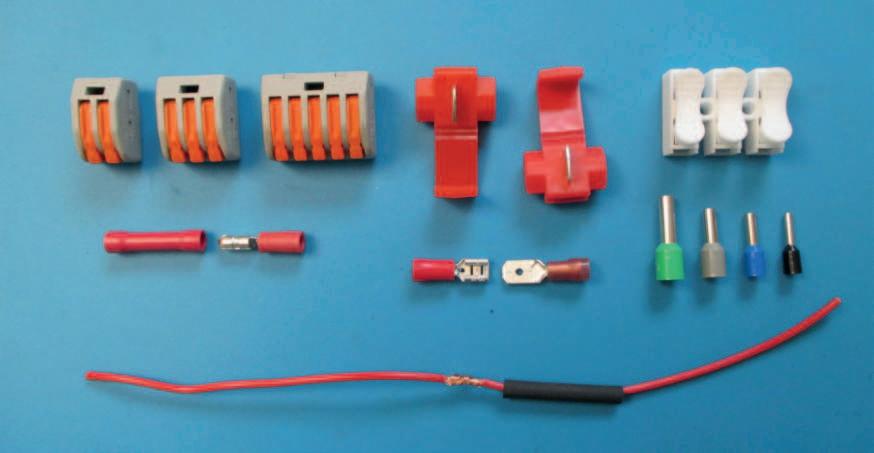
9 minute read
REWIRING
MAKING CONNECTIONS
NOTES ON DEALING WITH WIRING ON OLDER CARS. WORDS & PHOTOGR APHY Gil Keane
Advertisement
will start by apologising to those who thought
Ithis might be about improving their position in society. Although, as we all know, owning and running older cars is a wonderful way to make friends from all walks of life, and breaks down most of the traditional class barriers.
To keep older cars alive, we have to make them both safe and reliable, and the two are more connected than you might suppose. A car that has unreliable electrics can be unpredictable, and perhaps prone to stopping or slowing in unexpected places. This generates a hazard to all road users in the vicinity. Also, making older cars safe to use in modern road conditions can involve adding new equipment, or updating existing equipment, and how we do this can greatly affect the reliability of our cars.
TAKE NOTHING FOR GRANTED.
In a lifetime spanning many generations, most cars will have been subjected to the attentions of a lot of different, and (mostly) well-meaning hands. This can lead to some surprises. A wire which starts out as one colour as it makes its way through the car, may be a different colour when it arrives at its destination. This is just one example of the sort of pragmatism that was often necessary, especially during the years when our treasured classic or vintage car was worth very little. Using a test light to check which wires are live and which are earth makes life easier, and checking that a wire with live going in at one end has a live coming out at the other is a useful check to make as a matter of course. Finding a good earth wire is less straightforward, because, and this can be a very important point, a wire which is a live wire in your diagram will become an earth wire when the power is removed. This is because one end of it is attached to something (like a bulb) which is earthed. This is something you can turn to your advantage, and car makers often do, but you need to be aware of it, or be condemned to spend a lot of time scratching your head. Another thing you should never take for granted is that the bulb or other electrical item you have just installed, and which does not work, is clearly faulty. It might be, but not only will you waste quite a lot of your time if you are wrong, but you will waste other people’s time as well, and may have to repeat the process endlessly before you solve the problem. Using a simple
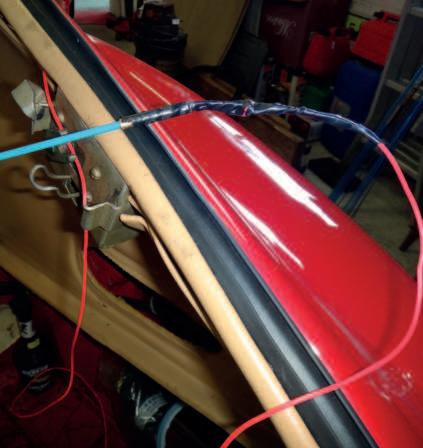
double-check method will help. If you are fitting a pair of bulbs, for example and one works fine but one doesn’t, swap them over. If the problem moves with the bulb, then you have a duff bulb. Or try the stubborn one on a battery or charger. If it works fine then, the problem is on the car, not the bulb. At times like this, it is worth remembering that things that draw a lot of current will often work fine in spite of poor connections. Things that draw very little will not, and that includes LEDs and most other electronic items. Another thing to know, is that totally different technologies (surprise!) work totally differently. If you say out loud “It must be the bulb because my old one works fine in there”, then you will hear a totally illogical statement, and there is a future for you in American politics. LEDs, for example, are so efficient because they are incredibly sensitive, and so react in a big way to tiny amounts of current. The bad news is that delicate things are easily destroyed. Not so many years ago, any LED device would have one shot at life, but if you connected it wrongly, it would die instantly and expensively. These days, we can design in miniaturised protection circuits that make them a lot more durable, but can lead to confusion. They need, for example, to be protected from spikes of voltage and reverse polarity, and if they encounter these, an internal “switch” will turn them off to protect the internals. So far, so good, but imagine that you have a car where the rear tail lights and the rear number plate light are all on one power line, daisy-chain fashion. Number plate lights are often vulnerable to damage or corrosion and often get taken apart for cleaning or to get replaced. They don’t always have the connections put back the same way around, and because a filament bulb will work either way, it won’t show. But your LED bulbs will detect this and may well go into “protect mode”. At this point, saying that the LED bulbs are hopeless and your own bulbs worked fine won’t fix the problem, but checking, and if necessary, correcting the reverse polarity will. And you will also be able to wear a slightly smug smile when you describe your adventure to fellow enthusiasts.
