, this way of thinking is not a part of the current status quo. Often, we have clients who request interior retrofits of their current office spaces with an expected lifespan of less than 5 years, which is expensive and wasteful.