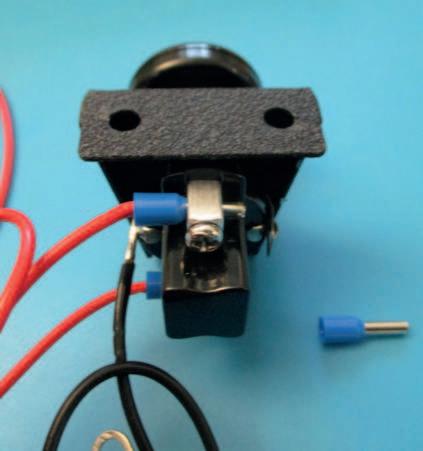
THINK AHEAD
When we add extra features to older cars, that invariably means running new and extra wires, often from front to rear. We will know that we need one, or perhaps two wires to achieve our goal, but what we cannot know is what the future holds. Part of our existing wiring loom could become damaged, or something that we had never considered may become either desirable or mandatory. For example, it has been possible for some time that red rear foglights might become compulsory for all cars of all ages. Instead of running the bare minimum of wires for the immediate need, consider running some black sheathed towbar multi-core wiring. That way, you can complete the job in hand and have spare wires in place for whatever needs may arise in the coming years.
JOINING THINGS TOGETHER
When joining wires together, or when connecting wires to various switches or other equipment, a couple of minutes considering the best way is time well spent.
Ori g i n a l w i re g o es s tr ai g h t th rou g h c o n n ec to r w i th o u t c u tti n g . Ori g i n a l w i re g o es s tr ai g h t th rou g h c o n n ec to r w i th o u t c u tti n g .
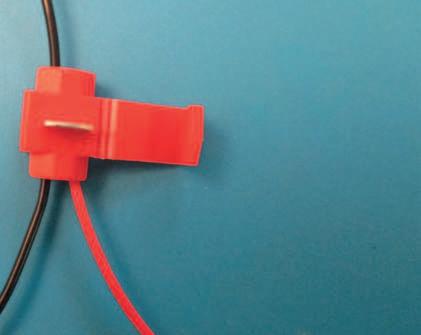
Seco n d w i re g o es i n to cul de sac Seco n d w i re g o es i n to cul de sac s e cti o n. Both ar e co n n ected s e cti o n. Both ar e co n n ected e l e c tr i ca l l y wh en co n n ector i s e l e c tr i ca l l y wh en co n n ector i s s n a p p e d s hu t. s n a p p e d s hu t.
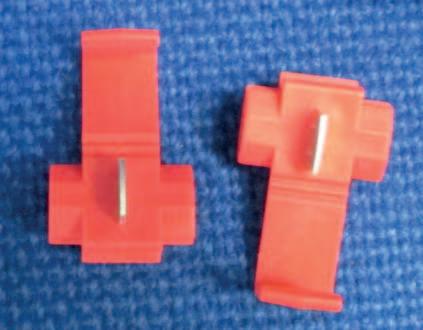
For example, most electrical equipment on early cars relied on you poking a bared wire into a screw terminal block. Now if you picture this in your head, and move into to a close up view, you are putting a multi-strand, soft, copper wire into a confined space, and then you are crushing it with a metal screw, which, just to ensure maximum damage, is being rotated. You won’t need the most fertile imagination to see how this is not ideal, and to understand why, when that wire is being bounced around by the suspension, wires sometimes break. If you have to use a screw terminal connector, you can slip a bootlace terminal over the end of the wire first. These can be crimped or soldered into position, or you can just hold it there until the screw locks it into position. That joint will stay good for decades. I mentioned solder a moment ago. This is a wonderful process, but only when done properly and in appropriate circumstances. In that order, when you are soldering, the correct technique is to melt a small amount of solder onto the tip of the iron, but this is only there to allow better heat transfer to the wire you want to solder. Then, you touch the tip of your solder to the wire, not the iron. When the temperature is right, it will melt into the wire and make a good joint. Otherwise, the solder will sit on the surface, looking good, but doing very little. That is known as a “dry joint”. When might soldering be inappropriate? Well one example is where you should really “prove” a circuit to ensure that you have everything connected correctly, before making it permanent. You could make temporary connections using scotchlocks or similar, and then make it a more durable job. Another time when soldering might be unwise is when the heat could cause a problem to nearby items and you can’t isolate those items. Finally, if a wire is likely to be bouncing up and down as you drive, and you tinned the end and then put it into a connector, you will have a rigid section, which suddenly becomes flexible, and the movement will be like you breaking a green twig, with the same eventual result. Either secure the wire fully, or don’t use solder. A soldered joint with heat-shrink tubing over it always looks neat, but please remember that heat-shrink is not waterproof unless you use the gluefilled variety, which is ideal for exposed areas.
MYTHS
If you are connecting wires in difficult to access places, like behind the dash, as long as you are working in an area which is not going to be subjected to moist conditions, there is nothing wrong with using the dreaded scotchlocks. These gained a bad reputation decades ago in the car alarm boom of the 80s, mainly because bad auto electricians, (or often fitters with no training) used them to cut fitting times and used them in places where they were exposed and they went rusty and caused problems. However, the initial design logic holds good. They enable you to try out a circuit and then change it, (as when you remove it, the insulation will self-heal), and to connect onto wires without cutting them. They also allow you to work in spaces that would otherwise be impossible with major dismantling. There are also small lever-arm multi connectors that are a godsend, especially when working with very thin wires, and can be permanent, or just to try out circuits. These might be frowned on by traditionalists, but if they are out of sight, and the do the job, where is the problem?
Gil Keane, The 4Sight Lighting Co. www.bettercarlighting.co.uk enquiries@bettercarlighting.co.uk
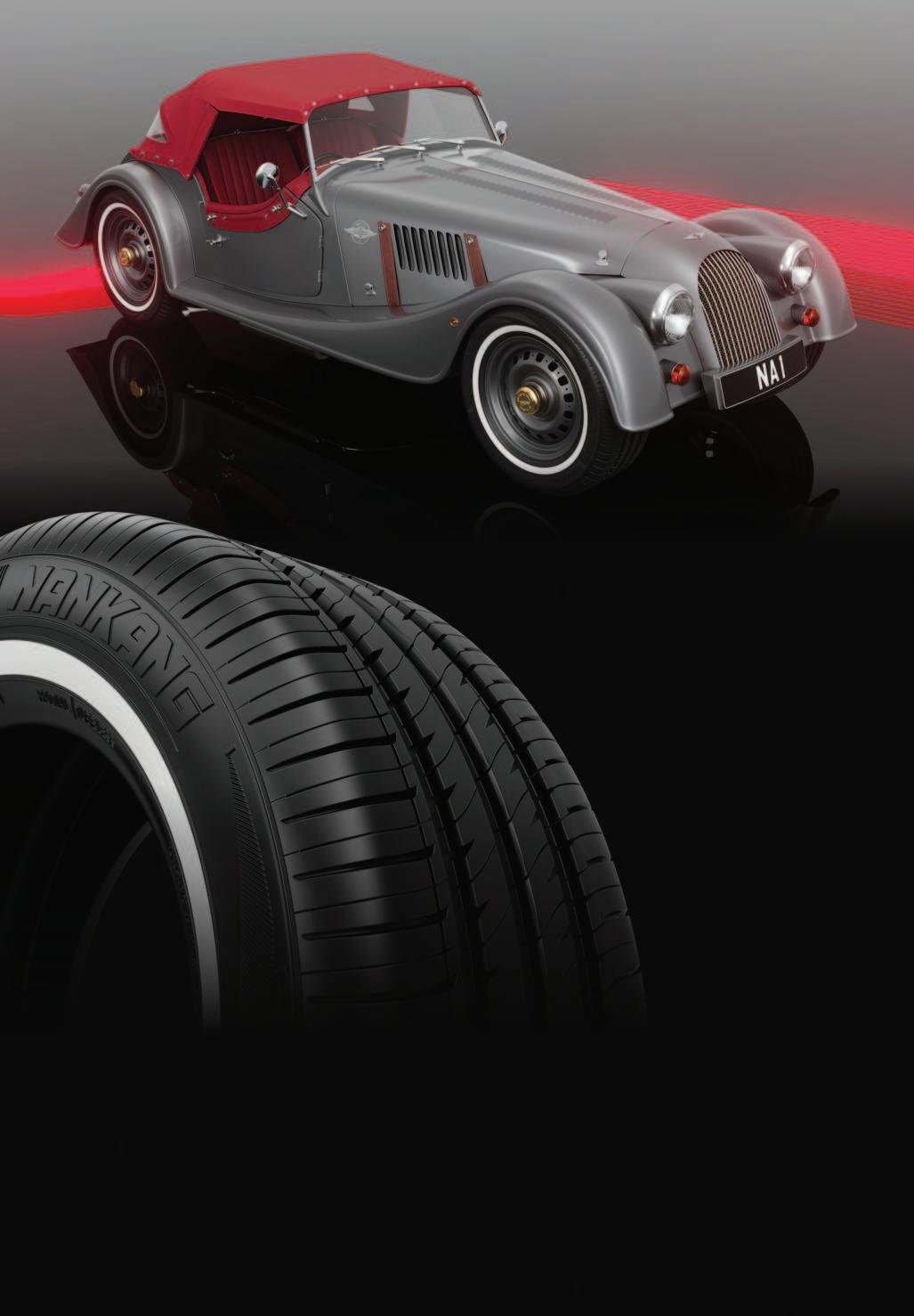